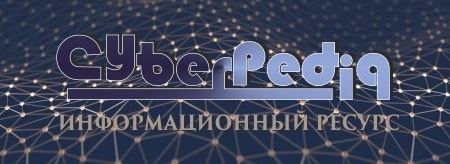
Организация стока поверхностных вод: Наибольшее количество влаги на земном шаре испаряется с поверхности морей и океанов (88‰)...
Поперечные профили набережных и береговой полосы: На городских территориях берегоукрепление проектируют с учетом технических и экономических требований, но особое значение придают эстетическим...
Топ:
Техника безопасности при работе на пароконвектомате: К обслуживанию пароконвектомата допускаются лица, прошедшие технический минимум по эксплуатации оборудования...
Эволюция кровеносной системы позвоночных животных: Биологическая эволюция – необратимый процесс исторического развития живой природы...
Устройство и оснащение процедурного кабинета: Решающая роль в обеспечении правильного лечения пациентов отводится процедурной медсестре...
Интересное:
Наиболее распространенные виды рака: Раковая опухоль — это самостоятельное новообразование, которое может возникнуть и от повышенного давления...
Уполаживание и террасирование склонов: Если глубина оврага более 5 м необходимо устройство берм. Варианты использования оврагов для градостроительных целей...
Как мы говорим и как мы слушаем: общение можно сравнить с огромным зонтиком, под которым скрыто все...
Дисциплины:
![]() |
![]() |
5.00
из
|
Заказать работу |
Основу машиностроения составляют различные соединения, в том числе, кинематические схемы, предназначенные для передачи крутящего момента. Особое место в нем занимают соединения и детали машин, имеющие элементы, в поперечном сечении которых заложен периодический профиль – профильные соединения, зубчатые колеса, муфты и т.п. Обработка такого класса деталей преимущественно осуществляется обкаточным инструментом [4,5,27].
Все соединения в технике разделяются на разъемные, позволяющие осуществлять сборку-разборку механизмов, машин и инструментальных наладок без их разрушения, и неразъемные, к которым относятся заклепочные, сварные, клеевые и т.д. Разъемные соединения делятся на две группы: фрикционные и жесткие.
К фрикционным относятся соединения, выполненные по посадке с натягом, такие как цилиндрические и конические соединения, в которых одна деталь охватывает другую по цилиндрической или конической поверхности, клеммные, с пружинными разжимными кольцами, болтовые соединения.
Соединение с натягом осуществляется подбором соответствующих посадок, в которых натяг создают необходимой разностью посадочных размеров сопряженных деталей. Взаимная неподвижность соединяемых деталей обеспечивается силами трения, возникающими на поверхности контакта деталей.
К жестким соединениям относятся штифтовые, шпоночные, шлицевые и профильные соединения.
Конструкции штифтов многообразны. Известны цилиндрические (а, б), конические (в, г, д), цилиндрические пружинные разрезные (е), просеченные цилиндрические, конические и др. (ж, з, и, к), простые, забиваемые в отверстия (б, в), выбиваемые из сквозных отверстий с другой стороны (гладкие, с насечками и канавками, пружинные, вальцованные из ленты, снабженные резьбой для закрепления или извлечения (д) и т.д. (рис.1.2). Применяются также специальные срезаемые штифты, служащие предохранителями.[9]
При закреплении колес на валу штифты передают как вращающий момент, так и осевое усилие.
Достоинства штифтовых соединений [109]:
- простота конструкции;
- простота монтажа-демонтажа;
- точное центрирование деталей благодаря посадке с натягом;
- работа в роли предохранителя, особенно при креплении колес к валу.
Недостатком штифтовых соединений является сильное ослабление соединяемых деталей отверстием. Проверочные расчеты работоспособности штифтов выполняют на срез и смятие.
