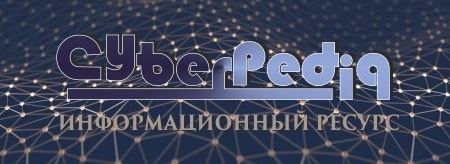
Состав сооружений: решетки и песколовки: Решетки – это первое устройство в схеме очистных сооружений. Они представляют...
Индивидуальные очистные сооружения: К классу индивидуальных очистных сооружений относят сооружения, пропускная способность которых...
Топ:
Основы обеспечения единства измерений: Обеспечение единства измерений - деятельность метрологических служб, направленная на достижение...
Особенности труда и отдыха в условиях низких температур: К работам при низких температурах на открытом воздухе и в не отапливаемых помещениях допускаются лица не моложе 18 лет, прошедшие...
Марксистская теория происхождения государства: По мнению Маркса и Энгельса, в основе развития общества, происходящих в нем изменений лежит...
Интересное:
Финансовый рынок и его значение в управлении денежными потоками на современном этапе: любому предприятию для расширения производства и увеличения прибыли нужны...
Лечение прогрессирующих форм рака: Одним из наиболее важных достижений экспериментальной химиотерапии опухолей, начатой в 60-х и реализованной в 70-х годах, является...
Принципы управления денежными потоками: одним из методов контроля за состоянием денежной наличности является...
Дисциплины:
![]() |
![]() |
5.00
из
|
Заказать работу |
Содержание книги
Поиск на нашем сайте
|
|
Виды статистического регулирования процессов. Задача статистического регулирования технологического процесса состоит в том, чтобы на основании результатов периодического (т.е. в динамике) контроля выборок относительно малого объема оценивать его стабильность и корректировать наладку процесса на требуемое качество.
Имеется две разновидности регулирования процессов: по количественному и альтернативному (качественному) признакам. Для каждой из разновидностей разработаны свои статистические методы регулирования.
Регулирование (или контроль) по количественному признаку заключается в определении с требуемой точностью фактических значений контролируемого параметра у отдельных представителей (выборки) продукции. Затем по фактическим значениям параметра определяются статистические характеристики процесса и по ним принимаются решения о состоянии технологического процесса. Такими характеристиками являются выборочное среднее, медиана, размах и выборочное среднее квадратическое отклонение. Первые две характеристики – характеристики положения, а последние две – характеристики рассеяния СВ X.
Регулирование (или контроль) по альтернативному признаку заключаются в определении соответствия контролируемого параметра или единицы продукции установленным требованиям(годная/дефектная). При контроле по альтернативному признаку не требуется знать фактическое значение контролируемого параметра – достаточно установить факт соответствия или несоответствия его установленным требованиям. Поэтому для контроля можно использовать простейшие средства: шаблоны, калибры и др. Решение о состоянии технологического процесса принимается в зависимости от числа дефектов или числа дефектных единиц продукции, выявленных в выборке.
|
Каждый из перечисленных способов регулирования (контроля) имеет свои преимущества и свои недостатки. Так, преимущество контроля по количественному признаку состоит в том, что он более информативен и поэтому требует меньшего объема выборки. Однако такой контроль более дорогой, поскольку для него необходимы такие технические средства, которые позволяют получать достаточно точные фактические значения контролируемого параметра. Кроме того, для статистического регулирования при контроле по количественному признаку необходимы (иногда сложные) вычисления, связанные с определением статистических характеристик.
Преимущество контроля по альтернативному признаку заключается в его простоте и относительной дешевизне, так как можно использовать простейшие средства контроля или даже визуальный контроль. К недостаткам такого контроля относится его меньшая информативность, что требует большого объема выборки при равных исходных данных.
Методы регулирования процессов. В настоящее время существует несколько методов статистического регулирования технологических процессов. Наиболее распространенный и эффективный из них – метод с использованием контрольных карт (карт Шухарта), на которых отмечают границы регулирования, ограничивающие область допустимых значений, вычисленных на основании статистических данных. Выход точки за границы регулирования (или появление её на самой границе) служит сигналом о разладке технологического процесса. Контрольная карта позволяет не только обнаружить какие-то отклонения от нормального хода процесса, но и в значительной степени объяснить причины этого отклонения.
