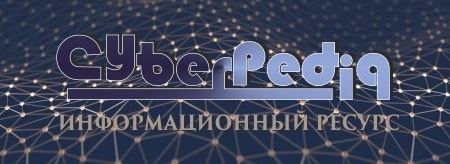
Таксономические единицы (категории) растений: Каждая система классификации состоит из определённых соподчиненных друг другу...
Биохимия спиртового брожения: Основу технологии получения пива составляет спиртовое брожение, - при котором сахар превращается...
Топ:
Характеристика АТП и сварочно-жестяницкого участка: Транспорт в настоящее время является одной из важнейших отраслей народного хозяйства...
Комплексной системы оценки состояния охраны труда на производственном объекте (КСОТ-П): Цели и задачи Комплексной системы оценки состояния охраны труда и определению факторов рисков по охране труда...
Особенности труда и отдыха в условиях низких температур: К работам при низких температурах на открытом воздухе и в не отапливаемых помещениях допускаются лица не моложе 18 лет, прошедшие...
Интересное:
Лечение прогрессирующих форм рака: Одним из наиболее важных достижений экспериментальной химиотерапии опухолей, начатой в 60-х и реализованной в 70-х годах, является...
Берегоукрепление оползневых склонов: На прибрежных склонах основной причиной развития оползневых процессов является подмыв водами рек естественных склонов...
Мероприятия для защиты от морозного пучения грунтов: Инженерная защита от морозного (криогенного) пучения грунтов необходима для легких малоэтажных зданий и других сооружений...
Дисциплины:
![]() |
![]() |
5.00
из
|
Заказать работу |
|
|
Точность обработки
Назначение любого вида обработки состоит в том, чтобы изготовить детали с заданной точностью. Под точностью обработки понимают соответствие размеров, формы и взаимного расположения участков обрабатываемых поверхностей заданной точности, а также чистоты обработки поверхности детали требованиям чертежа и техническим условиям.
Долговечность машин, работающих с большими скоростями и нагрузками, зависит во многом от качества поверхности трущихся деталей. Несмотря на большую точность и высокое совершенство современного металлорежущего оборудования, невозможно получить абсолютно точных размеров или формы деталей в соответствии с требованиями, заданными чертежом. Поэтому все изготовленные детали будут иметь некоторые отклонения (погрешности).
Величина погрешностей при изготовлении деталей зависит от многих причин:
Погрешности измерения могут быть уменьшены многократным измерением детали. Для этой цели деталь измеряют в одном и том же месте тем же самым инструментом несколько раз. Результаты измерения складывают и делят на число измерений.
Чистота поверхности
При любом методе обработки металлов резанием (сверление, развертывание, строгание, опиливание, шабрение, притирка и т. д.) не получится идеально гладкой и ровной поверхности деталей, всегда остаются следы в виде шероховатостей, впадин, надиров и другие неровности, называемые гребешками.
|
Даже поверхности, кажущиеся совершенно гладкими, после шабрения, притирки, развертывания и т. д. имеют мелкие неровности, не видимые невооруженным глазом, но отчетливо различаемые с помощью приборов.
Чем чище требуется обработка, тем ниже должны быть гребешки. Высота гребешков и глубина впадин (микрогеометрия) колеблются в значительных пределах — от десятых долей миллиметра до сотых долей микрона.
Высота и глубина микронеровностей зависит от способа обработки, степени вязкости металла обрабатываемой детали, конструкции режущего инструмента, режима механической обработки (скорости резания, подачи и др.). При опиливании высота гребешков получается больше, чем при шабрении или притирке.
При изготовлении деталей обработку необходимо вести с соблюдением установленных для них классов чистоты.
Критериями оценки шероховатости поверхности установлены два следующих параметра:
Рис. 71. Действительный профиль микронеровностей
В зависимости от величины Ra и Rz ГОСТ 2789—59 устанавливает 14 классов чистоты поверхности.
