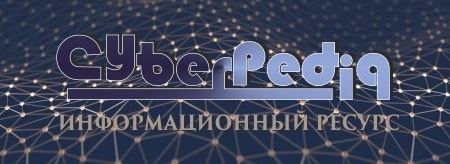
Папиллярные узоры пальцев рук - маркер спортивных способностей: дерматоглифические признаки формируются на 3-5 месяце беременности, не изменяются в течение жизни...
История создания датчика движения: Первый прибор для обнаружения движения был изобретен немецким физиком Генрихом Герцем...
Топ:
Теоретическая значимость работы: Описание теоретической значимости (ценности) результатов исследования должно присутствовать во введении...
Отражение на счетах бухгалтерского учета процесса приобретения: Процесс заготовления представляет систему экономических событий, включающих приобретение организацией у поставщиков сырья...
Устройство и оснащение процедурного кабинета: Решающая роль в обеспечении правильного лечения пациентов отводится процедурной медсестре...
Интересное:
Аура как энергетическое поле: многослойную ауру человека можно представить себе подобным...
Мероприятия для защиты от морозного пучения грунтов: Инженерная защита от морозного (криогенного) пучения грунтов необходима для легких малоэтажных зданий и других сооружений...
Искусственное повышение поверхности территории: Варианты искусственного повышения поверхности территории необходимо выбирать на основе анализа следующих характеристик защищаемой территории...
Дисциплины:
![]() |
![]() |
5.00
из
|
Заказать работу |
|
|
Введение
Настоящий конспект предназначен для подготовки (самоподготовки) работников, выполняющих сервисное обслуживание центробежних компрессоров природного газа типа НЦ-16 в условиях компрессорных станций ЕСГ ПАО «Газпром», а также для использования руководителей занятий при проведении технической учебы с ремонтным персоналом оборудования КС.
Центр обучения кадров
г. Брянск - 2015 год
НАЗНАЧЕНИЕ НАГНЕТАТЕЛЯ НЦ-16
Рост добычи газа и необходимость его транспортировки по магистральным трубопроводам большой протяженности требует специальных компрессорных станций, обеспечивающих движение газового потока с определенными расходными характеристиками,
Наличие гидравлического сопротивления трубопроводов приводит к снижению давления и скорости определяющих величину расхода газа, из-за потерь энергии на трение. Возмещение потерь энергии производится путем дополнительного сжатия газа на компрессорных станциях с помощью нагнетателей. При этом нагнетатель осуществляет повышение давления и обеспечивает необходимую расходную характеристику газа в трубопроводе.
Нагнетатель НЦ-16 является центробежной машиной непрерывного действия предназначенной для сжатия газа и обеспечивающей большие расходы.
ОСНОВНЫЕ ТЕХНИЧЕСКИЕ ДАННЫЕ НАГНЕТАТЕЛЯ
Тип и характеристика нагнетателя
1.1. Условные обозначения ______________________________________________________ - НЦ-16/76-1,44
1.2. Тип _______________________________________________________- центробежный, двухступенчатый с вертикальным разъемом
1.3. Направление вращения ротора _________________________________- против часовой стрелки
Основные параметры нагнетателя
|
2.1. Производительность
- приведенная к 2880К (150С)
и давлению 0,101 МПа
(1.033 кгс/см2), м3/с ____________________________________________-373,25 (32,68 млн. м3/сутки)
- приведенная к 2930К (200С)
и давлению 0,101 МПа, м3/с______________________________________-384,82 (33,25 млн. м3/сутки)
- по условиям всасывания, м3/с ___________________________________- 6,59
м3/мин ____________________________________-394,4
2.2. Давление газа
- на входе в нагнетатель, МПа ___________________________________- 5,17 (52 кгс/см2)
- на выходе из нагнетателя, МПа _________________________________- 7,45 (76 кгс/см2)
2.3. Степень повышения давления ______________________________________- 1,44
2.4. Политропный КПД нагнетателя
(не менее), %____________________________________________________-83
2.5. Расчетное повышение температуры
газа на режиме, 0С_______________________________________________-31
2.6. Частота вращения ротора
нагнетателя, с-1 (об/мин)__________________________________________-62,5...92,75 (3750...5565)
2.7. Номинальная мощность
при Тн =2880К и Рн =0,101 МПа, квт________________________________-16000
Габариты, масса нагнетателя
3.1. Длина, мм ______________________________________________________- 3695
3.2. Высота, мм _____________________________________________________- 1860
3.3. Масса нагнетателя, кг_____________________________________________ - 27000
Система смазки и уплотнения нагнетателя
4.1. Тип системы смазки ______________________________________________- циркуляционная под давлением с воздушным охлаждением
4.2. Тип системы уплотнения ___________________________________________- гидравлическая масляная щелевая с плавающими кольцами
4.3. Применяемое масло _______________________________________________- Турбинное ТП-22
ГОСТ 9972-74
