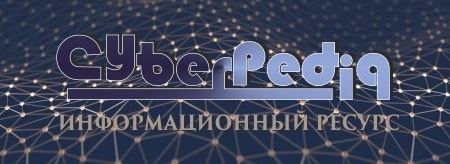
Организация стока поверхностных вод: Наибольшее количество влаги на земном шаре испаряется с поверхности морей и океанов (88‰)...
Папиллярные узоры пальцев рук - маркер спортивных способностей: дерматоглифические признаки формируются на 3-5 месяце беременности, не изменяются в течение жизни...
Топ:
Характеристика АТП и сварочно-жестяницкого участка: Транспорт в настоящее время является одной из важнейших отраслей народного хозяйства...
Оценка эффективности инструментов коммуникационной политики: Внешние коммуникации - обмен информацией между организацией и её внешней средой...
Отражение на счетах бухгалтерского учета процесса приобретения: Процесс заготовления представляет систему экономических событий, включающих приобретение организацией у поставщиков сырья...
Интересное:
Берегоукрепление оползневых склонов: На прибрежных склонах основной причиной развития оползневых процессов является подмыв водами рек естественных склонов...
Что нужно делать при лейкемии: Прежде всего, необходимо выяснить, не страдаете ли вы каким-либо душевным недугом...
Средства для ингаляционного наркоза: Наркоз наступает в результате вдыхания (ингаляции) средств, которое осуществляют или с помощью маски...
Дисциплины:
![]() |
![]() |
5.00
из
|
Заказать работу |
|
|
Подготовка МНЛЗ к разливке в соответствии с разделом 3.
Подготовка металла к разливке в соответствии с разделом 4.
Температуры стали в стальковше, после обработки на АКОС и в промковше должны соответствовать таблице 6
Таблица 6
Марка стали | Температура металла в стальковше, ºС | Средняя темп-ра металла в промковше, ºС | Время выдержки в стопе, час | |
1 плавка в серии | 2 и послед. плавки в серии | |||
03Х18Н11 | 1535 + 5 | 1525 + 5 | 1490 ±5 | 27 + 1 |
08Х18Н10 | 1535 + 5 | 1525 + 5 | 1490 ±5 | 27 + 1 |
12Х18Н9 | 1535 + 5 | 1525 + 5 | 1490 ±5 | 27 + 1 |
17Х18Н9 | 1535 + 5 | 1525 + 5 | 1490 ±5 | 27 + 1 |
20Х23Н18 | 1495 + 5 | 1485 + 5 | 1450 ±5 | 27 + 1 |
304 | 1535 + 5 | 1525 + 5 | 1490 ±5 | 27 + 1 |
08-10Х17Н13М2(3)Т | 1525 + 5 | 1515 + 5 | 1485 ±5 | 27 + 1 |
03Х18Н10Т | 1530 + 5 | 1525 + 5 | 1490 ±5 | 27 + 1 |
08-12Х18Н10Т | 1530 + 5 | 1525 + 5 | 1490 ±5 | 27 + 1 |
08Х22Н6Т | 1540 + 5 | 1530 + 5 | 1500 ±5 | 27 + 1 |
12Х21Н5Т | 1540 + 5 | 1530 + 5 | 1500 ±5 | 27 + 1 |
08Х21Н6М2Т | 1535 + 5 | 1525 + 5 | 1495 ±5 | 27 + 1 |
03Х22Н6М2 | 1540 + 5 | 1530 + 5 | 1500 ±5 | 27 + 1 |
04-08Х17Т | 1585 + 5 | 1575 + 5 | 1535 ±5 | не более 6 |
08Х18Т1 | 1585 + 5 | 1575 + 5 | 1535 ±5 | не более 6 |
316L | 1525 + 5 | 1515 + 5 | 1485 ±5 | 27 + 1 |
6.1. Установить на промковш предварительно разогретый в пределах от 900 до 1000ºС корундографитовый погружной стакан. Отцентрировать погружной стакан в кристаллизаторе и произвести выверку стакана по вертикали (визуально). Допустимые отклонения вертикально установленного стакана в сторону широких граней ± 5 мм, узких ± 10 мм. Отверстия для подвода металла должны быть направлены параллельно широким граням (контролируется визуально).