Для обозначения всех классов чистоты поверхности устанавливается один знак — равносторонний треугольник V, рядом с ним указывается номер класса и разряд, например: V7, V7б.
Шероховатость поверхностей грубее 1-го класса обозначается знаком над которым указывается высота неровностей в микронах.
|
Все поверхности по чистоте можно примерно разделить на следующие четыре группы:
Чистоту обработанной поверхности определяют различными методами.
Современная измерительная техника располагает различными средствами контроля микронеровностей. В зависимости от методов измерения приборы делятся на две основные группы: для непосредственного измерения чистоты поверхности и для косвенного определения чистоты поверхности.
Непосредственное измерение основано на контактном способе и осуществляется с помощью профилометра.
Косвенное определение производится с помощью микроскопа. Этот способ является наиболее точным и применяется для контроля поверхностей высокого класса чистоты.
На рис. 72 показан электродинамический профилометр. Игла 1 с радиусом закругления до 0,015 мм движется по проверяемой поверхности детали 4 с постоянной скоростью. Колебание иглы передается электромагнитным способом на датчик 2. Количественное значение непосредственно средних квадратичных отклонений определяется по шкале электроизмерительного прибора 3. С помощью электродинамического профилографа проверяют поверхности с чистотой 5—12 классов.
Рис. 72. Профилометр:
1 — алмазная игла, 2 — датчик, 3 — электроизмерительный прибор, 4 — проверяемая деталь
Профилометры применяются главным образом в измерительных лабораториях. В производственных условиях, особенно на небольших предприятиях, где при контроле чистоты поверхностей не требуется количественной оценки микронеровностей, применяются специально изготовляемые заводом «Калибр» образцы (эталоны), служащие для глазомерного определения чистоты поверхности. Эталонные образцы изготовляются из тех же металлов (чугун, сталь, алюминий, бронза и т. д.), что и проверяемые детали, так как поверхности деталей, обработанные одинаковым способом и имеющие один и тот же класс чистоты, будут иметь разные следы обработки, если они выполнены из разных металлов.
|
Наборы эталонных образцов (рис. 73) хранятся в пеналах.
Рис. 73. Набор эталонов для проверки чистоты поверхности (а), прием проверки (б)
В каждом держателе имеются четыре образцовые пластины.
При проверке чистоты поверхности берут эталонные образцы соответствующей формы, изготовленные из такого же металла и обработанные таким же способом, что и проверяемая деталь, и прикладывают к проверяемой детали. Сравнивая обработанную поверхность проверяемой детали с эталонным образцом, устанавливают класс чистоты обработки.
Описанный способ сравнения дает правильные результаты при проверке деталей с чистотой поверхности с 1 по 7-й класс. Недостатком этого метода является субъективность оценки. Кроме того, при этом методе необходимо иметь большое количество образцов, различных по форме, материалам, способу обработки. Вместе с тем образцы подвержены коррозии, что снижает их точность.
§ 3. Взаимозаменяемость деталей
Важнейшей предпосылкой, обеспечивающей экономичность производства и эксплуатацию машин, механизмов и приборов с минимальными простоями, а также ускорение их ремонта, является взаимозаменяемость деталей.
Готовые детали, которые можно использовать без дополнительной обработки (пригонки) при сборке узла или машины, а также для замены изношенных деталей, называются взаимозаменяемыми.
Взаимозаменяемость деталей исключает необходимость трудоемкой работы по пригонке деталей при монтаже, позволяет обеспечивать высокие темпы сборки на конвейере. Кроме того, взаимозаменяемые детали в процессе обработки легко устанавливать в приспособления. Взаимозаменяемость стала основой не только поточной сборки, но и необходимой предпосылкой комплексной механизации и автоматизации цехов и заводов.
