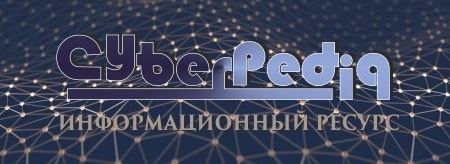
Архитектура электронного правительства: Единая архитектура – это методологический подход при создании системы управления государства, который строится...
Кормораздатчик мобильный электрифицированный: схема и процесс работы устройства...
Топ:
Определение места расположения распределительного центра: Фирма реализует продукцию на рынках сбыта и имеет постоянных поставщиков в разных регионах. Увеличение объема продаж...
Марксистская теория происхождения государства: По мнению Маркса и Энгельса, в основе развития общества, происходящих в нем изменений лежит...
Генеалогическое древо Султанов Османской империи: Османские правители, вначале, будучи еще бейлербеями Анатолии, женились на дочерях византийских императоров...
Интересное:
Уполаживание и террасирование склонов: Если глубина оврага более 5 м необходимо устройство берм. Варианты использования оврагов для градостроительных целей...
Аура как энергетическое поле: многослойную ауру человека можно представить себе подобным...
Национальное богатство страны и его составляющие: для оценки элементов национального богатства используются...
Дисциплины:
![]() |
![]() |
5.00
из
|
Заказать работу |
|
|
Практически в каждой организации присутствует конфликт контроля (см. рис. 7.2). Суть его такова:
Рисунок 7.2 – Конфликт контроля
Чтобы удовлетворять запросы клиентов (Задача), необходимо контролировать систему производства (Условие 1). Чтобы ее контролировать (Условие 1), следует распланировать производство до мельчайших деталей (Метод 1).
Но чтобы удовлетворять запросы клиентов (Задача), нам также необходимо сохранять гибкость, позволяющую нам реагировать на неудачные стечения обстоятельств (Условие 2). А чтобы ее сохранить (Условие 2), нам не следует планировать производство в деталях (Метод 2).
Гамлетовский вопрос: быть или не быть, детализировать или не детализировать? Практически всем представляется аксиомой, что подробное планирование и внимание к каждой мелочи положительно сказываются на эффективности контроля. Возможно, это и справедливо для случаев, когда неопределенность не играет существенной роли. Но там, где она проявляет себя, подробное планирование, скорее всего, будет напрасной потерей времени и, вполне возможно, принесет больше вреда, чем пользы. Этот факт хорошо известен военным — и стратегам, и тактикам. На поле боя неопределенность выражена еще более явно, чем в бизнесе, поэтому в военных планах очень мало деталей: ставится цель, выделяются силы (ресурсы), определяется подчинение и указывается время начала действий. Мы вскоре вернемся к данному конфликту и поймем, как его разрешить, но перед тем нам нужно обсудить некоторые связанные с ним вопросы.
Далее в этой главе мы условно примем, что на рис. 7.3 представлен типичный производственный процесс. Некоторые процессы, очевидно, намного сложнее этого, но, по-видимому, есть и такие, которые проще.
|
Рисунок 7.3 – Типичный производственный процесс
Буферы: традиционный ББК
Буфер—уникальная особенность ББК, отличающая этот метод от других подходов к управлению производством, таких как ЛТ (Just-in-Time—«точно вовремя»). Буферы защищают обязательства системы по выполнению заказов от негативных эффектов, вызванных внутренними отклонениями и внешней неопределенностью. В традиционном методе ББК выделяется три типа буферов:
1. Буфер отгрузки: защищает соблюдение сроков отгрузки.
2. Буфер РОМ: защищает ресурс с ограниченной мощностью от недогрузки.
3. Буфер сборки: защищает производственный поток, идущий от РОМ, от остановки вследствие недостатка комплектующих, которые поступают от других ресурсов.
Буфер отгрузки
Буфер отгрузки определяется как приблизительное время в производственном цикле от РОМ до полной готовности заказа. Если РОМ не входит в цепочку (т.е. у процесса нет внутренних ограничений), буфер отгрузки — это все время от передачи сырья в производство и до получения готовой продукции. На рис. 7.4 приводятся диаграммы, иллюстрирующие понятие буфера отгрузки для нескольких разных конфигураций процессов. Обратите внимание на выражение «приблизительное время». Как мы вскоре увидим, это время складывается не только из времени обработки и перемещения изделий.
