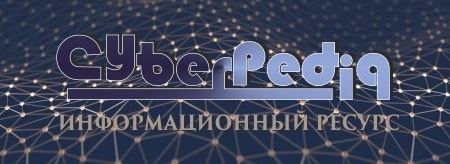
Автоматическое растормаживание колес: Тормозные устройства колес предназначены для уменьшения длины пробега и улучшения маневрирования ВС при...
Эмиссия газов от очистных сооружений канализации: В последние годы внимание мирового сообщества сосредоточено на экологических проблемах...
Топ:
Генеалогическое древо Султанов Османской империи: Османские правители, вначале, будучи еще бейлербеями Анатолии, женились на дочерях византийских императоров...
Устройство и оснащение процедурного кабинета: Решающая роль в обеспечении правильного лечения пациентов отводится процедурной медсестре...
Интересное:
Распространение рака на другие отдаленные от желудка органы: Характерных симптомов рака желудка не существует. Выраженные симптомы появляются, когда опухоль...
Уполаживание и террасирование склонов: Если глубина оврага более 5 м необходимо устройство берм. Варианты использования оврагов для градостроительных целей...
Отражение на счетах бухгалтерского учета процесса приобретения: Процесс заготовления представляет систему экономических событий, включающих приобретение организацией у поставщиков сырья...
Дисциплины:
![]() |
![]() |
5.00
из
|
Заказать работу |
Содержание книги
Поиск на нашем сайте
|
|
В производстве пластичных смазок применяют периодические, полунепрерывные и непрерывные процессы [1—З], технологические схемы которых многообразны. Однако различия во многих случаях обусловлены лишь разным аппаратурным оформлением. Это позволяет относительно небольшим числом технологических схем (в пособии рассмотрено шесть) охватить основные варианты процессов производства смазок.
Процесс производства смазок на мыльных загустителях, который является в отличие от других нефтехимических процессов по существу безотходным производством', состоит из следующих основных стадий: дозирования сырья, приготовления и термомеханического диспергирования загустителя, охлаждения расплава, гомогенизации, фильтрования, деаэрации и расфасовки [2]. Получающийся некондиционный продукт отправляют на переработку.
Дозирование сырья. Исходные компоненты дозируют обычно в жидком виде. В периодических и полунепрерывных процессах используют объемные дозирующие устройства, недостаточная точность работы которых устраняется смешением компонентов в реакторе с мешалкой. Широкое применение находят многокомпонентные дозирующие насосы с суммирующими устройствами, которые автоматически поддерживают необходимое соотношение компонентов и отключают насосы после заполнения мешалок. В непрерывных процессах дозирующие насосы — обязательный элемент производства. Они пригодны и для дозирования суспензий сыпучих реагентов (в частности, извести пушонки) в дисперсионной среде. Точность дозирования насосами ±3 %, что обеспечивает заданную концентрацию загустителя с отклонениями не более ±0,5 %.
Приготовление и термо-механическое диспергирование загустителя, С омыления жиров или нейтрализации жирных кислот начинается процесс получе-ния смазок. После окончания омыления из мыльно-масляной суспензии полностью (для гидратированных кальциевых и кальциево-натриевых смазок до определенного предела) удаляют влагу. При производстве смазок на сухих мылах мыльно-масляную суспензию получают непосредственным смешением компонентов в заданных соотношениях. Затем суспензию нагревают до получения однородного расплава. Известны способы получения смазок, когда мыльно-масляную суспензию нагревают при сравнительно невысокой температуре — проводят лишь набухание мыла в масле. Такой способ получил название «холодной варки» или низкотемпературного процесса производства.
|
На стадии охлаждения расплава загустителя в масле формируется структура смазок. Изменяя режим охлаждения (быстрое, медленное или изотермическая кристаллизация), можно воздействовать на размеры и форму дисперсных частиц структурного каркаса смазок и, следовательно, изменять их свойства. Широкое распространение получили комбинированные методы охлаждения (быстрое и медленное): расплав охлаждается при смешении с неиспользованной частью масла (примерно 1/3 расчетного количества), температура которого (50—70 °С) ниже температуры расплава (180—230 °С); далее охлаждение ведут с помощью хладагента, подаваемого в рубашку реактора или скребкового аппарата.
