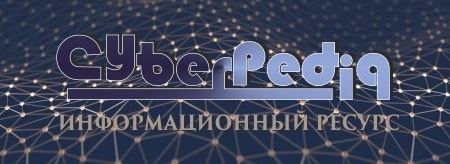
История создания датчика движения: Первый прибор для обнаружения движения был изобретен немецким физиком Генрихом Герцем...
Автоматическое растормаживание колес: Тормозные устройства колес предназначены для уменьшения длины пробега и улучшения маневрирования ВС при...
Топ:
Марксистская теория происхождения государства: По мнению Маркса и Энгельса, в основе развития общества, происходящих в нем изменений лежит...
Оценка эффективности инструментов коммуникационной политики: Внешние коммуникации - обмен информацией между организацией и её внешней средой...
Интересное:
Отражение на счетах бухгалтерского учета процесса приобретения: Процесс заготовления представляет систему экономических событий, включающих приобретение организацией у поставщиков сырья...
Лечение прогрессирующих форм рака: Одним из наиболее важных достижений экспериментальной химиотерапии опухолей, начатой в 60-х и реализованной в 70-х годах, является...
Подходы к решению темы фильма: Существует три основных типа исторического фильма, имеющих между собой много общего...
Дисциплины:
![]() |
![]() |
5.00
из
|
Заказать работу |
Содержание книги
Поиск на нашем сайте
|
|
Процесс замедленного коксования в необогреваемых камерах предназначен для получения крупнокускового нефтяного кокса как основного целевого продукта, а также легкого и тяжелого газойлей, бензина и газа. Сырьем для коксования служат малосернистые атмосферные и вакуумные нефтяные остатки, сланцевая смола, тяжелые нефти из битуминозных песков, каменноугольный деготь и гильсонит. Эти виды сырья дают губчатый кокс. Для получения высококачественного игольчатого кокса используют более термически стойкое ароматизированное сырье, например смолу пиролиза, крекинг-остатки и каталитические газойли.
Основными показателями качества сырья являются плотность, коксуемость по Конрадсону и содержание серы. Выход кокса определяется коксуемостью сырья и практически линейно изменяется в зависимости от этого показателя. При коксовании в необогреваемых камерах остаточного сырья выход кокса составляет 1,5—1,6 от коксуемости сырья. При коксовании дистиллятного сырья выход кокса не соответствует коксуемости сырья, поэтому составлять материальный баланс расчетным методом для такого сырья нельзя. Главным потребителем кокса является алюминиевая промышленность, где кокс служит восстановителем (анодная масса) при выплавке алюминия из алюминиевых руд. Кроме того, кокс используют в качестве сырья при изготовлении графитированных электродов для сталеплавильных печей, для получения карбидов (кальция, кремния) и сероуглерода.
Основными показателями качества кокса являются истинная плотность, содержание серы, зольность и микроструктура. Для игольчатого кокса истинная плотность должна быть не ниже 2,09 г/см3, для кокса марки КНПС (пиролизного специального), используемого в качестве конструкционного материала, она находится в пределах 2,04—2,08 г/см3 [15].
|
Содержание серы в коксе почти всегда больше, чем в остаточном сырье коксования. Из остатков малосернистых нефтей получают малосернистый кокс, содержащий, как правило, до 1,5 % (масс.) серы; кокс из сернистых остатков содержит обычно 2,0— 4,5 % (масс.) серы, а из высокосернистых — более 4,0 % (масс.) [16].
Содержание золы в коксе в значительной мере зависит от глубины обессоливания нефти перед ее перегонкой.
В Советском Союзе проектируются и находятся в эксплуатации установки замедленного коксования мощностью 300, 600 и 1500 тыс. т сырья в год. На рис. III-5 приведена установка мощностью 600 тыс. т в год, которая включает реакторный блок, состоящий из четырех коксовых камер, две трубчатые нагревательные печи, блок фракционирования и систему регенерации тепла и охлаждения продуктов [17].,
Сырье — гудрон или крекинг-остаток (или их смесь) — подается насосом 1 двумя параллельными потоками в трубы подовых и потолочных экранов печей 2 и 3, где оно нагревается до 350—380 °С. Затем сырье поступает в нижнюю часть колонны 9 на верхнюю каскадную тарелку. Сюда же под нижнюю тарелку поступают горячие газы и пары продуктов коксования, образующиеся в двух параллельно работающих камерах 5 (или 5'). В колонне сырье встречается с восходящим потоком газов и паров и в результате контакта тяжелые фракции паров конденсируются и смешиваются с сырьем. Таким образом, в нижней части колонны образуется смесь сырья с рециркулятом, обычно называемая вторичным сырьем. Если в сырье содержались легкие фракции, то они в результате контакта с высокотемпературными парами, испаряются и уходят в верхнюю часть колонны 9.
