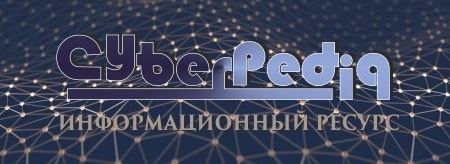
Автоматическое растормаживание колес: Тормозные устройства колес предназначены для уменьшения длины пробега и улучшения маневрирования ВС при...
Типы сооружений для обработки осадков: Септиками называются сооружения, в которых одновременно происходят осветление сточной жидкости...
Топ:
Эволюция кровеносной системы позвоночных животных: Биологическая эволюция – необратимый процесс исторического развития живой природы...
Марксистская теория происхождения государства: По мнению Маркса и Энгельса, в основе развития общества, происходящих в нем изменений лежит...
Выпускная квалификационная работа: Основная часть ВКР, как правило, состоит из двух-трех глав, каждая из которых, в свою очередь...
Интересное:
Аура как энергетическое поле: многослойную ауру человека можно представить себе подобным...
Финансовый рынок и его значение в управлении денежными потоками на современном этапе: любому предприятию для расширения производства и увеличения прибыли нужны...
Что нужно делать при лейкемии: Прежде всего, необходимо выяснить, не страдаете ли вы каким-либо душевным недугом...
Дисциплины:
![]() |
![]() |
5.00
из
|
Заказать работу |
|
|
Методы получения заготовок и припуски
Литые заготовки
Основой крупных и уникальных машин являются моноблочные детали сложной формы с большими габаритными размерами и массовыми характеристиками. В процессе эксплуатации такие детали воспринимают нагрузки в тысячи тонн.
На предприятиях тяжелого машиностроения выпуск отливок массой свыше 5000 кг достигает 45 % от общего выпуска литых заготовок. Получившие наибольшее распространение стальные и чугунные заготовки изготовляют литьем в песчаные и металлические формы, центробежным литьем и реже литьем по выплавляемым моделям. Качество отливок регламентируется ГОСТ 26645-85 и ГОСТ 25347-82.
Для единичного производства ручная формовка по деревянным и газифицируемым моделям часто остается единственным способом получения отливок. Она характеризуется высокой трудоемкостью, значительными припусками, низкими точностью получаемых размеров и качеством поверхностей отливок вследствие неоднородности набивки форм.
При машинной формовке чаще всего удается механизировать землеподачу, уплотнение формовочной смеси в опоке и извлечение моделей из формы. Это позволяет повысить производительность процесса и качество отливок, точность их размеров и улучшить условия труда рабочих. В качестве технологического оснащения заготовительных цехов используют крупные пескометы, встряхивающие столы, тяжелые формовочные машины, формы массой до 10 т.
Способ центробежного литья применяют главным образом для производства заготовок типа тел вращения (втулок, венцов зубчатых колес, гаек винтов нажимных устройств и т. п.) с диаметральными размерами до 2000 мм и массой до 3 т. При этом получают более тонкостенные отливки, в том числе из сплавов с низкой жидкотекучестью; достигают более жестких допусков на размеры, большей плотности и повышенных физико-механических свойств заготовок по сравнению с литьем в песчаные формы.
|
В силу особенностей единичного производства литье в металлические формы применяют сравнительно редко. Этим способом изготовляют заготовки поддонов для изложниц, надставок, крупных шкивов, не имеющие выступающих частей. В противном случае при усадке в отливке появляются трещины.
Припуски на обработку, допуски размеров, формы и расположения, неровности поверхности, допуски массы на отливки из черных и цветных металлов и сплавов регламентируют по ГОСТ 26645—85. Вместе с тем некоторые предприятия разрабатывают и используют нормативные материалы, учитывающие особенности изготовляемой ими продукции. Так, для крупных деталей рекомендуют увеличивать припуски на 5...8 мм в случае, если они подвергаются старению после черновой обработки. Уменьшения припусков добиваются путем правильного построения маршрута механической обработки заготовки и совершенствования технологии литья. В ряде случаев удается перейти от изготовления стальных отливок и поковок к производству отливок из высокопрочного чугуна с шаровидным графитом, имеющего временное сопротивление до 686 МПа, предел текучести до 441 МПа и относительное удлинение после отжига 10 %. Из высокопрочного чугуна отливают траверсы и подушки рабочих клетей, плиты окалиноломателей блюминга, коленчатые валы, станины молотов, зубчатые венцы и другие детали массой до 15 т. Это позволяет получать отливки на 20...25 % дешевле стальных отливок и в 3—4 раза дешевле поковок.
