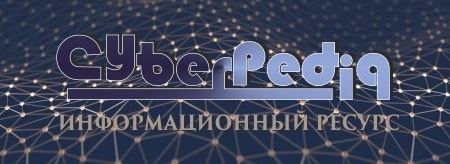
Опора деревянной одностоечной и способы укрепление угловых опор: Опоры ВЛ - конструкции, предназначенные для поддерживания проводов на необходимой высоте над землей, водой...
Поперечные профили набережных и береговой полосы: На городских территориях берегоукрепление проектируют с учетом технических и экономических требований, но особое значение придают эстетическим...
Топ:
Оснащения врачебно-сестринской бригады.
Проблема типологии научных революций: Глобальные научные революции и типы научной рациональности...
Комплексной системы оценки состояния охраны труда на производственном объекте (КСОТ-П): Цели и задачи Комплексной системы оценки состояния охраны труда и определению факторов рисков по охране труда...
Интересное:
Наиболее распространенные виды рака: Раковая опухоль — это самостоятельное новообразование, которое может возникнуть и от повышенного давления...
Средства для ингаляционного наркоза: Наркоз наступает в результате вдыхания (ингаляции) средств, которое осуществляют или с помощью маски...
Берегоукрепление оползневых склонов: На прибрежных склонах основной причиной развития оползневых процессов является подмыв водами рек естественных склонов...
Дисциплины:
![]() |
![]() |
5.00
из
|
Заказать работу |
|
|
Опорные элементы
Опорные точки реализуются в приспособлении в виде опорных элементов, которые по своему назначению подразделяются на основные и дополнительные. Основные элементы предназначены для реализации схемы базирования, дополнительные – для придания изделию необходимой жесткости в процессе сборки и сварки.
К основным опорным элементам относятся опорные штыри, пластины, пальцы, центры, плавающие и сблокированные опоры и др., a к дополнительным — подводимые и самоустанавливающиеся одиночные опоры, люнеты и т.д.
Условное графическое обозначение опорных изажимных элементов установлено ГОСТом 3.1107-81 (СТ СЭВ I803-79). Обозначения опор и установочных устройств приведены в табл. 4.1.
Иногда опорные элементы сочетаются с зажимами, в результате образуются опорно-зажимные элементы. К ним относятся, в частности, так называемые самоцентрирующие устройства (патроны двух- и трех- кулачковые, оправки цанговые и т.п.), которые одновременно с базированием выполняют и функции закрепления. В обозначениях этих элементов сочетаются обозначения опор и зажимов. Условные обозначения некоторых зажимов приведены в табл. 4.2.
Таблица 4.1
Условные обозначения опор и установочных элементов (ГОСТ 3.1107-81)
Наименование опоры и установочного устройства | Обозначение опоры на видах | ||
спереди, сзади | сверху | снизу | |
1. Неподвижная | | | |
2. Подвижная | |||
3. Плавающая | |||
4. Регулируемая | |||
5. Оправка цанговая | |||
6. Центр неподвижный | |||
7. Центр вращающийся | |||
8. Центр плавающий |
* Обозначение опоры на видах сверху, снизу соответствует обозначению на них спереди, сзади.
Таблица 4.2
Условные обозначения зажимов (ГОСТ 3.1107-8I)
Наименование зажима
| Обозначение зажима на видах | |||
спереди, сзади | сверху | снизу | ||
1. Одиночный | | |||
2. Двойной | |
Условные обозначения формы рабочей поверхности опор, зажимов и установочных устройств наносят слева от обозначения опоры, зажима или установочного устройства (табл. 4.3).
Таблица 4.3
Условные обозначения формы рабочей поверхности
опор, зажимов и установочных устройств (ГОСТ 3.1107-8I)
Наименование формы рабочей поверхности | Обозначение формы рабочей поверхности на всех видах |
1. Плоская | ![]() |
2. Сферическая | ![]() |
3. Цилиндрическая (шариковая) | ![]() |
4. Призматическая | ![]() |
5. Коническая | ![]() |
|
Условные обозначения приводов зажимных устройств приведены в табл. 4.4.
