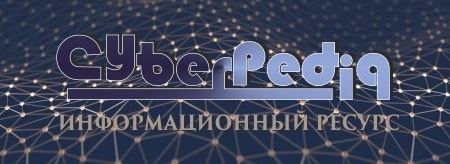
Общие условия выбора системы дренажа: Система дренажа выбирается в зависимости от характера защищаемого...
Эмиссия газов от очистных сооружений канализации: В последние годы внимание мирового сообщества сосредоточено на экологических проблемах...
Топ:
Основы обеспечения единства измерений: Обеспечение единства измерений - деятельность метрологических служб, направленная на достижение...
Процедура выполнения команд. Рабочий цикл процессора: Функционирование процессора в основном состоит из повторяющихся рабочих циклов, каждый из которых соответствует...
Оценка эффективности инструментов коммуникационной политики: Внешние коммуникации - обмен информацией между организацией и её внешней средой...
Интересное:
Принципы управления денежными потоками: одним из методов контроля за состоянием денежной наличности является...
Мероприятия для защиты от морозного пучения грунтов: Инженерная защита от морозного (криогенного) пучения грунтов необходима для легких малоэтажных зданий и других сооружений...
Искусственное повышение поверхности территории: Варианты искусственного повышения поверхности территории необходимо выбирать на основе анализа следующих характеристик защищаемой территории...
Дисциплины:
![]() |
![]() |
5.00
из
|
Заказать работу |
|
|
Одношпиндельные фасонно-отрезные автоматы 11Ф16, 11Ф25, 11Ф40 предназначены для обработки деталей из прутка диаметром до 40 мм; автоматы 1Б023, 1Б032 применяют для изготовления деталей из стальной проволоки диаметром до 8 мм и латунной проволоки диаметром до 10 мм, свернутой в бунт. На фасонно-отрезных автоматах обрабатывают детали длиной до 100 мм, для которых не требуется высокая точность. На этих автоматах ни пруток (проволока), ни шпиндельная бабка в процессе обработки продольного перемещения не имеют. Обработка ведется методом врезания фасонными, отрезными и другими резцами, установленными в резцовой вращающейся головке (поперечных суппортах). Некоторые станки имеют устройство для продольного точения, а также агрегатные головки для сверления, нарезания резьбы, фрезерования.
Одношпиндельные автоматы продольного точения (1103, 1Б10В, 1М06ДА, 1М10В, 1М10А, 11Т16В, 1Д25В, 1М32В и др.) предназначены для обработки деталей из прутка диаметром до 30 мм и длиной до 100 мм с точностью 5 —6-го квалитета по диаметру и 6-го квалитета по длине и с шероховатостью поверхности Ra = 5 ч-1,25 мкм.
На автоматах продольного точения шпиндельная бабка имеет продольное поступательное перемещение. Все суппорты (которых может быть четыре-пять) расположены веерообразно вокруг обрабатываемого прутка и имеют только поперечное перемещение. При одновременном согласованном перемещении шпиндельной бабки с прутком и поперечных суппортов с инструментами на этих автоматах возможна обработка конических и фасонных поверхностей без применения фасонных резцов. Разместив в стойке вертикальных суппортов дополнительную опору для прутка (неподвижный люнет), на автоматах продольного точения можно обрабатывать с высокой точностью достаточно длинные детали небольшого диаметра (l/d < 10). При обработке заготовок из квадратного и шестигранного прутка используют вращающийся люнет. Шпиндель в автоматах продольного точения всегда вращается в одну сторону и имеет левое вращение. Поэтому правую резьбу на них нарезают методом обгона.
|
Одношпиндельные токарно-револьверные автоматы (1Е110П, 1Ц110П, 1Л116П, 1Е125П, 11Е140П, 1Е165П и др.) предназначены для обработки деталей сложной формы из прутков диаметром 10 — 63 мм; на полуавтоматах из штучных заготовок обрабатывают детали диаметром до 160 мм. Наличие в токарно-револь- верных автоматах трех (а в некоторых — и четырех) поперечных суппортов и продольного суппорта с шестипозиционной револьверной головкой (в которой помещают державки со сверлами, зенкерами, развертками, резцами, резьбонарезными и другими инструментами) значительно расширяет их технологические возможности. Передний поперечный суппорт является отрезным, а на заднем и вертикальном обычно устанавливают резцы для обработки фасок, канавок, фасонных поверхностей, накатные и другие инструменты. Большинство технологических переходов выполняется при более быстром левом вращении шпинделя, а нарезание резьбы, развертывание и некоторые другие переходы — при более медленном правом вращении шпинделя. Переключение вращения шпинделя осуществляется автоматически.
