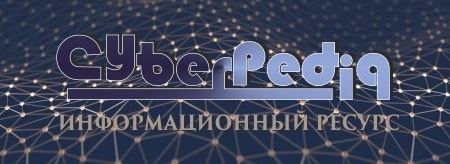
Индивидуальные очистные сооружения: К классу индивидуальных очистных сооружений относят сооружения, пропускная способность которых...
Археология об основании Рима: Новые раскопки проясняют и такой острый дискуссионный вопрос, как дата самого возникновения Рима...
Топ:
Техника безопасности при работе на пароконвектомате: К обслуживанию пароконвектомата допускаются лица, прошедшие технический минимум по эксплуатации оборудования...
Комплексной системы оценки состояния охраны труда на производственном объекте (КСОТ-П): Цели и задачи Комплексной системы оценки состояния охраны труда и определению факторов рисков по охране труда...
Установка замедленного коксования: Чем выше температура и ниже давление, тем место разрыва углеродной цепи всё больше смещается к её концу и значительно возрастает...
Интересное:
Берегоукрепление оползневых склонов: На прибрежных склонах основной причиной развития оползневых процессов является подмыв водами рек естественных склонов...
Что нужно делать при лейкемии: Прежде всего, необходимо выяснить, не страдаете ли вы каким-либо душевным недугом...
Отражение на счетах бухгалтерского учета процесса приобретения: Процесс заготовления представляет систему экономических событий, включающих приобретение организацией у поставщиков сырья...
Дисциплины:
![]() |
![]() |
5.00
из
|
Заказать работу |
|
|
Обжиг анодов сопровождается сложными физико-химическими процессами, происходящими в пекококсовых композициях в результате размягчения, дистилляции и коксования связующего. На начальной стадии нагревания «зеленых» анодов пековая фаза размягчается, а затем переходит в жидкое состояние. Пек остается жидким до момента спекания, т. е. до 400—450 °С.
В начальной стадии обжига завершаются процессы смачивания и пропитки (до 400 °С), которые не нашли полного развития в ходе смешения массы и виброуплотнения «зеленых» блоков. Однако капиллярные явления не являются единственными в ходе уплотнения анодного блока. При повышении температуры нагрева связующее подвергается усиленной дистилляции с выделением ароматических смол и непредельных углеводородов, происходит так называемый процесс «залечивания» труднодоступных пор в кресталическом теле.
На ранней стадии обжига наблюдается припекание пека к наполнителю с образованием общего каркаса блока.
.
Имеют место два механизма образования и развития контактного взаимодействия наполнителя и кокса из связующего:
Во-первых, взаимное сращивание путем механического заклинивания зерен наполнителя коксом из связующего. При таком механизме спекания отдельные компоненты системы сохраняют структурную индивидуальность, т. е. граница между ними сохраняется и с ней сохраняется понятие «контакт». Последующее уплотнение межзернового граничного слоя происходит в результате массопереноса в парогазовой фазе и отложения пиролитического углерода между зернами.
Во-вторых, химическое взаимодействие связующего с поверхностью кокса с образованием устойчивых химических связей и элементов общей кристаллической структуры пека и наполнителя.
|
Их структурная перестройка преобразований завершается при максимальной температуре обжига, т. е. при 1050—1100 °С образованием сплошной структурной решетки углерода.
Структурные превращения при спекании анода происходят не только на границе матрица-наполнитель, но и в объеме пленки связующего. Интенсивные превращения в каменноугольном пеке с выделением летучих веществ начинаются при температуре порядка 300 °С, что соответствует началу процессов молекулярной перестройки, сопровождающейся удалением продуктов разложения. При термическом разложении ароматических углеводородов в осколках молекул появляются ненасыщенные силы притяжения, которые при сближении обусловливают образование новых, более тяжелых молекул и ускоряют процесс дальнейшей молекулярной ассоциации. Последующее увеличение температуры приводит к активации реакций более высокого энергетического уровня и к образованию еще более тяжелых макромолекул.
Эти процессы в прослойках связующего происходят в интервале температур 300—500 °С, причем наиболее интенсивно при 450 °С и заканчиваются при 500—550 °С образованием полукокса. Дальнейшее изменение молекулярной структуры пека происходит в направлении упорядочения кристаллической решетки образующегося полукокса.
