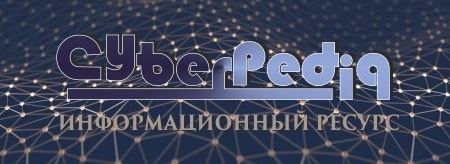
Автоматическое растормаживание колес: Тормозные устройства колес предназначены для уменьшения длины пробега и улучшения маневрирования ВС при...
Особенности сооружения опор в сложных условиях: Сооружение ВЛ в районах с суровыми климатическими и тяжелыми геологическими условиями...
Топ:
Оценка эффективности инструментов коммуникационной политики: Внешние коммуникации - обмен информацией между организацией и её внешней средой...
Эволюция кровеносной системы позвоночных животных: Биологическая эволюция – необратимый процесс исторического развития живой природы...
Генеалогическое древо Султанов Османской империи: Османские правители, вначале, будучи еще бейлербеями Анатолии, женились на дочерях византийских императоров...
Интересное:
Финансовый рынок и его значение в управлении денежными потоками на современном этапе: любому предприятию для расширения производства и увеличения прибыли нужны...
Распространение рака на другие отдаленные от желудка органы: Характерных симптомов рака желудка не существует. Выраженные симптомы появляются, когда опухоль...
Берегоукрепление оползневых склонов: На прибрежных склонах основной причиной развития оползневых процессов является подмыв водами рек естественных склонов...
Дисциплины:
![]() |
![]() |
5.00
из
|
Заказать работу |
МОМЕНТОПЕРЕДАЮЩИЕ СОЕДИНЕНИЯ В МАШИНОСТРОЕНИИ
Методы обработки и инструмент для получения профильных моментопередющих соединений.
Существуют различные инструменты и методы обработки зубчатых колес с внутренними зубьями. Внутренние зубья нарезают зубодолбление, фрезерованием специально спрофилированными дисковыми и пальцевыми фрезами на зубофрезерных станках, оснащенных специальными головками, в которые устанавливается инструмент. Кроме того, применяют методы характерные только для этого вида колес, например обработку зуботочением на зубофрезерных станках обкаточными резцами, обработку червячными фрезами с укороченными профилирующими кромками, протягивание цилиндрическими протяжками, зубострогание специальными резцами. Все методы приведены в таблице 1 [41].
Одним из основных методов нарезания внутренних зубьев является долбление на универсальных станках и станках с ЧПУ. Обработка колес зубодолблением основана на воспроизведении процесса обката в беззазорном зацеплении двух зубчатых колес, одно из которых является инструментом, а другое – заготовкой (рисунок 1.6).
Зубья открытых и полуоткрытых венцов колес обычно нарезают дисковыми долбяками; при обработке зубьев закрытых венцов применяют чашечные и хвостовые долбяки. В современном производстве производительность процесса зубодолбления увеличивают за счет усложнения конструкции долбяка (рисунок 1.7), в том числе его сдваивания, что позволяет за один установ обрабатывать детали более сложной конфигурации, имеющие одновременно наружные и внутренние зубья.
Таблица 1. Методы обработки внутренних профилей
Метод обработки | Эскиз | Станки, инструмент |
Долбление | ![]() | Зубодолбежные универсальные станки, зуборезные долбяки всех типов |
Фрезерование | ![]() | Зубофрезерные станки с накладной головкой |
Фрезерование | ![]() | Зубофрезерные станки с накладной головкой, червячная фреза |
Обработка обкаточным инструментом | ![]() | Зубофрезерные станки, одновитковая фреза- улитка |
Зуботочение | ![]() | Станки для зуботочения, многозаходная обкаточная резцовая головка |
Протягивание | ![]() | Зубопротяжной станок, протяжка |
Продолжение Таблица 1 | ||
Строгание | ![]() | Зубострогальный станок, зуборезная гребенка для обработки внутренних зубьев |
Шевингование | ![]() | Зубошшевинговальный станок, шевер |
Шлифование | ![]() | Зубошлифовальный станок, тарельчатый шлифовальный круг, профильный шлифовальный круг |
![]() |
Рисунок 1.6- Схема нарезания внутренних профилей долбяками: а- прямозубое колесо, б- косозубое колесо. 1- возвратно-поступательное движение долбяка; 2 и 3 – согласованное движение обката; 4- радиальный отвод инструмента; 5 – радиальное врезание; 6 – доворот долбяка.
