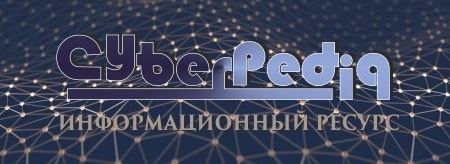
Таксономические единицы (категории) растений: Каждая система классификации состоит из определённых соподчиненных друг другу...
Поперечные профили набережных и береговой полосы: На городских территориях берегоукрепление проектируют с учетом технических и экономических требований, но особое значение придают эстетическим...
Топ:
Особенности труда и отдыха в условиях низких температур: К работам при низких температурах на открытом воздухе и в не отапливаемых помещениях допускаются лица не моложе 18 лет, прошедшие...
Характеристика АТП и сварочно-жестяницкого участка: Транспорт в настоящее время является одной из важнейших отраслей народного хозяйства...
Проблема типологии научных революций: Глобальные научные революции и типы научной рациональности...
Интересное:
Мероприятия для защиты от морозного пучения грунтов: Инженерная защита от морозного (криогенного) пучения грунтов необходима для легких малоэтажных зданий и других сооружений...
Средства для ингаляционного наркоза: Наркоз наступает в результате вдыхания (ингаляции) средств, которое осуществляют или с помощью маски...
Уполаживание и террасирование склонов: Если глубина оврага более 5 м необходимо устройство берм. Варианты использования оврагов для градостроительных целей...
Дисциплины:
![]() |
![]() |
5.00
из
|
Заказать работу |
|
|
На самую точную поверхность - отв.Ø110-0,0025-0,010 припуск определим расчетно-аналитическим методом. Эскиз детали покажем на рисунке 7.2
Рисунок 7.1 – шестерня
Расчет припусков выполняем в порядке, изложенном в [1, табл.4.1] и в соответствии с примером 4.1, приведенном в [1, с. 83…87]. Результаты промежуточных расчетов сводим в табл. 7.4.1.
1. Пользуясь рабочим чертежом детали и картой технологического процесса механической обработки, запишем в табл. 7.4.1 технологические переходы обработки в порядке последовательности их выполнения от черновой заготовки до окончательной обработки.
2. Запишем значения , Т, ρ, Е и δ,
где: – высота неровностей профиля, мкм; находим по таблицам 4.3, 4.5, 4.6;
Т – глубина дефектного поверхностного слоя, мкм; находим по таблицам 4.3, 4.5, 4.6;
ρ – суммарное пространственное отклонение поверхности, мкм.
Для штампованных заготовок типа дисков с прошиваемым центральным отверстием с установкой по наружному диаметру и торцу:
ρ = , [1, с. 67]
где: – погрешность от смещения частей штампа;
– погрешность от эксцентричности прошиваемого центрального отверстия по отношению к наружному контуру заготовки.
В соответствии с [2]
=500 мкм;
= 1000 мкм;
ρ = = 1118 мкм
Вследствие копирования погрешностей при обработке находим их значение для переходов механической обработки по формуле:
=
·
, [1, с. 73]
где – коэффициент уточнения формы;
для зенкерования = 0,06:
ρ = 1118·0,06 = 67 мкм
Для расточки черновой = 0,05:
ρ = 67· 0,05 ≈ 3 мкм.
Для расточки чистовой = 0,002:
ρ = 3· 0,002 ≈ 0,006 мкм
Погрешность установки определяется по формуле:
=
, [1, с. 73]
где: – погрешность базирования;
– погрешность закрепления;
– погрешность заготовки в приспособлении.
|
Для всех переходов = 0, т.к. базирование производится в самоцентрирующем патроне.
= 600 мкм – при установке штамповки в 3- кулачковом патроне. [1, табл. 4.10]
= 50 мкм – для токарной операции [1, с.74]
= 0 - для однопозиционной обработки [1, с.74]
Для зенкерования
=
= 602 мкм
= 0 – при хонинговании.
Учитываем копирование погрешности:
- для расточки черновой = 602·0,06=36 мкм;
- для расточки чистовой = 36·0,06=2,16 мкм;
Таблица.7.1- Расчет припусков и предельных размеров по технологическим переходам на обработку поверхности Ø110-0,025-0,010
Технолог. Переходы Для обработки отверстия Ø110-0,025-0,010 | Элем. припуска, мкм. | Расчетный припуск 2Zmin,мкм. | Расчетный размер dр, мм | Допуск δ, мкм. | Предельный Размер, мм. | Пред.знач припусков мкм. | |||||
Rz | Т | ρ | Е | dmin | dmax | ![]() | ![]() | ||||
Заготовка | 106,254 | 104,6 | 106,2 | ||||||||
Зенкерование | 2·1619 | 109,492 | 108,872 | 109,492 | |||||||
Растачивания черновое | 2·176 | 109,844 | 109,684 | 109,844 | |||||||
Растачивания чистовое | 0,006 | 2,16 | 2·63 | 109,970 | 109,935 | 109,970 | |||||
Хонингование | - | - | - | 2·10 | 109,99 | 109,965 | 109,990 | ||||
Итого: |
3. Расчетные минимальные припуски определяются по формуле: =2(
), [1, табл. 4.2]
где: индекс (і-1) указывает на предшествующий переход.