Рисунок 1.2 Виды штифтов. Цилиндрические (а, б), конические (в, г, д), цилиндрические пружинные разрезные (е), просеченные цилиндрические, конические (ж, з, и, к)
Различают ненапряженные и напряженные шпоночные соединения. Ненапряженные шпоночные соединения выполняют с помощью призматических и сегментных шпонок. Призматические шпонки (ГОСТ 23360-78) не удерживают детали от осевого смещения вдоль вала. Чтобы застопорить колесо от осевого смещения, применяют распорные втулки или установочные винты. Сегментные шпонки (ГОСТ 24071-91) имеют глубокую посадку и не перекашиваются под нагрузкой, они взаимозаменяемые. Однако глубокий паз существенно ослабляет вал, поэтому сегментные шпонки используют преимущественно для закрепления деталей на малонагруженных участках вала (на входных или выходных хвостовиках валов), что также является существенным недостатком применения данного вида соединений. Клиновые врезные шпонки (ГОСТ 24068-80) создают при запрессовке в паз напряженное соединение по широкому торцу. В клиновых соединениях возможны перекос детали при сборке и биение вследствие радиального смещения (рис.1.3). Поэтому область применения клиновых шпонок также ограничена. Тангенциальные шпонки являются разновидностью клиновых, состоят из двух клиньев с боковыми односторонними скосами. Их забивают в паз, образованный угловыми уступами на валу и ступице. Эти шпонки применяют только в парной установке под углом между парными шпонками α = 135°-180°. Скользящие шпонки (ГОСТ 12208-66) перемещающиеся вдоль вала вместе со ступицей, с которой соединены посредством цилиндрического выступа. Шпонки направляющие (ГОСТ 8790-79), с креплением на валу, применяются при необходимости перемещения ступицы вдоль вала.[109]
Шпоночные соединения имеют следующие преимущества:
ü простота конструкции;
ü удобство в сборке-разборке;
ü дешевизна.
Недостатки шпоночных соединений:
· ослабление сечения валов и ступиц колес;
· снижение нагрузочной способности сопрягаемых деталей;
· значительная концентрация напряжения в углах пазов;
· необходимость подгонки;
· нарушение центрирования колеса на вал.
Шпоночные соединения выходят из строя из-за смятия рабочих граней, а потому, исходя из статистики поломок, расчет на смятие проводится как проектный. По известному диаметру вала задаются стандартным сечением призматической шпонки и рассчитывают ее рабочую длину. Расчет на срез – проверочный. При невыполнении условий прочности увеличивают рабочую длину шпонки, что еще больше ослабляет вал и ответную деталь.
Рисунок 1.3 Типы шпонок: а) призматическая; б) сегментная; в) клиновая; г) тангенциальная; д) цилиндрическая; е) направляющая; ж) скользящая
Шлицевые (зубчатые) соединения подобны шпоночным, у которых зубья (шлицы) изготовлены заодно с валом. Зубья на валу фрезеруют или накатывают, а пазы в отверстиях ступицы получают протягиванием. По сравнению со шпоночными, шлицевые соединения имеют меньшие радиальные габариты, высокую несущую способность, взаимозаменяемы и обеспечивают хорошее центрирование деталей. Благодаря этому их используют в условиях массового производства конструкций и при большей частоте вращения валов. По форме профиля различают шлицевые соединения трех типов (рис.1.4) [3,9,109]:
- прямобочные (а), получившие наибольшее распространение в машиностроении, размеры которых стандартизованы по ГОСТ 1139-80;
- эвольвентные (б), отличающиеся от прямобочных более совершенной технологией изготовления, повышенной прочностью и точностью центрирования. Размеры стандартизованы по ГОСТ 6033-80;
- треугольные (в). Применяются для неподвижных соединений при небольших нагрузках, на тонкостенных деталях и т.п.
Допуски и посадки шлицевых соединений с прямобочным профилем устанавливаются по ГОСТ 1139-80. Условное обозначение содержит букву, обозначающую центрирующую поверхность – D, d или b, число зубьев z, номинальные значения размеров D, d и b, обозначение посадок диаметров размера b, помещенные после соответствующего размера.
