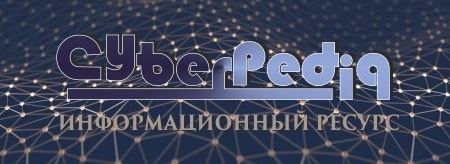
Автоматическое растормаживание колес: Тормозные устройства колес предназначены для уменьшения длины пробега и улучшения маневрирования ВС при...
Папиллярные узоры пальцев рук - маркер спортивных способностей: дерматоглифические признаки формируются на 3-5 месяце беременности, не изменяются в течение жизни...
Топ:
Марксистская теория происхождения государства: По мнению Маркса и Энгельса, в основе развития общества, происходящих в нем изменений лежит...
Комплексной системы оценки состояния охраны труда на производственном объекте (КСОТ-П): Цели и задачи Комплексной системы оценки состояния охраны труда и определению факторов рисков по охране труда...
Техника безопасности при работе на пароконвектомате: К обслуживанию пароконвектомата допускаются лица, прошедшие технический минимум по эксплуатации оборудования...
Интересное:
Принципы управления денежными потоками: одним из методов контроля за состоянием денежной наличности является...
Аура как энергетическое поле: многослойную ауру человека можно представить себе подобным...
Искусственное повышение поверхности территории: Варианты искусственного повышения поверхности территории необходимо выбирать на основе анализа следующих характеристик защищаемой территории...
Дисциплины:
![]() |
![]() |
5.00
из
|
Заказать работу |
|
|
Первостепенной причиной изнашивания деталей, сопрягаемых и трущихся при движении друг о друга, является трение.
Трение – процесс сопротивления относительному перемещению, возникающему между двумя телами в зонах соприкосновения их поверхностей по касательным к ним, сопровождаемый превращением энергии в теплоту.
Внешнее трение – явление сопротивления относительному перемещению, возникающему между двумя твердыми телами в зонах соприкосновения поверхностей по касательным к ним.
Внутреннее трение – явление сопротивления действию внешних сил, вызывающих течение смазывающих сопрягаемые твердые тела материалов (масел).
Смазочные материалы – масла, мази (обычно минеральные) – должны соответствовать ряду показателей, в том числе показателю вязкости (внутреннего трения). Различают вязкости динамическую, кинематическую и условную.
Под вязкостью жидкостей понимают их свойство, характеризующее сопротивление действию внешних сил, вызывающих течение жидкостей.
Динамическая вязкость (коэффициент вязкости внутреннего трения) выражает собой силу, затрачиваемую на перемещение одного слоя жидкости относительно другого. За единицу динамической вязкости принята паскаль-секунда (Па с), равная динамической вязкости среды, касательное напряжение в которой равно 1 Па при ламинарном течении и разности скоростей слоев, равной 1м/с на расстоянии 1 м к направлению скорости.
Кинематическая вязкость (удельный коэффициент внутренней вязкости) представляет отношение динамической вязкости жидкости к ее плотности. За единицу кинематической вязкости принят квадратный метр на секунду , при этом динамическая вязкость среды равна 1Па
с при ее плотности в 1кг/м3.
|
Условная вязкость – отношение времени истечения из вискозиметра 200 г масла ко времени истечения такого же количества дистиллированной воды при температуре 20 0С.
При подборе смазки для машин следует руководствоваться некоторыми правилами [10].
1. Быстроходные механизмы необходимо смазывать маслами пониженной вязкости с целью избежания расходования излишней энергии на преодоление сцепления частиц смазочного материала и излишнего нагрева соприкасающихся поверхностей деталей.
2. Тихоходные механизмы, работающие под большими нагрузками, нужно смазывать маслами высокой вязкости или же густыми (консистентами) смазками. Применение в механизмах, работающих с большими знакопеременными нагрузками, масел пониженной вязкости неизбежно ведет к выдавливанию смазки.
3. В процессе эксплуатации станков с тяжелыми столами, каретками при скорости движения менее 20 мм/мин часто наблюдается прерывистое (скачкообразное) перемещение. В этих случаях для уменьшения трения, обеспечения точности установочных перемещений узлов станков следует применять антискачковое масло.
4. Тяжелонагруженные тихоходные механизмы, работающие при высокой температуре, рекомендуется смазывать твердыми смазочными материалами (графит, тальк, слюда).