Для зенкерования:
=2·(150+200+
)=2·1619 мкм.
Для растачивания чернового:
=2(50+50+
)= 2·176 мкм.
Для растачивания чистового:
=2(30+30+
)=2·63 мкм.
Для хонингования:
=2(4+6+
)=2·10 мкм.
4. В графу «Расчетный размер» запишем для конечного перехода наибольший предельный размер детали по чертежу:109,99мм.
5. Для перехода, предшествующего конечному, находим расчетный размер
вычитанием из наибольшего предшествующего размера по чертежу расчетного припуска :
dр.растт чист= 109,990-2· 0,010 = 109,970мм;
6. Аналогично находим остальные расчетные размеры.
dр.растт черн= 109,97-2·0,0 63 = 109,844мм;
dр зенк =109,844-2·0.176=109,492 мм
dр заг =109,492-2·1,619=106,254 мм
7. Запишем наибольшие предельные размеры по всем переходам, округляя их уменьшением расчетных размеров; округление производим до того знака десятичной дроби, с каким дан допуск на размер для каждого перехода.
|
8. Определим наименьшие предельные размеры путем вычитания допуска из округленного наибольшего предшествующего размера.
7. Определим наименьшие предельные размеры вычитанием допуска из округленного наибольшего предельного размера.
dр заг =106,2-1,6=104,6 мм
dр зенк =109,64-0,620=108,872 мм
dр.растт черн = 109,97-0,070 = 109,935мм;
dр.растт чист = 109,99 – 0,025 =109,965мм
9. Запишем предельные значения припусков , как разность наименьших предельных размеров и
, как разность наибольших предельных размеров выполняемого и предшествующего переходов:
2 = dmax I - dmax i-1 и 2
= dmin i-dmin i-1
Для зенкерования:
2 = 108,872 - 104,6 = 4,272мм; 2
=109,492 -106,2 =3,292мм;
Для растачивания чернового:
2 = 109,684-108,87=0,814мм; 2
=109,844-109,49=0,354мм;
Для растачивания чистового:
2 = 109,935- 109,684 = 0,251мм; 2
= 109,970 – 109,844 = 0,126 мм;
Для хонингования
2 = 109,965 – 109,935= 0,030 мм;; 2
=109,99 -109,97 = 0,020 мм
9. Общие припуски:
2 =∑2
= 4270+814+251+30 = 5365мкм
=∑
= 3292+354+126+20 = 3792мкм
10. Проверяем правильность произведенных расчетов по формулам:
= δD-i- δDi
= δD3- δDд
Для зенкерования:
4272-3292=980мм; 1600-620=980 мм; 980=980
Для растачивания чернового:
814-354 = 460мм; 620-160 = 460 460=460
Для растачивания чистового:
251-126=125мм; 160-35=125 мм; 125=125
Для хонингования:
30-20=10 мм; 35-25=10 мм; 10=10
Равенства соблюдены, следовательно, расчеты были выполнены верно.
12. Общий номинальный припуск:
=
+
-
,
где и
– верхние отклонения размеров заготовки и детали;
= 3292 + 500-25 = 3767 мм.
13. Номинальный размер заготовки:
=
-
= 110 – 3,767 = 106,233 мм.
14. Схему графического расположения припусков и допусков покажем на рисунке 7.4.2.
Рисунок 7.1.2– Схема графического расположения припусков и допусков на обработку отверстия Ø110-0,025-0,010мм.
15. На остальные обрабатываемые поверхности припуски и допуски выбираются по ГОСТ7505-85. Все данные по припускам и допускам шестерни заносим в таблицу 7.4.2.
Таблица 7.1.2 - Припуски и допуски на обрабатываемые поверхности шестерни (по ГОСТ 7505-85, размеры в мм)
Поверхность | Размер | Припуск | Допуск | |
табличный | расчетный | |||
Ø163,8 | 2·1,75 | — | +1,6 -0,8 | |
2,3 | 92,5 | 2,5 | — | +1,1 -0,5 |
Ø110 | 2·1,6 | 2·2,1 | +0,5 -1,0 |
Расчет режимов резания
Расчет режимов резания ведется на измененную операцию.
|
Измененными являются операции 0031.
Операция 0031. Вертикально-сверлильная. Выполняется на станке 2С170
Зенкеровать отверстие Ø101 мм.
