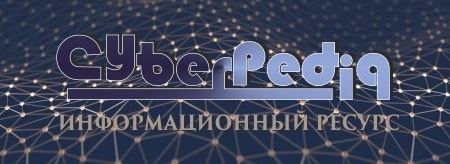
Наброски и зарисовки растений, плодов, цветов: Освоить конструктивное построение структуры дерева через зарисовки отдельных деревьев, группы деревьев...
Типы сооружений для обработки осадков: Септиками называются сооружения, в которых одновременно происходят осветление сточной жидкости...
Топ:
Устройство и оснащение процедурного кабинета: Решающая роль в обеспечении правильного лечения пациентов отводится процедурной медсестре...
Теоретическая значимость работы: Описание теоретической значимости (ценности) результатов исследования должно присутствовать во введении...
Оценка эффективности инструментов коммуникационной политики: Внешние коммуникации - обмен информацией между организацией и её внешней средой...
Интересное:
Аура как энергетическое поле: многослойную ауру человека можно представить себе подобным...
Искусственное повышение поверхности территории: Варианты искусственного повышения поверхности территории необходимо выбирать на основе анализа следующих характеристик защищаемой территории...
Распространение рака на другие отдаленные от желудка органы: Характерных симптомов рака желудка не существует. Выраженные симптомы появляются, когда опухоль...
Дисциплины:
![]() |
![]() |
5.00
из
|
Заказать работу |
Содержание книги
Поиск на нашем сайте
|
|
Замена воздуха водородом, безусловно, эффективна, но само по себе косвенное поверхностное охлаждение даже при повышении давления водорода не позволяет значительно увеличить плотность тока в обмотке статора и поднять мощность машин, т.к. 50-60% перепада температуры возникает на изоляционном обмоточном слое, теплопроводность которого ограничена.
б) Системы непосредственного охлаждения. Наиболее перспективен способ непосредственного - внутреннего охлаждения обмоток, когда газ, вода или масло циркулируют по внутрипроводниковым каналам и, соприкасаясь непосредственно с нагретой медью, отводят от нее теплоту при максимальной эффективности теплопередачи, так как между источником тепла и охлаждающей средой нет никаких барьеров. Эффективность вентиляции повышается при разделении потока охлаждающего агента на несколько параллельных струй.
На рис. 1.16 показана принципиальная схема вентиляции турбогенератора серии ТВВ, имеющего многоструйное радиальное непосредственное охлаждение сердечника статора и обмотки ротора водородом и аксиальное непосредственное охлаждение обмотки статора водой.
![]() |
Рис. 1.16. Многоструйная радиальная система непосредственного охлаждения сердечника статора и обмотки ротора водородом и аксиальная система непосредственного охлаждения обмотки статора водой
Холодный газ после газоохладителей поступает в радиальные каналы сердечника статора, охлаждая активную сталь статора, а затем, пройдя через зазор машины, по косым вентиляционным каналам попадает в обмотку ротора и выходит обратно в зазор с противоположной стороны катушки.
|
Захват водорода из зазора машины и выброс его в зазор осуществляется системой специальных заборных отверстий (заборников), просверленных в пазовых клиньях (Рис. 1.17).
Циркуляция газов в каналах ротора осуществляется за счет напора, создаваемого вращением ротора. Забор и выброс газа секционирован по длине. Зона впуска газа в ротор совпадает с зоной выхода газа из радиальных вентиляционных каналов статора, а зона выпуска газа в зазор - с зоной входа газа в каналы статора.
В лобовых частях проводники обмотки ротора полые.
![]() |
Схема системы газоснабжения генератора представлена на рис. 1.18.
Схема состоит из верхнего коллектора 1, соединенного с водородной рампой 3, нижнего коллектора 2, соединенного с рампой двуокиси углерода (углекислого газа) 4, осушителя 5 и панели управления газовой системой 6 с приемником автоматического газоанализатора 7. К нижней точке кол-лектора двуокиси углерода присоединен указатель жидкости 9 в машине. Частично к газовой схеме относятся бачок продувки 10 и поплавковый гидрозатвор 11.
Для контроля за давлением водорода в генераторе (перед вентилятором) имеются манометры 12 на панели газового управления и у водородной рампы. В схему, входят клапан 13 и регулятор 14, а также блок регулирования газовой смеси 8.
