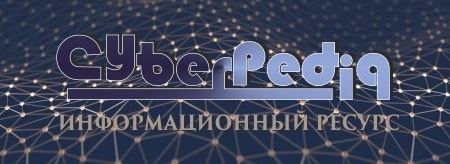
Семя – орган полового размножения и расселения растений: наружи у семян имеется плотный покров – кожура...
Адаптации растений и животных к жизни в горах: Большое значение для жизни организмов в горах имеют степень расчленения, крутизна и экспозиционные различия склонов...
Топ:
Оснащения врачебно-сестринской бригады.
Проблема типологии научных революций: Глобальные научные революции и типы научной рациональности...
Устройство и оснащение процедурного кабинета: Решающая роль в обеспечении правильного лечения пациентов отводится процедурной медсестре...
Интересное:
Средства для ингаляционного наркоза: Наркоз наступает в результате вдыхания (ингаляции) средств, которое осуществляют или с помощью маски...
Уполаживание и террасирование склонов: Если глубина оврага более 5 м необходимо устройство берм. Варианты использования оврагов для градостроительных целей...
Распространение рака на другие отдаленные от желудка органы: Характерных симптомов рака желудка не существует. Выраженные симптомы появляются, когда опухоль...
Дисциплины:
![]() |
![]() |
5.00
из
|
Заказать работу |
Содержание
Введение…………………………………………………………………………………….4
1. Назначение и конструкция детали………………………………………………..…….5
2. Определение типа производства…………………………………………………..……7
3. Анализ технологичности конструкции детали…………………………………..…….9
4. Выбор заготовки………………………………………………………………………..10
5. Анализ существующего технологического процесса…………………………..……12
6. Проектирование технологического процесса и оформление документации……….16
7. Расчет припусков на обработку……………………………………………………….16
8. Расчет режимов резания и технических норм времени……………………………...20
9. Расчет приспособления………………………………………………………………...31
10. Расчет режущего инструмента……………………………………………………...34
Заключение……………………………………………………………………………...…39
Список используемой литературы……………………………………………………….40
Введение
Машиностроение является главным технологом всех отраслей народного хозяйства. В связи с этим оно должно на базе новейших достижений науки и техники непрерывно разрабатывать новые технологические процессы, для осуществления которых нужно создавать и выпускать необходимых народному хозяйству количествах орудия производства и машины, отвечающие своему служебному назначению при наименьшей себестоимости.
Отрасль науки, занимающаяся изучением закономерности, действующих в процессе изготовления машин, с целью использования этих закономерностей для обеспечения требуемого качества машин и наименьшей их себестоимости, называется технологией машиностроения.
Человеку для его существования необходимы материальные и культурные блага. Источниками получения благ являются предметы природы и человеческий труд. Природа предоставляет в распоряжение человека ничтожно малое количество предметов, которые можно использовать непосредственно, без приложения труда человека. Поэтому человеку приходиться почти всегда затрачивать труд, чтобы путем качественного превращения приспосабливать предметы природы для удовлетворения своих потребностей.
Качественно изменение предметов природы, осуществляемое человеком, получило название технологического процесса. Осуществляя технологический процесс, человек ставит перед собой две задачи: 1) получить изделие, которое удовлетворяло бы его потребность; 2) затратить на его изготовление меньше труда.
Каждое изделие может удовлетворять ту или иную потребность человека только в том случае, если оно обладает качеством, которое определяется его назначением. Без надлежащего качества изделие становиться ненужным человеку, а затраченные на его получение труд и предметы природы расходуются бесполезно.
Целью выполнения курсовогопроекта является разработка технологического процесса изготовления корпуса воздухораспределителя.