Гомогенизация [2—5] повышает равномерность распределения загустителя в масле, улучшает внешний вид, а также коллоидную и механическую стабильность смазок. В простейшем случае гомогенизацию осуществляют продавливанием смазки через сетку или систему сит, через узкие (30—50 мкм) зазоры вальцовочных машин. Широко распространены методы однократной гомогенизации на заключительной стадии производства смазок [4]. Однако в непрерывных процессах успешно применяют и многократную гомогенизацию на каждой технологической стадии за счет циркуляции продукта через гомогенизирующие клапаны при относительно низком перепаде давления, что исключает применение специальных аппаратов.
|
Для удаления механических примесей смазки фильтруют, продавливая их через, устройство с металлическими сетками или используя самоочищающиеся фильтры.
В результате деаэрации — удаления попавшего при изготовлении смазки воздуха — улучшается внешний вид, повышается химическая стабильность и плотность смазок [5]. При получении смазок на сухих мылах во время дозирования сухого мыла в нее попадает много воздуха, который удаляется из расплава при повышенных температурах. При получении мыла в процессе производства смазки часть воздуха уходит вместе с парами воды, а оставшуюся часть удаляют на заключительной стадии после гомогенизации. Воздух может попасть в смазку при гомогенизации, если ее проводят при атмосферном давлении (например, на вальцовочных машинах). Удаляют воздух из тонкого слоя смазки (200— 500 мкм) в вакууме до 95 кПа.
В непрерывных процессах — при более тщательной подготовке исходных компонентов и проведении процесса под давлением — необходимость в деаэрации и фильтровании обычно отпадает.
При организации технологического процесса, выборе оптимального аппаратурного оформления и методов контроля учитывают реологические и тепло-физические свойства полупродуктов производства смазок.
Ниже показано влияние температуры на реологические и теплофизические свойства мыльно-масляной дисперсии по стадиям процесса для смазки на 12-оксистеарате лития (литол-24):
Температура, °С | Вязкость, (Па·с) | Плотность, кг/м3 | Теплопроводность, Вт/(м·К) | Теплоемкость, кДж/(кг·К) | |
при 10 с-1 | при 100 с-1 | ||||
0,62 0,71 1,24 32,20 | 0,072 0,085 0,131 4,230 | 0,150 0,149 0,158 0,129 | 2,427 2,477 3,150 2,612 | ||
Ввод одной трети масла | |||||
2,42 7,40 5,02 | 0,48 1,11 0,68 | 0,133 0,122 0,111 | 2,701 2,800 2,980 |
Аппаратурное оформление процесса производства смазок в значительной степени определяется реологическими свойствами (прежде всего их вязкостью) смазок и промежуточных продуктов. Для таких смазок, как литол-24, и для мыльных смазок отмечается резкое (в 50—80 раз) увеличение вязкости в процессе термо-механического диспергирования и ее зависимость от скорости деформирования. Поэтому к конструкции перемешивающего устройства реактора, в котором совмещаются стадии омыления, обезвоживания, получения и выдержки расплава, а также предварительного охлаждения, предъявляют сложные требования. Скребково-лопастные мешалки с переменным числом оборотов позволяют на каждой стадии менять режим перемешивания. Высокая эффективность этих перемешивающих устройств и гибкое регулирование интенсивности перемешивания сокращают длительность процесса, повышают качество смазок и воспроизводимость свойств отдельных партий.
|
На рис. XI-1 показан реактор со скребково-лопастным перемешивающим устройством емкостью 10 м3, поверхностью теплообмена 20 м2.
