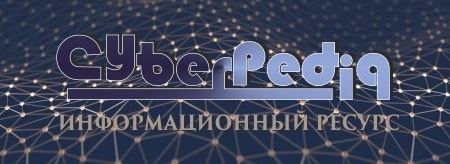
Состав сооружений: решетки и песколовки: Решетки – это первое устройство в схеме очистных сооружений. Они представляют...
Археология об основании Рима: Новые раскопки проясняют и такой острый дискуссионный вопрос, как дата самого возникновения Рима...
Топ:
Комплексной системы оценки состояния охраны труда на производственном объекте (КСОТ-П): Цели и задачи Комплексной системы оценки состояния охраны труда и определению факторов рисков по охране труда...
Техника безопасности при работе на пароконвектомате: К обслуживанию пароконвектомата допускаются лица, прошедшие технический минимум по эксплуатации оборудования...
Эволюция кровеносной системы позвоночных животных: Биологическая эволюция – необратимый процесс исторического развития живой природы...
Интересное:
Национальное богатство страны и его составляющие: для оценки элементов национального богатства используются...
Аура как энергетическое поле: многослойную ауру человека можно представить себе подобным...
Наиболее распространенные виды рака: Раковая опухоль — это самостоятельное новообразование, которое может возникнуть и от повышенного давления...
Дисциплины:
![]() |
![]() |
5.00
из
|
Заказать работу |
|
|
Условия эксплуатации вагонов на перспективу будут характеризоваться возрастанием веса грузовых поездов до 10—12 тыс. тс при длине состава 1200—1300 м, увеличением числа вагонов с весом брутто до 176 тс, повышением эффективности тормозов в поезде, увеличением средних скоростей соударения вагонов и т. п. Для нормальной работы в таких условиях эксплуатации автосцепное оборудование вагонов должно обладать соответствующей прочностью, повышенной энергоемкостью, необходимой поглощающей способностью и оптимальной формой силовой характеристики.
С целью повышения прочности автосцепного оборудования промышленность переходит на изготовление основных его деталей (корпуса автосцепки, тягового хомута, элементов механизма сцепления, упоров и т. д.) из сталей повышенной прочности, в частности легированных ванадием и марганцем. Механические свойства этих сталей существенно выше соответствующих свойств сталей, применяемых в настоящее время для изготовления тех же деталей автосцепного устройства. Продолжаются изыскания и других еще более прочных сталей и способов изготовления основных и наиболее ответственных деталей автосцепного оборудования.
Одновременно с применением легированных сталей для производства деталей автосцепного устройства идут конструкторские проработки усиления его элементов и узлов. Так, в последние годы введены в производство усиленные передний и задний упоры, тяговый хомут и корпус автосцепки. Автосцепка усилена введением четырех ребер в хвостовике, увеличением сечения стенки, изменением конструкции ребер большого зуба и т. д. Все это (наряду с применением низколегированной стали дало возможность увеличить разрывное усилие автосцепки. С целью повышения качества автосцепных устройств в целом и его узлов и "деталей в отдельности в промышленности постоянно совершенствуется технология их производства. Это достигается комплексной механизацией и автоматизацией процессов изготовления деталей и узлов автосцепного устройства.
|
Совершенствование поглощающих аппаратов автосцепных устройств направлено на улучшение их энергетических параметров и в первую очередь энергоемкости. При существующих схемах пружинно-фрикционных поглощающих аппаратов повышения их энергоемкости можно достичь оптимизацией параметров жесткости и трения. С этой целью изыскивают возможности усиления пружин поглощающих аппаратов в существующих габаритных
169
размерах и повышения коэффициента трения между деталями фрикционного узла аппарата.
Для существующих условий эксплуатации возможно создание фрикционно-пневматических поглощающих аппаратов, в которых в качестве упругого элемента будет использован пневмоцилиндр с внутренним давлением, соответствующим силе предварительной затяжки с учетом трения во фрикционной части, равной 25— 50 тс. Такой аппарат имеет ход 120 мм и может обеспечить соударение четырехосных груженых вагонов со скоростями 10—12 км/ч при ускорениях соответственно 2 g — 3 g и усилиях, не превышающих 200 тс.