Многошпиндельные горизонтальные автоматы (1Б216, 1Б225, 1В225, 1Б240, 1Б265, 1Б290 и др.) предназначены для изготовления деталей из калиброванных прутков круглого, квадратного или шестигранного сечения из стали и цветных металлов диаметром 12—100 мм, длиной до 160 мм (в зависимости от модели автомата), а полуавтоматы — из штучных заготовок диаметром до 200 мм (в зависимости от модели). В качестве заготовок могут использоваться также трубы. На многошпиндельных горизонтальных автоматах и полуавтоматах обработка проводится последовательно на четырех, шести или восьми позициях по числу шпинделей станка. Восьми- шпиндельные автоматы и полуавтоматы можно настраивать на двойную индексацию, в этих случаях шпиндельный блок поворачивается сразу на две позиции.
|
Шестишпиндельные автоматы и полуавтоматы также выпускают с двойной индексацией, но в отличие от восьмишпиндельных, они не могут быть переналажены на обработку с одинарной индексацией. Для выполнения в составе автоматной операции таких работ как фрезерование шлицев и лысок на торцах и цилиндрических поверхностях деталей, сверление радиальных отверстий и др. предусматривается исполнение автоматов с остановом и фиксированным остановом отдельных шпинделей, а также исполнение их с независимой частотой вращения шпинделей. Многошпиндельные горизонтальные автоматы и полуавтоматы отличаются от одношпиндельных большей производительностью и позволяют вести обработку более сложных деталей, хотя точность обработки ниже.
Токарные одно- и многошпиндельные горизонтальные автоматы предназначены для обработки цилиндрических, конических, шаровых, фасонных поверхностей вращения.
На базе одношпиндельных токарно-револь- верных, фасонно-отрезных, продольного точения и многошпиндельных автоматов возможна обработка штучных заготовок в автоматическом цикле при механизации и автоматизации загрузки и выгрузки заготовок либо в полуавтоматическом цикле с ручной загрузкой. Переналадка автомата или полуавтомата на обработку другой детали занимает не менее 3 — 5 ч, поэтому применять эти станки целесообразно только в случае длительной обработки одной партии деталей; переналадка на обработку других деталей ранее чем через 30 — 45 ч непрерывной работы не рекомендуется.
При расчете наладок в операционно-нала- дочной карте приводят схему наладки станка по переходам, расчет режимов резания и производительности. При проектировании наладок для повышения производительности и удобства наладки станка, а также для снижения брака при наладке следует по возможности применять быстросменные наладки-блоки и наладку инструментов на размер вне станка с использованием измерительных приспособлений.
На одношпиндельных токарно-револь- верных автоматах и полуавтоматах наружные поверхности обрабатывают с помощью продольных и поперечных суппортов. Обработку с продольной подачей осуществляют с револьверной головки инструментальным шпинделем или специальными приспособлениями. Конусные поверхности можно обработать цри применении копирных державок либо инструментами, установленными в специальной державке поперечного суппорта; продольное перемещение осуществляется револьверной головкой. Резьбу нарезают с револьверной головки метчиками, плашками и, главным образом, самооткрывающимися головками. Сверление отверстий и зацентровку выполняют с револьверной головки. Соответствующие скорости резания и подачи при сверлении глубоких отверстий малого диаметра обеспечиваются приспособлениями для быстрого сверления. Развертывание, растачивание, цекова- ние торцов производят с продольного суппорта.
|
Точность обработки на токарных автоматах и полуавтоматах достигается с допуском 0,03 — 0,06 мм по диаметру и 0,08 — 0,15 мм по линейным размерам. В некоторых случаях при применении специальной технологической оснастки может быть достигнута более высокая точность.
Параметр шероховатости поверхности при обработке на автоматах и полуавтоматах Ra = 5 -г 1,25 мкм.
Разрабатывая наладки на одношпин- дельные автоматы и полуавтоматы, следует совмещать работу инструментов, размещенных на поперечном суппорте и в револьверной головке, не совмещать обдирочную обработку с чистовой, не ослаблять сечение детали на первых переходах обработки во избежание вибрации и отжатий при последующих переходах.