4.4. Емкость маслосистемы с маслобаком, м3_____________________________-5,75 (5750 л)
4.5. Емкость маслобака
- рабочая, м3_________________________________________________- 3,5 (3500 л)
- общая, м3 __________________________________________________- 4,3 (4300 л)
4.6. Тарировка бака, см/м3_____________________________________________- 1/0,05 (1/50 см/л)
4.7. Безвозвратные потери масла в системе
смазки и уплотнения кг/с (не более)__________________________________- 1,38*10-4(0,5 кг/ч)
4.8. Температура масла, 0К
- в баке нагнетателя (не менее)__________________________________-288 (150С)
- на входе нагнетателя (не более)________________________________- 328 (550С)
- опорного подшипника №1 (не более)____________________________- 348 (750С) до 800С
- опорного подшипника №2 (не более)____________________________- 348 (750С) до 800С
|
- упорного подшипника ________________________________________- 348 (750С) до 800С
4.9. Мощность трубчатого электронагревателя, (двух) кВт __________________- 10 (20)
4.10. Емкость одного аккумулятора, м3__________________________________- 0,54 (540 л)
4.11. Главный насос смазки
- тип ________________________________________________________- шестеренчатый
- привод _____________________________________________________- от вала нагнетателя
- передаточное отношение привода ______________________________- 0,68
- давление на выходе, МПа _____________________________________- 0,6 (6 кгс/см2)
- производительность, м3/ч _____________________________________- 30,6 (510 л/мин)
- мощность, кВт ______________________________________________- 11
4.12.. Главный насос уплотнения _______________________________________- ЗВ8/100 ГОСТ 29883-75
- тип _______________________________________________________- винтовой
-привод _____________________________________________________- от вала нагнетателя
- передаточное отношение ______________________________________- 0,548
-давление на выходе, МПа _____________________________________- 9,81 (100 кгс/см2)
- производительность, м3/ч _____________________________________- 9,71 (162 л/мин)
- мощность, кВт ______________________________________________- 50,1
4.13. Пусковой насос смазки ___________________________________________ - ЗВ1б/25-22/б,3 Б-2
ГОСТ 29883-75
-тип ________________________________________________________- винтовой
- привод _____________________________________________________- электродвигатель В160-2
- мощность электропривода, кВт_________________________________- 15
- частота вращения, с-1_________________________________________- 48,7 (2920 об/мин)
- давление на выходе, МПа _____________________________________- 0,б3 (6,3 кгс/см2)
- производительность, м3/ч _____________________________________- 22 (367 л/мин)
4.14. Пусковой насос уплотнений _______________________________________- ЗВЗ/100 ГОСТ 29883-/0
- тип ________________________________________________________- винтовой
- привод _____________________________________________________- электродвигатель
- мощность электропривода, кВт ________________________________- 45
- частота вращения, с-1 ________________________________________- 48,7 (2920 об/мин)
- производительность, м3/ч _____________________________________- 11 (184 л/мин)
4.15. Степень фильтрации маслофильтров, мкм
- в системе смазки ____________________________________________- 40
- в системе уплотнений ________________________________________- 20
- на входе в бак _______________________________________________- 25
- на выходе из бака ____________________________________________- 40
- в контуре циркулируемого масла _______________________________-70
4.16. Перепад давления на фильтрах (не более), МПа
- смазки нагнетателя __________________________________________- 0,2(2 кгс/см2)
- уплотнений ________________________________________________- 0,6 (6 кгс/см2)
- в контуре циркулируемого масла ______________________________- 0,2(2 кгс/см2)
- приемных ПНС и ПНУ ______________________________________- 0,03 (0,3 кгс/см2)
|
Корпус нагнетателя
![]() |
С обоих торцов цилиндр закрыт стальными коваными крышками 9,13, осевое положение которых фиксируется разрезными стопорными кольцами 14,15 и кронштейнами 10.
На обеих крышках на наружной поверхности выполнены кольцевые проточки, в которые установлены уплотнительные кольца, герметизирующие внутреннюю полость нагнетателя. В центральном отверстии крышек выполнены проточки, сообщающиеся внутренними каналами со штуцерами подвода масла для смазки подшипников, подвода масла в уплотнения, уравнительной линии, уравнительной линии «масло-газ» на регуляторы перепада давления РПД-2М, слива масла из полости «масло-газ». В вертикальной плоскости выполнены каналы, для вывода из полости между уплотнительными кольцами в крышках.