Хотя далее в примере мы возьмем за основу верхнюю конфигурацию (сборка после РОМ), понятие буфера отгрузки применимо и к таким производственным линиям, где точка сборки находится перед РОМ, и даже к таким, где активного РОМ вообще нет. Определение буфера отгрузки во всех случаях одно и то же, но части процесса, охватываемые буфером, различаются. Буфер соответствует времени (по той ветви процесса, где находится РОМ) от окончания работы РОМ до момента попадания продукции на склад отгрузки. Если РОМ
отсутствует, буфер простирается назад до самого момента отпуска материалов со склада.
|
Рисунок 7.4 – Буфер отгрузки |
Буфер POM
Буфер РОМ, или буфер ограничения, — это приблизительное время в производственном цикле от отпуска материалов со склада до РОМ (см. рис. 7.5). Он включает все время, необходимое для перемещения материалов из точки их отпуска в точку непосредственно перед РОМ, где они ждут обработки. Это время, как и в случае буфера отгрузки, складывается не только из времени обработки и перемещения продукции, в чем мы вскоре убедимся.
Рисунок 7.5 – Буфер РОМ
Буфер сборки
Буфер сборки — это приблизительное время в производственном цикле от отпуска материалов со склада до точки соединения компонентов, проходящих и не проходящих через РОМ. На рис. 7.6 показано, как выглядит буфер сборки. Как видим, он охватывает все время, необходимое для перемещения материалов от точки их отпуска со склада до точки, где полуфабрикат готов к соединению с другим компонентом, на пути обработки которого находится РОМ. Здесь это время также включает не только время обработки и перемещения продукции.
Рис. 7.6 – Буфер сборки |
Предварительные действия
Теперь давайте посмотрим, как можно применить ББК в производственном процессе. Примем, что уже выполнены три основные задачи управления, присущие любому производственному процессу.
Для каждого вида продукции разработана логическая схема движения материальных потоков в производственном процессе (см. рис. 7.7).
Для каждого ресурса получены достаточно точные оценки времени выполнения операций в расчете на единицу продукции (или, если требуется, на партию). Это чистое время обработки для каждого шага производственного процесса, отмеченного в схеме материальных потоков. Для РОМ необходима максимальная точность. Ни время переналадки, ни время перемещения (от одного участка к другому) не учитывается. Получены оценки времени на переналадку (особенно для РОМ).
Рисунок 7.7 – Схема движения материальных потоков для разных видов продукции
Процесс планирования методом традиционного ББК
1. На первом шаге[5] процесса планирования методом традиционного ББК составляется то, что можно было бы назвать оптимистичным ОПП. Это план без ограничений, предполагающий, что вся включенная в него продукция может быть своевременно произведена и отгружена. Наш оптимистичный ОПП будет опираться исключительно на твердые заказы, обязательные сроки поставки и самый минимум прогнозируемых заказов, абсолютно необходимый для выполнения требований по своевременной поставке.
|
2. Отсортируйте строки оптимистичного ОПП по срокам поставки, начиная с ближайшей.
3. Соберите данные для составления графика работы РОМ. Для каждой строки оптимистичного ОПП, отсортированного по сроку поставки:
При использовании сложного алгоритма:
4а. Начните с последней строки отсортированного ОПП. Зарезервируйте время на РОМ (с учетом продолжительности наладки и обработки), так, чтобы к моменту, когда РОМ закончит обработку последней единицы продукции, до назначенного срока поставки оставалось время, равное времени буфера отгрузки. Если нужное время начала работы РОМ уже занято предыдущим заказом, сдвигайте операцию назад до тех пор, пока не обнаружите свободное время в графике РОМ. По сути, это обратное планирование.
Если работы по заказу нужно было начать до «нулевой точки» (т. е. до момента составления графика), его, а вместе с ним и все последующие заказы, нужно сдвинуть на более позднее время. Заказ с самым ранним сроком поставки запускается в производство немедленно, все последующие (с использованием РОМ) выстраиваются за ним в исходном порядке.
