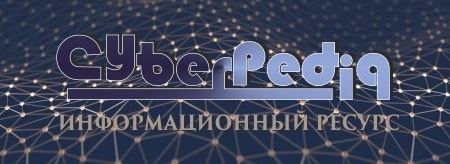
Археология об основании Рима: Новые раскопки проясняют и такой острый дискуссионный вопрос, как дата самого возникновения Рима...
Поперечные профили набережных и береговой полосы: На городских территориях берегоукрепление проектируют с учетом технических и экономических требований, но особое значение придают эстетическим...
Топ:
Марксистская теория происхождения государства: По мнению Маркса и Энгельса, в основе развития общества, происходящих в нем изменений лежит...
Методика измерений сопротивления растеканию тока анодного заземления: Анодный заземлитель (анод) – проводник, погруженный в электролитическую среду (грунт, раствор электролита) и подключенный к положительному...
Основы обеспечения единства измерений: Обеспечение единства измерений - деятельность метрологических служб, направленная на достижение...
Интересное:
Мероприятия для защиты от морозного пучения грунтов: Инженерная защита от морозного (криогенного) пучения грунтов необходима для легких малоэтажных зданий и других сооружений...
Подходы к решению темы фильма: Существует три основных типа исторического фильма, имеющих между собой много общего...
Как мы говорим и как мы слушаем: общение можно сравнить с огромным зонтиком, под которым скрыто все...
Дисциплины:
![]() |
![]() |
5.00
из
|
Заказать работу |
Содержание книги
Поиск на нашем сайте
|
|
Процесс контактной доочистки является завершающей стадией производства масел и предназначен для улучшения цвета масла и снижения коксуемости. В основу процесса положена способность естественных глин адсорбировать на своей поверхности различные вещества. При контактной доочистке применяют тонкодисперсный адсорбент — частицы размером около 0,1 мм.
Целевой продукт процесса — доочищенное базовое масло, побочный — отгон (смесь легких масляных фракций, продуктов разложения и т. п.). Отходом является отработанная земля, пропитанная маслом, содержание которого колеблется в зависимости от вязкости масла от 15 до 50% (масс.) на адсорбент; выход доочищенного масла 96—98% (масс.) на сырье.
Установка включает следующие секции: контактирования (основные аппараты: холодный смеситель, трубчатая печь, отпарная колонна) фильтрования (основные аппараты: горячий смеситель, дисковые и рамные фильтры. Технологическая схема установки представлена на рис. Х-2.
Сырье — депарафинированное масло — насосом / подается через паровой подогреватель 2 в хо лодный смеситель 3. В смесителе, оборудованном турбомешалкой, масло смешивается с молотой глиной, транспортируемой шнековым дозатором. Из смесителя суспензия насосом 4 направляется через теплообменник 5 в змеевик печи 6 и далее в испарительную колонну 7. В низ колонны для перемешивания и удаления легких компонентов подается острый водяной пар. Отходящая с верха колонны смесь паров проходит в конденсатор 9 и поступает в приемник 10. Конденсат из приемника 10 насосом 11 возвращается на орошение в колонну 7. Водяной пар конденсируется в конденсаторе смешения 12. Из колонны 7 суспензия масла с глиной подается насосом 8 через теплообменник 5 в горячий смеситель 13. Предусмотрена рециркуляция части суспензии.
|
Секция фильтрования, обслуживаемая насосами 14 и 18, представлена двумя типами фильтров: дисковые фильтры 15 — фильтры грубой очистки — и рамные фильтры 19 — фильтры тонкой очистки. Из приемника 13 насосом 14 суспензия подается вначале на дисковые фильтры 15. Масло, очищенное от глины, проходит через холодильник 16 и поступает в приемник 17, откуда насосом 18 подается в рамные фильтры 19. Очищенное масло поступает в приемник 20, а оттуда в резервуар.
Технологический режим установки:
Температура, °С суспензии в холодном смесителе суспензии при выходе из змеевика печи в дисковых фильтрах в рамных фильтрах Давление, МПа в дисковых фильтрах в рамных фильтрах Расход глины (неактивированной)*, % (масс.) | 70-80 130-220 130-170 70-110 0,40 0,35 5-10 |
* Зависит от характеристик доочищаемого масла, предъявляемых к нему требований и качества отбеливающей земли. |
Установка «Парекс»
Адсорбционный процесс «Парекс», разработанный в ГДР, применяется для разделения керосиновых фракций на два продукта: жидкие неразветвленные парафиновые углеводороды (н-парафины) и де-парафинированный керосиновый дистиллят, называемый денормализатом. Сырьем установки является прямогонный керосиновый дистиллят широкого или узкого фракционного состава (в зависимости от требований, предъявляемых к продуктам), который предварительно подвергается гидроочистке.
