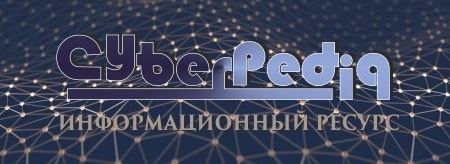
Автоматическое растормаживание колес: Тормозные устройства колес предназначены для уменьшения длины пробега и улучшения маневрирования ВС при...
Архитектура электронного правительства: Единая архитектура – это методологический подход при создании системы управления государства, который строится...
Топ:
Определение места расположения распределительного центра: Фирма реализует продукцию на рынках сбыта и имеет постоянных поставщиков в разных регионах. Увеличение объема продаж...
Оценка эффективности инструментов коммуникационной политики: Внешние коммуникации - обмен информацией между организацией и её внешней средой...
Интересное:
Что нужно делать при лейкемии: Прежде всего, необходимо выяснить, не страдаете ли вы каким-либо душевным недугом...
Отражение на счетах бухгалтерского учета процесса приобретения: Процесс заготовления представляет систему экономических событий, включающих приобретение организацией у поставщиков сырья...
Берегоукрепление оползневых склонов: На прибрежных склонах основной причиной развития оползневых процессов является подмыв водами рек естественных склонов...
Дисциплины:
![]() |
![]() |
5.00
из
|
Заказать работу |
Содержание книги
Поиск на нашем сайте
|
|
ВВЕДЕНИЕ
Путевое хозяйство является одной из основных отраслей железнодорожного транспорта. Около 40% затрат приходится на ремонт основных средств путевого хозяйства, составляющих 58% основных фондов железных дорог.
Основные задачи транспорта – своевременное и качественное, а так же полное удовлетворение потребностей народного хозяйства и населения в перевозках, повышение экономической эффективности его работы.
Для решения указанных задач необходимо обеспечить согласованное развитие единой транспортной системы страны, ее взаимодействие с другими отраслями промышленности, устранять нерациональные перевозки, сокращать сроки доставки грузов и обеспечить их сохранность, ускорить создание и внедрение новой технологии, укрепить материально-техническую и ремонтные базы, значительно поднять уровень комплексной механизации.
Важная роль в путевом хозяйстве отводится путевым машинным станциям (ПМС) в повышении уровня механизации, автоматизации и качества работ по строительству и ремонту железнодорожного пути, от качества выполнения которого зависит благополучная эксплуатация, техническое обслуживание железнодорожного пути.
Принципиальная основа отечественных технологических средств – это обеспечение наивысшей технически возможной производительности с целью уменьшения помех движения поездов.
Действовавшее в путевом хозяйстве Положение о проведении планово-предупредительных ремонтов верхнего строения пути, земляного полотна и искусственных сооружений не позволяло гибко реагировать на эксплуатационные условия работы сети и экономическую ситуацию.
Средства, затрачиваемые на ремонт и содержание пути, не дают должной отдачи из-за отсутствия современных путевых машин, обеспечивающих длительное стабильное положение пути.
|
Недостаточное развитие на дорогах базы материалов верхнего строения пути приводит к крайне ограниченному использованию возможностей их повторного применения и продления сроков службы.
Немалая часть видов деятельности, осуществляемая в системе железнодорожного транспорта, является монопольной. Причем по причинам технологического характера этот монополизм в ближайший период не может быть преодолен традиционными и рыночными методами. Поэтому необходимо выделить производственно-технологический сектор естественной монополии, который нуждается в особом режиме функционирования и управления при прямом регулировании со стороны государства.
К монопольному производственно-технологическому сектору на железнодорожном транспорте, прежде всего, относится вся его инфраструктура, т.е. железнодорожные пути и путевое хозяйство, системы и устройства электроснабжения, сигнализации и связи, станций, локомотивное хозяйство, пункты технического обслуживания подвижного состава в пути следования, депо, а также технические и информационные системы, обеспечивающие управление движением поездов. Сюда же относят все услуги и формирование заказов на пользование инфраструктурой железнодорожного транспорта. Область конкурентного сектора на железнодорожном транспорте - это доставка грузов и пассажиров, а также весь комплекс транспортно-экспедиционных услуг.