Для повышения энергоемкости резинометаллических поглощающих аппаратов необходимо изыскивать наиболее приемлемые марки резин, имеющие лучшие параметры упругости и внутреннего трения. Одним из средств повышения энергоемкости автосцепных устройств восьмиосных вагонов является применение сдвоенных поглощающих аппаратов типовой конструкции. Исследования, выполненные во ВНИИВ, показали, что восьмиосные груженые вагоны, оборудованные автосцепными устройствами со сдвоенными аппаратами Ш-1-Тм или Р-4П, обеспечивают возможность соударения их со скоростями до 7 км/ч. При этом усилие не превышает 200 тс. Если использованы сдвоенные аппараты Ш-2-Т, а также сочетания аппаратов Ш-2-Т и Р-4П, то допустима скорость соударения 7,5 км/ч. Исследования показали, что аппараты Ш-2-Т могут быть рекомендованы для оборудования как четырехосных (в одинарном варианте), так и восьмиосных (в сдвоенном варианте) вагонов. Такая унификация поглощающих аппаратов будет иметь очевидные преимущества как в эксплуатации, так и в производстве.
|
Одно из основных требований, предъявляемых к перспективному поглощающему аппарату, — ограничение силы, возникающей при его полном сжатии, величиной, не превышающей 250 тс. При этом от поглощающих аппаратов четырехосных грузовых вагонов требуется энергоемкость не менее 10 тс-м, а от аппаратов восьмиосных вагонов — не менее 16 тс-м. Для реализации указанных значений энергоемкости рекомендуются следующие значения ходов: для четырехосных вагонов 100—120 мм, для восьмиосных 160—200 мм. Коэффициент необратимого поглощения энергии должен составлять не менее 0,6. Сила закрытия аппарата при медленном нарастании нагрузки должна быть не менее 100 тс.
Исключительно высокие требования к энергоемкости поглощающих аппаратов при значительном ограничении предельных величин ходов и усилий могут быть реализованы в аппаратах, существенно отличающихся по конструкции от ныне применяемых. Наиболее приемлемой в отношении получения требуемых значений энергетических параметров и формы силовой характеристики в перспективе следует считать конструкцию гидравли-
170
ческих, гидрогазовых и других комбинированных аппаратов. Прототипом гидрогазовых аппаратов для перспективных условий эксплуатации могут служить опытные аппараты ГА-100М и ГА-500, которые в настоящее время проходят эксплуатационную проверку.
Для вагонов специального назначения, в которых транспортируют особо хрупкие и ценные грузы, нуждающиеся в надежной защите от ударов, целесообразно применение автосцепных устройств со специальными средствами ударозащиты и поглощения энергии. В этих устройствах, выполненных по принципу так называемой плавающей хребтовой балки, сочетается конструкция сквозной упряжи с гидропневматическим аппаратом. В таком автосцепном устройстве могут быть реализованы исключительно большие значения рабочих ходов, при которых достигается существенное снижение усилий и ускорений, развиваемых при соударении вагонов.
|
На перспективу намечено создание автосцепного устройства, обеспечивающего одновременное автоматическое соединение воздушных и электрических магистралей поезда. В таком автосцепном устройстве применяется жесткая автосцепка. Для автоматического соединения пневматических и электрических магистралей на корпусе автосцепки должны быть размещены соответствующие кронштейны с пневматическими патрубками и электрическими соединениями. Прототипом может служить автосцепка «Интермат», которая допускает одновременно автоматическое сцепление двух воздушных и одной электрической магистрали, состоящей из семи проводов. Она взаимосцепляема с автосцепкой СА-3 и может быть использована в сочетании с остальными узлами и деталями стандартного и модернизированного автосцепных устройств.
Одним из направлений развития автосцепного оборудования на перспективу может служить создание автосцепного устройства грузовых вагонов, допускающего их опрокидывание на роторных вагоноопрокидывателях без расцепления. Условием создания и внедрения такого автосцепного устройства будет служить применение роторных вагоноопрокидывателей, у которых ось вращения совпадает с продольной осью автосцепки. В автосцепном устройстве такого назначения должен быть применен узел связи автосцепки с тяговым хомутом, обеспечивающий ее полный или частичный поворот вокруг продольной оси соответственно углу поворота вагоноопрокидывателя.