Таблица 4.4
Условные обозначения приводов зажимных устройств
№ п/п | Наименование устройства зажима | Обозначение на всех видах |
1 | Пневматическое | Р |
2 | Гидравлическое | Н |
3 | Электрическое | Е |
4 | Магнитное | М |
5 | Электромагнитное | ЕМ |
6 | Прочее | Без обозначения |
Некоторые примеры нанесения условных обозначений опор, зажимов и установочных устройств на схемах приведены в табл.4.5.
Способы базирования деталей с главной базой, имеющей форму
Способы базирования деталей с главной базой, имеющей форму
Цилиндрического отверстия
Цилиндрические отверстия деталей и изделий в отдельных случаях целесообразно использовать в качестве главной базы.
Осуществить базирование заготовки отверстием — это значит совестить его ось с какой-то заданной линией в приспособлении. Наибольшее распространение получили следующие способы базирования: на цилиндрических оправках (пальцах), на коническую поверхность с малой конусностью и с помощью самоцентрирующего устройства.
Базирование на цилиндрических пальцах рекомендуется применять только для деталей с отверстием, обработанными по 6-9-му квалитетам по СТ СЭВ 144-75 (по 1-3-му классам точности по ГОСТУ), иначе получаются большие погрешности и перекос оси базы. Чтобы перекос оси базы не превышал допустимых пределов, длину оправки (кольца) принимают примерно равной 1,5 D, где D — номинальный диаметр базы, мм.
|
Установочные пальцы стандартизованы: короткие цилиндрические по ГОСТу 12209-66 (рис. 4.11, а), а короткие срезанные по ГОСТу 12210-66 (рис. 4.11, б).
Базирование на коническую поверхность с малой конусностью целесообразно применять только для деталей с базами, обработанными не грубее 7-го квалитета по СТ СЭВ (2-й класс точности по ГОСТУ); в противном случае оправки получаются недопустимо длинными.
При данном способе деталь главной базой — отверстием — надевается на оправку с малой конусностью 1:К (рис. 4.12). Величина конусности 1:К принимается в пределах 1:3000...1:1000.
Базирование с помощью самоцентрирующего устройства аналогично базированию деталей наружной цилиндрической поверхностью в самоцентрирующее устройство. Могут быть использованы самоцентрирующие устройства тех же конструктивных типов, например, с тремя кулачками (рис. 4.13, а), с разжимным кольцом (рис. 4.13, б).
При данном способе базированияпогрешность оси базы равна нулю.
ПРИСПОСОБЛЕНИЙ
Правила закрепления деталей
При закреплении детали или изделия в приспособлении необходимо соблюдать следующие основные правила:
– нельзя нарушать положение детали, достигнутое при ее базировании;
– закрепление должно быть надежным, чтобы во время сварки положение детали сохранялось неизменным;
– возникающее при закреплении смятие поверхности детали, а также ее деформации должны быть минимальными и находиться в допустимых пределах.
Правила закрепления выполняются, если выбраны рациональные схема закрепления и величина зажимного усилия Р. Выбор схемы закрепления следует производить одновременно с разработкой способа ее базирования. При определении относительного расположения опорных элементов, точек приложения и направления зажимных усилий необходимо руководствоваться следующим: для обеспечения контакта детали с опорным элементом и устранения возможного ее сдвига при закреплении зажимное усилие следует направлять перпендикулярно к поверхности опорного элемента (в отдельных случаях зажимное усилие можно направлять так, чтобы деталь одновременно прижималась к поверхности двух опорных элементов); для уменьшения смятия поверхностей детали при закреплении нужно уменьшать удельное давление в местах контакта путем рассредоточения зажимного усилия; при расчете усилий зажима следует вводить коэффициент запаса К = 3...5, учитывающий неточность расчетов, непостоянство условий сварки и установки изделия.
|
Приводы зажимных устройств
Пневматические приводы состоят из пневмодвигателей, пневматической аппаратуры и воздухопроводов. Энергоносителем в пневмоприводе является сжатый воздух с давлением q = 0,4...0,6 МПа (4…6 кгс/см2).
Пневматические силовые приводы разделяют по виду пневмодвигателя:
а) на пневматические цилиндры с поршнем (поршневые);
б) пневматические камеры с диафрагмами (диафрагменные);
в) пневматические шланги (пневмошланговые).