К передней крышке 13 осуществляется крепление уплотнения 8, корпуса опорного подшипника 18 и его кожуха 20.
К задней крышке 9 с наружной стороны крепятся уплотнения 8, корпус опорно-упорного подшипника 5 и кожух, на котором установлен блок маслонасосов 6. Со стороны нагнетания к крышке крепится улитка 4, которая совместно с внутренней поверхностью образует сборную полость с радиальным выходом. В центральной расточке установлена втулка лабиринтного уплотнения 12 между улиткой и поверхностью разгрузочного диска. Поверхности втулки 12 и улитки, улитки и крышки 9 уплотняются резиновыми кольцами.
|
Крышка 13 совместно с внутренним корпусом 2 образует полость с радиальным входом.
Внутренний корпус
Внутренний корпус (рис.3) состоит из камеры газоприемной 1; диафрагмы 3; аппарата входного направляющего 7; диффузоров 2 и 6 и обратного направляющего аппарата 5.
![]() |
С обратной стороны к газоприемной камере крепится лопаточный диффузор 2 первой ступени нагнетателя. Лопаточный диффузор обеспечивает выравнивание поля скоростей газового потока и способствует преобразованию кинетической энергии движущегося газа в потенциальную. Он состоит из основного диска, профильные лопатки которого выполнены фрезерованием, и вспомогательного.
Соединение конструктивных элементов диффузора осуществляется пайкой. Крепление диффузора 2 к газоприемной камере производится болтами, которые устанавливаются в отверстиях, выполненных в теле лопаток диффузора.
Лопаточный диффузор 6 второй ступени нагнетателя конструктивно выполнен также, и крепится болтами к диафрагме 3 внутреннего корпуса.
В центральной расточке диафрагмы 3 смонтирован и закреплен болтами обратный направляющий аппарат 5. Он является единственным горизонтально-разъемным узлом в конструкции нагнетателя. Такая конструкция статорной части позволяет производить монтаж и демонтаж ротора без извлечения внутреннего корпуса, что значительно упрощает обслуживание нагнетателя. Диафрагма 3 и газоприемная камера 1 соединены между собой болтами.
В центральной расточке газоприемной камеры 1 и обратного направляющего аппарата 5 установлены и закреплены втулки лабиринтных уплотнений с рабочими колесами первой и второй ступеней нагнетателя. Все втулки лабиринтных уплотнений выполнены из материала Ак-6, остальные детали внутреннего корпуса - из высокосортной стали.
Торцевые и диаметральные уплотнения между деталями внутреннего корпуса осуществляются уплотнительными резиновыми кольцами.
В нижней части внутреннего корпуса имеются ролики, на которых он вкатывается в корпус нагнетателя.
Ротор нагнетателя
Ротор (рис.4) представляет собой ступенчатый вал 1, на котором установлены два рабочих колеса 2 и 3, разгрузочный диск 4, две втулки уплотнений 7, диск упорного подшипника 5 и кольцо 6.
|
На приводимом конце вала расположены детали зубчатой муфты: полумуфта 8, обойма зубчатая 10, соединенные между собой призонными болтами 9. На противоположном конце вала имеется шлицевая муфта, с помощью которой передается вращение на блок маслонасосов. Вал выполнен из стали 20Х13.
Рабочие колеса и разгрузочный диск устанавливаются с натягом, что предотвращает поворот этих деталей относительно вала при работе нагнетателя. Сборка этих сопряжений производится путем нагрева колес и разгрузочного диска до температуры 240...3000С. От осевого смещения эти детали фиксируются стопорными кольцами и напрессованными втулками.
Рабочие колеса и разгрузочный диск изготовлены из стали 07Х16Н6. Рабочее колесо состоит из основного 15 и покрывного 14 дисков. В основном диске выполнены профильные лопатки путем фрезерования. Для повышения долговечности на поверхность лопаток и диска на входе в колесо наносится износостойкое покрытие: шликер ВКМ-65.
![]() |
Втулки уплотнений 7 (рис.4) относительно вала уплотняются резиновым кольцом и фиксируются от осевого смещения стопорным кольцом. На их поверхности нанесено износостойкое покрытие.
Упорный диск 5 вместе с дистанционной 12, определяющей осевое расположение диска, распорной 13 втулками и кольцом 6 закрепляются на валу гайкой 11.
Упорный диск 5 является конструктивным элементом упорного подшипника. Осевые нагрузки, возникающие при работе нагнетателя, с помощью упорного диска передаются через опорно-упорный подшипник на корпус нагнетателя.