Вторичное сырье с низа колонны 9 забирается насосом 6 и возвращается в змеевики печи 2 и 3, в верхние трубы конвекционной секции и правые подовые и потолочные экраны. Эта часть труб относится к «реакционному» змеевику, здесь вторичное сырье нагревается до 490—510 °С. Во избежание закоксовывания труб этой секции в трубы потолочного экрана подают перегретый водяной пар, так называемый турбулизатор, в количестве 3 % (масс.) на вторичное сырье. За счет подачи турбулизатор а увеличивается скорость прохождения потока через реакционный змеевик. Избыток перегретого} водяного пара может подаваться в отпарные колонны 10 и 11.
|
Парожидкостная смесь из печей 2 и 3 вводится параллельными потоками через четырехходовые краны 7 в две работающие камеры 5; две другие камеры (5) в это время подготавливают к рабочему периоду цикла. Горячее сырье подается в камеры вниз и постепенно заполняет их. Объем камер достаточно большой (внутренний диаметр 4,6—5,5 м, высота 27—28 м), и время пребывания сырья в них значительно. Здесь в камерах сырье подвергается крекингу. Пары продуктов разложения непрерывно выводятся из камер сверху и поступают в колонну 9, а тяжелый остаток остается. Жидкий остаток постепенно превращается в кокс.
В колонне 9 продукты коксования разделяются. С верха колонны уходят пары бензина и воды, а также газ коксования. Эти продукты проходят аппарат воздушного охлаждения 8, затем водяной холодильник 16 для дополнительного охлаждения и поступают в водогазоотделитель 17, где разделяются на водный конденсат, нестабильный бензин и жирный газ.
Часть нестабильного бензина нагнетается насосом 15 в качестве орошения на верхнюю тарелку колонны 9. Балансовое количество бензина проходит теплообменник 18, где нагревается за счет тепла легкого газойля, и передается в секцию стабилизации. Водный конденсат, отводимый из водогазоотделителя 17, подается насосом 14 через теплообменник 20 в пароперегреватели, расположенные в конвекционных секциях печей 2 и 3.
Легкий и тяжелый газойли, отводимые из отпарных колонн 10 и 11, направляются соответственно насосами 13 и 12 через теплообменники нагрева нестабильного бензина 18, водного конденсата 20 и
аппараты воздушного охлаждения 19 и 21 в резервуары.
После заполнения камер коксом, образующимся в процессе, камеры отключают и продувают водяным паром для удаления оставшихся жидких продуктов и нефтяных паров. Удаляемые продукты поступают вначале в колонну 9, а затем, когда температура кокса понизится до 400—405°С, поток паров отдувают в приемник 4. Подачу водяного пара продолжают до снижения температуры кокса до 200°С, далее в камеру подают воду до тех пор, пока вновь подаваемые порции воды, пары которой выходят в атмосферу, не перестанут испаряться, т. е. гока в сливной трубе приемника 4 не появится ода.
|
Кокс из камер выгружается гидравлическим способом — посредством гидрорезаков с использованием воды давлением 10—15 МПа.
Установка замедленного коксования мощностью 1,5 млн. т сырья в год аналогична описанной, но она оборудована шестью коксовыми камерами и тремя трубчатыми печами, каждая из которых обслуживает две камеры; диаметр камер 7 м, высота 30 м.