Существуют следующие виды контрольных карт:
средних арифметических значений ( – карта), медиан (
– карта), средних квадратических отклонений (S – карта), размахов (R – карта), числа дефектных изделий (
n – карта), доли дефектных изделий (Р – карта),числа дефектов (С – карта), числа дефектов на единицу продукции (U – карта).
|
Первые четыре вида контрольных карт применяют при контроле по количественному признаку, а последние четыре – при контроле по альтернативному признаку. Выбор контрольных карт определяется серийностью, точностью процессов и видом показателей качества продукции.
Контрольная карта – R применяется при измерении таких регулируемых показателей, как длина, масса, время, предел прочности, прибыль и т.д. Рекомендуется также ее использование при регулировании процессов изготовления продукции в серийном и массовом производстве, на технологических процессах с запасом точности, при показателях качества распределенных по закону Гаусса или Максвелла.
Контрольная карта Р применяется при контроле и регулировании технологического процесса на основе использования доли дефектных изделий, полученной делением числа обнаруженных дефектов на число проверенных изделий. Эту карту также можно использовать для определения интенсивности выпуска продукции, процента неявки на работу и т.д.
Контрольная карта nприменяется для контроля в случаях, когда контролируемым параметром является число дефектных изделий при постоянном объеме выборки n.
На первых этапах статистических методов регулирования часто используются гистограммы для предварительного исследования состояния технологического процесса.
19. Показатели качества
Система показателей качества продукции необходима для отражения экономической сущности качества через технические характеристики и свойства. Показатель качества – это количественное выражение одного или нескольких характеристик или свойств объекта применительно к определенным условиям его создания и эксплуатации.
Наиболее широко в практике оценки уровня качества используются единичные показатели, имеющие отношение к одному из свойств (характеристик) качества продукции. Единичные показатели легко поддаются сравнению и контролю:
Рассмотрим структуру эксплуатационных показателей:
· - показатели назначения (коэффициент полезного действия машины, производительность, потребляемая мощность, степень автоматизации),
· - показатели надежности,
· - эргономические показатели (учитывают антропометрические, биомеханические, инженерно-психологические свойства человека, проявляющиеся в эксплуатации объекта или в производственном процессе)
|
· - эстетические показатели,
· - экологические показатели,
· - патентно-правовые,
· - прочие.
К производственно-технологическим показателям относятся следующие: трудоемкость, материалоемкость, энергоемкость, стандартизации и унификации, блочность. Набор отдельных производственно-технологических показателей (трудоемкость, материалоемкость, энергоемкость) напрямую определяет величину издержек производства в себестоимости продукции, а значит и экономические показатели ее качества. Блочность – характеризует сложность работы по монтажу оборудования, состоящего из сборок, и определяется отношением числа специализированных (приспособленных) сборок к общему числу частей.
К экономическим показателям относятся капиталовложения в производство, капиталовложения в эксплуатацию, себестоимость единицы продукции, отпускная или рыночная цена, прибыль, рентабельность
Больший интерес представляют показатели надежности, к которым относятся безотказность, долговечность, ремонтопригодность, сохраняемость. Эти показатели входят в число важнейших показателей качества объекта, особенно если последний работает в динамическом режиме (например, транспортные средства, турбины и генераторы, двигатели и т.д.). Безотказность – свойство объекта выполнять заданные функции, сохраняя свои эксплуатационные параметры в заданных пределах в течение требуемого времени (например, средняя наработка на отказ, гарантийная наработка и т.д.). Долговечность – свойство объекта, характеризующее срок службы с учетом физического и морального износа до первого капитального ремонта (например, ресурс, средний срок службы, срок службы до первого капремонта и т.д.). Ремонтопригодность заключается в приспособленности объекта к предупреждению, обнаружению и устранению отказов и неисправностей (например, среднее время восстановления, средняя трудоемкость ремонтов и т.д.). Сохраняемость – свойство объекта сохранять обусловленные показатели в течение и после срока хранения и транспортирования (например, срок сохраняемости).