Задачами курсового проекта являются обобщение и систематизация знаний, полученных при изучении дисциплины «Технология машиностроения», практическое применение знаний, полученных при изучении таких предметов, как «Теория резания», «Металлорежущий инструмент», «Технология конструкционных материалов и материаловедение», «Сопротивление материалов», «Металлорежущие станки». Также задачейкурсового проекта является приобретение навыков и умений самостоятельной работы с государственными стандартами, справочной и научно-технической литературой. Значение этой работы заключается еще и в том, что она помогает подготовиться и получить все необходимые знания для написания дипломной работы и успешной сдачи итоговых экзаменов.
Выбор заготовки
Сущность литейного производства состоит в получении отливок – литых металлических изделий – заливкой жидкого сплава нужного состава в литейную форму. Отливки получают литьем в песчано-глинистые формы или специальными способами литья. Литье в песчано-глинистые формы – основной метод производства отливок. Этим методом получают литые детали, как простой, так и сложной формы, наиболее крупные отливки, которые нельзя получить другими способами. Вместе с тем литье в песчано-глинистые формы имеет и свои недостатки. К ним следует отнести менее высокие механические свойства отливок по сравнению получаемыми специальными методами литья. Кроме того, размерная точность и чистота поверхности отливок, полученных в песчано-глинистых формах, во многих случаях не удовлетворяют современным требованиям машиностроения. Это приводит к необходимости иметь в отливках повышенные припуски на механическую обработку, что удорожает ее, увеличивает расход металла.
К специальным способам относят литье в металлические формы (кокиль), литье под давлением, центробежное литье, литье в оболочковые формы, литье по выплавляемым моделям и многие другие. Указанные способы позволяют получить отливки повышенной точности, с минимальными допусками по размерам с высокой чистотой поверхности. Это сокращает или совсем исключает механическую обработку, давая экономию металла, особенно важную при использовании дорогостоящих и дефицитных сплавов приводит к сокращению парка металлообрабатывающих станков, снижению стоимости детали.
Литье под давлением является одним из специальных способов литья. Этот метод является наиболее производительным для изготовления небольших отливок из цветных сплавов с высокой точностью по размерам и чистотой поверхности. Но этот метод имеет ряд недостатков: высокая стоимость и сложность изготовления пресс-форм, сложность получения отливок со сложными полостями. Отливки имеют газоусадочную пористость и их нельзя подвергать термической обработке. При получении отливок пресс-формы имеют небольшую долговечность. Литье в металлические формы в свою очередь имеет ряд преимуществ перед литьем под давлением. Кокиль является формой многократного использования, в которой можно получить огромное количество отливок из более легкоплавких цветных металлов. Вследствии быстрого затвердевания сплав получает выгодную мелкозернистую структуру, что определяет его высокие механические свойства. Экономически целесообразно применять этот метод в массовом и крупносерийном производстве. Поэтому заготовку изготавливают из алюминиевого сплава АК7М2Мг литьем в кокиль.
Подобный метод обусловлен характеристикой материала детали, конструктивной формой и размерами детали, программой выпуска.
Сущность метода заключается в следующем: расплавленный металл заливается в металлическую форму – кокиль. Массивный кокиль обладает большой теплопроводностью, поэтому скорость кристаллизации расплава велика. Это создаёт мелко зернистую структуру и повышает механические свойства отливки.
Стойкость кокилей составляет от одной до нескольких тысяч отливок. Стоимость самого кокиля довольно высокая, поэтому кокильное литьё экономически целесообразно при серийном и массовом типах производства.
Кокильное литьё экономит металл на 10-20% за счёт сокращения литниковой системы.
В следствии этого трудоёмкость механической обработки уменьшается.
Кокильным литьём изготавливают отливки сравнительно простой конфигурации. Масса отливок от 0,5до 500 кг.
Отливки в кокиль имеют высокую точность размеров (11-12 квалитет), параметр шероховатости поверхности отливок Ra= 5-10 мкм. Все это позволяет в 2-3 раза уменьшить припуски на обработку резанием. У отливок отпадает необходимость обработки большинства поверхностей. Для отливок в кокиль характерна более плотная мелкозернистая структура металла, что способствует повышению их механических свойств на 15-30 %.