Необходима дальнейшая отработка резинометаллических поглощающих аппаратов и разработка средств уменьшения шума в пассажирских вагонах от автосцепного устройства.
171
Глава VI ГРУЗОВЫЕ ВАГОНЫ
ОСНОВНЫЕ ТРЕБОВАНИЯ К ГРУЗОВЫМ ВАГОНАМ
Новые конструкции грузовых вагонов независимо от их назначения необходимо создавать с учетом как современных, так и перспективных требований эксплуатации, и обеспечивать при этом безопасность движения, прочность и надежность. Кроме того, должны быть обеспечены максимальные удобства и наименьшие затраты при изготовлении, обслуживании и ремонте в эксплуатации, а также предусмотрена возможность модернизации. Особое внимание при проектировании следует обращать на обеспечение техники безопасности обслуживающего персонала. Все вагоны должны иметь поручни для сцепщика, подножки и поручни для составителей поездов, установленные с каждой стороны вагона, а также кронштейны для сигнального хвостового фонаря и т. д. Необходимо предусматривать максимальное снижение веса тары вагонов, экономное расходование металла и других материалов, а также обеспечение технологичности конструкций. Применяемые металлы и лакокрасочные покрытия должны увеличивать стойкость элементов вагона против коррозии. Конструкция вагона : должна обеспечивать неповреждаемость и сохранность перевозимых грузов при их транспортировании и маневровых работах.
|
Необходима максимальная унификация узлов и деталей вагонов. Они должны отвечать требованиям действующих ГОСТ, ОСТ, унифицированных чертежей, а также правилам технической эксплуатации соответствующих железных дорог. Вагоны должны быть максимально приспособлены для комплексной механизации -погрузочно-разгрузочных работ, а их конструкция — позволять рационально использовать существующие и разрабатываемые -на перспективу на транспорте и промышленных предприятиях погрузочно-разгрузочные средства. Для универсальных вагонов ' потери груза и применение тяжелого ручного труда при погру- -* зочно-разгрузочных работах должны быть сведены к минимуму,; а для специализированных — практически отсутствовать.
Грузовые вагоны должны иметь мощную несущую металлоконструкцию рамы, обеспечивающую безотказную эксплуатацию на сортировочных горках и в тяжеловесных поездах, а также прочную и по возможности простую конструкцию кузова и элементов оборудования.
172
Кроме этих основных требований для всех грузовых вагонов, к конкретным вагонам дополнительно предъявляют специфические требования, связанные с особенностями перевозимых в них грузов и эксплуатационных условий. При выборе параметров и разработке новых конструкций грузовых вагонов для обеспечения повышения провозной способности железных дорог необходимо предусматривать следующее.
1. Максимальное использование допускаемой для грузового вагона погонной нагрузки на 1 м пути, что позволяет увеличить вес поезда, не изменяя его длины. Одновременно следует максимально использовать допускаемую нагрузку от оси на рельс.
2. Повышение коэффициента использования номинальной грузоподъемности вагонов, для чего удельные объемы и площади их должны соответствовать структуре и параметрам перевозимых грузов. При этом необходимо максимально использовать габаритные возможности подвижного состава, чтобы повышение удельных объемов не приводило к увеличению длины вагона и снижению погонной нагрузки на путь.
|
В СССР для магистрального и промышленного транспорта производят грузовые вагоны более 100 типов. В основном это вагоны колеи 1520 (1524) мм, а также вагоны для Южно-Сахалинского отделения Дальневосточной ж. д. колеи 1067 мм, для узкоколейных дорог — колеи 750 мм и др.
Вагоны имеют современные ходовые части, тормозное и автосцепное оборудование. Несущую конструкцию кузовов вагонов в основном изготовляют из низколегированных сталей повышенной прочности.
ПЛАТФОРМЫ
Платформы служат для перевозки длинномерных, штучных, лесных и сыпучих грузов, контейнеров и оборудования, не требующего защиты от атмосферных осадков. Платформы могут быть универсальными, рассчитанными на большую номенклатуру перевозимых грузов, и специальными — предназначенными для перевозки определенных грузов.