Поковки
Наиболее тяжело нагруженные, ответственные, а также труднодемонтируемые для ремонта детали изготовляют из заготовок, получаемых методами горячего пластического деформирования металла. Для таких деталей используют углеродистые и легированные стали с временным сопротивлением до 980 МПа.
|
Основным методом получения поковок в условиях единичного производства является свободная ковка. Форма таких заготовок должна быть симметричной, образованной простыми геометрическими фигурами с плавными переходами. Их поверхность имеет значительные дефекты в виде местных вмятин, следов ковочных ударов, неравномерных слоев окалины. После нескольких нагревов толщина дефектного слоя достигает 7 мм и более. Поэтому форма заготовки может значительно отличаться от формы детали, а припуск для заготовок, полученных свободной ковкой, определяется отклонениями, возникающими в процессе их формообразования.
При разработке маршрута термообработку поковок рекомендуется проводить до начала черновых операций механической обработки, что способствует снижению припуска и цикла их изготовления.
Приведенные рекомендации следует учитывать особенно при производстве колонн прессов, коленчатых валов мощных машин, крупных роторов генераторов и т. п. Экономическая целесообразность замены заготовок, полученных свободной ковкой, на штампованные заготовки все больше склоняется в пользу последних. Это характерно при изготовлении сложных или небольших повторяющихся партий заготовок.
Сварные (комбинированные) заготовки
Технологические припуски на сварные и комбинированные заготовки устанавливают в зависимости от наибольшего размера обрабатываемой поверхности и размера между технологической базой и поверхностью, подлежащей обработке (рис. 4.1, а). Под наибольшим размером А условно принимают большую сторону прямоугольника, описывающего общий контур обрабатываемой поверхности. Припуск В на обработку поверхностей, расположенных в одной плоскости, но на различном расстоянии от технологической базы, должен быть одинаковым. Под наибольшими размерами Н 1 и Н 2 между обрабатываемыми плоскостями понимают максимальное расстояние между обрабатываемыми элементами сварной заготовки, включая их длины. Учитывают также наибольшее расстояние от технологической базы до обрабатываемой поверхности.
Рис. 4.1. Припуски на плоские (а) и цилиндрические (6) поверхности сварных конструкций
После обработки плоских элементов металлоконструкций их толщина не должна быть меньше 3 мм. Значения припусков для них приведены в табл. 4.1.
|
Для цилиндрических поверхностей припуск В назначают в зависимости от их радиуса R (рис. 4.1, б). В качестве определяющих параметров используют наибольшую длину образующей Б или расстояние Н между технологической базой и центром цилиндрической поверхности. Припуски на обработку цилиндрических поверхностей приведены в табл. 4.2.
Таблица 4.1
Припуск В на обработку плоских поверхностей, мм
H 1; H 2 | B при А, равном | |||||||
100 | 250 | 500 | 1000 | 2000 | 3000 | 4000 | 5000 | |
50 250 500 1000 2500 5000 10000 15000 | 4 5 5 5 6 10 12 15 | 5 5 5 5 8 10 15 15 | 5 5 8 10 10 15 15 15 | 5 8 10 10 15 15 18 18 | 10 10 12 15 15 15 20 20 | 10 12 15 15 15 18 22 22 | 12 15 15 15 18 20 22 22 | 15 15 15 15 18 20 22 22 |
Таблица 4.2
Припуск В на обработку цилиндрических поверхностей, мм
H 1; H 2 | B при А, равном | |||||||
100 | 250 | 500 | 1000 | 2000 | 3000 | 4000 | 5000 | |
100 250 500 1000 2000 3000 4000 5000 | 5 6 8 10 12 12 12 15 | 6 8 10 12 12 12 15 15 | 8 10 12 15 15 15 18 18 | 10 12 15 15 18 18 20 20 | 12 12 15 18 18 20 20 20 | 12 12 15 18 20 20 22 22 | 12 15 18 20 20 22 22 22 | 15 15 18 20 22 22 22 22 |
С учетом правки заготовок значения припусков можно снизить на 30 %. Если конструкции изготовлены из средне- и высокоуглеродистых сталей, то приведенные в табл. 4.1, 4.2 значения припусков следует увеличить на 30 %.