Концепцией предусматривается реформирование структуры железнодорожного транспорта на базе разграничения монопольного и конкурентного секторов с перспективой, по возможности, отказа от естественно-монопольных и конкурентных видов деятельности одними и теми хозяйствующими субъектами. Основу структуры федерального железнодорожного транспорта будут составлять железные дороги государственные унитарные предприятия, предоставляющие услуги по пользованию инфраструктурой железнодорожного транспорта, а также по перевозке грузов.
|
Железнодорожный транспорт в Российской Федерации имеет исключительно важное значение в жизнеобеспечении многоотраслевой экономики и реализации социально значимых услуг по перевозке пассажиров.
За последние годы значительно сократился уровень промышленного и сельскохозяйственного производства в Российской Федерации, сократился также торговый оборот России с государствами СНГ, снизились реальные доходы на душу населения, что привело к сокращению его подвижности. Все это предопределило сокращение объемов грузовых и пассажирских перевозок.
На первый план выдвигается ресурсосбережение за счет улучшения конструкций и условий работы пути, оптимального соотношения уровня нагрузок и скоростей движения, исключения перегрузок вагонов, снижения засоряемости пути сыпучими грузами, восстановления и использования старогодных материалов, ликвидация интенсивного бокового износа в кривых участках пути.
В отношении технических средств железнодорожного транспорта целью перехода на ресурсосберегающие технологии является экономия трудовых, топливно-энергетических и материальных ресурсов при улучшении качества содержания и ремонта, повышения уровня их технического состояния и надежности.
Земляное полотно на всем протяжении сети в основном удовлетворяет требованиям перевозочного процесса, однако более чем на 11% эксплуатационной длины оно имеет дефекты и деформации, негативно влияющие на перевозочный процесс.
Важнейшей задачей работников путевого хозяйства является обеспечение бесперебойного и безопасного движения поездов с установленными скоростями. Для успешного решения этой задачи предусматривается дальнейшее усиление пути: укладка рельсов тяжёлого типа Р65 и Р75,железобетонных шпал, бесстыковых плетей, что позволяет увеличивать скорости движения поездов. Необходимо более широко внедрять технологию выполнения работ по текущему содержанию и ремонту пути, предусматривающую использование комплекса наиболее производительных машин и механизмов, повышающих производительность труда, способствующих сокращению сроков выполнения работ и продолжительности «окна». Успешное выполнение поставленных задач требует от путейцев совершенствования их профессиональных знаний.
|
Особое внимание должно быть уделено подготовке специалистов для обслуживания новых специализированных машин. Необходимо отметить, что современные путевые машины отличаются высоким техническим совершенством, наличием большого числа элементов электроники и автоматики в системах управления, достаточно сложных в техническом обслуживании и ремонте. Этими машинами могут управлять лишь специалисты достаточно высокой квалификации. Поэтому необходимо постоянно вести широкую подготовку кадров механиков и других специалистов для новых путевых машин.
Основным направлением для повышения эффективности работы путевого хозяйства является переход на наиболее экономичные и прогрессивные технологии, соответствующие современным требованиям рынка, значительное повышение эффективности производства и приведения технического потенциала в соответствии с потребностями экономики в перевозка.
Технические требования в части надежности и функциональной безопасности для объектов путевого хозяйства должны включать:
а) требования надежности, в том числе:
1) требования безотказности;
2) требования ремонтопригодности;
3) требования долговечности;
4) требования готовности;
б) требования функциональной безопасности;
в) общие требования к обеспечению надежности и функциональной безопасности;
г) общие требования к подтверждению выполнения требований надежности и функциональной безопасности;
д) общие требования к порядку корректировки требований надежности и функциональной безопасности.
Характеристиками и особенностями, необходимыми для описания объекта путевого хозяйства, являются:
а) назначение:
1) ориентировочный маршрут следования,
2) ходовая скорость,
3) продолжительность эксплуатации или наработка в год,
4) доход владельца инфраструктуры от продолжительности эксплуатации или наработки в год,
5) свободное (нерабочее) время в день (время, когда объект путевого хозяйства не эксплуатируется и не находится в ожидании),
6) планируемое общее время использования (продолжительность срока службы в годах);
|
б) характеристика маршрута следования:
1) количество искусственных сооружений (туннелей, виадуков, мостов и т.д.), связанных с ориентировочным маршрутом следования,
2) общее расстояние по видам искусственных сооружений.
В путевом хозяйстве информационную базу УРРАН составляют комплексная автоматизированная система учета, контроля устранения отказов технических средств и анализа их надежности (КАСАНТ), АСУ-Путь и ЕК АСУ-И. По данным КАСАНТ определяется интенсивность отказов технических средств. Методология УРРАН использует этот показатель для оценки рисков нарушения безопасности движения, а также издержек в перевозочном процессе из-за отказов и затрат на их устранение и предупреждение. Данные из АСУ-Путь и ЕК АСУ-И используются для расчета практически всех показателей, включая затраты за период жизненного цикла пути.
