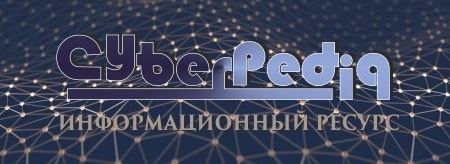
Индивидуальные очистные сооружения: К классу индивидуальных очистных сооружений относят сооружения, пропускная способность которых...
Автоматическое растормаживание колес: Тормозные устройства колес предназначены для уменьшения длины пробега и улучшения маневрирования ВС при...
Топ:
Выпускная квалификационная работа: Основная часть ВКР, как правило, состоит из двух-трех глав, каждая из которых, в свою очередь...
Теоретическая значимость работы: Описание теоретической значимости (ценности) результатов исследования должно присутствовать во введении...
Интересное:
Инженерная защита территорий, зданий и сооружений от опасных геологических процессов: Изучение оползневых явлений, оценка устойчивости склонов и проектирование противооползневых сооружений — актуальнейшие задачи, стоящие перед отечественными...
Наиболее распространенные виды рака: Раковая опухоль — это самостоятельное новообразование, которое может возникнуть и от повышенного давления...
Средства для ингаляционного наркоза: Наркоз наступает в результате вдыхания (ингаляции) средств, которое осуществляют или с помощью маски...
Дисциплины:
![]() |
![]() |
5.00
из
|
Заказать работу |
|
|
Зажимные устройства приспособлений разделяются на простые и комбинированные, состоящие из нескольких простых.
Простые зажимные устройства состоят из одного элементарного зажима, например, винтового, эксцентрикового, клинового, рычажного и т.п. В зависимости от источника силы зажимные устройства разделяются на ручные и механизированные. В ручных зажимных устройствах сила на рукоятке не должна превышать 150 Н (15 кгс).
Винтовые зажимы применяются в приспособлениях, как с ручным закреплением деталей, так и с механизированным (например, в сочетании с пневмоприводом). Они просты по конструкции и надежны в работе. Недостатки: значительное вспомогательное время, необходимое для зажима и разжима детали, и быстрый износ резьбы вследствие температурного воздействия сварочной дуги, и попадания брызг металла.
Для закрепления деталей винтовыми зажимами используются ключи, ручки, гайки, гайки-головки, установленные на конце винта. Зажимные винты и гайки изготовляются из стали 35 и 45 с точностью резьбы 9…11-го квалитета СТСЭВ 145-75 (по 3-му классу в системе ОСТ).
Усилие, развиваемое винтовым зажимом, зависит от длины рукоятки 2 и величины приложенной к ней силы Q, формы зажимного винта 1 и вида резьбы (рис. 5.7).
Без учета потерь на трение сила зажима, развиваемая винтом со сферическим торцом (рис. 5.7, а),
P = Ql /[ rcptg (α + φ пр)]. (5.18)
Развиваемая винтом с плоским торцом (рис. 5.7, б), сила зажима
P = Ql /[ rcptg (α + φ пр) + 0,67 fr ]. (5.19)
Сила зажима, развиваемая винтом со сферическим торцом, упирающимся в конусное гнездо зажимного башмака, предупреждающего порчу поверхности детали (рис. 5.7, в),
P = Ql /[ rcptg (α + φ пр) + fRctg (β / 2)]. (5.20)
|
где Q – сила на рукоятке или ключе резьбового зажима, Н; для ручных винтов Q = I50 Н; P – требуемая сила зажима винтом детали, Н; l – расстояние от оси винта до точки приложения силы, l ≈ I4 d (d – номинальный наружный диаметр резьбы), см; rcp – средний радиус резьбы винта, см; α ≈ 2о30'...3о30' – угол подъема витка резьбы; R – радиус конусного гнезда башмака, см.
Рассчитанное усилие зажима должно быть проверено на условие прочности резьбы. Для основной метрической резьбы
(5 21)
Отсюда номинальный внутренний диаметр винта (см)
(5.22)
где [σ в ] – допускаемый предел прочности на растяжение, MПa; для винтов из стали 45 с учетом износа резьбы [σ в ] = 80...100 МПа.
Диаметр округляют до ближайшего большего значения. В приспособлениях применяют резьбы от М8 до М42.
