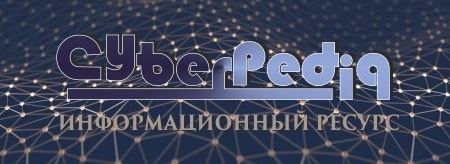
Автоматическое растормаживание колес: Тормозные устройства колес предназначены для уменьшения длины пробега и улучшения маневрирования ВС при...
История развития пистолетов-пулеметов: Предпосылкой для возникновения пистолетов-пулеметов послужила давняя тенденция тяготения винтовок...
Топ:
Основы обеспечения единства измерений: Обеспечение единства измерений - деятельность метрологических служб, направленная на достижение...
Определение места расположения распределительного центра: Фирма реализует продукцию на рынках сбыта и имеет постоянных поставщиков в разных регионах. Увеличение объема продаж...
Техника безопасности при работе на пароконвектомате: К обслуживанию пароконвектомата допускаются лица, прошедшие технический минимум по эксплуатации оборудования...
Интересное:
Берегоукрепление оползневых склонов: На прибрежных склонах основной причиной развития оползневых процессов является подмыв водами рек естественных склонов...
Аура как энергетическое поле: многослойную ауру человека можно представить себе подобным...
Национальное богатство страны и его составляющие: для оценки элементов национального богатства используются...
Дисциплины:
![]() |
![]() |
5.00
из
|
Заказать работу |
|
|
Основными инструментами для сборки резьбовых соединений являются ручные ключи и отвертки. При существующей разнообразной конфигурации головок резьбовых крепежных деталей грань между ключами и отвертками практически стерлась, однако до сих пор принято называть отвертками инструменты, у которых часть, входящая в готовку винта (шлиц, гнездо), представляет собой плоское или крестообразное лезвие. Практически один и тот же инструмент является ключом и отверткой при смене рабочего наконечника.
По способам контроля крутящего момента ключи (отвертки) можно разделить на несколько видов: 1) динамометрические, которые снабжены шкалой и стрелкой (или другим устройством), непрерывно показывающей значение момента, прикладываемого при затяжке резьбового соединения; 2) предельные, отличающиеся тем, что при достижении определенного момент затяжки в резьбовом соединении они отключаются (разновидностью являются ключи с регулируемым моментом); 3) ключи, конструкция которых не предусматривает ограничения крутящего момента.
По способам манипулирования во время работы ключи подразделяются на: переставляемые во время процесса завертывания (затяжки) резьбовой детали или ключи при работе с которыми необходим перехват руки оператора; не требующие перестановки или перехвата во время процесса затяжки резьбовой детали. В последнюю группу входят следующие ключи: с храповым механизмом (трещоточные); с обгонной муфтой; со специальной конструкцией зева, позволяющей отводить ключ, не снимая его с головки детали; нажимного действия (с винтовыми канавками), к которым прикладывается не окружное усилие, а осевая сила, коловороты (требующие работы двумя руками).
|
По устройству головки (зева) ключи подразделяются на: торцовые; с открытым зевом; с регулируемым зевом; кольцевые (с закрытым зевом); рожковые; трубные (накидные, рычажные, цепные).
Динамометрические ключи используют непосредственно для контролируемой затяжки или для контроля момента затяжки при работе ручными резьбозавертывающими машинами или гаечными ключами.
В машиностроении неподвижные и подвижные разъемные соединения очень часто выполняются посредством винтов, болтов с гайками и шпилек (рис. 45). Технология сборки таких резьбовых соединений состоит в последовательном выполнении следующих операций: установка и взаимная ориентация скрепляемых изделий; установка в отверстие крепежных деталей и их наживление (на 2-3 витка резьбы); завинчивание и затяжка с заданной осевой силой или крутящим моментом; контроль затяжки и стопорение крепежных легален (при необходимости).Такая последовательность наиболее полно подходит для сборки винтовых соединений (рис. 45а). При сборке болтовых соединений (рис. 45б) после установки болта в гладкое отверстие его необходимо удерживать от выпадения и проворачивания. Затем надевают шайбу, наживляют гайку и далее выполняют сборку в соответствии с вышеприведенной последовательностью. При сборке шпилечных соединений (рис. 45 в) в одно из скрепляемых изделий ввинчивают с натягом шпильки, контролируют момент затяжки и перпендикулярность относительно плоскости разъема.
Рисунок 45. Резьбовые соединения
Дальнейшая последовательность сборки аналогична сборке болтовых соединений. Для ввинчивания шпилек в скрепляемые детали применяют типовые патроны, которые по способу захвата бывают шариковые, роликовые и резьбовые, а по способу вращения — реверсивные и нереверсивные.
