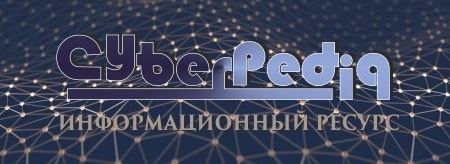
Индивидуальные очистные сооружения: К классу индивидуальных очистных сооружений относят сооружения, пропускная способность которых...
Кормораздатчик мобильный электрифицированный: схема и процесс работы устройства...
Топ:
Основы обеспечения единства измерений: Обеспечение единства измерений - деятельность метрологических служб, направленная на достижение...
Процедура выполнения команд. Рабочий цикл процессора: Функционирование процессора в основном состоит из повторяющихся рабочих циклов, каждый из которых соответствует...
Теоретическая значимость работы: Описание теоретической значимости (ценности) результатов исследования должно присутствовать во введении...
Интересное:
Наиболее распространенные виды рака: Раковая опухоль — это самостоятельное новообразование, которое может возникнуть и от повышенного давления...
Что нужно делать при лейкемии: Прежде всего, необходимо выяснить, не страдаете ли вы каким-либо душевным недугом...
Лечение прогрессирующих форм рака: Одним из наиболее важных достижений экспериментальной химиотерапии опухолей, начатой в 60-х и реализованной в 70-х годах, является...
Дисциплины:
![]() |
![]() |
5.00
из
|
Заказать работу |
|
|
Часть I
РАСЧЕТ РАБОЧЕГО ЦИКЛА И ПОКАЗАТЕЛЕЙ ДВИГАТЕЛЯ
ВЫБОР ИСХОДНЫХ ДАННЫХ ДЛЯ РАСЧЕТА
По заданным значениям номинальной мощности NH, номинальной частоте вращения коленчатого вала пн на базе справочных статистических данных, прежде всего, необходимо обосновать конструктивные параметры проектируемого двигателя (число и расположение цилиндров, наличие и степень наддува, степень сжатия и др.) [19, 20] (прил. 1 — 4).
Выбор степени сжатия е двигателя
При проектировании двигателей с принудительным воспламенением заряда от искры в целях повышения мощности и улучшения топливной экономичности в большинстве случаев выбирают максимальную е. Однако верхний предел ее при этом ограничивается возможностью нарушения процесса сгорания в виде детонации. Величина степени сжатия зависит от многих конструктивных и эксплуатационных факторов: диаметра цилиндра, типа системы охлаждения, материала, из которого изготовлены головка и блок двигателя, октанового числа (04) применяемого топлива, скоростного и нагрузочного режимов работы двигателя и т. д.
Взаимосвязь с 04 топлива выражается данными, представленными в табл. 1.1 [3].
ОЧ | 66 - 72 | 73 - 76 | 77-80 | 81-90 | 91-100 | |
ε | 5,5-6,5 | 6,6-7,0 | 7,1-7,5 | 7,6-8,5 | 8,6-9,5 |
Приближенно Зависимость от конструктивных параметров и ОЧ бензина может быть представлена формулой (12)
,
где D – диаметр цилиндра, принимаемый по двигателю-прототипу, мм; ОЧ – октановое число бензина.
В дизельных двигателях внутренного сгорания (ДВС) величина зависит от способа смесеобразования. Верхний её предел ограничивается нагрузками, действующими на детали кривошипно-шатунного механизма (КШМ). В безнаддувных дизелях с неразделенными камерами сгорания е равняется 14 — 19, в вихрекамерных и предкамерных — 16 — 22, в дизелях с наддувом — 12 — 17.
|
Выбор состава топливовоздушной смеси
Состав топливовоздушной смеси характеризуется величиной коэффициента избытка воздуха а. При расчете рабочих циклов, характерных для номинальных режимов работы двигателей внутреннего сгорания, ориентировочные значения а выбирают в таких пределах: для двигателей с искровым зажиганием — 0,85 — 0,95, для дизелей без наддува с неразделенными камерами сгорания и объемным смесеобразованием — 1,50 — 1,80, с пленочным смесеобразованием — 1,45 — 1,55, для вихрекамерных и предкамерных — 1,25 — 1,45, для дизелей с наддувом — 1,50 — 2,0.