Для небольших сил зажима целесообразно применять штыковое (байонетное) (рис. 5.8, а) устройство, а для значительных сил плунжерное (рис. 5.8,6). Эти устройства позволяют отводить зажимающий элемент 1 на большое расстояние от детали 2 и крепить ее поворотом стержня на небольшой угол.
Эксцентриковые зажимы. В приспособлениях используются обычно круглые эксцентрики (ГОСТ 9061-68) из стали 20Х с цементацией на глубину 0,8…1,2 мм с последующей закалкой до твердости НРС 55...60. Дисковой эксцентрик показан на рис. 5.9,а, а эксцентриковый валик с Г-образным прихватом – на рис. 5.9,6.
У стандартных круглых эксцентриков D = 32...70 мм и е = 1,7...3,5 мм. Следовательно, круглые эксцентрики имеют небольшой линейный ход и их не следует применять для зажима деталей с большим допуском на размеры в направлении зажима.
Достоинство круглых эксцентриков – простота изготовления; недостатки – изменение угла подъема и силы зажима при закреплении обрабатываемых деталей с большими колебаниями размеров в направлении зажима. Применение самотормозящих эксцентриковых устройств в соответствии с ГОСТом 12.2.029-77 допустимо при развивающемся расчетам усилии зажима, не превышающем 2200 Н.
|
Эксцентрик является самотормозящим, если угол подъема эксцентрика α в определенном его положении не больше угла трения φ.
Для установления зависимости между требуемой силой зажима и моментом на рукоятке эксцентрика в конце закрепления детали рассмотрим схему, изображенную на рис. 5.10.
В процессе закрепления на эксцентрик действуют сила на рукоятке Q, реакция заготовки T и реакция S от цапфы (оси) эксцентрика. Под действием этих сил система находится в равновесии. Реакция T представляет собой равнодействующую силы Р и силы трения F
Сумма моментов всех действующих сил относительно оси поворота эксцентрика равна нулю:
Ql – P е sin α ' – fP (R + lcos α ') – sρ = 0 (5.23)
где f – коэффициент трения скольжения между эксцентриком и заготовкой;
l – плечо, на котором прилагается усилие Q, см;
е – эксцентриситет эксцентрика, см;
α – угол поворота эксцентрика от начального положения α ' = 180º – α. град;
ρ – радиус круга трения цапфы, см;
R – радиус наружной поверхности эксцентрика, см.
Сила S мало отличается от нормальной силы Р. Приняв S = Р, получим момент на рукоятке эксцентрика
Ql = P fR [ + ρ + е (sinα ' + f cos α ')]. (5.24)
Для упрощения подученного выражения примем:
1) fR = tg φ R ≈ sin φ R (для угла трения покоя φ = 6º ошибка меньше 1%;
2) выражение sinα ' + f cos α ' заменим весьма близким, но более простым sin (α ' + φ), ошибка 1%.
После подстановок получим упрощенную формулу:
Ql= P [ Rsin φ + ρ + е sin (α' + φ)]. (5.25)
Радиус наружной поверхности эксцентрика R определяем из условий самоторможения. Из рассмотрения сил, действующих на круглый эксцентрик, следует, что равнодействующая реакции и сила трения F должна быть равна и противоположно направлена реакции со стороны цапфы. Последняя проходит касательно к кругу трения радиусом ρ. Из рис. 5.10
(5.26)
отсюда
(5.27)
Приняв во внимание выражение для R (5.27), получим
Ql = P е [ 1 + sin (α ' + φ)]. (5.28),
Эта приближенная формула позволяет определить значение момента Ql с точностью до 10%, что вполне допустимо.
|
Отсюда
Р = Ql / е [ 1 + sin (α ' + φ)] (5.29)
Клиновые зажимы обычно применяют в качестве промежуточного звена в сложных зажимных системах. Они просты в изготовлении, компактны, легко размещаются в приспособлении, позволяют увеличивать и изменять направление передаваемой силы. Для надежного закрепления детали в приспособлении клин должен быть самотормозящим, т.е. зажимать деталь после прекращения действия на клин исходной силы Q (рис. 5.11).
