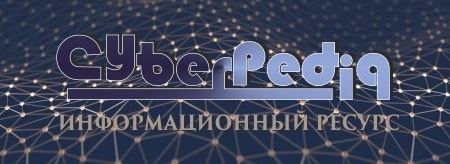
Индивидуальные и групповые автопоилки: для животных. Схемы и конструкции...
Историки об Елизавете Петровне: Елизавета попала между двумя встречными культурными течениями, воспитывалась среди новых европейских веяний и преданий...
Топ:
Комплексной системы оценки состояния охраны труда на производственном объекте (КСОТ-П): Цели и задачи Комплексной системы оценки состояния охраны труда и определению факторов рисков по охране труда...
Характеристика АТП и сварочно-жестяницкого участка: Транспорт в настоящее время является одной из важнейших отраслей народного...
Выпускная квалификационная работа: Основная часть ВКР, как правило, состоит из двух-трех глав, каждая из которых, в свою очередь...
Интересное:
Средства для ингаляционного наркоза: Наркоз наступает в результате вдыхания (ингаляции) средств, которое осуществляют или с помощью маски...
Мероприятия для защиты от морозного пучения грунтов: Инженерная защита от морозного (криогенного) пучения грунтов необходима для легких малоэтажных зданий и других сооружений...
Уполаживание и террасирование склонов: Если глубина оврага более 5 м необходимо устройство берм. Варианты использования оврагов для градостроительных целей...
Дисциплины:
![]() |
![]() |
5.00
из
|
Заказать работу |
|
|
Резьбовые соединения относятся к типовым сопряжениям, отличаются простотой, надежностью, возможностью многократной разборки и сборки соединений, поэтому они составляют 70–80% всех соединений современных машин.
Детали резьбового соединения: болт, шпилька, гайка, винт, поступающие на сборку, не должны иметь смятой и изношенной резьбы, отклонение от перпендикулярности оси резьбы к торцу шпильки должно быть 0,05–0,10 мм на длине 50…125 мм.
Во избежание коробления деталей резьбовые соединения следует затягивать в определенной последовательности (рис. 3.6).
Рис. 3.6. Последовательность затяжки гаек (болтов)
в различных сопряжениях
В начале соединение затягивается торцевым ключом до упора, затем все гайки необходимо довернуть на 1/3 оборота и, наконец, до полной затяжки динамометрическим ключом.
Не следует допускать перетяжки резьбового соединения. Максимальный момент при затяжке болтов и гаек равен:
, (3.6)
где – предел прочности материала болта и шпильки;
– диаметр болта или шпильки.
Распространены следующие разновидности резьбовых соединений:
а) для обеспечения неподвижности и прочности сопрягаемых деталей;
б) для обеспечения прочности и герметичности;
в) для правильности установки сопрягаемых деталей;
г) для регулирования взаимного положения деталей.
Неподвижную посадку шпильки в тело детали осуществляют одним из трех способов.
По первому способу – путем создания натяга по среднему диаметру (радиальный натяг) всех витков.
При втором способе шпилька идет достаточно свободно в гнездо вплоть до сбега, а при дальнейшем ее вращении создается натяг в витках сбега.
|
В третьем случае неподвижность шпильки обеспечивается за счет буртика, при упоре которого в корпус создается осевой натяг.
Крутящий момент, необходимый для завинчивания шпильки в корпус, зависит от натяга, размеров и состояния резьбы. Принимая условно корпус 1 (рис. 3.7) за толстостенную трубу диаметром D, в которую завинчивается шпилька 2, можно записать выражение:
, (3.7)
где – эффективный диаметральный натяг по среднему диаметру резьбы
, равный расчетному натягу
, уменьшенному на
, где
и
– максимальная высота микронеровностей резьб шпильки корпуса;
и
– соответственно модули упругости и коэффициенты Пуассона материала шпильки и корпуса.
Давление на условную цилиндрическую поверхность диаметром
равно:
(3.8)
или, принимая диаметр тела, куда ввинчивается шпилька, т. е. условной толстостенной трубы , получаем:
. (3.9)
Рис. 3.7. Схема завинчивания шпильки
На боковой поверхности витков резьбы будут действовать силы трения, вызываемые давлением , определяемым по следующему выражению:
, (3.10)
где – параметры резьбы.
Сила трения на боковых поверхностях витка резьбы равна:
, (3.11)
где – коэффициент трения;
– площадь двух боковых поверхностей витка.
. (3.12)
Момент силы трения , который нужно преодолеть при завинчивании шпильки, равен:
, (3.13)
где – число витков
Для метрической резьбы:
, (3.14)
где ;
;
;
.
Коэффициент трения для стальных шпильки и корпуса равен 0,1…0,2; для чугунного корпуса 0,07…0,15; для алюминиевого или бронзового – 0,04…0,1.
Допуски на перпендикулярность установки резьбовых шпилек назначаются в зависимости от точности и длины выступающей части шпильки.
Например, при длине выступающей части до 50 мм в зависимости от точности допускается отклонение в пределах от 50 до 75 мкм.
|
Болтовые и винтовые соединения, применяемые в машинах, как правило, используются с предварительной затяжкой (рис. 3.8).
Под действием силы затяжки (рис. 3.8а) болт, винт, шпилька удлиняются на величину
, а деталь сжимается на величину
.
Рис. 3.8. Схема резьбового соединения
;
;
, (3.15)
где – длина болта;
и
– модули упругости материала болта и детали;
и
– поперечные сечения болта и детали (условного цилиндра).