![]() |
Ввод в генератор и вытеснение водорода и воздуха из генератора производятся через верхний коллектор. При низком давлении водорода в генераторе (0,005 МПа) используется автоматическая подпитка при помощи регулятора типа РДВ-12, а при давлении водорода 0,15 МПа и выше обычно применяется ручная подпитка, так как при высоком давлении подпитку требуется производить 1 раз в смену, а то и еще реже. На мощных генераторах для автоматической подпитки применяется вентиль с электромагнитным приводом. Контроль газоплотности генератора обеспечивается манометром МЭД, записывающим давление газа на диаграмму и отмечающим все открытия вентиля.
|
Воздух в генератор подаётся через осушитель, для чего вентиль 15 открывается, а вентиль 16 закрывается. Двуокись углерода вводится в генератор и удаляется из генератора через нижний коллектор. Источником двуокиси углерода могут быть баллоны или централизованная установка двуокиси углерода.
Благодаря высокой теплоёмкости и небольшой вязкости воды наиболее эффективно непосредственное водяное охлаждение. На электрических станциях для охлаждения генераторов обычно используют отработанный конденсат турбин либо дистиллированную воду, которые не только обладают достаточно высокими изолирующими свойствами, но и негорючи.
В турбогенераторах с непосредственным охлаждением обмоток статора и ротора водой подвод охлаждающего конденсата к обмотке статора и его отвод осуществляют со стороны турбины в зоне головок лобовых частей с помощью фторопластовых шлангов, обладающих хорошей механической и электрической прочностью и необходимой эластичностью. Для непосредственного охлаждения обмотки ротора конденсат поступает через центральное отверстие вала машины (со стороны контактных колец), а оттуда по радиальным трубкам направляется в лобовые части обмотки. Схема замкнутой системы охлаждения обмотки статора водой показана на рис. 1.19.
![]() |
Рис. 1.19. Схема питания водой обмотки статора
Непосредственное охлаждение водой обмоток статора и ротора гидрогенераторов также весьма целесообразно, поскольку это позволяет уменьшить расход активных материалов, уменьшить диаметр и повысить предельную мощность гидроагрегата. Вследствие больших габаритов гидрогенераторов удельный расход материалов на 1 кВ А их мощности в среднем в 5 раз выше, чем у турбогенераторов.
|
Обмотка статора и вся система охлаждения заполняются конденсатом с содержанием соли не более 1 мг/л и электрическим сопротивлением не ниже 200 кОм-см. При работе генератора допускается повышение содержания соли до 5 мг/л и снижение электрического сопротивления до 75 кОм-см.
Для циркуляции конденсата по замкнутому контуру в схеме имеются два насоса 17, из которых один находится в работе, а другой в автоматическом резерве. Конденсат к насосам подается из бака 6. Уровень конденсата в этом баке поддерживается поплавковым регулятором 4. При снижении уровня конденсата из-за утечек в системе охлаждения поплавковый регулятор автоматически приоткрывается и за счёт добавления конденсата из магистрали обессоленной воды восстанавливает его прежний уровень в баке.
Благодаря соединению с паровым пространством конденсатора турбины или за счёт работы водяного инжектора в баке поддерживается вакуум. Конденсат, нагревшийся при прохождении по обмотке, попадая на решётку бака, разбрызгивается и под воздействием разрежения интенсивно очищается от воздуха. Выделившийся воздух удаляется через трубу и обратный клапан в конденсатор турбины или через инжектор 1 в циркуляционный водовод.
Давление конденсата в системе охлаждения не должно превышать 0,45 МПа. Поэтому на напорном коллекторе после насосов установлен предохранительный клапан 16, предотвращающий повышение давления конденсата сверх допустимого путем сброса конденсата в бак. Параллельно предохранительному клапану установлен обводной вентиль для ручной регулировки давления.
Из напорного коллектора после насосов конденсат поступает в водоводяные теплообменники 15. В одном из теплообменников он охлаждается конденсатом турбины, а в другом — циркуляционной водой.
Затем конденсат проходит через один из двух фильтров 14, солемер 13, шайбу для измерения расхода 12 и поступает в напорный кольцевой коллектор статора и из него в стержни статора. После прохождения через стержни конденсат собирается в сливной кольцевой коллектор и оттуда, пройдя струйное реле 8, возвращается в расширительный бак.
|
Наличие слива конденсата из обмотки контролируется струйным реле, которое сигнализирует о его прекращении.
