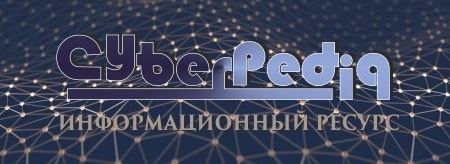
Опора деревянной одностоечной и способы укрепление угловых опор: Опоры ВЛ - конструкции, предназначенные для поддерживания проводов на необходимой высоте над землей, водой...
История развития хранилищ для нефти: Первые склады нефти появились в XVII веке. Они представляли собой землянные ямы-амбара глубиной 4…5 м...
Топ:
Процедура выполнения команд. Рабочий цикл процессора: Функционирование процессора в основном состоит из повторяющихся рабочих циклов, каждый из которых соответствует...
Эволюция кровеносной системы позвоночных животных: Биологическая эволюция – необратимый процесс исторического развития живой природы...
Особенности труда и отдыха в условиях низких температур: К работам при низких температурах на открытом воздухе и в не отапливаемых помещениях допускаются лица не моложе 18 лет, прошедшие...
Интересное:
Подходы к решению темы фильма: Существует три основных типа исторического фильма, имеющих между собой много общего...
Национальное богатство страны и его составляющие: для оценки элементов национального богатства используются...
Что нужно делать при лейкемии: Прежде всего, необходимо выяснить, не страдаете ли вы каким-либо душевным недугом...
Дисциплины:
![]() |
![]() |
5.00
из
|
Заказать работу |
|
|
НА КОМБИНИРОВАННОЙ
ДВУХ-, четырехручьевой МНЛЗ № 3
ТЕХНОЛОГИЧЕСКАЯ ИНСТРУКЦИЯ
ТИ 102-СТ.К-263-2011
Н. Тагил
2011
Открытое акционерное общество
«ЕВРАЗ Нижнетагильский металлургический комбинат»
УТВЕРЖДАЮ
Главный инженер ЕВРАЗ НТМК
С.В. Филатов
НЕПРЕРЫВНАЯ РАЗЛИВКА СТАЛИ
НА КОМБИНИРОВАННОЙ
ДВУХ-, четырехручьевой МНЛЗ № 3
ТЕХНОЛОГИЧЕСКАЯ ИНСТРУКЦИЯ
ТИ 102-СТ.К-263-2011
(Взамен ВТИ 102-СТ.К-263-2010)
РАЗРАБОТАНА
Начальник
технического управления
М.С. Фомичев
Начальник КЦ № 1
Н.В. Мухранов
Всего страниц 52
ОАО «ЕВРАЗ Нижнетагильский металлургический комбинат» | Технологическая инструкция «Непрерывная разливка стали на комбинированной двух-, четырехручьевой МНЛЗ № 3» | ТИ 102-СТ.К-263-2011 Взамен ВТИ 102-СТ.К-263-2010 |
Настоящая технологическая инструкция устанавливает технологию разливки стали на комбинированной двух-, четырехручьевой МНЛЗ № 3 и порядок выполнения подготовительных и вспомогательных операций. Инструкция предназначена для операторов и разливщиков стали, мастеров, начальника участка непрерывной разливки стали, обслуживающего персонала КЦ № 1, контролеров управления технического контроля (УТК).
|
Ответственность за выполнение настоящей инструкции возлагается на сменный технологический персонал цеха.
Контроль за соблюдением и правильным применением настоящей инструкции возлагается на начальника цеха и его заместителей, мастеров и контролеров УТК КЦ № 1.
ОСНОВНЫЕ ПОЛОЖЕНИЯ
1.1 Основными условиями осуществления процесса непрерывной разливки стали на МНЛЗ № 3 являются ниже изложенные.
1.1.1 Подготовка металла к разливке в соответствии с действующими технологическими инструкциями, технологическими указаниями по выплавке и внепечной обработке на конкретную марку стали и своевременная его передача на МНЛЗ № 3.
1.1.2 Подготовка и проверка всех узлов и механизмов МНЛЗ № 3, контрольно - измерительных приборов (КИП) и систем автоматического управления процессом разливки, своевременное выполнение текущих и плановых ремонтов.
1.1.3 Подготовка сталеразливочных и промежуточных ковшей в соответствии с действующими технологическими инструкциями и технологическими указаниями.
1.1.4 Использование при разливке стали в кристаллизаторе шлакообразующей смеси, обеспечивающей разливку в диапазоне скоростей от 0,20 до 1,20 м/мин.
1.1.5 Выполнение технологических операций, предусмотренных настоящей инструкцией, с учетом требований инструкций по охране труда указанных в разделе 10.