Плотность прилегания погружного стакана к поверхности стакана-дозатора обеспечивается фетровой прокладкой из минеральной ваты, поставляемой совместно с погружным стаканом, или плавкой вставкой, точностью конусного соединения.
6.2. По команде мастера разливки открыть шиберный затвор, в стык защитной трубы со стаканом-коллектором одновременно подать аргон (допускается вместо подачи аргона использование плавкой вставки). При достижении в промковше ¼ рабочего уровня металла, соответствующего двум кирпичам кладки на ребро (260 мм), закрыть зеркало металла шлакообразующей смесью марки ШОС 51 (предназначенной только для промковша) или ШОС 55, которую рекомендуется отдавать в район стопора-моноблока при сильном загущении шлака.
|
6.3. Время между последним измерением температуры металла на АКОС и открытием шиберного затвора должно составлять не более 30 мин, от момента поднятия горелок разогрева до поступления металла в промковш - не более 5 минут. Допускается производить установку погружного стакана в процессе наполнения промежуточного ковша.
Открытие шиберного затвора сталеразливочного ковша считается началом разливки. Оператор ГПУ по громкой связи объявляет "Металл в промковше".
6.4. После наполнения промковша металлом на одну треть высоты (от 260 до 300 мм, определяется визуально) разливщик стальковша проверяет работу шиберного затвора на открытие и закрытие, и при удовлетворительной работе отдает команду открыть стопор промежуточного ковша и подать металл в кристаллизатор. Время наполнения промковша на 1/3 от 18 до 20 сек при полном открытии шибера шиберного затвора и диаметре стакана 70 мм. При диаметре стакана 80 мм время наполнения 1/3 высоты промковша – от 16 до 18 сек. Одновременно в кристаллизатор в процессе его заполнения до уровня от 400 до 450 мм равномерно отдать по сторонам от 6 до 7 кг подготовленных холодильников. (Расход холодильников определяется в зависимости от ширины кристаллизатора). После заполнения кристаллизатора металлом до рабочего уровня и пуска качания подать аргон в стык погружного стакана (при использовании плавкой вставки подавать аргон в стык стакана-дозатора и погружного стакана не требуется). Расход аргона от 10 до 15 л/мин (показания ротаметра ф. «Ставерма»). Слабое «кипение металла» в кристаллизаторе без всплесков и оголения зеркала металла.
|
6.5. Оператор главного пульта управления объявляет: «Металл в кристаллизаторе» и начинает отсчет времени. Одновременно подать воду и воздух на ЗВО. Контролер УТК фиксирует время заполнения кристаллизатора до момента начала пуска качания (не должно быть менее 40 сек) и вытягивания заготовки. Время заполнения кристаллизатора фиксируется в журнале разливки.
При заполнении промковша металлом массой не менее 9,0 т в течение 40…45 сек необходимо постоянное присутствие на участке слесаря по ремонту гидравлики для принятия срочных мер в случае некрытия шиберного затвора.
6.6. После перекрытия выходных отверстий погружного стакана подать на мениск шлакообразующую смесь. Во время наполнения кристаллизатора разливщик проверяет работу стопора путем периодического перекрытия струи металла. В случае некрытия стопора необходимо приработать его. Заплески стенок кристаллизатора во время наполнения не допускаются.
6.7. Поверхность смеси, покрывающей мениск металла в кристаллизаторе, должна быть серого цвета. Оголение мениска не допускается. При появлении красных пятен ШОС равномерно подсыпается по всей поверхности. Запрещается перемешивание расплавленной ШОС с нерасплавленной.
