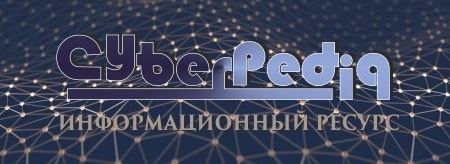
Типы оградительных сооружений в морском порту: По расположению оградительных сооружений в плане различают волноломы, обе оконечности...
Индивидуальные очистные сооружения: К классу индивидуальных очистных сооружений относят сооружения, пропускная способность которых...
Топ:
Характеристика АТП и сварочно-жестяницкого участка: Транспорт в настоящее время является одной из важнейших отраслей народного...
Эволюция кровеносной системы позвоночных животных: Биологическая эволюция – необратимый процесс исторического развития живой природы...
Установка замедленного коксования: Чем выше температура и ниже давление, тем место разрыва углеродной цепи всё больше смещается к её концу и значительно возрастает...
Интересное:
Распространение рака на другие отдаленные от желудка органы: Характерных симптомов рака желудка не существует. Выраженные симптомы появляются, когда опухоль...
Национальное богатство страны и его составляющие: для оценки элементов национального богатства используются...
Берегоукрепление оползневых склонов: На прибрежных склонах основной причиной развития оползневых процессов является подмыв водами рек естественных склонов...
Дисциплины:
![]() |
![]() |
5.00
из
|
Заказать работу |
|
|
8.4. Сверление отверстия до выхода в полость, выдерживая размер .
8.4.1. Расчет режимов резания:
1) Исходные данные:
· Заготовка – отливка;
· Материал заготовки – алюминиевый сплав АК7М2Мг;
· Предел прочности материала заготовки – σв = 300 Мпа;
· Твердость материала заготовки – HB 85;
· Глубинасквозного отверстия – l = 28 мм;
· Общий припуск на обработку –
· Глубина резания –
· Характер обработки – сверление отверстия под резьбу К1/4''.
· Модель станка – 2Н125;
2) Параметры режущего инструмента:
Сверло спиральное по ГОСТ 10903-77:
Материал рабочей части – быстрорежущая сталь Р6М5;
Геометрические параметры:
D = 11 мм;
L = 172 мм;
l = 94 мм;
3) Выбираем величину подачи:
Выбираем максимально допустимую по прочности сверла подачу.
S = 0,55мм/об; [5, стр. 277, табл. 25]
4) Рассчитываем скорость резания:
С v – постоянная, значение берется из справочника;
D – диаметр сверла;
q, у, m – показатели степени для конкретных условий обработки;
Т – средний период стойкости, мин;
S – подача, мм/об;
Kv – суммарный поправочный коэффициент, учитывает фактические условия резания, данные берутся из таблиц.
С v = 40,7; q = 0,25; y = 0,4; m = 0,125; [5, стр. 278]
Т = 60 мин; [5, стр.280]
Kv = Kmv · Kuv · Klu; [5, стр. 276]
Kmv – поправочный коэффициент, учитывающий обрабатываемый материал;
Kuv – поправочный коэффициент, учитывающий материал инструмента;
Klv – поправочный коэффициент, учитывающий глубину сверления
Kuv= 1,0; (2, стр.263);
Klv = 1,0; (2,стр. 280);
Kv = 0,8·1·1 = 0,8;
5) Рассчитываем частоту вращения шпинделя:
По паспорту стана выбираем n п = 1300 об/мин;
6) Рассчитываем фактическую скорость резания:
7) Определяем осевую составляющую силы резания по формуле:
Ср – постоянная, значение берется из справочника;
|
q, у – показатели степени для конкретных условий обработки для каждой из составляющих силы резания;
S – подача, мм/об;
D – диаметр сверла, мм;
Cp = 31,5; qp = 1,0; yp = 0,8;[5, стр. 281]
Kp – поправочный коэффициент на осевую составляющую силы резания
Kp =1; [5, стр. 280]
8) Рассчитываем крутящий момент:
С m – постоянная, значение берется из справочника;
q, у – показатели степени для конкретных условий обработки для каждой из составляющих крутящего момента;
S – подача, мм/об;
D – диаметр сверла, мм;
Kp – поправочный коэффициент на осевую составляющую силы резания.