При работе соединения на него действует возникающее в машине рабочее усилие , в результате сила предварительного натяга
уменьшится на величину
и болт (винт, шпилька) удлинится на величину
(рис. 3.8б).
Для болта (шпильки): . (3.16)
Для стягивания детали: . (3.17)
При затягивании гайки момент , прикладываемый к ней, идет на преодоление трения торца гайки
о неподвижную опорную поверхность скрепляемых деталей и трение в резьбе
:
; (3.18)
, (3.19)
где – коэффициент трения на торце гайки.
, (3.20)
где – сила затяжки, действующая по оси болта;
– угол подъема резьбы;
– угол трения;
– средний диаметр резьбы:
, (3.21)
где – шаг резьбы.
Для метрической резьбы:
, (3.22)
где – коэффициент трения в прямоугольной резьбе.
Контроль усилия или момента затяжки осуществляется:
· замером удлинения болта (для длинных мощных болтов);
· поворотом гайки на расчетный угол;
· применением динамометрических ключей.
Надежность резьбовых соединений обеспечивается: а) пружинными шайбами (гроверами), у которых развод разрезанных частей должен быть на величину их толщины, а кромки разреза не затуплены; б) шплинтами; в) отгибными шайбами; г) контргайками (с толщиной – высотой такой же, как и у основной гайки).
Сборка соединений с натягом
Все неподвижные неразъемные соединения с гарантированным натягом условно делят на поперечно-прессовые и продольно-прессовые.
Поперечно-прессовые осуществляют одним из следующих способов: нагреванием охватывающей детали перед сборкой, охлаждением охватываемой; путем пластической деформации (например, развальцовки); приданием упругости охватываемой детали.
При продольно-прессовом соединении охватываемая деталь запрессовывается в охватывающую в продольном направлении с натягом, в результате которого в соединении возникают силы трения, обеспечивающие относительную неподвижность деталей.
|
Трудоемкость таких соединений составляет 10…15% от общей трудоемкости сборочных работ.
Охватываемая деталь имеет наружный диаметр больший, чем диаметр отверстия охватывающей детали, в результате чего на поверхности контакта возникают значительные нормальные давления и сила трения, которые препятствуют сдвигу этих деталей. Способность прессовых соединений выдерживать значительные нагрузки зависит от натяга. Натяг одновременно является основным показателем, определяющим величину усилия запрессовки, Для определения действительного натяга (с учетом микрогеометрии) необходимо знать максимальную высоту неровностей обеих сопрягаемых поверхностей.
Номинальный натяг в сопряжении равен:
, (3.23)
где – диаметр вала;
– диаметр отверстия.
Действительный натяг равен:
, (3.24)
где – максимальная высота микронеровностей,
– средняя высота микронеровностей.
Условно принимая , получаем:
. (3.25)
Использование в процессе запрессовки смазки способствует повышению прочности соединения. Обычная скорость запрессовки не более 5–7 мм/сек.
Наибольшее усилие запрессовки продольно-прессового соединения с гарантийным натягом равно:
, кг, (3.26)
где – коэффициент трения;
– диаметр охватываемой детали, мм;
– длина запрессовки, мм;
– напряжение сжатия на контактной поверхности, кг/мм2.
Напряжение можно определить по формуле:
, (3.27)
где – натяг в мкм;
– модули упругости материала соответственно охватываемой и охватывающей детали, кг/мм2;
– коэффициенты, учитывающие параметры и свойства материала детали.
;
, (3.28)
где – коэффициенты (для стальных деталей
.
Коэффициент трения для стальной втулки ; чугунной –
; латунной –
.
Соединения с нагревом охватывающей детали или охлаждением охватываемой при передаче крутящего момента имеют прочность в 2–3 раза большую, чем прочность обычных прессовых посадок.
|
Температура, до которой следует нагреть охватывающую деталь, определяется из условия, что натяг будет меньше произведения:
, (3.29)
где – коэффициент линейного расширения материала охватывающей детали;
– температура нагрева (прибавляется к начальной температуре детали);
– диаметр соответственно охватывающей и охватываемой детали.
Температура нагрева охватывающей детали должна быть равна:
. (3.30)
Если принять, что изменение натяга подчиняется зависимости:
, (3.31)
то минимальная температура нагрева должна быть равна:
. (3.32)
Для стальных деталей эта формула может быть упрощена:
0С. (3.33)
Температура охлаждения охватываемой детали может быть определена по формуле:
, (3.34)
где – конечная температура охлаждения детали с учетом ее начальной температуры (отнимается от начальной температуры);
– значение минимального зазора, позволяющего ввести охватываемую деталь в охватывающую (берется из таблиц справочных материалов).
|
|
История создания датчика движения: Первый прибор для обнаружения движения был изобретен немецким физиком Генрихом Герцем...
Опора деревянной одностоечной и способы укрепление угловых опор: Опоры ВЛ - конструкции, предназначенные для поддерживания проводов на необходимой высоте над землей, водой...
Биохимия спиртового брожения: Основу технологии получения пива составляет спиртовое брожение, - при котором сахар превращается...
Автоматическое растормаживание колес: Тормозные устройства колес предназначены для уменьшения длины пробега и улучшения маневрирования ВС при...
© cyberpedia.su 2017-2024 - Не является автором материалов. Исключительное право сохранено за автором текста.
Если вы не хотите, чтобы данный материал был у нас на сайте, перейдите по ссылке: Нарушение авторских прав. Мы поможем в написании вашей работы!