Благодаря высоким изолирующим свойствам трансформаторного масла при непосредственном масляном охлаждении обмотки статора возможно использование более дешевой бумажной изоляции. Кроме того, хорошие изоляционные свойства масла облегчают подвод и отвод его из обмотки.
Применение масла для охлаждения обмоток генератора наиболее целесообразно при номинальных напряжения 35 кВ и выше, т.к. при таких напряжениях можно отказаться от повышающих трансформаторов и подключать генераторы не посредственно к шинам РУ повышенного напряжения. При этом уменьшатся токи и соответственно сечение обмотки статора.
В отечественных турбогенераторах типа ТВМ сердечник статора вместе с обмоткой помещен в заполненный маслом стеклотекстолитовый цилиндр, а ротор находится под небольшим вакуумом. Холодное масло из внешней системы поступает в камеру лобовых соединений, а затем попадает в аксиальные каналы сердечника и обмотки статора охлаждая их. Нагретое масло выходит с противоположного конца машины через камеру лобовых соединений и поступает в маслоохладители, откуда вновь насосами возвращается в машину. Обмотка ротора в таких турбогенераторах охлаждается водой.
Однако масляное охлаждение имеет и недостатки: движение масла вследствие его вязкости носит ламинарный характер, что снижает эффективность теплоотдачи с поверхности; для создания требуемой скорости движения масла необходимо большое давление, что сопряжено с дополнительными затратами энергии; масло является горючей средой; по сравнению с водой оно обладает меньшей теплоотводящей способностью.
1.2.2 Назначение, состав и обслуживание систем масляных уплотнений
Система масляных уплотнений предназначена для обеспечения работы генераторов с водородным охлаждением. Турбогенератор с водородным охлаждением полностью герметизирован, кроме выходов вращающегося вала. Вал уплотнен специальными масляными уплотнениями, не выпускающими водород из корпуса генератора. Надо отметить, что уплотнение вала работает в довольно тяжелых условиях: при частоте вращения генератора 3000 об/мин окружная скорость в месте уплотнения достигает 300-400 км/час.
Основной принцип конструкции большинства современных уплотнений вала турбогенератора - разделение водорода и воздуха потоком масла, давление которого несколько превосходит давление водорода.
а) Виды масляных уплотнений. Для предотвращения утечки водорода из корпуса генератора или компенсатора в местах прохода вала ротора через торцевые крышки применяются масляные уплотнения кольцевого или торцевого типа, представленные в разрезе на рис. 1.20 и рис. 1.21 соответственно.
|
Кольцевое уплотнение (рис. 1.20) состоит из вкладыша 2, охватывающего вал 1, и корпуса 3. Масло поступает в зазор между вкладышем и валом и разделяется на две части: в сторону водорода и в сторону воздуха.Масло, идущее в сторону водорода, предотвращает утечку водорода из корпуса машины через зазор между валом и вкладышем.
1 - вал ротора; 2 - вкладыш; 3 - корпус; | 1 - диск на валу ротора; 2 - вкладыш; 3 -пружина; 4 - корпус; 5 - кольцевая канавка |
Рис. 1.20 Кольцевое уплотнение: | Рис. 1.21 Торцевое уплотнение |
Основное достоинство кольцевых уплотнений заключается в том, что при кратковременном прекращении подачи масла они, как правило, не повреждаются. Подплавление их вкладышей, если оно и случается, обычно не вызывает повреждения рабочей поверхности вала. Но из-за большого зазора между вкладышем и валом (0,3÷0,4 мм) расход масла в сторону водорода достигает 40÷60 л/мин. Кроме того, из масла выделяется имеющийся в нем воздух, снижавший чистоту водорода. Это вызывает необходимость наличия вакуумной установки для очистки от воздуха масла, поступающего на уплотнения.
Торцевое уплотнение (рис. 1.21) имеет вкладыш 2, прижимаемый к упорному диску 1 на валу ротора. Как и в кольцевом уплотнении, масло, поступающее в кольцевую канавку на рабочей поверхности вкладыша, делится на две части.
