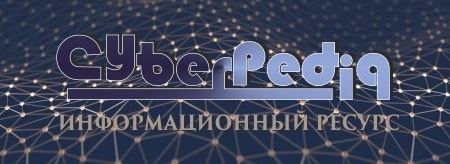
Особенности сооружения опор в сложных условиях: Сооружение ВЛ в районах с суровыми климатическими и тяжелыми геологическими условиями...
Семя – орган полового размножения и расселения растений: наружи у семян имеется плотный покров – кожура...
Топ:
Теоретическая значимость работы: Описание теоретической значимости (ценности) результатов исследования должно присутствовать во введении...
Определение места расположения распределительного центра: Фирма реализует продукцию на рынках сбыта и имеет постоянных поставщиков в разных регионах. Увеличение объема продаж...
Характеристика АТП и сварочно-жестяницкого участка: Транспорт в настоящее время является одной из важнейших отраслей народного хозяйства...
Интересное:
Принципы управления денежными потоками: одним из методов контроля за состоянием денежной наличности является...
Берегоукрепление оползневых склонов: На прибрежных склонах основной причиной развития оползневых процессов является подмыв водами рек естественных склонов...
Средства для ингаляционного наркоза: Наркоз наступает в результате вдыхания (ингаляции) средств, которое осуществляют или с помощью маски...
Дисциплины:
![]() |
![]() |
5.00
из
|
Заказать работу |
ТП представляет собой сложно организованную, целенаправленную структуру, элементами которой являются технологические операции.
Основную задачу управления ТП машиностроения можно сформулировать так (см. рис. 3.1): при известном векторе входных переменных и частично известном векторе условий
найти такой вектор управления
который гарантированно обеспечил бы выполнение условия
(3.3)
где — эталонный вектор выходных переменных;
— фиксированный вектор ошибки выходных переменных.
Вектор считается известным, так как при необходимости может быть проконтролирована или определена любая его составляющая. Вектор условий
включает составляющие, которые могут быть заданы, например режимы обработки, а также составляющие, которые характеризуют действие факторов, дестабилизирующих процесс. Выявление и определение закономерностей изменения этих факторов представляет определенные трудности, а иногда и невозможны. Поэтому следует считать вектор
частично определенным. Изменение составляющих вектора
может отразиться на составляющих вектора
. Например, увеличение припуска на поверхности заготовки неизбежно вызовет увеличение сил резания и, как следствие, рост значений ряда составляющих суммарной погрешности обработки, которые можно рассматривать как составляющие вектора
.
При отсутствии управления векторы входных переменных и условий определяют вектор выходных переменных. Поэтому одним из методов обеспечения стабильных значений составляющих вектора выходных переменных является стабилизация вектора входных переменных. Считается, что если
где — заданный вектор входных переменных;
— фиксированный вектор ошибки входных переменных, то гарантируется выполнение условия (3.3). Тем самым утверждается, что стабильное качество заготовки гарантирует стабильное качество готовой детали. Такой подход не учитывает случайный характер составляющих вектора
и самого ТП.
Дискретный характер ТП, его разбиение на отдельные технологические операции приводят к тому, что вектор управления процессом следует рассматривать как совокупность векторов управления отдельными технологическими операциями. Таким образом, управление ТП осуществляется только через управление отдельными технологическими операциями.
Задача управления ТП формулируется так: при известном век- торе входных переменных и частично известном векторе
условий найти вектор управления
для каждой технологической операции, чтобы обеспечить для выходных переменных ТП соблюдение условия (3.3).
Системный подход к управлению ТП заключается в том, что каждый вектор не обязательно должен обеспечивать выполнение условия (3.3), но совокупность векторов
должна гарантировать его выполнение для ТП в целом. Соблюдение условия (3.3) для каждой отдельной технологической операции является идеальным условием его выполнения и для процесса в целом. Однако это сопряжено со значительными сложностями и затратами.
В основе существующих методов управления ТП и реализующих это управление технических устройств лежат два основных принципа: активного контроля и адаптации.
Активный контроль включает сбор информации о выходных переменных процесса, сравнение их значений с требуемыми и подачу команды на управляющее устройство для подналадки процесса (изменений уровня настройки, режимов работы оборудования и т.д.). При реализации данного принципа вектор управления следует определять по модели объекта управления в зависимости от отклонения фактического вектора выходных переменных от заданного. Надежность управления зависит от надежности указанной математической модели или реализующих рассматриваемый принцип технических устройств. Разработка математических моделей, связывающих вектор
с отклонениями векторов выходных переменных, является весьма сложной задачей.
Управление, например, обработкой с помощью средств активного контроля в случае появления брака зачастую затруднительно, так как сложно выявить причины, которые привели к потере качества. Затруднительно также определить, какое воздействие должно быть оказано на процесс (подналадка, ремонт, замена инструмента и т. п.) для обеспечения его стабильности при достижении заданного уровня выходной переменной. Наиболее эффективно применение средств активного контроля при условии высокой надежности оборудования и оснастки на операциях механической обработки.