|
Показатели, характеризующие процесс, следует выбирать, исходя из следующих требований:
1. Адекватность, полнота и объективность отражения существующего положения дел;
2. Возможность сбора и обработки данных с установленной периодичностью;
3. Трудозатраты на сбор и обработку не превышают ценности информации
(полезность сбора данных);
4. Система показателей должна охватывать качественные и количественные
характеристики процесса;
5. Форма представления информации должна быть максимально понятной;
6. Информация должна быть сравнима с аналогичной.
Показатели, необходимые для управления процессом, можно получить из существующей в каждой организации системы управленческого учета. Для того чтобы эта система отвечала всем требованиям, которые предъявляет процессный подход к управлению, показатели процесса должны быть сгруппированы по трем основным направлениям:
• показатели продукта;
• показатели эффективности процесса;
• показатели (данные) удовлетворенности клиента;
Показатели продукта
Кпоказателям продукта относятся все параметры, которые характеризуют продукт.
1. Функциональные показатели: количество функций продукта; полнота функций продукта; диапазон параметров; сравнение с мировыми образцами продукта (услуги), бенчмаркинговая оценка выпускаемого продукта по сравнению с лучшими мировыми образцами; количество пунктов требований клиента, выполненных полностью.
2. Характеристики надежности: гарантийный срок; гарантированный сервис; наработка на отказ; гарантированное количество ошибок (дефектов при массовой поставке, AQL — Acceptable Quality Level — приемлемый уровень качества).
3. Показатели безопасности: экологические показатели; наличие сертификатов соответствия для обязательной сертификации товаров и услуг; фактические показатели безопасности товаров и услуг.
4. Наличие дополнительных услуг: «пакетные» закупки или сервис; скидки для постоянных или оптовых клиентов; премии для клиентов; послепродажный сервис; другие способы поддержки клиента (юридическая, техническая, аудиторская, инвестиционная, кредитная и др.).
Показатели эффективности процесса
1. Показатели затрат ресурсов: времени (цикл, длительность, производительность, скорость выполнения заказов); материальные (расходы средств, материалов, бюджеты подразделений, дебиторская и кредиторская задолженности, объемы «замороженного» капитала в виде складских запасов сырья или неликвидов).
2. Затраты на брак:
предупреждение на этапах разработки и производства; проведение альтернативных расчетов, проектов и испытаний; отбраковка в процессе производства;
|
исправление, доработка или переделка продукции (услуги), забракованной по результатам контроля;
замена и возврат брака, компенсация потребителю понесенного ущерба, а также транспортных и таможенных расходов.
3. Затраты на обучение, подготовку, повышение квалификации и аттестацию персонала.
4. Эффективность использования ресурсов на единицу продукции: коэффициенты использования оборудования, ресурсов, сырья, материалов, времени на проведение единицы работ или услуг).
Показатели (данные) удовлетворенности клиента
Данные удовлетворенности клиента продукцией (услугами) организации можно получить двумя способами:
- анкетирование представителей клиента, потребителя или заказчика по специально созданным анкетам;
- анализ взаимоотношений с клиентами, потребителями и поставщиками на основании собственных данных (косвенная оценка удовлетворенности).
Анкетирование клиентов. Данные удовлетворенности клиентов проще всего получать анкетированием клиентов, заказчиков и конечных потребителей. Для этих целей рассылают анкету в которой просят ответить в какой-либо форме о степени удовлетворенности продукцией и взаимоотношениями с организацией-поставщиком. При проведении опроса в анкету часто включают оценку значимости для клиента данного параметра.
Методы получения такой информации от клиентов разнообразны:
• рассылка анкет по почте, электронной почте (E-mail), факсу;
• заполнение анкет при телефонном опросе клиентов;
• проведение интервью с представителями руководства и клиента (при этом дополнительную информацию можно получить, если оценки работы вашей компании представителями руководства и клиента расходятся).
