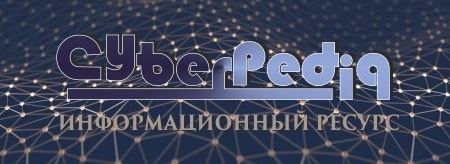
История развития пистолетов-пулеметов: Предпосылкой для возникновения пистолетов-пулеметов послужила давняя тенденция тяготения винтовок...
Историки об Елизавете Петровне: Елизавета попала между двумя встречными культурными течениями, воспитывалась среди новых европейских веяний и преданий...
Топ:
Основы обеспечения единства измерений: Обеспечение единства измерений - деятельность метрологических служб, направленная на достижение...
Выпускная квалификационная работа: Основная часть ВКР, как правило, состоит из двух-трех глав, каждая из которых, в свою очередь...
Оценка эффективности инструментов коммуникационной политики: Внешние коммуникации - обмен информацией между организацией и её внешней средой...
Интересное:
Наиболее распространенные виды рака: Раковая опухоль — это самостоятельное новообразование, которое может возникнуть и от повышенного давления...
Подходы к решению темы фильма: Существует три основных типа исторического фильма, имеющих между собой много общего...
Как мы говорим и как мы слушаем: общение можно сравнить с огромным зонтиком, под которым скрыто все...
Дисциплины:
![]() |
![]() |
5.00
из
|
Заказать работу |
|
|
При использовании фабричной последовательности обработки изделий ее анализируют на предмет выбора более оптимального варианта обработки, который, обеспечивая высокое качество, позволил бы снизить затраты времени и наиболее полно использовать производительность оборудования.
По каждой неделимой операции и узлу в технологической последовательности решается целесообразность усовершенствования обработки. Усовершенствовать технологическую последовательность можно за счет:
1) применения точного кроя;
2) улучшения организации производства;
3) применения малооперационной технологии;
4) использования новых материалов;
5) внедрения приспособлений малой механизации;
6) внедрения нового высокопроизводительного оборудования.
При внедрении нового высокопроизводительного оборудования экономическая эффективность достигается тремя путями:
ТЕХНОЛОГИЧЕСКИЕ ГРУППЫ
Операционные
уровни 05 03 01 02 04 06
ТЕХНОЛОГИЧЕСКИЕ ПОДГРУППЫ
рукав спинка кокетка перед карман воротник манжета
02 06 05 07 04 01 04
|
Рисунок 10 – Граф технологического процесса изготовления мужской сорочки
1) за счет увеличения скорости машины.
В этом случае новые затраты времени определяются по следующей формуле:
|
l × m × 60 1 1
tпр. = tфабр. - ¾¾¾¾ × (¾¾¾ - ¾¾¾),
Ки.с. n фабр. n пр.
где tпр., tфабр. – проектируемое и фабричное время по операциям, с;
l – длина строчки, см;
m – количество стежков в 1см строчки;
nпр., nфабр. – число оборотов главного вала проектируемого и заменяемого оборудования, об/мин.;
Ки.с. - коэффициент использования скорости машины ( 0,3÷0,4 – для коротких швов, 0,5÷0,6 -
для длинных швов).
2) за счет сокращения затрат времени на вспомогательные приемы.
В этом случае необходимо изменить затраты времени на вспомогательные приемы с учетом отраслевых поэлементных нормативов времени по видам работ и оборудования. Экономия определяется сопоставлением суммарных затрат времени до и после изменения.
3) за счет использования полуавтоматов и автоматов, изменяющих методы обработки.
В этом случае необходимо сопоставить применяемые на предприятии и проектируемые методы обработки по узлам, указав соответствующие затраты времени и получаемую экономию.
Иногда затрату времени по неделимым операциям можно определить исходя из производительности оборудования в смену, указанного в его технологической характеристике, по следующей формуле:
R
t пр. = ¾¾¾,
П об
где R – продолжительность рабочей смены, с;
Поб – производительность оборудования в единицах в смену.
На основании проделанной работы по усовершенствованию фабричной технологической последовательности составляется новая технологическая последовательность обработки изделия.
Экономическая эффективность в целом по изделию устанавливается по следующим показателям:
|
- сокращению затрат времени (СЗВ, %) на обработку, рассчитываемому по формуле:
,
где Тфабр., Тпр. – фабричные и проектируемые затраты времени на обработку изделия, с;
- росту производительности труда (РПТ, %), который определяется по формуле:
Предварительный расчет одномодельного потока
Предварительный расчет потоков выполняют как при проектировании новых, так и при реорганизации действующих потоков. Цель предварительного расчета состоит в том, чтобы на начальной стадии проектирования, на основе анализа исходных данных и показателей работы потоков произвести размещение их в цехе, определить наиболее целесообразные и эффективные формы организации потоков.
Вначале рассчитывают показатели работы основного потока, а затем неосновных потоков (по укрупненным показателям). Предварительный расчет выполняют по данным технического задания на проектирование, в котором указаны площадь цеха (при реконструкции) или один из параметров потока и ассортимент изделий. Для расчета потока необходима также затрата времени на изготовление изделий, которая берется из технологической последовательности (ТП) обработки. При предварительном расчете потока определяют его основные параметры: такт потока, выпуск изделий в смену и количество рабочих.