К заготовкам, отливаемым в кокиль, предъявляют определенные требования. Для легкости извлечения отливки из формы ее конфигурация должна иметь по возможности меньше выступающих элементов и уклоны в сторону плоскости разъема. Для создания условий нормального заполнения формы толщина стенок отливок у заготовок из цветных сплавов должна быть не менее 3-6 мм. Отливки не должны иметь резких утолщений, ребра необходимо располагать перпендикулярно к плоскости разъема.
Поверхности отливки, используемые в качестве баз для обработки резанием или разметки, следует располагать в одной части кокиля. Эти поверхности не должны лежать в плоскости разъема.
Таким образом, литье в кокиль является наиболее оптимальным (экономичным) по сравнению с литьем под давлением, литьем в оболочковые формы, а также литьем по выплавляемым моделям.
Расчет приспособления
Выполним расчет приспособления для закрепления заготовки на вертикально-сверлильном станке модели 2Н125. Операция 050 – вертикально-сверлильная.
9.1. Силовой расчет приспособления:
1) Определяем крутящий момент:
Для расчета силы закрепления заготовки выбираем наибольший крутящий момент на данной операции:
M кр = 17,4Н·м;
2) Определяем силу закрепления заготовки:
Рис. 9.1 – схема зажима.
f = 0,25 – коэффициент трения в месте контакта прихвата и заготовки; [8, стр. 17]
l = 0,04м;
K = K 0· K 1· K 2· K 3· K 4· K 5– коэффициент запаса; [8, стр. 7]
K 0 = 1,5 – гарантированный коэффициент запаса; [8, стр. 7]
K 1 = 1 – коэффициент, учитывающий состояние поверхности заготовки; [8, стр. 7]
K 2 = 1,15 – коэффициент, учитывающий увеличение сил резания вследствие затупления инструмента; [8, стр. 7, табл. 1]
K 3 = 1 – коэффициент, учитывающий увеличения сил резания при прерывистом резании; [8, стр. 7]
К 4 = 1 – коэффициент, характеризующий постоянство силы, развиваемой зажимным механизмом, при использовании пневматического зажимного механизма двустороннего действия; [8, стр. 7]
K 5 = 1,5 – коэффициент, учитываемый при наличии крутящего момента; [8, стр. 7]
K = 1,5·1·1,15·1·1·1,5 = 2,59;
3) Выбираем пневмопривод, т. к. он имеет следующие преимущества перед гидроприводом:
- отсутствует специальный источник давления, так как линии сжатого воздуха имеются на большинстве заводов;
- нет возвратных трубопроводов, так как отработанный воздух выпускают в окружающую среду;
- простые аппаратура и арматура.
Определяем диаметр пневмоцилиндра:
p = 0,63 МПа – избыточное давление сжатого воздуха;
Выбираем стандартное значение D = 100 мм. [7, стр. 433, табл. 8]
Выбираем встроенный пневмоцилиндр: обозначение 7020-0209 исполнение 1 ГОСТ 15608-81.
9.2. Расчет приспособления на точность:
Для обеспечения необходимой точности обрабатываемой детали должно соблюдаться условие:
Погрешность установки заготовки на выполняемой операции или переходе определяется по формуле:
ε з = 0,05 мм – погрешность закрепления; [9, стр. 145, табл. 3.24]
ε пр = 0,05 мм – погрешность положения заготовки, которая является следствием неточности изготовления приспособления и износа его базирующих элементов; [9, стр. 133]
Погрешность базирования равна допуску на размер базирующего отверстия:
ε б = 0,058 мм;
δ = 360 мкм – допуск на размер детали, обрабатываемый в приспособлении;
Условие выполняется, следовательно, приспособление обеспечивает заданную точность получаемого размера.