Примечание: Если РОМ загружается полностью, оба алгоритма — и простой и сложный — дадут одинаковые результаты, если же нет, сложный алгоритм позволит сдвинуть выполнение некоторых заказов на более поздний срок, при этом полный буфер отгрузки гарантирует своевременность поставок.
Дальнейшие шаги одинаковы для обоих алгоритмов.
5. Убедитесь, что для работ, которые РОМ должен выполнить первыми, подготовлены необходимые материалы. В идеальном случае объем работы, ожидающей своей очереди, должен соответствовать половине времени буфера РОМ. Если он меньше, проверьте, не запланированы ли на более отдаленное будущее работы, которыми можно загрузить РОМ прямо сейчас. Если да, переставьте соответствующие строки ближе к началу ОПП.
|
6. Удостоверьтесь в реальности выполнения сроков поставки. Найдите заказы, требующие больше половины времени буфера отгрузки, т.е. такие, которые, поступив на РОМ в соответствии с имеющимся графиком, выйдут с него, использовав более половины запланированного буфера отгрузки. Такая ситуация стоит на грани допустимого и ставит под угрозу своевременность поставки.
7. Если есть опасность, что какие-то из заказов не удастся закончить вовремя, примите меры, чтобы этого избежать. Один из возможных способов — попробовать сэкономить на времени переналадки, объединив некоторые заказы. Еще один вариант — работать сверхурочно или привлечь субподрядчиков (в зависимости от ситуации). Задача — обеспечить выполнение заказов, запущенных в производство позже срока, указанного в графике РОМ. Если нет возможности работать сверхурочно, добавить дополнительные смены, привлечь субподрядчиков или сократить количество переналадок, вернитесь к ОПП и отложите заказы, с которыми возникли проблемы.
8. После того как производственный план наконец-то будет откорректирован и принят как выполнимый, составьте план-график отпуска в производство материалов, которые пойдут через РОМ. Момент отпуска материалов в производство должен предшествовать планируемому началу обработки на РОМ, отличаясь от него на время буфера РОМ.
9. Составьте график отпуска в производство материалов, которые не проходят через РОМ. Сначала определите время отпуска со склада материалов для буфера сборки. Это материалы, которые объединяются с компонентами, прошедшими РОМ, но сами через РОМ не проходят. Самый надежный способ — запланировать отпуск материалов в буфер сборки, вычтя из назначенной даты поставки суммарное время буфера отгрузки и буфера сборки.
10.Время отпуска в производство материалов, никак не связанных с РОМ, определяется путем вычитания времени буфера отгрузки из назначенной даты отгрузки.
Традиционный ББК: общая картина
На рис. 7.8 отражено то, о чем мы только что говорили. График отгрузки защищается с помощью буфера отгрузки. Если из даты отгрузки вычесть буфер отгрузки, мы окажемся в точке окончания обработки данного заказа на РОМ.
ОПП — это барабан. Он определяет, чем и когда будет заниматься РОМ. Буфер РОМ гарантирует соблюдение графика.
План-график отпуска материалов со склада — это канат. Он определяет, когда материалы должны быть переданы в производство. Вычитая из запланированного срока выполнения заказа время буфера РОМ, получаем момент отпуска материалов для этого заказа в графике отпуска материалов в производство.
Что делать с не-ограничениями при использовании ББК
|
Мы уже видели, как велико искушение попытаться до мелочей распланировать все, что происходит в системе. Этому искушению очень тяжело противостоять, а ТОС и ББК в каком-то смысле только усугубляют положение, поскольку представляют нам ситуацию, в которой для многих системных компонентов график не нужен (и, пожалуй, даже не должен составляться). Естественно, не может не возникнуть вопрос: что делать при использовании метода ББК с не-ограничениями?
Пример планирования с применением традиционного метода ББК
Давайте рассмотрим пример использования традиционного ББК при планировании производства. В нем производятся и реализуются четыре вида продукции (А, Б, В и Г). В производстве участвуют десять рабочих участков. Подробная схема производства показана на рис. 7.9.
Рис. 7.9 – Планирование с применением традиционного метода ББК: пример
РОМ — это участок 5. Заметим, однако, что он не участвует в производстве продукта Г. Для производства всех четырех видов продукции используется всего четыре разновидности сырья. Производство ведется только на заказ, стандартный срок выполнения заказа, обещаемый клиентам, составляет три недели. Следовательно, горизонт планирования — те же три недели.