Рисунок 1.7- Усложненная конструкция долбяка.
Нарезание внутренних профилей дисковыми и пальцевыми фрезами реализуют на универсальных зубофрезерных станках, имеющих механизм единичного деления и сменную фрезерную головку, устанавливаемую на каретке фрезерного суппорта (рисунок 1.8).
Рисунок 1.8- Фрезерные головки к универсальным зубофрезерным станкам для обработки внутренних зубьев модульными фрезами: а – дисковыми, б – пальцевыми: 1 – фреза; 2 – приспособление на столе; 3 – венец; 4- шпиндель; 5 - фрезерная головка; 6 – суппорт.
Для нарезания применяют специальные фрезы (дисковые и пальцевые) с выпуклым профилем, воспроизводящие внутренний профиль мой детали. Режимы резания применяют такие же, что и при обработке этими же инструментами колес с внешними зубьями, но подачу необходимо уменьшать на 20 – 40% в зависимости от жесткости фрезерной головки [41].
При изготовлении деталей большого диаметра прямые зубья обрабатываются червячными фрезами. Конструкция фрезы может быть цельной- фреза – улитка (рисунок 1.9) и сборной – фреза конструкции ЦНИИТМАШ (рисунок 1.10), устанавливаемы на шпинделе сменной фрезерной головки, предназначенной для работы с дисковыми фрезами; из – за малого угла подъема витка таких фрез поворот оси фрезы не производится [41]. С осевой плоскостью колеса совмещается последний калибрующий зуб фрезы, имеющий форму и размеры впадин обрабатываемого колеса.
Рисунок 1.9- Фреза – улитка:
1- калибрующий зуб; 2 - черновые зубья
Рисунок 1.10- Одновитковая фреза для нарезания колес с внутренними зубьями:
1- корпус; 2 – чистовой (профилирующий) резец; 3- черновой резец
При крупносерийном производстве открытых венцов диаметром 200-300 мм, особенно при отсутствии потребности в точном центрировании внутренних зубьев относительно других поверхностей деталей обработка может производиться протягиванием (рисунок 1.11) [6,41,97].
Протяжки - это многозубые высокопроизводительные инструменты, нашедшие широкое применение в крупносерийном и особенно в массовом производствах. Они относятся к инструментам с конструктивной подачей, так как при протягивании движение подачи отсутствует. Процесс протягивания осуществляется на специальных горизонтальных и вертикальных протяжных станках.
Недостатками данного способа является невозможность обработки мелкомодульных колес, колес малого диаметра.
Зубчатая протяжка имеет центрирующую заднюю часть, базирующую деталь в процессе обработки. Число и количество протяжек в комплекте определяется модулем и материалом колеса. При обработке косых внутренних зубьев применяют косозубые внутренние протяжки, а также используют направляющее винтовое приспособление.
Рисунок 1.11- Схема протягивания зубчатого колеса
Однако у протягивания есть ряд недостатков, к числу которых относятся:
– высокие трудоемкость и стоимость инструмента из-за сложности конструкций протяжек и высоких требований к точности их изготовления;
– протяжки - это специальные инструменты, предназначенные для изготовления деталей только одного типоразмера;
– высокие затраты на переточку, обусловленные сложностью конструкций этих инструментов.
Условия работы зубьев протяжек неблагоприятны для оснащения их твердыми сплавами, так как они снимают тонкие и широкие стружки и работают при низких скоростях резания. Это вызывает колебание силы протягивания и может привести к разрушению твердого сплава. Применение твердых сплавов значительно повышает стоимость протяжек и ограничивается сложностью их изготовления.