Шпоночное соединение образуется шпонкой - стержнем, находящимся одновременно в пазах вала и установленной на него детали. Шпонки служат для передачи крутящего момента от вала к ступице, установленной на нем детали или наоборот, от этой детали к валу. Кроме этого шпонки фиксируют на валу положение детали в осевом направлении.
|
По условиям эксплуатации шпоночные соединения подразделяются на напряженные и ненапряженные. Напряженными называют соединения, в которых при отсутствии внешних сил и моментов постоянно действуют внутренние силы упругости, возникающие в результате предварительной затяжки.
В зависимости от конструкции различают шпоночные соединения с призматическими, сегментными, направляющими, скользящими и клиновыми шпонками, каждое из которых имеет свои преимущества и недостатки.
Рисунок 46. Последовательность сборки шпилечного соединения.
Шлицевое соединение образуют выступы (зубья) на валу, входящие в соответствующие впадины (шлицы) в ступице. Рабочими поверхностями являются боковые стороны выступов. Выступы на валу выполняют фрезерованием, строганием или накатыванием в холодном состоянии профильными роликами по методу продольной накатки. Впадины в отверстии ступицы изготовляют протягиванием или долблением. Условно можно представить шлицевое соединение, как многошпоночное соединение, у которого шпонки выполнены как одно целое с валом. Основное назначение шлицевых соединений - передача вращающего момента между валом и ступицей. При этом ступица может быть закреплена на колесе, фланце, шкиве, ролике или другом валу (карданный вал). Шлицевые соединения стандартизованы и широко распространены в машиностроении.
Рисунок 47. Шлицевое соединение
Перед сборкой шпоночных соединений проверяют поверхности собираемых деталей и устраняют забоины, заусенцы, задиры и другие дефекты. Отверстия насаживаемой детали центрируют относительно вала по его поверхности. При посадке с натягом применяют специальные приспособления, а в случае необходимости нагревают охватывающую деталь. Сборку соединения контролируют путем покачивания детали на валу, перемещения ее вдоль вала, а также определения биения плотной посадки шпонок.
При сборке соединения при помощи клиновой шпонки необходимо следить за тем, чтобы шпонка плотно прилегала ко дну паза вала и втулки закрепляемой детали. Шпонка должна иметь зазоры по своим боковым стенкам. Уклоны на рабочей поверхности шпонки и в пазу втулки должны совпадать, иначе деталь будет сидеть на валу с перекосом. Точность посадки шпонки проверяется щупом с обеих сторон ступицы. При этом проверяют плотность между дном паза ступицы и рабочей гранью шпонки. Наличие зазора с одной из сторон свидетельствует о несовпадении уклона шпонки с уклоном шпоночного паза в ступице.
|
Шлицевые соединения разделяют на соединения с прямобочным, эвольвентным и треугольным профилем шлицев. Наиболее широко в машиностроении распространены шлицевые соединения с прямобочными шлицами. Контроль прямобочных шлицевых деталей осуществляют обычно комплексным методом, реже по элементам. Для комплексного контроля шлицевых втулок в цеховых условиях применяют комплексные шлицевые калибры-пробки, а для шлицевых валов — комплексные шлицевые калибры-кольца. Комплексная шлицевая пробка с прямобочным профилем зуба показана на рис. 48. Контроль шлицевой втулки осуществляют по прохождению через шлицевое отверстие (рис. 48, а) комплексного калибра (рис. 48,б). Его прохождение означает, что размеры наружного D и внутреннего d диаметров втулки и ширины впадины b не меньше их наименьших предельных размеров. Одновременно проходной шлицевой калибр контролирует также правильность расположения впадин втулки и допускаемые отклонения их формы от прямолинейности и параллельности относительно оси втулки. Для обеспечения этого требования при расчете размеров калибра учитывают допускаемые отклонения как самих размеров, так и отклонений формы и расположения шлицев втулки.
Рисунок 48. Комплексные шлицевые калибры-пробки
Основы безопасности при сборке разъемных соединений.
1. Рабочее место должно содержаться в чистоте.
2. Рабочий инструмент должен находиться в исправном состоянии.
К инструменту предъявляются следующие требования;
а) гаечные ключи должны иметь неразработанный зев и соответствовать размерам гаек. Применять рычаги к ключам и подкладки между зевом и гайкой запрещается;
б) молотки и кувалды должны быть хорошо насажены на ручки и не иметь наклепа на ударной части;
в) на напильники и шаберы должны быть насажены деревянные ручки с кольцами;
|
г) зубила должны быть правильной формы и не иметь наклепа.