Пневматические силовые приводы изготовляют одно- и двухстороннего действия. У двигателей одностороннего действия обратный ход осуществляется пружиной, таким образом обеспечивается экономия сжатого воздуха до 30…40%, однако их габариты увеличиваются из-за установки пружины. В двигателях двухстороннего действия обратный ход осуществляется также сжатым воздухом. Они применяются в случаях, когда при зажиме и разжиме детали требуется большая сила, например, в приспособлениях с самотормозящими зажимными устройствами.
Достоинства пневмодвигателей: значительное сокращение времени на зажим и разжим деталей вследствие быстроты действия (0,5…1,2 с), постоянство силы зажима, возможность регулировали силы зажима, простота управления.
Недостатки: недостаточная плавность перемещения рабочих элементов, небольшое давление сжатом воздуха, относительно большие размеры пневмодвигателей для получения значительных сил на штоке.
Пневматические поршневые приводы двухстороннего действия регламентированы ГОСТом 15608-81 и выпускаются в следующих исполнениях:
а) по способу торможения:
1 – без торможения,
2 – с регулируемым торможением в конце хода;
б) по виду крепления:
0 – на удлиненных стяжках,
1 – на лапах,
2 – на переднем фланце,
3 – на заднем фланце,
|
4 – на пружине,
5 - на цапфах;
в) по выполнению конца штока:
1 – с наружной резьбой,
2 – с внутренней резьбой;
r) по присоединительной резьбе для подвод воздуха:
1 – с метрической резьбой,
2 – с конической резьбой.
Условные графические обозначения цилиндров должны соответствовать указанным на рис. 5.15.
Например, цилиндр без торможения, с креплением на удлиненных стяжках, с наружной резьбой на конце штока, с метрической присоединительной резьбой для подвода воздуха, диаметром D = 100 мм и ходом поршня S = 1000 мм обозначается так: пневмоцилиндр 1011 – 100х1000 ГОСТ 15608-81.
Основные параметры цилиндров должны соответствовать указанным в табл. 5.2.
Таблица 5.2
Основные параметры пневмоцилиндров (ГОСТ 15608-81)
Диаметр, мм | Статическое усилие на штоке (Н) при давлении воздуха в пневмосети 0,4 МПа | ||
цилиндра | штока | толкающее | тянущее |
25 | 12 | I60 | 130 |
32 | 250 | 220 | |
40 | 14 | 400 | 350 |
50 | 18 | 640 | 550 |
63 | 25 | 1000 | 900 |
80 | 1750 | 1560 | |
100 | 2700 | 2550 | |
125 | 32 | 4200 | 4000 |
160 | 40 | 7200 | 6800 |
200 | 11400 | 10800 | |
250 | 63 | 17700 | 16500 |
320 | 80 | 30000 | 28000 |
360 | 37600 | 36000 | |
400 | 90 | 46800 | 44500 |
Основные размера цилиндров без торможения с креплением на удлиненных стяжках приведены на рис. 5.16 и в табл. 5.3.
Таблица 5.3
Основные размера цилиндров без торможения с креплением на удлиненных стяжках
D | d | Резьба | B | l, не более | К | К1 | Ход поршня по ГОСТу 6540-68 | |||
наружная | внутренняя | |||||||||
d2 | l | d2 | l | |||||||
25 | 12 | М 10х1,25 | 22 | – | – | 38 | 10 | 92 | 115 | 10…250 |
32 | 45 | 10…320 | ||||||||
40 | 14 | М 12х1,25 | 24 | – | – | 55 | 20 | 98 | 127 | 10…400 |
50 | 18 | М 16х1,5 | 32 | М12х1,25 | 24 | 70 | 24 | 106 | 143 | 10…500 |
63 | 78 | 10…630 | ||||||||
80 | 25 | М 20х1,5 | 40 | М 16х1,5 | 32 | 93 | 28 | 120 | 160 | 10…800 |
100 | 115 | 170 | 10…1000 | |||||||
125 | 32 | М 27х2 | 54 | М 24х2 | 48 | 140 | 30 | 130 | 190 | 10…1250 |
160 | 180 | 33 | 203 | 10…1600 | ||||||
200 | 40 | М 36х2 | 72 | М 30х2 | 60 | 220 | 40 | 142 | 230 | 10…2000 |
250 | 63 | М 42х2 | 84 | М 42х2 | 84 | 275 | 50 | 160 | 255 | |
320 | 80 | М 48х2 | 96 | М 48х2 | 96 | 345 | 67 | 180 | 290 | 10…2500 |
Расчет силовых цилиндров производится по формулам, основанным на известной зависимости силы на штоке Р от диаметра цилиндра D и давления в цилиндре q (расчетное значение q = 0,40 МПа).