Привод перемешивающих устройств реактора осуществляется двухскоростным мотором-редуктором мощностью 40 кВт и специальной раздаточной коробкой с двумя соосными выходными валами, что обеспечивает противоположно направленное вращение центрального и периферийного перемешивающих устройств, а также возможность раздельной работы каждого из них.
Сократить длительность стадии омыления жиров можно. повышением температуры. Из-за наличия воды процесс проводят под давлением до 1 МПа в контакторах-автоклавах [2]. Вязкость системы на стадии омыления невелика, и в контакторах Применяют высокоскоростные мешалки (например, контакторы типа «Стратко» при производстве мыльных смазок за рубежом). Нагретая в контакторах до 150—170 °С смесь после омыления направляется в реакторы, работающие при атмосферном давлении. В результате дополнительного нагревания в реакторах удаляется влага и осуществляется термо-механическое диспергиро-вание образующегося мыльного загустителя.
Удаление влаги из мыльно-масляной дисперсии в большом. объеме реактора — длительная операция. В настоящее время разработан выпарной аппарат Г6], в котором смесь нагревается' (под давлением) до 150—160°С, и основная влага испаряется в камере распыла с последующим глубоким обезвоживанием. в стекающей пленке при подводе тепла через стенку. Подобный. аппарат используется при производстве литиевых, комплексных кальциевых, кальциевых гидратированных и других мыльных смазок.
|
Свойства мыльных смазок и особенно комплексных кальциевых зависят от температурного режима приготовления (максимальная температура нагревания, продолжительность термообработки) и последовательности. введения комплексообразующих компонентов. О влиянии максимальной температуры нагревания и продолжительности ее воздействия на свойства комплексных кальциевых смазок, приготовленных на основе синтетических жирных кислот Сщ—Qo и уксусной кислоты, свидетельствуют следующие данные:
Температура нагревания, °С | Время выдержки, мин. | Предел прочности при 50°С, Па | Вязкость при 50°С 100 с-1, Па·с | Отпрессовываемость масла, % |
2,2 3,2 4,9 6,0 | 10,6 4,9 3,0 4,2 |
Нагревание или охлаждение высоковязкого мыльно-масляного концентрата эффективно лишь в теплообменных аппаратах специальной конструкции. Например, в трубчатых скребковых "теплообменных аппаратах поверхность постоянно очищается, т. е. устраняется отрицательное влияние повышенной адгезии, и, кроме того, возможно приложение высоких сдвиговых напряжений, снижающих вязкость. На рис. XI-2 показан двухкорпусный скребковый аппарат с поверхностью теплообмена 3,5 м2.
В каждом корпусе расположен вращающийся вал с четырьмя «плавающими» скребками, которые под действием центробежной силы и давления перемешиваемой жидкости плотно прижимаются к хромированной поверхности цилиндра идаметром 0,35 м и длиной 1,67 м; полезный (свободный) объем цилиндра — 0,05 м3. Привод — индивидуальный, через редуктор; частота вращения в первом по ходу продукта (при охлаждении) корпусе п =- 240, во втором — 180 об/мин, соответственно мощность электродвигателя в первом корпусе — 17 кВт, во втором — 220 кВт. При нагревании порядок последовательного включения корпусов — обратный. При охлаждении в рубашку аппарата (в каждый корпус отдельно) подается охлажденная и очищенная от примесей и солей вода, а при нагревании — масло или другой жидкий теплоноситель. Производительность аппарата при охлаждении смазок в диапазоне температур от 200 до 60 °С составляет 2000—2500 кг/ч, соответственно расход охлаждающей воды с начальной температурой 5 °С — до 20 мУч. При нагревании производительность аппарата на 20—25 % выше, чем при охлаждении, при условии сохранения разности температур смазка — теплоноситель (хладоагент).