При расположении передаваемых сил односкосным клиновым механизмом между силами Р и Q, т.е. под прямым углом, получается зависимость, определяемая из силового многоугольника как
(5.30)
где Q – усилие, приложенное к клину, Н; Р – усилие зажатия, развиваемое клином, Н; α – угол скоса клина, град.
Знак "+" относится к закреплению клина, а знак "–" – к его откреплению.
Самоторможение клина имеет место при
α < φ1 + φ2. (5.31)
Если угол трения постоянен и равен φ, т.е. φ1 = φ2 = φ3 = φ (t g φ = f = 0,1...0,15), то зависимость является более простой:
Q = Ptg (α ± 2 φ). (5.32)
Отсюда сила зажатия, развиваемая клином,
P = Q/ tg (α ± 2 φ)
Рычажные зажимы применяются, как и клиновые, в сочетании с другими элементарными зажимами, образуя более сложные системы (механизмы). При помощи рычага можно изменять величину и направление передаваемой силы, а также одновременно и равномерно закреплять деталь в двух местах.
Для наиболее распространенного в зажимных устройствах двухплечевого рычага (рис. 5.12, а) отношение между силами Р и Q c учетом трения можно найти, беря сумму моментов относительно оси вращения 0.
Силу реакции на оси рычага S можно найти из силового многоугольника (рис. 5.12, б). Приближенно
При l 1 < l 2 S ≈ 0,96 P + 0,4 Q;
при l 1 = l 2 = l S ≈ 1,41 Q;
при l 1 > l 2 S ≈ 0,96 Q + 0,4 N.
Подставляя значения S в уравнение равновесия, получим усилие зажима Q:
для условия l 1 < l 2
(5.33)
для условия l 1 = l 2 = l
(5.34)
для условия l 1 > l 2
(5.35)
|
В этих формулах радиус круга трения ρ = f ' r. Значение f ' можно брать в пределах 0,18... 0,2.
Анализируя полученные зависимости, можно видеть, что для уменьшения потерь в рычажной передаче полезно уменьшать радиус оси и плечи l '1 и l '2.
Для рычага, изображенного на рис. 5.1I2, в, уравнение равновесия будет таким же, как для предыдущего случая. Однако
S = (Q + P) .
Подставляя S в уравнение равновесия и решая его относительно Q, получим
(5.36)
Для рычага, представленного на рис. 5.I2, г, эта зависимость приобретает следующий вид:
(5.37)
Центрирующие зажимные устройства (цанги, разжимные оправки) применяются при использовании в качестве установочных баз наружных или внутренних цилиндрических (многогранных) поверхностей.
Цанги, представляющие собой разрезные пружинящие гильзы (рис. 5.1З), выполняют из высокоуглеродистых сталей типа У10A и термически обрабатывают до твердости НРС 58…62 в местах губок и до твердости HRC 39…45 в хвостовой части. Угол конуса цанги α = 30...40º. При меньших углах возможно заклинивание цанги. Угол конуса сжимающей втулки делают на 1º меньше (см. рис. 5.13, а) или больше (см. рис. 5.13, б) угла конуса цанги.
Цанги обеспечивают концентричность установки в пределах 0,02…0,05 мм. Базовая поверхность деталей для закрепления в цангах должна иметь 7…9 квалитет по СТ CЭВ 145-75 (2…3-й класс точности в системе ОСТ).
Сила затяжки цанги при отсутствии упора (см. рис.5.13, а)
(5.38)
где Q – суммарная сила зажима, распределенная по базовой поверхности детали, Н;
Q ' – сила сжатия лепестков цанги, используемая для выбора зазора между ее губками и деталью, Н;
φ – угол трения между цангой и втулкой, град.
(5.39)
где r – радиус базовой поверхности детали, см;
M – момент, передаваемый цангой, Н см;
N – осевая сила, cдвигающая деталь, Н;
f 1 – коэффициент трения между деталью и цангой;
К – коэффициент запаса.
Силу Q ' находим, рассматривая лепесток цанги как консольно закрепленную балку:
(5. 4())
где E — модуль упругости материала цанги, МПа;
I – момент инерции сектора тонкого кольца в заделе лепестка цанги в см (сечение A–А на рис. 5.13, а),
(5.41)
здесь D – наружный диаметр поверхности лепестка, см;
S – толщина стенки лепестка, см; α1 – половина угла сектора лепестка цанги;
l – длина лепестка от места задела до середины конуcа, см;
п – число лепестков цанги;
f – стрела прогиба лепестка, равная половине зазора по диаметру между заготовкой и цангой, см.
