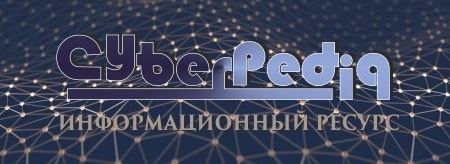
Биохимия спиртового брожения: Основу технологии получения пива составляет спиртовое брожение, - при котором сахар превращается...
Историки об Елизавете Петровне: Елизавета попала между двумя встречными культурными течениями, воспитывалась среди новых европейских веяний и преданий...
Топ:
Определение места расположения распределительного центра: Фирма реализует продукцию на рынках сбыта и имеет постоянных поставщиков в разных регионах. Увеличение объема продаж...
Марксистская теория происхождения государства: По мнению Маркса и Энгельса, в основе развития общества, происходящих в нем изменений лежит...
Устройство и оснащение процедурного кабинета: Решающая роль в обеспечении правильного лечения пациентов отводится процедурной медсестре...
Интересное:
Инженерная защита территорий, зданий и сооружений от опасных геологических процессов: Изучение оползневых явлений, оценка устойчивости склонов и проектирование противооползневых сооружений — актуальнейшие задачи, стоящие перед отечественными...
Что нужно делать при лейкемии: Прежде всего, необходимо выяснить, не страдаете ли вы каким-либо душевным недугом...
Подходы к решению темы фильма: Существует три основных типа исторического фильма, имеющих между собой много общего...
Дисциплины:
![]() |
![]() |
5.00
из
|
Заказать работу |
Содержание книги
Поиск на нашем сайте
|
|
Твердых промышленных и бытовых отходов
Сложившаяся в России система обезвреживания ТБО основана на приоритетном захоронении большей части отходов на полигонах и неорганизованных свалках, занимающих более 40 тыс. га.
Для определения методики переработки ТБО проводят анализ состава ТБО. По мере роста содержания бумаги ТБО становится легче сжигать. При содержании в таких отходах 20 и более процентов содержания органических веществ можно проводить компостирование. Данный биохимический процесс, осуществляется благодаря жизнедеятельности аэробных микроорганизмов (термофильных микроорганизмов). Эти микробы выделяют много тепла и нагревают ТБО до 700С. В результате болезнетворные микробы гибнут, сырье перегорает, в результате образуется компост. В естественных условиях этот процесс длится месяцами[ 7,10].
На заводах, где измельченные ТБО постоянно перемешивают, чтобы микробы имели требуемый им избыток воздуха, компостирование заканчивается за 2-3дня. Однако при снижении содержания пищевых отходов процесс резко замедляется и становится неэффективным.
Твердые промышленные и бытовые отходы (далее ТПО и ТБО) до сих пор в значительных объемах вывозят на полигоны и свалки.
Затратный, но крайней мере неопасный для природной среды вариант их обезвреживания заключается в капсулировании -- обволакивании токсичного отхода инертной пленкой (стеклообразной или полимерной).
При переработке использованных шин, изделий из резины и других полимеров в настоящее время преобладают методы механического измельчения с получением соответствующей крошки, которая находит применение в дорожном строительстве и других отраслях промышленности.
|
В мире возрастает объем повторного использования использованных изделий из ПЭТ (полиэтилентерефталата), один из немногих полимеров, пригодный для упаковки пищевых продуктов.
Первая стадия рециклинга ПЭТ измельчение (резание, размалывание), разделение компонентов отходов и очистка разделенных фрагментов. Российские предприятия используют много импортного оборудования для рециклинга, тем не менее можно наблюдать реальный прогресс в замещении импорта. Стандартная машина для резания (измельчения) недостаточно продуктивна, потому что ПЭТ бутылки слишком легкие и плохо отрабатываются роторным ножом. ООО "Салмис" (г.Москва) спроектировала технологическую линию для ПЭТ бутылок, которая позволяет в 7-10 раз увеличить производительность измельчения использованных ПЭТ бутылок и равна 1000 кг в час. Для повторного получения «пищевого»ПЭТ,на наш взгляд, наиболее надежен путь химического разложения использованных изделий из ПЭТ до исходных веществ ─ терефталевой кислоты и этиленгликоля ─ с последующим синтезом новой партии ПЭТ (рис.2.35).
