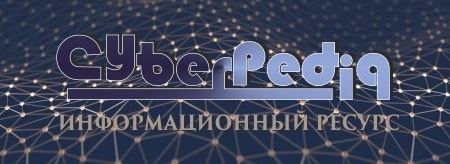
Автоматическое растормаживание колес: Тормозные устройства колес предназначены для уменьшения длины пробега и улучшения маневрирования ВС при...
Историки об Елизавете Петровне: Елизавета попала между двумя встречными культурными течениями, воспитывалась среди новых европейских веяний и преданий...
Топ:
Марксистская теория происхождения государства: По мнению Маркса и Энгельса, в основе развития общества, происходящих в нем изменений лежит...
Интересное:
Инженерная защита территорий, зданий и сооружений от опасных геологических процессов: Изучение оползневых явлений, оценка устойчивости склонов и проектирование противооползневых сооружений — актуальнейшие задачи, стоящие перед отечественными...
Средства для ингаляционного наркоза: Наркоз наступает в результате вдыхания (ингаляции) средств, которое осуществляют или с помощью маски...
Наиболее распространенные виды рака: Раковая опухоль — это самостоятельное новообразование, которое может возникнуть и от повышенного давления...
Дисциплины:
![]() |
![]() |
5.00
из
|
Заказать работу |
Содержание книги
Поиск на нашем сайте
|
|
Тепловой расчет системы пылеприготовления выполняют с целью определения кол-ва тепла, необходимого для подсушки сырого топлива от начальной влажности Wр до конечной влажности пыли Wп.
Тепловой баланс системы пылеприготовления составляется обычно на 1кг топлива в виде уравнения, выполняющего равенство прихода и расхода топлива кДж/кг.
,
где qс.а – физическое тепло сушильного агента;
– тепло выделяемое за счёт механической работы мелющих органов;
qпрс– физическое тепло присосанного воздуха;
qисп– тепло затраченное на испарение влаги топлива,
q2 – тепло, уносимое уходящим сушильным агентом, без учета тепла водяных паров испарённой влаги,
qтл– физическое тепло затраченное на подогрев топлива в процессе сушки,
q5 – потеря тепла от охлаждения мельничной установкой.
Вопрос № 86
Схемы разгрузки, подготовки и подвода жидкого топлива к котлам. Параметры топлива и пара. Оборудование мазутонасосной
Для перекачки мазута, заполнения и слива его из емкостей температура мазута должна быть не ниже 60—70°С, что соответствует вязкости не выше 30° ВУ, иначе он будет налипать на стенки.
Рис. 3.13. Технологическая схема подготовки мазута на электростанции.
1 — цистерна с мазутом; 2 — сливное устройство; 3 — фильтр грубой очистки; 4 — сливной резервуар с подогревом; 5 — перекачивающий насос; б — основной резервуар; 7, 3 —линии рециркуляции мазута; 9 — насос первого подъема: 10 —обратный клапан; 11 —подогреватель мазута; 12 — фильтр тонкой очистки; 13 — насос второго подъема; 14 — запорная задвижка; 15 — регулятор расхода; 16 — расходомер: 17 — задвижка; 18 — форсунка.
Технологический тракт подготовки мазута на электростанции (рис. 3.13) включает: приемно-сливное устройство (сливные эстакады с желобами, приемные резервуары с погруженными перекачивающими насосами), основные резервуары для хранения постоянного запаса мазута, мазутонасосную, систему трубопроводов для мазута и пара, группу подогревателей мазута и фильтров. Подготовка мазута перед сжиганием заключается в удалении механических примесей, повышении давления мазута и его подогреве, необходимых для снижения потерь энергии на транспорт мазута к котлам электростанции и его тонкого распыления в форсунках горелочных устройств. Температура мазута в баках поддерживается на уровне 60—80°С в любое время года за счет циркуляционного Подогрева путем возврата в бак части (до 50%) разогретого во внешних подогревателях мазута.