Одна из ключевых задач внедрения УРРАН в путевом комплексе — снижение стоимости жизненного цикла путевой инфраструктуры за счет обоснованного перераспределения ресурсов. Иными словами, эта технология помогает планировать работы так, чтобы вложенные средства обеспечивали максимально возможное сокращение совокупных затрат.
Показатели УРРАН позволяют, в частности, выявлять участки и их элементы, имеющие наибольшую частоту отказов за определенный период (наработку), обнаруживать накопление предотказов (дефектов) участков пути за определенный период времени, оценивать правильность выбора решений на этапе проектирования.
Формирование планов ремонтно-путевых работе учетом критериев системы УРРАН на всей сети ОАО «РЖД» начнется с планов на 2014 г. При этом в приоритетном порядке необходимо определить весовые коэффициенты всех семи критериев для наиболее обоснованного назначения к ремонтам участков в случаях ограниченных возможностей финансирования, отработать методологию и показатели критериев для промежуточных видов ремонтов, а также интегрировать АСУ-П, УРРАН и ЕК АСУ-И для автоматизации решения поставленных задач.
В современном комплексе путевого хозяйства разрабатываются типовые проектные решения, а в отдельных случаях не типовые проектные решения ремонтов пути. Одним из самых трудоемких ремонтов является капитальный ремонт пути. В связи развитием современной путейской техники технология проектов ремонтов пути необходимо усовершенствовать с каждым годом. Одним из главных моментов проведения капитального ремонта пути является составление технической документации, в частности составление технологического процесса.
В данном дипломном проекте мы разрабатываем технологический процесс капитального ремонта звеньевого пути пути с заменой балласта машиной СЧ-601 для условий Туймазинской дистанции пути.
|
Условия производства работ
Капитальный ремонт звеньевого пути выполняется в следующей последовательности:
· уборка лишнего балласта с обочины и междупутья земляного полотна. Данные работы выполняются по отдельным технологическим проектам, в ведомости трудозатрат не учтены и в графике не показаны.
· замена рельсошпальной решетки на новую из старогодних материалов.
· выправка пути с подбивкой на старом балласте.
· вырезка загрязненного балласта щебнеочистительной машиной СЧ-601 с последующей его погрузкой в составы для засорителей.
· выгрузка нового щебеночного балласта, первая выправка пути в плане и профиле, стабилизация балластного слоя.
· пополнение новым щебеночным балластом, вторая выправка пути в плане и профиле, стабилизация балластного слоя и оправка балластной призмы.
· шлифовка уложенных рельсов.
· очистка и ремонт водоотводов. Данные работы выполняются по отдельным технологическим проектам, в ведомости трудозатрат не учтены и в графике не показаны.
Таблица № 2.1 Объемы основных работ, подлежащие выполнению.
№ пп | Наименование работ | Единица измерения | Объемы выполняемых работ | |
на участке работ | на 1 км | |||
1. | Уборка лишнего загрязненного балласта с обочины и междупутья земляного полотна | м | ||
2. | Демонтаж рельсошпальной решетки | м | ||
3. | Срезка и планировка балластной призмы | м | ||
4. | Укладка старогодной рельсошпальной решетки | м | ||
5. | Вырезка загрязненного балласта машиной СЧ-601: без разделительного слоя с геотекстилем с пенополистеролом | м3 м3 м3 | ||
6. | Возвращенный в путь балласт: без раздел.слоя с геотекстилем с пенополистеролом | м3 м3 м3 | ||
7. | Выгрузка в путь нового щебеночного балласта: без разделительного слоя с геотекстилем с пенополистеролом | м3 м3 м3 | ||
8. | Подъемка, выправка пути | м | ||
9. | Очистка и ремонт водоотводных сооружений | м |
Все работы выполняются в 8-часовые «окна».
Работы по уборке лишнего балласта с обочины земляного полотна выполняются до начала основных работ по укладке пути и глубокой вырезке балласта. Работы выполняются по отдельным технологическим процессам, затраты труда данным процессом не учитываются, на графике работы не показаны.
Для обеспечения нормальной работы машин при подготовке участка снимаются заземлители опор контактной сети и удаляются препятствия и путевые устройства (Понаб, Диск, УКСПС и т.д.), которые могут вызвать повреждение или незапланированную остановку работающей техники.