При наличии осевого упора (см. рис. 5.13,б) возникает трение между губками цанги и деталью (угол трения φ1). В этом случае
|
(5.42)
Разжимные оправки различных конструкций показаны на рис. 5.14.
На рис. 5.14, а представлена консольная разжимная оправка 1 с прорезями на рабочей шейке. Деталь 2 закрепляется затяжкой внутреннего конуса 3. Точность центрирования для оправки находится в пределах 0,02…0,04 мм. Для консольной оправки силу затяжки можно определить по формуле для цанги:
(5.43)
Оправка с выдвижными радиальными сухарями (см.рис. 5.14,б) может быть рекомендована для толстостенных деталей с грубообработанной или черновой базой. Точность центрирования составляет 0,05…0,1 мм. Силу на штоке можно подсчитать, используя формулу для клина, приняв в ней φ = 0.
(5.44)
где W – суммарная сила, с которой кольцевая пружина оттягивает сухари к центру оправки, Н.
Приводы зажимных устройств
Пневматические приводы состоят из пневмодвигателей, пневматической аппаратуры и воздухопроводов. Энергоносителем в пневмоприводе является сжатый воздух с давлением q = 0,4...0,6 МПа (4…6 кгс/см2).
Пневматические силовые приводы разделяют по виду пневмодвигателя:
а) на пневматические цилиндры с поршнем (поршневые);
б) пневматические камеры с диафрагмами (диафрагменные);
в) пневматические шланги (пневмошланговые).
Пневматические силовые приводы изготовляют одно- и двухстороннего действия. У двигателей одностороннего действия обратный ход осуществляется пружиной, таким образом обеспечивается экономия сжатого воздуха до 30…40%, однако их габариты увеличиваются из-за установки пружины. В двигателях двухстороннего действия обратный ход осуществляется также сжатым воздухом. Они применяются в случаях, когда при зажиме и разжиме детали требуется большая сила, например, в приспособлениях с самотормозящими зажимными устройствами.
Достоинства пневмодвигателей: значительное сокращение времени на зажим и разжим деталей вследствие быстроты действия (0,5…1,2 с), постоянство силы зажима, возможность регулировали силы зажима, простота управления.
Недостатки: недостаточная плавность перемещения рабочих элементов, небольшое давление сжатом воздуха, относительно большие размеры пневмодвигателей для получения значительных сил на штоке.
Пневматические поршневые приводы двухстороннего действия регламентированы ГОСТом 15608-81 и выпускаются в следующих исполнениях:
а) по способу торможения:
1 – без торможения,
2 – с регулируемым торможением в конце хода;
б) по виду крепления:
0 – на удлиненных стяжках,
1 – на лапах,
2 – на переднем фланце,
3 – на заднем фланце,
4 – на пружине,
5 - на цапфах;
в) по выполнению конца штока:
1 – с наружной резьбой,
2 – с внутренней резьбой;
r) по присоединительной резьбе для подвод воздуха:
1 – с метрической резьбой,
2 – с конической резьбой.
Условные графические обозначения цилиндров должны соответствовать указанным на рис. 5.15.
Например, цилиндр без торможения, с креплением на удлиненных стяжках, с наружной резьбой на конце штока, с метрической присоединительной резьбой для подвода воздуха, диаметром D = 100 мм и ходом поршня S = 1000 мм обозначается так: пневмоцилиндр 1011 – 100х1000 ГОСТ 15608-81.
Основные параметры цилиндров должны соответствовать указанным в табл. 5.2.