9.3. Выявление и расчет размерной цепи приспособления:
1) При соединении корпуса и крышки винтами обеспечивается гарантированный зазор за счет несоосности отверстий под винт в крышке и корпусе. Замыкающим звеном цепи В Δ и назначаем межосевое расстояние отверстий в крышке. Тогда составляющими звеньями цепи будут межосевое расстояние отверстий в корпусе В 1 = 50 мм, а также величины зазоров между осями отверстий в корпусе (В 4; В 5) и осями отверстий в крышке (В 2; В 3).
Рис. 9.2 – эскиз крепления крышки к корпусу приспособления.
2) Уравнение размерной цепи:
Рис. 9.3 – схема размерной цепи.
3) Величину допуска звена B 1 выбираем по табл. 5 с. 24 в зависимости от номинального размера для одиннадцатого квалитета точности. Принимаем δВ 1=0,160 мм.
Звенья В 2, В 3 являются зазорами в соединении вал-отверстие,поэтому допуски на эти звенья устанавливаем с учетом вида посадки этого соединения. Назначаем посадку с гарантированным зазором H 9/ f 9 и выбираем по таблицам предельные отклонения.
Н 9: EI = 0 мкм; ES = 30 мкм.
f 9: ei = -40 мкм; es = -10 мкм.
Схема полей допусков представлена на рисунке 4:
Рис. 9.4 - схема полей допусков соединения вал-отверстие.
Из схемы видно, что размеры звеньев будут равны В 2 = В 3 = .
Поля допусков рассчитываем по формуле:
Звенья В 4, В 5 являются зазорами резьбовогосоединения, поэтому допуски на эти звенья устанавливаем с учетом вида посадки этого соединения. Назначаем посадку с гарантированным зазором 6 Н /6 g. По табл. 8,9 с. 27-28 выбираем предельные отклонения наружной и внутренней резьб в зависимости от диаметра и шага резьбы.
6 Н: ES = +150 мкм.
6 g: ei = -206 мкм; es = -26 мкм.
Схема полей допусков этого соединения представлена на рисунке 5:
Рис. 9.5 – схема полей допусков резьбового соединения.
Из схемы видно, что размеры звеньев будут равны В 4 = В 5 = .
Поля допусков рассчитываем по формуле:
4) Находим поле допуска замыкающего звена методом неполной взаимозаменяемости. Примем, что значение процента риска Р = 0,27%, следовательно коэффициент риска t В Δ = 3. Закон распределения размеров близок к закону нормального распределения.
Таким образом, размер межосевого расстояния отверстий в крышке равен:
B Δ = 50±0,25 мм.
Расчет режущего инструмента
Для расчета выбираем фрезу торцовую со вставными ножами для обработки плоской поверхности на операции 015 – карусельно-фрезерная.
Рис. 10.1 – фреза торцовая насадная со вставными ножами.
Конструкцию фрезы рекомендуется выбирать по ГОСТ 24359-80, присоединительные размеры – по ГОСТ 27066-86.
1) Исходные данные:
· Заготовка – отливка;
· Материал заготовки – алюминиевый сплав АК7М2Мг;
· Предел прочности материала заготовки – σв = 300 Мпа;
· Твердость материала заготовки – HB 85;
· Требуемая шероховатость – Ra 5;
· Ширина обрабатываемой поверхности – B = 48 мм;
· Расстояние между оправками – l = 500 мм;
· Общий припуск на обработку – h = 3 мм;
· Глубина резания – t = 3мм;
· Характер обработки – окончательная; торцовое фрезерование плоской поверхности;
· Модель станка – ГФ-2224 С1;
2) Расчет диаметра фрезы:
Диаметр фрезы рассчитываем по формуле:
Выбираем ближайший больший диаметр фрезы из стандартного ряда при знаменателе прогрессии φ = 1,26: [10, стр. 20]
3) Выбор подачи:
Sz = 0,048 мм/зуб; [10, стр. 23, табл. 3.3]
4) Расчет диаметра фрезы под оправку:
M 𝛴– суммарный момент при изгибе и скручивании оправки, Н·м;
𝜎и.д. = 250 МПа – допустимое напряжение на изгиб оправки;[10, стр. 23]
R –равнодействующая сил, Н;
R = 1,41· Pz;
l = 500 мм– расстояние между опорами фрезерной оправки, мм;
Pz – сила резания при фрезеровании, Н;
С p – постоянная, значение берется из справочника;
xp, yp, qp –показатели степени для конкретных условий обработки для каждой из составляющих силы резания;
B –ширина фрезерования, мм;
S –подача на зуб, мм;
z –числозубьев фрезы, принимаем равное 10;
D –наружный диаметр фрезы, мм;
t – глубина резания, мм.