Различают взаимозаменяемость полную и неполную (ограниченную). Полная взаимозаменяемость деталей (соответственно узлов) определяется их способностью занимать свои места в узле, механизме, машине, приборе при сборке или ремонте без какой- либо механической или ручной пригонки и после установки на место выполнять свои функции с соблюдением необходимых технических требований. Неполная, или ограниченная, или частичная, взаимозаменяемость характеризуется частичным или групповым подбором деталей по месту, либо сортировкой по размерам и группам, либо дополнительной обработкой в процессе сборочных операций одной из деталей, входящих в комплект соединения. Взаимозаменяемость обеспечивается изготовлением деталей с известными отклонениями от расчетных (номинальных) размеров. Обязательным условием взаимозаменяемости является, как мы уже говорили, изготовление деталей с определенной степенью точности в пределах допустимых отклонений. Эти отклонения обусловливаются Государственными стандартами. |
§ 4. Номинальные, действительные и предельные размеры При изготовлении деталей практически нельзя получить абсолютной точности размеров, но в этом и нет необходимости. Известно, что если отклонения размеров не выходят за определенные величины, то все детали с такими размерами будут одинаково годными для работы в машинах или механизмах. Во многих случаях нет необходимости добиваться высокой точности обработки, так как это увеличивает ее стоимость.
Размеры, указываемые на чертежах, бывают номинальные и предельные (рис. 74). Рис. 74. Графическое изображение размеров и отклонений и допусков (а), пример обозначений (б) Номинальным размером называется размер, полученный из расчета на прочность, жесткость и т. п., исходя из конструктивных и технологических соображений, согласованный с соответствующим стандартом и проставляемый на чертежах. Номинальные размеры принимают по ГОСТ 6636—62, от них отсчитываются отклонения. Действительным размером называется размер, полученный в результате непосредственного измерения с наивысшей практически допустимой точностью. Действительный размер готовой детали всегда будет отличаться от номинального, он бывает больше или меньше номинального. Однако разность между номинальным и действительным размерами не может превышать определенной величины. Предельными размерами называются два предельных значения размера, между которыми может колебаться действительный размер. Большее из них называется наибольшим предельным размером, меньшее — наименьшим предельным размером. Предельными размерами ограничиваются действительные размеры годных деталей, полученные измерением с допустимой погрешностью.
| ||||||||
§ 5. Понятие о допуске
Допуском размера называется разность между наибольшим и наименьшим предельными размерами. Величина допуска обозначается в десятых, сотых долях миллиметра, микронах (0,001 мм). Допуск указывают в виде двух отклонений от номинального: верхнего и нижнего.
Верхним предельным отклонением называется алгебраическая разность между наибольшим предельным размером и номинальным, а нижним предельным отклонением — алгебраическая разность между наименьшим предельным размером и номинальным.
Правильный выбор допуска имеет решающее значение для экономичности изготовления детали. Чем меньше допуск, тем сложнее изготовление деталей, выше стоимость станков и инструментов для их обработки и контроля. Выбирают такие допуски, которые обеспечивают надежную работу детали.
При графическом изображении допусков и посадок пользуются нулевой линией.
Нулевой линией называется линия, соответствующая номинальному размеру. Положительные отклонения в микронах откладываются вверх от нулевой линии, отрицательные — вниз.
Полем допуска называется интервал значений размеров между верхним и нижним отклонениями. Верхняя граница поля допуска соответствует наибольшему предельному размеру, нижняя граница — наименьшему предельному размеру.
Величина поля допуска зависит от назначения детали и от величины номинального размера. Размер готовой детали (действительный размер) должен лежать внутри поля допуска, т. е. между наибольшим и наименьшим предельными размерами. Если это требование не соблюдено, то деталь не соответствует предъявленным к ней требованиям и бракуется.
На чертежах номинальный размер обозначается целыми числами, а отклонения в виде десятичной дроби проставляются рядом с номинальным размером одно над другим: верхнее — вверху, нижнее — внизу. Перед цифрой положительного отклонения ставится знак плюс (+), перед цифрой отрицательного отклонения знак минус (—). Например
Как видно из примера, номинальный размер будет равен 30 мм, верхне отклонение +0,03, нижнее -0,02. Отсюда наибольший предельный размер 30 + 0,03=30,03 мм, наименьший предельный размер 30 - 0,02 = 29,98 мм. Следовательно, допуск в данном случае равняется: 30,03 - 29,98=0,05 мм.
