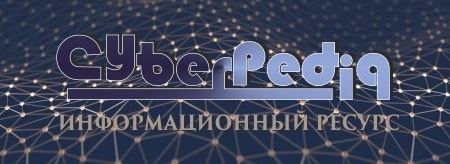
Наброски и зарисовки растений, плодов, цветов: Освоить конструктивное построение структуры дерева через зарисовки отдельных деревьев, группы деревьев...
Папиллярные узоры пальцев рук - маркер спортивных способностей: дерматоглифические признаки формируются на 3-5 месяце беременности, не изменяются в течение жизни...
Топ:
Характеристика АТП и сварочно-жестяницкого участка: Транспорт в настоящее время является одной из важнейших отраслей народного...
Процедура выполнения команд. Рабочий цикл процессора: Функционирование процессора в основном состоит из повторяющихся рабочих циклов, каждый из которых соответствует...
Выпускная квалификационная работа: Основная часть ВКР, как правило, состоит из двух-трех глав, каждая из которых, в свою очередь...
Интересное:
Аура как энергетическое поле: многослойную ауру человека можно представить себе подобным...
Что нужно делать при лейкемии: Прежде всего, необходимо выяснить, не страдаете ли вы каким-либо душевным недугом...
Финансовый рынок и его значение в управлении денежными потоками на современном этапе: любому предприятию для расширения производства и увеличения прибыли нужны...
Дисциплины:
![]() |
![]() |
5.00
из
|
Заказать работу |
|
|
Раздел 8. Обжиг «зеленых» анодных блоков
Обжиг «зеленых» анодных блоков является завершающей стадией производства угольных анодов для алюминиевых электролизеров,
при этом пекококсовая масса превращается в монолитный электрод.
Обжиг «зеленых» анодных блоков и формирование самообжигающегося анода непосредственно на электролизере имеют близкий по своей сущности механизм. В обоих случаях происходят замедленное спекание связующего и формирование структуры анода. Однако при обжиге «зеленых» блоков удается сохранить первоначальную структуру анода, заложенную при смешении и виброформовании. У самообжигающихся анодов, не удается избежать заметной сендиминтации жидкой фазы и нарушения заданной структуры анода, что приводит к снижению качества анода. Повышенное содержание связующего приводит к снижению плотности, пористости и повышению окисляемости при электролизе. Обжиг анодов можно проводить на любых печах, при условии выдержки графика обжига,создания восстановительной или нейтральной атмосферы для предотвращения окисления анода. На практике обжиг анодов проводится исключительно в кольцевых камерных печах открытого или закрытого типа. Именно на печах этого типа достигаются большая производительность, максимальная экономия топлива и наилучшие технологические результаты обжига, включая хорошее качество обожженных анодов.
Температурный режим обжига
Процесс обжига/спекания «зеленых» анодных блоков условно можно разделить на следующие стадии:
1-я — до 120 °С; предварительный нагрев «зеленых» блоков, который сопровождается релаксацией (ослаблением) имеющихся механических напряжений в структуре, размягчением пека и дистилляцией влаги.
|
2-я — 120—350 0С; термические преобразования в пеке и пекококсовой смеси, связанные с реакциями разложения органических соединений.
3-я — 350—600 0С; коксование связующего и начало спекания пекококсовой композиции.
4-я — 600—1100 °С; физико-химические преобразования, направленные на упорядочение структуры обожженного анода.
Разработка рационального температурного графика обжига, т. е. оптимального темпа подъема температуры на каждой из 4 стадий обжига является важным условием получения высокого качества обожженных анодов при минимальных энергетических затратах.
.
Темп нагрева в пределах 0—800 о С в среднем должен быть 9,5 оС/ч. При этом в зоне 0—350 оС темп нагрева 6—6,5 о С/ч.