Cm = 0,012; q = 2,0; y = 0,8; [5, стр. 281]
Kp= 1; [5, стр. 265, табл. 10]
1) Рассчитываем мощность резания:
2) Рассчитываем эффективную мощность резания:
Мощность привода шпинделя станка N ст = 2,2 кВтèстанок модели 2Н125 пригоден для использования на этой операции.
8.4.2. Расчет нормы времени:
1) Определяем длину рабочего хода:
l 1= 5 мм–величина врезания и перебега режущего инструмента;
2) Находим основное время:
8.5. Зенкование фаски, выдерживая размер 1,6±0,8.
8.5.1. Расчет режимов резания:
1) Исходные данные:
· Заготовка – отливка;
· Материал заготовки – алюминиевый сплав АК7М2Мг;
· Предел прочности материала заготовки – σв = 300 Мпа;
· Твердость материала заготовки – HB 85;
· Глубиназенкования – l = 1,6 мм;
· Глубина резания –
· Модель станка – 2Н125;
2) Параметры режущего инструмента:
Зенковка коническая по ГОСТ 14953-80:
Материал рабочей части – быстрорежущая сталь Р6М5;
Геометрические параметры:
D зен = 20мм;
d 0 = 4 мм;
L = 116мм;
l = 24мм;
3) Выбираем величину подачи:
S = 0,2мм/об; [5, стр. 277, табл. 25]
4) Рассчитываем скорость резания:
С v – постоянная, значение берется из справочника;
q, у, m – показатели степени для конкретных условий обработки;
Т – средний период стойкости, мин;
S – подача, мм/об;
Kv – суммарный поправочный коэффициент, учитывает фактические условия резания, данные берутся из таблиц.
С v = 36,3; q = 0,25; y = 0,55; m = 0,125; [5, стр. 278]
Т = 40 мин; [5, стр.280]
|
Kv = Kmv · Kuv · Klu; [5, стр. 276]
Kmv – поправочный коэффициент, учитывающий обрабатываемый материал;
Kuv – поправочный коэффициент, учитывающий материал инструмента;
Klv – поправочный коэффициент, учитывающий глубину сверления
Kuv= 1,0; (2, стр.263);
Klv = 1,0; (2,стр. 280);
Kv = 0,8·1·1 = 0,8;
5) Рассчитываем частоту вращения шпинделя:
По паспорту стана выбираем n п = 250 об/мин;
6) Рассчитываем фактическую скорость резания:
7) Рассчитываем крутящий момент:
С m – постоянная, значение берется из справочника;
q, у – показатели степени для конкретных условий обработки для каждой из составляющих крутящего момента;
S – подача, мм/об;
D – диаметр сверла, мм;
Kp – поправочный коэффициент на осевую составляющую силы резания.
Cm = 0,031; q = 0,85; y = 0,8; [5, стр. 281]
Kp= 1; [5, стр. 265, табл. 10]
8) Рассчитываем мощность резания:
9) Рассчитываем эффективную мощность резания:
Мощность привода шпинделя станка N ст = 2,2 кВтèстанок модели 2Н125 пригоден для использования на этой операции.
8.5.2. Расчет нормы времени:
1) Определяем длину рабочего хода:
l 1= 1,6 мм–величина врезания и перебега режущего инструмента;
2) Находим основное время:
8.6. Нарезание резьбы, выдерживая размер К1/4'' ГОСТ 6111-52.
8.6.1. Расчет режимов резания:
1) Исходные данные:
· Заготовка – отливка;
· Материал заготовки – алюминиевый сплав АК7М2Мг;
· Предел прочности материала заготовки – σв = 300 Мпа;
· Твердость материала заготовки – HB 85;
· Длина резьбы – l = 21 мм;
· Модель станка – 2Н125;
2) Параметры режущего инструмента:
Метчик К1/4'' по ГОСТ 6227-80:
Материал режущей части – быстрорежущая сталь Р6М5.