Принцип адаптации используют для решения задач управления как на уровне технологической операции, так и на уровне ТП в целом. Поэтому несколько различается и его трактовка.
На уровне технологической операции сущность адаптивного управления заключается в слежении и поддержании постоянства значения какого-либо параметра, влияющего на ход ТП и обеспечивающего заданный уровень выходного параметра, который определяет качество и производительность при минимальных затратах на выполнение рассматриваемой части ТП. Адаптивное управление осуществляется либо путем ограничения управляемого параметра, т. е. сигнал управления вырабатывается только тогда, когда управляемый параметр достиг предельно допустимого уровня, либо путем поиска оптимального для конкретных текущих условий значения управляемого параметра, т. е. сигнал управления вырабатывается непрерывно и его составляющие соответствуют оптимальным значениям управляемого параметра.
Для уровня технологической операции принцип адаптации применим в основном для операций изготовления деталей. В этом случае обрабатывающее оборудование оснащают автоматической системой, обеспечивающей постоянный контроль управляемого параметра и сравнение фактических результатов с заданными. При возникновении отклонения определяется его численное значение и знак и корректируется фактор, регулирующий управляемый параметр. Например, при изменении силы резания изменяется подача независимо от факторов, которые этому способствовали.
Практическое применение принципа адаптации для управления технологическими операциями связано с разработкой на его основе и внедрением автоматизированных (автоматических) систем управления. Эти системы должны работать в режиме реального времени, обеспечивая мгновенную реакцию на отклонение контролируемого параметра, что предъявляет высокие требования к их чувствительности и быстродействию. Современные технические средства не позволяют обеспечивать мгновенную управляющую реакцию на возникшее отклонение контролируемого параметра. Реакция системы запаздывает — система вырабатывает сигнал управления спустя некоторое время после возникновения отклонений контролируемого параметра. Сложность разработки адекватных математических моделей, недостаточные чувствительность и быстродействие стали причинами ограниченного использования адаптивных систем.
Применение принципа адаптации для управления ТП заключается в поддержании стабильности вектора выходных переменных при изменении в некоторых пределах векторов входных переменных и условий вследствие целенаправленного изменения структуры и параметров ТП. В данном случае управление направлено на адаптацию ТП к возникшим изменениям входных переменных и условий его протекания. Принцип адаптации применяют при управлении процессами изготовления изделий высокой эксплуатационной надежности в автоматизированном производстве.
Выполнение функции контроля и управления ТП в современном машиностроении неразрывно связано с решением проблемы автоматизации производства. Технологическую систему можно представить (рис. 3.4) как систему, объединяющую объект управления (ОУ) и управляющее устройство (УУ). На вход последнего подается задающее воздействие узад(τ), содержащее информацию о цели управления. Сформированный управляющим устройством вектор U (τ) в виде управляющего воздействия передается к объекту управления. В состав управляющего устройства могут входить чувствительное, вычислительное и исполнительное устройства.
Чувствительные устройства (измерительные устройства, датчики) служат для измерения подаваемых к управляющему устройству воздействий. Вычислительное устройство реализует алгоритм его работы.
Рис. 3.4. Структуры систем управлениякачеством про-дукции при механической обработке: а — без обратной связи; б — с обратной связью по возмущающим воз-действиям; в — то же по выходным переменным; г — с контролем входных переменных
В простейшем случае оно выполняет элементарные математические операции (сравнение, определение разности, интегрирование и т. п.). В более сложных случаях для решения задач управления используют вычислительную технику. Исполнительные устройства предназначены для непосредственного управления объектом, т. е. изменения его состояния в соответствии с сигналом управления. В частном случае в качестве исполнительного устройства могут использоваться, например, приводы исполнительных перемещений станка.
Рассмотрим структуры некоторых систем, применяющихся для управления качеством продукции при механической обработке
1. Системы без обратной связи по возмущающим воздействиям и выходным переменным (см. рис. 3.4, а), которые часто называют цикловыми.
2. Системы с обратной связью по возмущающим воздействиям (см. рис. 3.4, б). Их называют системами с контролем по параметрам обработки или самонастраивающимися системами. Разновидность систем, в которых контроль возмущающего воздействия выполняется непосредственно в процессе формообразования, а его результаты, преобразованные в сигнал управления, тут же обрабатываются, называют самоприспосабливающимися (адаптивными).
3. Системы с обратной связью по выходным переменным (см. рис. 3.4, в). Различают две разновидности таких систем: с прямым контролем — контроль выходных переменных и управление, сформированное по его результатам, осуществляются непосредственно при выполнении операций — и с контролем выходных параметров обработки — контроль выходных переменных осуществляется не в процессе формообразования, а после его окончания, т. е. у обработанной заготовки. Системы с обратной связью по выходным переменным называют самоподнастраива- ющимися.