6.8. При подходе уровня металла к номинальному (100 мм от верхнего среза медных стенок), но не ранее, чем через 40 секунд после начала заполнения кристаллизатора, по команде мастера, включить привод качания кристаллизатора. Частота качания соответствует таблице 7 в зависимости от принятой амплитуды качания (± 3мм; ± 4,5мм; ± 6мм) и скорости разливки.
6.9. В момент запуска привода качания кристаллизатора оператор по усилию вытягивания, разливщик и мастер визуально должны проконтролировать отсутствие "надрыва" корочки слитка с обеих сторон в результате "зависания". В случае появления искр под кристаллизатором немедленно сообщить оператору ГПУ.
Таблица 7 ЗАВИСИМОСТЬ ЧАСТОТЫ КАЧАНИЯ КРИСТАЛЛИЗАТОРА ОТ СКОРОСТИ РАЗЛИВКИ И АМПЛИТУДЫ
Амплитуда ± 3,0мм
Скорость разливки, м/мин | 0,2 | 0,25 | 0,3 | 0,35 | 0,4 | 0,45 | 0,5 | 0,55 | 0,6 | 0,65 | 0,7 | 0,75 | 0,8 | |||||||||
Частота качания, 1/мин | 40 33 30 | 44 37 34 | 48 41 37 | 52 44 41 | 56 47 43 | 60 50 46 | 63 53 49 | 66 56 51 | 69 58 54 | 71 60 56 | 75 63 58 | 78 65 59 | 81 68 62 | |||||||||
0,85 | 0,9 | 0,95
| 1,0 | 1,05 | 1,1 | 1,15 | 1,2 | 1,25 | 1,3 | |||||||||||||
83 70 65 | 86 73 67 | 88 75 69 | 91 77 72 | 91 80 74 | 96 82 76 | 98 84 78 | 101 86 80 | 103 88 82 | 105 90 84 | |||||||||||||
Амплитуда ± 4,5мм
Скорость разливки, м/мин | 0,2 | 0,25 | 0,3 | 0,35 | 0,4 | 0,45 | 0,5 | 0,55 | 0,6 | 0,65 | 0,7 | 0,75 |
Частота качания, 1/мин | 32 27 24 | 36 30 27 | 40 33 30 | 43 36 32 | 46 36 35 | 48 41 37 | 39 42 51 | 54 45 41 | 56 47 43 | 58 49 45 | 61 51 47 | 63 53 49 |
0,8 | 0,85 | 0,9 | 0,95 | 1,0 | 1,05 | 1,1 | 1,15 | 1,2 | 1,25 | 1,3 |
65 55 51 | 67 57 52 | 69 58 54 | 71 60 55 | 73 62 57 | 75 64 58 | 77 65 60 | 79 67 62 | 81 68 63 | 82 70 65 | 84 72 66 |
Амплитуда ± 6мм
Скорость разливки, м/мин | 0,2 | 0,25 | 0,3 | 0,35 | 0,4 | 0,45 | 0,5 | 0,55 | 0,6 | 0,65 | 0,7 | 0,75 |
Частота качания, 1/мин | 27 23 21 | 31 26 23 | 34 29 26 | 37 32 28 | 39 33 30 | 42 35 32 | 44 37 34 | 46 39 35 | 48 41 37 | 50 42 39 | 52 44 40 | 54 46 42 |
0,8 | 0,85 | 0,9 | 0,95 | 1,0 | 1,05 | 1,1 | 1,15 | 1,2 | 1,25 | 1,3 |
56 47 43 | 58 49 45 | 60 50 46 | 61 52 47 | 63 53 49 | 65 54 50 | 66 56 51 | 68 57 52 | 69 58 54 | 71 59 55 | 72 61 56 |
Примечание:
1. При разливке коррозионностойких марок стали ферритного класса и значений усилий вытягивания заготовки более 5 тс пользоваться нижними значениями частот качания.
2. При средних значениях температур разливки стали аустенитного класса и усилий вытягивания заготовки пользоваться средними значениями частот качания.