Рис.2.35. Схема синтеза и химического разложения ПЭТ
Термические методы минимизации объема твердых
Отходов.Пиролиз и сжигание
Процесс пиролиза -термообработка при высоких температурах в отсутствие или небольших концекнтрациях кислорода - проводят, например, на установки ЭЧУТО (рис.2.36),разработка Энергетического института им. Г.М. Кржижановского).следующим образом [10]. В камеру термического разложения
Рис. 2.36. Схема установки ЭЧУТО:
1 – термореактор, 2 – люк нижний, 3 – мешалка, 4 – камера термического разложения, 5 – шибер, 6 – газораспределитель, 7 – люк загрузки,
8 – картридж катализатора, 9 – теплообменник, 10 – линия рецикла дымовых газов, 11 - байпас с задвижкой, 12 – труба, 13 – скруббер, 14 – пульт управления, 15, 19 – насос, 16 – вентилятор (дымосос), 17 – фильтр, 18 – люк воздушный, 20 – горелка, 21 – воздухозаборник; РАО - радиоактивные отходы, А - воздух, Б - топливо, В - кек на стадию загрузки, Г - сжатыйвоздух, Д - вода.
|
через шлюз загружают исходные твердые отходы. После закрытия промежуточного шибера и верхнего люка внутренний объем камеры оказывается полностью изолированным от внешней атмосферы. В горелочное устройство подают топливо и воздух и за счет выделяющегося при горении тепла разогревают установку. Образующиеся в процессе горения продукты сгорания проходят через дымоходы обогревательной камеры, отдают тепло на нагрев камеры термического разложения и, последовательно пройдя через катализатор
(на катализаторе протекает процесс окисления токсичного оксида углерода до диоксида), теплообменник, скруббер, дымосос, дымовую трубу и выбрасываются в атмосферу.
По мере роста температуры в камере термического разложения начинается процесс термического разложения органической составляющей отходов и выделяющиеся газообразные продуты пиролиза через вертикальный газоход, поступают в горелочное устройство, где сгорают, обеспечивая теплотой сгорания соответствующую часть необходимого для процесса топлива. Огонь,
обезвреживая вредные компоненты, содержащиеся впродуктах пиролиза, чем обеспечивается значительное снижение содержания вредных веществ в дымовых газах. При достижении 600-6500С основной процесс выделения парогазовых летучих продуктов пиролиза завершается, после чего осуществляют механическое перемешивание массы отходов в камере для активации остаточных теплообменных процессов.
После практически полного завершения процесса пиролиза через внутренний канал мешалки 3 в камеру подают газифицирующий агент (воздух, паровоздушная или водовоздушная смесь) и полукокс газифицируют до коксозольного остатка при вращательном и возвратно-поступательном (механическом и гидродинамическом) перемешивании материала с одновре-менной подачей газифицирующего агента и активацией процесса газификации во всем объеме камеры.
Образующиеся газообразные продукты газификации также поступают в горелку, где подвергаются огневому обезвреживанию. После завершения процесса газификации через нижний люк коксозольный остаток сбрасывается в колосники, где дожигается в ходе последующего цикла.
Сжигание радиоактивных отходов проводят на установках ЭЧУТО (рис.2.32,) имеет следующие характеристики [10]:
|
●способность перерабатывать отходы сложного морфологического состава с содержанием негорючих компонентов до 40% (в том числе металлов);
●относительно малые объемы отходящих газов и малые уносы радиоактивности из печи;
●высокая степень сокращения первоначального объема отходов;
●получение конечного продукта в виде плавленого химически стойкого материала.
Ромелт-процесс разработан в 1979 году Московским институтом стали и сплавов, основанный на использовании печи Ромелт[10]..Данная печь представляет собой модернизированный вариант печи Ванюкова, используемой для переработки медных сульфидных руд и концентратов на штейн (рис.2.37).
В Ромелт-процессе с выcокой скоростью протекают восстановительные реакции в барботируемой жидкой шлаковой ванне при1450-1650°С. Отходы подают в загрузочное устройство периодически. Их сбрасывают в шлаковую ваннуна поверхность шлаковогорасплава, через который продувают через ниж-
ниефурмывоздух, обогащенный О2.В ванне отходы быстро погружаются в интенсивно перемешиваемый, вспененный за счет кислородо-воздушного дутья расплав.
Кислород используют для генерации тепла в ванне за счет неполного сгорания угля до СО. Для обеспечения полной теплопотребности шлаковой
ванны, выходящие из ванны продукты неполного сгорания угля (СО, Н2) дожигают О2, подаваемым через верхние фурмы в надшлаковомпространствепечи. Часть теплаот этого дожигания возвращают в ванну и используют в процессе (порядка 60-65 %) на нагрев шлака и на компенсацию затраттепла на восстановление. Остальная часть физического и химического тепла выходитиз печи и может быть использованадля производства пара либо других энергетических нужд.
Попадая врасплав, отходыошлаковываются и потоками шлака распределяютсяпо его объему. При этом удаляется влага и летучие компоненты.