Таблица 5.2
Основные параметры пневмоцилиндров (ГОСТ 15608-81)
Диаметр, мм | Статическое усилие на штоке (Н) при давлении воздуха в пневмосети 0,4 МПа | ||
цилиндра | штока | толкающее | тянущее |
25 | 12 | I60 | 130 |
32 | 250 | 220 | |
40 | 14 | 400 | 350 |
50 | 18 | 640 | 550 |
63 | 25 | 1000 | 900 |
80 | 1750 | 1560 | |
100 | 2700 | 2550 | |
125 | 32 | 4200 | 4000 |
160 | 40 | 7200 | 6800 |
200 | 11400 | 10800 | |
250 | 63 | 17700 | 16500 |
320 | 80 | 30000 | 28000 |
360 | 37600 | 36000 | |
400 | 90 | 46800 | 44500 |
Основные размера цилиндров без торможения с креплением на удлиненных стяжках приведены на рис. 5.16 и в табл. 5.3.
Таблица 5.3
Основные размера цилиндров без торможения с креплением на удлиненных стяжках
D | d | Резьба | B | l, не более | К | К1 | Ход поршня по ГОСТу 6540-68 | |||
наружная | внутренняя | |||||||||
d2 | l | d2 | l | |||||||
25 | 12 | М 10х1,25 | 22 | – | – | 38 | 10 | 92 | 115 | 10…250 |
32 | 45 | 10…320 | ||||||||
40 | 14 | М 12х1,25 | 24 | – | – | 55 | 20 | 98 | 127 | 10…400 |
50 | 18 | М 16х1,5 | 32 | М12х1,25 | 24 | 70 | 24 | 106 | 143 | 10…500 |
63 | 78 | 10…630 | ||||||||
80 | 25 | М 20х1,5 | 40 | М 16х1,5 | 32 | 93 | 28 | 120 | 160 | 10…800 |
100 | 115 | 170 | 10…1000 | |||||||
125 | 32 | М 27х2 | 54 | М 24х2 | 48 | 140 | 30 | 130 | 190 | 10…1250 |
160 | 180 | 33 | 203 | 10…1600 | ||||||
200 | 40 | М 36х2 | 72 | М 30х2 | 60 | 220 | 40 | 142 | 230 | 10…2000 |
250 | 63 | М 42х2 | 84 | М 42х2 | 84 | 275 | 50 | 160 | 255 | |
320 | 80 | М 48х2 | 96 | М 48х2 | 96 | 345 | 67 | 180 | 290 | 10…2500 |
Расчет силовых цилиндров производится по формулам, основанным на известной зависимости силы на штоке Р от диаметра цилиндра D и давления в цилиндре q (расчетное значение q = 0,40 МПа).
В цилиндрах двухстороннего действия при толкающем движении штока
(5.45)
при обратном — тянущем – движении штока
(5.46)
где d — диаметр штока.
В цилиндрах одностороннего действия с возвратной пружиной
(5.47)
Пользуясь этими формулами, можно решить обратную задачу, т.е. определить внутренний диаметр цилиндра D по заданному усилию на штоке Р и давлению сжатого воздуха q.
Коэффициент полезного действия η оценивает потери на трение в манжетах и уплотнениях, а также в направляющих штоках.
Для цилиндров средних размеров (D = 150...300 мм) приближенно можно принять η = 0,85. Однако в ответственных случаях следует непосредственно подсчитывать прямые потери на трение в манжетах поршня и штока /1/.
Для уплотнения и поршней, и штоков пневмоцилиндров чаще всего применяются манжеты угловые воротниковые (ГОСТ 6678-72) и V -образные (ГССТ 6969-54), а также кольцо круглого сечения. Все манжеты изготовляются из маслостойкой резины.
Разновидностью пневмоцилиндров являются вращающиеся пневмоцилиндры, которые с помощью воздухоподводящей муфты соединяются с сетью подачи сжатого воздуха (рис. 5.17).
Основные размеры и усилия, вращающихся пневмоцилиндров двухстороннего действия приведены в табл. 5.4 (ГОСТ 21821-76).