Рисунок 1.4 Виды шлицев:
а) прямобочные, б) эвольвентные, в) треугольные
Соединения с прямобочными зубьями широко распространены в машиностроении. В зависимости от числа зубьев (z = 6-20) и их высоты стандартом предусмотрены три серии соединений валов с диаметром от 23 до 125 мм (легкая, средняя и тяжелая). Большее число зубьев имеют соединения тяжелой серии. При необходимости точной соосности вала и ступицы центрирование производят по одному из диаметров, например, отверстие обрабатывают протягиванием, а вал – круглым шлифованием. Недостатком шлицевых соединений являются: высокая стоимость изготовления, шумность механизмов с применением данного типа соединений ввиду неизбежности циклического трения скольжения, вызываемого неточностью обработки шлицев, дороговизна обработки, необходимость применения специального фасонного инструмента. Соединения с треугольными зубьями применяют преимущественно в приборостроении при ограниченных радиальных габаритах [3,9,109].
По сравнению со шпоночными, шлицевые соединения:
ü имеют большую несущую способность;
ü лучше центрируют колесо на валу;
ü усиливают сечение вала за счет большего момента инерции ребристого сечения по сравнению с круглым;
Однако, ограничивающими факторами при их применении, служат следующие имеющиеся недостатки:
· необходимость в специальном оборудовании для изготовления отверстий;
· высокая стоимость изготовления;
· значительная концентрация напряжения в углах пазов;
· относительная неравномерность распределения нагрузки;
· сильная деформация после термической обработки;
· шумность работы шлицевых соединений.
Основными критериями работоспособности шлицев являются сопротивление боковых поверхностей смятию (расчет аналогичен шпонкам) и сопротивление износу при фреттинг-коррозии (малые взаимные вибрационные перемещения в локальной зоне). Смятие и износ связаны с одним параметром – контактным напряжением.
В настоящее время все более широкое распространение находят профильные моментопередающие соединения, также называемые в некоторых источниках как бесшпоночные. Кривые, описывающие профильные соединения могут описываться разными законами. Самыми простыми из них являются соединения в виде прямобочных правильных фигур и эллиптические, несколько более сложные контура выполняются трохоидальными, синусоидальными и в виде треугольника Рело, и т.п..
Согласно классификации, приведенной в работах Тимченко А.И. [106] и руководящем документе [85], профильные соединения можно подразделить на непрерывные контурные (рис.1.5, а) и срезанные (рис.Рисунок 1.5, б). При этом каждый из них также делится на два подвида. Первый подвид – профильный равноосный контур, т.е. с нечетным числом граней (РК-1, РК-3 и т.д.) и нечетным числом граней (К-2, К-4 и т.д.). Ко второму подвиду относятся профильные кривые со срезанными вершинами (КС-1, КС-2, КС-3 и т.д.). Также в машиностроении известны так называемые трефовые соединения. Распределение напряжений для такого вида соединений более благоприятны. По своей сути они представляют собой укрупненные шлицы трапецеидального профиля [110].
В отечественном и зарубежном машиностроении наибольшее распространение получили контурные кривые на основе трехгранного (РК-3) и срезанного (КС-3), четырьмя и пятью гранями. К сожалению, единого стандарта на территории Российской Федерации на профильные бесшпоночные соединения отсутствует, существуют лишь предпосылки для создания ГОСТов [85].
В германии основным регламентирующим документом на профильные бесшпоночные соединения являются DIN 32711 и DIN 32712.
Установлено, что прямобочный шлицевый вал выдерживает циклическую нагрузку с напряжением σ=30 кг/мм2 – 15000 циклов, а профильный вал с тремя гранями при этом же диаметре и той же нагрузке выдерживает 70000 циклов, т.е. прочность профильного вала в 4,67 раза больше шлицевого [59].
