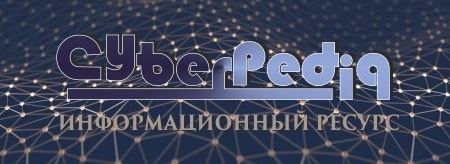
Папиллярные узоры пальцев рук - маркер спортивных способностей: дерматоглифические признаки формируются на 3-5 месяце беременности, не изменяются в течение жизни...
Историки об Елизавете Петровне: Елизавета попала между двумя встречными культурными течениями, воспитывалась среди новых европейских веяний и преданий...
Топ:
Методика измерений сопротивления растеканию тока анодного заземления: Анодный заземлитель (анод) – проводник, погруженный в электролитическую среду (грунт, раствор электролита) и подключенный к положительному...
Генеалогическое древо Султанов Османской империи: Османские правители, вначале, будучи еще бейлербеями Анатолии, женились на дочерях византийских императоров...
Характеристика АТП и сварочно-жестяницкого участка: Транспорт в настоящее время является одной из важнейших отраслей народного...
Интересное:
Как мы говорим и как мы слушаем: общение можно сравнить с огромным зонтиком, под которым скрыто все...
Уполаживание и террасирование склонов: Если глубина оврага более 5 м необходимо устройство берм. Варианты использования оврагов для градостроительных целей...
Что нужно делать при лейкемии: Прежде всего, необходимо выяснить, не страдаете ли вы каким-либо душевным недугом...
Дисциплины:
![]() |
![]() |
5.00
из
|
Заказать работу |
|
|
Введение
Главным средством интенсификации производства любого назначения является парк машин, которым располагает государство. Прогресс в развитии общества предопределяется техническим уровнем применяемых машин. Их создание, т.е. конструирование и изготовление, составляет основу машиностроения. Общепризнано, что именно машиностроение является главной отраслью народного хозяйства, которая определяет возможность развития других отраслей.
Применение машин резко увеличивает производительность труда, повышает качество продукции, делает труд безопасным и привлекательным. Это особенно важно для развивающихся государств, поскольку именно машиностроительное производство способствует резкому повышению благосостояния общества. В конкурентной борьбе отдельных государств и фирм неизменно побеждает тот, кто имеет более совершенные машины.
Производство машин является сложным процессом, в ходе которого из исходного сырья и заготовок изготавливают детали и собирают машины. Для обеспечения производства машин необходимо решить комплекс задач, связанных с технологической подготовкой их производства, и реализовать разработанные технологические процессы в действующих производственных системах-заводах, цехах, участках, обеспечивая при этом требуемое качество изделий на всех этапах технологического процесса в течение всего срока выпуска изделий.
В решении этих сложных и разнообразных вопросов основная роль принадлежит технологам-машиностроителям. Технология машиностроения является комплексной инженерной и научной дисциплиной, синтезирующей технические проблемы изготовления машин заданного качества с решением целого ряда организационных и экономических задач. Эти задачи вытекают из необходимости обеспечить выпуск изделий в определённом производственной программой количестве, в заданные сроки и при наименьшей себестоимости. Так, при освоении нового изделия отрабатывают конструкцию изделия на технологичность, а затем разрабатывают технологический процесс изготовления деталей и сборки изделия. При этом приходится решать и смежные технологические задачи, связанные с выбором и заказом исходных заготовок, термической обработкой заготовок на разных этапах технологического процесса, нанесением покрытий и т.д.
|
Технологический процесс всегда неоднозначен. Много вариантность разработки технологического процесса связано с преодолением существующих трудностей. Каждый разработчик процесса, анализируя многие факторы, приходит в итоге к определённому технологическому решению. Однако нельзя гарантировать, что именно принятое решение является наиболее приемлемым, поскольку задача разработки процесса с самого начала содержала много неизвестных факторов, в ряде случаев использовались гипотезы и предположения частного характера. Поэтому в настоящее время для решения многовариантных задач с успехом применяют ЭВМ. При этом удается не только учесть многие одновременно действующие факторы, но и выработать единое решение за короткое время.
Повышение эффективности современного машиностроительного производства на основе комплексной механизации и автоматизации технологических процессов означает широкое применение гибких производственных систем, робототехнических комплексов и другого основного и вспомогательного технологического оборудования, управляемого от ЭВМ, обеспечивающих автоматизацию механической обработки и сборки изделий.