Таблица 5.4
Основные размеры и усилия, вращающихся пневмоцилиндров
Обозначение цилиндра | Тип | Основные размеры, мм | Усилие на штоке, Н при давлении воздуха в пневмосети 0,4 МПа | Частота вращения С –1, об/мин | |||||||
D | d 3 | D 4 | L | L 1 | l2 | L 2 | толкающее | тянущее | |||
7020 – 0101 | I | 100 | 25 | 135 | 32 | 125 | 30 | 340 | 2710 | 2540 | 50 (3000) |
7020 – 0103 | I | 125 | 165 | 4230 | 4070 | 50 (3000) | |||||
7020 – 0105 | I | 160 | 200 | 7250 | 6950 | 50 (3000) | |||||
7020 – 0107 | 2 | 160 | 32 | 200 | 205 | 420 | 13820 | 13520 | 50 (3000) | ||
7020 – 0109 | I | 200 | 240 | 125 | 340 | 11300 | 10980 | 50 (3000) | |||
7020 – 0112 | 2 | 200 | 240 | 125 | 420 | 21850 | 21560 | 41,66(2500) | |||
7020 – 0114 | I | 250 | 290 | 40 | 145 | 370 | 17700 | 17050 | 41,66(2500) | ||
7020 – 0116 | 2 | 250 | 45 | 290 | 245 | 40 | 460 | 34300 | 33720 | 33,33(2000) | |
7020 – 0118 | I | 320 | 360 | 145 | 370 | 29000 | 28420 | 33,33(2000) | |||
7020 – 0121 | 2 | 320 | 360 | 50 | 255 | 470 | 56350 | 56450 | 33,33(2000) |
Время срабатывания пневмоцилиндра может быть приближенно подсчитано по формуле
. (5.48)
где D – диаметр цилиндра, см; L – ход поршня, мм; d 0 — диаметр воздухопровода, мм.
Диафрагменные пневмокамеры имеют ряд преимуществ перед пневмоцилиндрами: они проще в изготовлении и дешевле, долговечнее, так как диафрагма работает дольше и надежнее, чем поршневые уплотнения; в камерах практически отсутствует утечка воздуха, так как обе полости изолированы друг от друга; в камерах может быть использован сжатый воздух, более влажный и загрязненный, так как он не соприкасается с трущимися частями. К недостаткам пневмокамер относятся сравнительно малый ход штока (30…60 мм), ограниченный допускаемой деформацией диафрагмы; увеличенный (по сравнению с цилиндром того же усилия) наружный диаметр камеры.
Конструкция диафрагменной пневмокамеры одностороннего действия представлена на рис. 5.18, двухстороннего действия – на рис. 5.19, их размеры приведены в табл. 5.5 и 5.6.
В пневмокамерах применяются диафрагмы автомобильных тормозных камер, выпускаемые специализированными заводами. Материал диафрагм – бензомаслостойкая резина с двумя слоями ткани толщиной 1,8…2 мм.
Так как промышленность выпускает пневмокамеры в крайне ограниченном ассортименте, нередко их проектируют заново (особенно для больших усилий).
Таблица 5.5
Основные размеры диафрагменных пневмокамер одностороннего действия, мм
D | Ход на штоке L | D 1 | Т | Н | l | l1 | d | s | Усилие на штоке (Н) при 0,4 МПа |
175 | 30 | 115 | 132 | 88 | 30 | 35 | М16 | 80 | 2750 |
200 | 35 | 125 | 150 | 94 | 35 | 35 | М16 | 88 | 3250 |
230 | 40 | 140 | 180 | 101 | 35 | 40 | М20 | 120 | 6000 |
Усилие на штоке или диаметр пневмокамер могут быть подсчитаны по формулам, приведённым в табл. 5.7.
Таблица 5.6
Основные размеры диафрагменных пневмокамер двухстороннего действия, мм
D | Ход на штоке L | D 1 | D 2 | Н | d | К | Т | М | Усилие на штоке (Н) при 0,4 МПа |
174 | 40 | 154 | 130 | 122 | М12х1,75 | 17 | 48 | 48 | 3500 |
200 | 40 | 178 | 160 | 137 | М 16х2 | 17 | 56 | 45 | 4800 |
228 | 40 | 204 | 180 | 137 | М 16х2 | 17 | 56 | 45 | 6750 |
Пневмошланговые приводы (рис.5.20) отличаются простотой, портативностью и надежностью действия. Существенными их недостатками являются сравнительно малый рабочий ход и зависимость полезного усилия шланга от степени его сплющивания, т.е. от высоты внутренней полости шланга, а, следовательно, и от рабочего хода шланга.
При давлении воздуха q полезное усилие шланга на 1 мм погонной длины
Q = bq, Н/мм, (5.49)
где b – ширина площадки давления, мм.
