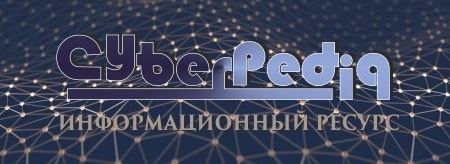
Состав сооружений: решетки и песколовки: Решетки – это первое устройство в схеме очистных сооружений. Они представляют...
Папиллярные узоры пальцев рук - маркер спортивных способностей: дерматоглифические признаки формируются на 3-5 месяце беременности, не изменяются в течение жизни...
Топ:
Характеристика АТП и сварочно-жестяницкого участка: Транспорт в настоящее время является одной из важнейших отраслей народного...
Выпускная квалификационная работа: Основная часть ВКР, как правило, состоит из двух-трех глав, каждая из которых, в свою очередь...
Теоретическая значимость работы: Описание теоретической значимости (ценности) результатов исследования должно присутствовать во введении...
Интересное:
Наиболее распространенные виды рака: Раковая опухоль — это самостоятельное новообразование, которое может возникнуть и от повышенного давления...
Принципы управления денежными потоками: одним из методов контроля за состоянием денежной наличности является...
Инженерная защита территорий, зданий и сооружений от опасных геологических процессов: Изучение оползневых явлений, оценка устойчивости склонов и проектирование противооползневых сооружений — актуальнейшие задачи, стоящие перед отечественными...
Дисциплины:
![]() |
![]() |
5.00
из
|
Заказать работу |
|
|
Процессы измельчения условно подразделяют на дробление (крупное, среднее, мелкое) и измельчение (тонкое, сверхтонкое). Измельчение материала осуществляется путем раздавливания, раскалывания, стирания в ударах. В большинстве случаев эти виды воздействия на материал используют комбинированно, при этом обычно основное значение имеет один из них, что обусловлено конструкцией машины, применяемой для измельчения.
Дробление материала обычно осуществляется сухим образом, тонкое измельчение чаще проводят влажным методом. Результат измельчения часто характеризуют степенью измельчения, равную отношению среднего характерного размера куска D материала, до измельчения среднему, характерному размеру d куска после измельчения. I = D /d
Характерным линейным размером куска шарообразной формы является диаметр, куска кубической формы – длина ребра. Характерный минимальный размер кусков неправильной геометрической формы может быть найден как средняя величина.
dx = 3√(ℓbh), где
ℓ, b, h – максимальные размеры куска по трем взаимным перпендикулярным направлениям. Наибольший из этих размеров ℓ (длина), средний – b (ширина), наименьший – h (толщина).
Для расчета средних характерных размеров кусков материала с помощью нескольких наборов сит, для кусков материала на несколько фракций:
dcp = (dmax + dmin) /2
Средний характерный размер куска смеси вычисляют по уравнению:
где
dcp1,2,3… - средние размеры частиц каждой фракции,
а1,2,3…- содержание в каждой фракции в весовых процентах.
По своему назначению измельчающие машины условно делятся на дробилки (крупного, среднего, мелкого дробления) и мельницы (тонкого, сверхтонкого измельчения). По основному способу механического воздействия на материал измельчающие материалы можно разделить на следующие основные группы:
|
1. раскалывающие машины,
2. раздавливающие,
3. истирающее – раздавливающие,
4. ударные,
5. ударно – истирающие.
Дробление и особенно измельчение – весьма энергоемкие операции, поэтому необходимо стремиться к уменьшению массы перерабатываемого материала. Целесообразно перед измельчающей машиной выделить куски мельче того размера, до которого производится измельчение на данной стадии.
Крупное дробление.
Рассмотрим щековые дробилки.
1,2 – неподвижная и подвижная щеки,
3 – эксцентриковый интервал,
4 – шатун,
5,6 – распорные плиты.
В щековой дробилке материал измельчается путем раздавливания в сочетании с раскалыванием между неподвижной и подвижной щеками. Подвижная щека приближается при рабочем ходе или отходит при холостом ходе от неподвижной щеки при вращении эксцентрикового вала. Во время рабочего хода происходит дробление, а во время холостого – выгрузка дробленого материала под действием собственного материала.
Различают щековые дробилки с нижним и верхним подвесом щеки. Преимущества: простота и надежность, широкое применение, компактность и легкость обслуживания. Недостатки: периодический характер дробящего усилия, отсюда возникает вибрация и возможность сбивания рабочего пространства.
Конусные дробилки.
1 – подвижный конус,
2 – неподвижный конус,
3 – эксцентриковый вал.
Крупное дробление в конусных дробилках осуществляется в эксцентриковых дробилках, где конус вращается вокруг неподвижной оси с валом, расположенной на конической шестерне (ее нет). Среднее и мелкое дробление в конусных дробилках с верхним подвесом. Преимущества: большая производительность, уравновешенная работа, высокая степень измельчения. Недостатки: очень сложная конструкция, дороговизна, большая высота, сложность обслуживания.
|
Среднее и мелкое дробление.
1. Волоковая дробилка
1 – неподвижный волок
2 – подвижный волок
Измельчение производится путем раздавливания между двумя волоками. Привод осуществляется на каждый волок. Дробилки могут различаться по количеству, форме и скорости волоков. Также могут быть зубчатые волоки. При различной скорости волоков усиливаются стирающие действия.