6.10. При отсутствии "подвисания" металла в кристаллизаторе, по команде мастера включить приводы вращения роликовых секций со скоростью 0,2 м/мин. Оператор главного поста объявляет: "Машина пущена".
6.11. Скорость разливки увеличивают по следующей схеме:
- скорость 0,2 м/мин в течение 30 сек до 0,3 м/мин до L = 0,1 м;
- скорость 0,3 м/мин в течение 20 сек до 0,4 м/мин до L = 0,2 м;
- скорость 0,4 м/мин в течение 15 сек до 0,5 м/мин до L = 0,3 м;
- скорость 0,5 м/мин в течение 12 сек до 0,6 м/мин до L = 0,4 м;
- скорость 0,6 м/мин в течение 10 сек до 0,7 м/мин до L = 0,5 м;
- скорость 0,7 м/мин в течение 8 сек до 0,8 м/мин до L = 0,6 м.
Скорость разливки аустенитных марок стали поддерживают в пределах 0,8 м/мин, до первого измерения температуры, а для ферритных марок стали, в пределах 0,6 м/мин. После измерения температуры скорость разливки должна соответствовать табл.8, уровень металла в кристаллизаторе поддерживают в пределах 50...100 мм от верхнего торца медной стенки. Выбранный уровень металла в кристаллизаторе поддерживать постоянно.
|
6.12. После запуска МНЛЗ промковш устанавливают до уровня погружения нижнего торца стакана в металл от 150 до 280 мм (без учета ШОС). (Среднее значение погружения погружного стакана от нижнего торца 230 мм). Уровень шлака в кристаллизаторе должен быть от 30 до 40 мм, что достигается при постоянно серой поверхности шлака. Уровень металла должен быть не ниже 60 мм, и не выше 200 мм выходного отверстия стакана.
6.13. Уровень металла в промковше доводится до рабочего (950мм от дна ковша с учетом шлакового слоя или 8 кирпичей) и поддерживается в течение всей разливки постоянно. Допустимое снижение уровня металла в промковше в процессе разливки должно составлять не более 100 мм. В течение разливки через каждые 10-15 минут разливщик производит приработку шиберного затвора закрытием (1- 2 раза).
6.14 В процессе разливки периодически проверяют работу стопора промковша.
6.15 В процессе разливки производят измерения температуры металла в промковше: после отливки 3 метров сляба, после отливки 10 метров и в последующем через 10 метров до конца разливки (при «непредставительном» замере, сделать повторный через 3 метра).
6.16 Скорость разливки должна соответствовать таблице 8.
Таблица 8 Температурно-скоростные режимы разливки коррозионностойких марок стали в зависимости от сечения заготовки
Температура разливки 1450 ± 10 ºС
(20Х23Н18)
Сечение кристаллизатора 170´1030 … 1100 мм
Темп-ра Ме в п/к, ºС | 1435 | 1440 | 1445 | 1450 | 1455 | 1460 | 1465 |
V разл., м/ мин | 1,05 | 1,0 | 0,95 | 0,90 | 0,85 | 0,80 | 0,75 |
раб. | раб. | раб. | раб. |
Сечение кристаллизатора 170´1250 … 1300 мм
Темп-ра Ме в п/к, ºС | 1470 | 1475 | 1480 | 1485 | 1490 | 1495 | 1500 | 1505 |