С p = 825; xp = 1,0; yp = 0,75; qp = 1,3;[5, стр. 291]
R = 1,41· 3002 = 4232,9 Н;
Рассчитанное значение диаметра посадочного отверстия округляем до целого и принимаем ближайший диаметр отверстия фрезы по ГОСТ 9472-90:
da = 32мм;
5) Корректировка значения заданного числа зубьев фрезы.
m –коэффициент, зависящий от типа фрезы;
m = 1,05; [10, стр. 24, табл. 3.4]
Принимаем число зубьев z = 12.
6) Определение шага зубьев фрезы.
Окружной шаг:
Осевой шаг:
[10, стр. 25, табл. 3.5]
7) Проверка рассчитанных величин z и на условие равномерного фрезерования.
Процесс фрезерования можно считать равномерным при выполнении следующего условия:
Коэффициент K близок по значению к целому, следовательно, условие выполняется.
8) Выбор шпоночного паза:
По ГОСТ 9472-90 выбираем размеры шпоночного паза:
a, мм | b, мм | c, мм | c1, мм | e, мм | r, мм | r1, мм |
8 | 7 | 27,0-0,2 | 34,8+0,2 | 0,25+0,15 | 1,2-0,3 | 0,25-0,09 |
Рис. 10.2 – геометрические параметры шпоночного паза.
9) Определяем геометрические параметры рабочей части фрезы:
χ = 45°;
χ1 = 45°;
Параметры режущей части ножей фрезы по ГОСТ 24359-80:
α = 12° – главный задний угол;
γ = 3° – передний угол;
φ = 30° – главный угол в плане;
α1 = 18° – вспомогательный задний угол;
λ = 9° – угол наклона главной режущей кромки;
L = 42 мм;
H = 18 мм;
B = 12 мм;
Рис. 10.3 – геометрические параметры ножей.
10) Выбор основных размеров клиньев по ГОСТ 24359-80:
L = 30 мм;
B 1 = 7,2 мм;
H = 15 мм;
Рис. 10.4 – клин.
11) Выбираем материал фрезы:
· корпуса – сталь 40Х;
· ножей – твердый сплав марки BК8;
· клиньев – углеродистая сталь У7.
Назначаем твёрдость деталей фрезы после термической обработки:
· корпуса 30-40 HB;
· режущей части ножей 60-65 HRCЭ;
· клиньев НRCЭ 40-50.
12) Допуски и на основные элементы фрезы и другие технические требования принимаем по ГОСТ 8721 – 69*, предельные отклонения размеров рифлений – по ГОСТ 2568 – 71*.
Заключение
В данном курсовом проекте был разработан технологический процесс механической обработки корпуса воздухораспределителя. Были рассчитаны припуски на обработку данной детали, режимы резания, был произведен расчет приспособления, применяемого в данном технологическом процессе, выявлена и рассчитана размерная цепь, а так же рассчитан и спроектирован металлорежущий инструмент.
В результате выполнения работы организовывалась работа с технологической документацией, с технической литературой и ГОСТами.
