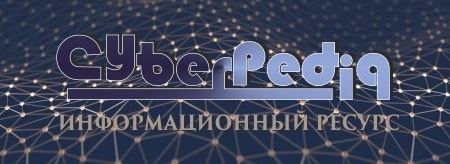
Эмиссия газов от очистных сооружений канализации: В последние годы внимание мирового сообщества сосредоточено на экологических проблемах...
Общие условия выбора системы дренажа: Система дренажа выбирается в зависимости от характера защищаемого...
Топ:
Определение места расположения распределительного центра: Фирма реализует продукцию на рынках сбыта и имеет постоянных поставщиков в разных регионах. Увеличение объема продаж...
Теоретическая значимость работы: Описание теоретической значимости (ценности) результатов исследования должно присутствовать во введении...
Выпускная квалификационная работа: Основная часть ВКР, как правило, состоит из двух-трех глав, каждая из которых, в свою очередь...
Интересное:
Финансовый рынок и его значение в управлении денежными потоками на современном этапе: любому предприятию для расширения производства и увеличения прибыли нужны...
Аура как энергетическое поле: многослойную ауру человека можно представить себе подобным...
Лечение прогрессирующих форм рака: Одним из наиболее важных достижений экспериментальной химиотерапии опухолей, начатой в 60-х и реализованной в 70-х годах, является...
Дисциплины:
![]() |
![]() |
5.00
из
|
Заказать работу |
|
|
Керамические изделия находят большое применение в строительстве. Неограниченные запасы широко распространенного сырья (глин), простота технологии и многовековый опыт производства, а также высокая долговечность их способствовали многообразному применению.Некоторые виды керамических материалов досего времени являются незаменимыми и наиболее распространенными в строительстве. Штучный не индустриальный кирпич пока остается основным стеновым материалом, составляя половину всех стеновых материалов, применяемых в настоящее время.Кирпичные стены зданий в средней полосе СССР возводятся толщиной в 2,5 кирпича (64 см). Столь большая массивность стен вызывает непроизводительные затраты трудовых и материальных ресурсов, увеличивает сроки строительства и удорожает его по сравнению с индустриальным строительством путем механизированной сборки зданий из крупных стеновых железобетонных панелей. Но для увеличения производства сборного железобетона требуются большие капитальные затраты и длительные сроки для строительства и освоения новых предприятий. Представляется целесообразным резко увеличивать производство пустотелой стеновой керамики (пустотелый кирпич, камни и блоки из них). Уже за последние годы производство пустотелой керамики составило около 4% общего объема выпуска кирпича и достигло 1 млрд. шт. условного кирпича. Применение пустотелой керамики, обладающей высокими конструктивными свойствами и малой теплопроводностью, особенно при минусовых температурах, дает возможность уменьшить толщину наружных стен зданий на 20—30 и даже на 40%, вес стен при этом снижается в среднем на 35%, расход вяжущего раствора — до 45%. Применение в качестве стенового материала укрупненных камней дает еще большую экономию, позволяя уменьшить толщину стен на 47%, а вес их на 60%, снизить расход раствора на 55% и керамических материалов на 50%. Соответственно уменьшаются при кладке стен из пустотелой керамики и затраты труда. Необходимо также отметить, что при выпуске пористо-пустотелой керамики расход сырья уменьшается на 30—40%, производительность сушилок и печей кирпичных заводов возрастает на 20—25%, что дает экономию топлива до 20%. Подсчеты показали, что реконструированный для выпуска пустотелой стеновой керамики кирпичный завод увеличивает свою производительность на 70— 80% (в условном исчислении). В настоящее время развитие нашей машиностроительной промышленности дает возможность непрерывно совершенствовать механическое оборудование заводов строительной керамики. Широко применяются новые виды дробильно-помольных, смесительных и формовочных машин. Предприятия оснащаются новейшим подъемно-транспортным оборудованием, особенно важным для керамического производства, нуждающегося в заготовке и перемещении больших масс сырья и тяжеловесной продукции. Перевод керамических предприятий на природный газ в качестве топлива не только повышает производительность труда и снижает себестоимость изделий, но и повышает качество вырабатываемой продукции. В ближайшее время помимо мероприятий общего технического прогресса — механизации и автоматизации, совершенствования технологии и улучшения организации труда — необходимо добиваться снижения себестоимости изделий и обратить особое внимание на организацию выпуска новых, высокоэффективных керамических строительных материалов и изделий.
|
62. Основы технологии производства извести. Сырье.