Кольцо 6, как элемент датчика, позволяет контролировать осевой сдвиг ротора относительно корпуса нагнетателя.
Перед сборкой вал и рабочие колеса подвергаются статической балансировке. Для вала допускается дисбаланс не более 10 г/см, а для колеса - не более 2 г/см на наружном диаметре колеса.
После сборки ротор проходит динамическую балансировку. Допускаемая величина дисбаланса должна быть не более 93 г/см.
Опорный подшипник
Опорный подшипник (рис.6) представляет собой горизонтально-разъемный корпус 1, обе половины которого соединены призонными болтами 8. В центральном отверстии корпуса 1 расположены, пять опорных колодок 7, зафиксированных от проворота штифтами 6. Опорные колодки от смещений в корпусе удерживаются специальными проточками, выполненными в разъемных втулках 4 и 5.
Опорные колодки выполнены из стали с заливкой рабочих поверхностей баббитом Б-83. Диаметральный зазор между колодками и валом является величиной расчетной и обеспечивается в процессе изготовления подшипника (0,14-0,24 мм).
Уплотнение подшипника и вала осуществляется разъемной втулкой 4 и вкладышем 3, на внутренней поверхности, которых выполнены кольцевые проточки, образующие с ответной поверхностью лабиринт. Втулка 4 и вкладыш 3 сделаны из алюминиевого сплава АК-6.
Величины зазоров в уплотнении являются расчетными (0,4-0,46 мм) и определяют расход смазки и температурный режим работы подшипника.
Подвод масла из системы смазки осуществляется через отверстия А в нижней и верхней половинах корпуса.
Контроль температурного режима работы подшипника производится с помощью датчика температуры масла.
![]() |
Опорно-упорный подшипник
Подшипник опорно-упорный (рис.7) воспринимает радиальные и осевые нагрузки ротора нагнетателя. Он состоит из опорного, конструкция которого рассмотрена выше, и упорного подшипников.
Упорный реверсивный, двухсторонний (по осевым нагрузкам) подшипник скольжения состоит из корпуса 8, в котором установлены два упорных пакета, регулировочное кольцо 5 и крышка 7.
Упорный пакет (конструкция левого и правого пакетов одинакова) включает в себя сепаратор 2, в пазах которого расположены упорные колодки 3, пружины 9 и кольцо 1. Сепаратор 2 фиксируется от проворота относительно кольца 1 винтами, а кольцо 1 относительной корпуса 8 штифтами. Для исключения смещения пружин 9 относительно упорных колодок в сепараторе 2 выполнены специальные расточки. Рабочая поверхность колодок 3 залита баббитом.
Осевой зазор между упорным диском ротора и упорными колодками 3 является расчетным (0,28-0,33) и обеспечивается подгонкой толщины регулировочного кольца 5.
Подвод масла из системы смазки к упорным пакетам производится раздельно, для чего в корпусе 8 имеются специальные каналы.
Для уплотнения полости упорного подшипника в крышке 7 установлена стальная втулка 6, рабочая поверхность которой залита баббитом. Зазор между втулкой и валом 0,4-0,46 мм.
Расход масла и температурный режим работы подшипника регулируются алюминиевым кольцом 4 (0,4-0,58 мм). Температура масла контролируется с помощью датчиков.
Корпус упорного подшипника крепится к корпусу опорного с помощью болтов и винтов. На крышке 7 установлены кронштейны для датчиков контроля вибраций ротора нагнетателя.
Бак нагнетателя
Бак предназначен для содержания объема масла, необходимого для нормальной работы систем смазки и уплотнений нагнетателя. За счет этого объема осуществляется заполнение маслом агрегатов систем нагнетателя, их нормальная работа а также возмещение безвозвратных потерь масла в системах. В баке производится предварительный прогрев масла с помощью трубчатых электронагревателей до 288...3030К (15...300С) и очистка его от механических примесей.
Бак нагнетателя (рис. ) представляет собой сварную конструкцию прямоугольной формы, выполненную из листовой стали, емкостью 4,3 м3 (рабочая емкость 3,5 м3). Он установлен на раме блока турбоагрегата в отсеке нагнетателя.
Внутренний объем бака разделен перегородками 1,2,3 на отсеки Б1, В1, Г1, Д1, сообщающиеся между собой.
Отработанное масло сливается в отсек Б1, проходит через сетки и пакеты наклонных перегородок 5, где происходит пеногашение, и через отсеки В1 и Г1 поступает в отсек Д1. В отсеке Д1 расположены заборные клапаны 6, 7 пусковых насосов смазки и уплотнений нагнетателя. В отсеке Г1 находится заборный фильтр 8 главного насоса смазки нагнетателя.