Предположим, на календаре 31 декабря 1999 г. Завтра начинается последний год старого тысячелетия. По счастью, нам не требуется останавливать завод на рождественские каникулы, и на первые три недели января у нас запланированы отгрузки. В Таблице 7.1 представлен основной план производства на этот период — если только мы не обнаружим, что не можем его выполнить.
Следующий шаг — составить график для РОМ, назначая задачи в соответствии с датами отгрузки (применяется простой алгоритм). Мы можем пропустить три первых заказа, которые не попадут на участок 5. Заказы 4 и 5 уже дошли до этого участка, так что наш РОМ может начать работу с ними. Материалы для остальных заказов еще не отпущены в производство.
Таблица 7.1 – Основной план производства
Заказ | Срок сдачи | Продукт | Количество | Состояние |
03.01.2000 | А | Завершен | ||
05.01.2000 | В | Завершен | ||
06.01.2000 | Г | Участок 8 | ||
07.01.2000 | В | Участок 5 | ||
10.01.2000 | Б | Участок 5 | ||
11.01.2000 | Г | Не запущен | ||
13.01.2000 | А | Не запущен | ||
14.01.2000 | Б | Не запущен | ||
17.01.2000 | Г | Не запущен | ||
17.01.2000 | В | Не запущен | ||
18.01.2000 | В | Не запущен | ||
20.01.2000 | А | Не запущен | ||
20.01.2000 | Г | Не запущен | ||
21.01.2000 | Б | Не запущен |
Буфер РОМ составляет пять дней, буфер сборки — всего три дня. Он нужен исключительно для сборки продукта Б, где на нижнем отрезке схемы производится деталь, не проходящая через участок 5. Деталь, производимая на верхнем отрезке схемы, проходит через участок 5 на четвертом шаге обработки.
В производстве продукта А участок 5 присутствует на обоих отрезках схемы, поэтому буфер сборки не нужен. Не нужен он, разумеется, и для продукта В, который производится вообще без сборки.
Буфер отгрузки для продуктов А, Б и В принимается равным пяти дням. Это полная продолжительность прохождения маршрута от участка 5 до полностью готового продукта. Для продукта Г этот буфер больше — восемь дней, поскольку данный продукт — «свободный», он не проходит через РОМ. Глядя на рис. 7.9, обратите внимание, что при отсутствии буфера РОМ схема производства для продукта Г содержит больше операций, нуждающихся в защите от неблагоприятных стечений обстоятельств.
Продолжительность производственного цикла для продуктов А, Б и В равна сумме буфера РОМ, времени обработки на РОМ и буфера отгрузки. Поэтому в нашем случае она составит десять рабочих дней плюс время, необходимое для работы РОМ, — от одного до трех дней в зависимости от заказа. Согласовывая с клиентом время выполнения заказа, нужно учитывать возможность того, что график РОМ изменится и обработка данного заказа будет задержана, поскольку ограниченный ресурс понадобится для более срочной работы. Давайте посмотрим, как такое могло бы произойти в нашем примере.
Г рафик работы РОМ
Примем, что переналадки на участке 5 не нужны и что работа происходит в одну смену (8 часов). Рассмотрим заказ 4 — 96 единиц продукта А. Суммарное время обработки на единицу продукции — 20 минут, соответственно, обработка всех 96 единиц займет 24 часа, или три рабочих дня. Переведем все производственные заказы в часы работы (для упрощения цифры в примере подобраны так, чтобы получались значения, кратные длительности смены). График работы РОМ приведен в таблице 7.2.
Таблица 7.2 – График работы РОМ
Сразу же видно, что у нас проблема. Время обработки заказа 14 на РОМ — один день; если не начать эту обработку до 20 января, мы никак не сможем подготовить заказ к отгрузке к 21-му. Хотя наш ОПП охватывает ближайшие три недели, мы рассчитываем, что РОМ закончит обработку всех заказов за пять дней (время буфера отгрузки) до даты отгрузки. Поскольку минимальное время, которое мы выделяем для защиты исходных сроков отгрузки, равняется половине буфера отгрузки, ЮМ должен закончить обработку производственных заказов не позднее, чем за два с половиной дня до конца горизонта планирования. Возможный вариант—предупредить заказчика, что продукция будет готова на день позже, а затем принять меры для ускоренного выполнения заказа.