Цель курсового проекта: систематизация, закрепление и расширение знаний теоретических методов технологии машиностроения.
Задачи курсового проекта:
|
- предложить и обосновать усовершенствование в базовом технологическом процессе;
- произвести требуемые расчеты на измененную операцию.
Ra 2,5 мкм
После проведённых качественной и количественной оценок детали на технологичность, можно сделать вывод, что деталь частично технологична
Как видно из таблицы 4.4, в техпроцессе применяют в основном стандартный покупной режущий инструмент. Отметим, что на токарных операциях применены резцы с напайными пластинами из твердого сплава. Вместе с тем применен и спец.инструмент: хон, шевер. Обработка ведется с применение СОЖ, что позволяет вести ее с высокими скоростями резания и сохранением оптимальных периодов стойкости инструмента.
Таблица 4.5 – Средства технического контроля
№ операции | наименование инструмента (прибора) и эталона | вид инструмента | точность измерения, мм | допуск на измеряемый размер, мм | время на 1-но измерение, мин |
штангенциркуль | станд. | 0,1 | 1,0 | 0,12 | |
нутромер Ø100,5+0,87 | станд. | 0,01 | 0,87 | 0,18 | |
шаблон 9±0,1 | спец. | 0,2 | 0,2 | 0,07 | |
шаблон 13,85+0,25 | спец. | 0,25 | 0,25 | 0,07 | |
пробка Ø99,2+0,23 | спец. | 0,23 | 0,23 | 0,09 | |
нутромер Ø103,6+0,46 | станд. | 0,01 | 0,46 | 0,17 | |
скоба Ø92,5-0,3 | спец. | 0,3 | 0,3 | 0,06 | |
нутромер НИ 100-160 | станд. | 0,01 | 0,035 | 0,17 | |
индикатор ИЧ 0-10 кл.1 | станд.. | 0,01 | 0,035 | - | |
кольцо Ø110 | спец. | - | - | - | |
штангенциркуль | станд. | 0,1 | 0,43 | 0,12 | |
пробка Ø8,43+0,3 | спец. | 0,3 | 0,3 | 0,06 | |
пробка Ø11,5+04,3 | спец. | 0,43 | 0,43 | 0,06 | |
пробка М10-7Н ПР НЕ | станд. | 7Н | 7Н | 0,21 | |
скоба Ø18,5-0,2 | спец. | 0,2 | 0,2 | 0,06 | |
шаблон 42±0,31 | спец. | 0,4 | 0,4 | 0,07 | |
скоба Ø130-1,6 | спец. | 0,029 | 0,029 | 0,15 | |
приспособление контрольное | спец. | 0,01 | 0,06 | 0,06 |
В технологическом процессе применены быстродействующие измерительные инструменты (стандартные и специальные). Точность измерения достаточно высокая, погрешность измерения не превышает 25% допуска на измеряемый размер. Оснащенность измерительными средствами операций обработки хорошая.
Рисунок 6.3.1 – Эскиз операции 0030
Рассмотрим погрешность установки заготовки в трехкулачковом самоцентрирующем патроне.Для любого приспособления в общем виде погрешность установки определяется как сумма трех погрешностей:
Еу=Еб + ЕЗ + ЕПР ,
Еу – отклонение фактически достигнутого положения заготовки при установке от требуемого;
|
Еб – погрешность базирования; Еб=0
ЕЗ – погрешность закрепления; Ез=0
ЕПР – погрешность положения; Епр=0.
В свою очередь Епр сосотит из
Епр = Еп + Ес + Есб + Еи,
Где Еп-погрешность, связанная с направлением режущего инструмента Еп=0
Ес-погрешность установки приспособления на станке, Ес=0, откуда следует что погрешность установки заготовки в трехкулачковом самоцентрирующем патроне = 0.
Рисунок 6.3.3- схема обработки на 1 установе токарной операции 005.
Для данной схемы базирования погрешности базирования для всех выдерживаемых размеров равны нулю:
- для диаметральных размеров – потому что патрон самоцентрирующий;
- для линейных размеров, потому что для одного размера технологическая база совпадает с измерительной, а остальные размеры проставлены до поверхностей, обрабатываемых с одного установа.