Графическое изображение допусков показано на рис. 74, б.
Посадки, зазоры и натяги
В соединении двух деталей, входящих одна в другую, различают внешнюю охватывающую и внутреннюю охватываемую поверхности соединения. Если охватывающая и охватываемая поверхности соединения являются круглыми, цилиндрическими поверхностями, то соединение называется гладким цилиндрическим. Если охватывающая и охватываемая поверхности образованы двумя параллельными плоскостями каждая, то соединение называется плоским с параллельными плоскостями.
У цилиндрических соединений охватывающую поверхность обычно называют отверстием, а охватываемую — валом. Названия «отверстие» и «вал» условно применимы также и к другим охватывающим и охватываемым поверхностям.
Посадкой называется характер соединения деталей, определяемый величиной получающихся в нем зазоров или натягов. Посадка характеризует большую или меньшую свободу относительного перемещения соединяемых деталей или степень сопротивления их взаимному смещению.
Зазором называется положительная разность между диаметрами отверстия и вала (при условии диаметр отверстия больше диаметра вала), создающая свободу относительного движения сопрягаемых деталей (рис. 75, а).
Рис. 75. Соединения деталей:
а — зазоры, б — натягн
Натягом называется отрицательная разность между диаметром вала и отверстия до сборки деталей (размер вала больше размера отверстия), характеризующая степень неподвижности соединения сопрягаемых деталей (рис. 75, б).
В связи с тем, что размеры охватываемой и охватывающей поверхности деталей могут быть больше или меньше номинального размера, зазоры и натяги могут быть наибольшими и наименьшими.
Самый большой зазор получится в том случае, если соединить между собой втулку (отверстие), имеющую самый большой диаметр, с валом наименьшего диаметра. Наибольшим зазором называется положительная разность между наибольшим предельным размером отверстия и наименьшим предельным размером вала.
Самый малый зазор получится в том случае, если соединить втулку с самым малым диаметром с валом самого большого диаметра. Следовательно, наименьшим зазором называется положительная разность между наименьшим предельным размером отверстия и наибольшим предельным размером вала.
Средний зазор — это среднее арифметическое между наибольшим и наименьшим зазорами.
Самый большой натяг получится в том случае, если соединить вал, имеющий самый большой диаметр, с отверстием наименьшего диаметра. Следовательно, наибольшим натягом называется отрицательная разность между наибольшим предельным размером вала и наименьшим предельным размером отверстия.
Самый малый натяг получится в том случае, если соединить вал, имеющий самый малый диаметр, и втулку наибольшего диаметра. Таким образом, наименьшим натягом называется отрицательная разность между наименьшим предельным размером вала и наибольшим предельным размером отверстия.
Средний натяг — это среднее арифметическое между наибольшим и наименьшим натягами.
В зависимости от взаимного расположения полей допусков отверстия и вала посадки подразделяются на три группы:
Рис. 76. Посадки:
а — с зазором (подвижные), б — с натягом (неподвижные), в — переходные
К посадкам с зазором относятся посадки, у которых поле допуска отверстия расположено над допуском вала, в том числе и скользящие посадки, у которых нижняя граница поля допуска отверстия совпадает с верхней границей поля допуска вала. Посадки с зазором применяются тогда, когда детали в сопряжении должны свободно перемещаться одна относительно другой.
К посадкам с натягом относятся посадки, у которых поле допуска вала расположено над полем допуска отверстия.
К переходным посадкам относятся посадки, у которых поля допусков отверстия и вала перекрываются.
Допуском посадки называется разность между наибольшим и наименьшим зазорами (в посадках с зазором) или наибольшим и наименьшим натягами (в посадках с натягом).
