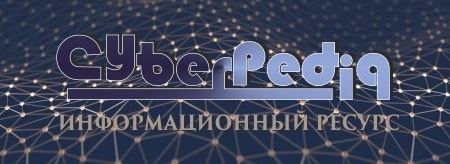
Эмиссия газов от очистных сооружений канализации: В последние годы внимание мирового сообщества сосредоточено на экологических проблемах...
Папиллярные узоры пальцев рук - маркер спортивных способностей: дерматоглифические признаки формируются на 3-5 месяце беременности, не изменяются в течение жизни...
Топ:
Комплексной системы оценки состояния охраны труда на производственном объекте (КСОТ-П): Цели и задачи Комплексной системы оценки состояния охраны труда и определению факторов рисков по охране труда...
Отражение на счетах бухгалтерского учета процесса приобретения: Процесс заготовления представляет систему экономических событий, включающих приобретение организацией у поставщиков сырья...
Установка замедленного коксования: Чем выше температура и ниже давление, тем место разрыва углеродной цепи всё больше смещается к её концу и значительно возрастает...
Интересное:
Уполаживание и террасирование склонов: Если глубина оврага более 5 м необходимо устройство берм. Варианты использования оврагов для градостроительных целей...
Подходы к решению темы фильма: Существует три основных типа исторического фильма, имеющих между собой много общего...
Средства для ингаляционного наркоза: Наркоз наступает в результате вдыхания (ингаляции) средств, которое осуществляют или с помощью маски...
Дисциплины:
![]() |
![]() |
5.00
из
|
Заказать работу |
|
|
Установка для охлаждения творога состоит из рамы 1, на которой монтируется корпус 2 со шнековым питателем 3, предназначенным для транспортирования продукта во время охлаждения, и нагнетательным патрубком 4.
Для создания достаточного для формования творожных брикетов давления в нагнетательной части витки шнекового питателя выполнены с убывающим шагом, в 4 раза меньше, чем шаг витков шнека в средней части корпуса.
На корпус 2 охладителя в средней его части монтируется вакуумная камера 5 с патрубком 6 для отвода парогазовой смеси.
Система создания и поддержания вакуума включает в себя вакуумный насос, конденсатор паров, запорную арматуру, а также датчики контроля давления в системе. Для приема творога, поступающего на охлаждение, предусмотрен загрузочный бункер 7. Вращение шнековому питателю 3 передается от электродвигателя 8 через редуктор 9 и цепную передачу 10.
Установка для охлаждения творога работает следующим образом.
Продукт, поступающий, например, из непрерывно действующего обезвоживателя барабанного типа, которым комплектуется комплексно-механизированная линия, попадает в загрузочный бункер 7 установки для охлаждения творога.
Изм. |
Лист |
№ докум. |
Подп. |
Дата |
Лис т |
9 |
ВКР-15.03.02-01-2022-О.Т.А-00.00.000 ПЗ |
|
Скорость движения творога в охладителе задается в зависимости от температуры поступающего на охлаждения продукта, его влажности и других технологических параметров.
При продвижении творога в установке с шагом шнекового питателя, в средней части, превышающим шаг витков со стороны загрузочного бункера в два раза, а со стороны разгрузочного патрубка в четыре раза, происходит уплотнение продукта и создается избыточное давление в нагнетательном патрубке 4, достаточное для нагнетания продукта в сваренную трубчатую оболочку из ленты типа сарана..
Натекание в вакуумную камеру не происходит, так как творог, обладая достаточной пористостью, под действием разности давлений и силы тяжести (в приемном бункере) наполняет все имеющиеся поры к неплотности в продукте.
По окончании работы установки осуществляется циркуляционная мойка. Для ее проведения в корпус установки для охлаждения творога устанавливают съемную моющую головку известной конструкции. Предварительно корпус освобождается от шнекового питателя, который изготавливается съемным для более полной санитарно-гигиенической обработки аппарата.
Изм. |
Лист |
№ докум. |
Подп. |
Дата |
Лис т |
27 |
КП-15.03.02-01-2021-О.Т.А-00.00.000 ПЗ 00 ПЗ |
Таблица 2.1-Технические характеристика закрытого охладителя творога.
Производительность, кг/ч | 800 |
Поверхность охлаждения, м2 | 3,7 |
Частота вращения вытеснительного барабана, c-1 | 0,49 |
Температура, 0C: | |
творога на входе | 28…30 |
творога на выходе | 8…10 |
хладагента | Не более 1 |
Расход хладагента, м3/ч | 9 |
Габаритные размеры, мм | 2060*970*2000 |
Масса, кг | 740 |
Изм. |
Лис т |
№ докум. |
Подп. |
Дата |
Лист |
8 |
ВКР-15.03.02-01-2022-О.Т.А-00.00.000 ПЗ |
Разраб. |
Алексеев Д.С. |
Пров. |
Панфилов В.А |
Реценз. |
Н. контр. |
Панфилов В.А. |
Утверд. |
Бредихин С.А. |
СОДЕРЖАНИЕ |
Лит. |
Листов |
1 |
РГАУ-МСХА имени К.А. Тимирязева. Кафедра ПАПП. 406 Д-Т |
|
Расчет производительности закрытого охладителя творога.