Содержание неразветвленных парафиновых углеводородов в получаемой фракции жидких м-парафинов (парафин-сырец) достигает 99 % (масс.) от сырья, а отбор их от потенциала высок. Для денор-мализата характерны низкие температуры помутнения и застывания. Ниже в качестве примера приведены показатели качества сырья и продуктов;
Показатели | Сырье (240-320°С) | Жидкие парафины | Денормализат |
Плотность, кг/м3 | |||
Температура, °С застывания помутнения | -22 -19 | -60 -47 | |
Содержание, % (масс.) н-парафинов серы | 21,3 0,01 | - | 4,0 0,011 |
|
Адсорбент, используемый на установке, избирательно адсорбирует н-парафины из смесей их с углеводородами другого строения. Десорбция адсорбента осуществляется нагретыми парами аммиака, который называется вытеснителем; последний циркулирует на установке. Используется также водо-родсодержащий газ, являющийся газом-носителем сырья. Применение циркулирующего газа-носителя препятствует быстрому падению адсорбционной емкости адсорбента и способствует удлинению пробега установки [2, З]. В целом обе стадии процесса— адсорбция и десорбция — являются парофазными. Для извлечения из циркулирующего водородсодержащего газа попутных паров аммиака используется вода.
К сырью предъявляются довольно жесткие требования по содержанию серы, олефинов и примесей.
Основные секции установки следующие: нагревательная, в которой смесь сырья с водородсодержа-щим газом нагревается в теплообменниках, а затем в змеевике печи (в этой же секции, но в отдельной печи нагревается аммиак перед направлением его в слой адсорбента); адсорбции и десорбции с тремя периодически переключаемыми вертикальными аппаратами (один — адсорбер, а два других в данный период — десорберы); сепарации с двумя параллельными линиями; эта секция предназначена для разделения смесей, выходящих из адсорбера (линия «денормализата») и из двух аппаратов, эксплуатируемых в данный промежуток времени как десорберы (линия н-парафинов). Технологическая схема установки представлена на рис. Х-3; здесь три контура циркуляции: водородсодержащего газа, аммиака — вытеснителя — и воды, поглощающей пары аммиака в промывной колонне.
К сырью, подаваемому насосом /, присоединяются свежий и циркулирующий водородсодержа-щий газ (нагнетается компрессором 2). После нагрева в теплообменниках (условно показано пунктирной линией, ведущей к печи 4} и змеевике печи 4 смесь поступает в адсорбер 6 с неподвижным слоем адсорбента, извлекающим из сырья н-парафины. По выходе из адсорбера денормализат в смеси с во-дородсодержащим газом и аммиаком (остатка от предшествующей операции — десорбции) охлаждается в теплообменнике 7. Пройдя далее конденсатор-холодильник 15, смесь разделяется в промывной колонне 16 на две части: жидкую—охлажденный конденсат денормализата — и газопаровую. В верхней части колонны 16 пары аммиака поглощаются циркулирующей водой, поступающей далее в две последовательно соединенные колонны 17 и 21 для дегазации. Здесь из водного раствора удаляется аммиак; пары аммиака после ступенчатого сжатия компрессорами 18, 19 и 3 используются в процессе десорбции.
|
Выходящий из верхней части колонны 16 водо-родсодержащий газ сжимается компрессором 2 и как рециркулят присоединяется к сырью.
Работающие в стадии десорбции аппараты 8 и 14 продуваются перегретым в змеевике печи 5 газообразным аммиаком. Последний в смеси с вытесненными к-парафинами проходит теплообменники 9 и 13, а затем конденсатор-холодильник 10; конденсат отделяется от газообразного аммиака в сепараторе 11. В работающем при менее высоком давлении сепараторе 12 из жидкости выделяется растворенный аммиак. Вспомогательным компрессором 18 аммиак подается на прием компрессора 3 повышенного давления. В секции адсорберов — десорберов коммуникации системы автоматического переключения аппаратов с одной операции на другую не показаны.
Режим процесса парофазной адсорбции: температура 300—400 °С, давление 0,5—1,0 МПа; длительность адсорбции примерно в два раза меньше продолжительности десорбции. Между этими стадиями в течение непродолжительного времени адсорбент продувается. Окислительную регенерацию адсорбента проводят обычно после 6000—8000 ч его эксплуатации [2, 3].
Глава XI
|
|
Папиллярные узоры пальцев рук - маркер спортивных способностей: дерматоглифические признаки формируются на 3-5 месяце беременности, не изменяются в течение жизни...
Организация стока поверхностных вод: Наибольшее количество влаги на земном шаре испаряется с поверхности морей и океанов (88‰)...
Археология об основании Рима: Новые раскопки проясняют и такой острый дискуссионный вопрос, как дата самого возникновения Рима...
Общие условия выбора системы дренажа: Система дренажа выбирается в зависимости от характера защищаемого...
© cyberpedia.su 2017-2024 - Не является автором материалов. Исключительное право сохранено за автором текста.
Если вы не хотите, чтобы данный материал был у нас на сайте, перейдите по ссылке: Нарушение авторских прав. Мы поможем в написании вашей работы!