Тактом потока называется средняя расчетная затрата времени, в течение которой один исполнитель выполняет свою организационную операцию в потоке. Такт потока показывает средний промежуток времени, через который изделие выпускается с потока (запускается в поток).
Расчетную величину такта определяют по формуле:
или
,
где - такт потока, с;
Т – затрата времени, необходимая для изготовления одного изделия (трудоемкость), с; N – количество рабочих в потоке, чел.;
R – продолжительность смены, с;
Мсм - заданный выпуск изделий в смену, ед.
Мощность потока выражают выпуском изделий в смену и определяют по формуле:
Mc м =
Количество рабочих в потоке N определяют по формуле:
Количество рабочих можно также определить, зная выпуск изделий в смену и трудоемкость изготовления изделия, по формуле:
Количество рабочих в потоке можно определить и по площади S, занятой потоком:
,
где Sн – норматив площади, на одного рабочего с учетом проходов, проездов для транспортных средств, организационной формы потока (секции), м2. Величина Sн зависит от вида ассортимента, мощности потока, применяемых транспортных средств, организационной формы потока (секции). Значения величины Sн приведены в таблице 4.
|
Таблица 4 Типовые нормы и площади на одного производственного
рабочего швейного цеха, м2
Наименование изделия | Агрегатно-групповой | Конвей-ерный | Комбини-рованный | Комплексно-механизирован-ные линии |
1 | 2 | 3 | 4 | 5 |
Пальто, полупальто женское, мужское из шерстяной, смесовой ткани | 9,6 | 8,7 | 8,9 | 10 |
Пальто, полупальто мужское, женское, детское из искусственного меха | 7,8 | 7,2 | 7,5 | – |
Плащ мужской, женский, детский школьный | 7,9 | 7,1 | 7,5 | 9,1 |
Куртка мужская, женская, детская школьная | 7,6 | 7,2 | 7,5 | 8,6 |
Пальто, полупальто, плащи, куртки для детей дошкольного и ясельного возраста | 7,4 | 6,8 | 7,2 | 8,5 |
Костюмы, жакеты мужские, женские и детские школьного возраста | 7,3 | 6,7 | 7,0 | 8,8 |
Костюм шерстяной мужской и для мальчиков школьного возраста | 8,3 | 7,6 | 7,9 | 9,4 |
Брюки мужские, женские и для детей школьного возраста | 6,0 | 5,6 | 5,8 | 6,4 |
Производственная и бытовая одежда | 6,7 | 6,1 | 6,4 | 6,7 |
Платья, блузки, юбки женские и для детей школьного возраста | 7,5 | 6,8 | 7,1 | 7,9 |
Сорочки мужские и для детей школьного возраста | 7,4 | 6,7 | 7,1 | 7,9 |
Платья, блузки, сорочки, юбки, брюки для детей дошкольного и ясельного возраста | 5,7 | 5,7 | 5,5 | 5,9 |
Белье и предметы женского туалета | 5,3 | 4,4 | 5,0 | 5,3 |
Головные уборы шитые и фетровые | 5,6 10,8 | 5,6 10,8 | 5,6 10,8 | 5,6 10,8 |
Количество рабочих мест в потоке всегда больше количества рабочих в результате наличия запасных мест (оборудования), многостаночного обслуживания и наличия мест больших размеров (полуавтоматы, прессы и др.), имеющих шаг рабочего места больше, чем само машинное место (стандартное для данного потока).
Количество рабочих мест Крм в потоке определяют по формуле:
где Кср – коэффициент, характеризующий среднее количество рабочих мест в потоке, приходящихся на одного рабочего.
Шагом рабочего места l называется расстояние между центрами смежных рабочих мест, или расстояние от начала до конца рабочего места. Шаг рабочего места и размеры рабочих столов зависят от габаритов пошиваемых изделий и от вида выполняемых работ.
|
Рабочие места, расположение которых обеспечивает перемещение полуфабриката вдоль агрегата в одном направлении, называют поточной линией.
Длину поточной линии определяют по формуле:
где Lпл – длина поточной линии, м
– шаг рабочего места, м
Значения величины Кср и приведены в таблице 5.
Таблица 5 Шаг рабочих мест и среднее количество рабочих мест на одного рабочего
Наименование изделия | Шаг рабочего места ![]() | Среднее количество рабочих мест на одного рабочего, Кср |
Белье | 1,15 - 1,20 | 1,10 - 1,15 |
Платье | 1,20 - 1,25 | 1,10 - 1,15 |
Костюмы | 1,20 - 1,25 | 1,15 - 1,20 |
Пальто | 1,25 - 1,30 | 1,20 - 1,25 |
|
|
Общие условия выбора системы дренажа: Система дренажа выбирается в зависимости от характера защищаемого...
Папиллярные узоры пальцев рук - маркер спортивных способностей: дерматоглифические признаки формируются на 3-5 месяце беременности, не изменяются в течение жизни...
Наброски и зарисовки растений, плодов, цветов: Освоить конструктивное построение структуры дерева через зарисовки отдельных деревьев, группы деревьев...
Типы сооружений для обработки осадков: Септиками называются сооружения, в которых одновременно происходят осветление сточной жидкости...
© cyberpedia.su 2017-2024 - Не является автором материалов. Исключительное право сохранено за автором текста.
Если вы не хотите, чтобы данный материал был у нас на сайте, перейдите по ссылке: Нарушение авторских прав. Мы поможем в написании вашей работы!