4. Системы с контролем входных переменных (см. рис. 3.4, г). В таких системах контроль выполняется до начала процесса формообразования, а его результаты учитываются при выработке вектора управления.
В настоящее время наибольшее распространение получили цикловые системы (обработка на станках-автоматах и полуавтоматах, гидрокопировальных станках, станках с ЧПУ, автоматических линиях и т. д.); они просты и надежны в работе, что, собственно, и определило их широкое распространение. Обработка при использовании таких систем происходит по жесткому циклу. Цикл не прерывается, если в процессе обработки возникает отклонение параметра качества. Это основной недостаток таких систем. Несмотря на высокую надежность самой системы, надежность протекания процесса обработки низка. В этих системах практически полностью отсутствует управление точностью в сфере самого производства (реализации ТП), поэтому они не позволяют компенсировать влияние любых факторов на точность обработки. Управление точностью в цикловых системах ограничено сферой ТПП. Именно на стадии ТПП формируется содержание задающего воздействия. Управление точностью сводится к расчетам ожидаемой точности, осуществляемым в процессе проектирования операции, и назначению таких условий ее выполнения, которые обеспечивали бы заданные параметры качества.
В самонастраивающихся системах предусмотрен контроль факторов, обусловливающих появление погрешностей обработки, и последующая компенсация их влияния непосредственно при производстве. Контроль параметров (условий) обработки возможен как до начала цикла автоматизированной обработки, так и в самом цикле. Однако и в том, и в другом случае он предшествует процессу формообразования. В результате такого контроля случайные (для цикловой автоматики) факторы превращаются в систематические. Такие системы применяют для компенсации погрешностей установки заготовок, тепловых деформаций элементов оборудования, износа инструмента и т. д. Они позволяют существенно уменьшить влияние случайных, закономерно изменяющихся и постоянных факторов на точность обработки. Самонастраивающиеся системы наиболее удобны для применения на станках с ЧПУ. Алгоритм управления в таких системах основан на тех же зависимостях, по которым выполняется расчет ожидаемой точности обработки для цикловых систем. Невысокая точность расчета по этим зависимостям сказывается на качестве управления, что является недостатком самонастраивающихся систем.
Самоприспосабливающиеся (адаптивные) системы обеспечивают контроль и управление одним или несколькими факторами (составляющими вектора условий), обусловливающими формирование параметров качества. Процесс контроля и управления происходит синхронно с процессом формообразования. Преимущества и недостатки этих систем рассмотрены ранее при анализе принципа адаптации.
Системы с обратной связью по выходным переменным позволяют практически полностью исключить влияние технологических факторов на точность выдерживаемого параметра. Недостаток таких систем управления — ограниченная область применения, что обусловлено главным образом техническими трудностями их конструктивного оформления для многих конкретных случаев обработки. Системы с контролем выходных параметров обработки фиксируют результат завершенного процесса и не имеют возможности управлять случайными составляющими погрешности обработки. Управлять можно только закономерно изменяющимися погрешностями (вызываемыми износом инструмента, тепловыми деформациями и т.д.), а также систематическими, если таковые возникают в процессе обработки. В основе информационного обеспечения этих систем лежат известные методы статистического контроля.
Системы с контролем входных переменных позволяют учесть фактические размеры заготовки, а в отдельных случаях и физико-механические свойства ее материала при настройке технологической системы. Однако данный вариант управления имеет ограниченное применение ввиду сложности его реализации.
Обеспечение заданной точности при механической обработке в большинстве случаев связано с регулированием настройки технологической системы. Различают регулирование статической и динамической настройки. Под статической настройкой понимают изменение настроечных размеров в технологической системе, выполняемое при отсутствии процесса формообразования (резания). Статическая настройка встречается в цикловых системах и в системах с контролем выходных параметров обработки. В самонастраивающихся системах, а также в системах с прямым контролем изменение настройки осуществляется непосредственно в процессе формообразования, что позволяет отнести их к системам регулирования динамической настройки.
Кормораздатчик мобильный электрифицированный: схема и процесс работы устройства...
Своеобразие русской архитектуры: Основной материал – дерево – быстрота постройки, но недолговечность и необходимость деления...
Таксономические единицы (категории) растений: Каждая система классификации состоит из определённых соподчиненных друг другу...
Поперечные профили набережных и береговой полосы: На городских территориях берегоукрепление проектируют с учетом технических и экономических требований, но особое значение придают эстетическим...
© cyberpedia.su 2017-2024 - Не является автором материалов. Исключительное право сохранено за автором текста.
Если вы не хотите, чтобы данный материал был у нас на сайте, перейдите по ссылке: Нарушение авторских прав. Мы поможем в написании вашей работы!