Геометрические параметры:
P = 1,411 мм – шаг резьбы;
L = 65 мм;
l = 24 мм – длина режущей части;
l 1 = 22 мм – длина хвостовика;
3) Параметры нарезаемой резьбы:
d = 13,572 мм – наружный диаметр в основной плоскости;
d 1 = 11,314 мм – внутренний диаметр резьбы в основной плоскости;
d ср = 12,443 мм – средний диаметр;
4) Определяем высот профиля резьбы:
5) Определяем глубину резания:
t = h = 1,129 мм; [1, стр. 44]
6) Определяем величину подачи:
Величина подачи при нарезании резьбы равна шагу резьбы.
S = P = 1,411 мм; [1, стр. 44]
7) Рассчитываем скорость резания:
Коэффициент Cv и показатели степеней находим из таблиц [5, стр. 296, табл. 49]:
Cv = 64,8;
q = 1,2;
m = 0,9;
y = 0,5;
T = 90 мин – стойкость инструмента;
Kv = Kmv · Kuv · Kτu – общий поправочный коэффициент; [5, стр. 297]
|
Kmv = 1; [5, стр. 298, табл. 50]
Kuv = 1; [5, стр. 298, табл. 50]
Kτu = 0,8; [5, стр. 298, табл. 50]
Kv = 1·1·0,8 = 0,8;
8) Рассчитываем частот вращения шпинделя:
По паспорту стана выбираем n п = 350 об/мин;
9) Рассчитываем фактическую скорость резания:
10) Рассчитываем крутящий момент:
Коэффициент Cm и показатели степеней находим из таблиц [5, стр. 298, табл. 51]:
Cm = 0,027;
q = 1,4;
y = 1,5;
Kp = 1 – поправочный коэффициент; [5, стр. 198, табл. 50]
11) Рассчитываем мощность резания:
12) Рассчитываем эффективную мощность резания:
Мощность привода шпинделя станка N ст = 2,2 кВт è станок модели 2Н125 пригоден для использования на этой операции.
8.6.2. Расчет нормы времени:
1) Определяем длину рабочего хода:
l 1= 1,411 мм–величина врезания и перебега режущего инструмента;
2) Находим основное время:
n1 = 455 об/мин – частота обратного вращения шпинделя;
8.7. Расчет штучного времени для всей операции:
1) Находим суммарное основное время:
2) Находим вспомогательное время:
Вспомогательное время составляет 50% от основного времени. [1, стр. 42]
T в = 0,21·0.5 = 0,11 мин;
3) Вычисляем оперативное время:
T оп = T 0 + T в; [1, стр. 42]
T оп = 0,21 + 0,11 = 0,32 мин;
4) Находим время обслуживания рабочего места:
Время обслуживания рабочего места составляет 5% от оперативного времени.
T обс. = 0, 32·0,05 = 0,02 мин;
5) Находим время перерывов на отдых:
Время перерывовна отдых составляет 5% от оперативного времени.
T отд.= 0,32·0,05 = 0,02 мин;
6) Вычисляем норму штучного времени:
T ш = T оп + T обс. + T отд.;[1, стр. 42]
T ш =0, 32 + 0,02 + 0,02 = 0,36 мин;
Расчет приспособления
Выполним расчет приспособления для закрепления заготовки на вертикально-сверлильном станке модели 2Н125. Операция 050 – вертикально-сверлильная.
9.1. Силовой расчет приспособления:
1) Определяем крутящий момент:
Для расчета силы закрепления заготовки выбираем наибольший крутящий момент на данной операции:
M кр = 17,4Н·м;
2) Определяем силу закрепления заготовки:
Рис. 9.1 – схема зажима.
f = 0,25 – коэффициент трения в месте контакта прихвата и заготовки; [8, стр. 17]
l = 0,04м;
K = K 0· K 1· K 2· K 3· K 4· K 5– коэффициент запаса; [8, стр. 7]
K 0 = 1,5 – гарантированный коэффициент запаса; [8, стр. 7]
|
K 1 = 1 – коэффициент, учитывающий состояние поверхности заготовки; [8, стр. 7]
K 2 = 1,15 – коэффициент, учитывающий увеличение сил резания вследствие затупления инструмента; [8, стр. 7, табл. 1]
K 3 = 1 – коэффициент, учитывающий увеличения сил резания при прерывистом резании; [8, стр. 7]
К 4 = 1 – коэффициент, характеризующий постоянство силы, развиваемой зажимным механизмом, при использовании пневматического зажимного механизма двустороннего действия; [8, стр. 7]
K 5 = 1,5 – коэффициент, учитываемый при наличии крутящего момента; [8, стр. 7]
K = 1,5·1·1,15·1·1·1,5 = 2,59;
3) Выбираем пневмопривод, т. к. он имеет следующие преимущества перед гидроприводом:
- отсутствует специальный источник давления, так как линии сжатого воздуха имеются на большинстве заводов;
- нет возвратных трубопроводов, так как отработанный воздух выпускают в окружающую среду;
- простые аппаратура и арматура.