Совокупность процессов образования полукокса сводится к первоначальному образованию плоских макромолекул, основными структурными элементами которых являются правильные гексогональные ячейки преимущественно с атомами водорода или -СНn группами на углах (Рис 8.1)
Таким образом, формирование первоначальной структурной сетки полукокса связано одновременно с расщеплением (крекингом) ароматических углеводородов и ассоциаций (конденсацией) образовавшихся осколков в плоскую сетку. Формирование плоских макромолекул завершается до температуры 500—550 °С. дальнейшие превращения происходят уже в твердой фазе и выражаются в переходе структуры полукокса в кокс.
|
Переход полукокса в кокс означает ориентацию, упорядочение и наслоение гексогональных сеток в обьемные кристаллы, т.е рост толщины кристаллов и формирование графитообразной структуры.
При коксовании связующего образуется значительное количество смол и газов (метана и этана) которые подвергаются вторичному пирогинетическому разложению. Продуктами пиролиза являются элементарный углерод и водород
Углерод, образующийся в результате пирогенетических процессов, активно участвует в заполнении свободных пор и «залечивании» вакансий, повышая структурную плотность решетки углерода. Полнота использования пиролитического углерода напрямую зависит от скорости нагревания обжигаемого изделия, особенно на стадии интенсивного выделения парогазовой фазы. При замедленном нагреве процессы пирогенетического разложения углеводородов успевают полностью завершиться, а пиролитический углерод отложиться в порах и пустотах обжигаемого изделия. При высоких температурах (>750 ОС), когда в газообразных продуктах коксования начинает преобладать водород, количество выделенного пиролитического углерода резко снижается, а к концу обжига прекращается полностью.
Температурный режим обжига
Процесс обжига/спекания «зеленых» анодных блоков условно можно разделить на следующие стадии:
1-я — до 120 °С; предварительный нагрев «зеленых» блоков, который сопровождается релаксацией (ослаблением) имеющихся механических напряжений в структуре, размягчением пека и дистилляцией влаги.
2-я — 120—350 0С; термические преобразования в пеке и пекококсовой смеси, связанные с реакциями разложения органических соединений.
3-я — 350—600 0С; коксование связующего и начало спекания пекококсовой композиции.
4-я — 600—1100 °С; физико-химические преобразования, направленные на упорядочение структуры обожженного анода.
Разработка рационального температурного графика обжига, т. е. оптимального темпа подъема температуры на каждой из 4 стадий обжига является важным условием получения высокого качества обожженных анодов при минимальных энергетических затратах.
.
Темп нагрева в пределах 0—800 о С в среднем должен быть 9,5 оС/ч. При этом в зоне 0—350 оС темп нагрева 6—6,5 о С/ч.
Темп подъема температуры в интервале 800—1100 оС как и темп охлаждения обожженных анодов не лимитируется так строго, как зона предварительного нагрева. Тем не менее превышение этого показателя более 20 оС/ч также недопустимо, так как слишком интенсивный нагрев или охлаждение могут вызвать опасные локальные температурные напряжения в анодах и их растрескивание. Оптимальное значение конечной температуры обжига 1050—1100°С, причем сдвиг в сторону1100°С является предпочтительным
|
|
Опора деревянной одностоечной и способы укрепление угловых опор: Опоры ВЛ - конструкции, предназначенные для поддерживания проводов на необходимой высоте над землей, водой...
Адаптации растений и животных к жизни в горах: Большое значение для жизни организмов в горах имеют степень расчленения, крутизна и экспозиционные различия склонов...
Состав сооружений: решетки и песколовки: Решетки – это первое устройство в схеме очистных сооружений. Они представляют...
Архитектура электронного правительства: Единая архитектура – это методологический подход при создании системы управления государства, который строится...
© cyberpedia.su 2017-2024 - Не является автором материалов. Исключительное право сохранено за автором текста.
Если вы не хотите, чтобы данный материал был у нас на сайте, перейдите по ссылке: Нарушение авторских прав. Мы поможем в написании вашей работы!