Рисунок 1.5 Виды профильных соединений по РД23.800.2.02-89:
а) непрерывные типа РК и К; б) срезанные типа КС
В работе [106] было произведено сравнение геометрических и эксплуатационных параметров различных валов относительно вала со шпоночным пазом. Так профильные соединения по сравнению со шлицевыми и шпоночными имеют ряд преимуществ. Основными из них являются:
ü сопротивление усталости профильного вала до 5 раз выше, чем у шлицевого;
ü способность профильных валов передавать крутящий момент в несколько раз выше по сравнению со шлицевыми валами;
ü равноосноконтурные профильные соединения с тремя осями симметрии обладают свойством автоматического центрирования;
ü приработочный износ деталей с профильными соединениями трех равных осей, меньше в 2,5-3 раза;
ü пониженный шум;
ü масса деталей с профильными поверхностями может быть уменьшена по сравнению со шлицевыми и шпоночными при тех же передаваемых усилиях;
ü симметричное распределение нагрузки в сечении;
ü большая контактная площадь;
ü стоимость обработки профильных соединений сравнима, либо дешевле по сравнению со шлицевыми.
Тем не менее, широкого распространения в отечественном машиностроении на данный момент такой тип соединений не нашел. При лучших качественных показателях данных валов, их производство считается не технологичным. Анализ литературных источников и патентный поиск методов формообразования выявил наиболее приемлемые способы получения профильных валов. Изготовление данного вида деталей возможно при помощи создания профильной фрезы; на станках с ЧПУ; при помощи полигонального точения.
Сборные фасонные фрезы имеют преимущество в возможности многоразового использования корпуса после замены изношенных режущих элементов, однако его производство затратное, а производимые расчеты для определения ориентации сменных пластин на корпусе фрезы сложны и объемны. После установки сменных режущих пластин может возникнуть необходимость в заточке, с целью корректировки общей формообразующей линии фрезы, также требующей специальных расчетов и оборудования, что в условиях эксплуатации заводом-потребителем режущего инструмента не всегда возможно, в отличие от специализированного инструментального производства.
Долбление, наряду с обработкой фрезерованием, является одним из наиболее распространенных и производительных процессов резания в отечественном машиностроении. Применяемые при этом конструкции инструмента для данного металлообрабатывающего парка станков являются точными, метод производительным, а операции, выполняемые на станках зачастую единственно возможными для данного вида детали, либо в условиях конкретного производства.
Полигональное точение обеспечивает изготовление только деталей валов профильных соединений на основе правильных прямобочных n -гранных фигур (квадрат, шестигранник и т.д.), либо с нечетным числом, но при более сложном согласовании движений обрабатываемой детали и режущего инструмента, кроме того, для осуществления полигонального точения необходимо дооснащение станка дополнительным оборудованием, либо наличие станков с ЧПУ, что также ограничивает применение данного способа.
При обработке точных поверхностей возникает необходимость в обеспечении жесткости системы СПИД. Одним из факторов влияющих на ее жесткость, является наличие в системе дополнительных связей. Таким образом, чем меньшее количество приспособлений имеется на станке, тем жестче кинематика цепочки станок-приспособление. При проектировании инструментального обеспечения не маловажную роль играет сборная или монолитная конструкция применяется при обработке. Данный аспект обеспечивает кинематику инструмент-деталь. Соответственно, чем инструмент проще и жестче, тем более точной будет обработка.
Архитектура электронного правительства: Единая архитектура – это методологический подход при создании системы управления государства, который строится...
Опора деревянной одностоечной и способы укрепление угловых опор: Опоры ВЛ - конструкции, предназначенные для поддерживания проводов на необходимой высоте над землей, водой...
История развития хранилищ для нефти: Первые склады нефти появились в XVII веке. Они представляли собой землянные ямы-амбара глубиной 4…5 м...
Автоматическое растормаживание колес: Тормозные устройства колес предназначены для уменьшения длины пробега и улучшения маневрирования ВС при...
© cyberpedia.su 2017-2024 - Не является автором материалов. Исключительное право сохранено за автором текста.
Если вы не хотите, чтобы данный материал был у нас на сайте, перейдите по ссылке: Нарушение авторских прав. Мы поможем в написании вашей работы!