Во избежание нестабильности размеров и появления уступов на обработанной поверхности необходимо совмещать моменты начала и окончания работы различных инструментов. Окончательную обработку наружных поверхностей тонкостенных деталей следует предусматривать после обработки отверстий, так как при сверлении, зенкеровании и развертывании отверстий наблюдается увеличение наружных размеров. С целью получения малых параметров шероховатости поверхности и стабильных размеров деталей при обработке фасонными резцами с поперечных суппортов необходимо пользоваться упором для зачистки; центровочные сверла следует задерживать в конце подачи на несколько оборотов для зачистки.
|
Обтачивание наружных цилиндрических поверхностей револьверной головкой целесообразно совмещать с обработкой отверстий, а обработку фасок и наружных торцов деталей совмещать с отрезкой; совершенно недопустимо совмещение отрезки с обдирочными или другими переходами, требующими больших сил. Резьбу следует нарезать после обдирочных переходов, но при неослабленной детали во избежание скручивания. В резьбовых отверстиях, нарезаемых метчиком, для компенсации погрешностей наладки и размещения стружки необходимо предусмотреть зазор между дном отверстия и торцом метчика в конечном положении длиной не менее трех витков резьбы. Для предотвращения поломок сверл при обработке глубоких отверстий требуется осуществлять прерывистую подачу.
При наличии свободных гнезд для инструментов в револьверной головке выгодно длину сверления распределить на несколько позиций.
В случаях обработки штучных заготовок малой жесткости на полуавтоматах для обеспечения точности и уменьшения влияния сил зажима на деформацию детали целесообразно использовать зажимные приспособления, обеспечивающие при черновых переходах большую силу, затем разжим и зажим с меньшими силами для чистовых переходов.
На многошпиндельных автоматах и полуавтоматах наружные поверхности обрабатывают как с продольных, так и с поперечных суппортов. С поперечных суппортов обрабатывают фасонные поверхности деталей, у которых длина контурной линии относительно диаметра невелика (l/d < 1,5), и окончательно обтачивают детали для получения точных линейных размеров. Длинные детали обтачивают с использованием люнетных державок.
В некоторых случаях для обработки широких деталей сложного профиля применяют ко- пирное приспособление, устанавливаемое вместо переднего поперечного суппорта. Отверстия обрабатывают с продольных суппортов, в которые устанавливают инструменты для центрования, сверления, зенкерования, развертывания, растачивания, снятия фасок. Выточки в отверстиях получают резцами, закрепленными в специальных державках. Резец получает поперечное перемещение после упора державки в неподвижную стойку. Внутренние конусные поверхности растачивают с помощью специальных качающихся державок с продольного суппорта.
Внутренние резьбы нарезают метчиками, наружные резьбы — самооткрывающимися головками с продольных суппортов. Накатывать резьбы можно как с продольных, так и с поперечных суппортов с помощью специальных головок. Рифления накатывают роликами с продольного и поперечного суппортов с применением люнетных державок. Детали отрезают с поперечного суппорта.
|
При проектировании наладок на автоматы и полуавтоматы необходимо стремиться к максимальному совмещению работы продольных и поперечных суппортов. При этом следует избегать совмещения обдирочных и чистовых переходов. Тяжелую обдирочную обработку рекомендуется выполнять в первую очередь, а окончательную доводочную обработку выносить на отдельные позиции. Для обработки фасонных поверхностей с точностью линейных размеров 0,08—0,15 мм и диаметральных размеров 0,08 — 0,2 мм следует применять не менее двух фасонных резцов — для черновых и чистовых переходов. При обработке многогранных прутков для облегчения последующей работы фасонных резцов целесообразно обдирочные операции осуществлять простыми резцами с продольного либо поперечного суппорта. Для обеспечения точных диаметральных размеров с допуском 0,03—0,05 мм необходимо использовать специальные качающиеся роликовые державки с бреющими резцами, работающие с поперечных суппортов.
При работе с поперечных суппортов для получения стабильных размеров детали следует предусматривать выдержку без подачи в течение 7—10 оборотов.
При особых требованиях к концентричности наружных и внутренних поверхностей окончательную их обработку рекомендуется выполнять на одной позиции.