Заполнение (пополнение) и слив масла осуществляется через штуцер Ж1 и И1. При переполнении бака слив масла из него производится через штуцер Е1.
Для подогрева масла на крышке бака установлены два электроподогревателя 10 суммарной мощностью 20 кВт. Днище 11 выполнено наклонным с понижением в сторону сливного штуцера И1. Внутренние полости бака с целью удобства обслуживания имеют лючки, которые закрываются крышками 12,13,14.
Для контроля уровня масла в баке на крышке 9 размещен поплавковый сигнализатор уровня 15, работающий в автоматическом режиме и позволяющий одновременно осуществлять визуальный контроль.
Аккумулятор масла
Аккумулятор масла (рис.1.2.) служит для подачи масла в уплотнения нагнетателя при аварийном останове агрегата.
Аккумулятор представляет собой сварную конструкцию, состоящую из цилиндрического корпуса 1 и двух сферических днищ 2 и 4. Снизу к корпусу 1 приварены две опоры 5, с помощью которых аккумулятор устанавливается на корпусе нагнетателя. К переднему днищу приварен фланец в котором установлен входной штуцер А. Сверху на аккумуляторе расположены штуцер Б с обратным клапаном 6 для входа и выхода газа (воздуха), а также штуцер В для сообщения внутренней полости с указателем уровня 7. В нижней части аккумулятора имеются штуцер Д для соединения с трубопроводом подачи масла в уплотнения нагнетателя и штуцер Г для соединения с трубопроводом слива масла и с указателем уровня.
Обратный клапан 6 предназначен для выпуска воздуха при заполнении аккумуляторов маслом и для сообщения с газовой полостью нагнетателя при аварийном маслоснабжении уплотнений.
Емкость аккумулятора 0,54 м3 (рабочая емкость - 0,50 м3).
Шариковый клапан
Шариковый клапан (обратный) предназначен для заполнения газом аккумулятора при аварийном останове агрегата с целью обеспечения работы систем смазки и уплотнений нагнетателя. Он препятствует образованию газовой подушки в аккумуляторе при заполнении его маслом от пускового насоса смазки,
Клапан состоит (рис.1.3.) из стального корпуса 1, в котором установлены шарик-клапан 3 и втулка 4. Втулка имеет осевое и продольное отверстия. Её положение в корпусе 1 может фиксироваться с помощью винта 2. Для нормальной работы клапана нужно обеспечить необходимый зазор А между конической поверхностью седла корпуса 1 и шариком 3.
Клапан работает следующим образом: при заполнении гидроаккумулятора маслом вытесняемый газ будет выходить через клапан.
Движение потока газа приводит к возникновению сил давления, действующих на шарик. Канал, образованный конической поверхностью корпуса клапана и сферической поверхностью шарика, представляет собой сужающуюся щель, в которой скорость потока значительно возрастает, а давление снижается.
На шарик со стороны конической поверхности втулки 4, благодаря осевому отверстию, действует давление потока, скорость которого равна нулю. В результате разниц давлений, действующих на шарик, появляется результирующая сила, направленная вверх. Пока через клапан движется газ, результирующая сила оказывается меньше силы шарика и клапан остается открытым. Как только аккумулятор оказывается заполненным и через клапан начинает двигаться масло, имеющее гораздо большую плотность, перепад давления на клапане резко увеличивается. Величина результирующей силы, действующей на шарик, становится больше силы тяжести шарика. Клапан закрывается. Под действующим перепадом давления масла и газа клапан остается в закрытом положении. Открытие клапана произойдет как только давление газа за аккумулятором и масла в аккумуляторе начнет выравниваться. Шарик 3 под действием силы тяжести опустится на коническую поверхность втулки 4, открывая доступ газа во внутреннюю полость аккумулятора.
Клапан предохранительный
Клапан предохранительный (рис.1.6.) предназначен для ограничения величины давления за главным и пусковым насосами уплотнения. Величина настройки клапанов соответственно составляет:
для ГПА-Ц-16/76_____________- 8,5 МПа и 7,5 МПа.
для ГПА-Ц-16/100____________- 10,0 МПа и 8,0 МПа.
Клапан предохранительный состоит из стального корпуса 8, внутри которого установлены седло клапана 6 с клапаном 5. Сила прижатия клапана 5 к седлу 6 обеспечивается редукционной пружиной 9, регулирование которой осуществляется винтом 2.