В цилиндрах двухстороннего действия при толкающем движении штока
(5.45)
при обратном — тянущем – движении штока
(5.46)
где d — диаметр штока.
В цилиндрах одностороннего действия с возвратной пружиной
(5.47)
Пользуясь этими формулами, можно решить обратную задачу, т.е. определить внутренний диаметр цилиндра D по заданному усилию на штоке Р и давлению сжатого воздуха q.
Коэффициент полезного действия η оценивает потери на трение в манжетах и уплотнениях, а также в направляющих штоках.
Для цилиндров средних размеров (D = 150...300 мм) приближенно можно принять η = 0,85. Однако в ответственных случаях следует непосредственно подсчитывать прямые потери на трение в манжетах поршня и штока /1/.
|
Для уплотнения и поршней, и штоков пневмоцилиндров чаще всего применяются манжеты угловые воротниковые (ГОСТ 6678-72) и V -образные (ГССТ 6969-54), а также кольцо круглого сечения. Все манжеты изготовляются из маслостойкой резины.
Разновидностью пневмоцилиндров являются вращающиеся пневмоцилиндры, которые с помощью воздухоподводящей муфты соединяются с сетью подачи сжатого воздуха (рис. 5.17).
Основные размеры и усилия, вращающихся пневмоцилиндров двухстороннего действия приведены в табл. 5.4 (ГОСТ 21821-76).
Таблица 5.4
Основные размеры и усилия, вращающихся пневмоцилиндров
Обозначение цилиндра | Тип | Основные размеры, мм | Усилие на штоке, Н при давлении воздуха в пневмосети 0,4 МПа | Частота вращения С –1, об/мин | |||||||
D | d 3 | D 4 | L | L 1 | l2 | L 2 | толкающее | тянущее | |||
7020 – 0101 | I | 100 | 25 | 135 | 32 | 125 | 30 | 340 | 2710 | 2540 | 50 (3000) |
7020 – 0103 | I | 125 | 165 | 4230 | 4070 | 50 (3000) | |||||
7020 – 0105 | I | 160 | 200 | 7250 | 6950 | 50 (3000) | |||||
7020 – 0107 | 2 | 160 | 32 | 200 | 205 | 420 | 13820 | 13520 | 50 (3000) | ||
7020 – 0109 | I | 200 | 240 | 125 | 340 | 11300 | 10980 | 50 (3000) | |||
7020 – 0112 | 2 | 200 | 240 | 125 | 420 | 21850 | 21560 | 41,66(2500) | |||
7020 – 0114 | I | 250 | 290 | 40 | 145 | 370 | 17700 | 17050 | 41,66(2500) | ||
7020 – 0116 | 2 | 250 | 45 | 290 | 245 | 40 | 460 | 34300 | 33720 | 33,33(2000) | |
7020 – 0118 | I | 320 | 360 | 145 | 370 | 29000 | 28420 | 33,33(2000) | |||
7020 – 0121 | 2 | 320 | 360 | 50 | 255 | 470 | 56350 | 56450 | 33,33(2000) |
Время срабатывания пневмоцилиндра может быть приближенно подсчитано по формуле
. (5.48)
где D – диаметр цилиндра, см; L – ход поршня, мм; d 0 — диаметр воздухопровода, мм.