В переходных посадках допуск посадки равен алгебраической разности между наибольшим и наименьшим натягами или сумме шего зазора.
Каждой посадке дано название и соответствующее обозначение (табл. 1).
Таблица 1
Виды посадок
Посадки неподвижные характеризуются наличием гарантированного натяга, т. е. при этих посадках наименьший натяг больше нуля. Следовательно, для получения неподвижной посадки необходимо, чтобы диаметр сопрягаемого вала был больше диаметра сопрягаемого отверстия.
Горячая посадка (Гр) применяется в соединениях, которые никогда не должны разбираться, например бандажи железнодорожных колес, стяжные кольца и др. Для получения такой посадки деталь с отверстием нагревается до температуры 400—500° С, после чего производится насадка на вал.
Прессовая посадка (Пр) применяется для прочного соединения деталей. Эта посадка осуществляется под значительным усилием гидравлического или механического пресса или специального приспособления. Примером такой посадки может служить посадка втулок, зубчатых колес, шкивов и пр.
Легкопрессовая посадка (Пл) применяется в тех случаях, когда требуется возможно более прочное соединение, и в то же время недопустима сильная запрессовка из-за ненадежности материала или из-за опасения деформировать детали. Такая посадка осуществляется под легким давлением пресса.
Переходные посадки не гарантируют натяга или зазора, т. е. одна пара деталей, соединенных с одной из переходных посадок, может иметь натяг, а другая пара, сопряженная с такой же посадкой, зазор. Чтобы повысить степень неподвижности деталей, соединенных с переходными посадками, применяется дополнительное крепление винтами, штифтами и т. п. Чаще всего эти посадки применяются при необходимости обеспечить соосность, т. е. совпадение осевых линий двух деталей, например вала и втулки.
Глухая посадка (Г) применяется для соединения деталей, которые при всех условиях работы должны быть связаны прочно и могут быть собраны или разобраны при значительном давлении. При таком соединении детали дополнительно крепят шпонками, стопорными винтами, например зубчатые колеса, которые вследствие износа нужно заменить, планшайбы на шпинделях токарных станков, неразрезные подшипниковые втулки, золотниковые и круглые втулки и пр. Осуществляется эта посадка сильными ударами молотка.
Тугая посадка (Т) применяется для часто разбираемых соединений, детали которых должны прочно соединяться и могут быть собраны или разобраны со значительным усилием.
Напряженная посадка (Н) применяется для соединения таких деталей, которые при работе должны сохранять свое относительное положение и могут быть собраны или разобраны без значительных усилий с помощью ручного молотка или съемника. Чтобы соединенные с такой посадкой детали не проворачивались и не сдвигались, их закрепляют шпонками или стопорными винтами. Эта посадка, осуществляемая ударами молотка, применяется для соединения зубчатых колес, часто сменяющихся втулок подшипников, которые при разборке машин вынимаются, подшипников качения на валах, шкивах, сальниковых втулок, маховиков на кривошипных и иных валах, фланцах и т. п.
Плотная посадка (П) применяется для соединения таких деталей, которые собирают или разбирают вручную или же при помощи деревянного молотка. С такой посадкой соединяются детали, требующие точной центровки: поршневые штоки, эксцентрики на валах, ручных маховичках, шпинделях, сменных зубчатых колесах, установочных кольцах и т. п.
Подвижные посадки характеризуются наличием гарантированного зазора, т. е. при этих посадках наименьший зазор больше нуля; применяются для свободных соединений, т. е. когда между валом и отверстием должен быть зазор.
Скользящая посадка (С) применяется для соединения деталей, которые при наличии смазки могут перемещаться относительно друг друга от руки, но имеют точное направление.
С такой посадкой соединяются сменные зубчатые колеса на станках, фрезы на оправках, шпиндели на задних бабках токарных станков, различные золотники в приборах регулирования и распределения, шариковые подшипники в корпусах машин. Соединения со скользящей посадкой должны иметь самый малый зазор.