Технологический расчет.
Пропускная способность охладителя закрытого одноцилиндрового G (кг/ч):
G = ) = 3,14*0,4*0,047*1 *1050(0,1722-0,1682)*3600= 893 кг/ч
где S – шаг шнека, S = 0,12 м;
n –частота вращения шнека, n = 0,047 c-1;
– коэффициент уменьшения площади свободного прохода,
– коэффициент объемного перемещения (для охладителя закрытого одноцилиндрового
= 0,4);
– плотность продукта,
1050 кг/м3;
R 2 – внутренний радиус рабочего цилиндра, R 2 = 0,172 м;
R 1 – наружный радиус вытеснительного барабана, R 1 = 0,168 м;
= 1- b/ π(R 2- R 1)cosαc = 1- 0,018/3.14(0.172-0.168) cos450 = 1
где b – толщина витка шнека b = 0,018 м;
αc – среднее значение угла наклона витков шнека, αc = 45 град.
Производительность закрытого одноцилиндрового охладителя П (кг/ч):
П= kF [ c (t 1- t 2)
] = 40*3,7
[2,205(302-282)1,2] =800 кг/ч
где k – коэффициент теплопередачи, k = 40 Вт/(м2*К);
F – площадь поверхности теплопередачи, F =3,7 м2;
t 1и t 2 – температура продукта в начале охлаждения и в конце, t 1= 302 К t 2 = 282 К;
– тепловой КПД,
= 1,1…1,2.
с – удельная теплоемкость продукта, c = 2,205 Дж/(кг*К).
Площадь поверхности теплопередачи:
F = =
= 3,7 м2
где Q – тепловая нагрузка аппарата (определяется из теплового баланса);
– средняя разность между температурами продукта и теплоносителя, 286 К;
Конструктивный расчет.
Ширина теплообменника b (мм):
b = b э+20= 650+20 = 670мм
где b э = эффективная ширина теплообменнника
Изм. |
Лист |
№ докум. |
Подп. |
Дата |
Лис т |
9 |
ВКР-15.03.02-01-2022-О.Т.А-00.00.000 ПЗ |
b = D = 670 мм
Внутренний радиус r (мм).
Каждый полувиток спирали строится по радиусам r 1 и r 2, которые для первых витков равны.
r 1 = =
=247,5 мм
r 2 = + S 1 =
+ 85 = 332,5 мм
где d — диаметр первого витка внутренней спирали; м
S 1 - шаг спирали со стороны загрузки, мм.
Внутренний диаметр d (мм):
d = 2 r + S = 2*247,5 = 495
Ширина керна (мм):
h= 2*247,5=495мм
Шаг спирали (мм):
S 1 = b 1 + δ 1 = 50+35 =85 мм
S 2 = S 1*2 = 85*2 = 170 мм
S 3 = S 2 / 4 =170 / 4 = 42.5 мм
где b = 50 мм; σ = 30 мм
|
Длина спирали при числе витков n равна:
l 0 = π (d - S ср ) n + 2 Sπn 2 = 3,14(495-99,2) = 1250 мм
где n – число витков, n = 18;
S ср – средний шаг спирали, мм:
S ср = =
= 99,2 мм
Теплотехнический расчет.
Расход холода на охлаждение творога Ф (Вт) определяют по уравнению:
Ф = Ф 1 +Ф 2+ Ф 3 = 39381+3920+4704 = 48005 Вт
где Ф 1 – количество холода, необходимое для охлаждения творога, Вт;
Ф 2 – количество холода, необходимое для компенсации теплоты, выделяемой в результате механического воздействия на творог (только для закрытых охладителей), Вт;
Ф 3 – теплопотери, Вт;
Изм. |
Лист |
№ докум. |
Подп. |
Дата |
Лис т |
9 |
ВКР-15.03.02-01-2022-О.Т.А-00.00.000 ПЗ |
Ф 1 = Gc (t 1- t 2) = 893*2.205(29-9) = 39381 Вт
где G – пропускная способность охладителя, G = 893 кг/ч;
с – теплоемкость творога, Дж/(кг*К);
t 1 – температура творога на входе, t 1 = 29 0C;
C – температура творога на выходе, t 2 = 9 0C.
Ф 2 = А N = 0,981*4*1000 =3920 Вт
где А – тепловой эквивалент работы, A =0,981 H*м/Дж;
N – мощность, расходуемая на охлаждение творога при его перемещении вдоль цилиндра, = 4 кВт.
Если потери теплоты в окружающую среду учесть коэффициентом тепловых потерь ( = 1,1…1,2), то
Ф = (Ф 1 +Ф 2) = (39381+3920)*1.2 = 51962 Вт
Расход хладоносителя (кг/ч) можно определить по формуле:
Gx = Q/[cх(t х1 - t х2)]= 35280/[1527(273,15 - 136,58)] = 170 кг/ч
где cх – теплоемкость хладоносителя, cх = 1527 Дж/(кг*К);
t х1, t х2 – начальная и конечная температуры хладоносителя, t х1 = 273,15 К, t х2 = 136,58 К;
Q – количество холода, необходимое для охлаждения творога.
