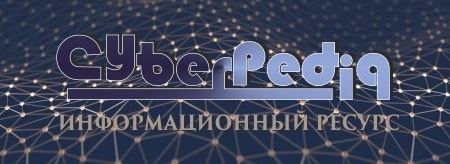
Наброски и зарисовки растений, плодов, цветов: Освоить конструктивное построение структуры дерева через зарисовки отдельных деревьев, группы деревьев...
Организация стока поверхностных вод: Наибольшее количество влаги на земном шаре испаряется с поверхности морей и океанов (88‰)...
Топ:
Техника безопасности при работе на пароконвектомате: К обслуживанию пароконвектомата допускаются лица, прошедшие технический минимум по эксплуатации оборудования...
Эволюция кровеносной системы позвоночных животных: Биологическая эволюция – необратимый процесс исторического развития живой природы...
Проблема типологии научных революций: Глобальные научные революции и типы научной рациональности...
Интересное:
Средства для ингаляционного наркоза: Наркоз наступает в результате вдыхания (ингаляции) средств, которое осуществляют или с помощью маски...
Финансовый рынок и его значение в управлении денежными потоками на современном этапе: любому предприятию для расширения производства и увеличения прибыли нужны...
Подходы к решению темы фильма: Существует три основных типа исторического фильма, имеющих между собой много общего...
Дисциплины:
![]() |
![]() |
5.00
из
|
Заказать работу |
|
|
Рассмотрим особенности управления ТП применительно к автоматизированному механообрабатывающему производству.
Для автоматизированного производства характерны:
работа оборудования в автоматическом режиме, по автоматическому циклу (исключение иногда составляют позиции загрузки);
снижение или полное отсутствие возможности вмешательства в процесс формообразования оператора, тенденция к реализации в автоматизированных производственных системах «безлюдного» режима обработки;
стремление к объединению конструкторской, технологической подготовок производства и собственно производства в единый комплекс на базе вычислительной техники, т. е. компьютеризированное интегрированное производство;
тенденция к автоматизации производства любого типа (единичного, серийного, массового).
Тип производства в основном определяет степень его автоматизации и специфику задач управления ТП.
Автоматизацию единичного и мелкосерийного производства осуществляют в основном на базе использования станков с ЧПУ. Специфику задач управления при обеспечении качества продукции в единичном и мелкосерийном производстве определяют следующие особенности.
1. Повышенное рассеяние входных переменных, что обусловлено, например, более низким качеством заготовок. Это порождает увеличение случайной составляющей погрешности обработки. Для обеспечения заданного качества, как правило, приходится снижать производительность обработки (увеличивать число переходов и рабочих ходов, снижать режимы обработки). Основными путями устранения указанного недостатка являются совершенствование методов получения заготовок, а также повышение качества управления в цикловых системах. Получение заготовок высокого качества в единичном или мелкосерийном производстве сопряжено со значительными затратами. Однако, например, для литых и штампованных заготовок разрабатывают быстропереналаживаемую оснастку (модели, штампы) по типу универсально-сборных приспособлений, которая позволяет обеспечить высокое качество заготовок при малых программах выпуска.
|
2. Высококонцентрированное построение операций обработки, в частности на станках с ЧПУ. В этих условиях становится практически невозможным для цикловых систем управление погрешностями от тепловых деформаций и размерного износа инструмента, поскольку сильно затруднен их расчет.
3. Широкая номенклатура и малые программы выпуска изделий (деталей). В течение смены на одном станке могут быть обработаны заготовки нескольких типоразмеров. Кроме того, получают все большее распространение новые организационные
формы запуска заготовок в обработку. Стремятся ввести обработку комплектами, причем в комплект включают детали, входящие в одну сборочную единицу, что позволяет уменьшить потребные складские площади, сократить цикл производства изделия. В этих условиях вообще идет непрерывная смена операций на станке с ЧПУ и одновременно остро встает проблема выполнения размерной наладки (статической настройки), так как известные методы наладки в таких условиях либо полностью непригодны, либо малоэффективны.