Большая часть направляется в сторону воздуха, обеспечивая смазку трущихся поверхностей, меньшая - в сторону водорода, предотвращая выход водорода через зазор между вкладышем и диском, поскольку давление масла в кольцевой канавке больше давления водорода в статоре на 0,03÷0,09 МПа.
Меньшая часть масла обеспечивает также смазку внутреннего запорного пояска вкладыша. Расход масла в сторону водорода ввиду малого зазора между вкладышем и диском, определяемого только толщиной масляной пленки, невелик (3÷5 л/мин).
Малый зазор и, соответственно, малый расход масла в сторону водорода являются основным преимуществом торцевого уплотнения над кольцевым.
На надежность уплотнений большое влияние оказывает характер изменения усилия, прижимающего вкладыш к диску, в зависимости от снижения давления масла, когда из- за ухудшения смазки резко повышается напряженность работы уплотнения. В зависимости от способа создания усилий, прижимающих вкладыш к диску, а также по количеству автономных камер для масла, торцевые уплотнения разделяются на четыре типа (рис. 1.22).
Рис. 1.22 Торцевые уплотнения
В уплотнениях типа I при аварийном снижении давления масла усилие, прижимающее вкладыш, сохраняется на прежнем высоком уровне, а в уплотнениях типа III оно даже повышается. Характер изменения усилия на вкладыш определяет требования к надежности схемы маслоснабжения и, в частности, допустимую длительность перебоя в снабжении маслом.
По количеству автономных камер для масла уплотнения делятся на однокамерные (однопоточные), и двухкамерные (двухпоточные).
В однопоточном уплотнении вкладыш прижимается к диску пружинами и давлением водорода на его тыльную сторону. Давление уплотняющего масла на прижимающее усилие влияния не оказывает. Камера уплотняющего масла между корпусом и вкладышем уплотняется шнуром из маслостойкой резины.
В двухпоточных уплотнениях вкладыш прижимается к диску не пружинами, а усилием от давления прижимающего масла в первой камере и от давления водорода в генераторе на тыльную сторону вкладыша. Уплотняющее масло поступает на рабочую поверхность вкладыша через вторую камеру. Достоинство двухпоточных уплотнений состоит в возможности регулирования усилия, прижимающего вкладыш к диску, изменением давления прижимающего масла, т.е. без разборки уплотнения.
Наиболее напряженно вкладыши работают при частоте вращения ниже 2000 об/мин и особенно при 400÷500 об/мин. Это требует при остановке и особенно при пуске машины повышенного внимания к работе уплотнений: необходимо следить за температурой, давлением масла и водорода, не допускать перебоя в подаче масла.
б) Особенности схем маслоснабжения уплотнений. В схеме маслоснабжения однопоточных торцевых уплотнений, представленной на рис. 1.23, основным источником масла является инжектор 1, в сопло которого поступает масло из системы регулирования турбины.
Рис. 1.23 Схема маслоснабжения однопоточных торцевых уплотнений
Под действием струи этого масла в инжектор из системы смазки подшипников засасывается более холодное масло, что позволяет получить температуру масла после инжектора на 4÷6°С ниже, чем температура масла в системе регулирования.
Резервными источниками маслоснабжения являются маслонасосы с двигателями переменного 2 и постоянного 3 тока. Нормально оба насоса стоят в резерве, включаясь в работу автоматически. При снижении давления масла в системе первым автоматически включается маслонасос с приводом переменного тока. Если по каким-либо причинам давление масла не восстановится, то с выдержкой времени 0,5÷0,7 с включится маслонасос с двигателем постоянного тока.
На остановленном генераторе, когда давление масла в системе регулирования равно нулю, в работе находится маслонасос переменного тока, а маслонасос постоянного тока - в автоматическом резерве.
Схема маслоснабжения двухпоточных уплотнений отличается от рассмотренной только наличием второго регулятора. Кроме того, отсутствует инжектор, зато установлены три маслонасоса, два из них - с двигателями переменного тока. Для удаления водорода из маслосистемы применяется вентилятор (эксгаустер), который должен работать непрерывно. Его колесо для исключения искрообразования выполняется из латуни.
В соответствии с техническими требованиями, предъявляемыми к работе уплотнений вала генератора [31] ресурс работы вкладыша должен быть таким, чтобы обеспечивалась надёжная работа уплотнений в период от одного планового ремонта до другого.