Разработана Техническим управлением, КЦ № 1 | Внесена техническим управлением | Срок действия С 20.10.2011 До 20.10.2014 |
1.2 Основным режимом разливки стали является, разливка стали под управлением УРОВНЯ 2 автоматизации:
- управление вторичным охлаждением;
- порезка на мерные заготовки;
- маркировка заготовок;
- работа с системой слежения за качеством продукта;
- оптимизация закрытия ручьев;
- формирование паспорта плавки;
- автоматическое поддержание уровня металла в кристаллизаторе.
Данный режим обеспечивает наиболее качественную разливку металла.
|
1.3 Режим разливки в автоматическом режиме под управлением базисной автоматики (УРОВЕНЬ 1) и режим ручного управления используются при невозможности применения режима управления разливкой под управлением УРОВНЯ 2 (аварийные ситуации, выходы из строя датчиков, оборудования и т.д.).
1.4 Все работы по подготовке МНЛЗ №3 к разливке и разливка стали должны осуществляться под руководством сменного мастера производственного участка MHЛЗ.
ПОДГОТОВКА УЗЛОВ МНЛЗ № 3 К РАБОТЕ
Подготовка кристаллизаторов
2.1.1 В период подготовки МНЛЗ № 3 кристаллизаторы должны быть проверены оператором МНЛЗ № 3 и слесарями участка блока ремонтных мастерских (БРМ), о чем производится запись в соответствующем журнале.
Проверка механизма качания
2.7.1 Проверяется герметичность соединений кристаллизатора и подъемного стола механизма качания.
2.7.2 Характер возвратно-поступательных движений на отсутствие резких толчков.
2.7.3 Коэффициенты качания кристаллизатора МНЛЗ № 3 приведены в приложении А (таблица А.1).
Проверка элементов системы первичного и вторичного
Подготовка затравки
2.9.1 Головки затравок подготавливаются на участке хранения.
2.9.2 До ввода затравки в кристаллизатор головка затравки должна быть очищена от остатков металла. При повреждении головки ее эксплуатация запрещается.
2.9.3 Паз для сцепления затравки со слитком осматривается, при его разгаре эксплуатация головки запрещается.
ПОДГОТОВКА МНЛЗ № 3 К РАЗЛИВКЕ ЖИДКОГО МЕТАЛЛА
Подготовка промежуточных ковшей
3.1.1 Футеровка промежуточных ковшей производится в соответствии с требованиями ТИ 102-СТ.К-208-2009.
3.1.2 Монолитный промежуточный ковш, торкретированный и высушенный, с участка подготовки промежуточных ковшей передается в разливочное отделение. Не допускается наличие на днище и стенках промковшей мусора и неспекшейся торкретмассы.
3.1.3 Промежуточный ковш устанавливается на тележку, устанавливаются стопора, затем путем повторного открывания и закрывания проверяется посадка стопора. Стопорный механизм должен обеспечивать плавный вход стопора в воронку стакана - дозатора. При необходимости, с помощью крепежных контргаек, производится регулировка посадки стопора путем перемещения стопора в вилке так, чтобы он занял необходимое положение в стакане.
|
После установки стопоров «стопорное железо» с гайкой обматывается асбестовым шнуром. Перед включением горелок стопора поднимаются в верхнее положение и фиксируются.
3.1.4 Разогрев футеровки промежуточного ковша ведется до температуры 1100 °С - 1200 °С. Степень прогрева футеровки оценивается как по температуре внутренней ее поверхности, так и по температуре кожуха, которая должна быть не менее 60 °С при отрицательных температурах окружающего воздуха и не менее 70 °С при положительных.
Температура замеряется в трех точках боковой стены – в центре и у торцов - на расстоянии 400-500 мм от днища.
Продолжительность разогрева промежуточного ковша должна быть не менее 3 ч и не более 6 ч.
3.1.5 С целью увеличения степени прогрева футеровки промковшей, перед основным разогревом допускается предварительный подогрев рабочей футеровки до температуры 350 °С - 450 °С.
Продолжительность предварительного подогрева не более 6 ч.
Контроль за предварительным подогревом промежуточных ковшей осуществляют сменные бригадиры и мастера.
3.1.6 При разогреве промежуточного ковша стаканы – дозаторы снизу подогреваются с помощью эжекторов.
3.1.7 Погружные корундографитовые стаканы перед разливкой разогреваются до светло-красного свечения. Длительность разогрева от 40 до 90 мин. Перед установкой визуально проверяется их целостность.
3.1.8 Контроль за режимом разогрева и подготовкой промежуточного ковша к плавке осуществляется сменным производственным мастером МНЛЗ.
Заведение затравки
3.3.1 Перед вводом затравки в кристаллизатор производится включение механизма качания для определения его работоспособности.
3.3.2 Заведение затравки осуществляется в автоматическом режиме. При подходе затравки к кристаллизатору, автоматическая подача затравки выключается, и осуществляется переключение в ручной режим заведения затравки.