При демонтаже рельсошпальная решетка укладывается в пакеты звеньями длиной по 25 м с применением путеукладочного крана УК-25/9-18. Перетяжка пакетов по составу производится 3-мя моторными платформами МПД-2. Все платформы для перевозки пакетов оборудованы съемным оборудованием УСО.
После снятия звеньев 2-мя бульдозерами и автогрейдером производится срезка и планировка верхнего слоя балластной призмы с поперечным уклоном 0,04 в полевую сторону.
Вырезка загрязненного балласта производится с помощью машины СЧ-601 с погрузкой в составы для засорителей СЗ-240/6. Работа по загрузке и вывозу засорителей производится с применением двух составов, один из которых работает челночным методом.
Новый щебеночный балласт доставляется на место работ и выгружается из хоппер-дозаторов.
После выгрузки балласта производится подъемка пути на заданную высоту электробалластером ЭЛБ.
Выправка пути производится:
· машиной ВПО-3000 после замены путевой решетки;
· машиной ВПР-02 после выгрузки и досыпки щебеночного балласта;
· машиной Дуоматик в плане, профиле и по уровню со сплошной подбивкой шпал с постановкой пути в проектное положение.
Динамический стабилизатор ДСП стабилизирует балластную призму после работы машин ВПР-02 и Дуоматик.
Отделка пути, планировка междупутья и обочины земляного полотна выполняется планировщиком балласта ПБ.
Уборка балласта под подошвой рельсов осуществляется вручную.
Лишний балласт у опор контактной сети убирается грейферной установкой АГД-1М (А) в комплекте с прицепом УП-4.
Шлифовка уложенных рельсов производится рельсошлифовальным поездом РШП на стадии заключительных работ.
После выполнения комплекса работ в «окно» путь должен быть приведен в состояние, обеспечивающее безопасный пропуск первых 2-х поездов со скоростью не менее 25 км/час, а последующих со скоростью 60 км/ч Скорость более 100 км/ч устанавливается после пропуска 350 тыс.т брутто после окончательной выправки и стабилизации ДСП.
Производственный состав
Руководящий и обслуживающий персонал.
Начальник (заместитель) ПМС (руководитель работ) ч – 1
Старший дорожный мастер - 1
Дорожный мастер - 2
Сигналисты - 8
Бригадиры пути (неосвоб. в составе м.п.) - 1
Итого (без неосвобожденных бригадиров пути) - 12 чел.
В производственный состав входят:
колонна подготовительных, основных и отделочных работ 52 чел.
бригада № 1 10 чел
бригада № 2 8 чел
бригада № 3 8 чел
бригада № 4 8 чел
бригада № 5 10 чел
бригада № 6 8 чел
цех по обслуживанию машин и механизмов
основного производства 53 чел.
Кроме того бригада рельсошлифовального поезда 12 чел.
Таблица 2.2 Состав цеха по обслуживанию машин основного производства (без учета локомотивов).
№ п/п | Наименование машин | Кол-во машин | Количество машинистов |
1. | УК-25/9-18 | ||
2. | Платформы МПД | ||
3. | Автогрейдер ДЗ-98 | ||
4. | Бульдозер Т-170 | ||
5- | СЧ-601 | ||
6. | Состав СЗ-240-6 | 12 вагонов | |
7. | ВПО-3000 | ||
8. | ВПР-02 | ||
9. | ДСП | ||
10. | ПБ | ||
11. | ХДВ | ||
12. | Дуоматик | ||
13. | АГД-1М(А)сУП | ||
Итого: |
Примечание: 1. Если по условиям производства работ по дням для монтеров пути возникают технологические перерывы, то в эти дни рабочие используются на других видах работ, вне данного технологического процесса.
Организация работ
Работы по капитальному ремонту звеньевого пути на фронте 9600 м выполняются силами путевой машинной станции в «окна» продолжительностью 8 часов.
Подготовительные работы.
В подготовительный период по отдельным технологическим процессам производится:
· на производственной базе - сборка звеньев рельсошпальной решетки на железобетонных шпалах со скреплением АРС, разборка старых звеньев.
· на перегоне - уборка лишнего балласта с обочины и междупутья земляного полотна.
Затраты труда на данные работы в ведомости не учитываются, на графиках не показываются.