в) Обслуживание системы маслоснабжения уплотнений вала ТГ. Несмотря на то, турбогенератор находится в заведовании электроцеха, система маслоснабжения уплотнений вала обслуживается эксплуатационным персоналом турбинного цеха в соответствии с местной инструкцией, составляемой для каждого типа генераторов. Однако, в ряде случаев требуются совместные действия ЭЦ и ТЦ. В качестве примера разберём обязанности эксплуатационного персонала ЭЦ при обслуживании системы маслоснабжения уплотнений вала турбогенератора при ее выводе из работы.
Отключение системымаслоснабжения уплотнений вала турбогенератора без слива масла при выводе в плановый ремонт осуществляется в следующей последовательности:
1. Остановить турбоагрегат (осуществляет персонал турбинного цеха).
2. Перевести турбогенератор на воздух (осуществляет персонал электрического цеха после расхолаживания металла паровпуска ЦВД турбины до температуры < 160оС),
3. Отключить валоповоротное устройство, электросхему приводного электродвигателя - «разобрать».
4. Переключатели блокировок МНУ поставить в положение " Отключено ";
5. Вывести из действия технологические защиты по снижению уровня масла в ДБ и по отключению электродвигателей МНУ;
6. Отключить работающий МНУ. Закрыть напорные задвижки на всех МНУ.
7. Перекрыть доступ масла на уплотнения из ДБ.
8. Разобрать электрические схемы двигателей всех МНУ.
9. Отключить эксгаустеры сливного маслопровода и ГМБ.
10. При необходимости снять напряжение с устройств защиты, сигнализации и КИП.
Учитывая известные сложности (ответственные переключения; потери водорода и углекислоты), связанные с переводом турбогенератора на водород (при пуске турбоагрегата) и при переводе генератора с водорода на воздух, отключение системы маслоснабжения уплотнений вала генератора производится только при выводе турбоагрегата в ремонт или при его останове в длительный резерв.
Во всех остальных случаях турбогенератор находится под сниженным давлением водорода и включённой в работу системе маслоснабжения вала турбогенератора.
г) Особенности конструкции и э ксплуатации масляной системы подпятников и подшипников гидрогенераторов. Гидрогенераторы, в большинстве своём вертикальные, поэтому снабжены подпятниками (ПП) и направляющими подшипниками (НП).
На рис. 1.24 представлены две классические компоновки гидроагрегатов.
Рис. 1.24 Компоновки гидрогенераторов
Подпятники воспринимает основную вертикальную нагрузку - вес вращающихся частей гидрогенератора, гидротурбины и усилие осевой реакции воды на лопастях рабочего колеса гидротурбины.
Направляющие подшипники подвержены гораздо меньшим радиальным нагрузкам. Гидрогенератор имеет обычно один или два НП, зачастую второй НП находится в турбине.
Зонтичный гидроагрегат имеет один верхний НП. Второй НП находится в гидротурбине, а ПП расположен под ротором Р гидрогенератора и опирается или на специальную нижнюю крестовину, или на конусообразную опору, поставленную на крышку гидротурбины.
При подвесной компоновке гидроагрегата ПП расположен над ротором Р генератора. Такой генератор обычно имеет отдельный нижний НП и верхний НП, объединенный с ПП.
Вертикальное исполнение вала ГГопределяет ряд специфических требований к эксплуатации подпятников и направляющих подшипников.Они располагаются в масляных ваннах с естественной циркуляцией масла, снабженных водяными маслоохладителями. При эксплуатации периодически, один раз в смену, проверяется уровень масла в ванне, его температура и мутность, за которой можно следить через специальное окно в маслованне.
Мутность масла может быть вызвана вспениванием или попаданием в него воды, например из-за течи в маслоохладителях. Наличие воды в ванне НП и ПП периодически проверяют открыванием крана, расположенного в нижней точке ванны. Оттуда может потечь скопившаяся в ванне вода. Она ухудшает смазывающие свойства масла и, что самое опасное, приводит к коррозии зеркала подпятника и шейки вала. Содержание влаги в масле проверяют не только визуально, но и химическим анализом.
При эксплуатации гидроагрегата наиболее уязвимым элементом является его ПП, состоящий из ступицы ПП, укрепленной на валу гидрогенератора, нижняя часть которой снабжена диском с полированной поверхностью – зеркалом ПП. Вся вертикальная нагрузка передается через зеркало ступицы ПП на сегменты ПП (рис. 1.25).