V разл., м/мин | 1,0 | 0,95 | 0,90 | 0,85 | 0,80 | 0,75 | 0,70 | 0,65 |
раб. | раб. | раб. | раб. |
Температура разливки 1485 ± 10 ºС
08-10Х17Н13М2(3)Т
Сечение кристаллизатора 170´1030 … 1100 мм
Темп-ра Ме в п/к, 0С | 1470 | 1475 | 1480 | 1485 | 1490 | 1495 | 1500 | 1505 |
V разл., м/ мин | 1,05 | 1,0 | 0,95 | 0,90 | 0,85 | 0,80 | 0,75 | 0,70 |
раб. | раб. | раб. | раб. |
Сечение кристаллизатора 170´1250 … 1300 мм
Темп-ра Ме в п/к, 0С | 1470 | 1475 | 1480 | 1485 | 1490 | 1495 | 1500 | 1505 |
V разл., м/ мин | 1,0 | 1,95 | 0,90 | 0,85 | 0,80 | 0,75 | 0,70 | 0,65 |
раб. | раб. | раб. | раб. |
Температура разливки 1490 ± 10ºС
03Х18Н11, 08-12Х18Н9(10), 08-12Х18Н10Т
Сечение кристаллизатора 170´1030 … 1100 мм
Темп-ра Ме в п/к, 0С | 1475 | 1480 | 1485 | 1490 | 1495 | 1500 | 1505 | 1510 |
V разл., м/ мин | 1,05 | 1,0 | 0,95 | 0,90 | 0,85 | 0,80 | 0,75 | 0,70 |
раб. | раб. | раб. | раб. |
Сечение кристаллизатора 170´1250 … 1350 мм
Темп-ра Ме в п/к, 0С | 1475 | 1480 | 1485 | 1490 | 1495 | 1500 | 1505 | 1510 |
V разл., м/ мин | 1,0 | 0,95 | 0,90 | 0,85 | 0,80 | 0,75 | 0,70 | 0,65 |
раб. | раб. | раб. | раб. |
|
Сечение кристаллизатора 170´1380 … 1420 мм
Темп-ра Ме в п/к, 0С | 1475 | 1480 | 1485 | 1490 | 1495 | 1500 | 1505 | 1510 |
V разл., м/ мин | 0,95 | 0,90 | 0,85 | 0,80 | 0,75 | 0,70 | 0,65 | 0,65 |
раб. | раб. | раб. | раб. |
Сечение кристаллизатора 170´1460 … 1550 мм
Темп-ра Ме в п/к, 0С | 1475 | 1480 | 1485 | 1490 | 1495 | 1500 | 1505 | 1510 |
V разл., м/ мин | 0,90 | 0,85 | 0,80 | 0,75 | 0,70 | 0,70 | 0,65 | 0,65 |
раб. | раб. | раб. | раб. |
Для сечения 170´1460…1550 мм допускается изменение основной рабочей скорости разливки в пределах + 0,05 м/мин (при угрозе быстрой потери температуры металла в стальковше, промковше).
Температура разливки 1495 ± 10ºС
(08Х21Н6М2Т)
Сечение кристаллизатора 170´1030 … 1100 мм
Темп-ра Ме в п/к, 0С | 1480 | 1485 | 1490 | 1495 | 1500 | 1505 | 1510 | 1515 |
V разл., м/ мин | 1,05 | 1,0 | 0,95 | 0,90 | 0,85 | 0,80 | 0,75 | 0,70 |
раб. | раб. | раб. | раб. |
Температура разливки 1500 ± 10 ºС
(08Х22Н6Т, 12Х21Н5Т, 03Х22Н6М2)
Сечение кристаллизатора 170´1030…1100 мм
Темп-ра Ме в п/к, 0С | 1485 | 1490 | 1495 | 1500 | 1505 | 1510 | 1515 | 1520 |
V разл., м/ мин | 1,05 | 1,0 | 0,95 | 0,90 | 0,85 | 0,80 | 0,75 | 0,70 |
раб. | раб. | раб. | раб. |
Температура разливки 1535± 10 ºС
(04-08Х17Т, 08Х18Т1)
Сечение кристаллизатора 170´1030…1100 мм
Темп-ра Ме в п/к, 0С | 1520 | 1525 | 1530 | 1535 | 1540 | 1545 | 1550 |
V разл., м/ мин | 0,90 | 0,85 | 0,80 | 0,75 | 0,70 | 0,65 | 0,60 |
раб. | раб. | раб. | раб. |
Примечание:
- при разливке выдерживать максимальный уровень металла в промковше (14 т).