3.3.3 Заведение затравки в кристаллизатор осуществляется в толчковом режиме.
3.3.4 Для сечений 200х525 мм, 120/410х655 мм, 165/395х530 мм и 165/485х620 мм, затравка вводится в кристаллизатор на уровень 420 мм ниже верхней кромки медной пластины и опускается на 50 мм, расстояние от верхней кромки должно быть (470 + 20) мм.
|
3.3.5 Для сечения 300х380 мм, затравка вводится в кристаллизатор на уровень 650 мм ниже верхней кромки медной пластины.
3.3.6 После ввода в кристаллизатор головка затравки обдувается сжатым воздухом для удаления загрязнений и влаги. Зазоры между стенками кристаллизатора и головкой затравки забиваются асбестовым шнуром, а затем засыпаются чугунной прокаленной стружкой. После уплотнения головки затравки на нее укладываются «холодильники».
Углы кристаллизатора промазываются тестообразной массой, состоящей из 2/3 шлакообразующей смеси и 1/3 солидола.
3.3.7 После уплотнения головки затравки кристаллизатор закрывается плитой, которая снимается только перед началом разливки.
РАЗЛИВКА стали на МНЛЗ № 3
Начало разливки плавки
4.1.1 После установки сталеразливочного ковша на подъемно-поворотный стенд, на ковш устанавливается крышка, к шиберному затвору подсоединяется гидравлический цилиндр, разворотом траверсы поворотного стенда ковш устанавливается в рабочую позицию с поднятием его в крайнее верхнее положение.
4.1.2 Оператор пульта управления № 1 по громкоговорящей связи подает команду «Ковш подан». Отключаются и поднимаются в верхнее положение горелки для разогрева промежуточного ковша. Проверяется работа стопоров, затем они устанавливаются в положение «закрыто».
4.1.3 Промежуточный ковш перемещается в позицию разливки, центрируется и поднимается в крайнее верхнее положение. На ковш устанавливаются погружные стаканы, в воронку которых непосредственно перед стыковкой со стаканом – дозатором устанавливается герметизирующая воронка (адаптер). Ковш опускается, проверяется центровка погружных стаканов по оси кристаллизаторов (отклонение оси стакана от оси кристаллизатора должно быть не более 5 мм - определяется визуально), подключается разводка патрубков стопоров – моноблоков к аргонопроводу, радиационный излучатель устанавливается в положение «открыто».
4.1.4 Манипулятором подсоединяется защитная труба, в воронку которой предварительно устанавливается адаптер из эластичного огнеупорного материала, открывается шиберный затвор и промежуточный ковш наполняется металлом.
4.1.5 В случае непоступления металла в промежуточный ковш, защитная труба отсоединяется, при открытом шиберном затворе канал сталеразливочного стакана прожигают кислородом до появления металла. При стабилизации струи металла шиберный затвор закрывается и защитная труба манипулятором устанавливается в рабочее положение, после чего вновь открывается шиберный затвор.
Время разливки металла без применения защитной трубы не должно превышать 1 мин. Перерыв с момента закрытия шиберного затвора и последующего открытия с защитной трубой не должен превышать 40 с.
|
4.1.6 Глубина погружения защитной трубы в процессе разливки в металл должна быть в пределах 200-300 мм от нижнего среза трубы – определяется визуально.
4.1.7 При наполнении промежуточного ковша до 8-10 т по массе жидкого металла открываются стопора и производится наполнение кристаллизаторов.
4.1.8 При достижении уровня металла в промежуточном ковше 15-17 т в промежуточный ковш, на зеркало металла, присаживается теплоизолирующая смесь марки ПК-2, производства КХП, в количестве 6-8 мешков.
В процессе разливки уровень металла в промковше должен поддерживаться на уровне, т, для заготовок:
19-20............................. сечением 200х525 мм, 120/410х655 мм, 165/395х530 мм и 165/485х620 мм;
25-26............................. сечением 300х380 мм.
4.1.9 По ходу разливки плавки отдача утепляющей смеси в промежуточный ковш производится по мере ее проплавления. Оголения зеркала металла во время разливки плавки не допускается.
4.1.10 Измерение температуры металла в промежуточном ковше производится в районе стопоров моноблоков не менее чем через 5 мин, но не более чем через 15 мин от начала разливки плавки, второй и последующие замеры - через 10–20 мин после предыдущего.
4.1.11 В середине разливки из промежуточного ковша отбираются 2 пробы на химический анализ плавки. Каждая проба клеймится номером плавки и номером пробы. Пробы отправляются в экспресс - лабораторию.
Замена погружного стакана
4.5.1 Замена погружного стакана производится под руководством старшего разливщика.
4.5.2 Замену рекомендуется производить на мерной длине заготовки.