В случаях расчета циклов на режимах, отличных от номинальных, диапазон варьирования коэффициента избытка воздуха в зависимости от нагрузки может находиться в следующих пределах: для двигателей с искровым зажиганием — 0,7 — 1,3, для дизелей — 1,2 — 6,0.
РАСЧЕТ ПРОЦЕССОВ ГАЗООБМЕНА
Процессы газообмена включают очистку цилиндра от продуктов сгорания и наполнение его свежим зарядом. Перед началом процесса впуска в объеме Vc камеры сгорания всегда содержится некоторое количество остаточных газов. Давление их рг зависит от числа и расположения клапанов, сопротивления впускного и выпускного коллекторов, фаз газораспределения, частоты вращения и нагрузки двигателя, способа наддува и других факторов. В автотракторных двигателях, работающих на номинальном режиме без наддува, = (1,05... 1,25)р0, с наддувом -
= (0,75... 0,98)рк.
Для карбюраторных двигателей при полностью открытом дросселе в зависимости от частоты вращения для нахождения рг можно использовать зависимость [3]
(4)
где пх — текущая частота вращения коленчатого вала двигателя, об/мин.
При необходимости определения рг двигателя, работающего на различных скоростных режимах, пользуются формулой [3]
(5)
Температура остаточных газов Тг зависит от конструктивных параметров и режима работы двигателя. Для четырехтактных двигателей, работающих на номинальном режиме, она принимается в следующих пределах: для карбюраторных — 900 — 1 100 К, для дизелей — 600 — 900, для газовых — 750 — 1 000 К.
|
При выборе значения Тг следует учитывать, что с повышением частоты вращения температура остаточных газов возрастает, а при увеличении степени сжатия и угла опережения зажигания (подачи топлива) — снижается.
Температура подогрева свежего заряда ∆T зависит от конструкции впускного трубопровода, его установки, способа подогрева свежего заряда, скоростного режима двигателя. В двигателях с наддувом величина ∆T снижается из-за уменьшения температурного перепада между нагретыми деталями двигателя и наддувочным воздухом. При повышении ∆T улучшается смесеобразование, но снижается плотность заряда и, как следствие, наполнение и мощность двигателя.
При расчете номинальных режимов работы четырехтактных двигателей значения ∆T [16] принимают в следующих пределах: для карбюраторных — -5 - +25, для дизелей без наддува — +20 - +40, для двигателей с наддувом — 0 - +10 °С.
При частотах вращения вала двигателя пх, отличных от номинальной, величина подогрева заряда на впуске может быть определена по формуле [3]
∆Т = ∆ТН • (110 - 0,0125пх)/(110 - 0,0125пн). (6)
Давление заряда в конце впуска ра
Под давлением конца впуска ра понимается среднее давление за весь процесс впуска. Так как впускная система двигателя оказывает сопротивление прохождению заряда, для безнаддувных двигателей оно всегда ниже атмосферного давления р0. Для двигателей с наддувом ра меньше давления наддувочного воздуха рк:
Потери давления ∆ра на впуске определяются гидравлическим сопротивлением воздушного фильтра Арф, впускного трубопровода ∆ртр, впускного клапана Аркл, карбюратора ∆ркар, охладителя наддувочного воздуха ∆рохл и других устройств ∆рп [3 ]:
(7)
Сопротивление воздушного фильтра ∆рф может быть найдено по графику (рис. 1.1) в зависимости от пылеемкости фильтра [9]:
(8)
где Пф — пылеемкость фильтра, г • ч/м3; — запыленность воздуха, г/м; t — срок службы фильтра, ч.