Температура шлака ─ 1400-1500°С. За счет интенсивной теплоотдачи отходы подвергают скоростному пиролизу и газифицированию. Минеральная часть отходов растворяется в шлаке, а металлические предметы ─ расплавляются. Жидкий металл опускается на подину.
|
При низкой калорийности отходов для стабилизации теплового режимав качестве дополнительного топлива в печь подают в небольших количествах энергетическийуголь. или природный газ.
Дляполученияшлаказаданногосоставазагружаютфлюс, как правило, известняк. Шлак выпускаютиз печи черезсифон непрерывно или периодически и подают в жидкомвиде на переработку.
Рис.2. 37. Схема печи РОМЕЛТ
(продольный и поперечный разрезы);
1 - Барботируемый слой шлака; 2 - фурмы длядожигания; 3 -патрубок
газоотвода; 4 - загрузочная воронка; 5 - загрузка;6 - крышка;7 - загрузочное устройство; 8 - слой спокойного шлака; 9 - барботажные фурмы
Химический состав шлака можно регулировать в широких пределах, получая композиции для производства различных стройматериалов ─ каменного литья, щебня, наполнителей для бетонов, минерального волокна, цемента.
Металлподаютв сифон и непрерывноили порциями сливают в ковш и далее передают на переработку или непосредственно у печи разливают в чушки или гранулируют с получением чугунной дроби.
Получаемый металл близокпо составу к чугуну, легированному медью, и может быть использован для получения чугунных отливок, художественного декоративного литья и т.д. Печные высокотемпературные газы (1400 - 1600°С) под разрежением, создаваемым дымососом, отводят из печи в паровой котел для охлаждения и полезного использования их энергия. В котле осуществляют полное дожигание газов. Затем охлажденные газы перед сбросом направляют в систему очистки от пыли и вредных примесей.
Для 1 т отходов, в зависимости от состава и влажности, потребляется 150 - 400 куб.м О2, ≈ 200 кг угля или ≈ 100 куб.м природного газа. Уголь может быть любого качества, в том числе угольная пыль, отсев и т. д.
Процесс пригоден для переработки одновременно ТБО и ТПО, в первую очередь железосодержащих, а также отходов горюче-смазочных материалов, отходов деревообработки, листвы, больничных отходов, отходов текстильной промышленности, а также некоторых токсичных органических и неорганических отходов.
Процесса «Ромелт» обладает следующими преимуществами по обеспечению экологической безопасности. Высокие температуры процесса (1400-1500°С), ступенчатое сжигание горючих компонентов отходов (неполное горение в объеме шлака с последующим дожиганием над ним), сочетание окислительно-восстановительного потенциала газовой фазы и температурного режима, обуславливают низкое содержание оксидов азота (NOХ) (менее 60 мг/м3) и др. вредных примесей в дымовых газах.
Сжигание отходов происходит непосредственно в объеме шлакового расплава, что позволяет осуществить их быстрый нагрев и зажигание, то есть исключается выделение при низкой температуре газов, содержащих органические соединения, в том числе такие особо опасные, как диоксины. Сжигание производится О2, или воздухом, обогащенным О2. Замена воздуха О2 в 2 - 4 раза сокращает объем дымовых газов, облегчает их очистку и уменьшает сброс токсичных веществ в атмосферу. Газы на выходе из ванны имеют температуру 1400-1600° С, что обеспечивает полное разложение углеводородов и сжигание их до CO2 и Н2О.
|
Выходя из агрегата дымовые газы проходят котел-утилизатор, где окончательно дожигаются воздухом. Котел производит пар энергетических параметров, который направляют в паровую турбину для получения электроэнергии, частично используемой для производства О2, идущегонапроцесс сжигания. Отходящие высокотемпературные газы могут также использоваться для получения горячей воды для систем городского или промышленного теплоснабжения. Охлажденные дымовые газы после очистки от пыли и газообразных вредных неорганических. соединений выбрасывают в атмосферу. Перевод в результате процесса щелочных и щелочноземельных металлов в парогазовую фазу способствует связыванию хлора, фтора, оксидов серы в безопасные соединения, улавливаемые газоочисткой.
Вместо большого количества экологически опасного зольного остатка (до 25% масс), содержащего тяжелые цветные металлы и диоксины, получают инертный шлак ─ ценное сырье для производства стройматериалов.
Количество пыли в 2 - 4 раза меньше, чем на традиционных печах. Вынос пыли из установки при переработке отходов составляет 0,5 - 1% от веса отходов, которую улавливают на газоочистке в твердом состоянии. Крупную пыль (до 60% по массе) возвращают в печь. Мелкая пыль представляет концентрат тяжелых цветных металлов (Zn,Pb,Cd,Sn и др.), пригодный для извлечения в цветной металлургии.