4.5.3 При замене погружного стакана при двухручьевом варианте разливки на ручье, где производится замена погружного стакана осуществляются следующие операции:
- в кристаллизатор дополнительно засыпается шлакообразующая смесь для утепления зеркала металла во время процесса замены, оголение металла не допускается;
- скорость вытягивания слитка снижается до пусковой;
- стопором перекрывается канал стакана - дозатора. Уровень жидкого металла при смене стакана в кристаллизаторе не должен опускаться ниже середины высоты кристаллизатора;
- после установки предварительно нагретого погружного стакана, двух-трехкратным открыванием и закрыванием стопора кристаллизатор наполняется металлом до нижнего уровня погружного стакана (при разливке через прямоточные стаканы) или до верха сталевыпускных окон стакана (при разливке металла через глуходонные стаканы), на зеркало металла присаживается шлакообразующая смесь. Затем кристаллизатор заполняется металлом до рабочего уровня;
- разливка стали на ручье с пусковой скоростью производится в течение 1,5 мин, затем в течение 3 мин производится разгон до рабочей скорости;
- образовавшийся при замене погружного стакана дефектный участок заготовки длиной по 500 мм выше и ниже пояса вырезается.
4.5.4 При замене погружного стакана при четырехручьевом варианте разливки осуществляются следующие операции:
- в обе полости кристаллизатора засыпается шлакообразующая смесь для утепления зеркала металла во время процесса замены, оголение металла не допускается.
- скорость вытягивания слитков снижается до пусковой;
- стопорами перекрываются каналы стаканов – дозаторов сдвоенного ручья. Уровень жидкого металла в обоих полостях кристаллизатора не должен опускаться ниже середины высоты кристаллизатора;
- после замены на одном ручье погружного стакана, двух-трехкратным открыванием и закрыванием стопоров обе полости кристаллизатора наполняются металлом до нижнего уровня погружного стакана (при разливке через прямоточные стаканы) или до верха сталевыпускных окон стакана (при разливке металла через глуходонные стаканы), на зеркало металла присаживается шлакообразующая смесь. Затем кристаллизаторы заполняются металлом до рабочего уровня;
- разливка стали с пусковой скоростью на сдвоенном ручье производится в течение 1,5 мин, затем в течение 3 мин производится разгон до рабочей скорости;
- на обоих ручьях вырезается дефектный участок заготовки образовавшийся при замене погружного стакана. Длина дефектного участка составляет по 500 мм выше и ниже пояса для каждого ручья.
4.5.5 В случае, если при замене погружного стакана подача металла в кристаллизатор не производилась более 3 мин, разливка на сдвоенном ручье прекращается и горячие слитки выводится из МНЛЗ № 3.
Окончание разливки плавки
4.7.1 По окончании разливки плавки из сталеразливочного ковша закрывается шиберный затвор. Защитная труба отмыкается и переводится в резервную позицию. Сталеразливочный ковш поворачивается и снимается с подъемно-поворотного стенда разливочным краном. Труба осматривается, очищается от остатков металла и герметизирующей вставки и при удовлетворительном состоянии используется повторно.
4.7.2 Распределение оставшегося металла из промежуточного ковша
по ручьям производится из расчета получения последней мерной заготовки с учетом минимальной величины хвостовой обрези путем последовательного закрытия ручьев в автоматическом или ручном режимах. Разливка в это время производится на скорости 0,5-0,6 м/мин. Минимальный уровень жидкого металла в промежуточном ковше в момент последнего закрытия должен составлять 6-8 т.
4.7.3 Минимальная величина хвостовой обрези должна составлять, мм, для заготовок:
800-1000....................... сечением 200х525 мм, 120/410х655 мм, 165/395х530 мм и 165/485х620 мм;
1800-2000..................... сечением 300х380 мм.
4.7.4 По окончании подачи металла в кристаллизаторы закрываются стопора, прекращается подача аргона и промежуточный ковш тележкой переводится в резервную позицию над шлаковнями.
4.7.5 Оператор пульта управления № 1 по громкоговорящей связи объявляет: «Машина № 3 разливку закончила». Скорость разливки снижается до пусковой до выхода заготовок из кристаллизатора.
4.7.6 При помощи кислорода удаляются настыли с крышки. Ковш передается на участок удаления остатков шлака и металла.
4.7.7 Радиационный излучатель на кристаллизаторе перекрывается, плиты кристаллизаторов обдуваются воздухом.
4.7.8 Полость кристаллизатора очищается от корольков металла, шлака; затем поверхность рабочих стенок протирается ветошью и проверяется их состояние.
4.7.9 Клеймение заготовок производится клеймовочным устройством. Идентификация металла осуществляется в соответствии с требованиями ТИ 102- СТ.К-106-2009.
4.7.10 После маркировки заготовки транспортируются на участок поперечного транспортера, с поперечного транспортера на передаточный рольганг, а затем со сталкевателя краном укладываются на специальные
платформы (вагон - термос).