Перед производством основных работ по замене рельсошпальной решетки в подготовительный период 11 монтеров пути снимают путевые знаки, путевые обустройства (УКСПС, Диск, Понаб и т.д.) подготавливают места для заезда на путь и съезда с него бульдозеров и автогрейдеров, которые доставляются на перегон на платформах.
Условия производства работ
Объем основных работ:
· укладка рельсовых плетей с вводом в оптимальную температуру, м пути 9600;
· алюминотермитная сварка рельсовых стыков методом промежуточного литья, стык 32.
Укладка и сварка рельсовых плетей выполняется в составе комплекса работ по капитальному ремонту пути на перегоне, протяжением 9.6 км.
Новые рельсовые плети свариваются до длины 800 м в рельсосварочном поезде, транспортируются на специально оборудованном составе и выгружаются в середину колеи напротив места укладки под прикрытием «окна» для производства основных работ или в технологические «окна».
Укладка сварных рельсовых плетей бесстыкового пути производится с помощью приспособления для надвижки плетей с одновременной уборкой инвентарных рельсов с подкладок путеукладочным краном УК-25/9-18. Последняя рельсовая плеть на блок-участке укладывается вместе с изолирующим клееболтовым стыком.
Сварные рельсовые плети доставляются на перегон с двумя болтовыми отверстиями (2-ым и 3-им).
В пределах блок-участка бесстыковые рельсовые плети укладываются без уравнительных пролетов и скрепляются накладками на 4-х болтах.
Укладка рельсовых плетей бесстыкового пути с одновременным вводом укладываемых плетей в оптимальный температурный интервал эксплуатации за счет принудительного изменения их длины при помощи гидравлических натяжных приборов производится при разности температуры рельсовых плетей и планируемой температурой закрепления равной 20° С.
В случае затруднений при растяжении плетей применяются ударные механизмы с клиновыми упорами, которые устанавливаются на рельсовую плеть на расстоянии не более 2/3 длины плети от растягивающего прибора. Ударным механизмом ударяют в конец клина. Усилие передается на плеть и происходит перемещение плети. При необходимости ударный механизм перемещается вдоль рельсовой плети.
При выполнении принудительного ввода плетей в оптимальную температуру плети вывешиваются на парные полиэтиленовые пластины толщиной по 5 мм устанавливаемые на резиновые прокладки на каждой 15-ой шпале: нижняя Г-образная с вертикальной полкой, направленной вниз, верхняя — плоская. Закрепление плетей в пределах анкерных участков производится путем установки монорегулятора в третью позицию.
После завершения работ по сварке монорегуляторы узлов АРС на анкерных участках устанавливаются в первую позицию, рельсы простукиваются деревянными кувалдами и монорегуляторы закрепляются. Эта работа выполняется при скорости пропуска поездов не более 25 км/час.
После проведения указанных работ температура закрепления на участке соответствует оптимальной.
Работы по принудительному вводу плетей в оптимальную температуру выполняются в соответствии с Правилами и технологией выполнения основных работ при текущем содержании пути ЦПТ-52-1998 г.
Закрепление плетей производится после полного их удлинения от неподвижного конца к подвижному на каждой 5-ой шпале, затем – на оставшихся.
На длину перегона рельсовые плети свариваются методом промежуточного литья, с применением специализированного оборудования, оснастки, огнеупорных и формовочных материалов, литейного компонента, соответствующих Техническим условиям (ТУ 0783-001-59033294-2004 «Компонент литейный для алюминотермитной сварки рельсов методом промежуточного литья») и выполняются специалистами, прошедшими обучение и аттестацию.
Алюминотермитную сварку необходимо выполнять при температуре не ниже -5° С.
Стыковой зазор соединяемых рельсов должен быть шириной 25±1 мм.
При установке стыкового зазора между торцами свариваемых рельсов допускается обрезка конца одного рельса таким образом, чтобы расстояние от торца рельса до края ближайшего болтового отверстия составляло не мене 50 мм.
Перед проведением алюминотермитной сварки концы рельсов должны быть совмещены в вертикальной и горизонтальной плоскости. Поверхности катания рельсов должны быть на одном уровне. Несовпадение торцов стыкуемых рельсов должно быть смещено по высоте на подошву, а по ширине головки - в сторону нерабочей грани. При этом несовпадение свариваемых торцов не должно превышать по высоте и ширине 1 мм.
Для компенсации возможной просадки литейного шва концы соединяемых рельсов приподнимаются с помощью клиньев по вертикальной оси стыка на высоту 2,0±0,5 мм.