Экономическая эффективность применения протяжек достигается лишь в массовом и крупносерийном производствах.
Экономический эффект производства продукции, а конкретно профильного соединения, во многом зависит от целесообразного применения таких составляющих технологического процесса, как методы обработки, оборудование и инструмент. Выбор этих составляющих во многом опирается на тип производства, в котором работает организация. В условиях современной экономики масштаб производства большинства фирм и организаций мелкосерийный. Номенклатура изготовляемых деталей очень разнообразна. Вследствие этого необходимо выбрать инструмент, удовлетворяющий таким условиям, как низкая себестоимость и широкая универсальность.
Наиболее рациональным при таких требованиях является способ зубодолбления, так как он более универсален, один и тот же долбяк может использоваться для нарезания внутренних и внешних профильных соединений. Так же этот способ позволит реализовать принцип единства технологической системы, что сократит погрешность изготовления изделия. Единственный способ, который может составить конкуренцию зубодолблению – протягивание. Однако протяжка- очень дорогой инструмент по сравнению с долбяком и ее применение рационально только в условиях крупносерийного и массового производства. Кроме того, долбяки можно оснащать твердыми сплавами, что позволяет повысить их стойкость и увеличить режимы обработки [76,103]
При проектировании технологического процесса очень важным моментом является выбор оборудования, применяемого при зубодолблении. Станки должны удовлетворять таким требованиям, как: быстрая переналадка, высокая производительность и качество изготовляемых на них деталей и т.д.
Таблица 2- Технические характеристики зубодолбежных станков.
Фирма | Модель | Диаметр обработки, мм | Максимальный модуль, мм | Ширина венца,мм |
Gleason-Pfauter | GP200 ES | 6.0 | ||
GP300 ES | 6.0 | |||
P 600 ES | 6.0 | |||
PSA-120 | 4.0 | |||
Liebherr | LS 82 | 3.0 | ||
LFS 182 | 6.0 | |||
LFS 200 | 12.0 | |||
LFS 282 | 6.0 | |||
LFS 382 | 6.0 | |||
LFS 420 | 6.0 | |||
LCC 150 | 3.0 | |||
Mitsubishi | SN 25A | 6.0 | ||
SE 15A | 4.0 | |||
SE 25A | 6.0 |
Для зубодолбежных станков, фирм Gleason и Liebherr, характерным направления развития является расширение их технологических возможностей путем переноса большей части функций процесса обработки на устройство ЧПУ.
На станке мод. Р600ES фирмы Gleason, например, это реализуется путем использования так называемой электронной винтовой направляющей и разработки совершенно новой конструкции долбежной головки. Кроме того, улучшен отвод стружки через рабочий стол при обработке внутренних зубьев. Хотя станок рассчитан на долбление зубчатых колес (в том числе косозубых с углом наклона ± 450) диаметром до 600 мм и модулем до 6 мм, диапазон обработки по заказу может быть увеличен до 800 мм. Максимальное количество дв.ход./мин. до 800 [82].