Список использованной литературы
1) Курсовое проектирование по технологии машиностроения: Методические указания для студентов специальности «Профессиональное обучение» / Сост. С.И. Моднов. – Ярославль.гос. техн. ун-т. Ярославль, 2007 – 59 с.
2) Косилова А.Г., Мещеряков Р.К., Калинин М.А.: Точность обработки, заготовки и припуски в машиностроении. Справочник технолога. М., «Машиностроение», 1976, 288с. с ил.
3) Расчет припусков и межпереходных размеров в машиностроении: Учеб.пособ. для машиностроит. спец. вузов/ Я.М. Радкевич, В.А. Тимирязев, А.Г. Схиртладзе, М.С. Островский; под ред. В.А. Тимирязева. – М.: Высш. шк., 2004 – 272 с.: ил.
4) Курсовое проектирование по технологии машиностроения: Методические указания для студентов специальности «Профессиональное обучение» / Сост. С.И. Моднов. – Ярославль.гос. техн. ун-т. Ярославль, 1998 – 32 с.
5) Справочник технолога-машиностроителя: В 2-х т. Т.2 / Под ред. А.Г.Косиловой, Р.К.Мещерекова. – М.: Машиностроение, 1986.
6) Н.А. Нефедов, К.А. Осипов. Сборник задач и примеров по резанию металлов и режущему инструменту – М.: Машиностроение, 1990.
7) Станочные приспособления: Справочник. В 2-х т. /Ред. совет: Б.Н. Вардашкин (пред.) и др. – М.: Машиностроение, 1984. – Т. 1 /Под ред. Б.Н. Вардашкина, А.А. Шатилова, 1984. 592 с., ил.
8) Антонюк В.Е., Королев В.А., Башеев С.М.: Справочник конструктора по расчету и проектированию станочных приспособлений. Минск. «Беларусь», 1969. 392 с.
9) Дипломное проектирование по технологии машиностроения: [Учеб.пособие для вузов / В.В. Бабук, П.А. Горезко, К.П. Забродин и др.] Под общ. ред. В.В. Бабука. – Мн.: Выш. школа, 1979. – 464 с., ил.
10) Проектирование и расчет металлорежущего инструмента: Метод. указания и задания /Сост. М.И. Иродов. – Яросл. политехн. ин-т. – Ярославль. 1993. – 40 с.
Содержание
Введение…………………………………………………………………………………….4
1. Назначение и конструкция детали………………………………………………..…….5
2. Определение типа производства…………………………………………………..……7
3. Анализ технологичности конструкции детали…………………………………..…….9
4. Выбор заготовки………………………………………………………………………..10
5. Анализ существующего технологического процесса…………………………..……12
6. Проектирование технологического процесса и оформление документации……….16
7. Расчет припусков на обработку……………………………………………………….16
8. Расчет режимов резания и технических норм времени……………………………...20
9. Расчет приспособления………………………………………………………………...31
10. Расчет режущего инструмента……………………………………………………...34
Заключение……………………………………………………………………………...…39
Список используемой литературы……………………………………………………….40
Введение
Машиностроение является главным технологом всех отраслей народного хозяйства. В связи с этим оно должно на базе новейших достижений науки и техники непрерывно разрабатывать новые технологические процессы, для осуществления которых нужно создавать и выпускать необходимых народному хозяйству количествах орудия производства и машины, отвечающие своему служебному назначению при наименьшей себестоимости.
Отрасль науки, занимающаяся изучением закономерности, действующих в процессе изготовления машин, с целью использования этих закономерностей для обеспечения требуемого качества машин и наименьшей их себестоимости, называется технологией машиностроения.
Человеку для его существования необходимы материальные и культурные блага. Источниками получения благ являются предметы природы и человеческий труд. Природа предоставляет в распоряжение человека ничтожно малое количество предметов, которые можно использовать непосредственно, без приложения труда человека. Поэтому человеку приходиться почти всегда затрачивать труд, чтобы путем качественного превращения приспосабливать предметы природы для удовлетворения своих потребностей.