Последовательность расчетов выполняем по [6, карта С-1].
Длина рабочего хода
LР.Х = LРЕЗ +y +LДОП,
где LРЕЗ – длина резания, мм;
y – длина подвода, врезания и перебега инструмента, мм;
LДОП - дополнительная длина рабочего хода, вызванная в отдельных случаях особенностями наладки и конфигурации детали, мм.
LРЕЗ = 102 мм
y =2 мм
LДОП =0 мм – особенностей нет.
LР.Х =102+2=104 мм
По [6, карта С-2] находим рекомендуемые значения подачи на оборот:
для сверла Ø101,5 мм - S0 =0,35 мм/об – по 3-й группе подач; [6, с.112]
Стойкость в минутах резания
ТР =ТМ·λ, [6, карта С-2]
где ТМ - стойкость в минутах машинной работы станка;
λ – коэффициент времени резания.
λ= LРЕЗ / LР.Х =102/104=0,9
ТМ =90 мин [6, с.114]
ТР = 90·0,9=81 мин
Скорость резания принимаем по действующему техпроцессу, т.к. обработка многошпиндельная
V=15 м/мин – для зенкера Ø101,5 мм;
Частота вращения шпинделя
n=1000V/πD =1000·15/π·101,5 =47,06мин-1 – для зенкера Ø101,5 мм;
Минутная подача
SМ = S0 ·n=0,35·47,06=16,47мм/мин – для зенкера Ø101,5 мм;
Принимаем для шпинделя станка: S0 =0,35 мм/об; nШП=45 мин-1;
Тогда принятое значение для шпиндельной коробки: SМ =0,35·45=15 мм/мин
Действительные значения подач на оборот для шпинделей:
S0 =15/45=0,33 мм/об - для зенкера Ø101,5 мм;
Основное время обработки
Т0 =LР.Х / SМ =104/15=6,9 мин
Проверочные расчеты
а) определение осевой силы резания в кГ
Р0 =РТАБЛ ·к, [6, с.124]
где РТАБЛ – табличное значение силы, кГ;
к – коэффициент, зависящий от обрабатываемого материала;
РТАБЛ =150 кГ - для зенкера Ø101,5 мм; [6, с.124]
К=1,1 [6, с.125]
Р0=150·1,1=165 кГ=1620 Н - для зенкера Ø101,5 мм;
б) определение мощности резания
NРЕЗ =NТАБЛ ·кN ·n/1000, [6, с.126]
где NТАБЛ - табличное значение мощности, кВт;
кN - коэффициент, зависящий от обрабатываемого материала;
n - частота вращения шпинделя, мин-1.
NТАБЛ =0,7 кВт - для зенкера Ø101,5 мм; [6, с.127]
кN =1,1
N=0,7·1,1·45/1000=0,32 кВт; для зенкера Ø101,5 мм;
в) проверим по допустимым значениям
8320 Н<9000 Н – условие выполняется
Должно выполняться условие
NРЕЗ ≤1,2NДВ ·η,
где NДВ – мощность электродвигателя станка, кВт;
|
η – КПД станка.
1,2NДВ · η =1,2·2,2·0,8=2,11 кВт; 1,46<2,11 кВт
Значения Р0 и NРЕЗ меньше допустимых, следовательно, обработка на данном станке 2Н125 при принятых режимах резания возможна.
Режимы резания на остальные операции рассчитываем аналогично, результаты расчетов заносим в таблицу 7.2.1.