Косвенная оценка удовлетворенности клиентов. Несмотря на кажущуюся сложность этой оценки, зачастую она бывает более объективна, чем оценка методом анкетирования. Все основные данные для проведения такой оценки у организации имеются и доступны для регулярной обработки.
Косвенно степень удовлетворенности клиента можно оценить по следующим показателям:
1. Рост объема продаж продукции (услуг). Этот показатель может колебаться около среднего значения, поэтому для его адекватной оценки лучше воспользоваться тренд-анализом или регрессионным анализом. Во многих отраслях спрос на продукцию носит сезонный характер, поэтому для адекватной оценки необходимо учитывать фактор сезонности. Такой учет проводят двумя способами:
• сопоставлением — отношением величин объема продаж за отчетный период к величине объема продаж за аналогичный период прошлого года; сглаживанием — величиной суммарного объема продаж за последние 12 мес, включая отчетный, вне зависимости от фактора сезонности.
3. Длительность деловых связей. Этот показатель растет при стабильной работе на рынке с постоянными клиентами и снижается, если компания теряет постоянных клиентов или часто обновляет их состав. С другой стороны, этот показатель совершенно непригоден в случае поставщика-монополиста и потре
3. Число (процент) постоянных клиентов. Введение этого показателя потребует определения, кого считать постоянными клиентами компании, какой срок сотрудничества можно принять за критерий постоянства. Для молодых компаний с быстрым оборотом средств такой срок может быть равен 1—2 года. Для компаний с длительной историей срок может достигать 10—15 лет и т. д.
4. Количество претензий, рекламаций, жалоб, замечаний. Наличие учета претензий и рекламаций является одним из обязательных условий в организации, которая стремится достичь успеха. Очень часто клиент перед заключением крупного или важного контракта проверяет, проводится ли такой учет и работа по устранению причин рекламаций.
5. Число (процент) клиентов, «потерянных» за период времени. Данный показатель не всегда отражает реальную картину улучшения или ухудшения общего успеха организации, так как, пользуясь методами CRM (Custom Relationship Management), организация может осознанно сокращать число клиентов, отказываясь от невыгодных.
6. Доля рынка по продукту (услуге). Измеряется, как правило, в процентах от общей емкости сегмента рынка. Показатель позволяет организации оценить свое положение в данном сегменте рынка.
7. Число «имиджевых клиентов». Показатель используется в основном при оценке деятельности всей организации или служб маркетинга и сбыта. Измеряется числом клиентов, которые повышают имидж организации, и упоминание о них является для организации хорошей рекламой. В дореволюционной России, например, существовало почетное звание «Поставщик Императорского двора». Сегодня компании гордятся своими поставками для таких корпораций, как «Тойота», «Сони», «Мерседес»
Методы сбора данных
контрольный листок – бумажный бланк, на котором заранее напечатаны контролируемые параметры, с тем, чтобы можно было легко и точно записать данные наблюдений или измерений. Его назначение имеет две цели: облегчить процесс сбора данных и упорядочить их для последующей обработки.
Рассмотрим некоторые типы контрольных листков в зависимости от назначения сбора информации.
Контрольный листок для регистрации видов дефектов. При обнаружении дефекта ставится метка в строке, соответствующей обнаруженному дефекту. В нижней части листка ставится метка каждой дефектной детали (чтобы учесть не только кол-во дефектов, но и кол-во дефектных деталей). К недостаткам этого листка можно отнести невозможность проведения расслоения данных. Это недостаток можно компенсировать заполнением контрольного листка причин дефектов. Очевидно, что анализ причин дефектов при такой регистрации данных значительно облегчается.
Контрольный листок локализации дефектов. Такого типа контрольные листки полезны для диагноза процесса, поскольку причины дефектов часто можно найти, только исследуя места их возникновения.
Контрольный листок для регистрации распределения измеряемого параметра позволяет выявить изменения в размерах детали. Как правило, такие листки заполняются для анализа стабильности технологического процесса путем построения гистограмм. Форма: размер, отклонение, результат, частота, примечание.