Зубодолбёжные станки модели GP200ES и GP300ES с электронной винтовой направляющей созданы на базе всемирно признанных зубодолбёжных станков Gleason-Pfauter. На станках этих моделей применяется зубодолбёжная головка, отличающаяся прямым безлюфтовым приводом шпинделя долбяка. Максимальное число двойных ходов долбяка реализуемое станками - 1000 дв.ход./мин. Система ЧПУ обеспечивает дополнительный поворот долбяка, требуемый для косозубых шестерён, за счёт доворота штосселя долбяка. Все данные по зубонарезанию, оснастке и режимах обработки вводятся с помощью интерактивной системы. Система управления ЧПУ(CNC) рассчитывает все необходимые параметры наладки станка.[42]
В станке мод. PSA 120 фирмы Gleason Pfauter заложена модульная концепция зубофрезерных станков этой фирмы, а также использованы некоторые их узлы, что упрощает эксплуатацию и обслуживание указанного станка. В то же время этот станок обладает рядом конструктивных особенностей, позволяющих добиться его высокой жесткости и точности. Так, стационарный рабочий стол имеет делительный механизм со сдвоенной прецизионной беззазорной червячной передачей с предварительным натягом, а внутри литой станины через 2 камеры производится принудительная циркуляция СОТС, обеспечивающая максимальную тепловую стабилизацию всего станка. Шпиндель долбяка, выполненный на гидростатических опорах, имеет беззазорную делительную передачу со сдвоенным червяком. Управление станком может по выбору осуществляться от 4-координатного УЧПУ фирм Siemens (мод. Sinumerik 840 C) или Fanuc (мод. 160 I-MA), но в любом случае для перемещений по всем осям координат использованы цифровые сервоприводы. При применении станка в крупносерийном производстве для увеличения производительности есть возможность оснащения станка двумя видами загрузочно – разгрузочных устройств – 2-позиционным кольцевым загрузчиком с ориентированной подачей заготовок с накопителем, либо загрузчиком с произвольной подачей заготовок в рабочую зону.[42,82]
Ярким примером реализации современных тенденций в зубообработке являются зубодолбежные станки с ЧПУ немецкой фирмы Liebherr-Verzahntechnik GmbH семейства LFS. Особенность моделей LFS 182, LFS 282 и LFS 382 — возможность позиционирования долбяка в широком диапазоне угловых положений при сохранении длины его осевого перемещения. Это позволяет обрабатывать блочные колеса при неизменном их закреплении и сократить потребность в технологической оснастке. Широкий диапазон линейных перемещений ползуна упрощает замену инструмента. В станках предусмотрено программное управление по 6 осям координат: вращение долбяка и заготовки, радиальное перемещение салазок стойки, регулирование числа двойных ходов салазок долбежной головки, возвратно – поступательное движение шпинделя долбяка и вращение кулачка отвода. При помощи дополнительной специальной оснастки на этих моделях обрабатываются также корончатые зубчатые колеса.
Зубодолбежный станок мод. LFS 200 оснащен управляемой от ЧПУ наклонной стойкой и соответствующим устройством для ее бокового регулирования, что позволяет обрабатывать также конические зацепления, причем не только с охлаждением, но и без него. Количество двойных ходов доходит до 1200.[43]
Станок мод. LFS 420 имеет подвижных салазки долбежной головки, что позволяет значительно расширить его рабочий диапазон в связи с возможностью подвода долбяка в любую позицию и, следовательно, обработки за один установ как многовенцовых зубчатых колес наружного зацепления и внутренних зацеплений без установки дополнительных приспособлений. Это позволяет значительно сократить основные и вспомогательные времена, упростить коррекцию долбяка после каждой его переточки и облегчить его смену оператором. Число двойных ходов долбяка регулируется в пределах до 1200 дв.ход./мин.. Стандартное число осей координат, управляемых от ЧПУ типа CNC фирмы Siemens, составляет 6. Поворотный стол выполнен с бесступенчато регулируемой частотой вращения. Связь между вращением стола с заготовкой и шпинделем долбяка, а также между возвратно-поступательным движением долбяка и его отводом при обратном ходе осуществляется посредством центральной системы ЧПУ. Кроме того, имеется самодиагностика всех важнейших функций управления. При использовании в крупносерийном производстве для повышения производительности 2 станка могут быть соединены между собой транспортером, образуя гибкую производственную ячейку с накопителем заготовок, причем в каждом станке устанавливается в таком случае 4-позиционное карусельное загрузочное устройство.
На станке мод. LS 82, управляемом по пяти осям координат, можно нарезать прямозубые и косозубые зубчатые колеса внутреннего и внешнего зацепления. Его высокая производительность обусловлена количеством двойных ходов долбяка до 2500 дв.ход./мин..