Q = П* c (t 1 – t 2) = 800*2.205(302-282) = 35280 Дж
Расчет шнека на прочность.
Рисунок 3.4.1. Расчётная схема нагружения шнека и его опор.
Максимальные касательные напряжения τmax на поверхности шнека, Н/м2:
τmax = =
= 1,92 Н/м2
Изм. |
Лист |
№ докум. |
Подп. |
Дата |
Лис т |
9 |
ВКР-15.03.02-01-2022-О.Т.А-00.00.000 ПЗ |
W p = (1− α4) =
(1− 0,744) =26424,285 м
α= =
= 0,74
Окончательно имеем:
τmax = , н/м2
Крутящий момент M кр, действующий на шнек, Н⋅м,
M кр = 573 = 573
= 50752,5 Н*м
где Ф = Ф 1 + Ф 2 = 39381+3920 = 43401 Вт – мощность, затрачиваемая на продвижение материала по каналу шнека;
|
n – частота вращения шнека, n = 0,49 с.
Нормальные напряжения вызываются осевой силой S ос и распределённой нагрузкой q. Максимальные напряжения будут возникать в месте закрепления шнека (у первого подшипника):
σmax = =
=727,2 Н/м2
где W н.о – осевой момент сопротивления относительно нейтральной оси, м3;
M и max – максимальный изгибающий момент от распределённой нагрузки шнека,Н⋅м:
M и max = =
= 13827762 H*м
где γ = 7850*9,81 = 77008,5 Н/м;
ρ – плотность материала шнека, ρ = 7850 кг/м3;
g = 9,81 – ускорение свободного падения, м/с2;
L – длина шнека, L = 1,525 м
F – площадь поперечного сечения шнека, м2.
С учётом значения площади поперечного сечения шнека:
F = (1−α2) =
(1−0,742) = 154,42 м
изгибающий момент будет равен:
M и = (1−α2) =
(1−0,742) =2204417 Н*м
Осевой момент сопротивления относительно нейтральной оси:
W н.о = (1−α4) =
(1−0,744) = 20662,62 м
Изм. |
Лист |
№ докум. |
Подп. |
Дата |
Лис т |
9 |
ВКР-15.03.02-01-2022-О.Т.А-00.00.000 ПЗ |
σmax = , Н/м2
Максимальное давление, развиваемое шнеком (Р max). Максимальное давление развивается шнеком, когда отверстие в головке закрыто и нет выхода материала из машины (производительность равна нулю):
0
откуда
P max = =
= 4,81 МПа
где µср – средняя по длине шнека вязкость перерабатываемого материала, МПа*с;
αi = 0,65 м3 и βi = 0,0000381 м3– постоянные прямого и обратного потоков для шнеков с постоянной или переменной глубиной нарезки в зоне дозирования или переменным шагом;
F α и F β – коэффициенты формы прямого и обратного потоков (при переработке термопластичных материалов принимают F α = F β = 1).
Значение средней вязкости материала µср определяют из следующего
соотношения:
Q = αi* F α* n - βi* F β
где Q – производительность машины;
∆ P общ – перепад давления в головке, ∆ P общ = 10 МПа.
Откуда
µср = =
= 0,000058 МПа*с
Максимальное осевое усилие, действующее на шнек,
S ос = P max F = 0,000058 *106*154,42 = 8956,4
Условие прочности шнека по третьей теории прочности:
σp = ≤ [σ]
σp = = 730 Н/м2
где [σ] = 540…790 Н/м2 – допускаемое для материала и заданных условий его работы напряжение.
Условие прочности выполнено.
Изм. |
Лист |
№ докум. |
Подп. |
Дата |
Лис т |
9 |
ВКР-15.03.02-01-2022-О.Т.А-00.00.000 ПЗ |
Крутящий момент на валу рабочего органа Tр = 179 Hм
Номинальная мощность электродвигателя, Pдв = 4 кВт,
Частота вращения электродвигателя, nдв = мин-1,
Частота вращения рабочего органа, nр = 140 мин-1.
Максимальное время работы электродвигателя L = 10 000 ч
|
|
Механическое удерживание земляных масс: Механическое удерживание земляных масс на склоне обеспечивают контрфорсными сооружениями различных конструкций...
Биохимия спиртового брожения: Основу технологии получения пива составляет спиртовое брожение, - при котором сахар превращается...
Опора деревянной одностоечной и способы укрепление угловых опор: Опоры ВЛ - конструкции, предназначенные для поддерживания проводов на необходимой высоте над землей, водой...
Кормораздатчик мобильный электрифицированный: схема и процесс работы устройства...
© cyberpedia.su 2017-2024 - Не является автором материалов. Исключительное право сохранено за автором текста.
Если вы не хотите, чтобы данный материал был у нас на сайте, перейдите по ссылке: Нарушение авторских прав. Мы поможем в написании вашей работы!