Сжигание является до сих пор наиболее распространенным способом термического обезвреживания твердых отходов. Примером может являться мусоросжигательный завод №4 представляющим собой производством по переработке и термическому обезвреживанию (сжиганию) твердых бытовых отходов жизнедеятельности населения города Москвы и коммерческих отходов торгового и гостиничного сектора города Москвых[ 16 ].
Завод расположен в производственной зоне «Руднево» и включает в себя комплекс различных основных и вспомогательных производств, взаимосвязанных по технологической схеме (рис. 2.38).
Проектная мощность завода составляет:
●По переработке отходов 275 тыс. тонн за год,
●По термическому обезвреживанию 235 тыс. тонн за год.
В процессе переработки отходов из них для последующей утилизации осуществляется отбор наиболее ценных компонентов:
●картона и бумаги,
●тканевых материалов,
●стекла,
●черных металлов,
а также хлорсодержащих пластмасс, исключение которых из процесса сжигания позволяет значительно снизить нагрузки на газоочистное оборудование.
В результате эксплуатации мусоросжигательного завода №4 ГУП «Экотехпром» в промзоне «Руднево» образуются отходы в виде смеси котла-утилизатора (52,6%), циклонов (26,4%), абсорбера (4,6%), а также летучей золы (золы уноса) или золы рукавного фильтра (16,4%).
Зола как вторичный токсичный отход, относящийся к 3 классу (смесь золы котла-утилизатора, циклонов, абсорбера и золы рукавного фильтра) опасности, подлежит вывозу на полигоны захоронения отходов с соблюдением соответствующих требований безопасности.
Рис. 2.38. Технологическая схема завода по переработке неутилизируемой части бытовых отходов: 1_Мостовой грейферный кран; 2_Загрузочная воронка с питателем; 3_ Печь с кипящим слоем; 4_Газовые горелки розжига; 5_Стабилизирующая газовая горелка; 6_ Котел-утилизатор; 7_ Сдвоенный циклон; 8_Распылительный абсорбер; 9_Реактор летучего потока; 10_Рукавный фильтр; 11_Бункер песка; 12_Подпиточный бункер; 13_ Бункер известковой муки;14_ Двойное вибросито; 15_ Шлаковый транспортер; 16_ Бункер шлака;17_Бункеры золы уноса; 18_Бункер продуктов газоочистки; 19_Бункер гидрата кальция; 20_Резервуар для приготовления известкового молока;21_Вентилятор рециркуляции дымовых газов; 22_Дымосос; 23_ Вентилятор вторичного воздуха; 24_Вентилятор первичного воздуха; 25_Вентилятор для удаления золы; 26_Бункер смеси активированного угля и извести;27_Система подогрева рукавного фильтра; 28_Паровая турбина;
29_ Генератор; 30_ Дымовая труба.
Завод построен с использованием современных и отработанных зарубежных и отечественных технологий в области термического обезвреживания отходов и утилизации образующейся теплоэнергии. Технологическое оборудование для сжигания отходов и очистки дымовых газов полностью изготовлено в Германии. Оборудование для утилизации вырабатываемого пара, производства электрической и тепловой энергии, а также все вспомогательное оборудование произведено в РФ.
На заводе установлены три технологические линии по сжиганию отходов с производительностью по 13,5 т/час каждая. Сжигание предварительно подготовленных отходов производится в печах с вихревым кипящим слоем инертного материала.
Сжигание бытовых отходов с вихревым кипящим слоем позволяет:
●исключить механические устройства в зоне сжигания отходов;
●обезвреживать отходы в широком диапазоне изменения их влажности и зольность;
●достигать высокие удельные тепловые нагрузки при равномерном распределении температур в кипящем слое;
●обеспечивать пониженное содержание оксидов азота в дымовых газах.
Прием ТБО. Поступающие на завод отходы взвешивают на участке подвоза (2 линии с производительностью 25 машин в час). Основная нагрузка на весовую приходится на промежуток времени 8:30-13:30 (первый рейс мусоровозов). В весовой установлены приборы для контроля радиоактивности. Для обеспечения равномерной разгрузки мусоровозного транспорта в приемном отделение предусмотрено 8 постов разгрузки. Мусоровоз выгружается непосредственно на ленту питателя (4 поста) участка подготовки ТБО, либо в промежуточный бункер объемом 1000 м³ (4 поста), и краном подаются в четыре приемные воронки системы подготовки ТБО.