Принята следующая классификация запыленности атмосферного воздуха: пониженная — меньше 0,0005 г/м3, малая — 0,0005 — 0,002; повышенная — 0,002 — 0,01, максимальная — 0,01 — 0,60, „нулевая" видимость — 0,8 —. 1,0 г/м3 [9]. Величины других сопротивлений, входящих в формулу, приближенно соответствуют следующим значениям: ∆ртр = ∆ркл = 0,001... 0,0015-∆Ркар - 0.015 - 0,02 МПа.
|
Показатели сопротивления охладителя ∆рохл и других устройств ∆рп подбирают так, чтобы суммарные гидравлические потери ∆ра для 4-тактных двигателей, работающих на номинальном режиме, находились в таких пределах: для карбюраторных двигателей — (0,05... 0,2)ро, дизелей без наддува — (0,03... 0,16)ро, с наддувом — (0,03... 0,10)рк.
Величина уг характеризует качество очистки цилиндра от продуктов сгорания. При тепловом расчете двигателя она может быть определена по формуле
При безнаддувочном варианте двигателя в дальнейшем будем считать Тк = То; рк = р0.
Расчетные значения уг двигателей, работающих на номинальном режиме, не должны выходить за следующие пределы: 0,04 — 0,08 — для карбюраторных и газовых двигателей, 0,03 — 0,06 — для дизелей.
Температура заряда в конце впуска Та рассчитывается по формуле
Значения Та для 4-тактных ДВС, работающих на номинальном режиме, должны находиться в следующих пределах: для карбюраторных — 320 — 380 К, для дизелей без наддува — 310 — 350, с наддувом — 320 - 400 К.
.Коэффициент наполнения tjv представляет собой отношение действительного количества свежего заряда Gj, поступившего в цилиндр в процессе впуска, к количеству Go, которое могло бы, поместиться в рабочем объеме цилиндра при условии, что температура и давление в нем равны температуре и давлению среды, из которой поступает свежий заряд (р0 и То — для двигателей без наддува, рк и Тк — для двигателей с наддувом) [16].
При расчете процесса наполнения величину t]v для 4-тактных двигателей можно определить по следующей формуле [14].
Численные значения r/v для 4-тактных двигателей с номинальным режимом работы должны находиться в следующих пределах [14]: для карбюраторных — 0,7 — 0,9, для дизелей без наддува — 0,80 — 0,94, с наддувом — 0,80 — 0,97.
РАСЧЕТ ПРОЦЕССА СЖАТИЯ
Основными параметрами процесса сжатия являются давление рс и температура Тс конца сжатия. Их рассчитывают по формулам
,
,
где n1 — средний показатель политропы сжатия, характеризующий теплообмен между зарядом и стенками цилиндра и зависящий от многих конструктивных и эксплуатационных характеристик. Все факторы, способствующие уменьшению отвода теплоты от заряда в окружающую среду, приводят к увеличению nj и, следовательно, к улучшению выходных показателей цикла.
|
Возможные значения n1, рс и Тс двигателя, работающего на номинальном режиме, даны в табл. 1.2 [16].
предыдущего цикла, к числу молей свежего заряда Mb поступившего в цилиндр в процессе впуска [14]:
Таблица 1.2
Тип двигателя | n1 | pC, МПа | TC, K |
Карбюраторный Дизель без наддува Дизель с наддувом (без промежуточный охлаждения воздуха) | 1,34-1,39 1,38-1,42 1,35-1,38 | 0,8-2,0 3,5-5,0 6,0-8,0 | 550-800 700-950 900-1100 |
При отсутствии данных о величине показателя политропы сжатия проектируемого двигателя, а также двигателей, работающих на скоростных режимах, отличных от номинального, можно задаться зависимостью
n1 = 1,41 – 110/ n
где n — частота вращения коленчатого вала, об/мин.
1.4. РАСЧЕТ ПРОЦЕССА СГОРАНИЯ
В процессе сгорания тепло, подведенное к рабочему телу, расходуется на изменение его внутренней энергии и совершение внешней работы. Расчет процесса сгорания производится в два этапа: 1 — термохимический для определения количества рабочего тела в цилиндре; 2 — термодинамический для установления параметров состояния рабочего тела.