Определяем диаметр пневмоцилиндра:
p = 0,63 МПа – избыточное давление сжатого воздуха;
Выбираем стандартное значение D = 100 мм. [7, стр. 433, табл. 8]
Выбираем встроенный пневмоцилиндр: обозначение 7020-0209 исполнение 1 ГОСТ 15608-81.
9.2. Расчет приспособления на точность:
Для обеспечения необходимой точности обрабатываемой детали должно соблюдаться условие:
Погрешность установки заготовки на выполняемой операции или переходе определяется по формуле:
ε з = 0,05 мм – погрешность закрепления; [9, стр. 145, табл. 3.24]
ε пр = 0,05 мм – погрешность положения заготовки, которая является следствием неточности изготовления приспособления и износа его базирующих элементов; [9, стр. 133]
Погрешность базирования равна допуску на размер базирующего отверстия:
ε б = 0,058 мм;
δ = 360 мкм – допуск на размер детали, обрабатываемый в приспособлении;
Условие выполняется, следовательно, приспособление обеспечивает заданную точность получаемого размера.
9.3. Выявление и расчет размерной цепи приспособления:
1) При соединении корпуса и крышки винтами обеспечивается гарантированный зазор за счет несоосности отверстий под винт в крышке и корпусе. Замыкающим звеном цепи В Δ и назначаем межосевое расстояние отверстий в крышке. Тогда составляющими звеньями цепи будут межосевое расстояние отверстий в корпусе В 1 = 50 мм, а также величины зазоров между осями отверстий в корпусе (В 4; В 5) и осями отверстий в крышке (В 2; В 3).
Рис. 9.2 – эскиз крепления крышки к корпусу приспособления.
2) Уравнение размерной цепи:
Рис. 9.3 – схема размерной цепи.
3) Величину допуска звена B 1 выбираем по табл. 5 с. 24 в зависимости от номинального размера для одиннадцатого квалитета точности. Принимаем δВ 1=0,160 мм.
Звенья В 2, В 3 являются зазорами в соединении вал-отверстие,поэтому допуски на эти звенья устанавливаем с учетом вида посадки этого соединения. Назначаем посадку с гарантированным зазором H 9/ f 9 и выбираем по таблицам предельные отклонения.
|
Н 9: EI = 0 мкм; ES = 30 мкм.
f 9: ei = -40 мкм; es = -10 мкм.
Схема полей допусков представлена на рисунке 4:
Рис. 9.4 - схема полей допусков соединения вал-отверстие.
Из схемы видно, что размеры звеньев будут равны В 2 = В 3 = .
Поля допусков рассчитываем по формуле:
Звенья В 4, В 5 являются зазорами резьбовогосоединения, поэтому допуски на эти звенья устанавливаем с учетом вида посадки этого соединения. Назначаем посадку с гарантированным зазором 6 Н /6 g. По табл. 8,9 с. 27-28 выбираем предельные отклонения наружной и внутренней резьб в зависимости от диаметра и шага резьбы.
6 Н: ES = +150 мкм.
6 g: ei = -206 мкм; es = -26 мкм.
Схема полей допусков этого соединения представлена на рисунке 5:
Рис. 9.5 – схема полей допусков резьбового соединения.
Из схемы видно, что размеры звеньев будут равны В 4 = В 5 = .
Поля допусков рассчитываем по формуле:
4) Находим поле допуска замыкающего звена методом неполной взаимозаменяемости. Примем, что значение процента риска Р = 0,27%, следовательно коэффициент риска t В Δ = 3. Закон распределения размеров близок к закону нормального распределения.