3. Встречная рубка металла и зачистка швов не допускается.
4. Рубку кромок заклепок и болтов слесарь обязан производить
осторожно, чтобы отскочившие куски металла не вызвали травм. Сам
слесарь должен пользоваться защитными сетчатыми очками.
5. Проверка пальцем совпадения отверстий в деталях при сборке
категорически запрещается.
Порядок проведения занятия
1. Ознакомиться с настоящим описанием.
2. Изучить инструкцию по охране труда при сборке разъемных соединений.
3. Изучить основные понятия и определения, характеризующие шабрение, доводку и притирку.
4. Научиться пользоваться оборудованием и инструментами слесарной мастерской, применяемыми при шабрении, доводке и притирке.
5. Соединение деталей болтами, винтами и шпильками: последовательность выполнения. Фиксирование и соединение деталей болтами и гайками в групповом соединении. Типичные дефекты при сборке разъемных соединений, причины появления и способы предупреждения.
- подготовить сборочную единицу (коробка скоростей, редуктор);
- произвести разборку;
- произвести чистку деталей;
- при необходимости устранить неполадки;
- собрать изделие;
- проверить качество сборки.
Контрольные вопросы
1. Перечислить виды разъемных соединений.
2. Какие бывают виды резьбовых соединений.
3. Ручной инструмент для сборки резьбовых соединений.
4. Последовательность сборки шпилечного соединения.
5. Шпоночные соединения и их сборка.
6. Технология шлицевых соединений.
7. Как контролируют детали шпоночного и шлицевого соединения перед сборкой.
Практическое занятие №9
2. Сборка неразъемных соединений (клепка).
Цель занятия
1. Изучить виды неразъемных соединений. Назначение и применение клепки. Виды заклепочных соединений. Типы заклепок. Инструменты и приспособления, применяемые при клепке. Приемы и способы клепки. Определение размеров заклепки. Механизация клепальных работ. Возможные дефекты при клепке и меры их предупреждения.
Технология пайки, технология склеивания, технология сварки. Организация рабочего места и техника безопасности при клепке.
2. Научиться выполнять подготовку материалов к склепыванию, склепывание двух листов в потай заклепками с круглой головкой под обжимку, склепывание листового металла с листовым изоляционным материалом трубчатыми заклепками из цветных металлов.
В результате освоения данной темы обучающийся должен приобрести следующие умения У1-У6, У8
получить практический опыт О1, О2
Неразъёмными называют соединения, которые невозможно разобрать без нарушения или повреждения деталей. К ним относятся заклёпочные, сварные, клеевые соединения, соединения, полученные пайкой, а также условно посадки с натягом.
|
Рисунок 49. Виды неразъемных соединений
Технология процесса клепки.
Ручная клепка производится обычно на рабочем месте слесаря и выполняется в тисках или на верстаке. В ряде случаев соединения заклепками с потайной головкой выполняют на плите. Для получения заклепочных соединений высокого качества большое значение имеет взаимная подгонка деталей. Соединяемые детали должны быть плотно подогнаны одна к другой и без напряжения ложиться на место. Плохая подгонка деталей ведет к возникновению напряжений после клепки, к образованию трещин, выпуклостей и др. Сверление отверстий под заклепки производят по накерненной разметке. Чтобы отверстия склепываемых деталей совпадали, их сверлят в собранном виде сжатыми ручными тисочками, струбцинами или болтами. Заусенцы, образовавшиеся после сверления, снимают зенковкой или сверлом большего диаметра. Затем детали переносят к верстаку и в подготовленное отверстие вставляют заклепку, укладывая ее закладную головку на зажатую в тисках поддержку. После этого производят уплотнение соединяемых деталей путем осадки их ударом молотка по натяжке. Затем, сделав несколько прямых ударов, направленных вдоль оси заклепки с целью утолщения стержня для плотного заполнения Отверстия, осадку продолжают косыми ударами молотка по окружности головки, чередуя их с прямыми ударами. В результате получится головка в виде грубого полушара. Окончательное формирование замыкающей головки производится ударами молотка по обжимке, установленной на образующуюся головку заклепки.