Станок модели SN 25A фирмы Mitsubishi используется запатентованный прецизионный вал балансира (рисунок 1.12). Это максимально предотвращает шум и вибрации станка, возникающие при его работе без использования СОТС. Обработка заготовок производится с бесступенчато регулируемой круговой подачей в пределах от 3 до 5300 мм/мин, радиальной в интервале 0,0012 – 0,1 мм/ход и ускоренной радиальной, равной 10000 мм/мин. Заготовки устанавливают на рабочий стол диаметром 330 мм и обрабатывают долбяком, устанавливаемым на шпинделе диаметром 90 мм и перемещаемым с числом двойных ходов в минуту до 1500 дв.ход./мин. от приводного электродвигателя мощностью 11 кВт. [82]
Рисунок 1.12- Прецизионный вал балансира.
Станки моделей SE 15A и SE 25A для нарезания зубчатых колес внутреннего и внешнего зацепления также используют технологию обработки без СОТС. Их высокая производительность достигается за счет большого числа двойных ходов долбяка- до 2000 дв.ход./мин и 1800 дв.ход./мин соответственно. [45]
Зубофрезерно – долбежный станок COMBI CUT мод. LСС 150 совместно разработанный фирмами Liebherr и Lorenz является примером совмещения технологических операций на одном станке. Применяется для нарезания зубчатых колес максимальным диаметром 150 мм и модулем до 3 мм. Он имеет высокую степень унификации с рядом станков, выпускаемых этими фирмами. От них взяты, например, фрезерная и долбежная головки, причем долбежная головка выполнена на гидростатических опорах, а число ее двойных ходов достигает 3000 дв.ход./мин.. Высокая технологическая гибкость станка достигается путем управления от ЧПУ соотношения между частотой вращения червячной фрезы и заготовки, а также частотой вращения долбяка заготовки и числом двойных ходов долбежной головки на один шаг. Возможность наклона стойки долбяка на 1250 позволяет нарезать широкую номенклатуру прямо- и косозубых (± 300) цилиндрических колес диаметром до 150 мм, модулем до 3 мм и шириной до 23 мм с обычным или конусным зубом. Основная область применения станка – нарезание зубчатых колес с дополнительными соединительными зацеплениями типа муфт. Стойка фрезы (диаметром до 90 мм и длиной до 200 мм) вместе с салазками и фрезерной головкой конструктивно одинакова с соответствующими узлами зубофрезерных станков серии LC фирмы Liebherr. Управление станком осуществляется от контурного микропроцессорного УЧПУ фирмы Siemens с цифровыми приводами, встроенным программируемым контроллером и плоским цветным дисплеем. В число управляемых от ЧПУ девяти осей координат входят следующие: вращение стола с заготовкой; вращение фрезы; тангенциальный сдвиг фрезы; осевое перемещение фрезы; радиальное перемещение фрезы; вращение долбяка; возвратно – поступательное движение долбяка; вращение отводящего кулачка; радиальное перемещение долбяка (стойки). В условиях крупносерийного производства станок оснащают системой автоматической загрузки – разгрузки и накопителем заготовок.[43,82]
Одним из критериев, характеризующим производительность, является основное время нарезания колеса. Было рассчитано теоретическое основное время для нарезания колеса с внутренними зубьями m=2.25, z=27 и шириной зубчатого венца b=15 мм при максимальном количестве двойных ходов долбяка характерному определенной модели станка по методам назначения режимов долбления изложенным в [103]. Данные расчетов представлены в таблице 3.