Универсальная четырехосная платформа грузоподъемностью 63 тс (мод. 13-401) показана на рис. 59. Кроме распределенной по всей площади платформы нагрузки 63 тс, платформа допускает перевозку груза 45 тс, сосредоточенного в середине на длине 3 м, и груза 60 тс, сосредоточенного в середине на длине 4,3 м с опорой на боковые балки. Платформа имеет мощную стальную сварную раму с деревянным настилом пола и стальные боковые и торцовые борта. Рама состоит из хребтовой балки (два двутавра № 60), двух боковых (двутавр № 60), двух концевых, двух шкворневых и двух основных поперечных балок, а также дополнительных поперечных и продольных балок, поддерживающих настил пола и служащих для установки тормозного оборудования. По концам рамы между концевыми и шкворневыми балками ставят раскосы,
173
Рис. 59. Универсальная четырехосная платформа
более равномерно распределяющие продольные силы от автосцепки между хребтовой и боковыми балками.
На боковых балках устанавливают скобы стоек для перевозки леса, державки петель боковых бортов с запирающимися устройствами и увязочные кольца. На концевых балках имеются кронштейны и державки петель торцовых бортов, скобы стоек, поручни для составителя, розетки автосцепки и кронштейны рычага автосцепки и сигнального фонаря. Продольные борта высотой 500 мм и торцовые борта высотой 400 мм изготовляют из специальных гнутых профилей, подвешивают на петлях и удерживают в закрытом положении запирающими клиньями. Грузы можно перевозить при закрытых и открытых бортах. Настил пола, выполненный из досок толщиною 55 мм, по периметру через стальную армировку болтами прикреплен к балкам рамы. Платформа имеет габарит 01-Т, вес тары 20,9 тс, погрузочную площадь пола 36,8 м2 и длину по осям автосцепок 14 620 мм.
Учитывая высокую эффективность контейнерных перевозок, ВНИИВ и ДВЗ разработали специальные четырехосные платформы
174 |
грузоподъемностью 60 тс для перевозки типовых большегрузных контейнеров весом брутто 10, 20 и 30 тс. Были разработаны и испытаны платформы двух вариантов: I — «широкая» платформа, при необходимости допускающая возможность оборудования деревянным настилом пола и устройствами для крепления колесной техники; II — «узкая» платформа (модель 13-470), не приспособленная для настила пола и более легкая; она предназначена только для перевозки большегрузных контейнеров (рис. 60). По конструкции платформы обоих вариантов различаются мало. Сварная рама платформы имеет хребтовую балку из двух двутавров № 60, сверху перекрытых по всей длине листами 400X12 мм, а снизу в середине на длине 7м — полосами 150Х X 14 мм; две боковые балки из двутавров № 60; две^ концевые балки из штампованного уголкового профиля толщиной 10 мм и верхних листов 250 X 12 мм; две шкворневые балки, сваренные из двух вертикальных листов 10 мм и двух горизонтальных (верхнего и нижнего) 480X12 мм; три средние поперечные балки замкнутого сечения и две поперечные балки, расположенные над внутренними колесами тележки. Между концевыми и шкворневыми балками имеются раскосы из двутавра № 10. Для поддержки пола, в случае его настила (вариант I) и крепления тормозного оборудования имеются дополнительные продольные и поперечные балки. Платформы оборудованы устройствами для установки и надежного крепления (от продольных и боковых перемещений) типовых большегрузных контейнеров.
|
|
Организация стока поверхностных вод: Наибольшее количество влаги на земном шаре испаряется с поверхности морей и океанов (88‰)...
Двойное оплодотворение у цветковых растений: Оплодотворение - это процесс слияния мужской и женской половых клеток с образованием зиготы...
Наброски и зарисовки растений, плодов, цветов: Освоить конструктивное построение структуры дерева через зарисовки отдельных деревьев, группы деревьев...
Эмиссия газов от очистных сооружений канализации: В последние годы внимание мирового сообщества сосредоточено на экологических проблемах...
© cyberpedia.su 2017-2024 - Не является автором материалов. Исключительное право сохранено за автором текста.
Если вы не хотите, чтобы данный материал был у нас на сайте, перейдите по ссылке: Нарушение авторских прав. Мы поможем в написании вашей работы!