При изготовлении деталей по разовым заказам допускается увеличивать табличные значения припусков на 15 %, но не более чем на 3 мм.
Разметка заготовок
Специфичными и трудоемкими в условиях единичного производства являются разметочные операции. Их применяют для нанесения установочных базовых рисок, необходимых для дальнейшей механической обработки, границ снятия припуска и границ обработки; правильного распределения припуска на обработку; контроля геометрических форм и размеров заготовок и деталей. Разметочная операция связана с процессом вычерчивания на поверхностях заготовки различных геометрических элементов, заданных на рабочем чертеже. Плоскостную или пространственную разметку применяют в соответствии с характером размечаемой поверхности.
Построение того или иного геометрического элемента связано с необходимостью задания вычерчивающему инструменту строго определенной траектории движения, которая, в свою очередь, определяется характером кинематических связей между применяемыми для разметки инструментами, обусловливающими их взаимные перемещения.
|
В случае разметки прямой линии специальной чертилкой последней необходимо обеспечить прямолинейное движение, для чего
используют кинематическую связь, представленную в виде простейшей поступательной пары, у которой одним соединяемым звеном является линейка 1, а другим — чертилка 3 (рис. 4.2). Линейка неподвижно связана с размечаемой поверхностью 4, чертилку перемещают по направляющим поверхностям 2 и 3.
Рис. 4.2. Плоскостная разметка прямой линии
С помощью пространственных кинематических связей, реализуемых с помощью соответствующих разметочных инструментов и приспособлений, осуществляют пространственную разметку. В связи с необходимостью разметки деталей самых разнообразных конфигураций и размеров используют большое число универсальных и специальных разметочных инструментов: универсальные и плоские чертилки, кернеры, рейсмусы, центроиска- тели, штангенциркули и т. п. Эффективным путем уменьшения трудоемкости разметочных операций является развитие методов разметки по шаблонам.
Все разметочные работы предусматривают использование контрольно-измерительных инструментов и приспособлений универсального и специального назначения. Линейные размеры контролируют стальными линейками, рулетками и наборами плиток концевых мер, угловые — угольниками и угломерами.
Важным вопросом при проектировании операции разметки является выбор баз. Необходимо определить какими поверхностями заготовку следует устанавливать на разметочную плиту и от каких базироваться при разметке. Назначенные базовые поверхности заносят в операционные разметочные карты. Для случая плоскостной разметки рекомендуется следующий порядок выполнения приемов работы. Сначала выбирают разметочные технологические базы. Ими могут быть ребра заготовок, кромки листов, различные риски. Приоритет здесь следует отдавать точно обработанным поверхностям. Далее проводят риски, параллельные базовым поверхностям, перпендикулярные им и наклонные, а затем окружности, дуги и лекальные кривые.
При последовательном выполнении ряда графических построений происходит накопление погрешности разметки, поэтому разметка дорогостоящих сложноконтурных деталей требует выполнения каждого элементарного построения с максимальной точностью.
|
|
Автоматическое растормаживание колес: Тормозные устройства колес предназначены для уменьшения длины пробега и улучшения маневрирования ВС при...
Архитектура электронного правительства: Единая архитектура – это методологический подход при создании системы управления государства, который строится...
История развития хранилищ для нефти: Первые склады нефти появились в XVII веке. Они представляли собой землянные ямы-амбара глубиной 4…5 м...
История создания датчика движения: Первый прибор для обнаружения движения был изобретен немецким физиком Генрихом Герцем...
© cyberpedia.su 2017-2024 - Не является автором материалов. Исключительное право сохранено за автором текста.
Если вы не хотите, чтобы данный материал был у нас на сайте, перейдите по ссылке: Нарушение авторских прав. Мы поможем в написании вашей работы!