Когда поверхности двух сопрягаемых деталей полностью разделены слоем смазки и нагрузка воспринимается смазочной пленкой, имеет место так называемое жидкостное трение. Коэффициент жидкостного трения равен 0,001–0,008. Величина коэффициента трения, например подшипников качения, колеблется в зависимости от значения относительной скорости трущихся поверхностей, способа подачи смазки, ее вязкости.
С повышением частоты вращения вала начинает увеличиваться толщина клинового слоя за счет увеличения количества смазки, увлекаемой цапфой в клиновой зазор. При бесконечно большой частоте вращения ось цапфы совпадает с осью подшипника, а толщина масляного клина достигает максимальной величины, способствуя жидкостному трению (в отличие от состояния покоя и начала вращения).
|
Полужидкостное трение имеет место в том случае, когда большая часть сопряженных поверхностей разделена слоем смазки, но отдельные их элементы соприкасаются (коэффициент трения при этом равен 0,08–0,08). При полужидкостном трении работают тяжелонагруженые валы с частотой вращения до 400 об./мин и детали, совершающие касательное и возвратно-поступательное движения.
Когда скользящие поверхности разделены очень тонким слоем смазки (толщиной до 0,15 мкм или всего в несколько молекул), то трение между поверхностями называется граничным. В нормальных условиях изнашивание происходит так же, как при полужидкостном трении.
Сухое трение возникает при отсутствии смазки между скользящими поверхностями, когда невозможно произвести смазывание или сопряжение работает при высоких температурах (свыше 300 0С). Коэффициент сухого трения равен 0,1–0,8, но его величину можно снизить путем нанесения защитных пленок, термообработки и правильного подбора материалов сопряженных деталей.
Если слой смазки между двумя трущимися поверхностями разделят их лишь частично, то имеет место полусухое трение.
Основная характеристика внешнего трения – сила трения. Имеют место: сила трения скольжения (подшипники скольжения) и сила трения качения (подшипники качения).
Сила трения скольжения обусловлена двумя основными параметрами:
, (2.1)
где – коэффициент трения скольжения;
– нормальная к плоскости трения нагрузка.
Сила сухого трения качения шара или цилиндра определяется следующими параметрами:
, (2.2)
где – коэффициент трения качения;
– радиус качения.
Из анализа формул (2.1) и (2.2) следует вывод, что подшипники качения более прогрессивны по сравнению с подшипниками скольжения, т. к. нормальная нагрузка уменьшается на величину радиуса качения.
Сила трения зависит от факторов механического и молекулярного происхождения:
, (2.3)
где – силы соответственно механического и молекулярного происхождения;
– площадь трущихся поверхностей;
– коэффициенты, определяемые опытным путем.
Сила трения при жидкостном трении определяется следующими факторами:
|
, (2.4)
где – динамическая вязкость масла;
S – площадь сопрягаемых поверхностей;
– относительная скорость перемещения поверхностей;
– толщина масляного слоя.
На основании гидродинамической теории трения может быть определен наивыгоднейший зазор между сопрягаемыми поверхностями, при котором обеспечивается оптимальная толщина масляного слоя () для создания условий гарантированного жидкостного терния [11]:
, (2.5)
где – диаметр вала, мм;
– частота вращения вала, об./мин;
– динамическая вязкость масла, Па.с;
– удельное давление, Па;
– поправочный коэффициент на длину подшипника.
Максимально допустимый зазор определяется по формуле:
, (2.6)
где – величина неровностей (макро- или микронеровностей) вала и подшипника.
Экспериментальной проверкой установлено, что для подвижных посадок сопряжения вал – подшипник скольжения имеет место следующее соотношение между предельным зазором ( в мм) и максимальным конструктивным зазором в сопряжении новых деталей (
в мм):
. (2.7)
Коэффициент трения в слое смазки для идеального сопряжения качественно зависит от следующих параметров:
, (2.8)
где ;
– относительный зазор (
– диаметр охватываемой детали);
– давление;
– относительный эксцентриситет (
, где
– величина эксцентриситета, т. е. смещения осей вала и втулки);
– длина подшипника;
– динамическая вязкость масла;
– поправка на эксцентриситет;
– поправка на конечность размеров.
Минимальная толщина слоя смазки определяется по выражению:
, (2.9)
где – геометрический параметр
.