Обратный клапан 7 служит затвором, предотвращающим стекание масла из системы в сливную магистраль и предохраняющим насосы от обратного вращения давлением масла в моменты пуска и останова агрегата. Клапан 7 прижимается к своему седлу 10 пружиной 11 с небольшим усилием, необходимым для ориентирования его по посадочному месту.
При работе насосов масло, отжимая обратный клапан 7, движется от входного штуцера к выходному. Как только давление масла превысит величину настройки силы давления, действующие на клапан 5, оказываются больше усилия редукционной пружины 9. В результате разницы сил клапан 5 открывается от седла 6 и осуществляет перепуск части масла через диаметральные отверстия направляющей втулки 12 и штуцер слива.
Слив масла будет осуществляться до тех пор, пока давление масла не понизится до величины настройки. Тогда усилием редукционной пружины 9 клапан 5 опять возвратится на седло 6.
Маслоотводчик
Маслоотводчик (рис.1.7.) предназначен для дренирования масла высокого давления, поступающего в газовую полость уплотнения нагнетателя и для возвращения этого масла в бак.
Маслоотводчик представляет собой сварной сосуд, состоящий из корпуса 2 и днища 6. НА днище 6 установлен поплавок 3 с рычажной системой 4 и клапаном 5 устройство с золотником 10. В зависимости от уровня масла в маслоотводчике поплавок 3 перемещается вверх или вниз, открывая или закрывая при помощи рычажной системы 4 клапан 5.
С целью уменьшения массы поплавка 3 и рычажной системы 4 на работу клапана в конструкции маслоотводчика предусмотренна регулировочная пружина 7, за счет которой уравновешивается основная масса попловка и рычагов.
Масло из уплотнения нагнетателя подводится к маслоотводчику через штуцер Г. Через штуцер В маслоотводчик соединен с уравнительной линией «масло-газ».
При отсутствии масла в маслоотводчике клапан закрывает слив через штуцер Б. Если в таком положении в маслоотводчике появится газ под давлением, то выход его в атмосферу оказывается невозможен, так как сливное отверстие закрыто. Наполнение маслоотводчика маслом сопровождается всплытием поплавка 3. Рычажная система 4 начинает открывать сливное отверстие в клапане 5. С этого момента в маслоотводчике поддерживается определенный уровень масла и давление в нем и уплотнениях выравнивается. Величина площади поперечного сечения сливного отверстия устанавливаются в зависимости от количества масла в корпусе маслоотводчика.
Слив масла из маслоотводчика, при регламентных и ремонтных работах, осуществляется через штуцер А открытием вентиля 1.
Дегазатор масла
Дегазатор масла (рис.1.8.) предназначен для окончательного удаления газа из масла, поступающего из системы уплотнений нагнетателя.
Масло из маслоотводчика подается через штуцер А и трубопровод 2 в стакан 3 дегазатора. При наполнении стакана масло переливается через его верхний край и стекает на змеевик 4. Через штуцер Б в змеевик 4 подается горячий воздух. Нагреваясь, масло частично освобождается от газа и тонкой пленкой стекает по наклонным лоткам 8 испарителя 7, где происходит окончательное отделение газа.
Дегазированное масло скапливается в нижней части корпуса 1, откуда поступает в бак нагнетателя. Корпус дегазатора имеет наклонное днище 9, на котором смонтировано смотровое окно 10 со сливным штуцером Г.
Газ, выделяющийся на всем пути движения масла через каплеуловители 5 и штуцер Д, отсасывается эжектором. Каплеуловители представляют собой последовательно установленные конусы, выполненные из перфорированного листа.
Регулятор перепада давления
Регулятор перепада давления «масло-газ» (Рис.1.9) предназначен, для поддержания избыточного давления масла, идущего на поддув уплотнения нагнетателя, в пределах 0,16...0,2 МПа (1,6...2,0 кг/см2).
Конструктивно регулятор выполнен в виде агрегата с корпусом 1 и штуцерами подвода А и слива Б масла из системы уплотнения. В корпусе регулятора устанавливается гильза (втулка) 2, имеющая продольные окна В для прохода сливаемого масла. Внутри гильзы размещается двух кромочный пустотелый золотник с рабочими поясками 3. Золотник внутренней резьбой ввернут на шпильку 4 и законтрен гайкой 5. Герметизация полости регулятора со стороны гайки осуществляется колпачком 6. Шпилька 4 ввернута в центральную часть подвижного элемента 7 регулятора, которым осуществляется крепление упругой мембраны 8 по внутреннему диаметру. По наружному диаметру мембрана защеплена двумя кольцевыми элементами 9. На подвижный элемент опирается пружина 10 регулятора, усилие затяжки которой определяется положением опорной шайбы 11 на регулировочном винте 12. Пружинная полость регулятора образованная днищем и цилиндрическим стаканом с помощью фланцевого соединения и переходника 13 крепится к корпусу регулятора.