Таким образом, размер межосевого расстояния отверстий в крышке равен:
B Δ = 50±0,25 мм.
Расчет режущего инструмента
Для расчета выбираем фрезу торцовую со вставными ножами для обработки плоской поверхности на операции 015 – карусельно-фрезерная.
Рис. 10.1 – фреза торцовая насадная со вставными ножами.
Конструкцию фрезы рекомендуется выбирать по ГОСТ 24359-80, присоединительные размеры – по ГОСТ 27066-86.
1) Исходные данные:
· Заготовка – отливка;
· Материал заготовки – алюминиевый сплав АК7М2Мг;
· Предел прочности материала заготовки – σв = 300 Мпа;
· Твердость материала заготовки – HB 85;
· Требуемая шероховатость – Ra 5;
· Ширина обрабатываемой поверхности – B = 48 мм;
· Расстояние между оправками – l = 500 мм;
· Общий припуск на обработку – h = 3 мм;
· Глубина резания – t = 3мм;
· Характер обработки – окончательная; торцовое фрезерование плоской поверхности;
· Модель станка – ГФ-2224 С1;
2) Расчет диаметра фрезы:
Диаметр фрезы рассчитываем по формуле:
Выбираем ближайший больший диаметр фрезы из стандартного ряда при знаменателе прогрессии φ = 1,26: [10, стр. 20]
3) Выбор подачи:
Sz = 0,048 мм/зуб; [10, стр. 23, табл. 3.3]
4) Расчет диаметра фрезы под оправку:
M 𝛴– суммарный момент при изгибе и скручивании оправки, Н·м;
𝜎и.д. = 250 МПа – допустимое напряжение на изгиб оправки;[10, стр. 23]
R –равнодействующая сил, Н;
R = 1,41· Pz;
l = 500 мм– расстояние между опорами фрезерной оправки, мм;
Pz – сила резания при фрезеровании, Н;
С p – постоянная, значение берется из справочника;
xp, yp, qp –показатели степени для конкретных условий обработки для каждой из составляющих силы резания;
B –ширина фрезерования, мм;
S –подача на зуб, мм;
z –числозубьев фрезы, принимаем равное 10;
D –наружный диаметр фрезы, мм;
t – глубина резания, мм.
С p = 825; xp = 1,0; yp = 0,75; qp = 1,3;[5, стр. 291]
R = 1,41· 3002 = 4232,9 Н;
Рассчитанное значение диаметра посадочного отверстия округляем до целого и принимаем ближайший диаметр отверстия фрезы по ГОСТ 9472-90:
da = 32мм;
5) Корректировка значения заданного числа зубьев фрезы.
m –коэффициент, зависящий от типа фрезы;
m = 1,05; [10, стр. 24, табл. 3.4]
Принимаем число зубьев z = 12.
6) Определение шага зубьев фрезы.
Окружной шаг:
Осевой шаг:
[10, стр. 25, табл. 3.5]
7) Проверка рассчитанных величин z и на условие равномерного фрезерования.
Процесс фрезерования можно считать равномерным при выполнении следующего условия:
Коэффициент K близок по значению к целому, следовательно, условие выполняется.
8) Выбор шпоночного паза:
По ГОСТ 9472-90 выбираем размеры шпоночного паза:
a, мм | b, мм | c, мм | c1, мм | e, мм | r, мм | r1, мм |
8 | 7 | 27,0-0,2 | 34,8+0,2 | 0,25+0,15 | 1,2-0,3 | 0,25-0,09 |
Рис. 10.2 – геометрические параметры шпоночного паза.
9) Определяем геометрические параметры рабочей части фрезы:
χ = 45°;
χ1 = 45°;
Параметры режущей части ножей фрезы по ГОСТ 24359-80:
α = 12° – главный задний угол;
γ = 3° – передний угол;
φ = 30° – главный угол в плане;
α1 = 18° – вспомогательный задний угол;
λ = 9° – угол наклона главной режущей кромки;
L = 42 мм;
H = 18 мм;
B = 12 мм;
Рис. 10.3 – геометрические параметры ножей.
10) Выбор основных размеров клиньев по ГОСТ 24359-80:
L = 30 мм;
B 1 = 7,2 мм;
H = 15 мм;
Рис. 10.4 – клин.