2.2. Изнашивание деталей. Классификация видов изнашивания. Методы определения величины износа
Износ поверхностей деталей – результат их изнашивания, определяемый в установленных единицах (в единицах длины, объема, массы и др.), проявляющийся в виде отделения и (или) остаточной деформации материала.
|
Изнашивание – процесс разрушения и отделения материала с поверхности твердого тела и (или) накопления его остаточной деформации при трении, проявляющейся в постоянном изменении размеров и (или) формы тела.
Изнашивание бывает трех основных видов: а) механическое, б) молекулярно-механическое, в) коррозионно-механическое.
Механическое изнашивание является результатом действия сил трения скольжения одной детали по другой. При этом виде изнашивания происходит истирание (срезание) поверхностного слоя металла и искажение геометрических размеров у совместно работающих деталей.
Молекулярно-механическое изнашивание имеет следующие основные подвиды [12]: а) абразивное; б) окислительное; в) усталостное; г) изнашивание при заедании; д) изнашивание при фреттинг-процессе; е) водородное; ж) гидро-газоэрозионное; з) гидро-газоабразивное; и) ка-витационное; к) электроэрозийное.
Наиболее разрушительное действие на детали оказывает абразивное изнашивание, которое наблюдается в тех случаях, когда трущиеся поверхности загрязняются мелкими абразивными и металлическими частицами. Они длительное время сохраняют свои режущие свойства, образуют на поверхностях деталей царапины, задиры, смешиваясь с жидкими составляющими образуют роль абразивной пасты.
Износ при заедании возникает в результате прилипания (схватывания) одной поверхности к другой. Это явление наблюдается при недостаточной смазке, а также значительном давлении, при котором две сопрягаемые поверхности сближаются настолько плотно, что между ними начинают действовать молекулярные силы, приводящие к их схватыванию. Имеют место холодное (первого рода) и горячее (второго рода) схватывание.
Взаимодействие поверхностей деталей без относительного перемещения вызывает смятие металла, что характерно для шпоночных, шлицевых, резьбовых соединений.
Усталостный износ является результатом действия на деталь переменных нагрузок, при этом получается характерный вид излома с двумя зонами – зоной развивающихся трещин и зоной, по которой произошел излом. Следует помнить, что грубо обработанная поверхность, наличие рисок и царапин могут стать причиной возникновения усталостных трещин.
Коррозионный износ является результатом изнашивания деталей и машин и установок, находящихся под непосредственным воздействием воды, воздуха, химических веществ, колебаний температуры.
Обычно коррозионный износ сопровождается и механическим износом вследствие сопряжения одной детали с другой. В этом случае происходит так называемый коррозионно-механический, т. е. комплексный износ.
Эрозия металлов является комплексным физическим и физико-химическим процессом, протекающим в результате окисления, наклепа, температурных напряжений, хрупкого и усталостного разрушения.
|
Характеристиками изнашивания являются: скорость, интенсивность, износостойкость (величина обратная скорости).
Фундаментальные закономерности абразивного изнашивания следующие:
а) значение износа при постоянных условиях (постоянной твердости металла) прямо пропорционально пути трения;
б) скорость изнашивания прямо пропорциональна следующим параметрам:
, (2.10)
где – значение износа;
– время;
– коэффициент пропорциональности;
– нагрузка;
– скорость трения;
в) значение интенсивности изнашивания прямо пропорционально значению нормальной нагрузки :
, (2.11)
где – длина пути трения (величина наработки).
Металлы и сплавы могут быть разделены на четыре группы по сочетанию двух параметров: а) износостойкости оксидных пленок и б) склонности к схватыванию.
Первая группа – металлы и сплавы, склонные к схватыванию, но оксидные пленки – износостойкости (железо и его сплавы, медь и ее сплавы, алюминий и др.).
Вкладыши из сплава представителей этой группы – алюминия и олова – хорошо работают на износ в условиях окислительных процессов в дизельных двигателях внутреннего сгорания.
Вторая группа – металлы и сплавы, не склонные к схватыванию, их оксидные пленки износостойки. Они хорошо работают на износ в любых условиях. Примером такого металла может быть олово (Sn).
Третья группа – металлы и сплавы, которые не склонны к схватыванию, оксидные пленки не износостойки. Хорошо работают на износ без окислительных процессов (сурьма, висмут, кадмий; сплавы типа СОС-6-6 (Pb, Sn – 6%, Su – 6%)), которые используют при изготовлении, например, вкладышей коленчатого вала двигателей автомобилей марки ГАЗ.