Операция, позиция, переход | t, мм | Lрез/Lр.х. мм | λ | Тм/Тр, мин | So, об/мин | V ,м/мин | n, мин-1 | Sм, мм/мин | То, мин | ||
003.Токарная | 0,24 | 2,5 | |||||||||
0031. Вертикально-сверлильная | 0,35 | 2,5 | |||||||||
005.Токарная | |||||||||||
Установ А | Позиция I Загрузочная | ||||||||||
Позиция III 1.Подрезать торец. 2. Точить поверхность Ø149 | 24/34 25/35 | 0,84 0,75 | 0,35 0,35 | 27,7 21,7 | 21,31 16,45 | 1,1 | |||||
Позиция V 1. Подрезать торец.. 2.Точить поверхность Ø138 | 30/40 72/82 | 0,75 0,87 | 0,35 0,35 | 21,7 17,86 | 17,57 17,57 | ||||||
Позиция VII 5. Подрезать торец 6. Точить поверхность Ø130 и фаску Ø113 | 1,5 1,5 | 96/106 | 0,9 0,75 | 0,35 0,32 | 11,4 11,4 | ||||||
Установ Б | Позиция II 1.Точить поверхность Ø167 2.Точить поверхность Ø115 3. Расточить отв. Ø106,5 | 1,5 | 45/55 2/6 96/106 | 0,8 0,3 0,9 | 0,35 0,35 0,35 | 17,57 | |||||
Позиция IV 2.Точить поверхность Ø163,8 3. Расточить отв. Ø108,7 | 1,5 | 20/30 96/106 | 0,6 0,9 | 0,35 0,35 | 57,3 57,3 | 17,57 | |||||
Позиция VI 1. Расточить отв.Ø106,5 | 96/106 | 0,75 | 0,35 | 19,95 | |||||||
Позиция VIII 1. Расточить фаску отв.Ø114 | 2/6 | 0,3 | 0,35 | 19,95 | |||||||
009. Токарная с ЧПУ | |||||||||||
1.Подрезать торец Ø292,5 | 2,7 | 15/20 | 0,75 | 0,6 | 0,28 | ||||||
2.Точить поверхность Ø114за 2 прохода и фаску | 15,3/20 | 0,76 | 0,6 | 0,33·2 | |||||||
4. Точить поверхностØ109 | 26/30 | 0,87 | 0,6 | 0,42 | |||||||
5.Подрезать выточку Ø138 | 0,5 | 6,5/8 | 0,81 | 0,6 | 0,05 | ||||||
010 Токарная | ||||||||||||||||||||||||||||||||||||||||||||||||||||||||||||||||||||||||||||||||||||||||||||||||||||||||
Установ А | Позиция I Загрузочная | |||||||||||||||||||||||||||||||||||||||||||||||||||||||||||||||||||||||||||||||||||||||||||||||||||||||
Позиция III 1.Подрезать торец. 2. Точить поверхность Ø149 | 24/34 25/35 | 0,84 0,75 | 0,35 0,35 | 27,7 21,7 | 21,31 16,45 | |||||||||||||||||||||||||||||||||||||||||||||||||||||||||||||||||||||||||||||||||||||||||||||||||||
Позиция V 1. Подрезать торец.. 2.Точить поверхность Ø138 | 30/40 72/82 | 0,75 0,87 | 0,35 0,35 | 21,7 17,86 | 17,57 17,57 | |||||||||||||||||||||||||||||||||||||||||||||||||||||||||||||||||||||||||||||||||||||||||||||||||||
Позиция VII 1. Точить поверхность Ø140 и фаску | 1,5 | 96/106 | 0,9 | 0,35 | 11,4 | |||||||||||||||||||||||||||||||||||||||||||||||||||||||||||||||||||||||||||||||||||||||||||||||||||
Установ Б | Позиция II 1.Точить поверхность Ø167 2.Точить поверхность Ø115 3. Расточить отв. Ø106,5 | 1,5 | 45/55 2/6 96/106 | 0,8 0,3 0,9 | 0,35 0,35 0,35 | 17,57 | ||||||||||||||||||||||||||||||||||||||||||||||||||||||||||||||||||||||||||||||||||||||||||||||||||
Позиция IV 2.Точить поверхность Ø163,8 3. Расточить отв. Ø108,7 | 1,5 | 20/30 96/106 | 0,6 0,9 | 0,35 0,35 | 57,3 57,3 | 17,57 | ||||||||||||||||||||||||||||||||||||||||||||||||||||||||||||||||||||||||||||||||||||||||||||||||||
Позиция VI 1. Расточить отв.Ø106,5 | 96/106 | 0,75 | 0,35 | 19,95 | ||||||||||||||||||||||||||||||||||||||||||||||||||||||||||||||||||||||||||||||||||||||||||||||||||||
Позиция VIII 1. Расточить фаску отв.Ø114 | 2/6 | 0,3 | 0,35 | 19,95 | ||||||||||||||||||||||||||||||||||||||||||||||||||||||||||||||||||||||||||||||||||||||||||||||||||||
011. Токарная с ЧПУ. | ||||||||||||||||||||||||||||||||||||||||||||||||||||||||||||||||||||||||||||||||||||||||||||||||||||||||
|
Операция 047. Зубофрезерная. | |||||||||||
|
|
|
Историки об Елизавете Петровне: Елизавета попала между двумя встречными культурными течениями, воспитывалась среди новых европейских веяний и преданий...
Автоматическое растормаживание колес: Тормозные устройства колес предназначены для уменьшения длины пробега и улучшения маневрирования ВС при...
История развития пистолетов-пулеметов: Предпосылкой для возникновения пистолетов-пулеметов послужила давняя тенденция тяготения винтовок...
Типы оградительных сооружений в морском порту: По расположению оградительных сооружений в плане различают волноломы, обе оконечности...
© cyberpedia.su 2017-2024 - Не является автором материалов. Исключительное право сохранено за автором текста.
Если вы не хотите, чтобы данный материал был у нас на сайте, перейдите по ссылке: Нарушение авторских прав. Мы поможем в написании вашей работы!