Наладка по пробным деталям, во-первых, становится очень трудоемкой (до 40 % и более трудоемкости обработки всей партии) и, во-вторых, вносит большую погрешность, так как количество пробных деталей здесь не превышает одной. Наладка по эталону в целом непригодна вследствие экономической нецелесообразности изготовления эталонов при малом выпуске изделий, к тому же точность наладки в большинстве случаев недостаточна для обеспечения требуемой точности обработки. Взаимозаменяемая наладка, широко применяемая на станках с ЧПУ, не решает задачу первичной наладки и используется только при замене инструментов.
|
Для применения в цикловых системах управления в МГТУ им. Н.Э. Баумана разработан метод групповой размерной наладки, применяемый при обработке деталей различных типоразмеров, составляющих группу либо комплект. В этом методе наладка ведется не на наладочный размер, определяемый из условия обеспечения заданного размера обрабатываемой поверхности, а на произвольно выбранный размер. Выполняется статическая настройка (по эталону) или динамическая (по пробной стружке). Перед обработкой деталей каждого типоразмера инструмент перемещается в исходную («нулевую») точку заданием соответствующего перемещения на устройстве ЧПУ либо по сигналам управляющего компьютера. Требуемые наладочные положения перед обработкой конкретных поверхностей заготовок каждого типоразмера инструмент занимает по программе, для чего в процессе ее подготовки выполняется соответствующий расчет координат опорных точек (перемещений инструмента). Метод позволяет уменьшить трудоемкость наладки, однако не обеспечивает ее высокую точность, так как при расчете координат опорных точек используются зависимости, неадекватно описывающие реально протекающий процесс. Поэтому и здесь появляется необходимость оперативного регулирования статической или даже динамической настройки, с помощью описанных ранее методов и систем.
В крупносерийном и массовом автоматизированных производствах специфику задач управления определяют следующие требования:
обеспечение высокой производительности обработки. Время измерения необходимых для управления параметров и время, затрачиваемое на реализацию результатов измерения (компенсация погрешностей, подналадка и т.д.), должны максимально перекрываться оперативным временем;
повышение устойчивости производственных систем к отказам. Это особенно относится к производственным системам, работающим в тактовом режиме, например автоматическим линиям, а также к производственным системам, управляемым едиными управляющими комплексами. Для производственных систем, функционирующих в «безлюдном» режиме, необходимо обеспечение поддержания их работоспособности.
|
Специфика задач управления в серийном автоматизированном производстве в той или иной мере отражает специфику задач рассмотренных выше производств. Требование обеспечения качества изделий широкой номенклатуры может сочетаться, например, с требованием обеспечения заданной производительности производственной системы, функционирующей в «безлюдном» режиме.
Специфика управления автоматизированными (гибкими) производственными системами позволила выделить особый класс задач ситуационного управления, общая постановка которых заключается в следующем. Известна структура автоматизированной производственной системы (состав оборудования, взаимосвязь отдельных элементов системы и т. д.), а также номенклатура, программы выпуска, параметры заготовок, обрабатываемых в данной системе. Задается ситуация, возникающая в определенном месте (элементе) системы: отказ оборудования, риск появления брака, поломка или прогрессирующий износ инструмента, отказ элемента транспортной системы и т. п. Необходимо принять решение, являющееся оптимальным с позиции эффективности работы системы, описываемой системой соответствующих критериев.
Каждое из конкретных решений задачи ситуационного управления можно рассматривать как методическую и информационную основу для его представления в виде соответствующей программы управления. Совокупность таких программ образует программное обеспечение управления и определяет его эффективность.
|
|
Поперечные профили набережных и береговой полосы: На городских территориях берегоукрепление проектируют с учетом технических и экономических требований, но особое значение придают эстетическим...
Кормораздатчик мобильный электрифицированный: схема и процесс работы устройства...
Автоматическое растормаживание колес: Тормозные устройства колес предназначены для уменьшения длины пробега и улучшения маневрирования ВС при...
История развития хранилищ для нефти: Первые склады нефти появились в XVII веке. Они представляли собой землянные ямы-амбара глубиной 4…5 м...
© cyberpedia.su 2017-2024 - Не является автором материалов. Исключительное право сохранено за автором текста.
Если вы не хотите, чтобы данный материал был у нас на сайте, перейдите по ссылке: Нарушение авторских прав. Мы поможем в написании вашей работы!