Диафрагменные пневмокамеры имеют ряд преимуществ перед пневмоцилиндрами: они проще в изготовлении и дешевле, долговечнее, так как диафрагма работает дольше и надежнее, чем поршневые уплотнения; в камерах практически отсутствует утечка воздуха, так как обе полости изолированы друг от друга; в камерах может быть использован сжатый воздух, более влажный и загрязненный, так как он не соприкасается с трущимися частями. К недостаткам пневмокамер относятся сравнительно малый ход штока (30…60 мм), ограниченный допускаемой деформацией диафрагмы; увеличенный (по сравнению с цилиндром того же усилия) наружный диаметр камеры.
Конструкция диафрагменной пневмокамеры одностороннего действия представлена на рис. 5.18, двухстороннего действия – на рис. 5.19, их размеры приведены в табл. 5.5 и 5.6.
В пневмокамерах применяются диафрагмы автомобильных тормозных камер, выпускаемые специализированными заводами. Материал диафрагм – бензомаслостойкая резина с двумя слоями ткани толщиной 1,8…2 мм.
Так как промышленность выпускает пневмокамеры в крайне ограниченном ассортименте, нередко их проектируют заново (особенно для больших усилий).
Таблица 5.5
Основные размеры диафрагменных пневмокамер одностороннего действия, мм
D | Ход на штоке L | D 1 | Т | Н | l | l1 | d | s | Усилие на штоке (Н) при 0,4 МПа |
175 | 30 | 115 | 132 | 88 | 30 | 35 | М16 | 80 | 2750 |
200 | 35 | 125 | 150 | 94 | 35 | 35 | М16 | 88 | 3250 |
230 | 40 | 140 | 180 | 101 | 35 | 40 | М20 | 120 | 6000 |
Усилие на штоке или диаметр пневмокамер могут быть подсчитаны по формулам, приведённым в табл. 5.7.
Таблица 5.6
Основные размеры диафрагменных пневмокамер двухстороннего действия, мм
D | Ход на штоке L | D 1 | D 2 | Н | d | К | Т | М | Усилие на штоке (Н) при 0,4 МПа |
174 | 40 | 154 | 130 | 122 | М12х1,75 | 17 | 48 | 48 | 3500 |
200 | 40 | 178 | 160 | 137 | М 16х2 | 17 | 56 | 45 | 4800 |
228 | 40 | 204 | 180 | 137 | М 16х2 | 17 | 56 | 45 | 6750 |
Пневмошланговые приводы (рис.5.20) отличаются простотой, портативностью и надежностью действия. Существенными их недостатками являются сравнительно малый рабочий ход и зависимость полезного усилия шланга от степени его сплющивания, т.е. от высоты внутренней полости шланга, а, следовательно, и от рабочего хода шланга.
При давлении воздуха q полезное усилие шланга на 1 мм погонной длины
Q = bq, Н/мм, (5.49)
где b – ширина площадки давления, мм.
Так как шланг армирован тканью и поэтому не может растягиваться по окружности, то в деформированном по рис. 5.20, б шланге приближенно соблюдается геометрическое равенство π d ш = 2 b + π (h+ Δ), откуда
(5. 50)
где h – вертикальный рабочий ход шланга, мм;
Δ – остаточный зазор внутри полости сплющенного шланга в его рабочем состоянии (для зажимных устройств можно принимать Δ = 3... 5 мм).
Если заданными величинами являются q, p и h, то необходимый внутренний диаметр шланга определяется совместным решением уравнений, т.е.
(5. 51)
По имеющимся сортаментам подбирают шланг ближайшего большего диаметра, обычно прорезиненный пожарный рукав. При конструировании пневмошлангового привода следует иметь в виду, что обычный шланг или пожарный рукав при переходе от рабочего состояния (под давлением) в нерабочее (без давления) не может сплющиться самопроизвольно под действием собственного веса, так как этот вес явно недостаточен для преодоления жесткости шланга и тем более для быстрого вытеснения воздуха из него. Поэтому в пневмошланговом приводе, как правило, предусматривается то или иное устройство для быстрого принудительного возврата шланга в нерабочее состояние. Наиболее распространены следующие типы возвратных устройств:
Таблица 5.7
Расчетные формулы для определения исходного усилия,
развиваемого пневмокамерами
Пневмокамера | Эскиз пневмокамеры | Расчетные формулы |
Пневмокамеры одностороннего действия | ![]() | В исходном положении штока
![]() ![]() ![]() ![]() |
![]() | В исходном положении штока.