- в промковш на первую плавку в один прием отдать 80 кг ШОС51(ШОС-55Д, или ШОС-56Д) (10 мешков), а на последующие плавки равномерно по 40 кг (5 мешков) порциями. Для разжижения шлака допускается отдача в промковш в область до перегородки и после нее ШОС-55д, ШОС-56д.
6.17. Отбор двух проб на химический анализ производится на 30-35 метре разливки пробоотборниками ПМ или ПМ-39 (без раскисления), или литой пробы в медные стаканчики из-под сталеразливочного ковша.
6.18. Не рекомендуется изменение скорости разливки более чем на 0,2 м/мин и более двух раз за плавку. Все изменения скорости разливки оператор ГПУ фиксирует в журнале. Оператор ПУ-1 производит корректировку расходов воды на зоны вторичного охлаждения (табл.4).
6.19. Обо всех изменениях скорости разливки операторам ПУ-2, ПУ-3 сообщает по внутренней связи оператор ГПУ. При этом корректировка расхода воды на вторичное охлаждение по зонам и граням производится автоматически через АСУ, а в случае отказа - вручную.
В случае неисправности АСУТП и КИП и когда нет возможности во время разливки производить корректировку воды на ЗВО с пульта управления ПУ-10, разрешается подача воды через байпасы в узле водяного регулирования. Разливку при аварийном охлаждении прекратить. Засечь время аварийного охлаждения.
6.20. Шлакообразующая смесь, применяемая для защиты зеркала металла в кристаллизаторе, засыпается равномерным слоем толщиной 30-40 мм, толщина жидкого слоя не должна превышать 20 мм. Контролировать визуально.
6.21. Запрещается перемешивать расплавленный слой шлака с порошкообразным нерасплавленным слоем. Для контроля и извлечения "коржей", «настылей» на зеркале металла используются чистые или слабо «ошлакованные» крючки.
6.22. При достижении усилия вытягивания слитка 12 тс аустенитного класса и 10 тс ферритного класса скорость разливки должна быть снижена до 0,2 м/мин, частота качания в пределах таблицы 7.
6.23. В процессе разливки постоянно поддерживается темная поверхность шлака путем непрерывной подсыпки ШОС малыми дозами. Не допускается оголение поверхности металла, особенно в районе узких граней. Подсыпка ШОС в кристаллизатор осуществляется лопатами или совками с отверстиями диаметром 3÷5 мм, с шагом 5-10 мм по несущей поверхности. Удаление гарнисажа по периметру кристаллизатора осуществляется только после полного проплавления ШОС во избежание захвата потоком металла нерасплавленных частиц шлака и загрязнения металла неметаллическими включениями.
Запрещается подъем уровня металла после резкого его снижения без предварительного удаления слоя гарнисажа по периметру кристаллизатора.
6.24. Отделение затравки производится устройством для ее отделения.
6.24.1. После получения команды "Машина пущена", оператор гидравлических ножниц обязан включить автоматический режим функционирования устройства отделения затравки и проконтролировать готовность оборудования.
6.24.2. В случае неотделения затравки необходимо попытаться отделить затравку с местного пульта управления.
6.24.3. В случае второго не отделения затравки оператор гидравлических ножниц и УПС должен осуществить порезку головной обрези на гидравлических ножницах. Головка затравки вместе с головной обрезью слитка длиной 1400-1500 мм передается в пролет охлаждения слябов с помощью крана № 25 или № 26.
6.25. Слиток по рольгангу поступает на ножницы, где во время движения происходит порезка слитка на заданные ПРУ мерные слябы согласно таблице 9.
Таблица 9 Раскрой непрерывнолитой заготовки на мерные длины (слябы) в горячем состоянии с учетом линейной усадки.