Посадка движения (Д) является самой точной из подвижных посадок; она применяется для соединения деталей с небольшим, но определенным зазором, например, подшипников, шпинделей сверлильных станков, ползунов долбежных станков, передвижных зубчатых колес и т. д.
Наружные кольца шариковых и роликовых подшипников могут устанавливаться в корпус также с посадкой движения.
Посадка ходовая (X) применяется для соединения деталей, которые должны перемещаться одна в другой с более заметным зазором, чем при посадке движения. Ходовая посадка широко распространена в тракторостроении и комбайностроении. Шейки коленчатых валов в подшипниках, поршни в цилиндрах, звездочка контрпривода комбайна на валу и многие другие сопряжения имеют ходовые посадки.
Легкоходовая посадка (Л) применяется для соединения деталей, которые должны перемещаться с большим зазором одна в другой, например длинных валов в подшипниках скольжения.
Легкоходовую посадку имеют также многие детали масляных насосов, например палец во втулке ведомого зубчатого колеса, валик во втулке маслонасоса, валик привода маслонасоса во втулке кронштейна и др.
Широкоходовая посадка (Ш) является самой свободной и имеет самый большой зазор. Предназначена для соединения деталей, которые должны свободно перемещаться одна относительно другой, например подшипники в сельскохозяйственных машинах.
Широкоходовая посадка применяется также в особых случаях, например для соединения деталей, которые при работе нагреваются до значительных температур. Широкоходовую посадку имеют стержни клапанов в направляющих втулках.
§ 7. Система допусков и посадок для гладких цилиндрических изделий
Системой допусков и посадок определяется строгий порядок условий изготовления и приема деталей в отношении допустимых отклонений их действительных размеров и форм от заданных.
Система допусков—это закономерная планово построенная совокупность допусков и посадок, обеспечивающая взаимозамен няемость деталей.
Введение системы допусков и посадок потребовало от промышленности изготовления взаимозаменяемых деталей. В связи с тем, что существует международная торговля машинами, приборами и прочими предметами машиностроительного производства, создана единая международная система допусков. Система допусков и посадок подразделяется на две основные системы: систему отверстия и систему вала. Системой отверстия называется совокупность посадок, в которых предельные отклонения отверстий одинаковы (при одном и том же классе точности и одном и том же номинальном размере), а различные посадки достигаются путем изменения предельных отклонений валов (рис. 77, а). Во всех стандартных посадках системы отверстия нижнее отклонение отверстий равно нулю. Такое отверстие называется основным. Поля допусков основных отверстий обозначаются буквой А. Рис. 77. Системы допусков: Системой вала называется совокупность посадок, в которых предельные отклонения валов одинаковы (при одном и том же классе точности и одном и том же номинальном размере), а различные посадки достигаются путем изменения предельных отклонений отверстий (рис. 77, б). Во всех стандартных посадках системы вала верхнее отклонение вала равно нулю. Такой вал называется основным. Поля допусков основных валов обозначаются буквой В. ГОСТ 7713—62 приняты система вала и система отверстия. Предприятия выбирают ту или иную систему, исходя из экономической целесообразности. Система отверстия имеет некоторые преимущества перед системой вала и наиболее распространена на заводах, производящих станки для обработки металлов, дерева, небольшие точные станки и приборы, различные двигатели и т. п. При работе по системе отверстия требуется меньше режущего и измерительного инструмента, так как все отверстия обрабатываются инструментом, который не требует настройки станка на размер обрабатываемого отверстия. Кроме того, пригонка вала к отверстию значительно проще и дешевле, чем пригонка отверстия к валу. Однако в некоторых случаях более целесообразно применять систему вала. |
§ 8. Классы точности
В зависимости от величины допусков отверстий и валов ряды допусков и посадок группируются по классам точности. По стандартам посадки установлены в следующих классах точности (в порядке убывания точности): для размеров от 0,1 до 1 и от 1 до 500 мм: 1; 2; 2а; 3; За; 4 и 5; для размеров свыше 500 до 10 000 мм: 2; 2а; 3; За; 4 и 5; для размеров менее 0,1 мм (по ГОСТ 8809—58) установлены лишь ряды допусков в классах точности 01; 0; 1; 2; 2а; 3; За; 4 и 5.