Таблица 3- Основное время для нарезания колеса с внутренними зубьями m=2,25, z=27, b=50 мм
Фирма | Модель | Максимальное количество дв.ход./мин. | Скорость резания, м/мин | tосн , мин |
Gleason-Pfauter | P 600 ES | 1,91 | ||
GP200 ES | 1,53 | |||
Liebherr | LS 82 | 0,61 | ||
LFS 420 | 1,28 | |||
LCC 150 | 0,51 | |||
Mitsubishi | SN 25A | 1,02 | ||
SE 15A | 0,77 | |||
SE 25A | 0,85 |
Современные зубодолбежные станки разделились на три группы по применяемости СОТС: рассчитанные на работу с применением СОТС, на работу без ее применения и станки, работающие и в том и другом режимах. Приоритетным направлением является сокращение и полный отказ от использования СОТС. Технологические возможности оборудования существенно расширяются за счет увеличения количества управляемых от ЧПУ осей координат.
Из таблицы 3 видно, что имеется тенденция у фирм производителей зубодолбежного оборудования к приближению скорости резания к скорости звука. При значениях скорости резания выше скорости звука наблюдается явление сверхрезания. Материал перестает сопротивляться режущему лезвию. В таком случае силы резания уменьшаются и соответственно уменьшаются погрешности при обработке, повышается производительность оборудования. Так же производительность зубодолбежных станков обеспечивается за счет увеличением круговых подач и обработки в несколько проходов.
Рисунок 2.1- Определение положения впадины колеса с внутренними зубьями 1 относительно зуба долбяка 2.
Взаимосвязь угла и угла положения впадины колеса относительно межосевого расстояния- Ф, выразится соотношением:
(2.2)
где и
- радиусы начальных окружностей долбяка и колеса.
Обозначим через U1, подставим его в выражение (2.2) и затем (2.2) в (2.1), получим:
Уравнение траектории перемещения любой точки внутреннего профиля детли относительно долбяка получим, проектируя отрезки О0О1 и О0N на координатные оси (рисунок 2.1):
(2.3)
где - межосевое расстояние долбяка и детали с внутренним,
- отношение числа зубьев колеса к числу зубьев долбяка,
Ф – угол, определяющий положение впадины колеса относительно межосевого расстояния,
- элементарный угол поворота за время двойного хода долбяка:
, (2.4)
где - окружная подача,
- радиус делительной окружности долбяка,
- радиус – вектор точки на впадине зубчатого колеса с внутренними зубьями;
- угол между радиус – вектором точки впадины зубчатого колеса с внутренними зубьями и осевой линией.
Параметры и
определяются из выражений:
(2.5)
где xi и yi координаты точки профиля впадины зубчатого колеса с внутренними зубьями.
Профиль моментопередающего соединения РК- и К- профиля задается в торцевом сечении. Использование такого задания образующей позволяет находить практически неограниченное количество точек линии контакта инструментальной и номинальной поверхностей. Ввиду особенностей разработанной методики профилирования, каждая кривая образующей линии торцевого сечения профильного моментопередющего соединения РК- и К- профиля, который представляет собой совокупность дуг окружностей, задается системой уравнений в параметрическом виде в декартовой системе координат XOY в параметрическом виде:
;
(2.6)
где ,
- координаты точки профиля впадины зубчатого колеса с внутренними зубьями;
- параметр, определяющий положение точки в торцевом сечении зубчатой поверхности.
Схема построения дуг профиля представлена на рисунке 2.2.
Рисунок 2.2 - Схема построения дуги окружности, составляющей торцевое сечение профильного моентопередающего соединения РК- и К- профиля.
Методика профилирования строится на определении, для каждого участка профиля впадины зубчатого колеса, толщины срезаемого слоя и последующем выборе её значения близкого к нулю. Для каждого положения впадины колеса на определенном элементарном участке исходного профиля впадины точка с толщиной близкой к нулю будет одна. Данную точку условно можно считать принадлежащей и впадине колеса и зубу долбяка, а ее координаты будут являются координатами профиля зуба инструмента.
Рисунок 2.3 Схема определения профильной точки
Определение профильной точки производилось по схеме, представленной на рисунке 2.2. Толщина срезаемого слоя определяется в направлении вектора , перпендикулярного плоскости р,касательной к поверхности резания в точке N. Плоскость р определяется суммарным вектором скорости
и вектором
, направленным вдоль режущей кромки и определяемым, как частные производные от функции перемещения по параметру u.
