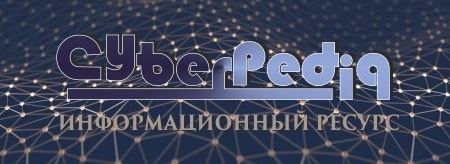
Индивидуальные очистные сооружения: К классу индивидуальных очистных сооружений относят сооружения, пропускная способность которых...
Наброски и зарисовки растений, плодов, цветов: Освоить конструктивное построение структуры дерева через зарисовки отдельных деревьев, группы деревьев...
Топ:
Когда производится ограждение поезда, остановившегося на перегоне: Во всех случаях немедленно должно быть ограждено место препятствия для движения поездов на смежном пути двухпутного...
Методика измерений сопротивления растеканию тока анодного заземления: Анодный заземлитель (анод) – проводник, погруженный в электролитическую среду (грунт, раствор электролита) и подключенный к положительному...
Интересное:
Мероприятия для защиты от морозного пучения грунтов: Инженерная защита от морозного (криогенного) пучения грунтов необходима для легких малоэтажных зданий и других сооружений...
Уполаживание и террасирование склонов: Если глубина оврага более 5 м необходимо устройство берм. Варианты использования оврагов для градостроительных целей...
Что нужно делать при лейкемии: Прежде всего, необходимо выяснить, не страдаете ли вы каким-либо душевным недугом...
Дисциплины:
![]() |
![]() |
5.00
из
|
Заказать работу |
|
|
Регулирование динамической настройки выполняется непосредственно в процессе формообразования того комплекса поверхностей, качество которых необходимо обеспечить. Выполнить это можно одним из следующих способов:
1) поддержанием заданного уровня статической настройки путем введения корректирующих управляющих воздействий, учитывающих случайные составляющие векторов входных переменных и условий;
2) автоматическим генерированием, поддержанием и изменением наиболее оптимального для данных условий уровня настройки, гарантированно обеспечивающего заданное качество.
В системах, обеспечивающих регулирование динамической настройки, наблюдается наиболее полный компромисс принципов активного контроля и адаптации. Контроль и управление осуществляются, как правило, по составляющим вектора условий.
На рис. 3.12 показана блок-схема широкоуниверсального следящего гидравлического люнета для токарных станков с ЧПУ, сконструированного в МГТУ им. Н.Э. Баумана.
Резец 1, установленный в револьверном суппорте, выполняет обработку цилиндрической поверхности заготовки 2. В контакте с заготовкой находятся опорные ролики 3 люнета. Коромысло люнета расположено на штоке гидроцилиндра 8. Управление перемещениями опорных роликов 3 люнета осуществляется с помощью технологических команд ЧПУ, обеспечивающих включение либо левой, либо правой обмотки реверсивного золотника 7.
Рис. 3.12. Блок-схема широкоуниверсального следящего гидравлического люнета для токарных станков с ЧПУ
Это обеспечивает перемещение штока гидроцилиндра 8 к заготовке или в крайнее от нее положение. Выполнение необходимых перемещений контролируется датчиками положения 5, 6. Силы резания, возникающие при обработке заготовки, контролируются датчиками 4, 11. Сигналы от датчиков 4, 11 сравниваются в блоке 10. При наличии сигнала рассогласования подается команда на управляющий золотник 9. Последний обеспечивает перемещение штока в нужном направлении до тех пор, пока силы на штоке и суппорте не уравняются (сигнал рассогласования становится равным нулю). Таким образом, радиальная составляющая силы резания уравновешивается силой на люнете, что исключает деформацию заготовки.
|
Рассмотренная система является самонастраивающейся. В системах управления и обеспечения качества продукции все более широкое применение находят средства вычислительной техники. В МГТУ им. Н.Э. Баумана была разработана система управления точностью диаметральных размеров и положением осей отверстий заготовок, обрабатываемых на многооперационных станках (рис. 3.13). Обрабатываемая заготовка 1 установлена в приспособлении на столе многооперационного станка 4, имеющего собственную измерительную систему. Управление станком осуществляет устройство ЧПУ 9. Электронное устройство управления 6 с терминалом ввода-вывода данных 7 соединена интерфейсами сопряжения 5 и связи 8 с измерительной системой станка 4 и устройством ЧПУ 9, управляющим приводами 10 станка.
Рис. 3.13. Блок-схема системы управления точностью диаметральных размеров и положением осей отверстий
На программоносителе перед управляющей программой обработки заготовки записаны дополнительная программа, содержащая данные о заготовке, и подпрограмма измерения первичных погрешностей заготовки. С терминала 7 в устройство 6 вводят дополнительные данные об условиях обработки, о жесткости технологической системы, используемых инструментах и материале. После ввода программоносителя перед началом обработки отрабатывается подпрограмма измерения заготовки. Измерительный щуп 2 по командам подпрограммы измерения устанавливается в шпиндель станка и автоматически с помощью устройства передачи сигнала 3 подключается к измерительной системе станка. Измерение каждого элемента заготовки выполняется в строго определенной в подпрограмме последовательности.
|
Станок на этом этапе выполняет функции измерительной машины. С программоносителя в устройство 6 передается код схемы измерения элемента и команды на прием и обработку результатов измерения. По подпрограмме измерения щуп 2 на ускоренной подаче подходит к измеряемой поверхности заготовки 1 до касания. В момент касания щуп выдает сигнал в виде импульса, который является командой для остановки движения и передачи в управляющее устройство значений координат, соответствующих моменту касания с измерительной системой станка 4. В соответствии с индивидуальной для каждого элемента стратегией измерения проводится необходимое число замеров и переход к следующему измеряемому элементу. Обработка результатов выполняется между измерениями. Определяются положение заготовки в системе координат станка, погрешности заготовки, ожидаемая точность обработки отверстий. Ожидаемая точность сравнивается с заданной, введенной с программоносителя. При удовлетворительном результате заготовка обрабатывается по основной (заданной) управляющей программе, при отрицательном — выполняется необходимая корректировка условий обработки (смещение оси отверстия от настроечного размера или изменение режима резания).