2. Ударно – центробежные дробилки
Молотковая дробилка
1 – корпус
2 – отбойная плита
3 – диск
4 – молотки
5 – колосниковая решетка
Преимущества: высокая степень измельчения. Недостатки: значительный износ плит и молотков, сложность балансировки ротора.
3. Отражательная дробилка
1 – колосниковая решетка
2 – ротор
3 – лопатки
4 – щитки
Материал, проходя через решетку, поступает на ротор, обращающийся с окружной скоростью. С помощью лопаток куски отбрасываются на щитки, и измельчение происходит при ударе лопаток и кусков о щитки. Преимущества: высокая степень измельчения, высокая однородность продукта. Недостатки: износ лопаток и щитков.
Тонкое измельчение.
Барабанные мельницы
Измельчение происходит внутри измельчающего барабана под действием мелющих тел. Мелющие тела – шары или стержни – не применяют. Мелющие тела под воздействием центробежных сил и сил трения увлекаются вместе с движущейся стенкой на определенную высоту, а затем падают и измельчают материал ударами, истиранием, раздавливанием. Измельчение проводят как мокрым, так и сухим методом. Преимущества: универсальность, постоянство скорости вращения, надежность и простота обслуживания. Недостатки: износ мелющих тел, загрязнение продуктов, шум.
*. Сверхтонкое измельчение
При сверхтонком измельчении материала разрушение происходит не по поверхности трещин, пересекающих всю толщу частиц, а главным образом путем «отшелушивания» (усталостного разрушения) вследствие поверхностной трещиноватости измельчаемых частиц. Наиболее эффективно и с наименьшими затратами энергии сверхтонкое измельчение осуществляется при высокочастотном воздействии на материал посредством сравнительно слабых ударов. Часто повторяющиеся, но относительно слабые воздействия на материал могут быть получены в мельницах с минимальной массой мелющих тел или без них.
Сверхтонкое измельчение производят в вибрационных, струйных и коллоидных мельницах, в которых частицы материала измельчаются ≈ от 10 – 0,1 мм до 75*10-5 – 1*10-4 мм.
|
Вибрационная мельница
представляет собой цилиндрический или корытообразный корпус – 1, примерно на 80 % своего объема загруженный шарами (иногда стержнями) – 2. Корпус приводится в колебательные движения валом – 3, снабженным дебалансом (в мельницах инерционного типа) или эксцентриковым валом (в гравитационных мельницах). При вращении неуравновешенной массы вала (вибратора) – 3 со скоростью от 1000 до 3000 мин-1 корпус – 1 с шарами в нем и измельчаемым материалом совершает качательное движение по элептической траектории в плоскости, перпендикулярной оси вибратора. Мелющие тела при этом вращаются вокруг собственной оси, а все содержимое корпуса приводится в планетарное движение в сторону обратную направлению вибратора. Материал интенсивно измельчается под действием частых соударений мелющих тел и истиранием. Корпус установлен на пружинящие опоры – 4 и деревянные подкладки, предотвращающие передачу вибраций основанию мельницы. Вибрационные мельницы используют для сухого и мокрого измельчения периодического и непрерывного действия.
Схема струйной мельницы с трубчатой камерой:
1 – трубчатый контур, в нижнюю часть которого через систему сопел – 2 поступает энергоноситель. Материал на измельчение подается таким образом, чтобы каждая пара струй пересекалась в вертикальной плоскости на некотором расстоянии от противоположной стенки трубы. Материал измельчается при многократных соударениях частиц в точках пересечения струй и в общем вихревом потоке. Разделение измельченного материала по крупности частиц происходит в поле центробежных сил при поворотах потока в коленах 4 и 5 трубы. Крупные части отбрасываются к внешней стенке и вновь попадают в зону измельчения. Мелкие движутся у внутренней стенки трубы, выходят вместе с энергоносителем через жалюзи – 6 инерционного пылеразделителя в трубу -7 и далее во внешнюю систему улавливания (циклоны и матерчатый фильтр).
Достоинства струйных мельниц: высокая энергонапряженность и эффективность измельчения, отсутствие вращающихся деталей и мелющих тел, возможность сочетания помола и классификации с сушкой, окислением, восстановлением и т.д.
|
Недостатки: большой расход энергоносителя, высокая энергоемкость.
Коллоидные мельницы. В коллоидных мельницах, применяемых в основном для мокрого сверхтонкого измельчения, материал измельчается в весьма малом (до 0,05 мм) зазоре между быстро вращающимися (ω до 100 м/сек) дисковым ротором и неподвижным корпусом (статором). В вихревом потоке, образующемся в этом зазоре, частицы материала вращаются вокруг собственных осей с такими скоростями, что центробежные силы разрывают их.
|
|
Историки об Елизавете Петровне: Елизавета попала между двумя встречными культурными течениями, воспитывалась среди новых европейских веяний и преданий...
Археология об основании Рима: Новые раскопки проясняют и такой острый дискуссионный вопрос, как дата самого возникновения Рима...
Семя – орган полового размножения и расселения растений: наружи у семян имеется плотный покров – кожура...
Особенности сооружения опор в сложных условиях: Сооружение ВЛ в районах с суровыми климатическими и тяжелыми геологическими условиями...
© cyberpedia.su 2017-2024 - Не является автором материалов. Исключительное право сохранено за автором текста.
Если вы не хотите, чтобы данный материал был у нас на сайте, перейдите по ссылке: Нарушение авторских прав. Мы поможем в написании вашей работы!