Вектор скорости в направлении движения резания:
(2.7)
Частные производные по параметру движения резания для дуги окружности:
Вектор скорости перемещения в направлении движения подачи:
(2.8)
- для дуги окружности:
Для вычисления толщины срезаемого слоя необходимо получить уравнение плоскости касательной к поверхности резания- р в точке N. Эта плоскость определяется тремя векторами: вектором касательным к режущей кромке, координаты которого определяются как производные по параметру режущей кромки
координат X,Y,Z математического отображения схемы резания, суммарного вектора
и вектором
.
Частные производные по параметру режущей кромки для дуги окружности:
Угол λ определяется по формуле:
Составив определитель и раскрыв его получаем уравнение плоскости р:
Вектор
, в направлении которого изменяется толщина срезаемого слоя, должен быть перпендикулярен к плоскости p в точке N:
Спроектировав на направление вектора вектор подачи
, получим толщину срезаемого слоя:
,
где - координаты вектора
Рисунок 2.4. Определение положения зуба долбяка относительно впадины колеса с внутренними зубьями.
Взаимосвязь угла положения межосевого расстония и угла положения профиля относительно межосевого расстояния- aw, выразится соотношением:
(2.8)
где и
- радиусы начальных описанных окружностей долбяка и РК- и К- профиля.
Обозначим через U0, подставим его в выражение (2.8), а затем (2.8) подставим в (2.3), получим:
Уравнение траектории перемещения любой точки внутреннего РК- и К- профиля относительно долбяка получим, проектируя отрезки С0С1 и С1B на координатные оси (рисунок 2.5):
;
;(2.9)
.
где -межосевое расстояние долбяка и обрабатываемого колеса,
U0- отношение диаметра описанной окружности долбяка к диаметру описанной окружности профиля детали,
ω - угол, определяющий положение зуба долбяка относительно межосевого расстояния,
Δω - элементарный угол поворота за время двойного хода долбяка,
(2.10)
и
- радиус вектор точки профиля зуба долбяка и угол, определяющий его положение относительно линии симметрии зуба.
Параметры и
определяются из выражений:
(2.11)
где xi и yi - координаты точки профиля зуба долбяка, полученные после профилирования.
В общем виде, для математического отображения схемы обработки внутренних моментопередающих профилей, формулы приобретают вид:
;
; (2.9)
.
Для математического отображения схемы обработки внешних профилей профильных (рисунок 2.5) моментопередающих соединений произведем расчеты в такой же последовательности.
Для получения уравнения траектории перемещения точки при профилировании долбяка проецируем отрезок С0С1, являющийся межосевым расстоянием, на оси X и Y (рисунок 2.3):
(2.7)
где - угол, определяющий положение центра зубчатого колеса относительно долбяка;
- межосевое расстояние зубчатого колеса и долбяка;
Взаимосвязь угла положения межосевого расстояния и угла положения профиля относительно межосевого расстояния - ω, выразится соотношением:
(2.8)
где и
- радиусы описанных окружностей долбяка и внешнего РК- и К- профиля.
Рисунок 2.5. Определение положения зуба долбяка относительно впадины колеса с внутренними зубьями.
Обозначим через U0, подставим его в выражение (2.8), а затем (2.8) подставим в (2.3), получим:
Уравнение траектории перемещения любой точки внешнего РК- и К- профиля относительно долбяка получим, проектируя отрезки С0С1 и С1B на координатные оси (рисунок 2.5):
;
; (2.9)
.
Анализ полученного отображения схемы резания позволяет определять кинематические изменения заднего и переднего углов, угла наклона режущей кромки и толщину срезаемого слоя материала для любой точки профиля и в любой момент, что является основой прогнозирования составляющих силы резания, а впоследствии- износа инструмента, шероховатости поверхности зубчатого венца неэвольвентных колес с внутренними зубьями и точности их обработки.