4.7.11 Передача непрерывнолитых заготовок из конвертерного цеха в прокатные цехи производится в соответствии с ТИ 102 - СТ.К-106-2009.
РАЗЛИВКА СТАЛИ СЕРИЯМИ
Замена промежуточного ковша
5.3.1 Замена промежуточного ковша производится под руководством сменного производственного мастера МНЛЗ.
5.3.2 Находящийся в промежуточном ковше металл разливается до остатка металла 6-8 т, по мере снижения уровня металла скорость разливки плавно снижается до пусковой. При достижении уровня в промежуточном ковше 6-8 т все стопора перекрываются, толщину шлакообразующей смеси в кристаллизаторе доводят до 40-60 мм (определяется визуально).
5.3.3 Уровень металла в кристаллизаторах опускается до половины высоты кристаллизатора, останавливаются механизмы вытягивания слитка, механизмы качания кристаллизаторов не выключаются, из кристаллизаторов удаляется шлаковый гарнисаж.
5.3.4 На разогретый промежуточный ковш устанавливаются погружные стаканы, в воронки которых устанавливаются вставки из эластичного огнеупорного материала, ковш подается в позицию разливки.
5.3.5 Погружные стаканы центрируются относительно оси кристаллизаторов.
5.3.6 Траверса подъемно-поворотного стенда со сталеразливочным ковшом опускается в нижнее положение, открывается шиберный затвор и промежуточный ковш заполняется металлом. Наполнение промежуточного ковша осуществляется согласно 4.1.3-4.1.11.
5.3.7 Перерыв в подаче металла в кристаллизаторы при смене промежуточных ковшей не должен превышать 3 мин. Если перерыв в подаче металла составил более 3 мин, разливка металла прекращается и слитки выводятся из машины.
5.3.8 Пояс от перерыва разливки выводится из кристаллизаторов на
пусковой скорости в течение 3 мин, после чего скорость разливки увеличивается в течение 3 мин до рабочей.
5.3.9 При замене промежуточного ковша длина переходной зоны определяется следующим образом:
- для заготовок сечением сечением 200х525 мм, 120/410х655 мм, 165/395х530 мм и 165/485х620 мм от заготовки предыдущей плавки отрезается кусок длиной 800-1000 мм от пояса, от заготовок последующей плавки - кусок длиной не менее 500 мм от пояса;
- для заготовок сечением 300х380 мм от заготовки предыдущей плавки отрезается кусок длиной 1800-2000 мм от пояса, от заготовок последующей плавки - кусок длиной не менее 500 мм от пояса.
5.3.10 Учитывая то, что минимальная длина заготовки, проходящей по рольгангу, должна быть не менее 3600 мм, недостающая длина отрезается от того или иного конца заготовки, примыкающей к дефектному участку, в зависимости от оптимальных вариантов раскроя.
МЕРЫ ПО ИХ УСТРАНЕНИЮ
Прогар футеровки ковшей
6.3.1 Основные причины прогара:
- нарушение технологии кладки и сушки ковша;
- деформация корпуса ковша;
- неудовлетворительная установка стакана в гнездовом кирпиче;
- подача под разливку ковша с изношенной футеровкой;
- наличие в швах футеровки остатков металла.
6.3.2 Ковш передается на аварийные емкости.
Остановка ручья
6.10.1 При кратковременных (не более 3 мин) остановках ручья подача металла в кристаллизатор прекращается. Мениск поддерживается в жидком состоянии перемешиванием или кратковременной подачей порций жидкого металла. При возобновлении разливки вытягивание слитка производится с пусковой скоростью до выхода пояса из кристаллизатора, после чего скорость разливки плавно увеличивается до рабочей.
6.10.2 При длительных (более 3 мин) остановках ручья разливка на данном ручье прекращается. После выдержки ручья в течении 2-3 мин производится запуск ручья, вытягивание слитка производится с пусковой скоростью до выхода пояса из кристаллизатора. После вывода слитка из кристаллизатора скорость разливки плавно увеличивается до рабочей.
6.10.3 Если после запуска ручья выдать слиток не удается, вытягивание слитка прекращается, производится повторная выдержка в течении 2-3 мин, после чего производится запуск МНЛЗ № 3 в порядке, указанном в 6.10.2.
6.10.4 При невозможности вывода слитка из МНЛЗ № 3 в течение 15 мин с момента остановки, слиток остается в роликовых секциях до полного застывания. После застывания слитка производится его порезка между секциями и выдача по частям.
6.10.5 При кратковременных (не более 3 мин) остановках ручья в четырехручьевом варианте разливки, подача металла в обе полости кристаллизатора прекращается. Мениск поддерживается в жидком состоянии перемешиванием или кратковременной подачей порций жидкого металла. При возобновлении разливки вытягивание слитков производится с пусковой скоростью до выхода поясов из кристаллизатора, после чего скорость разливки плавно увеличивается до рабочей.