Таблица 1.3
Топливо | Состав 1 кг топлива, кг | Содержание газов, % по массе (объему) | Низшая теплота сгорания | |||||
углерод | водород | кислород | метан | пропан | бутан | кДж/кг | кДж/м3 | |
Автомобильный бензин | 0,854 | 0,144 | - | - | - | - | - | |
Дизельное топливо | 0,864 | 0,126 | 0,01 | - | - | - | - | |
Сжиженный газ: СПБТЛ (летний) СПБТЗ (зимний) | - - | - - | - - | 4,0 6,0 | 75,0 33,0 | 20,0 60,0 | - - | |
Сжатый газ А Б | - - | - - | - - | 1,5 1,5 | 1,0 1,0 | - - |
Количество остаточных газов Мг (кмоль)
. (24)
Количество продуктов сгорания М2 (кмоль), образующихся при сгорании 1 кг жидкого топлива, может быть определено по формулам, приведенным ниже.
При а > 1 (для дизельных двигателей)
при (для карбюраторных двигателей)
(26)
Количество продуктов сгорания (кмоль) газообразного топлива (м3) [16]
(27)
где — количество азота в топливе (1 кмоль азота /1 кмоль топлива).
Изменение количества газов при сгорании определяют как разность между количеством продуктов сгоранияи свежего заряда :
(28)
Для дизелей
(29)
для карбюраторных двигателей
(30)
для газовых двигателей
(31)
При сгорании жидкого топлива в двигателях всегда происходит увеличение количества газа вследствие повышения суммарного числа молекул при химических реакциях их распада и образования новых в результате сгорания водорода и участия в реакциях кислорода, содержащегося в топливе. При сгорании газообразного топлива в зависимости от состава газа
может быть положительным, отрицательным или равным нулю.
|
Относительное изменение количества газа в цилиндре двигателя при сгорании горючей смеси характеризуется химическим коэффициентом молекулярного изменения
(32)
Для дизельных двигателей
(33)
для карбюраторных
(34)
для газовых
(35)
С увеличением химический коэффициент молекулярного изменения
будет приближаться к единице, причем для жидких топлив он будет всегда уменьшаться с повышением
, а для газообразных характер изменения (возрастание или уменьшение) будет зависеть от положительного или отрицательного значения
В конце сгорания заряд в цилиндре двигателя будет состоять из продуктов сгорания топлива
и остаточных газов
(кмоль):
(36)
Для дизелей при
(37)
для карбюраторных двигателей при
(38)
для двигателей, работающих на газовом топливе,
(39)
Относительное изменение количества газа (в киломолях) в цилиндре двигателя при сгорании рабочей смеси характеризуется действительным коэффициентом молекулярного изменения :
(40)
или
(41)
Для карбюраторных двигателей значения находятся в пределах 1,05 — 1,08, для дизелей — 1,01 — 1,05.
Рис. 4.1. Силы, действующие в КШМ
Для каждого поворота коленчатого вала φ ее находят по индикаторной диаграмме, построенной на основании теплового расчета.
4.1. ПОСТРОЕНИЕ ИНДИКАТОРНОЙ ДИАГРАММЫ В КООРДИНАТАХ Р — φ
Перестроение индикаторной диаграммы из координат р — V в развернутую диаграмму по углу поворота коленчатого вала осуществляется по методу профессора Ф. А. Брикса. Для этого под индикаторной диаграммой строят полуокружность с радиусом г (см. рис. 1.2, а), имея в "виду, что Полуокружность делят на дуги с центральным углом 30°, точки полуокружности соединяют с центром 0, затем смещают его в сторону НМТ на величину
Из нового центра 0 строят лучи параллельно радиусам, проведенным к точкам на окружности. Из полученных точек проводят перпендикуляры к диаметру окружности и продолжают их до пересечения с линиями индикаторной диаграммы. Эти точки дают значения давления газов рг, соответствующие данному углу поворота кривошипа.