Последовательность выполнения работ при клепке. При ручной клепке поступают следующим образом:
- пригоняют поверхности соединяемых заготовок;
- рассчитывают длину заклепок: l = S + (1,2... 1,5) d, где S — суммарная толщина соединяемых заготовок; d — диаметр заклепки;
- определяют шаг заклепок;
- рассчитывают расстояние между рядами в соединении;
- рассчитывают расстояние от центра отверстия до края соединяемых заготовок;
- размечают соединяемые заготовки для сверления отверстий под заклепки;
- выбирают сверло и сверлят отверстия под заклепки, скрепив предварительно соединяемые заготовки при помощи струбцины;
- вводят снизу заклепку в отверстие и устанавливают поддержку под ее закладную головку;
- устанавливают на стержень заклепки натяжку и осаживают соединяемые заготовки;
- наносят по стержню заклепки удары под углом к ее оси, обеспечивая предварительное формирование замыкающей головки таким образом, чтобы она была концентрична стержню;
- устанавливают обжимку на предварительно сформированную замыкающую головку и производят ее окончательное формирование;
- контролируют правильность установки заклепок 1 и 5 по высоте головок над поверхностью склепываемых заготовок при помощи шаблона 2 или линейки 3 и щупа 4 (Рис. 50).
Рисунок 50. Контроль правильности установки заклепок
Виды заклепок. Заклепка представляет собой стержень из пластичного металла, на одном конце которого выполнена головка, называемая закладной. В процессе выполнения операции на второй стороне стержня, вставляемого в отверстие соединяемых заготовок, образуется вторая головка заклепки, которую называют замыкающей. Необходимость применения пластичного металла для изготовления заклепок обусловлена тем, что головки заклепок образуются в результате пластического деформирования стержня. При выполнении заклепочного соединения заклепки следует выбирать из того же материала, из которого изготовлены детали, подлежащие соединению.
Разнообразие заклёпочных соединений порождает соответственно большое число разновидностей самих заклёпок.
Рисунок 51. Виды заклепок
По форме закладных головок заклёпки бывают (рис. 51):
с полукруглой (полусферической) а; потайной б; полупотайной в; цилиндрической г и др. головками. А по форме стержня (тела) заклёпки могут быть: сплошными (полнотельными) а-в; пустотелыми (со сквозным центральным отверстием) д; полупустотелыми (часть стержня сплошная, а часть пустотелая – с отверстием) г.
Инструменты для ручной клепки. При ручной клепке применяют слесарные молотки, или кувалды, поддержки, натяжки, обжимки и чеканки. Слесарные молотки применяют с квадратным бойком. Вес молотка выбирают в зависимости от диаметра заклепки. Поддержки являются опорой для заклепки во время осадки и отделки замыкающей головки. Конструкции поддержек самые разнообразные. Поддержки выбирают не только по форме заклепки, но и по весу. Вес поддержки должен быть в 3-5 раз тяжелее веса молотка, так как при большом весе трудно работать, а при малом весе поддержка при клепке будет отскакивать от заклепки. Обжимки служат для придания замыкающей головке заклепки после осадки требуемой формы. Натяжка представляет собой бородок с отверстием на рабочем конце. Диаметр отверстия обычно делают на 0,2 мм больше диаметра заклепки. Чеканка представляет собой слесарное зубило с плоской рабочей гранью и применяется для создания герметичности шва, обжатия (подчеканки) замыкающей головки и края листа.
Преимущества и недостатки заклепочных соединений. Среди положительных сторон выделяют: простое технологическое исполнение; способность соединять разнородные металлы; высокая надежность соединения; противодействует вибрационным и ударным нагрузкам. Однако, как и у каждого соединения, имеются свои отрицательные стороны, среди которых выделяют следующее: чтобы создать заклепочное скрепление, необходимо затратить большое количество металла; требует существенных трудовых затрат; высокая стоимость; заклепочные соединения могут разрушаться из-за неправильного диаметра отверстий, которые находятся на краях изделий; в процессе эксплуатации герметичность соединения уменьшается.
|
|
Типы сооружений для обработки осадков: Септиками называются сооружения, в которых одновременно происходят осветление сточной жидкости...
История создания датчика движения: Первый прибор для обнаружения движения был изобретен немецким физиком Генрихом Герцем...
Поперечные профили набережных и береговой полосы: На городских территориях берегоукрепление проектируют с учетом технических и экономических требований, но особое значение придают эстетическим...
Историки об Елизавете Петровне: Елизавета попала между двумя встречными культурными течениями, воспитывалась среди новых европейских веяний и преданий...
© cyberpedia.su 2017-2024 - Не является автором материалов. Исключительное право сохранено за автором текста.
Если вы не хотите, чтобы данный материал был у нас на сайте, перейдите по ссылке: Нарушение авторских прав. Мы поможем в написании вашей работы!