Темп подъема температуры в интервале 800—1100 оС как и темп охлаждения обожженных анодов не лимитируется так строго, как зона предварительного нагрева. Тем не менее превышение этого показателя более 20 оС/ч также недопустимо, так как слишком интенсивный нагрев или охлаждение могут вызвать опасные локальные температурные напряжения в анодах и их растрескивание. Оптимальное значение конечной температуры обжига 1050—1100°С, причем сдвиг в сторону1100°С является предпочтительным
Футеровка печи обжига
Вся печь размещается в бетонном каркасе, представляющем собой прямоугольную форму, механически удерживающую внутреннюю футеровку печи. Каркас может быть установлен на нулевой отметке или слегка заглублен в землю. Полное заглубление печи обжига удорожает строительство, а при капитальном ремонте, проводимом каждые 12—15 лет, затрудняет демонтажные и монтажные работы.
В бетонном каркасе выкладывается внутренняя футеровка печи. Футеровка состоит из огнеупорной и теплоизоляционной частей. Теплоизоляционная футеровка устанавливается со стороны стенок и днища бетонного каркаса и исполняется в виде двухслойной стенки, сначала из довольно широкого круга материалов (диатомита, керамзитобетона, силикаткальциевых плит) – только для обеспечения теплоизоляции, затем из шамотного легковеса с повышенной пористостью и огнеупорностью.
|
Рабочая зона печи несет основную термическую нагрузку и выполняется из высококачественных муллитовых огнеупоров и жаростойких бетонов,
Основные нагрузки на футеровку в печах обжига:
- в течение одного технологического цикла футеровка нагревается до температуры 1200 °С и принудительно охлаждается до температуры наружного воздуха;
- смена атмосферы в печи от восстановительной при нагреве печи до окислительной при продувке простенков атмосферным воздухом;
-механическое воздействие при загрузке и разгрузке кассет.
.
.
Организация работы печи
Многокамерные печи открытого типа состоят из большого количества камер. Камеры группируются по числу огней. На рисунке 8.35 представлена организация работ на многокамерной печи.
В камерах 4,5,6 установлены горелочные рампы с подключением всех простенков на сжигание топлива. Камера 4или первая обогреваемая камера по ходу огня, составляет зону форсированного нагрева, температура в ней поднимается с800 до12000С. Камеры 5,6 называется зона «полного огня», температура газа в огневых каналах этих камер составляет 1200-12500С и поддерживается постоянной. Принято говорить, камеры4,5,6 находятся «на огне».
Продукты сгорания топлива под воздействием разряжения, создаваемого эксгаустером, проходят через простенки камер №1,2,3 и передают тепло загруженным «зеленым» анодам, в эксгаустер попадает газ охлажденный до 160-2000С. Камеры №1,2,3 выполняют роль рекуператоров, зона этих камер называется зоной предварительного нагрева.
После завершения обжига в камере №6 горелочный мостик переставляется на три камеры вперед, т.е на камеру №3.Эксгаустер также передвигается вперед и переставляется с межкамерного простенка №1в простенок за за «мертвой» камерой.
Камера «6 поступает на охлаждение, продувкой холодным воздухом. С этой целью в межкамерные простенки за камерами №10и12 устанавливаются дутьевые трубы(манифольды), которые оснащены вентилятором нагнетающий в огневые простенки камер воздух. Воздух проходя простенки камер с №12 по№6 охлаждает футеровку простенков и обожженные аноды. Нагретый воздух проходящий через простенки зоны охлаждения поступает в топливные каналы простенков зоны «огня», повышая тепловой КПД печи.
|
Особенность многокамерной кольцевой печи состоит в том, что обжигаемые изделия находятся в состоянии покоя, а зона огня или зона обжига периодически передвигается от камеры к камере по кольцу печи. Весь теплотехнологический цикл, включая зоны предварительного нагрева, форсированного огня и охлаждения, а также камеры подготовительного цикла (загрузка, разгрузка) носят название «огня». При большом числе камер печь работает на нескольких «огнях».
Как правило, один огонь формируется из 18—20 камер, распределенных следующим образом. Одна «мертвая» камера, т. е. камера, запирающая первую в системе огня камеру. Эта камера находится под полной загрузкой «зелеными» анодами, и при передвижении огня она становится первой в зоне предварительного нагрева. Три камеры находятся под естественным нагревом, одна камера- с форсированным подогревом, две камеры- с полным огнем. 6-8 камер на охлаждении. По две камеры по загрузкой и разгрузкой и одна на ремонте. Работа печи обжига должна быть организована таким образом, чтобы максимально использовать все камеры, обеспечить исполнение заданного графика обжига и получить требуемое качество обожженных анодов.