Так как шланг армирован тканью и поэтому не может растягиваться по окружности, то в деформированном по рис. 5.20, б шланге приближенно соблюдается геометрическое равенство π d ш = 2 b + π (h+ Δ), откуда
(5. 50)
где h – вертикальный рабочий ход шланга, мм;
Δ – остаточный зазор внутри полости сплющенного шланга в его рабочем состоянии (для зажимных устройств можно принимать Δ = 3... 5 мм).
Если заданными величинами являются q, p и h, то необходимый внутренний диаметр шланга определяется совместным решением уравнений, т.е.
(5. 51)
По имеющимся сортаментам подбирают шланг ближайшего большего диаметра, обычно прорезиненный пожарный рукав. При конструировании пневмошлангового привода следует иметь в виду, что обычный шланг или пожарный рукав при переходе от рабочего состояния (под давлением) в нерабочее (без давления) не может сплющиться самопроизвольно под действием собственного веса, так как этот вес явно недостаточен для преодоления жесткости шланга и тем более для быстрого вытеснения воздуха из него. Поэтому в пневмошланговом приводе, как правило, предусматривается то или иное устройство для быстрого принудительного возврата шланга в нерабочее состояние. Наиболее распространены следующие типы возвратных устройств:
Таблица 5.7
Расчетные формулы для определения исходного усилия,
развиваемого пневмокамерами
Пневмокамера | Эскиз пневмокамеры | Расчетные формулы |
Пневмокамеры одностороннего действия | ![]() | В исходном положении штока
![]() ![]() ![]() ![]() |
![]() | В исходном положении штока.
![]() ![]() ![]() | |
Пневмокамеры двухстороннего действия | ![]() | В исходном положении штока.
![]() ![]() ![]() |
![]() | В исходном положении штока.
![]() ![]() ![]() |
добавочный груз, постоянно действующий на шланг; возвратные пружины (рис. 5.21), всасывающие эжекторы или эксгаустеры, образующие (на короткое время) вакуум в шланге; вспомогательный возвратный шланг-рукав (рис. 5.22). Первые два из этих устройств являются для рабочего шланга нагрузкой, снижающей величину его полезного усилия; возвратные устройства двух других типов не влияют на величину полезного усилия рабочего шланга.
Опыт показал, что для быстрого возврата шланга в нерабочее состояние достаточно усилия Рдоб = 0,05 Q или, в случае всасывающего устройства, достаточно создать разряжение в рабочем шланге примерно 0,02 МПа.
Гидравлические приводы поршневого типа приводятся в действие от отдельного или группового насоса. Гидравлическая установка состоит из электродвигателя, рабочих гидроцилиндров, насоса для подачи масла в цилиндры, бака масла, аппаратуры управления и регулирования, трубопроводов. Рабочей жидкостью служат минеральные масла II-го класса чистоты по ГОСТ 17216-71.
По сравнению с пневматическими гидравлические силовые узлы имеют меньшие габариты вследствие применения более высокого давления масла
(6 МПа и выше).
Недостатками устройства являются наличие трубопроводов для слива выпускаемого из цилиндра масла, а также необходимость работы нагнетательного насоса и электродвигателя в течение цикла зажима.
Гидроцилиндры могут быть одностороннего действия со сплошным (ГОСТ 19897-74) и с полым (ГОСТ 19898-74) штоком, а также двухстороннего действия (ГОСТ 19899-74, в том числе укороченные по ГОСТу 19900-74).
Конструкция и основные размеры гидроцилиндров одностороннего действия со сплошным штоком (ГОСТ 19897-74) на номинальное давление 10 МПа представлены на рис. 5.23 и в табл. 5.8.
Конструкция и основные размеры гидроцилиндров двухстороннего действия на номинальное давление 10 MIIa (100 кгс/см2) по ГОСТУ 19899-74 представлены на рис. 5.24 и в табл. 5.9.
Исходными данными для расчета гидравлических зажимных устройств являются: требуемая сила Р на штоке гидроцилиндра, длина хода поршня L и время рабочего хода поршня t.