контрольных карты явл-ся как методом сбора, так и методом анализа данных. Для управления процессом с помощью контрольных карт надо проверить, приемлема ли его воспроизводимость, т.е. определить, стабилен ли процесс и указывает ли диапазон варьирования показателя качества на карте на удовлетворительное согласование с требованиями документации. Если оказывается, что процесс неадекватен, и показатель качества находится в неконтролируемом состоянии, надо проработать план проведения экспериментов, позволяющих выявить причины отклонений и преодолеть ненормальность в рамках действующих контрольных границ, одновременно улучшая процесс.
Если контрольная карта показывает, что процесс после улучшения находится в желаемом состоянии, то принятые новые контрольные границы и вводятся для управления процессом.
Существуют следующие виды контрольных карт: средних арифметических значений ( – карта),медиан (
– карта),средних квадратических отклонений (S – карта),размахов (R – карта),числа дефектных изделий (
n – карта),доли дефектных изделий (Р – карта),числа дефектов (С – карта),числа дефектов на единицу продукции (U – карта).
Первые четыре вида контрольных карт применяют при контроле по количественному признаку, а последние четыре – при контроле по альтернативному признаку. Контрольная карта позволяет не только обнаружить какие-то отклонения от нормального хода процесса, но и в значительной степени объяснить причины этого отклонения. Выбор контрольных карт определяется серийностью, точностью процессов и видом показателей качества продукции.
Контрольная карта –R применяется при измерении таких регулируемых показателей, как длина, масса, время, предел прочности, прибыль и т. д. Рекомендуется также ее использование при регулировании процессов изготовления продукции в серийном и массовом производстве, на технологических процессах с запасом точности, при показателях качества распределенных по закону Гаусса или Максвелла.
Контрольная карта Р применяется при контроле и регулировании технологического процесса на основе использования доли дефектных изделий, полученной делением числа обнаруженных дефектов на число проверенных изделий. Эту карту также можно использовать для определения интенсивности выпуска продукции, процента неявки на работу и т. д.
Контрольная карта применяется для контроля в случаях, когда контролируемым параметром является число дефектных изделий при постоянном объеме выборки n.
На первых этапах статистических методов регулирования часто используются гистограммы для предварительного исследования состояния технологического процесса.
Методы анализа данных
Диаграмма (блок-схема) потока процессов (ДПП). Для повышения качества технологических процессов необходимо выявлять и устранять причины несоответствий показателей процесса установленным требованиям. Во многих случаях эти несоответствия заложены в нарушении последовательности операций (или переходов) или подмене звеньев процесса. Очевидно, что оценка несоответствий возможна только в случае анализа реального (а не проектного) процесса. Обычно для построения и дальнейшего анализа блок-схемы процесса привлекаются лица, в нем задействованные, т.е. исполнители процесса. В то же время причины несоответствий могут быть заложены и в проектной схеме процесса, и возможное изменение его последовательности или замена отдельных звеньев может стабилизировать процесс. Для тщательного анализа процесса и строится его диаграмма (блок-схема), приведенная на рис. 4.9.
Желательно в диаграмме воспроизвести все элементы процесса, в том числе места, в которых принимаются решения, а также порядок документирования той или иной операции, наличие базы данных или появление дополнительной информации о процессе. Таким образом, диаграмма потока процесса – не просто перечень и последовательность технологических звеньев, но и сопровождающая их технологическая и контрольная информация. Анализируя ДПП, желательно ответить на ряд следующих вопросов:
- можно ли изменить ту или другую операцию за счет применения другой технологии, оборудования или изменения методов работы,
- можно ли сократить время процесса,
- можно ли сократить затрачиваемые ресурсы,
- можно ли уменьшить число транспортировок,
- можно ли совместить операции и т.д.
Для снижения затрат при отладке процесса важно не дожидаться появления несоответствий в реальном процессе, а провести анализ блок-схемы процесса еще в проектном варианте.