Алюминотермитная сварка выполняется с предварительным подогревом концов рельсов до температуры 800-900°С кислородно-пропановой горелкой.
Снятие полуформ разрешается не ранее чем через 3-4 мин с момента начала кристаллизации шва. После завершения процесса сварки, литейный шов стыка обрабатывается по поверхности катания и боковым краям головки рельсов путем срезания грата и литников в горячем состоянии (температура металла не должна быть выше 450° С) гратоснимателем, и должны быть обработаны так, чтобы контур сечения литейного шва совпадал с контуром сечения соединяемых рельсов.
После обработки сварных швов поверхности катания и боковые грани головки рельсов в месте сварки должны быть прямолинейными с допуском в вертикальной плоскости не более +0,5 мм и в горизонтальной плоскости не более 0,3 мм на длине 1,0 м. Седловины в местах сварки не допускаются. Проверка качества литейного шва на отсутствие внутренних дефектов выполняется в течение 10 дней после проведения сварочных работ приборами ультразвукового контроля. Дефектоскопирование выполняется после снятия накладок и ограничения скорости до 40 км/час.
После проверки шва на прямолинейность на стыке рельсов, выполненном алюминотермитной сваркой, устанавливаются предохранительные шестидырные накладки, закрепленные 4-мя болтами (средние болты не устанавливаются).
Сварные стыки должны быть отмечены белой несмываемой краской путем нанесения полос шириной 20 мм на шейке и верхней части подошвы рельсов на расстоянии 100 мм с обеих сторон шва. Полосы должны быть продублированы на накладке.
Около каждого сварного стыка на расстоянии 500 - 1500 мм от оси наносится маркировка с номером стыка, согласно записи в журнале учета работ по алюминотермитной сварке; последние две цифры года сварки и код преприятия производителя работ. Маркировка наносится на внутренней стороне шейки рельса белой несмываемой краской.
Перед открытием перегона после основных работ путь приводится в состояние, обеспечивающее пропуск одного-двух поездов со скоростью не более 25 км/час, последующих - с установленной скоростью.
Производственный состав
Работы по замене рельсовых плетей и их сварке на длину перегона выполняются работниками пути ПМС в следующем составе:
Руководящий и обслуживающий персонал:
Заместитель начальника - 1 чел.
Дорожный мастер - 1 чел.
Бригадиры пути (неосвобожденные бригадиры входят в состав монтеров пути) на укладке рельсовых плетей - 6 чел.
Сигналисты - 5 чел.
Итого (без неосвобожденных бригадиров пути) 7 чел.
Состав бригад монтеров пути.
Бригада №1 - 12 чел. Бригада №4 - 12 чел.
Бригада №2 - 12 чел. Бригада №5 - 13 чел.
Бригада №3 - 12 чел. Бригада №6 - 12 чел.
Итого: 73чел.
Монтеры пути на сварке стыков - 4 чел.
Сварщики (2 бригады по 3 чел.) - 6 чел
Дефектоскопист - 1 чел
Итого: 11 чел.
Таблица 3.1 Состав цеха по обслуживанию машин (без учета локомотивов).
№ п/п | Наименование машин | Количество машинистов |
УК-25/9-18 (с платформой МПД) | ||
МПТ | ||
Итого | 5 чел. | |
Всего занято | 96 чел |
Организация работ
Подготовительные работы.
Подготовительные работы выполняются в рельсосварочном предприятии, на производственной базе и на перегоне.
В рельсосварочном предприятии производятся испытания 4-х контрольных образцов сваренных стыков из каждой партии термита на прочность и пластичность.
Для подготовки контрольных образцов отрезают куски рельсов длиной 550-650 мм в количестве 8 штук из тех типов рельсов, которые подлежат сварке.
Результаты испытаний должны соответствовать Техническим указаниям ТУ 0921-127-01124323-2005 «Сварка рельсов алюминотермитная методом промежуточного литья».
Результаты испытаний должны соответствовать Техническим указаниям ТУ 0921-127-01124323-2005 «Сварка рельсов алюминотермитная методом промежуточного литья».
На производственной базе производится погрузка на платформу МПТ инструментов для ввода рельсовых плетей в оптимальный режим эксплуатации и оборудования для сварочных работ.
На перегоне выполняются работы по выгрузке полушпал для опорных прокладок, выгрузке рельсовых плетей внутрь колеи и закреплении их на полушпалах, установке предохранительных башмаков.
Условия производства работ
Объем основных работ выполняемых в «окно» на один стрелочный перевод.