Производительность печи(Q) определяется по формуле:
Q =24∙ g ∙ n ∕ t (т/час)
g - загрузка одной камеры (с пересчетом на обожженные аноды),т
n - число огней на работающей печи
t - «темп огня»
Темп огня определяется делением полной продолжительности обжига на число камер, находящихся на подогреве и огне.
Продолжительность обжига в одной камере называется также режимом обжига.
В отопительных простенках.
Как указывалось выше, Обогрев простенков проводится за счет сжигания топлива в горелочных устройствах и дожига летучих продуктов коксования. Безусловно, сжигание топлива дает основной вклад в тепловой баланс печи и образует основной поток печных газов.
Однако смолы и газы коксования, выделяющиеся при коксовании пека, также оказывают существенное влияние на аэродинамический и температурный режим печей обжига. Если количество топлива, подаваемого на обогрев печи, легко контролируется и регулируется по результатам измерения температуры, то поступление продуктов коксования и их горение с трудом поддаются контролю и управлению. Это негативно отражается на темпе подъема температуры в наиболее важной зоне 300—650 оС, где отмечается наибольшее выделение смол и тяжелых углеводородов в виде паров.
|
На (рис 8.41) представлена диаграмма отражающая современную стратегию управления горения топлива и летучих веществ коксования в печи обжига.
Вся структура контроля и управления горением топлива и летучих веществ коксования в печи обжига подразделяется на три основных блока:
— контроль отходящих газов;
— контроль горения топлива;
— контроль дутьевого режима воздухом на охлаждение блоков.
8.2.5 Обслуживание печи обжига.
Обслуживание печи обжига включает все операции, связанные с загрузкой и разгрузкой камер, перемещением оборудования во время продвижения огня, контролем за работой простенков, ремонтом и заменой огневых простенков и т. д.
Подача «зеленых» блоков на обжиг проводится автоматически с помощью центрального конвейера, размещенного вдоль оси печи (см. рис. 8.15, поз. 10). Как правило, аноды собираются пакетами по З штуки и автоматически останавливаются у загружаемой камеры. С помощью многооперационного крана специальным захватом с гидроприводом аноды поднимаются и в один прием загружаются в кассету, при этом блоки герметизируются со всех сторон пересыпкой. Крановщик из кабины мостового крана включает подающий конвейер и следующий пакет из З анодов подводится к камере.
Перед загрузкой пакета из З анодов на подину засыпается слой пересыпки из прокаленного нефтяного кокса крупностью—5+1 мм. Высота слоя пересыпки в среднем 50 мм, но в зависимости от состояния подины она может быть несколько больше или меньше.
В том случае, если подина в хорошем состоянии — без трещин и деформации, подсыпка может быть уменьшена или не проводиться вообще.
После загрузки каждого пакета оператор подсыпает поверх анодов слой пересыпки толщиной 5—10 см. После установки последнего ряда свободное пространство между стенками кассеты и «зелеными» блоками засыпается коксовой пересыпкой. для создания хорошего уплотнения против подсосов воздуха и тепловой изоляции верх кассет заполняется слоем пересыпки по верхнему ряду блоков толщиной 500—700 мм. Пересыпка из прокалённого нефтяного кокса крупностью -5+1 мм выполняет функции защиты обжигаемых изделий от окисления, создавая внутри кассет восстановительную атмосферу.
Пересыпка берется из бункера расположенного на кране.
|
Разгрузочная операция обожженных анодов выполняется в обратном порядке. Вначале снимается верхний слой пересыпки, затем порядно извлекаются аноды. Обожженные аноды устанавливаются на транспортный конвейер, по которому они направляются к станции очистки от прикоксованной коксовой пересыпки. Выгрузка одной кассеты продолжается в среднем 60 мин, а загрузка в два раза короче, т. е. 30 мин.