6.10.6 При длительных (более 3 мин) остановках ручья разливка на данном сдвоенном ручье прекращается, производится закрытие сдвоенного ручья и вывод слитков на пусковой скорости. На оставшемся сдвоенном ручье осуществляется окончание разливки плавки и остановка МНЛЗ № 3.
ОХРАНА ТРУДА И ТРЕБОВАНИЯ БЕЗОПАСНОСТИ
10.1 Все операции технологического процесса непрерывной разливки стали должны соответствовать требованиям следующих документов:
ПБ 03-517-02 «Общие правила промышленной безопасности для организаций, осуществляющих деятельность в области промышленной безопасности опасных производственных объектов».
ПБ 11-493-02 «Общие правила безопасности для металлургических и коксохимических предприятий и производств» (Утв. Постановлением Госгортехнадзора РФ от 21.06.2002 № 35);
ПБ 11-552-03 «Правила безопасности в сталеплавильном производстве» (Утв. Постановлением Госгортехнадзора России от 24.04.2003 № 25);
ПБ 11-401-01 «Правила безопасности в газовом хозяйстве металлургических и коксохимических предприятий и производств» (Утв. Постановлением Госгортехнадзора России от 20.02.2001 № 9);
ОТИ 0.1-2010 «Инструкция по охране труда для всех работников комбината»;
ОТИ 102-62-2011 «Инструкция для стропальщиков»;
ОТИ 006-12-2009 «Инструкция по охране труда для разливщика стали МНЛЗ конвертерного цеха»;
ОТИ 006-18-2009 «Инструкция по охране труда для оператора МНЛЗ»;
ОТИ 006-03-2008 «Инструкция по охране труда для оператора наладки механического оборудования МНЛЗ КЦ № 1».
10.2 Уровень и концентрация вредных факторов при разливке стали (запыленность, загазованность, температура и т.д.) должны соответствовать действующим нормам ГН 2.2.5.1313-03 «Предельно допустимые концентрации вредных веществ в воздухе рабочей зоны».
Нормативные показатели неблагоприятных факторов производственной среды и трудового процесса, оказывающих вредное влияние на человека, должны соответствовать нормам, указанным в следующих документах:
ГН 2.2.5.1313-03 «Предельно допустимые концентрации вредных веществ в воздухе рабочей зоны», Постановление главного государственного санитарного врача Российской Федерации от 30.04.2003 № 76;
СанПиН 2.2.4.548-96 «Гигиенические требования к микроклимату производственных помещений», утверждённые Постановлением Госкомсанэпиднадзора России от 01.10.96 № 21;
СН 2.2.4/2.1.8.562-96 «Шум на рабочих местах, в помещениях жилых, общественных зданий и на территории жилой застройки», утверждённые постановлением Госкомсанэпиднадзора России от 31.10.96 № 36.
10.3 Все посты управления МНЛЗ № 3 и рабочие места разливщиков должны быть оборудованы взаимосвязанной громкоговорящей связью, средствами звуковой и световой сигнализации, предупреждающей о нарушении установленных режимов работы и возникновении аварийных
ситуаций. Главный пост управления должен быть оборудован телефонным коммутатором, связывающим МНЛЗ № 3 с диспетчером цеха и участками, от которых зависит бесперебойная работа МНЛЗ № 3.
МНЛЗ № 3
Все мероприятия по техническому обслуживанию радиоизотопных приборов (РИП) технического контроля уровня жидкого металла (ПТКУ) в кристаллизаторах МНЛЗ № 3 проводятся дефектоскопистами участка РИП ЦТА, осуществляющими открывание – закрывание блока источника, монтаж-демонтаж блока, транспортирование, ликвидацию особых технологических ситуаций с блоком источника (повреждение жидким металлом блока источника).
Для извлечения блока-излучателя из поврежденного оборудования возможно привлечение персонала КЦ № 1. Работы производятся после проведения инструктажа, согласно «Плану организации восстановительных работ на случай ликвидации особых технологических ситуаций с радиоактивными источниками, находящимися в эксплуатации конвертерного цеха № 1», утвержденному главным инженером НТМК 07.07.2008, под контролем персонала поста радиационного контроля службы радиационной безопасности.