Последовательность переходов обработки целесообразно назначать так, чтобы заготовка на первых позициях не была ослаблена протачиванием канавок или фасонных поверхностей около зажимного патрона.
Чтобы избежать появления рисок от резца на обработанной поверхности при обратном ходе суппортов, рекомендуется оставлять минимальные припуски на окончательную обработку, устанавливать резец несколько выше линии центров и совмещать окончательное обтачивание с отрезкой детали так, чтобы к моменту обратного хода суппорта деталь была отрезана. Для этих целей целесообразно применять специальные державки с «отскоком» резца при обратном ходе суппорта.
Нарезание резьбы на автомате нельзя совмещать в одной позиции с другими переходами, а иногда целесообразно выделять его в отдельную операцию.
Увода сверла можно избежать при применении предварительного центрования детали центровочным сверлом. Предварительное центрование полезно и при тяжелых поперечных нагрузках, когда короткое сверло служит в качестве поддерживающего центра в момент обработки других поверхностей.
При обработке ступенчатых отверстий рекомендуется вначале сверлить отверстия большего диаметра. Глубокие отверстия необходимо сверлить с перерывами, чтобы избежать заедания и поломки сверл.
Отрезку детали можно совмещать с окончательными переходами. Для сокращения пути отрезного резца при отрезке жестких деталей выгодно предварительно осуществлять прорезку под отрезной резец; с этой же целью следует пропускать сверло на расстояние, превышающее длину детали.
Применяя специальные дополнительные механизмы с приводом от кинематической цепи станка, можно расширить технологические возможности токарных автоматов путем осуществления при обработке деталей дополнительных переходов, не выделяемых в так называемые доделочные операции. Так, на токарных автоматах осуществляют поперечное сверление, сверление и снятие фасок со стороны отрезки, фрезерование шлицев, прошивание фасонных отверстий, развальцовывание, накатывание клейм и др.
Сверление поперечных или эксцентрично расположенных отверстий, как правило, проводят с остановкой шпинделя.
Примеры наладок. На рис. 96 представлена схема наладки типовой детали из бунта на фасонно-отрезном автомате. После отрезки заготовки резцы 7 и 2 вращающейся головки отходят, и бунт подается вперед, выталкивая изготовленную деталь (рис. 96,а); затем бунт зажимается. Далее происходит быстрый подвод резца 1 (рис. 96,6) для обтачивания по диаметру 2,5 мм и фаски отрезаемой детали; резец 2 подрезает торец, отрезает деталь и обтачивает конус последуюшей детали.
Сталь 45 |
0,5*45 |
Рис. 96. Схема наладки типовой детали из бунта на фасонно-отрезном автомате |
Обработка типовой детали на автомате
Рис. 97. Схема наладки типовой детали на автомате продольного точения |
^ 'it tssi f If "у |
0,5 XU50
![]() |
Просриль 5 насечки |
Рис. 99. Наладка одношпиндель- ного токарно-револьверного автомата для обработки детали с насечкой по торцу |
![]() |
![]() |
п/ | |
Шг/ш* | ц |
![]() |
продольного точения (рис. 97) осуществляется путем последовательного чередования (переходы I—XIII) продольного перемещения шпиндельной бабки с прутком и поперечных перемещений резцов. Только на XIII переходе готовая деталь отрезается при одновременном перемещении прутка с бабкой и отрезного резца.
На рис. 98 представлена наладка одно- шпиндельного токарно-револьверного автомата для одновременной обработки деталей двух наименований. За пять (/ — V) переходов подачу прутка до упора проводят на длину двух деталей с припуском для отрезки. Отверстие диаметром 5 мм сверлят на глубину, которая обеспечивает получение фаски у следующей детали. Комбинированным отрезным резцом поочередно отрезают сначала первую деталь, затем вторую.
На рис. 99 показана наладка токарно-ре- вольверного автомата для обработки детали за шесть переходов с использованием роликового накатника, установленного в револьверной головке.