Рисунок 2.5. Определение составляющих резания.
Силы, действующие на режущие лезвия, определяются по формулам [3]:
(2.15)
(2.16)
где Ф – угол положения зуба долбяка относительно межосевого расстояния;
- угол между радиус-вектором точки бокового режущего лезвия долбяка и линией симметрии зуба;
Используя зависимости (2.12) - (2.16), можно найти составляющие силы резания в любой момент работы зуба долбяка при нарезании впадины колеса для любых начальных параметров - профиля зуба, подачи, чисел зубьев колеса и долбяка. При этом предусматривается визуализация изменения значений сил, действующих на каждое режущее лезвие, как одного зуба долбяка, так и для всех зубьев, находящихся в резании.
Рисунок 2.6. Управление параметрами качества профильными моментопередающими соединениями РК- и К- профиля при зубодолблении.
Алгоритм управляющей программы представлен на рисунках 2.7 и 2.8.
Следствием реализации алгоритма является построение профиля зуба долбяка, определение режимов резания, числа проходов, материала инструмента и модели станка, при которых может быть достигнуты заданные конструкторами машиностроительных производств точностные и качественные характеристики нарезаемых деталей профильных моментопередающих соединений.
Алгоритм управления качеством профильными моментопередающими соединениями РК- и К- при зубодолблении реализуется следующим образом. После ввода исходных данных, таких как, геометрия профильного соединения, начальные режимы обработки, модель станка, материал инструмента, число проходов и т.п. Осуществляется профилирование режущих лезвий долбяка. По предлагаемой методике условным инструментом является обрабатываемая деталь, а заготовкой- долбяк. Из рассчитываемых толщин срезаемого слоя а выбираются и выводятся координаты точек для которых a=0 (блок 3 и 4).
Рисунок 2.7. Алгоритм программы, профилирующей инструмент и управляющей качеством нарезаемых рофильных моментопередающих соединений РК- и К- профиля при зубодолблении (начало).
Рисунок 2.8 Алгоритм программы, профилирующей инструмент и управляющей качеством нарезаемых профильных моментопередающих соединений РК- и К- профиля при зубодолблении. (окончание).
Затем рассчитываются кинематические параметры процесса (угол наклона режущей кромки, кинематические изменения переднего и заднего углов, толщина срезаемого слоя, приходящаяся на элементарный участок режущей кромки, площадь срезаемого слоя и максимально допустимая окружная подача) (блок программы 5). В блоке 6 проходит сравнение предварительно выбранной окружной подачи с максимально допустимой. В блоке 7 окружная подача увеличивается и рассчитываются заново кинематические параметры. В блоке программы 8 определяются динамические параметры процесса, необходимые для расчета точности нарезаемого зубчатого венца. В блоке 9 сравнивается расчетная шероховатость (определяется параметром Rz) с допустимой, т.е. заданной конструктором. Если расчетная больше допустимой, то блок 10 понижает окружную подачу и пересчитывает динамические характеристики. В блоке 11 определяются точностные параметры профильного
Двойное оплодотворение у цветковых растений: Оплодотворение - это процесс слияния мужской и женской половых клеток с образованием зиготы...
Своеобразие русской архитектуры: Основной материал – дерево – быстрота постройки, но недолговечность и необходимость деления...
Наброски и зарисовки растений, плодов, цветов: Освоить конструктивное построение структуры дерева через зарисовки отдельных деревьев, группы деревьев...
История создания датчика движения: Первый прибор для обнаружения движения был изобретен немецким физиком Генрихом Герцем...
© cyberpedia.su 2017-2024 - Не является автором материалов. Исключительное право сохранено за автором текста.
Если вы не хотите, чтобы данный материал был у нас на сайте, перейдите по ссылке: Нарушение авторских прав. Мы поможем в написании вашей работы!