Протяженность участка работ:
- стрелочный перевод + примыкающие звенья 51,565 + 12,5 м х 2 (по прямому направлению).
-вырезка балласта глубиной 40 см с погрузкой засоренного балласта в думпкары 153 м3.
-укладка геотекстиля 52 п.м./ 208 м2.
-планировка балластной призмы автогрейдером (бульдозером) 296,247 м2.
-выгрузка в путь нового балласта 119 м3.
-добавление в путь нового балласта во время балластировочно- выправочных работ 34 м3.
-выправка и рихтовка машиной Унимат 08-275 по прямому направлению 77 м.
-выправка и рихтовка машиной Унимат 08-275 по боковому направлению 47 м.
Работы по замене старогодного одиночного съезда на железобетонных брусьях на новый одиночный съезд проекта 2728 (2799) выполняются за четыре этапа.
- На первом этапе в отдельное "окно" первая часть (старогодный стрелочный перевод №1) старогодного съезда по четному II пути делится на блоки, снимается с пути путеукладочным краном УК-25/28СП, грузится с прилегающими звеньями на специальный подвижной состав №1 и отправляется с места работ.
Экскаватором и автогрейдером (бульдозером) производится глубокая вырезка балласта с погрузкой в порожние думпкары.
Поверхность балластной призмы планируется автогрейдером (бульдозеом) с односкатным поперечным уклоном 0,02 %о на всей ширине площадки в сторону водоотвода. Контроль за уровнем среза (уклона 0,02 %о) осуществляется визированием площадки балластной призмы нивелиром.
На подготовленную поверхность балластной призмы вручную укладывают геотекстиль.
С соседнего пути из думпкаров на геотекстиль выгружается новый щебеночный балласт, перераспределяется с дальнейшей планировкой по всей площади балластной призмы автогрейдером (бульдозером).
Далее краном УК-25/28СП со специального подвижного состава №2 по четному II пути укладывается блоками первая часть (стрелочный перевод №1 проекта 2726 (2750)) нового съезда проекта 2728 (2799).
По уложенному новому стрелочному переводу №1 производятся балластировочно-выправочные работы с применением хоппер-дозатора ВПМ-770 и Унимат 08-275 по прямому и боковому направлению.
- На втором этапе в отдельное "окно" вторая часть (старогодный стрелочный перевод №2) старогодного съезда по нечетному I пути делится на блоки, снимается с пути путеукладочным краном УК- 25/28СП, грузится на специальный подвижной состав и отправляется с места работ.
Экскаватором и автогрейдером (бульдозером) производится глубокая вырезка балласта с погрузкой в порожние думпкары.
Поверхность балластной призмы планируется автогрейдером (бульдозером) с односкатным поперечным уклоном 0,02 %о на всей ширине площадки в сторону водоотвода. Контроль за уровнем среза (уклона 0,02 %о) осуществляется визированием площадки балластной призмы нивелиром.
На подготовленную поверхность балластной призмы вручную укладывают геотекстиль.
С соседнего пути из думпкаров на геотекстиль выгружается новый щебеночный балласт, перераспределяется с дальнейшей планировкой по всей площади балластной призмы автогрейдером (бульдозером).
Далее краном УК-25/28СП со специального подвижного состава по нечетному I пути укладывается блоками вторая часть (стрелочный перевод №2 проекта 2726 (2750)) нового съезда проекта 2728 (2799).
Во время укладки крестовинного блока обеспечивается правильное взаимное положение укороченных брусьев первого и второго стрелочных переводов.
После укладки стрелочного перевода №2 снимаются инвентарные рельсовые рубки по боковому направлению в крестовинном и закрестовинном блоках, и укладываются рельсы с длинами согласно проекта.
По уложенному новому стрелочному переводу №2 производятся балластировочно-выправочные работы с применением хоппер-дозатора ВПМ-770 и Унимат 08-275 по прямому и боковому направлению и далее полностью весь съезд.
На третьем этапе в следующие отдельные "окна" производится сварка стыков вновь уложенного одиночного съезда алюминотермитным способом. Работы по сварке стыков одиночного съезда алюминотермитным способом выполняются по отдельному технологическому процессу, затраты труда не учитываются, на графике производства работ не показаны.
На четвертом этапе в следующее отдельное "окно" производится шлифовка рельсов одиночного съезда проекта 2728 (2799) рельсошлифовальной машиной RR-16.
Работы по шлифовке рельсов одиночного съезда машиной RR-16 выполняют- ся по отдельному технологическому процессу, затраты труда не учитываются, на графике производства работ не показаны.