Подготовка ТБО. Участок подготовки ТБО состоит из 4 линий производительностью 25 т ТБО/ч каждая. Работу осуществляют в одну смену (12 часов, 305 суток в году).ТБО принимают на ленту питателя типа 2-24-90Б электростальского завода тяжелого машиностроения (ширина ленты – 2,4 м, длина – 9 м, угол наклона – 150, скорость ленты 0,06-0,17 м/с) укомплектованного поперечной балкой, регулирующей выходящий слой. Над лентой питателя размещены 2 крана грузоподъемностью 5 тонн для обслуживания питателя и извлечения с ленты крупногабаритных (более 1 м) предметов. Крупногабаритные предметы складируются в бункеры и вывозятся.
С питателя ТБО поступает на наклонный ленточный конвейер. На наклонной конвейерной ленте (ширина – 1600 мм, скорость, регулируемая около 0,2 м/с) поступающие на завод ТБО (250 тыс. тонн в год) проходят стадию ручной сортировки. Толщина слоя отходов на ленте транспортера составляет 100 - 400 мм, что не позволяет обеспечить высокую степень извлечения целевых фракций. Количество извлекаемых из ТБО утилизируемых компонентов (бумага, картон, текстиль, стекло, полимеры), а также балласта и мешающих компонентов (камни, керамика, строительный мусор, хлорсодержащие полимеры) оценивается в 117 т/сут. (14,3% от исходных ТБО). Ценные фракции прессуются с формированием обвязных тюков (2 пресса для легких фракций). Каждый пресс оснащен счетчиком обвязных тюков. Вес выделенных фракций регистрируют лишь в момент их отгрузки потребителю или на захоронение. Планируется строительство цеха переработки утилизируемых фракций.
Остальные отходы проходят грохочение (4 барабанных грохота – 7,3 м, диаметр – 2,5 м, ячейки 250 мм, скорость вращения – 15 об/мин, паспортная производительность - 20 т/ч), после чего подрешетный продукт (60,8%) проходит магнитную сепарацию с отделением черного металла (0,9%), а надрешетный продукт подвергается дроблению (роторные ножницы из двух валов с фрезерами фирмы Линдеман, производительностью 30–40 т/ч) и повторному грохочению (250 мм). Надрешетный продукт (2,3%) проходит повторное дробление, после чего соединяется с подрешетным продуктом первого и второго грохочения. Из общего потока (84,8% исходных ТБО) отделяется черный (1,2%) и цветной металл (0,3%). Выделенный металл прессуется (пресс для металла Азовского ПО «Донпрессмаш», усилие прессования 90-100 тс, время цикла пакетирования 1,5 мин, размер тюка 400*320*320 мм). Остаток сортировки (683 т/сут, 83,3% массы исходных ТБО) направляется в основной бункер, из которого происходит загрузка топок ROWITEC.
Термическая обработка. Сжигание отходов осуществляют в топке ROWITEC, которая разделена на зону вихревого кипящего слоя и зону дожигания (надслоевое пространство). Зона вихревого кипящего слоя формируется разделенной на две половины колпачковой сопловой решеткой с 36 напорными камерами для подачи первичного воздуха:
1) Динамическая зона в центре включает в себя 12 напорных камер. Предварительная установка расхода возможна в каждой группе камер с помощью установленных вручную заслонок с жесткой фиксацией.
2) Зоны завихрения с обеих сторон динамической зоны включают в себя по 6 напорных камер, воздушные потоки которых также регулируют при помощи заслонок с жесткой фиксацией.
3) Зоны выгрузки негорючих материалов снаружи обеих сторон завихрения и в нижней наклонной части распределительного коллектора включают в себя по 6 напорных камер. Расход воздуха контролируется с помощью заслонок.
Расход первичного воздуха (подается из помещения приемного бункера) в первые две зоны устанавливается на уровне, обеспечивающем эффект стабильного вихревого кипящего слоя. Расход воздуха устанавливается в зависимости от нагрузки. Дроссельные заслонки установлены вручную в зонах 1 и 2 таким образом, что в зону 2 постоянно в определенном соотношении подается больше воздуха, чем в зону 1.
В надслоевое пространство вводится вторичный воздух (подается из помещения приемного бункера), расход которого определяется заданной концентрацией кислорода в домовых газах.
Воздухозаборные отверстия расположены справа и слева над бункером ТБО, каждое из которых снабжено всасывающим фильтром и шумоглушителем. Всасывающие фильтры регулируются с помощью регулятора перепада давления.
Воздух, поступающий в зону 1 и 2, в случае необходимости нагревается при помощи пароподогревателя.