Типовой является двухступенчатая схема подачи топлива, разработанная институтом; «Теплоэлектропроект». По этой схеме подача топлива в устройства для подготовки к сжиганию (подогрев, перемешивание мазута в резервуарах, фильтрация от внешних загрязнений) осуществляется при низком давлении мазута (около 1 МПа), а насосы второго подъема -перекачивают в главное здание мазут при высоком давлении (3,5—4,5 МПа).
|
При высокой скорости мазута в распыливающих форсунках может иметь место сильный абразивный износ металла мазутных каналов форсунки и быстрый выход ее из строя. Кроме того, при размере каналов менее 3 мм не исключено их забивание крупными твердыми частицами. Очистка мазута от твердых фракций происходит вначале в фильтрах грубой очистки с размером ячеек сетки 1,5×1,5 мм2, а затем в фильтрах тонкой очистки с ячейками 0,3—0,5 мм, установленных перед насосами второй ступени на подогретом мазуте.
Повышение температуры мазута обеспечивается в паровых подогревателях до температуры, меньшей температуры вспышки паров (90–140ºС) и не выше 95ºС во избежание вскипания влаги. Для поддержания температуры мазута на нужном уровне независимо от потребления его котлом обеспечивается непрерывный расход его ч/з линию за счет частичного возврата в бак (рециркуляция).
Вопрос № 87
Подготовка к сжиганию газа
Рис. 16.3. Схема газового хозяйства ТЭС:
1— запорная задвижка; 2 — расходомер; 3 — фильтр; 4 — регулятор давления; 5—предохранительный клапан; 6 — байпасная линия; 7 — регулятор расхода газа; 8 — импульсный отсечный быстродействующий клапан; 9— пробковый кран
Газ поступает на электростанцию от магистрального газопровода или газораспределительной станции (ГРС) с давлением 0,7 — 1,3 МПа. Газохранилищами электростанции не располагают. Для снижения давления поступающего газа до необходимого уровня у горелок (0,13—0,2 МПа) предусматривается его дросселирование в газорегуляторном пункте (ГРП), который ввиду повышенной взрывоопасности и резкого шума при дросселировании газа размещают в отдельном помещении на территории ТЭС (рис. 3.14).
|
В каждом ГРП выполняется несколько (чаще три) ниток газопровода с установкой регуляторов давления, одна из которых является резервной. Кроме того, предусматривается байпасная линия помимо регуляторов. Для очистки газа от механических примесей перед регулирующими клапанами имеются фильтры. Регулирующие клапаны поддерживают необходимое давление «после себя». Для защиты от аварийного повышения давления газа установлены предохранительные клапаны. Количество газа, прошедшего газорегуляторный пункт, регистрируется расходомерами.
Основными устройствами на газопроводе к каждому паровому котлу являются автоматический регулятор расхода газа (АРР) и отсекающий быстродействующий клапан (БК). Регулятор АРР обеспечивает необходимую тепловую мощность котла в любой момент времени. Импульсный отсекающий БК отключает подачу газа в топку парового котла в случае аварийной ситуации, когда поступление газа может создать опасность взрыва (обрыв факела, падение давления воздуха у горелок, останов электродвигателей дымососа или дутьевого вентилятора и т. п.).
Для исключения взрывоопасных ситуаций в нерабочий период газовые линии продувают воздухом через специальные отводы в атмосферу (свечи). Последние выведены за пределы здания в места, недоступные для пребывания людей. Через свечи вытесняют также газовоздушную смесь из газопроводов перед растопкой котла. Окончание продувки линии газом определяют по содержанию кислорода в пробе не выше 1%.
Эксплуатация газового оборудования на электростанции ведется в соответствии с правилами безопасности в газовом хозяйстве Госгортехнадзора.
Вопрос № 88
Конструкции циклонов, мигалок, питателей и бункеров системы пылеприготовления
Циклон применяется для отделения готовой пыли от транспортирующего воздуха. Отделение происходит за счет центробежного эффекта, а также при повороте воздушного потока в центральную отводную трубу. На входе в нее устанавливают направляющие лопатки для обеспечения спокойного входа воздуха. Центробежный эффект усиливается с увеличением входной скорости в циклон и при уменьшении диаметра циклона. Однако при росте скорости усиливается возврат отсепарированных частиц в поток воздуха и уменьшается КПД очистки потока, а уменьшение диаметра ведет к росту сопротивления циклона и необходимости установки вместо одного нескольких циклонов на поток аэропыли. Обычная скорость пылевоздушного потока на входе в циклон wц=18–22 м/с
Коэффициент полезного действия циклонов составляет 80—93 %. Следовательно, сушильный агент после циклона содержит еще много мельчайших частиц пыли, не уловленных в циклоне. Диаметр циклонов, применяемых в пылесистемах электростанций, Dц = 3–4 м. В схемах пылеприготовления, где необходимо наиболее полно отделить пыль от транспортирующего ее сушильного агента, кроме основного циклона большого диаметра применяют батарейные циклоны, представляющие собой набор большого числа циклонов малого диаметра (200—300мм). Сочетание основного и батарейного циклонов обеспечивает отделение пыли с КПД около 99 %.