Кран УК-25/28СП имеет максимальную грузоподъемность 30 т. и может снимать и укладывать блок максимальной длиной 25 м.
Он также оборудован поворотными порталами, которые в транспортном положении находятся в габарите подвижного состава, а на месте работ разворачиваются и имеют проем между внутренними стенками порталов 6 м. Работа с раздвижными порталами производится с нарушением габарита по отношению к соседнему пути при ширине междупутья 5,00 м и менее.
Новый одиночный съезд проекта 2728 (2799) на железобетонных брусьях (состоящий из двух стрелочных переводов проекта 2726 (2750)), собранный на специальном стенде производственной базы ПМС разделен на блоки (приложение №4) и погружен на специальный подвижной состав вместе с примыкающими звеньями рельсошпальной решетки длиной по 12,5 м (приложение №5):
- первый стрелочный перевод по четному II пути
- платформа ПР звено примыкания 12,5 м к рамному блоку
- сцеп из двух платформ ПР рамный блок №1
- платформа ППКЗВ (с наклонной рамой) блок №2 крестовинный
- платформа ППК2В (с наклонной рамой) блок №3 закрестовинный
- платформа ПР звено примыкания 12,5 м по прямому направлению второй стрелочный перевод по нечетному I пути
- платформа ПР звено примыкания 12,5 м к закрестовинному блоку по прямому направлению
- платформа ППК2В (с наклонной рамой) блок №1 закрестовинный
- платформа ППКЗВ (с наклонной рамой) блок №2 крестовинный
- сцеп из двух платформ ПР рамный блок №3
- платформа ПР звено примыкания 12,5 м к рамному блоку.
При этом во время сборки на стенде и укладки в путь крестовинных блоков первого и второго стрелочных переводов проектов 2726, на крестовинах устанавливаются струбцины с деревянными вкладышами, фиксирующие подвижной остряк, для предотвращения его изгиба. После укладки и окончательной фиксации крестовинных блоков струбцины с вкладышами снимаются.
Блоки на платформах с наклонными рамами транспортируются к месту работ в транспортном положении. На месте работ платформы приводятся в горизонтальное (рабочее) положение.
Подача блоков и звеньев примыкания под консоль путеукладочного крана УК25/28СП производится методом перетягивания блоков по роликам на платформах при помощи крановых лебедок. Среднее время на перетягивание одного блока принимаем 5 мин.
В данном технологическом процессе укладка нового одиночного съезда проекта 2728 (2799) производится:
- по четному II пути первый стрелочный перевод проекта 2726 (2750) в направлении от рамного в сторону закрестовинного блока;
- по нечетному I пути второй стрелочный перевод проекта 2726 (2750) в направлении от закрестовинного в сторону рамного блока.
Сплошная выправка первого и второго стрелочных переводов в плане, профиле и по уровню производится машиной Унимат 08-275, после досыпки балласта по прямому и боковому направлению, и весь одиночный съезд после укладки второго стрелочного перевода.
Очистку желобов на стрелочном переводе производят вручную монтеры пути.
Перед открытием движения поездов по вновь уложенному новому одиночному съезду, после выполнения основных работ, съезд и примыкающие участки пути приводятся в состояние, обеспечивающее безопасный пропуск по месту работ первых одного-двух поездов со скоростью не более 25 км/ч., последующих согласно состояния стрелочного перевода.
Установленная скорость на данном участке, восстанавливается только после завершения всего комплекса выправочных работ, полной стабилизации пути и прохода путеизмерительного вагона.
После обкатки съезда, необходимо произвести сварку рельсовых стыков, кроме изолирующих, и стыка в корне кресто<
|
|
Типы оградительных сооружений в морском порту: По расположению оградительных сооружений в плане различают волноломы, обе оконечности...
Своеобразие русской архитектуры: Основной материал – дерево – быстрота постройки, но недолговечность и необходимость деления...
Автоматическое растормаживание колес: Тормозные устройства колес предназначены для уменьшения длины пробега и улучшения маневрирования ВС при...
Биохимия спиртового брожения: Основу технологии получения пива составляет спиртовое брожение, - при котором сахар превращается...
© cyberpedia.su 2017-2024 - Не является автором материалов. Исключительное право сохранено за автором текста.
Если вы не хотите, чтобы данный материал был у нас на сайте, перейдите по ссылке: Нарушение авторских прав. Мы поможем в написании вашей работы!