Качественно изменение предметов природы, осуществляемое человеком, получило название технологического процесса. Осуществляя технологический процесс, человек ставит перед собой две задачи: 1) получить изделие, которое удовлетворяло бы его потребность; 2) затратить на его изготовление меньше труда.
Каждое изделие может удовлетворять ту или иную потребность человека только в том случае, если оно обладает качеством, которое определяется его назначением. Без надлежащего качества изделие становиться ненужным человеку, а затраченные на его получение труд и предметы природы расходуются бесполезно.
Целью выполнения курсовогопроекта является разработка технологического процесса изготовления корпуса воздухораспределителя.
Задачами курсового проекта являются обобщение и систематизация знаний, полученных при изучении дисциплины «Технология машиностроения», практическое применение знаний, полученных при изучении таких предметов, как «Теория резания», «Металлорежущий инструмент», «Технология конструкционных материалов и материаловедение», «Сопротивление материалов», «Металлорежущие станки». Также задачейкурсового проекта является приобретение навыков и умений самостоятельной работы с государственными стандартами, справочной и научно-технической литературой. Значение этой работы заключается еще и в том, что она помогает подготовиться и получить все необходимые знания для написания дипломной работы и успешной сдачи итоговых экзаменов.
Назначение и конструкция детали
В коробках передач за счет работы воздухораспределителя осуществляется управление демультипликатором. Конструкция воздухораспределителя показана на Рис. 1.1.
Рис. 1.1 – Устройство воздухораспределителя.
1 – корпус воздухораспределителя;
2 – золотник;
3 – клапан впускной в сборе;
4 – сапун в сборе;
5 – шайба упорная;
6 – ввертыш (4 шт.);
7 – кольцо уплотнительное;
8 – цилиндр(2 шт.);
9 – прокладка цилиндра (2 шт.);
10 – поршень (2 шт.);
11 – кольцо уплотнительное (2 шт.);
12 – пружина толкателя;
13 – пружина клапана впускного;
14 – толкатель;
15 – крышка клапана;
16 – втулка толкателя центрирующая;
17 – прокладка крышки клапана;
18 – диафрагма толкателя в сборе;
19 – шайба упорная (2 шт);
20 – шайба (4 шт.);
21 – болт М6.1.20 (11 шт.);
22 – шайба 6 (8 шт.);
23 – шайба 6Т (11 шт.);
24 – гнездо золотника;
25 – кольцо уплотнительное;
26 – корпус впускного клапана;
27 – кольцо уплотнительное;
28 – кольцо уплотнительное золотника (2 шт.);
Управление демультипликатором состоит из воздушного силового цилиндра, поршень которого воздействует через шток на вилку и коронную шестерню, а так же системы подачи воздуха в разные полости цилиндра.
Система подачи воздуха в цилиндр управления демультипликатором состоит из крана переключения демультипликатора (установленного на рычаге переключения передач или на панели кабины), воздухораспределителя, подсоединенного к крышке (корпусу) механизма переключения передач, электромагнитного клапана блокировки, электронного реле, электронного датчика частоты вращения вала демультипликатора коробки передач и, соответственно, фланца, который соединяется с карданным валом транспортного средства, воздухопроводов, электропроводов. Работоспособность системы обеспечения воздухом обеспечивается за счет соединения с воздушным ресивером транспортного средства.
Воздухораспределитель состоит собственно из корпуса воздухораспределителя 1 с золотником 2, с воздушными цилиндрами 8, поршнями 10 и пневмомеханического устройства блокировки включения диапазонов демультипликатора.
Корпус является составной частью воздухораспределителя многоступенчатых коробок передач и служит для управления переключением демультипликатора за счет сжатого воздуха.
Корпус крепится к коробке передач двумя болтами с помощью фланца с отверстиями Ø9 мм. Между коробкой передач и корпусом воздухораспределителя при сборке устанавливается картонная прокладка.