Для случаев, когда нет необходимости в допусках, предусмотренных для валов и отверстий стандартных посадок, установлены «большие допуски»:
В зависимости от назначения детали изготовляют по тому или иному классу точности. По 1-му классу точности изготовляют особо точные детали, например, детали приборов, измерительных инструментов, кольца шарикоподшипников. Этот класс точности вследствие чрезвычайно небольшого предела отклонения от номинального размера имеет ограниченное применение, так как для получения такой точности требуются специальные особо точные приборы и приемы обработки. 2-й класс точности является основным и применяется в точном машиностроении. По этому классу точности обрабатывают наиболее ответственные детали металлорежущих станков, автомобилей, тракторов, комбайнов, текстильных, обувных и многих других машин и механизмов. 3-й класс точности широко применяется в тяжелом машиностроении, тракторостроении и комбайностроении. По этому классу точности обрабатываются, например, рабочие поверхности гильз цилиндров. Класс точности 2а является промежуточным между 2 и 3-м классами, а класс точности За — промежуточным между 3 и 4-м классами. Промежуточные классы точности находят применение в некоторых отраслях промышленности, где не требуется высокая точность. 4-й класс точности довольно широко распространен и применяется при изготовлении деталей с относительно большими допусками, например, неответственных деталей сельскохозяйственных машин, паровозов и др. 5-й класс точности применяется при грубой обработке деталей. По этому классу обрабатываются многие детали сельскохозяйственных машин и некоторые детали тракторов и комбайнов и различных грубых механизмов. 6-й класс точности ГОСТ 3047—66 установлен для деталей небольших размеров (менее 1 мм) и применяется редко. 7; 8; 9; 10 и 11-й классы точности имеют самые большие допуски на изготовление, поэтому отклонения фактических размеров детали от номинального размера могут быть весьма значительными. С такими классами точности изготовляются детали, не имеющие сопряжений, т. е. заготовки, поковки и литье. | |||||
§ 9. Обозначение допусков на чертежах
ГОСТ 3047—66 предусматривает определенный порядок обозначений размеров, отклонений, посадок, классов точности на рабочих и сборочных чертежах.
На чертежах деталей предельные отклонения указываются непосредственно после номинального размера. При этом обычно на рабочих чертежах отклонения указываются цифрами, а на сборочных чертежах — условными обозначениями — символами (буквами), присвоенными той или иной посадке с добавлением индекса, указывающего класс точности сопряжения. Числовые значения отклонений, проставляемые на рабочих чертежах, выписываются из таблиц.
Допустим, что на чертеже проставлен размер Он читается так: номинальный размер диаметра равен 50 мм, наибольший предельный размер диаметра равен: 50+0,05=50,05 мм, наименьший предельный размер: 50—0,03=49,97 мм. Все детали, изготовленные с действительными размерами диаметра, колеблющимися в пределах от 49,97 до 50,05 мм, окажутся годными. Буквенные обозначения, относящиеся к отверстию, пишутся над чертой дроби, а относящиеся к валу — под чертой дроби, например Такая запись означает, что сопряжение имеет номинальный размер 25 и выполняется по системе вала В (основной деталью является вал), а сопрягаемая деталь (отверстие) изготовляется с допуском, соответствующим плотной (П) посадке. Отверстие выполняется по 2а классу точности, а вал — по 3-му. Для определения абсолютных отклонений пользуются таблицами допусков, которые составлены для каждого класса точности по системе вала и по системе отверстия отдельно. Для выбора отклонений необходимо знать номинальный размер сопряжений, систему посадки, класс точности и посадки. Если обработка производится по системе отверстия А, отклонения размеров диаметра отверстия и вала находят по таблицам для системы отверстия соответствующего класса точности. При обработке по системе вала В отклонения вала и отверстия находят по таблицам системы вала соответствующего класса точности. |
Глава XIII. Разметка
§ 1. Понятие о разметке. Виды разметки
Заготовки поступают на обработку в виде отливок (получают из металла, заливаемого в предварительно подготовленные формы — земляные, металлические и т. п.), поковок (получают ковкой или штамповкой), либо в виде кусков прокатного материала — листов, прутков и т. д. (получают путем пропуска металла между вращающимися в разные стороны валиками, имеющими профиль, соответствующий получаемому прокату).