11) Выбираем материал фрезы:
· корпуса – сталь 40Х;
· ножей – твердый сплав марки BК8;
· клиньев – углеродистая сталь У7.
Назначаем твёрдость деталей фрезы после термической обработки:
· корпуса 30-40 HB;
· режущей части ножей 60-65 HRCЭ;
· клиньев НRCЭ 40-50.
12) Допуски и на основные элементы фрезы и другие технические требования принимаем по ГОСТ 8721 – 69*, предельные отклонения размеров рифлений – по ГОСТ 2568 – 71*.
Заключение
В данном курсовом проекте был разработан технологический процесс механической обработки корпуса воздухораспределителя. Были рассчитаны припуски на обработку данной детали, режимы резания, был произведен расчет приспособления, применяемого в данном технологическом процессе, выявлена и рассчитана размерная цепь, а так же рассчитан и спроектирован металлорежущий инструмент.
В результате выполнения работы организовывалась работа с технологической документацией, с технической литературой и ГОСТами.
Список использованной литературы
1) Курсовое проектирование по технологии машиностроения: Методические указания для студентов специальности «Профессиональное обучение» / Сост. С.И. Моднов. – Ярославль.гос. техн. ун-т. Ярославль, 2007 – 59 с.
2) Косилова А.Г., Мещеряков Р.К., Калинин М.А.: Точность обработки, заготовки и припуски в машиностроении. Справочник технолога. М., «Машиностроение», 1976, 288с. с ил.
3) Расчет припусков и межпереходных размеров в машиностроении: Учеб.пособ. для машиностроит. спец. вузов/ Я.М. Радкевич, В.А. Тимирязев, А.Г. Схиртладзе, М.С. Островский; под ред. В.А. Тимирязева. – М.: Высш. шк., 2004 – 272 с.: ил.
4) Курсовое проектирование по технологии машиностроения: Методические указания для студентов специальности «Профессиональное обучение» / Сост. С.И. Моднов. – Ярославль.гос. техн. ун-т. Ярославль, 1998 – 32 с.
5) Справочник технолога-машиностроителя: В 2-х т. Т.2 / Под ред. А.Г.Косиловой, Р.К.Мещерекова. – М.: Машиностроение, 1986.
6) Н.А. Нефедов, К.А. Осипов. Сборник задач и примеров по резанию металлов и режущему инструменту – М.: Машиностроение, 1990.
7) Станочные приспособления: Справочник. В 2-х т. /Ред. совет: Б.Н. Вардашкин (пред.) и др. – М.: Машиностроение, 1984. – Т. 1 /Под ред. Б.Н. Вардашкина, А.А. Шатилова, 1984. 592 с., ил.
8) Антонюк В.Е., Королев В.А., Башеев С.М.: Справочник конструктора по расчету и проектированию станочных приспособлений. Минск. «Беларусь», 1969. 392 с.
9) Дипломное проектирование по технологии машиностроения: [Учеб.пособие для вузов / В.В. Бабук, П.А. Горезко, К.П. Забродин и др.] Под общ. ред. В.В. Бабука. – Мн.: Выш. школа, 1979. – 464 с., ил.
10) Проектирование и расчет металлорежущего инструмента: Метод. указания и задания /Сост. М.И. Иродов. – Яросл. политехн. ин-т. – Ярославль. 1993. – 40 с.
|
|
Поперечные профили набережных и береговой полосы: На городских территориях берегоукрепление проектируют с учетом технических и экономических требований, но особое значение придают эстетическим...
История развития хранилищ для нефти: Первые склады нефти появились в XVII веке. Они представляли собой землянные ямы-амбара глубиной 4…5 м...
Архитектура электронного правительства: Единая архитектура – это методологический подход при создании системы управления государства, который строится...
Археология об основании Рима: Новые раскопки проясняют и такой острый дискуссионный вопрос, как дата самого возникновения Рима...
© cyberpedia.su 2017-2024 - Не является автором материалов. Исключительное право сохранено за автором текста.
Если вы не хотите, чтобы данный материал был у нас на сайте, перейдите по ссылке: Нарушение авторских прав. Мы поможем в написании вашей работы!