Справа от диаграммы р — V чертят прямоугольные координатные оси (см. рис. 1.2,6). Ось абсцисс (ось р) должна находиться на одном уровне с линией атмосферного давления на индикаторной диаграмме и иметь длину, равную (в масштабе φ) продолжительности рабочего цикла в одном цилиндре двигателя. Затем ось абсцисс диаграммы Р — φ разбивают на одинаковые интервалы (30 °) и через полученные точки деления проводят вертикальные линии. На каждую из них проецируют точки 1, 2, 3 и другие из индикаторной диаграммы р — V и на развернутой индикаторной диаграмме Р — φ получают соответственно точки 1,2,3 и т. д. Таким же образом находят остальные точки диаграммы Р — φ. Соединив их плавной кривой, получают развернутую индикаторную диаграмму. Если умножить полученные ординаты на масштаб силы давления газов , то развернутая диаграмма будет являться также графиком сил давления газов по углу поворота коленчатого вала:
(123)
где Fn — площадь днища поршня.
(124)
где у — высота ординаты, мм.
По данным табл. 4.4 на новой координатной сетке, которую рекомендуется размещать под координатной сеткой графиков сил строится график тангенциальной силы
в том же масштабе, что и графики сил
(рис. 4.2).
Рис. 4.2. Примерный вид трафика изменения тангенциальной силы 4-тактного двигателя
Силу К, действующую вдоль щеки кривошипа, рассчитывают по формуле
(130)
Значения тригонометрического многочлена cos (φ +)5)/cos/3 для различных углов φ представлены в прил. 10.
Направления положительных и отрицательных сил Т и К показаны на рис. 4.1.
Рис. 4.3. Примерный вид графика изменения силы К = f(y>) 4-тактного двигателя
4.5. ПОСТРОЕНИЕ ГРАФИКА КРУТЯЩЕГО МОМЕНТА ДВИГАТЕЛЯ. ОПРЕДЕЛЕНИЕ СРЕДНЕГО ЭФФЕКТИВНОГО МОМЕНТА
Кривая изменения силы является также кривой изме-
нения индикаторного крутящего момента одноцилиндрового 4-тактного двигателя в масштабе
(рис. 4.4, а).
Кривая суммарного крутящего момента многоцилиндрового двигателя строится методом графического суммирования кривых крутящих моментов каждого цилиндра [7, 16]. Суть данной методики сводится к следующему: на графике от начала координат откладывают угловой интервал, вычисляемый по формуле
(131)
Масштаб должен быть равен масштабу
. График крутящего момента одного цилиндра делится по оси абсцисс на равные части, число которых равно числу цилиндров. Для получения графика суммарного крутящего момента двигателя достаточно перенести эти части на угловой интервал G и выполнить их графическое сложение с учетом знаков ординат (рис. 4.4,6). Как видно из рисунка, график
является периодической функ-
цией с периодом изменения
Среднее значение крутящего момента многоцилиндрового двигателя определяется по формуле
(132)
где — положительная и отрицательная площади графика
м — масштаб крутящего момента, Н • м/мм;
— длина отрезка АВ, мм. Крутящий момент двигателя
(133)
где — его механический КПД. Рассчитанная таким образом величина эффективного крутящего момента должна совпадать с величиной, вычисленной ранее по формуле
(134)
где — эффективная мощность двигателя, кВт; п — частота вращения вала двигателя,, об/мин.
Разница между показателями не должна быть более ±5 — 8 %.
Для V-образного двигателя диаграмму суммарного крутящего момента (тангенциальной силы) строят в несколько иной последовательности по сравнению с рядным [3, 7]. Сначала выполняют диаграмму изменения крутящего момента (тангенциальной силы) за рабочий цикл для первого цилиндра правого ряда (рис. 4.5, а), ниже ее — диаграмму крутящего момента (тангенциальной силы) для первого цилиндра левого ряда, сдвинутую по фазе с запозданием относительно первого цилиндра правого ряда на угол развала цилиндров (рис. 4.5,6). С интервалом 10 — 30° алгебраически складывают ординаты MRp для первых двух цилиндров правого и левого рядов, точки соединяют плавной
кривой и получают диаграмму суммарного крутящего момента (тангенциальной силы) '(рис. 4.6).
