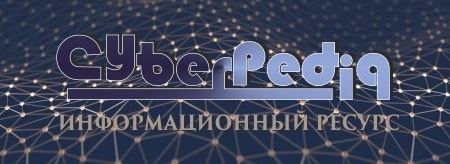
Поперечные профили набережных и береговой полосы: На городских территориях берегоукрепление проектируют с учетом технических и экономических требований, но особое значение придают эстетическим...
Архитектура электронного правительства: Единая архитектура – это методологический подход при создании системы управления государства, который строится...
Топ:
Марксистская теория происхождения государства: По мнению Маркса и Энгельса, в основе развития общества, происходящих в нем изменений лежит...
Характеристика АТП и сварочно-жестяницкого участка: Транспорт в настоящее время является одной из важнейших отраслей народного хозяйства...
Проблема типологии научных революций: Глобальные научные революции и типы научной рациональности...
Интересное:
Национальное богатство страны и его составляющие: для оценки элементов национального богатства используются...
Наиболее распространенные виды рака: Раковая опухоль — это самостоятельное новообразование, которое может возникнуть и от повышенного давления...
Лечение прогрессирующих форм рака: Одним из наиболее важных достижений экспериментальной химиотерапии опухолей, начатой в 60-х и реализованной в 70-х годах, является...
Дисциплины:
![]() |
![]() |
5.00
из
|
Заказать работу |
|
|
Для высокоточных деталей проблема обеспечения надежности играет особую роль. Это относится и к высокоточным валам, работающим с высокими частотами вращения. Превышение допустимых значений отклонения формы и расположения поверхностей ведет к появлению вибрации, повышенному изнашиванию, что в экстремальных условиях может явиться причиной аварии. Обеспечение надежности высокоточных валов является задачей, решение которой связано с преодолением существенных технологических трудностей. Важно не только получить необходимые свойства изделия, но и сохранить их в течение длительного срока эксплуатации. Поскольку показатели качества машин обеспечиваются в процессе их изготовления, то ТП должен быть надежным, т. е. не допускать отклонения таких параметров, которые могут влиять на качество выпускаемой продукции. Исследования путей повышения точности формы и расположения поверхностей в прошлом ограничивали рамками отдельных операций. Такой подход неприемлем, особенно для высокоточных деталей. Нужно рассматривать все операции не изолированно, а во взаимосвязи, ибо конечные характеристики обработанных деталей формируются под действием всего комплекса выполняемых операций. В условиях современного производства можно обеспечить размерную точность до 0,001 мм, отклонения формы до 0,005 мм, шероховатость поверхности Ra = 0,04...0,08 мкм. Однако в течение долгого времени это удавалось получить только доводкой. Такое положение было вызвано тем, что существуют причины возникновения погрешностей при обработке высокоточных поверхностей деталей. Особенно ярко наследственные связи проявляются при обработке внутренних и наружных поверхностей вращения прецизионных деталей типа валов, гильз и т. п. Высокие требования по точности и шероховатости, предъявляемые к ответственным поверхностям прецизионных валов, предопределяют ряд особенностей технологии их изготовления. Это касается метода подготовки технологических баз для операции финишной обработки, метода выполнения финишной обработки подшипниковых шеек, характера упрочнения и стабилизации структуры материала валов, способа контроля размеров и взаимного расположения ответственных поверхностей валов.
|
Шейки валов в основном обрабатывают при базировании на неподвижных упорных центрах станка, которые обеспечивают наивысшие жесткость и точность обработки. При этом поверхности центрового отверстия и упорного центра можно рассматривать как подшипники скольжения, испытывающие нагрузку от радиальной составляющей силы резания при шлифовании. Для получения точных по форме подшипниковых шеек необходима тщательная подготовка упорных центров станка и центровых отверстий или опорных фасок вала.
Опорные поверхности упорных центров станка должны иметь точную форму по параметру отклонения от круглости и конусности. При вращении шпинделя на точных по форме упорных центрах точки контакта центровых отверстий с поверхностью упорных центров остаются неизменными, ось вращения и геометрическая ось вала также не меняют своих положений. Тем самым создается возможность получения высокой круглости шеек шпинделя.
Если при изготовлении деталей обычной точности технологические базы рассматривают как геометрически правильные элементы, то в случае обработки высокоточных деталей такое допущение ошибочно. Влияние погрешности формы поверхностей центровых отверстий на отклонение формы обработанных поверхностей высокоточных деталей оказывается весьма значимым. Установлено, что центровые отверстия в поперечном сечении имеют несколько выступов (волн), так что при обработке вала в центрах эти неровности, контактируя с жестким центром, вызывают перемещение детали относительно режущего инструмента в радиальном и осевом направлениях. Погрешность технологических баз наследуется, т. е. переносится на обработанную поверхность детали. Полученное при этом отклонение формы зависит от числа волн на центровом отверстии, их высоты и силы резания.
|
Для выполнения точных по форме центровых отверстий необходима тщательная подготовка. Высокая точность формы центровых отверстий и базовых фасок вала возможна при их обработке на станках для шлифования центровых отверстий. Применяют несколько типов станков для такого шлифования, различающихся схемой обработки и схемой базирования.