Технологический режим установки:
Температура, °С входа сырья в камеры выхода паров из камеры Давление в камерах, Мпа Кратность циркуляции (на сырьё) Время заполнения камеры коксом, ч | 490-510 440-460 0,18-0,60 0,1-1,1 |
Ниже приведены материальные балансы процесса коксования, полученные экспериментально (в лабораторных условиях), для различных видов сырья:
Показатели | Гудрон туймазинской нефти | Крекинг-остаток туймазинской нефти | Гудрон туркменской нефти | Смола пиролиза |
Характеристика сырья Плотность при 20 °С, кг/м3 Коксуемость, % (масс.) Содержание серы, % (масс.) | 16,0 2,80 | 23,0 3,30 | 12,0 0,50 | 8,6 0,56 |
Материальный баланс Взято, % (масс.) Сырьё | 100,0 | 100,0 | 100,0 | 100,0 |
Итого | 100,0 | 100,0 | 100,0 | 100,0 |
Получено, % (масс.) Газ Бензин Лёгкий газойль Тяжёлый газойль Кокс | 11,0 16,0 49,0 24,0 | 11,0 7,0 47,0 35,0 | 14,4 16,8 20,6 32,8 15,4 | 18,1 0,9 21,1 - 59,9 |
Итого | 100,0 | 100,0 | 100,0 | 100,0 |
На рис. III-6 приведены материальные балансы процесса замедленного коксования прямогонного остатка и крекинг-остатка; выходы даны в зависимости от плотности сырья (при 20° С) коксования.
Установка непрерывного коксования в псевдоожиженном слое кокса (термоконтактный крекинг)
Назначением процесса термоконтактного крекинга (ТКК) является получение дистиллятов, богатых ароматическими углеводородами, и газа, содержащего до 50 % (об.) непредельных углеводородов. В качестве сырья используют высокосернистые нефтяные остатки — гудрон вакуумной перегонки или мазут атмосферной перегонки.
|
Процесс может быть направлен на получение сырья для нефтехимии: увеличенного выхода газа, более богатого непредельными углеводородами, жидких продуктов, из которых могут быть выделены бензол, толуол и нафталин. Тяжелые фракции могут являться сырьем для производства технического углерода. В этом случае режим процесса более жесткий: температура в реакторе 600 °С и коксонагревателе 670—700°С. Газойли коксования используют на некоторых заводах (иногда после гидроочистки) "как компоненты сырья установки каталитического крекинга.
Установка термоконтактного крекинга состоит из реакторного блока (реактор, коксонагреватель, сепаратор-холодильник кокса, воздуходувка и др.) и блока разделения (парциальный конденсатор, ректификационная колонна, отпарная колонна, газосепаратор). Технологическая схема установки представлена на рис. III-7.
Сырье — гудрон, отводимый с низа вакуумной колонны, или мазут с низа атмосферной колонны — подается насосом 14 в реактор 11 через систему распылителей 9 (форсуночного типа) под уровень псевдоожиженного слоя частиц кокса, непрерывно циркулирующих в реакторном блоке и обеспечивающих подвод тепла в реактор. Форсунки размещаются обычно по высоте слоя в несколько ярусов, на крупных установках их число достигает 100.
Процесс крекинга осуществляется на поверхности горячих частиц кокса при температуре (600—620 °С). Продукты коксования — газы и пары — по выходе из слоя проходят через систему циклонных сепараторов 12 для отделения коксовой пыли и поступают в скруббер — парциальный конденсатор 13, который для уменьшения закоксовывания передаточных линий расположен непосредственно на реакторе 11На верх скруббера в качестве орошения подается охлажденный тяжелый газойль. За счет контакта паров продукта с тяжелым газойлем конденсируются наиболее тяжелые компоненты паров. Сконденсированная смесь (рециркулят) забирается с низа скруббера 13 и направляется насосом 15 в реактор 11.
Частицы кокса-теплоносителя с отложившимся на них тонким слоем образовавшегося в процессе кокса (балансового кокса) опускаются в низ отпарной секции реактора, при этом они продуваются встречным потоком водяного пара. Далее они перемещаются по изогнутому трубопроводу 8 (пневмотранспорт) -в коксонагреватель 5. С помощью воздуходувки 1 под распределительную решетку 6 коксонагревателя подается воздух в объеме, необходимом для нагрева циркулирующего кокса до заданной температуры. Кокс нагревается за счет теплоты сгорания части балансового кокса. Продукты сгорания (дымовые газы) проходят двухступенчатые циклоны 4, где от них отделяются мелкие частицы кокса, и поступают в паровой котел утилизатор (на схеме не показан).