Во втором установе (рисунок 7.2.2) в качестве баз используются обработанные в первом установе центрально отверстие (разжимная оправка) и торец ступицы. Так как оправка разжимная, погрешности базирования всех размеров равны нулю по причинам, аналогичным первому установу.
Рисунок 6.3.4- схема обработки на 2 установе токарной операции 005.
На токарной операции 00600 в качестве баз используются необработанные наружная поверхность бодьшего венца и торец венца с его стороны.. Базирование производим в трехкулачковом самоцентрирующем патроне.
Рисунок 6.3.5- схема обработки на токарной операции 00600.
Для данной схемы базирования погрешности базирования для всех выдерживаемых размеров равны нулю.
На токарной операции с ЧПУ 00900 в качестве баз используются необработанные наружная поверхность бодьшего венца и торец венца с его стороны.. Базирование производим в трехкулачковом самоцентрирующем патроне.
Рисунок 6.3.6- схема обработки на токарной операции 00900.
Для данной схемы базирования погрешности базирования для всех выдерживаемых размеров равны нулю
На токарной операции 01000 На станке 1К282 производится токарная обработка на восьми позициях (рисунок 7.2.5).В качестве баз используются обработанные наружная поверхность большего венца и торец венца с его стороны.. Базирование производим в трехкулачковом самоцентрирующем патроне.
|
Рисунок 6.3.7- схема обработки на токарной операции 01000
Для данной схемы базирования погрешности базирования для всех выдерживаемых размеров равны нулю
На зубофрезерной операции 00450 и 04700, зубошевинговальной операции 06000, зубообкатных операциях 0105 и 065, хонинговальной операции 09000 детали базируются по внутреннему отверстию на разжимной оправке с упором в торец, поэтому погрешность базирования равна нулю.
Принятые схемы базирования на операциях обеспечат выполнение всех размеров и технических требований согласно чертежу шестерни.
6.4 Выбор варианта технологического маршрута обработки по критерию минимальной себестоимости обработки
При выборе варианта операции затраты определяются в виде удельных величин на один станко-час работы оборудования [5, с.80].
где Sз – основная и дополнительная зарплата с начислениями, руб/ч;
Sч.з – часовые затраты на эксплуатацию рабочего места, руб/ч;
Ен – нормативный коэффициент экономической эффективности капитальных вложений;
Кс,Кз – удельные часовые капитальные вложения соответственно в станок и здание, руб/ч.
SЗ = ·СТФ·к·у, [5, с.81]
где =2,66 – коэффициент к часовой тарифной ставке, учитывающий оплаты за переработку норм, за работу по технически обоснованным нормам, премию, дополнительную зарплату, льготы и выплаты из фондов общественного потребления (включая отчисления на социальное страхование), [5, с.81];
СТФ – часовая тарифная ставка станочника-сдельщика соответствующего разряда, руб/ч;
к – коэффициент учитывающий зарплату наладчика; для серийного производства к=1, т.к. обычно наладка производится самим рабочим;
y – коэффициент штучного времени, учитывающий оплату труда рабочего при многостаночном обслуживании.
Часовые затраты на эксплуатацию рабочего места:
; [5, c.81]
где – практические часовые затраты на базовом рабочем месте, руб/ч;
Для серийного производства:
; [5, c.81]
Здесь и далее цены, приведенные в литературах [2] и [5], умножаются на коэффициент K=3, позволяющий примерно привести их к современным условиям.
– коэффициент, показывающий, во сколько раз затраты, связанные с работой данного станка, больше, чем аналогичные расходы, связанные с работой базового станка.
Капитальные вложения в станок и здание:
;
;[5, с.84]
где Ц – балансовая стоимость станка, руб.;
– стоимость 1м2 площади цеха, руб.;
=375 руб. [5, с.84].
=4055 ч – эффективный годовой фонд времени оборудования;
=0,8 – коэффициент загрузки станка для серийного производства;
A – производственная площадь, занимаемая станком, с учетом проходов.
А=a·КА; [5, c.84]
где а – площадь станка в плане, м2;
КА – коэффициент, учитывающий дополнительную производственную площадь.
|
В данной работе будем сравнивать операции обработки отверстия действующего и предлагаемого техпроцессов.
Действующий вариант.
Операция 0031. Вертикально-сверлильная.