Таблица 5.8
Основные размеры гидроцилиндров одностороннего действия
со сплошным штоком, мм (ГОСТ 19897-74)
Обозначение цилиндров | D | D 1 | d | d 1 | L | Ход поршня, l | Усилие теоретическое (Н) при давлении 10 MIIa |
7021– 0061 | 40 | 56 | 22 | М12 | 90 | 12 | 11760,0 |
7021– 0065 | 50 | 67 | 25 | М16 | 100 | 16 | 18453,4 |
7021– 0069 | 63 | 80 | 32 | М20 | 105 | 16 | 29263,0 |
7021– 0074 | 80 | 105 | 36 | М24 | 110 | 16 | 47530,0 |
Для толкающих гидроцилиндров одностороннего действия:
сила на штоке
(5.52)
для тянущих гидроцилиндров
(5.53)
Для гидроцилиндров двухстороннего действия при подаче масла в бесштоковую полость
(5.54)
а при подаче масла в штоковую полость
(5.53)
где D – диаметр поршня гидроцилиндра, мм; q – давление масла на поршень, МПа; η = 0,85…0,9 – КПД цилиндра; Рпруж – сила сопротивления сжатой пружины при крайнем рабочем положении поршня, Н; d – диаметр штока, мм.
Пневмогидравлические приводы позволяют без применения насосных станций и специальной гидросети высокого давления осуществить питание рабочих силовых цилиндров жидкостью (маслом) вместо сжатого воздуха.
Для этого достаточно использовать пневмогидравлические мультипликаторы, подключенные к цеховой сети сжатого воздуха. Схемы питания рабочих гидроцилиндров с помощью простейших беспоршневых мультипликаторов, имеющих коэффициент мультипликации, равный единице, представлены на рис. 5.25 и 5.26. В этих схемах пневмогидравлические мультипликаторы 3 представляют собой простые цилиндрические сосуды, рассчитанные на давление сжатого воздуха до 0,7 МПа, с емкостью, несколько большей, чем суммарный полезный объем всех питаемых рабочих гидроцилиндров.
Таблица 5.9
Основные размеры гидроцилиндров двухстороннего действия, мм
Обозначение цилиндров | D | D 1 | d 1 | d 2 | L | Ход поршня, l | Усилие теоретическое (Н) | |
толкающее | тянущее | |||||||
7021-0121 | 40 | 56 | 22 | М12 | 105 | 12 | 12308,8 | 8684,8 |
7021-0126 | 125 | 32 | ||||||
7021-0129 | 145 | 50 | ||||||
7021-0134 | 175 | 80 | ||||||
7021-0138 | 50 | 67 | 25 | М16 | 110 | 16 | 19237,4 | 14425,4 |
7021-0143 | 125 | 32 | ||||||
7021-0147 | 145 | 50 | ||||||
7021-0152 | 175 | 80 | ||||||
7021-0156 | 63 | 80 | 32 | М20 | 115 | 16 | 30536,8 | 22657,6 |
7021-0161 | 130 | 32 | ||||||
7021-0166 | 150 | 50 | ||||||
7021-0169 | 180 | 80 | ||||||
7021-0174 | 80 | 105 | 36 | М24 | 125 | 16 | 49235,2 | 39268,6 |
7021-0178 | 140 | 32 | ||||||
7021-0183 | 155 | 50 | ||||||
7021-0187 | 185 | 80 | ||||||
7021-0192 | 100 | 125 | 45 | М30 | 125 | 16 | 76930,0 | 61348,0 |
7021-0196 |
|
|
Особенности сооружения опор в сложных условиях: Сооружение ВЛ в районах с суровыми климатическими и тяжелыми геологическими условиями...
Эмиссия газов от очистных сооружений канализации: В последние годы внимание мирового сообщества сосредоточено на экологических проблемах...
Археология об основании Рима: Новые раскопки проясняют и такой острый дискуссионный вопрос, как дата самого возникновения Рима...
Типы оградительных сооружений в морском порту: По расположению оградительных сооружений в плане различают волноломы, обе оконечности...
© cyberpedia.su 2017-2024 - Не является автором материалов. Исключительное право сохранено за автором текста.
Если вы не хотите, чтобы данный материал был у нас на сайте, перейдите по ссылке: Нарушение авторских прав. Мы поможем в написании вашей работы!