Станция очистки состоит из двух камер со скребковыми ножами, которые очищают аноды со всех сторон. Аноды протягиваются гидравлическими толкателями через камеры чистки. В третьей камере аноды подвергаются тонкой очистке сжатым воздухом. Снятый с анода коксовый материал собирается в сборный контейнер. Станция очистки подключена к фильтру очистки от пали.
Продвижение огня – повседневная операция и состоит из операций:
-прекращение отсоса дымовых газов по всей печи на время переноса эксгаустера
- прекращение подачи топлива на горелочные мостики
- снятие крышек с дымовых колодцев следу за «мертвой» камерой поперечного простенка
- перестановка эксгаустера краном на поперечный простенок за «мертвой» камерой
- установка крышек на дымовые колодцы освобожденного соединительного простенка
- запуск отсоса дымовых газов
-запуск подачи топлива на горелочные мостики
-перенос мостика термопар
- перестановка дальнего горелочного моста на две камеры вперед, т.е на место третьей камеры предварительного нагрева
- смещение на одну камеру по ходу огня обеих дутьевых труб
- подсоединение перемещенных мостов горелок и термопар к шкафу регулирования, пуск горелок совместно с системой регулирования.
К операция по обслуживанию печи относятся также ремонт и замена огнеупорных простенков. Средний срок службы простенка 38мес, для 60камерной печи, необходимо менять 5-ть простенков каждые две недели.
Срок службы печи составляет 12-15 лет.
Пуск печи после капитального ремонта осуществляется двумя способами:
- с предварительным разогревом и сушкой до5000С
- без предварительного разогрева
При 5000С сушатся и нагреваются все камеры печи, подогрев и последующий запуск можно производить как на одном огне с последующим вовлечением всех камер, так и на всех огнях, что сокращает время ввода печи в эксплуатацию.
Пуск печи без предварительной сушки, т.е сушкой при обжиге, сокращает сроки пусковых работ. Однако предпочтение отдается пуску с предварительной сушкой по специальному графику, который длительней графика обжига.
После завершения сушки камеру охлаждают проводят ее ревизию и загружаются «зеленые» аноды с пересыпкой. По мере завершения пусконаладочных работ возможен запуск печи на полную мощность.
Раздел 8. Обжиг «зеленых» анодных блоков
Обжиг «зеленых» анодных блоков является завершающей стадией производства угольных анодов для алюминиевых электролизеров,
при этом пекококсовая масса превращается в монолитный электрод.
Обжиг «зеленых» анодных блоков и формирование самообжигающегося анода непосредственно на электролизере имеют близкий по своей сущности механизм. В обоих случаях происходят замедленное спекание связующего и формирование структуры анода. Однако при обжиге «зеленых» блоков удается сохранить первоначальную структуру анода, заложенную при смешении и виброформовании. У самообжигающихся анодов, не удается избежать заметной сендиминтации жидкой фазы и нарушения заданной структуры анода, что приводит к снижению качества анода. Повышенное содержание связующего приводит к снижению плотности, пористости и повышению окисляемости при электролизе. Обжиг анодов можно проводить на любых печах, при условии выдержки графика обжига,создания восстановительной или нейтральной атмосферы для предотвращения окисления анода. На практике обжиг анодов проводится исключительно в кольцевых камерных печах открытого или закрытого типа. Именно на печах этого типа достигаются большая производительность, максимальная экономия топлива и наилучшие технологические результаты обжига, включая хорошее качество обожженных анодов.
|
|
Двойное оплодотворение у цветковых растений: Оплодотворение - это процесс слияния мужской и женской половых клеток с образованием зиготы...
Наброски и зарисовки растений, плодов, цветов: Освоить конструктивное построение структуры дерева через зарисовки отдельных деревьев, группы деревьев...
Своеобразие русской архитектуры: Основной материал – дерево – быстрота постройки, но недолговечность и необходимость деления...
Автоматическое растормаживание колес: Тормозные устройства колес предназначены для уменьшения длины пробега и улучшения маневрирования ВС при...
© cyberpedia.su 2017-2024 - Не является автором материалов. Исключительное право сохранено за автором текста.
Если вы не хотите, чтобы данный материал был у нас на сайте, перейдите по ссылке: Нарушение авторских прав. Мы поможем в написании вашей работы!