Выполняется на специальном вертикальном 6-шпиндельномстанке с поворотным столом модели 2С170. Тшт = 3,36 мин.
Предлагаемый вариант.
Операция 0031. Вертикально-сверлильная. Выполняется на станке 2Н125.На операции будет обрабатываться отверстие Ø101,5.Тшт = 0,77 мин
Предложение вызвано тем, что в базовом варианте используeтся вертикально - сверлильный станок модели 2С170, используемый для специальных наладок. На данном станке использован 3-позиционный поворотный стол и 8-шпиндельная коробка. Станок очень производительный, т.к. загрузка-выгрузка детали производится во время обработки. Однако, такой станок дороже простых вертикально - сверлильных станков не менее, чем в 10 раз, имеет значительно большую площадь за счет поворотного стола, более энергоемкий. Станок выполнен специальным, непереналаживаемым, только под заданную деталь. Заданную годовую программу он выполнит за 1-2 недели и остальное время будет простаивать.
В предлагаемом варианте используются менее производительные, но более экономичные по цене, площади и мощности станки, которые могут быть применены для других деталей.
Исходные данные:
Станок – 2С170; Оптовая цена – ЦОПТ = 53700 руб; Тогда Ц=1,1· ЦОПТ =
=1,1·53700 = 59070 руб; Площадь станка а= 2,6х2,1=5,46 м2; и
А= a·КА =5,46х3,0=16,38 м2; Разряд работы станочника – 4; СТФ=2,01 руб/ч;
Расчет:
SЗ = 2,66х2,01х1х 1 =5,35 руб/ч;
= 18,21 руб/ч;
=1,89 руб/ч;
SП.З =5,35+2,73+0,15(18,21+1,89)=11,1 руб/ч
Теперь рассчитаем затраты по предлагаемому варианту обработки. Исходные данные:
1.Станок – 2Н125; Оптовая цена – ЦОПТ = 4260 руб; Тогда Ц=1,1· ЦОПТ =
=1,1·4260 = 4686 руб; Площадь станка а= 1,13х0,805=0,91 м2; и
А= a·КА =0,91х4=3,64 м2; Разряд работы станочника – 3; СТФ =1,82 руб/ч;
Расчет:
SЗ = 2,66х1,82х1х 1 =4,84 руб/ч;
= 1,44 руб/ч;
=0,42 руб/ч;
SП.З =4,84+0,87+0,15(1,44+0,42)= 5,99 руб/ч
Технологическая себестоимость операции механической обработки (руб.) определяется по формуле [5, c.84]:
где – штучно-калькуляционное время на операцию, мин.
= 1,3 – коэффициент выполнения норм.
Действующий вариант
Предлагаемый вариант
Итак, технологическая себестоимость обработки предлагаемого варианта ниже, чем для действующего техпроцесса, поэтому в принятом техпроцессе обработку отверстия будем производить на станке 2Н125.
Таблица 6.4 – Сравнительные данные по параметрам себестоимости 2-х вариантов техпроцесса
Показатели | Действующий вариант | Предлагаемый вариант |
Станок | 2С170 | 2Н125 |
Производственная площадь, занимаемая станком, с учетом проходов, А м2 | 16,38 | 3,64 |
Оптовая цена, ЦОПТ, руб. | ||
Разряд работы станочника | ||
Часовая тарифная ставка станочника-сдельщика соответствующего разряда, СТФ руб/ч; | 2,01 | 1,82 |
Штучно-калькуляционное время на операцию ![]() | 3,36 | 0,77+0,74=1,51 |
Удельные производственные затраты ![]() | 11,1 | 5,99 |
Технологическая себестоимость обработки ![]() | 0,47 | 0,11 |
Итак, технологическая себестоимость обработки предлагаемого варианта ниже, чем для действующего техпроцесса, поэтому в принятом техпроцессе обработку будем производить на станке 2Н125.
Расчет режимов резания
Расчет режимов резания ведется на измененную операцию.
Измененными являются операции 0031.
Операция 0031. Вертикально-сверлильная. Выполняется на станке 2С170
Зенкеровать отверстие Ø101 мм.
Последовательность расчетов выполняем по [6, карта С-1].