![]() ![]() ![]() | |
Пневмокамеры двухстороннего действия | ![]() | В исходном положении штока.
![]() ![]() ![]() |
![]() | В исходном положении штока.
![]() ![]() ![]() |
добавочный груз, постоянно действующий на шланг; возвратные пружины (рис. 5.21), всасывающие эжекторы или эксгаустеры, образующие (на короткое время) вакуум в шланге; вспомогательный возвратный шланг-рукав (рис. 5.22). Первые два из этих устройств являются для рабочего шланга нагрузкой, снижающей величину его полезного усилия; возвратные устройства двух других типов не влияют на величину полезного усилия рабочего шланга.
Опыт показал, что для быстрого возврата шланга в нерабочее состояние достаточно усилия Рдоб = 0,05 Q или, в случае всасывающего устройства, достаточно создать разряжение в рабочем шланге примерно 0,02 МПа.
Гидравлические приводы поршневого типа приводятся в действие от отдельного или группового насоса. Гидравлическая установка состоит из электродвигателя, рабочих гидроцилиндров, насоса для подачи масла в цилиндры, бака масла, аппаратуры управления и регулирования, трубопроводов. Рабочей жидкостью служат минеральные масла II-го класса чистоты по ГОСТ 17216-71.
По сравнению с пневматическими гидравлические силовые узлы имеют меньшие габариты вследствие применения более высокого давления масла
(6 МПа и выше).
Недостатками устройства являются наличие трубопроводов для слива выпускаемого из цилиндра масла, а также необходимость работы нагнетательного насоса и электродвигателя в течение цикла зажима.
Гидроцилиндры могут быть одностороннего действия со сплошным (ГОСТ 19897-74) и с полым (ГОСТ 19898-74) штоком, а также двухстороннего действия (ГОСТ 19899-74, в том числе укороченные по ГОСТу 19900-74).
Конструкция и основные размеры гидроцилиндров одностороннего действия со сплошным штоком (ГОСТ 19897-74) на номинальное давление 10 МПа представлены на рис. 5.23 и в табл. 5.8.
Конструкция и основные размеры гидроцилиндров двухстороннего действия на номинальное давление 10 MIIa (100 кгс/см2) по ГОСТУ 19899-74 представлены на рис. 5.24 и в табл. 5.9.
Исходными данными для расчета гидравлических зажимных устройств являются: требуемая сила Р на штоке гидроцилиндра, длина хода поршня L и время рабочего хода поршня t.
Таблица 5.8
Основные размеры гидроцилиндров одностороннего действия
со сплошным штоком, мм (ГОСТ 19897-74)
Обозначение цилиндров | D | D 1 | d | d 1 | L | Ход поршня, l | Усилие теоретическое (Н) при давлении 10 MIIa |
7021– 0061 | 40 | 56 | 22 | М12 | 90 | 12 | 11760,0 |
7021– 0065 | 50 | 67 | 25 | М16 | 100 | 16 | 18453,4 |
7021– 0069 | 63 | 80 | 32 | М20 | 105 | 16 | 29263,0 |
7021– 0074 | 80 | 105 | 36 | М24 | 110 | 16 | 47530,0 |
Для толкающих гидроцилиндров одностороннего действия:
сила на штоке
(5.52)
для тянущих гидроцилиндров
(5.53)
Для гидроцилиндров двухстороннего действия при подаче масла в бесштоковую полость
(5.54)
а при подаче масла в штоковую полость
(5.53)
где D – диаметр поршня гидроцилиндра, мм; q – давление масла на поршень, МПа; η = 0,85…0,9 – КПД цилиндра; Рпруж – сила сопротивления сжатой пружины при крайнем рабочем положении поршня, Н; d – диаметр штока, мм.
Пневмогидравлические приводы позволяют без применения насосных станций и специальной гидросети высокого давления осуществить питание рабочих силовых цилиндров жидкостью (маслом) вместо сжатого воздуха.