К первому типу относят станки, у которых шлифовальный круг имеет форму конуса с углом 60°, вершина инструмента при обработке центрового отверстия охватывает всю коническую поверхность, а обрабатываемая деталь при этом неподвижна (рис. 4.16, а). Существенным недостатком этой схемы обработки является отсутствие возможности свободного выхода шлама, что приводит к быстрому засаливанию шлифовального круга, перегреву заготовки, прижогам, снижению производительности. Эту схему обработки используют в основном перед операциями чистового точения и предварительного шлифования.
Ко второму типу относятся станки, у которых шлифовальный круг касается обрабатываемой поверхности по образующей конуса, а обработка всей поверхности центрового отверстия осуществляется при вращении обрабатываемой детали вокруг собственной геометрической оси (рис. 4.16, б). Для улучшения качества обработки шлифовальный круг получает осциллирующее движение вдоль обрабатываемого отверстия.
Рис. 4.16. Схемы обработки базовых поверхностей
Недостатком этой схемы обработки является передача погрешности с базовой (наружной) поверхности на обрабатываемую. В итоге приходится многократно повторять цикл обработки, постепенно уменьшая остаточную погрешность формы, что резко снижает производительность.
К третьему типу относятся станки, у которых шлифовальный круг совершает три вида движения: вокруг собственной оси, планетарное вокруг оси обрабатываемого отверстия и осциллирующее вдоль образующей обрабатываемого отверстия (рис. 4.16, в). Деталь при этом способе обработки, как правило, неподвижна.
|
К четвертому типу относятся станки, у которых шлифование центровых поясов осуществляется кругом, имеющим прямой профиль (рис. 4.16, г). Деталь при этом базируется по наружной поверхности в призмах. Скорость резания у различных точек по дайне образующего круга одинакова. Эта схема обеспечивает наиболее высокую точность обработки. Передача вращения на деталь осуществляется посредством компенсирующих устройств (сильфона, муфты и др.), благодаря чему отсутствует передача погрешностей вращения привода на деталь. Профиль круга позволяет обрабатывать не только конические, но также плоские торцевые и цилиндрические поверхности.
В производственной практике используют призмы различных типов, отличающиеся формой, расположением и подвижностью опорных поверхностей. Выбор поверхности призмы, обеспечивающей наивысшую точность технологических операций, зависит от конкретных условий и проведения тщательных исследований.
Актуальны также ТР, позволяющие использовать центровые отверстия обычной точности с отклонениями формы в пределах
1...4 мкм и уменьшить наследственный перенос погрешностей. Так, в МГТУ им. Н.Э. Баумана разработан метод шлифования валов с неравномерной окружной скоростью вращения заготовки, которая обеспечивается введением в привод вращения заготовки специальных поводковых устройств. Специальный поводковый патрон позволяет принудительно изменять скорость вращения заготовки в пределах каждого ее оборота. Для использования этого устройства необходимо иметь информацию о точности формы поперечных сечений центровых отверстий, которую можно получить с помощью кругломеров.
Число выступов и их расположение на центровом отверстии может быть различным. В большинстве случаев проявляются низкочастотные гармонические составляющие некруглости (овальность, трехгранка) (рис. 4.17).
Изменяя скорость вращения заготовки соответственно числу выступов на центровом отверстии, можно существенно уменьшить наследственный перенос погрешности формы центровых отверстий на обработанную наружную поверхность вала. Окружная скорость
вращения n заг заготовки должна уменьшаться при проходе
шлифовальным кругом участков заготовки, соответствующих впадинам центровых отверстий (см. рис. 4.17). Особо следует отметить тот факт, что приведенные выше технологические операции выполняют в термо-константных помещениях.
Предварительная аттестация центровых гнезд заготовки и настройка специального поводкового патрона ограни-чивают применение рассмотренного метода
обработки в других производствах
Рис. 4.17. Схема круглого шлифования
|
|
Типы сооружений для обработки осадков: Септиками называются сооружения, в которых одновременно происходят осветление сточной жидкости...
Папиллярные узоры пальцев рук - маркер спортивных способностей: дерматоглифические признаки формируются на 3-5 месяце беременности, не изменяются в течение жизни...
Наброски и зарисовки растений, плодов, цветов: Освоить конструктивное построение структуры дерева через зарисовки отдельных деревьев, группы деревьев...
История развития хранилищ для нефти: Первые склады нефти появились в XVII веке. Они представляли собой землянные ямы-амбара глубиной 4…5 м...
© cyberpedia.su 2017-2024 - Не является автором материалов. Исключительное право сохранено за автором текста.
Если вы не хотите, чтобы данный материал был у нас на сайте, перейдите по ссылке: Нарушение авторских прав. Мы поможем в написании вашей работы!