Длина рабочего хода
LР.Х = LРЕЗ +y +LДОП,
где LРЕЗ – длина резания, мм;
y – длина подвода, врезания и перебега инструмента, мм;
LДОП - дополнительная длина рабочего хода, вызванная в отдельных случаях особенностями наладки и конфигурации детали, мм.
LРЕЗ = 102 мм
y =2 мм
LДОП =0 мм – особенностей нет.
LР.Х =102+2=104 мм
По [6, карта С-2] находим рекомендуемые значения подачи на оборот:
для сверла Ø101,5 мм - S0 =0,35 мм/об – по 3-й группе подач; [6, с.112]
Стойкость в минутах резания
ТР =ТМ·λ, [6, карта С-2]
где ТМ - стойкость в минутах машинной работы станка;
λ – коэффициент времени резания.
λ= LРЕЗ / LР.Х =102/104=0,9
ТМ =90 мин [6, с.114]
ТР = 90·0,9=81 мин
Скорость резания принимаем по действующему техпроцессу, т.к. обработка многошпиндельная
V=15 м/мин – для зенкера Ø101,5 мм;
Частота вращения шпинделя
n=1000V/πD =1000·15/π·101,5 =47,06мин-1 – для зенкера Ø101,5 мм;
Минутная подача
SМ = S0 ·n=0,35·47,06=16,47мм/мин – для зенкера Ø101,5 мм;
Принимаем для шпинделя станка: S0 =0,35 мм/об; nШП=45 мин-1;
Тогда принятое значение для шпиндельной коробки: SМ =0,35·45=15 мм/мин
Действительные значения подач на оборот для шпинделей:
S0 =15/45=0,33 мм/об - для зенкера Ø101,5 мм;
Основное время обработки
Т0 =LР.Х / SМ =104/15=6,9 мин
Проверочные расчеты
а) определение осевой силы резания в кГ
Р0 =РТАБЛ ·к, [6, с.124]
где РТАБЛ – табличное значение силы, кГ;
к – коэффициент, зависящий от обрабатываемого материала;
РТАБЛ =150 кГ - для зенкера Ø101,5 мм; [6, с.124]
К=1,1 [6, с.125]
Р0=150·1,1=165 кГ=1620 Н - для зенкера Ø101,5 мм;
б) определение мощности резания
NРЕЗ =NТАБЛ ·кN ·n/1000, [6, с.126]
где NТАБЛ - табличное значение мощности, кВт;
кN - коэффициент, зависящий от обрабатываемого материала;
n - частота вращения шпинделя, мин-1.
NТАБЛ =0,7 кВт - для зенкера Ø101,5 мм; [6, с.127]
кN =1,1
N=0,7·1,1·45/1000=0,32 кВт; для зенкера Ø101,5 мм;
в) проверим по допустимым значениям
8320 Н<9000 Н – условие выполняется
Должно выполняться условие
NРЕЗ ≤1,2NДВ ·η,
где NДВ – мощность электродвигателя станка, кВт;
η – КПД станка.
1,2NДВ · η =1,2·2,2·0,8=2,11 кВт; 1,46<2,11 кВт
Значения Р0 и NРЕЗ меньше допустимых, следовательно, обработка на данном станке 2Н125 при принятых режимах резания возможна.
Режимы резания на остальные операции рассчитываем аналогично, результаты расчетов заносим в таблицу 7.2.1.