Известь (CaO) – это продукт, получаемый при высоких температурах в результате кальцинирования известняка. Производство извести протекает в вертикальных шахтных печах или во вращающихся печах, сжигающих уголь, нефтепродукты или природный газ. Кальциевый известняк в сухом виде содержит 97-98% карбоната кальция. Остаток состоит из карбоната магния, оксида алюминия, оксида железа и диоксида кремния. Однако некоторые виды известняка содержат 35-45% карбоната магния, в этом случае известняк классифицируется как доломит. Строительную известь получают путем обжига (до удаления углекислоты) из кальциево-магниевых горных пород — мела, известняка, доломитизированных и мергелистых известняков, доломитов. Для производства тонкодисперсной строительной извести гасят водой или размалывают негашеную известь, вводя при этом минеральные добавки в виде гранулированных доменных шлаков, активные минеральные добавки или кварцевые пески. Производство извести состоит из следующих основных операций: добычи и подготовки сырья и топлива, обжига, превращения продукта обжига в порошок путем гашения или помола. Перед обжигом породу соответствующим образом подготавливают: сортируют по размеру кусков и, если необходимо, дробят.В производстве строительной извести используются следующие материалы: карбонатные породы, минеральные добавки (гранулированные доменные или электротермофосфорные шлаки, активные минеральные добавки, кварцевые пески). Строительную известь применяют для приготовления строительных растворов и бетонов, вяжущих материалов и в производстве искусственных камней, блоков и строительных деталей. В зависимости от условий твердения различают строительную известь воздушную, обеспечивающую твердение строительных растворов и бетонов и сохранение ими прочности в воздушно-сухих условиях, и гидравлическую, обеспечивающую твердение растворов и бетонов и сохранение ими прочности как на воздухе, так и в воде. Воздушная известь по виду содержащегося в ней основного оксида бывает кальциевая, магнезиальная и доломитовая. Воздушную известь подразделяют на негашеную и гидратную (гашеную), получаемую гашением кальциевой, магнезиальной и доломитовой извести. Гидравлическую известь делят на слабогидравлическую и сильногидравлическую. Различают гидравлическую известь комовую и порошкообразную. Порошкообразная известь бывает двух видов: молотая и гидратная (гашенная вода). Комовую известь выпускают без добавок и с добав-ками. Строительную негашеную известь по времени гашения делят на быстрогасящуюся — не более 8 мин, среднегасящуюся — не более 25 мин, медленногасящуюся — более 25 мин.Технологический процесс получения извести состоит из добычи известняка в карьерах, его подготовки (дробления и сортировки) и обжига. После обжига производят помол комовой извести, получая молотую негашеную известь, или гашение комовой извести водой, получая гашеную известь. Основным процессом при производстве извести является обжиг, при котором известняк декарбонизуется и превращается в известь по реакции СаСО3↔ СаО + СО2.При обжиге из известняка удаляется углекислый газ, составляющий до 44% его массы, объем же продукта уменьшается примерно на 10%, поэтому куски комовой извести имеют пористую структуру. Обжиг известняка производят в различных печах: шахтных, вращающихся, в «кипящем слое», во взвешенном состоянии и т. Д
|
|
|
|
Механическое удерживание земляных масс: Механическое удерживание земляных масс на склоне обеспечивают контрфорсными сооружениями различных конструкций...
Индивидуальные и групповые автопоилки: для животных. Схемы и конструкции...
Археология об основании Рима: Новые раскопки проясняют и такой острый дискуссионный вопрос, как дата самого возникновения Рима...
Организация стока поверхностных вод: Наибольшее количество влаги на земном шаре испаряется с поверхности морей и океанов (88‰)...
© cyberpedia.su 2017-2024 - Не является автором материалов. Исключительное право сохранено за автором текста.
Если вы не хотите, чтобы данный материал был у нас на сайте, перейдите по ссылке: Нарушение авторских прав. Мы поможем в написании вашей работы!