Рис. 4.5. Диаграмма тангенциальных сил первого (а) и четвертого (б) цилиндров V-образного 6-цилиндрового двигателя с углом развала цилиндров, равным 120
Рис. 4.6. Совместная диаграмма тангенциальных сил первого и четвертого цилиндров
Кривую суммарного крутящего момента первых двух цилиндров разбивают на участки О' — число цилиндров одного ряда) и переносят эти участки кривой
на угловой интервал
Далее осуществляют графическое суммирование ординат кривых крутящих моментов на угловом интервале в, отмечают полученные точки на графике и вычерчивают результирующую кривую крутящего момента для многоцилиндрового двигателя. На остальных угловых участках рабочего цикла она будет периодически повторяться (рис. 4.7).
Рис. 4.7. Результирующая диаграмма тангенциальных сил 6-цилиндрового V-образного двигателя
Среднее значение крутящего момента V-образного двигателя определяют так же, как и рядного, по зависимости (132).
4.6. ОПРЕДЕЛЕНИЕ СИЛ, ДЕЙСТВУЮЩИХ НА ШАТУННЫЕ И КОРЕННЫЕ ШЕЙКИ
Из схемы сил, приведенной на рис. 4.1, видно, что шатунная шейка коленчатого вала нагружается силой S, передаваемой шатуном от верхней головки, и центробежной силой Рс. Составляющие силы S (Т и К) определяются по формулам (129) и (130)
для любого угла поворота кривошипа в заносятся в табл. 4.4 и 4.5.
По. данным расчета построим векторную диаграмму нагрузок на шатунную шейку в координатах Т и К. Для этого возьмем прямоугольные оси координат (рис. 4.8), где ось абсцисс представляет собой ось сил Т, а ось ординат — сил К. Примем силы Т положительными, если они направлены в сторону от оси цилиндра, и отрицательными, если они имеют обратное направление.
Рис. 4.8. Полярная диаграмма нагрузок на шатунную шейку 4-тактного двигателя: а — карбюраторного; б — дизеля
Силы К считают положительными, если они направлены вниз (сжимают кривошип), и отрицательными, если они направлены вверх (растягивают кривошип). При построении диаграммы ось шатунной шейки считают неподвижной, а цилиндр — вращающимся вокруг оси шатунной шейки, поэтому отсчет точек ведут против часовой стрелки. Полученные точки соединяют последовательно плавными кривыми и получают полярную диаграмму нагрузок шатунной шейки от действия сил Т и К (см. рис. 4.8).
Для учета нагруженности шатунной шейки центробежной силой от массы нижней головки шатуна тн „„ вниз (см. рис. 4.8) из начала координат откладывают значение Рс, вычисленное по формуле
(135)
Масштаб силы должен быть таким же, как и сил Т и К. Радиус-вектор
будет равен в масштабе нагрузке на поверхность шатунной шейки, соответствующей данному углу поворота коленчатого вала (см. рис. 4.8).
Для прочностного расчета кривошипа векторную диаграмму нагрузки на шатунную шейку, как правило, перестраивают в развернутую (рис. 4.9). С этой целью наносят прямоугольные оси координат, где по оси абсцисс откладывают углы поворота , а по оси ординат в масштабе— нагрузки
, определяемые длиной радиуса-вектора.
По этой диаграмме определяют площадь , заключенную между кривой и осью φ, которая будет характеризовать величину средней нагрузки на шатунную шейку за цикл работы двигателя:
(136)
где — длина диаграммы
, мм.
Удельную нагрузку на рабочую поверхность шатунной шейки, определяющую условия работы шатунного подшипника и срок его службы, находят по формуле
(137)
где — соответственно диаметр и длина шатунной шейки, м.
Среднее удельное давление на шейки коленчатого вала при работе двигателя с номинальной нагрузкой может достигать: у карбюраторного — 4 — 12, у дизеля — 6 — 16 МПа. Для антифрикционных сплавов подшипников скольжения [qn] оно должно быть меньше допустимых нагрузок. Для сплавов АСМ АО — 28, для свинцовистой бронзы БрС — 30 — 32 МПа. Развернутую диаграмму
используют также для определения места сверления отверстия в шатунной шейке, по которому подводится смазка к подшипнику скольжения. Обычно его сверлят в зоне наименьшего давления.