Наладка одношпиндельного токарно-ре- вольверного автомата для полной механической обработки детали за пять переходов показана на рис. 100. В наладку включены три «доделочные» операции. На переходе III при невращающемся шпинделе фрезеруют две лы- ски до размера 4,5 мм и сверлят отверстие диаметром 7 мм комбинированным сверлом. Сверление отверстия диаметром 6,6 мм и снятие фаски осуществляются с помощью вспо-
![]() |
![]() |
30°с двух сторон |
Рис. 102. Наладка четырехшпиндельного автомата для обработки гаек одинакового размера |
И |
![]() |
tv |
Ш
-—-"л
Й
Рис. 101. Наладка четырехшпиндельного автомата для одновременной обработки двух деталей
могательного устройства (переход IVa) после отрезки детали («обратная обработка»).
2^У0'73 |
Рис. 103. Наладка восьмишпиндельного автомата для обработки поршня тормозной пневмосистемы |
Наладка четырехшпиндельного автомата (рис. 101) позволяет рационально использовать обрабатываемый материал. На позиции / трубчатым сверлом высверливают среднюю часть прутка в виде стержня, из которого изготовляют втулку меньшего диаметра (на позициях II—IV). Аналогично этому обрабатывают другие мелкие детали (шпильки, штифты и т. п.).
На рис. 102 показана наладка четырехшпиндельного автомата для одновременной обработки трех гаек за один рабочий цикл.
Наладка восьмишпиндельного автомата (рис. 103) для обработки поршня тормозной пневмосистемы из латуни обеспечивает точность поверхностей с допуском 0,043 — 0,065 мм и параметр шероховатости Ra = 1,25 мкм. Обработка наружных поверхностей осуществляется в основном твердосплавным инструментом на скоростях резания до 145 м/мин. В наладке предусмотрено использова
ние специальных приспособлений для фрезерования лысок (позиция VII), нарезания резьбы гребенкой (позиция VI), обтачивания фасонным бреющим твердосплавным резцом с поддержкой роликом (позиция V). Внутренние поверхности обрабатываются ступенчатыми сверлами и развертками из быстрорежущей стали (позиции I, IV), а поверхности диаметром 24 мм и более — твердосплавным ступенчатым зенкером. На позиции VI с помощью специального приспособления проводится глубокое сверление отверстия диаметром 8+0'2 мм. На позиции VIII деталь перехватывается специальным цанговым зажимом, после чего отрезается без заусенцев на торце.
![]() |
На рис. 104 показана наладка шестишпин- дельного автомата для обработки пальца синхронизатора. Для обеспечения точности обработки на позиции IV применены бреющий фасонный резец и поддерживающий ролик. На позиции VI дополнительно установлены специальный цанговый зажимной патрон и приспособление для обработки с обратной стороны после отрезки детали (позиции VIa).
Наладка шестишпиндельного автомата для обработки специальной гайки (рис. 105) предусматривает применение приспособлений для фрезерования шлица на позиции III, для фрезерования внутренней канавки на позиции IV и нарезания резьбы на позиции V.
Наладка восьмишпиндельного автомата для обработки поршня резцами с механическим креплением неперетачиваемых пластин твердого сплава показана на рис. 106. Особенностью этой наладки является применение фрезерной головки на позиции V для фрезерования пазов. В момент фрезерования шпиндель останавливается. На позиции VIII осуществляется перехват детали в специальную головку, и поршень обрабатывается с обратной стороны.
![]() |
hi | кгТТНГЪ»-/! | ||
м Г | ГТ | ||
![]() |
На рис. 107 приведена наладка шестишпин- дельного автомата, в которой предусмотрен максимальный съем стружки на первых позициях. В последующих позициях проводится получистовая и чистовая обработка, а затем отрезка детали. Обработка наружного профиля ввиду необходимости снятия большого
объема стружки осуществляется с поперечных суппортов в пяти позициях, причем черновая обработка разбита на три перехода, которые выполняются в позициях I—III. Одновременно с обработкой наружного профиля отрезаемой детали выполняется и предварительное формирование торцовой поверхности следующей детали. Получистовое обтачивание торцов выполняется в позиции IV, где нет больших осевых сил, а чистовая точная обработка с помощью бреющей державки — в позиции V.
Отверстия сложной формы обрабатываются во всех шести позициях с продольного суппорта, причем для получения наименьшего рабочего хода продольного суппорта сверление разбито на три перехода, выполняемых в позициях I— III. В позиции I сверление предусматривается без предварительного центрования ввиду небольшой его глубины — 1,4 диаметра. Сверло должно быть комбинированным для образования фаски в отверстии, а его общий вылет не должен превышать четырех диаметров. В позиции II диаметр сверла на 0,2 мм меньше с целью устранения быстрого изнашивания по наружной поверхности, которое может быть вызвано отклонением от соосности с обрабатываемой деталью. В позиции III сверлится отверстие под резьбу; учитывая его малый диаметр, для обеспечения благоприятных режимов резания применено быстросверлильное устройство. Предварительно просверленное отверстие создает направление для сверла в этой позиции.