Применение рассмотренной системы позволяет обеспечить точность позиционных отклонений оси отверстий не ниже 0,01 мм, а диаметральных размеров до 0,015 мм при уменьшении числа предварительных переходов растачивания отверстий.
Большинство известных реализаций самоприспосабливающихся (адаптивных) систем в целом, хотя и считаются системами регулирования динамической настройки, обеспечивают поддержание заданного уровня статической настройки путем компенсации действия случайных составляющих векторов входных переменных и условий. Адаптивная система, схема которой изображена на рис. 3.14, предназначена для компенсации упругих деформаций технологической системы под действием сил резания.
На фрезерном станке с ЧПУ обрабатывается заготовка 4 концевой фрезой 5. Управление приводами 11 подач осуществляет устройство ЧПУ 1. Возникающие при обработке силы резания вызывают упругие деформации технологической системы, фиксируемые датчиком 6. Заданное управляющей программой понижение контролирует датчик 2. Сигналы датчиков сравниваются в сумматоре 8. При возникновении сигнала рассогласования последний усиливается усилителем 7 и подается на вход исполнительного элемента привода управления 9. Исполнительный элемент 9 сдвигает верхнюю плиту накладного динамометрического стола 3 вместе с установленной на ней заготовкой относительно стола 10 станка. Расстояние и направление корректирующего перемещения соответствуют значению и направлению деформации технологической системы.
|
Рис. 3.14. Блок-схема адаптивной системы, обеспечивающей компенсацию упругих деформаций технологической системы
На рис. 3.15 приведена общая схема системы адаптивного управления качеством заготовки 1 при шлифовании кругом 2. Данные о диаметре D, шероховатости Ra поверхности заготовки и радиальной силе Р шлифования в виде электрических сигналов от соответствующих датчиков поступают в электронные преобразующие устройства 3, откуда их значения поступают на аналоговый вход вычислительной машины 4.
Рис. 3.15. Блок-схема системы адаптивного управления качеством обрабатываемой заготовки при шлифовании
Сигнал работы А шлифования определяется по скорости изменения измеряемого диаметра D заготовки. Вычислительная машина в зависимости от измеренных и вычисленных параметров (Ra, Р, D, А) оптимизирует значение поперечной подачи Sпоп, передаваемой в управляющее устройство 5, где оно кодируется и поступает в виде электрического сигнала на шаговый электродвигатель 6. Сигнал радиальной силы Р шлифования также поступает на управляющее устройство для своевременного переключения быстрого подвода круга на рабочую подачу при соприкосновении круга с заготовкой и остановки станка, если радиальная сила шлифования превысит допустимую.
Системы с прямым контролем нашли широкое применение для компенсации погрешностей размера при врезном наружном и внутреннем шлифовании, компенсации погрешности формы шеек валов в продольном сечении при обтачивании на токарных станках и т.д. На рис. 3.16 показан пример использования системы с прямым контролем для управления точностью размера при шлифовании желоба кольца подшипников.
|
Рис. 3.16. Схема управления точностью размера при прямом контроле: а — схема измерения; б — схема шлифования
Управление приводами станка осуществляется по результатам контроля диаметрального размера измерительной головкой, расположенной в корпусе 1. Измерительный шток 2 с алмазным наконечником вводится в желоб. В процессе шлифования по мере увеличения диаметра желоба шток 2 поднимается. Под действием кольца 3 крестообразная пружина 4 изгибается и отклоняет подвижный контакт 5. При его отходе от неподвижного контакта 7 дается команда исполнительным органам станка на переход с чернового шлифования на чистовое. По достижении заданного размера подвижный контакт 5 замыкается с неподвижным 6 и процесс шлифования прекращается.
Эффективность систем управления и в особенности систем оперативного регулирования динамической настройки в значительной мере определяется эффективностью применяемых в них диагностических датчиков, по сигналам которых выдаются необходимые управляющие команды.
В зависимости от задач контроля и контролируемых параметров при управлении ТП применяют датчики следующих групп: датчики контроля качества обработки (точности размеров и взаимного расположения поверхностей), точности установки заготовок, размерного износа инструмента, точности настройки инструмента, температурных деформаций заготовки и оборудования;
датчики сил резания и упругих деформаций элементов технологической системы, а также состояния (износ и поломка) режущего инструмента;
датчики контроля состояния элементов технологической системы и системы управления.
|
|
Семя – орган полового размножения и расселения растений: наружи у семян имеется плотный покров – кожура...
Индивидуальные и групповые автопоилки: для животных. Схемы и конструкции...
Таксономические единицы (категории) растений: Каждая система классификации состоит из определённых соподчиненных друг другу...
Адаптации растений и животных к жизни в горах: Большое значение для жизни организмов в горах имеют степень расчленения, крутизна и экспозиционные различия склонов...
© cyberpedia.su 2017-2024 - Не является автором материалов. Исключительное право сохранено за автором текста.
Если вы не хотите, чтобы данный материал был у нас на сайте, перейдите по ссылке: Нарушение авторских прав. Мы поможем в написании вашей работы!