Для определения нагрузки на коренные шейки коленчатого •вала на векторной диаграмме (см. рис. 4.8) начало радиуса-вектора необходимо перенести в новую точку Ог, которая должна отстоять от начала координат (точка 0) на расстояние, соответствующее в масштабе величине центробежной силы вращающихся масс кри-вошипно-шатунного механизма:
(138)
где — масса вращающихся элементов кривошипа (щек шатунной шейки).
Радиус-вектор (см. рис. 4.8) будет в масштабе силы давать нагрузку на поверхность коренной шейки, соответствующую данному углу поворота коленчатого вала.
Построение развернутой диаграммы и определение средней нагрузки RKnICp на коренную шейку осуществляют так же, как и для шатунной шейки. Удельная нагрузка на коренную шейку рассчитывается по формуле
(139)
где — соответственно диаметр и длина коренной шейки коленчатого вала, м.
Значения некоторых типов двигателей даны в прил. 1, 2.
5. ОПРЕДЕЛЕНИЕ КОЭФФИЦИЕНТОВ НЕРАВНОМЕРНОСТИ КРУТЯЩЕГО МОМЕНТА И ХОДА ДВИГАТЕЛЯ
Как видно из диаграммы (см. рис. 4.4), крутящий момент даже при установившемся режиме работы двигателя является переменной величиной, зависящей от сил давления газов в цилиндрах, угла поворота кривошипа и сил инерции возвратно-поступательно движущихся масс. Такое изменение крутящего момента вызывает соответствующую неравномерность хода (вращения вала) двигателя, от которой зависит возникновение крутильных колебаний в коленчатом валу, что еще более увеличивает неравномерность его вращения. Неравномерность крутящего момента оценивают коэффициентом его неравномерности [16]:
(140)
где — соответственно максимальное, минимальноеи среднее значения индикаторного крутящего момента.
Колебание угловой скорости со за цикл при установившемся режиме характеризуется коэффициентом неравномерности хода двигателя
(141)
где— соответственно максимальное, минимальное и среднее значения угловой скорости за цикл работы двигателя.
Коэффициент неравномерности хода можно найти из выражения
(142)
где — индикаторная мощность двигателя, Вт;
— приведенный момент инерции движущихся масс двигателя, кг • м;
— наибольшее значение максимальной избыточной работы, Дж;
— работа средней суммарной тангенциальной силы на фланце коленчатого вала за один оборот, Дж.
Приближенно величину избыточной работы можно найти из формулы
(143)
При практических расчетах коэффициента неравномерности хода по формуле (142) величину отношения принимают в зависимости от числа цилиндров и тактности двигателя (табл. 5.1) [16].
Таблица 5.1
Число цилиндров | Отношение Lизб/Lср | Число цилиндров | Отношение Lизб/Lср | ||
Для 4-х тактных двигателей | Для 2-х тактных двигателей | Для 4-х тактных двигателей | Для 4-х тактных двигателей | ||
3,10 1,30 0,80 0,17 | 1,30 0,58 0,25 0,11 | 0,30 0,10 0,13 0,09 | 0,045 0,025 0,010 – |
Расчетные значения величины δ не должны превышать допустимые: для тракторных двигателей — 0,003 — 0,01, для автомобильных — 0,01 — 0,02.
Приведенный момент инерции 10 движущихся масс двигателя приближенно можно определить по формуле В. П. Терских [8,16]:
где D и d — диаметры цилиндра и коренной шейки коленчатого вала, см; b — число рабочих полостей, приходящихся на одно колено (для V-образных двигателей b равно 2, для рядных— 1); к' — коэффициент, учитывающий длину шатуна и тип двигателя; h — расстояние между цилиндрами, см; г — радиус кривошипа, см. В пределах применимости формулы (144), определяемой неравенством значения
рассчитывают по следующим выражениям:
— для двигателей с чугунными поршнями
(145)
— для двигателей с поршнями из алюминиевого сплава
(146)
где — длина шатуна, см.