Четвертая группа – металлы и сплавы, склонные к схватыванию, оксидные пленки не износостойки. Примером данных металлов, не износостойких в любых условиях, может служить цинк (Zn).
Для увеличения маслоемкости поверхности (повышения износостойкости) могут применяться пористое хромирование, виброобкатывание.
Методы определения величины износа включают в себя:
а) интегральный – по результатам общей и углубленной диагностики, регистрирующим изменения показателей технической характеристики – показателей качества работы объекта, например по падению компрессии, т. е. уменьшению мощности двигателя из-за износа цилиндро-поршневой группы;
б) суммарный, к которому относятся: 1 – определение величины износа взвешиванием изнашиваемого объекта; 2 – определение величины износа по количеству удаленного с изнашиваемой поверхности материала (металла) в смазывающей сопряжение жидкости – масле; 3 – определение величины износа по количеству удаленных с изнашиваемой поверхности ранее нанесенных радиоактивных изотопов; данные методы чаще всего используются в научно-исследователь-ской практике при изучении износостойкости различных материалов;
в) метод определения местного (конкретного) линейного износа (например, метод лунок), также обычно используемый в научно-исследо-вательской практике;
г) метод микрометрических измерений, широко используемый в ремонтной практике.
Метод микрометрирования может быть использован для организации и последующего совместного использования так называемого графического метода определения износов деталей машин и оборудования, т. е. для построения кривых износа сопряженных деталей (рис. 2.1, 2.2).
Рис. 2.1. Кривая износа сопряжения Рис. 2.2. Кривые износа деталей по времени: а – шпоночное соединение; б – сальниковые сопряжения
Сопряженные детали имеют три ярко выраженных участка (первый – I; второй – II; третий – III).
Первый участок характеризует процесс приработки трущихся поверхностей.
Второй участок характеризует интенсивность изнашивания поверхностей и нарастание зазора в период нормальной эксплуатации машины, когда изнашивание происходит сравнительно медленно и равномерно. Он определяет срок службы сопряженных деталей :
, (2.12)
где – соответственно предельно допустимый и начальный зазоры сопряжения;
– величина, характеризующая интенсивность износа сопряжения (нарастание зазора на 1 ч, на 1 км пробега и др.).
Третий участок кривой износа характеризует период резкого возрастания интенсивности изнашивания поверхностей (участок аварийного износа).
На рис. 2.2 показаны кривые износа для некоторых сменных конструктивных элементов, например шпоночных соединений, сальниковых сопряжений. Как видно, в первом случае происходит разработка неподвижного соединения и срезание шпонки; на второй кривой отсутствует участок форсированного износа.
Величина износа зависит от целого ряда факторов:
· рода трения (скольжения, качения, качения с проскальзыванием);
· вида трения (без смазки, граничного, жидкостного);
· среды, в которой работает деталь (воздух, вода, кислота, смазочные материалы и др.);
· вида и величины нагрузки (постоянной, знакопеременной и др.);
· контакта трущихся поверхностей (линия, точка, сфера и др.);
· характера движения (равномерного, неравномерного, прерывистого и др.);
· вида движения (вращательного, возвратно-поступательного);
· скорости перемещения трущихся поверхностей;
· температуры, при которой работает деталь;
· вида материала (сталь, чугун, полимеры, хрупкие тела и др.).
Профессор И. В. Крагельский величину износа деталей рекомендует определять по выражению:
, (2.13)
где – коэффициент, характеризующий конструктивные особенности узла;
– показатель нагруженности узла;
– показатель скоростного режима трения;
– показатели, характеризующие закономерности влияния скорости и нагрузки на процесс изнашивания.
|
|
Таксономические единицы (категории) растений: Каждая система классификации состоит из определённых соподчиненных друг другу...
Своеобразие русской архитектуры: Основной материал – дерево – быстрота постройки, но недолговечность и необходимость деления...
Двойное оплодотворение у цветковых растений: Оплодотворение - это процесс слияния мужской и женской половых клеток с образованием зиготы...
Механическое удерживание земляных масс: Механическое удерживание земляных масс на склоне обеспечивают контрфорсными сооружениями различных конструкций...
© cyberpedia.su 2017-2024 - Не является автором материалов. Исключительное право сохранено за автором текста.
Если вы не хотите, чтобы данный материал был у нас на сайте, перейдите по ссылке: Нарушение авторских прав. Мы поможем в написании вашей работы!