![]() |
Ш и ш'5 |
![]() |
В позиции IV установлен зенкер для получистовой обработки отверстия под развертку и снятия ступеньки от применения сверл разных диаметров. Рабочий ход зенкера должен быть вдвое больше рабочего хода продольного суппорта, что обеспечивается применением устройства с независимой подачей от кулачков инструментального барабана. В позиции V чистовая обработка отверстия проводится разверткой. При этом используется устройство с независимой подачей для получения нужной длины рабочего хода. В позиции VI нарезаются резьбы, для чего устанавливается резьбона
резное устройство с реверсированием и применяется независимая подача инструмента. После выхода из детали резьбонарезного инструмента заканчивается ее отрезка.
На рис. 108 представлена наладка горизонтального шестишпиндельного полуавтомата для обработки корпусной детали из штучной заготовки. Заготовка из алюминиевого сплава, полученная методом точного литья, обрабатывается на расточном станке, на котором обтачивается базовый поясок и торец, после чего она поступает на полуавтомат. В наладке применены специальные приспособления для отвода резца при обратном ходе во избежание получения рисок и повреждения поверхностей при обтачивании по наружному диаметру 104 + 0 20 мм> растачивании отверстии диаметром 64 + 0'074 и 65 + 0'074 мм на позициях III и IV. Для обеспечения малого параметра шероховатости поверхностей диаметром 64 и 65 мм на позиции VI в шпинделе с независимой подачей применена двухступенчатая раскатка. Предусмотрены также резцы с механическим креплением неперетачиваемых твердосплавных пластин с наладкой на размер вне станка на специальных приспособлениях. Режим резания: скорость резания 500 м/мин; подача 0,01—0,16 мм/об; цикл обработки детали составляет 37 с.
0J6 |
Рис. 108. Наладка шестишпин- дельного полуавтомата для обработки корпусной детали с высокими требованиями по точности и шероховатости |
Для обтачивания длинных деталей из штучных заготовок (рис. 109) требуются лю-
1 н | ||
ни | J |
![]() |
![]() |
10 Под ред. А. Г. Косиловой и Р. К. Мещерякова
![]() |
![]() |
нетные державки (позиция II). Шейки диаметром 9,27_о,о9 и Ю,27_о,о9 мм обтачивают бреющими резцами на позициях III и IV.
![]() |
На рис. 110 показана двухиндексная наладка восьмишпиндельного полуавтомата для полной токарной обработки заготовок зубчатых колес с двух сторон. На позициях III, V, VII проводится обработка в патроне отверстия, торцов и фасок с одной стороны, затем на позиции II заготовку устанавливают по обработанным отверстию и торцу, и в позициях IV, VI, VIII ведется обработка наружной поверхности, торцов и фасок с другой стороны.
Наладки шестишпиндельных полуавтоматов для обработки штучных заготовок промежуточных зубчатых колес представлены на рис. 111. Требования по точности и параметрам шероховатости высоки. Для обеспечения указанных требований на позиции V обоих станков применены при первом зажиме раскатка (рис. 111, л), а также специальное приспособление для окончательного обтачивания и выглаживания сферы (рис. 111.6).
ОБРАБОТКА
|
|
Механическое удерживание земляных масс: Механическое удерживание земляных масс на склоне обеспечивают контрфорсными сооружениями различных конструкций...
Состав сооружений: решетки и песколовки: Решетки – это первое устройство в схеме очистных сооружений. Они представляют...
Архитектура электронного правительства: Единая архитектура – это методологический подход при создании системы управления государства, который строится...
История создания датчика движения: Первый прибор для обнаружения движения был изобретен немецким физиком Генрихом Герцем...
© cyberpedia.su 2017-2024 - Не является автором материалов. Исключительное право сохранено за автором текста.
Если вы не хотите, чтобы данный материал был у нас на сайте, перейдите по ссылке: Нарушение авторских прав. Мы поможем в написании вашей работы!