№ п/п | Длина сляба в холод.сост.для стана 2300/1700 | Длина непрерывнолитой заготовки | ||
Среднее значение длины сляба, мм | Минимальное значение, мм | Максимальное значение, мм | ||
1 | 3200 +50-30 | 3240 | 3216 | 3280 |
2 | 3250 +50-30 | 3291 | 3276 | 3331 |
3 | 3300 +50-30 | 3341 | 3317 | 3383 |
4 | 3350 +50-30 | 3392 | 3377 | 3434 |
5 | 3400 +50-30 | 3443 | 3417 | 3485 |
6 | 3450 +50-30 | 3493 | 3477 | 3536 |
7 | 3500 +50-30 | 3544 | 3518 | 3588 |
8 | 3550 +50-30 | 3594 | 3578 | 3639 |
9 | 3600 +50-30 | 3645 | 3615 | 3696 |
10 | 3650 +50-30 | 3696 | 3666 | 3747 |
11 | 3700 +50-30 | 3767 | 3716 | 3797 |
12 | 3750 +50-30 | 3798 | 3767 | 3848 |
13 | 3800 +50-30 | 3848 | 3818 | 3898 |
14 | 3850 +50-30 | 3900 | 3868 | 3949 |
15 | 3900 +50-30 | 3950 | 3919 | 4000 |
16 | 3950 +50-30 | 4000 | 3970 | 4050 |
17 | 4000 +50-30 | 4051 | 4020 | 4100 |
18 | 4050 +50-30 | 4102 | 4071 | 4152 |
19 | 4100 +50-30 | 4152 | 4121 | 4202 |
20 | 4150 +50-30 | 4203 | 4172 | 4253 |
21 | 1600 +50-30 | 1621 | 1591 | 1671 |
22 | 1650 +50-30 | 1671 | 1642 | 1721 |
23 | 1700 +50-30 | 1722 | 1691 | 1772 |
24 | 1750 +50-30 | 1772 | 1742 | 1822 |
25 | 1800 +50-30 | 1823 | 1792 | 1873 |
26 | 1850 +50-30 | 1874 | 1843 | 1924 |
27 | 1900 +50-30 | 1924 | 1894 | 1974 |
Головная обрезь длиной от 1400 до 1500 мм передается в пролет охлаждения и снимается специальными клещами. Согласно раскрой в автоматическом, полуавтоматическом или ручном режимах оператор контролирует визуально по мерной линейке длину каждой отрезаемой слябы.
6.26. Хвостовая обрезь длиной до 1500 мм передается в пролет охлаждения и снимается специальными клещами.
6.27. После обрезки мерного сляба рольганг за ножницами переключается на транспортную скорость, передает сляб на транспортные рольганги и по ним сляб транспортируется к месту маркировки. Маркировка каждой слябы производится устройством для маркировки слябов.
6.28. Уборка пакетов слябов производится со стеллажа цеховым краном с клещевым захватом. При переполнении основных стеллажей возможен набор пакетов слябов на стеллажах, расположенных между МНЛЗ-1 и МНЛЗ-2 на ручном управлении УПС с поста управления.
6.29. При отказе ножниц в аварийных случаях порезку остатка непрерывного слитка можно произвести на МГР. При этом:
- наполнить короб для улавливания шлама водой;
- развернуть МГР в рабочее положение и зафиксировать ее;
Порезка на МГР производится при неподвижном слитке. Разливка на МНЛЗ в этом случае должна быть прекращена и слиток выводится из криволинейной части на рольганги. Передвижение слитка осуществляется при ручном управлении рольгангами.
6.30. После получения команды "Конец разливки" (окончание разливки металла из промежуточного ковша) оператор гидравлических ножниц должен переключить АСУ "РЕЗ" на нижний датчик измерения длины и раскроить оставшийся в ЗВО слиток на целое число заготовок, руководствуясь рекомендациями АСУ "РЕЗ".
6.31. В накопителе УПС в каждой стопе маркируется нижний сляб порядковым номером (по ходу), окончательная маркировка наносится на стеллажах в пролете охлаждения.