![]() |
Рис. 1.25 Сегменты подпятника гидрогенератора
Стальной сегмент (рис. 1.26) состоит из тела сегмента 2 и подушки 1, покрытой слоем антифрикционного материала - баббита или фторопласта.
Рис.1.26 Сегмент подпятника
гидрогенератора
Для облегчения пуска у мощных гидроагрегатов иногда предусматривают центральное отверстие в сегменте, из которого под зеркало в момент пуска гидроагрегата подается масло под высоким давлением около 29 МПа (300 кгс/см2), т.н. «клизма». Поступающее масло создает слой между сегментом и зеркалом, обеспечивающий «всплытие» ПП. Тем самым значительно повышается надежность ПП, у которого 90% всех повреждений происходит именно в момент пуска агрегата.
В некоторых конструкциях ПП (рис. 1.26) предусмотрено внутреннее охлаждение сегмента - на рисунке видны трубки, по которым циркулирует вода. Усложнение конструкции сегмента и всего ПП окупается повышением надежности ПП. Дело в том, что сегмент нагревается потерями на трение, возникающими на его верхней поверхности. Это приводит к тому, что верхняя часть сегмента всегда горячее нижней. Такой неравномерный нагрев неизбежно приводит к тепловой деформации сегмента: его центральная часть выпячивается, а края опускаются. Таким образом, центральная часть сегмента оказывается более нагруженной, баббит там перегревается и быстрее изнашивается. Внутреннее охлаждение сегмента предотвращает его выгибание.
Большое значение для надежной эксплуатации ПП имеет равномерное распределение нагрузки ПП на все сегменты. Каждый сегмент С (рис. 1.26) с баббитовым слоем Б, нагруженный зеркалом 3 установлен на винтовой опоре О, стоящей на стуле СТ опоры ПП. Гайкой винтовой опоры регулируется сегмент по высоте для обеспечения равномерной нагрузки всех сегментов.
Нагрузка сегмента контролируется с помощью тензометрии, сократившей трудоемкость балансировки подпятников в 6-7 раз, а их аварийность - в пять раз.
![]() |
Рис. 1.27 Подпятник на регулируемых винтовых опорах подпятника
Жесткость винтовой опоры сегмента ПП является её недостатком, которого лишена конструкция ПП на гидростатической опоре (рис. 1.28), где сегмент опирается на упругий стальной сильфон - сосуд, наполненный маслом.
Сильфоны всех сегментов связаны между собой трубопроводами, обеспечивающими одинаковое давление во всех сильфонах и тем самым - одинаковую нагрузку всех сегментов.
Для контроля теплового режима ПП в каждый сегмент ПП вставлены термометры сопротивления. Они погружены в холодное масло, поступающее в зазор между сегментом, и в горячее масло, выходящее из зазора.
Рис. 1.28 Подпятник на гидравлической опоре
Температура ПП периодически (несколько раз в смену, а также во время пуска и остановки агрегата) проверяют по логометру или автоматически установкой термоконтроля СТК-200, которая может опрашивать с заданной периодичностью до 200 термометров сопротивления и печатать результаты измерений. При недопустимом нагревании установка подает предупредительный и аварийный сигналы.
При наличии местных потертостей шабрится баббитовый слой. При большом износе баббитового слоя производится замена и новая балансировка всех сегментов ПП на жестких опорах, однако ПП на гидравлических опорах в ней не нуждается. Опытная эксплуатация ПП с антифрикционным покрытием из фторопласта показала значительно большую их долговечность и износостойкость по сравнению с баббитовым покрытием.
|
|
Индивидуальные очистные сооружения: К классу индивидуальных очистных сооружений относят сооружения, пропускная способность которых...
История создания датчика движения: Первый прибор для обнаружения движения был изобретен немецким физиком Генрихом Герцем...
Биохимия спиртового брожения: Основу технологии получения пива составляет спиртовое брожение, - при котором сахар превращается...
Кормораздатчик мобильный электрифицированный: схема и процесс работы устройства...
© cyberpedia.su 2017-2024 - Не является автором материалов. Исключительное право сохранено за автором текста.
Если вы не хотите, чтобы данный материал был у нас на сайте, перейдите по ссылке: Нарушение авторских прав. Мы поможем в написании вашей работы!