Анализ Парето. Особенно важно выявить причины несоответствий, приводящие к большим экономическим потерям. Для этого сначала целесообразно провести ранжирование несоответствий (дефектов) по их потенциальному ущербу производству.
Одним из наиболее распространенных на практике методов выявления наиболее значимых (по затратам) дефектов является анализ Парето. Сущность анализа Парето заключается в выявлении таких дефектов, на поиске причин которых необходимо сосредоточить особое внимание. При этом действует правило Парето, что 80% всех дефектов вызвано небольшим числом причин.
Очевидно также, что для производственников важно прояснить картину распределения дефектов и потерь, вызванных отбраковкой продукции, где эти дефекты проявятся. Конечно, важно устранить причины наиболее многочисленных дефектов. Но в отдельных ситуациях еще важнее выявить причины появления пусть немногочисленных, но приводящих к большим производственным издержкам дефектов. Для этого применяется одна из разновидностей анализа Парето – метод АВС (кривая Лоренца).
По рез-там деят-ти диаграмма Парето отражает дефекты, рекламации, срывы сроков поставок, несчастные случаи. Готовится и заполняется контрольный листок для регистрации видов дефектов, оформляется бланк для построения диаграммы: дефект, кол-во, накопленное кол-во, накопленный %.
Диаграмма Исикавы. Выявить основные источники брака, еще не значит определить его причины. А причин может быть много, так же как и множество факторов, вызывающих эти причины. Прежде, чем искать причины, необходимо обозначить наиболее вероятные факторы, которые эти причины инициируют.
На втором этапе команда специалистов методом «мозгового штурма» выделяет наиболее вероятные (главные и второстепенные) причины отклонений показателя качества. Создание команды не исключает привлечения к обсуждению проблемы других специалистов функциональных подразделений или работников подразделения, в котором сформировалась проблема.
На третьем этапе производится сортировка причин по их предполагаемой значимости (вероятности). При сортировке можно использовать диаграмму Парето с целью экспериментальной проверки в первую очередь тех вероятных причин, суммарная значимость которых превышает 75-80 %.
На четвертом этапе разрабатываются мероприятия по экспериментальной проверке этих причин. При планировании экспериментов необходимо подбирать контрольные партии образцов с учетом расслоения вероятных факторов. Анализ и проверка продолжаются, пока не будут выяснены истинные причины отклонения показателя. При длительных безуспешных поисках выделенных причин целесообразно вернуться к диаграмме и определить новые направления поиска. Процесс поиска можно считать законченным, если издержки производства по данному показателю качества снизились в 2-5 раз.
Гистограмма. Строится на основе контр. листка для регистрации распределения контролируемого параметра, показывает частоту попадания значений контролируемого параметра в заданные интервалы. Наиболее эффективным способом исследования распределения размера параметра является построение гистограммы. Гистограмма распределения – это графическое отображение вариабельности процесса. Для построения гистограммы необходимо собрать необходимые данные о процессе.
На основе этих данных строится график рассеяния фактических размеров столбчатого типа – гистограмма (рис. 4.6).
По этим данным легко построить кривую нормального распределения, наложив ее на график рассеяния фактических размеров (гистограмму).
Величина заштрихованной площади поверхности в границах поля допуска, отнесенная ко всей площади кривой нормального распределения, определяет вероятность Р(D) изготовления деталей, находящихся в поле допуска (по диаметру ролика). А отсюда вытекает, что вероятность брака (несоответствия допуску) равна 1 – Р(D).
Имеются и другие методы оценки точности технологического процесса. Один из них связан с определением индекса воспроизводимости процесса Ср[1], характеризующего соотношение поля рассеяния щ и поля допуcка Т:
Сравнение гистограммы с границами допуска. При сравнении и анализе величин и взаимного положения полей допуска и рассеивания можно выделить 5 типичных вариантов.
Первый вариант. Поле рассеивания значительно меньше поля допуска, w < T. Технологический процесс протекает нормально, требуется только поддерживать существующее состояние.
Второй вариант. технологический процесс протекает нормально, но нет запаса надежности. Можно провести мероприятия по уменьшению поля рассеивания, если затраты на эти мероприятия будут меньше, чем потери от возможного брака.