Размеры заготовки всегда больше размеров будущего изделия. При обработке с поверхности заготовки удаляется определенный слой металла (припуск), в результате чего уменьшаются ее размеры.
Чтобы не допустить ошибки при изготовлении детали на заготовке откладывают точно по чертежу размеры детали и отмечают их линиями (рисками), обозначающими границы обработки, до которых следует снимать слой металла.
Операция по нанесению на поверхность заготовки линий, определяющих форму и размеры детали называется разметкой.
Разметка применяется преимущественно в индивидуальном и мелкосерийном производстве. На заводах крупносерийного и массового производства надобность в разметке отпадает благодаря использованию специальных приспособлений — кондукторов, упоров и т. п.
В настоящее время применяют три основные группы разметки: машиностроительную, котельную и судовую. Машиностроительная разметка является самой распространенной операцией слесарной обработки. Котельная и судовая разметки имеют некоторые особенности, и им посвящена специальная литература.
В зависимости от формы размечаемых заготовок и деталей разметка бывает плоскостная и пространственная (объемная).
Плоскостная разметка — это нанесение рисок на поверхности плоских деталей, листовом и полосовом металле, а также на поверхностях литых и кованых деталей.
При пространственной разметке разметочные линии наносят в нескольких плоскостях или на нескольких поверхностях.
Применяют различные способы разметки: по чертежу, шаблону, образцу и по месту. Выбор способа разметки определяется формой заготовки, требуемой точностью и количеством изделий, подлежащих изготовлению.
Точность выполнения разметки в значительной мере влияет на качество обработки. Степень точности разметки колеблется в пределах 0,25—0,5 мм. Ошибки, допущенные при разметке, обычно приводят к браку и порче ценного материала.
На машиностроительных заводах разметку осуществляют рабочие разметчики, однако и слесарю часто приходится выполнять ее.
§ 2. Разметочные плиты
На разметочной плите (ГОСТ 10905—64) устанавливают подлежащие разметке детали и располагают все приспособления и инструмент. Разметочная плита отливается из серого мелкозернистого чугуна, в нижней части она имеет ребра жесткости, которые предохраняют плиту от возможного прогиба под тяжестью собственного веса и размечаемых деталей. Верхнюю, рабочую поверхность и боковые стороны плиты точно обрабатывают на строгальных станках и затем шабрят.
На рабочей поверхности больших плит иногда делают продольные и поперечные канавки на равных расстояниях одна от другой (200—250 мм), образующие равные квадраты. Канавки имеют глубину 2—3 мм, ширину 1—2 мм, они облегчают установку на плите различных приспособлений. Размер плиты выбирают так, чтобы ее ширина и длина были на 500 мм больше соотве
![]() Типы сооружений для обработки осадков: Септиками называются сооружения, в которых одновременно происходят осветление сточной жидкости... ![]() Состав сооружений: решетки и песколовки: Решетки – это первое устройство в схеме очистных сооружений. Они представляют... ![]() Семя – орган полового размножения и расселения растений: наружи у семян имеется плотный покров – кожура... ![]() Двойное оплодотворение у цветковых растений: Оплодотворение - это процесс слияния мужской и женской половых клеток с образованием зиготы... © cyberpedia.su 2017-2024 - Не является автором материалов. Исключительное право сохранено за автором текста. |