Операция, позиция, переход | t, мм | Lрез/Lр.х. мм | λ | Тм/Тр, мин | So, об/мин | V ,м/мин | n, мин-1 | Sм, мм/мин | То, мин | ||
003.Токарная | 0,24 | 2,5 | |||||||||
0031. Вертикально-сверлильная | 0,35 | 2,5 | |||||||||
005.Токарная | |||||||||||
Установ А | Позиция I Загрузочная | ||||||||||
Позиция III 1.Подрезать торец. 2. Точить поверхность Ø149 | 24/34 25/35 | 0,84 0,75 | 0,35 0,35 | 27,7 21,7 | 21,31 16,45 | 1,1 | |||||
Позиция V 1. Подрезать торец.. 2.Точить поверхность Ø138 | 30/40 72/82 | 0,75 0,87 | 0,35 0,35 | 21,7 17,86 | 17,57 17,57 | ||||||
Позиция VII 5. Подрезать торец 6. Точить поверхность Ø130 и фаску Ø113 | 1,5 1,5 | 96/106 | 0,9 0,75 | 0,35 0,32 | 11,4 11,4 | ||||||
Установ Б | Позиция II 1.Точить поверхность Ø167 2.Точить поверхность Ø115 3. Расточить отв. Ø106,5 | 1,5 | 45/55 2/6 96/106 | 0,8 0,3 0,9 | 0,35 0,35 0,35 | 17,57 | |||||
Позиция IV 2.Точить поверхность Ø163,8 3. Расточить отв. Ø108,7 | 1,5 | 20/30 96/106 | 0,6 0,9 | 0,35 0,35 | 57,3 57,3 | 17,57 | |||||
Позиция VI 1. Расточить отв.Ø106,5 | 96/106 | 0,75 | 0,35 | 19,95 | |||||||
Позиция VIII 1. Расточить фаску отв.Ø114 | 2/6 | 0,3 | 0,35 | 19,95 | |||||||
009. Токарная с ЧПУ | |||||||||||
1.Подрезать торец Ø292,5 | 2,7 | 15/20 | 0,75 | 0,6 | 0,28 | ||||||
2.Точить поверхность Ø114за 2 прохода и фаску | 15,3/20 | 0,76 | 0,6 | 0,33·2 | |||||||
4. Точить поверхностØ109 | 26/30 | 0,87 | 0,6 | 0,42 | |||||||
5.Подрезать выточку Ø138 | 0,5 | 6,5/8 | 0,81 | 0,6 | 0,05 | ||||||
010 Токарная | |||||||||||||||||||||||||||||||||||||||||||||||||||||||||||||||||||||||||||||||||||||||||||||||||||||||
Установ А | Позиция I Загрузочная | ||||||||||||||||||||||||||||||||||||||||||||||||||||||||||||||||||||||||||||||||||||||||||||||||||||||
Позиция III 1.Подрезать торец. 2. Точить поверхность Ø149 | 24/34 25/35 | 0,84 0,75 | 0,35 0,35 | 27,7 21,7 | 21,31 16,45 | ||||||||||||||||||||||||||||||||||||||||||||||||||||||||||||||||||||||||||||||||||||||||||||||||||
Позиция V 1. Подрезать торец.. 2.Точить поверхность Ø138 | 30/40 72/82 | 0,75 0,87 | 0,35 0,35 | 21,7 17,86 | 17,57 17,57 | ||||||||||||||||||||||||||||||||||||||||||||||||||||||||||||||||||||||||||||||||||||||||||||||||||
Позиция VII 1. Точить поверхность Ø140 и фаску | 1,5 | 96/106 | 0,9 | 0,35 | 11,4 | ||||||||||||||||||||||||||||||||||||||||||||||||||||||||||||||||||||||||||||||||||||||||||||||||||
Установ Б | Позиция II 1.Точить поверхность Ø167 2.Точить поверхность Ø115 3. Расточить отв. Ø106,5 | 1,5 | 45/55 2/6 96/106 | 0,8 0,3 0,9 | 0,35 0,35 0,35 | 17,57 | |||||||||||||||||||||||||||||||||||||||||||||||||||||||||||||||||||||||||||||||||||||||||||||||||
Позиция IV 2.Точить поверхность Ø163,8 3. Расточить отв. Ø108,7 | 1,5 | 20/30 96/106 | 0,6 0,9 | 0,35 0,35 | 57,3 57,3 | 17,57 | |||||||||||||||||||||||||||||||||||||||||||||||||||||||||||||||||||||||||||||||||||||||||||||||||
Позиция VI 1. Расточить отв.Ø106,5 | 96/106 | 0,75 | 0,35 | 19,95 | |||||||||||||||||||||||||||||||||||||||||||||||||||||||||||||||||||||||||||||||||||||||||||||||||||
Позиция VIII 1. Расточить фаску отв.Ø114 | 2/6 | 0,3 | 0,35 | 19,95 | |||||||||||||||||||||||||||||||||||||||||||||||||||||||||||||||||||||||||||||||||||||||||||||||||||
011. Токарная с ЧПУ. | |||||||||||||||||||||||||||||||||||||||||||||||||||||||||||||||||||||||||||||||||||||||||||||||||||||||
|
Операция 047. Зубофрезерная. | |||||||||||
|
Заключение
В данном курсовом проекте был разработан техпроцесс изготовления детали «Шестерня» 70-1701041, входящей в состав редуктора трактора МТЗ-80, выпускаемого Минским тракторным заводом.