Регулятор работает следующим образом. Масло из системы уплотнения по штуцеру А подводится во внутреннюю полость корпуса 1 и к подвижному элементу 7. С противоположной стороны на подвижный элемент действует сила давления газа, подводимого в пружинную полость регулятора и сила пружины 10. Поэтому, если сила давления масла не превышает суммарного усилия от давления газа и пружины, золотник рабочими поясками 3 перекрывает слив масла из магистрали системы уплотнения. Давление в системе увеличивается за счет подачи масла работающим насосом.
При увеличении разности давления масла и газа до 0,16...0,2 МПа, золотник открывает слив масла из системы, ограничивая дальнейшее увеличение давления масла. В выходной магистрали Б установлен дроссель, выполненный в виде винта цилиндрической частью перекрывающего часть площади проходного сечения сливной магистрали, предназначен для установки давления в напорной линии при отсутствии газа в контуре нагнетателя (Заводская настройка 5 кг/см2 при расходе 250 л/мин).
Золотник 3 должен выступать на 5 мм ниже втулки 2. Регулировку РПД производить при давлении газа в контуре 3 – 5 кг/см2.
Блок маслонасосов
Блок маслонасосов со встроенным редуктором (рис.1.10) предназначен для обеспечения маслом систем смазки и уплотнений нагнетателя. Он представляет собой работающие совместно шестеренчатый насос смазки и трехвинтовой насос уплотнений ЗВ-8/100. Привод блока маслонасосов осуществляется от вала ротора.
Блок маслонасосов состоит из чугунного корпуса 1, в котором расположены редуктор и шестеренчатый насос. Корпус 1 с внутренней стороны закрыт крышкой 3, а с наружной к нему крепится трехвинтовой насос 2.
Крутящий момент от ротора нагнетателя через полумуфту 4 и торсионный вал 5 передается на ведущую вал-шестерню 6, с неё на ведомые вал-шестерню 7 и шестерню 8.
Вал-шестерня 7 благодаря внутреннему шлицевому зацеплению передает вращение на вал трехвинтового насоса уплотнений, а шестерня 8 - на вал насоса смазки.
Шестерни редуктора и насоса смазки установлены на подшипниках скольжения. Смазка подшипников скольжения насоса смазки осуществляется за счет давления в самом маслонасосе. Смазка подшипников скольжения редуктора, зубчатых и шлицевых соединений производится через сверления в корпусе 1 и трубопроводы, соединенные с нагнетательным патрубком насоса смазки.
Для рассмотрения работы шестеренчатого насоса обратимся к рис.1.11. Шестеренчатый насос с наружным зацеплением представляет собой пару одинаковых шестерен 1 и 7, находящихся в зацеплении и помещенных в корпус 13. Стенки корпуса 13 охватывают шестерни по внешней поверхности с минимальными зазорами. Втулки 2 и 12, 5 и 8, являющиеся подшипниками скольжения ведущей 1 и ведомой
Рисунок 1.10
7 шестерен, обеспечивают их торцевое уплотнение. По обе стороны зацепления 6 в корпусе 13 имеются полости подвода А и отвода Б, соединенные с линиями высокого Р2 и низкого Р1 давлений.
При выходе шестерен из зацепления происходит увеличение объема между зубьями и за счет создаваемого разряжения в полость подвода А поступает масло по линии с давлением Р1. Поступившее
в полость А масло захватывается шестернями и в виде дискретных объемов С переносится в полость отвода Б. При входе шестерен в зацепление происходит уменьшение объема между зубьями и вытеснение масла в линию с давлением Р2. Обратному перетеканию масла из полости Б в полость А препятствует высокое гидравлическое сопротивление зазоров между зубьями шестерен и корпусом. Для уменьшения перетекания масла по торцевым зазорам часто применяется гидравлический поджим боковых втулок. С этой цель в полость Д подводится масло под давлением Р2. Начальный поджим втулок 8 и 12 производится пружинами 10. Для самоориентации шестерен 1 и 7 между втулками, а также для отвода утечек масла, области 4 и 9 соединены с полостью, находящейся под давлением Р1.
Развитые поверхности трения вызывают значительные механические потери, поэтому КПД шестеренчатых насосов наружного зацепления невысок и не превышает 0,6...0,7.