Температурный режим для топки ROWITEC: температура в слое - около 650° С, в надслоевом пространстве и на выходе дымовых газов из топки - около 950° С. Газы выдерживаются при этой температуре не менее 2 секунд за счет длинного газохода.
Для снижения температуры в сжигательном устройстве и содержания существует возможность рециркуляции дымового газа в нижний ярус распределения вторичного воздуха в сжигательном устройстве.
Для направления золы из топочного устройства в зону выгрузки используется воздух, подаваемый в зону выгрузки через 12 напорных камер, расположенных снаружи обеих зон завихрения. Выгрузка золы осуществляется поочередно двумя разгрузочными водоохлаждаемыми шнеками. Температура золы на входе в шнек составляет 600-650° С. Смесь песка и золы слоя подается шнеком (скорость вращения шнеков 2,3-23,3 об /мин.) на один из двух двухдечныхвиброгрохотов фирмы Mogensen (максимальная температура материала - 500°С, максимальный размер фракций на входе - 300 мм, на деках колосников установлена ситовая ткань с квадратным переплетением). Частицы более 1,6 мм направляют транспортером на участок переработки шлака, а мелкие, шнековым транспортером, а затем ковшовым элеватором (длина цепи 29,75 м), направляют в перепускную емкость (объем 5 м3, максимальная температура материала 500°С). Туда же по мере необходимости добавляют свежий песок из силоса песка (объем 7,5м3), куда он поступает с помощью пневмотранспорта из участка подготовки аддитивов. Выгрузка перепускной емкости в топку управляется уровнемерами минимального и максимального уровня. При достижении максимального уровня слоя открывается клапан выгрузки, который закрывается после разгрузки емкости до минимального уровня. Предусмотрено, что в случае превышения перепада давления в слое выше 140 мбар, содержимое перепускной емкости направляется непосредственно на конвейер силоса золы кипящего слоя.
Расход песка оценивается в 340 кг/ч (при сжигании 24 т/ч ТБО) или 10,18 кг/т ТБО. Регулируемым параметром, определяющим подачу песка в топку, является высота слоя в топке, определяемая по перепаду давления. Регистрация количества песка, загружаемого в перепускную емкость, не предусмотрена. Оценить средний расход песка возможно лишь по времени расходования партии, загруженной в силос песка.
Для формирования кипящего слоя, по данным ТЭО, необходима единовременная загрузка 40 т песка. Фактическое количество загружаемого в топку песка составило величину порядка 90-95 т.
Утилизация тепла в котле-утилизаторе. За каждым сжигательным устройством установлено по котлу утилизатору. Дымовые газы сжигательного устройства направляются к котлу по обмурованному газоходу круглого сечения (диаметр - 4050 мм). На выходе дымовых газов сжигательного устройства и на входе в котел установлены компенсаторы. После выхода из сжигательного устройства газоход расположен наклонно вверх и, в последней части, вниз в направлении входа в котел, что предотвращает значительное отложение пыли. В высшей точке газохода находится заслонка с противовесом для сброса избыточного давления из сжигательного устройства.
Котёл-утилизатор барабанный с Г-образной горизонтальной компоновкой, с естественной циркуляцией, имеет две ступени экомайзера и две ступени пароперегревателя.
Подготовку известкового молока осуществляют централизовано для трех линий в двух емкостях, где происходит смешивание гидроксида кальция с водой. Заданная концентрация (15%) обеспечивается дозированием гидроксида кальция в заполненной водой смеситель до заданной плотности известкового молока. Гидроксид кальция из силоса, объемом 200 м3, барабанным дозатором через шнековый транспортер подается в одну из емкостей приготовления известкового молока. Силос гидроксида кальция периодически подается из бункера, расположенного на участке подготовки аддитивов.
Выработкаэлектроэнергии. Дымовые газы на выходе из топки, имеющие температуру около 900°С, направляют в котел утилизатор, вырабатывающий за счет отбора тепла газов пар, давлением 1,6МПа и температурой310°С.
Выработанный котлами пар используют частично для получения электроэнергии, в том числе для собственных нужд завода, а частично отбирается для покрытия нужд завода в тепле.Для сглаживания возможных колебаний паропроизводительности котлов-утилизаторов и параметров пара установлены два паровых котла ПО «Белэнергомаш» БЭМ-25/1,6-310Г.
Цех переработки золовых отходов. В составе золы, присутствуют (подвижные) водорастворимые формы токсичных металлов, а также мышьяка и селена, которые при утилизации являются чрезвычайно опасными источниками вторичного приземного атмосферного воздуха, почвы, поверхностных и грунтовых вод.