При выполнении работы в первую очередь были тщательно изучены чертеж детали, условия работы шестерни в узле, нагрузки, которые воспринимают поверхности детали, проверена правильность выбора материала детали, выполнен анализ технологичности конструкции детали, проанализирован действующий техпроцесс обработки.
При выборе оптимального метода получения заготовки рассматривался действующий метод Поковка КГШП, открыт штамп и предлагаемый
(альтернативный) – поковка КГШП закрытый штамп. Благодаря более низкой себестоимости и более высокому коэффициенту использования материала предпочтение отдано КГШП закрытый штамп.
В результате анализа действующего техпроцесса вместо операции 031, выполняемой на станке 2С170, было введено:
- 031. Вертикально – сверлильная. Выполняется на станке 2Н125. На операции будет обрабатываться отверстие Ø101,5.
В базовом варианте используeтся вертикально - сверлильный станок модели 2С170, используемый для специальных наладок. На данном станке использован 3-позиционный поворотный стол и 8-шпиндельная коробка. Станок очень производительный, т.к. загрузка-выгрузка детали производится во время обработки, и одновременно производится сверление 6-ти отверстий и нарезание резьбы в 2-х отверстиях. Однако, такой станок дороже простых вертикально - сверлильных станков не менее, чем в 10 раз, имеет значительно большую площадь за счет поворотного стола, более энергоемкий. Станок выполнен специальным, непереналаживаемым, только под заданную деталь. Заданную годовую программу он выполнит за 1-2 недели и остальное время будет простаивать.
В предлагаемом варианте используются менее производительные, но более экономичные по цене, площади и мощности станки, которые могут быть применены для других деталей. Расчет по минимуму приведенных затрат показал выгодность предложения.
На измененные операции были рассчитаны режимы резания, произведено нормирование, определено количество оборудования.
Введение
Главным средством интенсификации производства любого назначения является парк машин, которым располагает государство. Прогресс в развитии общества предопределяется техническим уровнем применяемых машин. Их создание, т.е. конструирование и изготовление, составляет основу машиностроения. Общепризнано, что именно машиностроение является главной отраслью народного хозяйства, которая определяет возможность развития других отраслей.
Применение машин резко увеличивает производительность труда, повышает качество продукции, делает труд безопасным и привлекательным. Это особенно важно для развивающихся государств, поскольку именно машиностроительное производство способствует резкому повышению благосостояния общества. В конкурентной борьбе отдельных государств и фирм неизменно побеждает тот, кто имеет более совершенные машины.
Производство машин является сложным процессом, в ходе которого из исходного сырья и заготовок изготавливают детали и собирают машины. Для обеспечения производства машин необходимо решить комплекс задач, связанных с технологической подготовкой их производства, и реализовать разработанные технологические процессы в действующих производственных системах-заводах, цехах, участках, обеспечивая при этом требуемое качество изделий на всех этапах технологического процесса в течение всего срока выпуска изделий.
В решении этих сложных и разнообразных вопросов основная роль принадлежит технологам-машиностроителям. Технология машиностроения является комплексной инженерной и научной дисциплиной, синтезирующей технические проблемы изготовления машин заданного качества с решением целого ряда организационных и экономических задач. Эти задачи вытекают из необходимости обеспечить выпуск изделий в определённом производственной программой количестве, в заданные сроки и при наименьшей себестоимости. Так, при освоении нового изделия отрабатывают конструкцию изделия на технологичность, а затем разрабатывают технологический процесс изготовления деталей и сборки изделия. При этом приходится решать и смежные технологические задачи, связанные с выбором и заказом исходных заготовок, термической обработкой заготовок на разных этапах технологического процесса, нанесением покрытий и т.д.
Технологический процесс всегда неоднозначен. Много вариантность разработки технологического процесса связано с преодолением существующих трудностей. Каждый разработчик процесса, анализируя многие факторы, приходит в итоге к определённому технологическому решению. Однако нельзя гарантировать, что именно принятое решение является наиболее приемлемым, поскольку задача разработки процесса с самого начала содержала много неизвестных факторов, в ряде случаев использовались гипотезы и предположения частного характера. Поэтому в настоящее время для решения многовариантных задач с успехом применяют ЭВМ. При этом удается не только учесть многие одновременно действующие факторы, но и выработать единое решение за короткое время.