Третий вариант. (рис.10.11, в). Процесс ненормальный. Необходимо добиться смещения середины поля рассеивания к центру поля допуска.
Четвертый вариант. (w > T) и размещено симметрично относительно центра поля допуска (рис.10.11, г). Процесс ненормальный. Необходимо провести мероприятия по уменьшению поля рассеивания. Пятый вариант. Поле рассеивания больше поля допуска и смещено относительно центра допуска (рис.10.11, д). Процесс ненормальный. Это худший вариант взаимного положения полей, при котором количество забракованных изделий возрастает.
Диаграмма рассеяния. Предназначена для изучения связи между 2 показателями.
Стратификация данных. Для стратификации удобен метод 5М: провести стратификацию по квалификации работников (men), по используемому оборудованию, по материалам, по технологии изготовления, по методам и средствам измерения.
контрольных карты явл-ся как методом сбора, так и методом анализа данных. Для управления процессом с помощью контрольных карт надо проверить, приемлема ли его воспроизводимость, т.е. определить, стабилен ли процесс и указывает ли диапазон варьирования показателя качества на карте на удовлетворительное согласование с требованиями документации. Если оказывается, что процесс неадекватен, и показатель качества находится в неконтролируемом состоянии, надо проработать план проведения экспериментов, позволяющих выявить причины отклонений и преодолеть ненормальность в рамках действующих контрольных границ, одновременно улучшая процесс.
Если контрольная карта показывает, что процесс после улучшения находится в желаемом состоянии, то принятые новые контрольные границы и вводятся для управления процессом.
Существуют следующие виды контрольных карт: средних арифметических значений ( – карта),медиан (
– карта),средних квадратических отклонений (S – карта),размахов (R – карта),числа дефектных изделий (
n – карта),доли дефектных изделий (Р – карта),числа дефектов (С – карта),числа дефектов на единицу продукции (U – карта).
Семь новых инструментов УК
Совершенствование менеджмента качества привело к разработке новых инструментов руководства качеством, включающего системный подход к организации «мозгового штурма», который применяется, когда требуется выбрать неординарный путь решения проблемы. Таким неординарным подходом является подключение к решению задачи коллектива специалистов, то есть «коллективного разума». Семь новых инструментов УК обеспечивают понимание сложных ситуаций и позволяют обеспечить задачу УК путем улучшения процесса проектирования продукции или услуги. Инструменты усиливают процесс планирования благодаря их способности:
- уяснять задачи;
- устранять недостатки;
- содействовать распространению и обмену инф-ей м/д заинтересованными сторонами;
- использовать бытовую лексику и позволяют вырабатывать оптимальные решения в кратчайшие сроки.
Диаграмма сродства и диаграмма связей обеспечивают общее планирование, диаграмма дерева, матричная диаграмма и матрица приоритетов обесп-ют промежуточное планирование. Блок-схема процесса принятия решения и стрелоч.диаграмма - детальное планирование.
Последовательность применения методов м.б. различной в зависимости от поставленной цели. Эти методы можно рассматривать и как отдельные инструменты, и как систему методов. Каждый метод может находить свое самостоятельное применение в зависимости от того, к какому классу отн-ся задача.
Использование инструментов УК позволяет экономить ресурсы и, тем самым, улучшает чистую прибыль компании.
«+» наглядность, простота освоения и применения; богатый наглядный язык, позволяющий пользователю легко исслед-ть и анализ-ть различные процессы.
«-» низкая эффективность при проведении анализа сложных процессов.
1. Диаграмма сродства. Этот этап представляет собой процесс генерирования группой специалистов идей по решению какой-то проблемы, высказываемых на основе ассоциативных впечатлений от идеи предыдущего участника «штурма», и фиксации этих идей. «Круги мозгового штурма» сцепляются или расходятся, в зависимости от их сродства, т.е. взаимозависимости.
2. Граф связей - инструмент, позволяющий выявить логические связи м/д основной идеей, проблемой и различными факторами влияния.