При установлении факта происшествия с блоком должны быть приняты меры согласно:
- СТП 102-201 М-2006 «Система управления охраной труда и промышленной безопасностью. Организация работы по обеспечению радиационной безопасности»;
- «Инструкции по действию персонала НТМК при нарушениях (аварийных ситуациях), связанных с источником ионизирующего излучения», утвержденной приказом Управляющего директора НТМК от 07.05.2008
№ 276;
- «Инструкции по радиационной безопасности при эксплуатации и техническом обслуживании ПТКУ в кристаллизаторах МНЛЗ конвертерного цеха» от 01.03.2007 № 037-10-260;
- плана мероприятий по защите персонала при ликвидации возможных аварийных и особых технологических ситуаций с гамма-источниками ионизирующего излучения (ИИИ) для участка РИП ЦТА, ОНРС КЦ № 1, участка БЗУ доменного цеха от 12.05.2008 № 331-15/207.
ТРЕБОВАНИЯ ОХРАНЫ ОКРУЖАЮЩЕЙ СРЕДЫ
12.1 Нормативы воздействия на окружающую среду технологического процесса и оборудования представлены в приложении Д.
При выполнении технологических операций должны соблюдаться нормативы выбросов загрязняющих веществ от технологического оборудования в атмосферу согласно «Проекту нормативов предельно допустимых выбросов (ПДВ) и временно согласованных выбросов (ВСВ)», утвержденному главным инженером НТМК 01.12.2006.
12.2 В период аварийных ситуаций необходимо руководствоваться СТП 102-177 М-2011 «Система экологического менеджмента. Подготовленность к аварийным ситуациям и реагирование на них».
В период неблагоприятных метеорологических условий (НМУ) необходимо руководствоваться СТП 102-240 М-2008 «Система экологического менеджмента. Организация деятельности в период неблагоприятных метеорологических условий», с обязательным учетом выполненных мероприятий в специальном журнале, который хранится в диспетчерской конвертерного цеха.
12.3 Контроль за источниками выброса загрязняющих веществ в атмосферу производится специалистами УОПС.
12.4 Для технологических нужд используется вода чистого оборотного цикла ОНРС, грязного оборотного цикла вторичного охлаждения слитка, химически обессоленная вода замкнутого оборотного цикла охлаждения кристаллизатора.
Использование воды на технологические нужды должно соответствовать «Индивидуальным текущим нормам водопотребления и водоотведения ОАО «НТМК».
12.5 Качество оборотной воды должно соответствовать утвержденным нормативам. Контроль за качеством оборотной воды производится аккредитованной лабораторией экоаналитического центра УОПС.
Отходы производства
12.6.1 При обращении с отходами производства и потребления необходимо руководствоваться Регламентом по обращению с отходами производства и потребления в ОАО «НТМК» (утвержденным приказом Управляющего директора НТМК от 23.06.2010 № 346).
12.6.2 Окалина из горизонтальных отстойников ямы окалины по мере накопления убирается и частично используется в металлургическом производстве, частично передается сторонним организациям для производства агломерата.
12.6.3 Отходы черных металлов – головная, донная обрезь, скрап из промежуточных ковшей, аварийный скрап-передают в цех переработки металлолома.
12.6.4 Шлак из сталеразливочных ковшей и шлаковен сливается или кантуется в шлаковые чаши и отправляется на шлакоразделку конвертерного цеха.
12.6.5 Отходы от чистки узлов МНЛЗ № 3 (кристаллизаторы, головки затравки, зоны вторичного охлаждения и др.) - остатки металла, заусеницы, скрап, окалина, остатки шлака, шлак от машины газовой резки и прочие отходы от чистки оборудования в думпкарах вывозятся на шлаковый отвал на станцию Ольховка.
12.6.6 Отработанные масла МНЛЗ № 3 сливаются в емкость, частично регенерируются и используются в цехе, частично передаются на мазутный участок ПСЦ.
12.6.7 Отходы асбестового шнура вместе с мусором от уборки производственных помещений в думпкарах вывозятся на площадку мусоров шлакового отвала.