В таблице 7.3 показаны сроки сдачи заказов — исходные, расчетные (окончание обработки на участке 5 плюс пять дней буфера отгрузки) и минимальные (окончание обработки на участке 5 плюс два с половиной дня). Отгрузка продукта Г считается просроченной только в случае, если время, оставшееся до даты поставки, составляет меньше половины буфера, а материалы еще не отпущены в производство. Но в данном случае это не так, поэтому мы считаем, что все отгрузки продукта Г пройдут в срок.
Судя по всему, мы недооценили серьезность положения. Хуже всего обстоят дела с заказом 5: его нужно отгрузить 10 января, а мы, даже ускорив завершение, сумеем сделать это не ранее 13 января, на три дня позже срока! На самом деле 10 января РОМ (участок 5) только закончит обработку заказа, а его планировалось в этот день сдать. Какие действия здесь возможны?
Таблица 7.3 – Статус производственных заказов
Заказ № | 3 4 | ||||||||||
Запланированная | 06.01 07.01 | 10.01 | 11.01 | 13.01 | 14.01 | 17.01 | 17.01 | 18.01 | 20.01 | 20.01 | |
сдача | |||||||||||
Завершение | 06.01 12.01 | 17.01 | 11.01 | 18.01 | 19.01 | 21.01 | 24.01 | 25.01 | 20.01 | 21.01 | |
Ускоренное | 06.01 10.01 | 13.01 | 11.01 | 14.01 | 17.01 | 17.01 | 19.01 | 20.01 | 21.01 | 20.01 | 25.01 |
Завершение |
В действительности есть способ сократить опоздание до одного дня (а об однодневной задержке предупредить заказчика). Посмотрите на схему движения материальных потоков (рис. 7.9). Обратите внимание, что после ограничения продукт Б проходит еще два этапа обработки. Согласно графику, 6 января РОМ должен начать обработку заказа 5. Если мы установим размер передаточной партии равным одной единице продукции, а компоненты, поступающие с другого отрезка схемы, уже будут ждать в точке сборки, то большая часть заказа, скорее всего, будет готова к 10 января, и только нескольким последним изделиям еще нужно будет пройти две оставшиеся операции. Если так, у нас есть хорошие шансы отгрузить заказанную продукцию 11 января.
В отношении описанного варианта нужно уточнить два момента. Во-первых, мы предполагаем, что компоненты, необходимые для продукта Б, которые не проходят через РОМ, будут находиться в точке сборки, поскольку они не могут двигаться дальше без деталей, обрабатываемых на РОМ. Во-вторых, предполагается, что на втором отрезке есть достаточно избыточных мощностей, чтобы обеспечить своевременное поступление компонентов в точку сборки. Если эти компоненты почему-либо застрянут на более раннем этапе производственного процесса, предлагаемый вариант осуществить не удастся.
Можно ли рассчитывать, что мы сумеем ускорить завершение заказа по производству 72 единиц продукта Б? Да, но только если нам удастся ускорить обработку компонентов на РОМ и обеспечить, чтобы последующие участки, через которые должен затем пройти продукт Б, были свободны. В состоянии ли мы это гарантировать?
В целом, если предприятие производит несколько видов продукции, нужно с большой осторожностью утверждать сроки поставок, до которых остается меньше половины буфера отгрузки после окончания обработки на РОМ.
На самом деле у нас есть всего две возможности: либо изменить первоначальный план производства (предупредив об этом заказчика), либо нарастить мощность ограничения. Если в течение трех рабочих дней в период до 10 января участок 5 будет работать в две смены, наши шансы вовремя выполнить заказ 5 (и последующие заказы) существенно возрастут.
Одно предупреждение: можно ли быть уверенным, что, если мы повысим мощность только на участке 5, ни один другой ресурс не превратится на время в ограничение? Добавив на участке вторую смену, мы фактически временно расширяем ограничение. Всякий раз, расширив ограничение, следует проверить, не появилось ли где-то другое. Автоматизированная система планирования поможет легко ответить на этот вопрос, отслеживая загрузку не-ограничений в течение заданного периода времени. Однако для этих целей нужны очень точные данные по не-ограничениям, а они имеются далеко не всегда.