Межцилиндровое расстояние h при расчетах находят из отношения [16]; для карбюраторных двигателей оно равно 1,2 — 1,28, для дизелей — 1,47 — 1,55.
Момент инерции маховика двигателя
(147)
Значения приведенного момента инерции и коэффициента неравномерности крутящего момента для некоторых типов двигателей представлены в табл. 5.2 [16].
Таблица 5.2
Марка двигателя | Момент инерции I0, кг*м2 | Коэффициент неравномерности крутящего момента |
ЗИЛ – 130 ЯМЗ -236 ЯМЗ – 238 Д-50, Д-240 СМД -60, СМД-62 | 0,61 2,45 2,45 2,40 2,00 | 1,36 2,28 1,36 3,35 2,28 |
Размеры маховика определяются с помощью выражения
(148)
где — средний диаметр обода маховика.
Задавшись диаметром обода найдем необходимую массу маховика
При известной массе по выражению (148) можно вычислить
Для автомобильных двигателей он равен 0,30 —
0,45, для тракторных — 0,30 — 0,50 м.
Маховик обеспечивает заданную степень равномерности вращения коленчатого вала и минимальную частоту его вращения на холостом ходу. В процессе расчета его конструктивных параметров необходимо учитывать, что если значение малое, затрудняется трогание трактора или автомобиля с места, если чрезмерно большое, ухудшаются приемистость двигателя и разгон МТА или автомобиля.
При определении массы маховика считают, что момент его инерции 1М составляет: для автомобильного двигателя — 80 — 90, для тракторного — 75 — 90 % от приведенного момента инерции
С целью обеспечения необходимой прочности наружный диаметр маховика выбирают по допустимой скорости VM на наружной окружности:
(149)
Допустимое значение окружной скорости для чугунных маховиков не должно превышать 70 м/с, для стальных литых — 100, для стальных штампованных — 110 м/с.
6. РАСЧЕТ ОСНОВНЫХ СИСТЕМ ДВИГАТЕЛЯ
БИБЛИОГРАФИЧЕСКИЙ СПИСОК
1. Артамонов М. Д., Морин Af. М., Скворцов Г. Л. Основы теории и конструирования автотракторных двигателей. М.: Высш. шк., 1978. 133 с.
2. Банковский Ю. М., Галактионов В. А., Михайлова Т. Н. Графор. Графическое расширение Фортрана. М.: Наука, 1985. 288 с.
3. Богатырев А. В., Корабельников А. II., Чумаков В. Л. Тракторы и автомобили: В 2 ч. Ч. I. Двигатели: Учеб.-метод. пособие по выполнению курсовой работы/ МГАУ им. В. П. Горячкина. М., 1993. 87 с.
4. Ветчинников М. #., Шилова Г. М. Основы работы и выполнения чертежей на персональных ЭВМ: Учеб. пособие / Саранск: Изд-во Мордов. ун-та, 1995. 88 с.
5. ГОСТ 14846—81. Двигатели автомобильные: Методы стендовых испытаний. М.: Изд-во стандартов, 1981. 37 с.
6. ГОСТ 18509—88 (СТ СЭВ 2560—80). Дизели тракторные и комбайновые: Методы стендовых испытаний. М.: Изд-во стандартов, 1988. 70 с.
7. Двигатели внутреннего сгорания: Системы поршневых и комбинированных двигателей / По
|
|
Двойное оплодотворение у цветковых растений: Оплодотворение - это процесс слияния мужской и женской половых клеток с образованием зиготы...
Биохимия спиртового брожения: Основу технологии получения пива составляет спиртовое брожение, - при котором сахар превращается...
Общие условия выбора системы дренажа: Система дренажа выбирается в зависимости от характера защищаемого...
Адаптации растений и животных к жизни в горах: Большое значение для жизни организмов в горах имеют степень расчленения, крутизна и экспозиционные различия склонов...
© cyberpedia.su 2017-2024 - Не является автором материалов. Исключительное право сохранено за автором текста.
Если вы не хотите, чтобы данный материал был у нас на сайте, перейдите по ссылке: Нарушение авторских прав. Мы поможем в написании вашей работы!