Руководитель разработки-
Начальник отдела внепечной
металлургии и НРС технического управления Е.В. Шеховцов
Исполнитель –
Начальник бюро НРС отдела ВПМ и НРС
технического управления П.В. Эккерт
СОГЛАСОВАНО
Начальник управления
технического контроля В.И. Хрипко
Заместитель главного инженера ЕВРАЗ НТМК –
начальник сервисного центра С.С. Дружинин
Заместитель главного инженера ЕВРАЗ НТМК –
начальник управления охраны труда
и промышленной безопасности В.А. Никифоров
Начальник управления
охраны природной среды С.А. Пермяков
Начальник отдела
главного метролога-
главный метролог П.А. Фирстов
Начальник службы
радиационной безопасности
управления по делам ГО и ЧС В.И. Ромашев
Зарегистрирована
Начальник бюро
стандартизации С.П. Хандрамайлова
Приложение А
(обязательное)
Приложение Б
(обязательное)
Таблица Б.3 – Малокремнистые марки стали типа «Ю»
Скорость разливки, м/мин | Расход воды, л/мин, по зонам | |||||||||
1 зона | 2 зона | 3 зона | 4 зона | 5 зона | торец | |||||
малый | большой | малый | большой | малый | большой | малый | большой | |||
радиус | радиус | радиус | радиус | радиус | радиус | радиус | радиус | |||
0,4 | 31,3 | 20,7 | 20,7 | 12,4 | 13,7 | - | - | - | - | 9,0 |
0,5 | 40,4 | 23,1 | 23,1 | 13,8 | 15,3 | 10,0 | 15,8 | - | - | 10,0 |
0,6 | 51,0 | 31,0 | 31,0 | 18,6 | 20,5 | 22,8 | 27,9 | 10,2 | 13,8 | 13,4 |
0,7 | 61,2 | 33,5 | 33,5 | 20,1 | 22,2 | 24,6 | 30,1 | 11,0 | 14,9 | 14,5 |
0,8 | 70,0 | 39,6 | 39,6 | 23,7 | 26,2 | 29,1 | 35,6 | 13,0 | 17,6 | 17,2 |
0,9 | 80,4 | 42,2 | 42,2 | 25,3 | 27,9 | 31,0 | 37,9 | 13,9 | 18,8 | 18,3 |
1,0 | 89,5 | 44,6 | 44,6 | 26,7 | 29,5 | 32,8 | 40,1 | 14,7 | 19,9 | 19,3 |
1,1 | 98,5 | 47,0 | 47,0 | 28,1 | 31,1 | 34,6 | 42,2 | 15,5 | 20,9 | 20,4 |
1,2 | 107,5 | 49,0 | 49,0 | 29,4 | 32,4 | 36,1 | 44,1 | 16,1 | 21,8 | 21,3 |
1,3 | 113,7 | 50,9 | 50,9 | 30,5 | 33,7 | 37,4 | 45,8 | 16,8 | 22,7 | 22,1 |
Примечания 1 Расходы даны на одну грань слитка в зонах 2, 3, 4, 5 и торец. 2 Первая зона закольцована, расходы в ней даны на 4 грани. |
Б.2 Режимы вторичного охлаждения заготовки сечением 120/410х655 мм приведены в таблицах Б.4, Б.5.
Таблица Б.4 - жесткий режим охлаждения.
Зона | Скорость, м/мин | ||||||||||
0,10 | 0,20 | 0,30 | 0,40 | 0,50 | 0,60 | 0,70 | 0,80 | 0,90 | 1,00 | 1,10 | |
Расход воды, л/мин | |||||||||||
1 | 9,4 | 38,0 | 58,0 | 79,0 | 100,0 | 121,0 | 142,0 | 162,0 | 184,0 | 204,0 | 226,0 |
2 | 34,0 | 52,0 | 99,0 | 163,0 | 225,0 | 281,0 | 331,0 | 382,0 | 432,0 | 483,0 | 533,0 |
3 | 54,0 | 54,0 | 54,0 | 54,0 | 69,0 | 100,0 | 143,0 | 195,0 | 244,0 | 284,0 | 324,0 |
4 | 67,0 | 67,0 | 67,0 | 67,0 | 67,0 | 67,0 | 67,0 | 67,0 | 71,0 | 89,0 | 110,0 |
5 | 61,0 | 61,0 | 61,0 | 61,0 | 61,0 | 61,0 | 61,0 | 61,0 | 61,0 | 61,0 | 61,0 |
Таблица Б.5 - средний режим охлаждения.
Зона | Скорость, м/мин | ||||||||||
0,10 | 0,20 | 0,30 | 0,40 | 0,50 | 0,60 | 0,70 | 0,80 | 0,90 | 1,00 | 1,10 | |
Расход воды, л/мин | |||||||||||
1 | 8,5 | 31,0 | 48,0 | 65,0 | 82,0 | 99,0 | 116,0 | 133,0 | 151,0 | 167,0 | 185,0 |
2 | 34,0 | 48,0 | 85,0 | 135,0 | 185,0 | 230,0 | 271,0 | 313,0 | 354,0 | 395,0 | 437,0 |
3 | 54,0 | 54,0 | 54,0 | 54,0 | 65,0 |
|
|
Историки об Елизавете Петровне: Елизавета попала между двумя встречными культурными течениями, воспитывалась среди новых европейских веяний и преданий...
Особенности сооружения опор в сложных условиях: Сооружение ВЛ в районах с суровыми климатическими и тяжелыми геологическими условиями...
Типы сооружений для обработки осадков: Септиками называются сооружения, в которых одновременно происходят осветление сточной жидкости...
Семя – орган полового размножения и расселения растений: наружи у семян имеется плотный покров – кожура...
© cyberpedia.su 2017-2024 - Не является автором материалов. Исключительное право сохранено за автором текста.
Если вы не хотите, чтобы данный материал был у нас на сайте, перейдите по ссылке: Нарушение авторских прав. Мы поможем в написании вашей работы!