Существует несколько способов обезвреживания золовых отходов:
●Стеклование в электродуговых печах.
●Капсулирование с использованием различных марок цемента
●Метод применения гумино-минерального концентрата (ГМК)с последующим получением технологического грунта. Данный метод экологически безопасен, а применяемый гумино-минеральный концентрат, изготавливаемый из природных продуктов, не вступает в конфликт с окружающей средой.
Технология обезвреживания золоотходов путем применения ГМК разработано и освоено ООО «ЭФАТ».
Применение гуминовых кислот в форме модифицированного гумино-минерального концентрата обеспечивает эффективную детоксикациюзоловых отходов за счет связывания тяжелых металлов, а именно образование таких соединений гуминовых кислот с тяжелыми металлами, подвижность которых в природных объектах существенно ограничена. Кроме этого гуминовые кислоты ускоряют протекание биогеохимических процессов, в результате которых нейтрализуется и обезвреживается большое количество органических и неорганических экотоксикантов.
Рекомендуют производить смешивание смеси зол котла-утилизатора, циклона, абсорбера и рукавного фильтра, при этом оптимальная доза ГМК составляет до 30% от массы смеси зол, а объем воды 70% от массы ГМК. В пересчете на техногенный грунт оптимальная масса смеси зол составляет 66%, масса ГМК до 20% и масса воды - 14%.
2 .7. Нанотехнологии и повышение уровня
Техносферной безопасности
Нанотехнология— область прикладной науки и техники, имеющая дело с объектами размером менее 100 нанометров (1 нанометр равен 10−9 метра).Нанотехнология‑ совокупность методов и приемов, обеспечивающих возможность контролируемым образом создавать и модифицировать объекты, включающие компоненты с размерами менее 100 нм, имеющие принципиально новые качества и позволяющие осуществлять их интеграцию в полноценно функционирующие системы большего масштаба[ 1,12,14,33,37 ].
Фундаментальные исследования в этом направлении дали начало развитию новой области знаний, которая, очевидно, в обозримом будущем внесет революционные изменения в технологии XXI века. Подобным структурам соответствует такое состояние вещества, когда в их поведении проявляются и доминируют принципиально новые явления, в числе которых квантовые эффекты, статистические временные вариации свойств и их масштабирование в зависимости от размеров структур, преобладающее влияние поверхности, отсутствие дефектов в объеме монокристаллов, значительная энергонасыщенность, определяющая высокую активность в химических реакциях, процессах сорбции, спекания, горения и т.п. Эти явления наделяют наноразмерные частицы и структуры уникальными механическими, электрическими, магнитными, оптическими, химическими и другими свойствами, которые открывают дверь в принципиально новую область манипулирования материей с применениями, трудно представимыми в обычной ситуации.
Следует особо отметить, что отличие свойств малых частиц от свойств массивного материала известно ученым давно и используется в различных областях техники. Примерами наноразмерных структур могут служить широко применяемые:
● аэрозоли,
●красящие пигменты,
●цветные стекла, окрашенные коллоидными частицами металлов.
Впечатляющие примеры связаны с биологией, где природные объекты имеют наноструктуры на уровне клеточного ядра.
Таким образом нанотехнология, как научное направление, не является чем-то новым. Качественная характеристика нанотехнологии заключается в практическом использовании нового уровня знаний о физико-химических свойствах материи. В этом одновременно и исключительность нанотехнологии – новый уровень знаний предполагает выработку концептуальных изменений в направлениях развития техники, медицины, сельскохозяйственного производства, а также изменений в экологической, социальной и военной сферах.
Важной отличительной особенностью нанометрового масштаба является также способность молекул самоорганизовываться в структуры различного функционального назначения, а также порождать структуры, себе подобные (эффект саморепликации). Методами так называемого механосинтеза реализуются новые, не имеющие аналогов, молекулярные соединения. Проведены эксперименты, в которых тысячи и десятки тысяч молекул соединяются в кристаллы, обладающие изначально заданными свойствами, которые не встречаются у природных материалов.
Использование перечисленных выше свойств в практических приложениях и составляет суть нанотехнологии. На ее основе уже реализованы:
●образцы наноструктурированных сверхтвердых, сверхлегких, коррозионно- и износостойких материалов и покрытий,
●катализаторов с высокоразвитой поверхностью,
●нанопористых мембран для систем тонкой очистки жидкостей,
●сверхскоростных приборов наноэлектроники.