Для этого достаточно использовать пневмогидравлические мультипликаторы, подключенные к цеховой сети сжатого воздуха. Схемы питания рабочих гидроцилиндров с помощью простейших беспоршневых мультипликаторов, имеющих коэффициент мультипликации, равный единице, представлены на рис. 5.25 и 5.26. В этих схемах пневмогидравлические мультипликаторы 3 представляют собой простые цилиндрические сосуды, рассчитанные на давление сжатого воздуха до 0,7 МПа, с емкостью, несколько большей, чем суммарный полезный объем всех питаемых рабочих гидроцилиндров.
Таблица 5.9
Основные размеры гидроцилиндров двухстороннего действия, мм
Обозначение цилиндров | D | D 1 | d 1 | d 2 | L | Ход поршня, l | Усилие теоретическое (Н) | |
толкающее | тянущее | |||||||
7021-0121 | 40 | 56 | 22 | М12 | 105 | 12 | 12308,8 | 8684,8 |
7021-0126 | 125 | 32 | ||||||
7021-0129 | 145 | 50 | ||||||
7021-0134 | 175 | 80 | ||||||
7021-0138 | 50 | 67 | 25 | М16 | 110 | 16 | 19237,4 | 14425,4 |
7021-0143 | 125 | 32 | ||||||
7021-0147 | 145 | 50 | ||||||
7021-0152 | 175 | 80 | ||||||
7021-0156 | 63 | 80 | 32 | М20 | 115 | 16 | 30536,8 | 22657,6 |
7021-0161 | 130 | 32 | ||||||
7021-0166 | 150 | 50 | ||||||
7021-0169 | 180 | 80 | ||||||
7021-0174 | 80 | 105 | 36 | М24 | 125 | 16 | 49235,2 | 39268,6 |
7021-0178 | 140 | 32 | ||||||
7021-0183 | 155 | 50 | ||||||
7021-0187 | 185 | 80 | ||||||
7021-0192 | 100 | 125 | 45 | М30 | 125 | 16 | 76930,0 | 61348,0 |
7021-0196 | 140 | 32 | ||||||
7021-0201 | 155 | 50 | ||||||
7021-0205 | 185 | 80 |
Эти сосуды-мультипликаторы должны располагаться в сборочно-сварочной установке выше уровня рабочих гидроцилиндров во избежание попадания в них воздуха. Верхние полости сосудов сообщаются со сжатым воздухом или атмосферой в зависимости от положения воздухораспределительного управляющего крана 5, нижние всегда заполнены маслом и сообщаются с рабочими гидроцилиндрами 2. Таким образом, эти сосуды-мультипликаторы преобразуют энергию сжатого воздуха в энергию сжатой рабочей жидкости без изменения давления.
Схемы питания рабочих гидроцилиндров с помощью поршневых пневмогидравлических мультипликаторов представлены на рис.5.27 и 5.28.
Давление масла в гидроцилиндрах q в этом случае повышается пропорционально соотношению квадратов диаметров мультипликатора:
(5.56)
где q – давление сжатого воздуха в пневмосети, МПа; D 1 – диаметр воздушной полости мультипликатора, мм; D 2 – диаметр жидкостной полости, мм; η – КПД мультипликатора, учитывающий потери на трение поршней и плунжеров, а также потери в трубопроводах, η = 0,85.
Сравнивая две системы питания рабочих гидроцилиндров пневмогидравлическими мультипликаторами – беспоршневыми и поршневыми, необходимо отметить следующее. Первая система отличается предельной простотой конструкции мультипликатора и надежностью его работы, трансформирование энергии сжатого воздуха в энергию жидкость происходит без дополнительных потерь на трение. Недостаток системы – трансформирование энергии газа в энергию жидкости без увеличения ее давления. Следовательно, диаметры рабочих гидроцилиндров будут такими же, как и диаметры пневмоцилиндров, предназначенных для этой цели. Выигрыш в этом случае состоит лишь в обеспечении плавности хода цилиндра. Вторая система позволяет значительно повысить давление жидкости в рабочих гидроцилиндрах. Недостаток системы – сравнительно низкий KПД, равный произведению KПД мультипликатора η м и рабочего цилиндров η ц.