Повышение эффективности современного машиностроительного производства на основе комплексной механизации и автоматизации технологических процессов означает широкое применение гибких производственных систем, робототехнических комплексов и другого основного и вспомогательного технологического оборудования, управляемого от ЭВМ, обеспечивающих автоматизацию механической обработки и сборки изделий.
Цель курсового проекта: систематизация, закрепление и расширение знаний теоретических методов технологии машиностроения.
Задачи курсового проекта:
- предложить и обосновать усовершенствование в базовом технологическом процессе;
- произвести требуемые расчеты на измененную операцию.
Описание объекта производства
Объектом производства для заданной детали является трактор «Беларусь» МТЗ-80, см. рисунок 1
![]() |
Рисунок 1-Трактор МТЗ-80
Трактор МТЗ-80 - колесный, универсально-пропашной, тягового класса 1.4. Трактор МТЗ-80 предназначен для проведения сельскохозяйственных и транспортных работ с применением различных навесных и прицепных агрегатов. Навесная гидравлическая система трактора МТЗ-80 - универсальная, раздельно-агрегатная, с силовым и позиционным
регулированием глубины обработки, с механической фиксацией навесного устройства в транспортном положении.
Трактор «Беларусь» МТЗ-80 - универсально – пропашной колёсный трактор, выпускаемый Минским тракторным заводом с 1974 года по настоящее время (в 2000-х годах—под маркой «Беларус-80»). Трактор МТЗ-80 является глубокой модернизацией выпускавшихся ранее тракторов МТЗ-50. Степень унификации деталей и сборочных единиц у этих тракторов достигает 70%. Трактор выполнен по традиционной для своего семейства компоновке: полурамная конструкция с несущими картерами узлов трансмиссии, переднее расположение двигателя, задние ведущие колёса увеличенного диаметра, передние направляющие колёса уменьшенного диаметра. Трактор МТЗ-80 имеет привод только на задние колёса.
На тракторе установлен четырехтактный дизельный двигатель Д-240 (Д-243) жидкостного охлаждения с непосредственным впрыском топлива, запуском от электростартера. Двигатель Д-240Л, установленный на тракторе МТЗ-80Л, запускают от пускового двигателя с блокирующим приспособлением, исключающим пуск двигателя при включенной передаче. Трактор оборудован силовым и позиционным регулированием гидравлической навесной системы, автоматической блокировкой дифференциала заднего моста, двухскоростным ВОМ. дополнительным редуктором КП, ходоуменшителем и пневматическими приводами тормозов прицепов.
Муфта сцепления фрикционная, однодисковая, сухая, постоянно замкнутая.
Коробка передач механическая с девятью передачами вперед и двумя - назад. Понижающий редуктор КП, представляющий собой две пары цилиндрических прямозубых шестерен, удваивает число передач.
Главная передача состоит из пары конических шестерен со спиральными зубьями.
Силовой (позиционный) регулятор установлен на кронштейне заднего гидроцилиндра и соединен маслопроводами с распределителем и гидроувеличителем сцепного веса (ГСВ). Наличие такого регулятора в гидросистеме в сочетании с ГСВ способствует повышению производительности тракторного агрегата
|
|
История развития пистолетов-пулеметов: Предпосылкой для возникновения пистолетов-пулеметов послужила давняя тенденция тяготения винтовок...
Опора деревянной одностоечной и способы укрепление угловых опор: Опоры ВЛ - конструкции, предназначенные для поддерживания проводов на необходимой высоте над землей, водой...
Организация стока поверхностных вод: Наибольшее количество влаги на земном шаре испаряется с поверхности морей и океанов (88‰)...
Автоматическое растормаживание колес: Тормозные устройства колес предназначены для уменьшения длины пробега и улучшения маневрирования ВС при...
© cyberpedia.su 2017-2024 - Не является автором материалов. Исключительное право сохранено за автором текста.
Если вы не хотите, чтобы данный материал был у нас на сайте, перейдите по ссылке: Нарушение авторских прав. Мы поможем в написании вашей работы!