Наноструктуры, построенные «из первых принципов», с использованием атомномолекулярных элементов, представляют собой мельчайшие объекты, которые могут быть созданы искусственным путем. Они характеризуются новыми физическими, химическими и биологическими свойствами и связанными с ними явлениями. В связи с этим возникли понятия нанонауки,нанотехнологии и наноинженерииию
Нанонаука занимается фундаментальными исследованиями свойств наноматериалов и явлений в нанометровом масштабе,
Нанотехнология – созданием наноструктур,
Наноинженерия – поиском эффективных методов использованиянаноматериалов и изделий (см. рис. 2.39).
Наноматериалы‑ материалы, содержащие структурные элементы, геометрические размеры которых хотя бы в одном измерении не превышают 100 нм, и обладают качественно новыми свойствами,функциональными и эксплуатационными характеристиками.
В настоящее время наноматериалы используют для изготовления:
●защитных и светопоглощающих покрытий,
●спортивного оборудования,
●транзисторов,
●светоиспускающих диодов,
●топливных элементов,
●лекарств и медицинской аппаратуры,
●материалов для упаковки продуктов питания,
●косметики и одежды.
Рис. 2.39. Научные основы и объекты нанонауки
и нанотехнологии[15]
Примером может служить использование добавок на основе наноразмерного оксида церия к дизельному топливу, что позволяет на 4-5% повысить КПД двигателя и снизить степень загрязнения выхлопных газов.
Наноэнергетика включает в себя[14] топливные элементы: водородные элементы, передача энергии (высокотемпературные сверхпроводники, формирование градиента температур) внимание уделяют топливным элементам
с твердым полимерным электролитом (ТПЭ). В России успешные исследования и разработки ы этом направлении ведутся в РНЦ «Курчатовский институт» и некоторых других организациях. В качестве носителей катализаторов сейчас, как правило, используют сажу или технический углерод. Недавние эксперименты показали, что замена их на углеродные нанотрубки или нановолокна позволяет повысить активность электрокатализаторов и эффективность работы топливных элементов с ТПЭ.
Уникальные свойства углеродных нанотрубок (УНТ) и нановолокон (УНВ) – высокая удельная поверхность, электропроводность, прочность - позволяют создавать на их основе эффективные носители катализаторов для различных процессов.
Нанобиотехнология объединяет достижения нанотехнологии и молекулярной биологии[14]. В ней широко используется способность биомолекул к самосборке в наноструктуры. По мнению ряда ученых, нанобиотехнологии существенно упрощают и ускоряют решение традиционных проблем генетики сельскохозяйственных видов. Таких, к примеру, как контрольпроисхождения,
выявление носителей неблагоприятных мутаций или инфекций, а также генов, связанных с желательными хозяйственно ценными признаками, включая устойчивость к неблагоприятным факторам окружающей среды.
Современные достижения в области наноматериалов и нанотехнологий открывают новые возможности для повышения в десятки раз тактико-технических характеристик систем безопасности и являются по своей сути инновационными, поскольку направлены на создание, главным образом, новой продукции, востребованной рынком систем безопасности. В ближайшие 3–10 лет наиболее перспективны следующие направления использования нанотехнологий в системах безопасности [32]:
1.Новые средства и методы контроля и защиты документов от подделки, путем использования наноматериалов, микропечати, тонких электронных схем, бумаги с добавлением наночастиц, компактных устройств считывания данных.
2. Системы контроля доступа в помещения на основе наносенсоров, определяющих отпечатки пальцев, тепловые рисунки вен руки или головы, геометрические формы руки в динамике.
3.Многофункциональные сенсоры типа «электронный нос», который способен обнаруживать и идентифицировать сверхмалые количества взрывчатых, наркотических и опасных веществ.
4. Компактные, чуткие и информативные портативные и стационарные металлоискатели и детекторы движения на основе наносенсоров..«Умная наносенсорнаяпыль» для охраны границ и периметров объектов.
Объемное наноструктурирование как инструмент «технологического мониторинга» позволит решать задачи по обеспечению качества и повышенного ресурса оборудования, устранить необходимость завышенного коэффициента запаса прочности, что повы
|
|
Индивидуальные и групповые автопоилки: для животных. Схемы и конструкции...
Механическое удерживание земляных масс: Механическое удерживание земляных масс на склоне обеспечивают контрфорсными сооружениями различных конструкций...
Семя – орган полового размножения и расселения растений: наружи у семян имеется плотный покров – кожура...
Типы оградительных сооружений в морском порту: По расположению оградительных сооружений в плане различают волноломы, обе оконечности...
© cyberpedia.su 2017-2024 - Не является автором материалов. Исключительное право сохранено за автором текста.
Если вы не хотите, чтобы данный материал был у нас на сайте, перейдите по ссылке: Нарушение авторских прав. Мы поможем в написании вашей работы!