|
Работа циклона резко ухудшается при подсосе в него снизу атмосферного воздуха. Поэтому под циклоном всегда устанавливают два последовательно расположенных на течке пыли клапана-мигалки, которые пропускают накопившуюся пыль порциями с последующим закрытием течки. При этом достаточную плотность поддерживает слой пыли, который постоянно находится в пылеподводящем патрубке. Мигалки устанавливают не только под циклоном, но и под другими элементами пылесистемы, из которых необходимо выдать топливо или его пыль без присоса воздуха.
Бункера сырого (дробленого) угля устанавливают индивидуально для каждого парового котла, имеющего пылеприготовительную установку (один-два бункера). Вместимость бункеров должна обеспечить работу котла с номинальной нагрузкой от 5 до 8 ч в зависимости от вида топлива. Для исключения калипакия сырого угля на стенки они имеют угол наклона не менее чем 60–70 ºС в зависимости от влажности топлива и одновременно снабжаются пневмообрушителями.
Бункер пыли является емкостью для хранения запаса пыли около работающего котла. Объем пылевого бункера определяют, исходя из работы парового котла на запасе пыли в нем в течение 2—3 ч с номинальной нагрузкой и с сохранением по истечении этого срока минимальной высоты слоя пыли в бункере не менее 3м для обеспечения равномерной загрузки питателей пыли.
Бункера пыли должны иметь вертикальные гладкие металлические стенки для исключения налипания и застревания пыли в бункере. У выпускных патрубков наклон стенок к горизонту должен быть больше угла естественного откоса свежей угольной пыли, т. е. не менее 65°.
Питатели сырого угля устанавливают для равномерной и регулируемой подачи топлива в углеразмольные мельницы. На электростанциях находят применение ленточные (для сухих утлей) и скребковые (для влажных, склонных к замазыванию углей) питатели угля. Ленточный питатель сырого угля представляет собой конвейер с прорезиненной транспортной лентой. Подача топлива регулируется положением щибера, изменяющего толщину слоя топлива на ленте, либо изменением скорости ее движения. Здесь же происходит взвешивание топлива с автоматической записью расхода. Скребковый питатель также выполнен как конвейер, но его лента имеет вертикальные скребки (перегородки) обеспечивающие транспорт увлажненного слипающегося топлива. Для уменьшения присоса холодного воздуха в мельницу в течке топлива за питателем устанавливается клапан-мигалка, но еще лучше выполнить питателъ с закрытым кожухом. В последнее время стали внедряться шнековые питатели сырого угля.
|
Питатели пыли устанавливают под бункером пыли для регулирования подачи ее в пылепроводы. Питатели пыли выполняют в двух модификациях. Шнековый питатель регулирует подачу пыли изменением частоты вращения шнека. Для равномерности заполнения ячеек шнека пылью передние витки имеют увеличивающуюся высоту стенки, а для сокращения самопроизвольного протекания пыли вдоль шнека шаг его последних витков уменьшается.
Лопастный питатель исключает перетекание пыли. Подача пыли производится вращающимися звездочками, расположенными между неподвижными со сбросными окнами на противоположных сторонах. Регулирование частоты вращения питателей пыли производится электродвигателями постоянного тока. На каждую горелку работает отдельный питатель пыли.
Вопрос № 89
|
|
История развития хранилищ для нефти: Первые склады нефти появились в XVII веке. Они представляли собой землянные ямы-амбара глубиной 4…5 м...
Археология об основании Рима: Новые раскопки проясняют и такой острый дискуссионный вопрос, как дата самого возникновения Рима...
Кормораздатчик мобильный электрифицированный: схема и процесс работы устройства...
Состав сооружений: решетки и песколовки: Решетки – это первое устройство в схеме очистных сооружений. Они представляют...
© cyberpedia.su 2017-2024 - Не является автором материалов. Исключительное право сохранено за автором текста.
Если вы не хотите, чтобы данный материал был у нас на сайте, перейдите по ссылке: Нарушение авторских прав. Мы поможем в написании вашей работы!