Воздух к корпусу подводится через крышку, которая через прокладку крепится болтами к треугольному фланцу.
Воздух через систему клапанов, каналов золотниковые устройства подается по воздухопроводам в полости цилиндра переключения. В отверстия отвода воздуха устанавливаются стальные ввертыши во избежание срыва резьбы при затяжке болтов крепления воздухопроводов.
В корпусе имеется отверстие с конической резьбой, в которое устанавливается сапун для отвода отработавшего воздуха.
Многоступенчатое поперечное отверстие служит для размещения седла впускного клапана и ряда других деталей; для обеспечения их необходимой работоспособности заданы требования соосности, биения базовых поверхностей, неперпендикулярности торца, примыкающего к коробке передач.
В продольном направлении корпус имеет отверстия для запрессовки гнезд золотника, а так же расточки для установки цилиндров управления. Цилиндр крепится четырьмя болтами, стык уплотняется прокладками.
Все резьбовые отверстия для обеспечения собираемости заданы с позиционным допуском.
В верхней части корпуса имеется технологическое отверстие, которое при сборке заглушается штифтом.
Для повышения удобства сборки узла в корпусе имеются отверстия Ø3 мм.
Условия работы узла:
- рабочая температура до 100°С;
- давление воздуха до 0,5 МПа;
- смазка трущихся поверхностей смазкой «Литол 24».
Качество изготовления детали – отливка должна быть плотной, герметичной, на обработанных поверхностях детали не допускаются усадочные раковины и другие литейные дефекты.
Таблица 1.1 – Химический состав сплава
Таблица 1.1 – химический состав сплава.
Марка Сплава | Химический состав, % (по массе), остальное алюминий | Плотность, г/см3 | |||||||||
Cu | Mn | Mg | Si | Fe | Zn | Cr | Ti | Прочие | |||
отдельно | вместе | ||||||||||
АК7М2Мг | <0.1 | 0.6-1 | 4-4.9 | <0.4 | <0.4 | <0.2 | 0.05-0.25 | <0.1 | <0.05 | <0.15 | 2.66 |
Характерные свойства сплава: сплав устойчив к морской воде, обладает хорошей химической и коррозионной устойчивостью к погодным условиям, хорошими свойствами при повышенных и очень низких температурах, хорошо сваривается.
Сплав применяется в химических аппаратах, технике для низких температур, пищевой промышленности, строительстве, солеварении, автомобилестроении, машиностроении, строительстве резервуаров, изоляционной обшивке.
Таблица 1.2 –физические свойства сплава.
Марка сплава | Предел прочности sв, МПа | Предел текучести sт, МПа | Удлинение, % | Твердость НВ | Область затвердевания, | |||
d5 | d10 | °С | К | |||||
АК7М2Мг | 300 | 210 | 12 | 10 | 85 | 575-640 | 848-913 | |
Электропроводность c, | Теплопроводность l, | Коэффициент термического расширения при 20-100 °С | ||||||
16-19 | 1,1-1,2 | 23,7 | ||||||
Стоимость алюминиевого сплава АК7М2Мг: 81 руб/кг.
Кормораздатчик мобильный электрифицированный: схема и процесс работы устройства...
Биохимия спиртового брожения: Основу технологии получения пива составляет спиртовое брожение, - при котором сахар превращается...
Типы оградительных сооружений в морском порту: По расположению оградительных сооружений в плане различают волноломы, обе оконечности...
История развития пистолетов-пулеметов: Предпосылкой для возникновения пистолетов-пулеметов послужила давняя тенденция тяготения винтовок...
© cyberpedia.su 2017-2024 - Не является автором материалов. Исключительное право сохранено за автором текста.
Если вы не хотите, чтобы данный материал был у нас на сайте, перейдите по ссылке: Нарушение авторских прав. Мы поможем в написании вашей работы!