Вакуумные приводы. Принцип работы этих приводов основан на непосредственной передаче атмосферного давления на закрепляемую деталь.
Использование вакуумных зажимных устройств весьма эффективно для крепления заготовок типа пластин из любых материалов. Недостатком их является малое удельное усилие закрепления.
Схемы вакуумных зажимов представлены на рис. 5.29.
Заготовка 1 устанавливается в центрирующую выточку ( см. рис. 5.25,а)или на плоскость (рис. 5.29,б) корпуса приспособления 2, из полости которого удаляют воздух. Заготовка к корпусу приспособления прижимается атмосферным давлением. Герметичность системы обеспечивается уплотнением из круглого или прямоугольного резинового шнура из вакуумной резины. Другой вариант уплотнения в виде резиновой полосы показан на рис. 5.29,б. Остаточное давление q = 0,01...0,045 МПа является оптимальным и применять глубокий вакуум не следует, так как тогда значительно возрастает стоимость привода. Для создания вакуума применяют различные насосы: поршневой одноступенчатый насос создает вакуум 0,005 МПа, ротационный (марки ВМ-I) – 0,015 МПа, а центробежный многоступенчатый – 0,03 МПа.
Величину зажимного усилия Q (Н), развиваемого вакуумным приводом, определяют по формуле
Н (5.57)
где Fп – полезная площадь заготовки, ограниченная уплотнением, мм2; Q и – избыточное давление, равное разности между атмосферным давлением и вакуумом в полости 4, МПа, т.е. qu = 1 – q в, где q в – вакуум в полости, МПа
(q в = 0,001...0,015 МПа); К – коэффициент герметичности вакуумной системы
(K = 0,8...086).
Открепление заготовки осуществляется сообщением полости с атмосферой. Для уменьшения времени срабатывания и расхода энергии объем этой полости должен быть минимальным. Для равномерного прижима тонких деталей на установочной плоскости можно выполнить большое количество мелких тесно расположенных отверстий (см. рис. 5.29,в), и в этом случае закрепление допустимо производить без уплотнения.
Электромагнитные приводы. Принцип действия их основан на том, что магнитный поток, проходящий через деталь, создает силу, препятствующую ее отрыву от приспособления.
Электромагнитные зажимные устройства выполняют преимущественно в виде плит и планшайб, используемых для закрепления стальных и чугунных заготовок с плоской базой. Основные размеры и технические характеристики прямоугольных электромагнитных плит регламентированы ГОСТом 17519-81.
На рис. 5.30 показана схема плиты, в корпусе 1 которой заключены электромагниты 6.
Заготовку 5 устанавливают на крышку 2. В крышке выполнены полюсы 3, окруженные изоляцией 4 из немагнитного материала (латунь, баббит, эпоксипласт). Толщина изоляции обычно не превышает 5 мм. Магнитный поток замыкается через заготовку, проходя через корпус и крышку плиты. Удерживающая сила возникает в местах контакта заготовки с полюсами и крышкой плиты. Она растет до определенного предела с увеличением толщины и площади поперечного сечения заготовки и снижается с увеличением шероховатости базовой поверхности заготовки.
При конструировании электромагнитных зажимных устройств исходными данными являются размеры и конфигурация плиты заготовки в плане, ее толщина, материал и необходимая удерживающая сила Q.
Рекомендуемое расположение полюсов под опорной поверхностью: у плит – параллельное, у планша
|
|
Автоматическое растормаживание колес: Тормозные устройства колес предназначены для уменьшения длины пробега и улучшения маневрирования ВС при...
Историки об Елизавете Петровне: Елизавета попала между двумя встречными культурными течениями, воспитывалась среди новых европейских веяний и преданий...
Таксономические единицы (категории) растений: Каждая система классификации состоит из определённых соподчиненных друг другу...
История создания датчика движения: Первый прибор для обнаружения движения был изобретен немецким физиком Генрихом Герцем...
© cyberpedia.su 2017-2024 - Не является автором материалов. Исключительное право сохранено за автором текста.
Если вы не хотите, чтобы данный материал был у нас на сайте, перейдите по ссылке: Нарушение авторских прав. Мы поможем в написании вашей работы!