Работу трехвинтового насоса рассмотрим по рис.1.12. Трех винтовой насос имеет ведущий 1 и два ведомых 3 винта. Винты образованы тремя двузубыми шестернями с циклоидальным зацеплением, имеющими начальные окружности диаметром d н. Боковые поверхности зубьев образованы циклоидами, а периферийные - цилиндрами, скользящими по поверхности корпуса 4.
Находясь в зацеплении, винты образуют изолированные объемы (видимая часть границы одного из объемов заштрихована и обозначена а, б, в, г, д, е, ж, з, и, к). Теоретически объемы полностью отделены друг от друга. Однако, на некоторых участках объемов, в местах сопряжения боковых поверхностей зубьев, разделение осуществляется не протяженными щелями, а линиями касания. Поэтому для создания насосов с малыми утечками точность изготовления винтов должна быть высокой.
При вращении винтов объемы перемещаются поступательно. В начале рабочего цикла каждый из них соединяется с полостью подвода масла, а в конце - с полостью отвода, куда перенесенное масло вытесняется боковыми поверхностями 7 винтов.
В винтовых насосах имеют место только внутренние утечки. В насосах высоких давлений уменьшения утечек, так как они происходят вдоль поверхностей зацепления, достигают путем удлинения винтов.
Одно из преимуществ винтовых насосов заключается в том, что зацепление ведущего и ведомых винтов не является силовым. Силы давления масла, действующие на боковые поверхности зубьев ведомых винтов со стороны полости отвода, стремятся вращать их в том же направлении, что и ведущий винт.
Осевые силы, являющиеся результатом разницы давлений в полостях подвода и отвода, уравновешиваются гидростатически подводом по каналам 2 во внутреннюю полость подпятников 6 под торцы винтов 1 и 3 масла под давлением Р2.
Радиальные силы, отталкивающие ведомые винты от ведущего, воспринимаются корпусом 4. Механические потери сводятся к трению винтов о корпус, трению в зацеплении и в подшипниках. При этом объемный КПД достигает у насосов высокого давления (до 25 МПа) 0,7...0,8.
Благодаря удобному подводу, обеспечивающему доступ масла к входу в винты с минимальными потерями, насосы обладают хорошей всасывающей способностью.
Преимуществами винтовых насосов является малая неравномерность подачи, отсутствие пульсации давления и бесшумность работы. Это объясняется тем, что несмотря на дискретный характер переноса масла, благодаря разделения перемещаемых объемов линиями контакта, а не протяженными щелями, вытеснение масла в полость отвода осуществляется непрерывно.
Работа масляной системы
Основными узлами масляной системы (рис.2.1) являются:
- маслобак 1 с устройствами очистки, подогрева, подачи и слива масла;
- насосы ПНС 2, ГНС 16, ПНУ 25 и ГНУ 15 с входными фильтрующими сетками и обратными клапанами;
- фильтры ФСН 4 и ФУН 19 очистки масла с входными и выходными вентилями;
- редукционные клапаны 3,17,18;
- аккумуляторы пневмогидравлические 11;
- регуляторы перепада давления 13;
- аппараты воздушного охлаждения масла 7 с устройствами подогрева масла;
- маслоотводчики 23 и дегазатор масла 24;
- регулятор температуры масла 5;
- соединительные магистрали масла, газа, воздуха и дренажной системы.
Для смазки подшипников и торсионного вала масло забирается из бака 1 главным шестеренчатым насосом 16, вращающимся от привода ротора нагнетателя, или пусковым насосом 2 и подается к аппаратам воздушного охлаждения 7, после чего направляется к регулятору температуры 5. Для выпуска воздуха из системы при её заполнении маслом, а также для доступа воздуха в систему при сливе масла установлены обратные клапаны 8. Слив масла из системы производится через электромагнитные вентиля 6 по сигналу системы пожаротушения или вручную. Для разогрева масла при пуске агрегата в условиях низких температур в АВО масла преду
|
|
Археология об основании Рима: Новые раскопки проясняют и такой острый дискуссионный вопрос, как дата самого возникновения Рима...
История развития пистолетов-пулеметов: Предпосылкой для возникновения пистолетов-пулеметов послужила давняя тенденция тяготения винтовок...
Индивидуальные и групповые автопоилки: для животных. Схемы и конструкции...
Типы оградительных сооружений в морском порту: По расположению оградительных сооружений в плане различают волноломы, обе оконечности...
© cyberpedia.su 2017-2024 - Не является автором материалов. Исключительное право сохранено за автором текста.
Если вы не хотите, чтобы данный материал был у нас на сайте, перейдите по ссылке: Нарушение авторских прав. Мы поможем в написании вашей работы!