В промышленных условиях при охлаждении литиевых смазок коэффициент теплопередачи составляет 600—650 Вт/м2·К), что примерно в 20 раз выше, чем в трубчатых теплообменных аппаратах. Перспективным и эффективным для нагревания и охлаждения смазок в непрерывных схемах является змеевиково-скребковый аппарат.
|
Для гомогенизации смазок применяют клапанные гомогенизаторы (производительность 3,0—3,5 т/ч при максимальном давлении продавливания до 50 МПа) и гомогенизаторы типа коллоидной мельницы (производительность 1,0—3,0 т/ч зависит от зазора между ротором и статором, скорости подачи и состава смазки) [4, 7]. Для литиевых смазок можно рекомендовать оба типа гомогенизаторов; при ограниченном давлении (до 20 МПа) в клапанных гомогенизаторах для комплексных кальциевых смазок предпочтительно применять гомогенизаторы типа коллоидной мельницы.
В промышленности используют деаэратор, разработанный ВНИИПКнефтехимом (рис. XI-3), производительностью 1—3 т/ч с регулируемым зазором в пределах 0,1—0,5 мм. Из нижней части вакуумной камеры (емкость 0,16 м3) деаэрированный продукт непрерывно отбирается шестеренчатым насосом, при вод которого осуществляется через мотор-вариатор. Регулированием частоты вращения достигается синхронизация потоков на входе и выходе из деаэратора. При вакууме 93—95 кПа в таком деаэраторе воздух удаляется практически полностью.
В полунепрерывных и особенно непрерывных технологических схемах важно правильно выбрать насосы для перекачивания полупродуктов и смазок, а также конфигурацию накопителей готовой продукции для гибкого регулирования и согласования производительности технологической установки с производительностью автоматических линий по затариванию готовой продукции. Из-за повышенной вязкости для транспортирования смазок применяют роторно-зубчатые и винтовые насосы. В качестве сборников-накопителей используют бункеры с обогреваемыми стенками, которые оборудованы системой замкнутой циркуляции смазок через гомогенизирующий клапан.
Кроме обычных методов непрерывного контроля (температуры, давления, расхода), в схемах предусматривают локальные системы автоматического регулирования стадий процесса С применением общетехнических и специальных приборов и устройств. На стадии получения мыльной основы, например, литиевых смазок для контроля полноты омыления по щелочности, успешно используется рН-метр. Контролируется также содержание влаги в высоковязких системах. Качество смазок на заключительной стадии их приготовления оценивают показателями реологических свойств на потоке (предел текучести и вязкость при различных скоростях сдвига).
Размещение оборудования на установках зависит от конкретных условий. Наиболее распространена поэтажная компановка с размещением оборудования в соответствии с направлением технологических потоков (на верхнем этаже — дозаторы, ниже — аппараты с мешалками,еще ниже — насосы и другое вспомогательное оборудование).
Теплоносителем для обогревания аппаратов служит водяной пар, а также масло или органические теплоносители, например дифенильная смесь. Сборники-накопители смазок при температуре ниже 100 °С могут обогреваться горячей водой. Водяной пар вводится в аппарат сверху, а конденсат удаляется снизу. Все жидкие теплоносители (а также хладагенты) при вертикальном расположении аппаратов вводятся снизу и удаляются сверху.
В качестве хладоагентов используют холодное масло (если хладоагент подается в аппарат, для нагревания которого использовалось горячее масло), проточная или охлажденная вода в замкнутой системе охлаждения.
|
|
Биохимия спиртового брожения: Основу технологии получения пива составляет спиртовое брожение, - при котором сахар превращается...
Типы оградительных сооружений в морском порту: По расположению оградительных сооружений в плане различают волноломы, обе оконечности...
Адаптации растений и животных к жизни в горах: Большое значение для жизни организмов в горах имеют степень расчленения, крутизна и экспозиционные различия склонов...
Механическое удерживание земляных масс: Механическое удерживание земляных масс на склоне обеспечивают контрфорсными сооружениями различных конструкций...
© cyberpedia.su 2017-2024 - Не является автором материалов. Исключительное право сохранено за автором текста.
Если вы не хотите, чтобы данный материал был у нас на сайте, перейдите по ссылке: Нарушение авторских прав. Мы поможем в написании вашей работы!