|
Нагретый в коксонагревателе 5 кокс возвращается по изогнутому трубопроводу 7 (пневмотранспорт) в реактор 11. Транспортирующей средой также является водяной пар. Поскольку количество сжигаемого кокса меньше вновь образующегося, то избыток его в виде фракции более крупных частиц непрерывно выводится из системы через сепаратор-холодильник 3. Менее крупные частицы возвращаются из сепаратора-холодильника в коксонагре-ватель 5. Отделение мелких частиц кокса от крупных обеспечивается с помощью водяного пара, подаваемого в низ сепаратора. Выходящий с низа сепаратора 3 кокс транспортируется водяным паром в приемник (на схеме не показан). Размеры частиц кокса, циркулирующего в реакторном блоке колеблются в пределах от 0,075 до 0,300 мм, а частиц балансового кокса — от 0,4 мм и выше.
Из коксонагревателя 5 к верхнему днищу реактора 11 по линии 10 подается «горячая струя» частиц кокса. Таким образом здесь повышается концентрация частиц кокса в парах: частицы, механически воздействуя на устья циклонов 12, предотвращают их закоксовывание.
Пары бензина и воды, а также газ коксования, выходящие с верха колонны 18, охлаждаются в аппарате воздушного охлаждения 22 и холодильнике 23 и поступают в водогазоотделитель 24. Здесь происходит разделение продуктов на жирный газ, нестабильный бензин и водный конденсат. Бензин насосом 29 частично подается как орошение на верхнюю тарелку колонны 18, а балансовое его количество после теплообменника 25 направляется на стабилизацию.
С низа отпарной колонны 19 насосом 21 выводится легкий газойль. Обычно он используется как теплоноситель в теплообменнике 25 для нагрева нестабильного бензина (этот бензин передается в блок физической стабилизации, который на схеме не показан) утилизатор (на схеме не показан).. Далее легкий газойль доохлаждается в холодильнике воздушного охлаждения 26 и выводится с установки. Тяжелый газойль выводится с низа колонны 18, насосом 20 прокачивается через парогенератор 27 и аппарат воздушного охлаждения 28. Частично тяжелый газойль используется как орошение в скруббере 13, а балансовое его количество отводится с установки.
Избыток тепла отводится из колонны 18 промежуточным циркуляционным орошением (насос 16 и аппарат воздушного охлаждения 17). Топка 2 под давлением служит для разогрева системы при пуске.
Технологический режим реакторного блока:
Температура, °С Реактора Коксонагревателя Давление в реакторе и коксонагревателе, Мпа Кратность циркуляции кокс: сырьё Массовая скорость подачи сырья | 510-540 600-620 0,14-0,16 7-8 0,6-1,0 |
Ниже приводятся выходы продуктов коксования при переработке мазута и гудрона ромашкинской нефти:
Показатели | Мазут | Гудрон |
Характеристика сырья Плотность при 20°С, кг/м3 Коксуемость, % (масс.) Содержание серы, % (масс.) Материальный баланс Взято, % (масс.) Сырьё | 11,5 2,55 100,0 | 19,0 3,15 100,0 |
Итого | 100,0 | 100,0 |
Получено, % (масс.) Газ Бензин Легкий газойль Тяжелый газойль Кокс в т.ч. товарный | 8,4 10,7 9,9 59,5 11,5 6,3 | 15,7 20,0 19,2 24,6 20,5 11,5 |
Итого | 100,0 | 100,0 |
Учитывая высокое содержание серы в порошкообразном коксе, вызывающее значительное образование диоксида серы в продуктах сгорания, было предложено этот кокс газифицировать. В зарубежной литературе процесс термоконтактного крекинга, совмещенный с газификацией кокса, называют флексикокинг.
|
|
Эмиссия газов от очистных сооружений канализации: В последние годы внимание мирового сообщества сосредоточено на экологических проблемах...
Состав сооружений: решетки и песколовки: Решетки – это первое устройство в схеме очистных сооружений. Они представляют...
Организация стока поверхностных вод: Наибольшее количество влаги на земном шаре испаряется с поверхности морей и океанов (88‰)...
Типы сооружений для обработки осадков: Септиками называются сооружения, в которых одновременно происходят осветление сточной жидкости...
© cyberpedia.su 2017-2024 - Не является автором материалов. Исключительное право сохранено за автором текста.
Если вы не хотите, чтобы данный материал был у нас на сайте, перейдите по ссылке: Нарушение авторских прав. Мы поможем в написании вашей работы!