6.32. После охлаждения сляб до 300ºС уборщик горячего металла ОЗЛЗ в присутствии и под контролем УТК наносит краской № плавки, № сляба (согласно их расположения) и марку стали на каждый сляб с торца или со стороны узкой грани. Короткие слябы выдаются отдельно, но нумерация сохраняется.
6.33. Клеймение сляба производится согласно инструкции.
Темплет на химанализ при необходимости отрезается от каждой плавки, кроме первого и последнего сляба. Отбор и подготовка темплетов производится согласно ТИ 134-ЭС6Р-05-05.
6.34. При появлении шлака в струе из сталеразливочного ковша шибер перекрывают и разворачивают ковш в резервную позицию.
6.35. Окончание разливки производят, по возможности, на мерной длине слитка с учетом головной обрези. В любом случае разливка прекращается при уровне металла в промежуточном ковше 100 мм.
При остаточной массе металла в промковше ~ 4÷5 т по команде мастера разливки, разливщика стали оператор ГПУ плавно снижает скорость разливки до 0,40 м/мин и до закрытия стопора разливка ведется на данной скорости.
6.36. Мастер разливки по громкой связи объявляет "Конец разливки", после этого закрывается стопор промежуточного ковша. Оператор ГПУ после закрытия стопора промежуточного ковша плавно снижает скорость разливки до 0,2 м/мин, отключают подачу воды на все зоны форсуночного охлаждения кроме первой зоны, торцов и подбоя. Тележка с промежуточным ковшом переводится в резервную позицию. Отводится на резервную позицию площадка разливщика стальковша.
6.37. Оператор ГПУ нажатием клавиши подает команду в программное обеспечение АСУТП МНЛЗ на окончание разливки, где происходил раскрой слитка. Информация передается на дисплей резчика ПУ-11 или ПУ-13.
В случае отказа программного обеспечения АСУТП МНЛЗ, оператор гидравлических ножниц должен раскроить слиток согласно заданного раскроя. Длина слитка, без «хвостовой» обрези и, при необходимости, темплета. Порезка осуществляется в полуавтоматическом или ручном режимах.
6.38. Из кристаллизатора удаляются остатки ШОС. На зеркало металла отдается мелкая, просушенная металлическая сечка. После образования на мениске корочки, допускается производить охлаждение головной части слитка путем распыления воды на стенки кристаллизатора. При этом персонал не должен находиться вблизи полости кристаллизатора.
6.39. Запрещается выводить хвостовую часть слитка из кристаллизатора, если она не затвердела по всей поверхности.
6.40. После выхода формирующегося слитка из кристаллизатора механизм качания отключается и скорость вытягивания постепенно увеличивается до 0,4-0,6 м/мин.
После прохождения первой секции, управление роликовыми секциями передается оператору гидравлических ножниц и отключается подача воды на первую зону охлаждения и "подбоя".
6.41. По окончании разливки, в течении 60 мин, технологический персонал обязан обмыть водой кристаллизатор и крышку кристаллизатора, осмотреть состояние форсунок ЗВО и ножей гидравлических ножниц, проверить настройку кристаллизатора.
Все обнаруженные неполадки и замечания заносятся в технологические журналы, для устранения вызывается дежурный персонал соответствующих служб.
|
|
Эмиссия газов от очистных сооружений канализации: В последние годы внимание мирового сообщества сосредоточено на экологических проблемах...
Индивидуальные и групповые автопоилки: для животных. Схемы и конструкции...
Археология об основании Рима: Новые раскопки проясняют и такой острый дискуссионный вопрос, как дата самого возникновения Рима...
Механическое удерживание земляных масс: Механическое удерживание земляных масс на склоне обеспечивают контрфорсными сооружениями различных конструкций...
© cyberpedia.su 2017-2024 - Не является автором материалов. Исключительное право сохранено за автором текста.
Если вы не хотите, чтобы данный материал был у нас на сайте, перейдите по ссылке: Нарушение авторских прав. Мы поможем в написании вашей работы!