3. Диаграмма «дерево» - инструмент стимулирования процесса творческого мышления, способствующий систематическому поиску наиболее подходящих и эффективных средств решения проблемы; необходимо выстроить в логически упорядоченную, иерархическую структуру.
4. Матричная диаграмма - Идеи, переведённые в инженерные характеристики, формируются в упорядоченные таблицы. Обычно исп-ся двумерные матрицы в виде таблиц со строками и столбцами.
5. Матрица приоритетов – инструмент для обработки большого кол-ва числовых данных, полученных при построении матричных диаграмм, с целью выявления корреляционной зависимости между характеристиками.
6. Блок-схема процесса принятия решения – инструмент, который помогает запустить механизм непрерывного планирования. Его использование способствует уменьшению риска практически в любом деле. Планирует каждый мыслимый случай, который может произойти, перемещаясь от утверждения проблемы до возможных решений.
7. Сетевой график или стрелочная диаграмма – инструмент, позволяющийпланировать оптимальные сроки выполнения всех необх-ых работ для реализации поставленной цели и эффективно их контролировать. является распространённым подходом при выборе кратчайшего (по времени) пути для практической реализации решения.
23. QFD Структурирование функции качества (СФК)
это систематизированный путь развертывания нужд и пожеланий потребителя через структурирование функций и операций деятельности компании по обеспечению такого качества на каждом этапе жизненного цикла вновь создаваемого продукта, которое бы гарантировало получение конечного результата, соответствующего ожиданиям потребителя. При этом производитель д. иметь чёткое представление о «профиле качества» создаваемого продукта.
«Профиль качества» - модель, предложенная Н. Кано (Япония), которая включает три составляющих профиля качества: базовое, желаемое и требуемое.
Профиль базового качества – совокупность тех параметров качества продукта, наличие которых потребитель считает обязательным, то есть «само собой разумеющимся». Об этих параметрах потребитель не считает даже необходимым говорить производителю. Примеры таких параметров: гарантии безопасности пассажирских транспортных средств,
Профиль требуемого качества – это совокупность показателей качества, представляющих собой технические и функциональные характеристики продукции. Примеры технических параметров: бесшумность, малое потребление горючего автомобилем, быстродействие и память компьютера. Они рекламируются.
Профиль желаемого качества – это группа показателей качества, представляющих для потребителя неожиданные (скрытые) ценности предлагаемого ему продукта, о наличии которых он мог только мечтать. Производитель должен помнить, что рассматриваемые профили качества очень изменчивы. Сегодня – это желаемые параметры качества, а завтра – требуемые.
Суть метода: требования потребителей должны развёртываться и конкретизироваться поэтапно, начиная с исследования рынка, заканчивая продажами. М-д позволяет преобразовать требования потребителей, выраженных в абстрактной форме в технические требования к изделиям и процессам. Технология метода требует совместного участия специалистов отдела маркетинга и конструкторского отдела, Метод QFD является экспертным, в нем использованы специфические табличные формы «Дом качества». Процесс структурирования функции качества складывается из нескольких стадий. Выделим основные (ключевые):
1. выяснение и уточнение требований потребителя,
2. выделение приоритетных потребительских требований,
3. перевод требований потреби
|
|
Поперечные профили набережных и береговой полосы: На городских территориях берегоукрепление проектируют с учетом технических и экономических требований, но особое значение придают эстетическим...
Кормораздатчик мобильный электрифицированный: схема и процесс работы устройства...
Механическое удерживание земляных масс: Механическое удерживание земляных масс на склоне обеспечивают контрфорсными сооружениями различных конструкций...
Адаптации растений и животных к жизни в горах: Большое значение для жизни организмов в горах имеют степень расчленения, крутизна и экспозиционные различия склонов...
© cyberpedia.su 2017-2024 - Не является автором материалов. Исключительное право сохранено за автором текста.
Если вы не хотите, чтобы данный материал был у нас на сайте, перейдите по ссылке: Нарушение авторских прав. Мы поможем в написании вашей работы!