Чтобы предотвратить появление нового ограничения, можно добавить вторую смену на тех участках, загрузка которых приближается к максимальной, а может быть, и на других ресурсах. Тогда мы будем уверены, что в рамках буфера все не-ограничения будут способны сделать все, что необходимо для максимально эффективного использования РОМ. В нашем примере есть несколько заказов с практически исчерпанным буфером отгрузки, так что стоит снизить нагрузку не только на ограничение, но и на не-ограничения. Поэтому идея на три дня добавить вторую смену на всех участках представляется правильной.
Когда придет время реально ввести двухсменную работу, возникнет еще одна проблема. Давайте сначала изменим график (см. табл. 7.4). Последний рабочий день для ограничения — 17 января. Ожидается, что к тому времени все заказы уже пройдут РОМ, и в течение последних пяти дней, соответствующих буферу отгрузки, они будут проходить заключительные этапы. Но нам нужны другие пять дней на то, чтобы материалы, отпущенные в производство, дошли до РОМ. Материалы под заказы 7 и 8 еще не отпущены со склада. Даже если отпустить их утром 3 января, у них останется соответственно три и четыре дня, чтобы дойти до ограничения.
Таблица 7.4 – Исправленный график работы РОМ с добавлением второй смены
Рабочие дни | 03.01 04.01 05.01 06.01 07.01 10.01 11.01 12.01 13.01 14.01 17.01 18.01 19.01 20.01 21.01 |
Дополнительные смены | 1 1 1 |
Участок 5, заказ № | 4 4и5 5 7 8 10 10 11 12 12 14 |
С одной стороны, можно надеяться, что нам хватит половины буфера РОМ. С другой, учитывая, что все ресурсы будут работать в две смены, а исходный пятидневный буфер, как мы помним, был рассчитан на односменную работу, лучше выразить длительность буфера в сменах, а не в днях, чтобы у нас не возникло проблем с отпуском материалов в производство.
Теперь мы можем составить план-график отпуска материалов (табл. 7.5). Обратите внимание, что сырье, используемое при изготовлении продукта Б (заказы 8 и 14), которое не проходит через РОМ, отпускается со склада всего за три дня до начала обработки соответствующего заказа на РОМ, поскольку буфер сборки составляет всего три дня.
Таблица 7.5 – План-график отпуска материалов
Рабочие дни | 03.01 | 04.01 | 05.01 | 06.01 | 10.01 | 12.01 |
Сырье 1 | 24 Заказ 7 | 24 Заказ 8 | 48 Заказ 12 | 24 Заказ 14 | ||
Сырье 2 | 24 Заказ 7 | 4и5 | 32 Заказ 11 | 48 Заказ 12 | ||
Сырье 3 | 24 Заказ 8 64 Заказ 10 | 24 Заказ 14 | ||||
Сырье 4 | 36 Заказ 6 | 30 Заказ 9 | 30 Заказ 13 |
Хотя ОПП охватывает три недели, в графике РОМ отражены только две недели и один день, а в графике отпуска материалов еще меньше — всего полторы недели. Эта разница соответствует длительности буферов.
Итак, мы рассмотрели простой пример, иллюстрирующий применение при планировании метода ББК. Заметьте, что в графиках указываются только даты отгрузки, время использования РОМ и время отпуска материалов, а операции, связанные с не-ограничениями, вообще никак не учитываются.
|
|
Таксономические единицы (категории) растений: Каждая система классификации состоит из определённых соподчиненных друг другу...
Археология об основании Рима: Новые раскопки проясняют и такой острый дискуссионный вопрос, как дата самого возникновения Рима...
Кормораздатчик мобильный электрифицированный: схема и процесс работы устройства...
Биохимия спиртового брожения: Основу технологии получения пива составляет спиртовое брожение, - при котором сахар превращается...
© cyberpedia.su 2017-2024 - Не является автором материалов. Исключительное право сохранено за автором текста.
Если вы не хотите, чтобы данный материал был у нас на сайте, перейдите по ссылке: Нарушение авторских прав. Мы поможем в написании вашей работы!