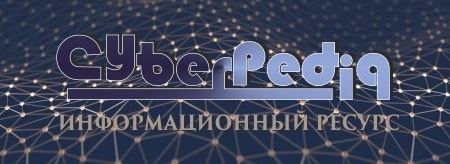
Наброски и зарисовки растений, плодов, цветов: Освоить конструктивное построение структуры дерева через зарисовки отдельных деревьев, группы деревьев...
Биохимия спиртового брожения: Основу технологии получения пива составляет спиртовое брожение, - при котором сахар превращается...
Топ:
Отражение на счетах бухгалтерского учета процесса приобретения: Процесс заготовления представляет систему экономических событий, включающих приобретение организацией у поставщиков сырья...
Характеристика АТП и сварочно-жестяницкого участка: Транспорт в настоящее время является одной из важнейших отраслей народного...
Процедура выполнения команд. Рабочий цикл процессора: Функционирование процессора в основном состоит из повторяющихся рабочих циклов, каждый из которых соответствует...
Интересное:
Финансовый рынок и его значение в управлении денежными потоками на современном этапе: любому предприятию для расширения производства и увеличения прибыли нужны...
Отражение на счетах бухгалтерского учета процесса приобретения: Процесс заготовления представляет систему экономических событий, включающих приобретение организацией у поставщиков сырья...
Уполаживание и террасирование склонов: Если глубина оврага более 5 м необходимо устройство берм. Варианты использования оврагов для градостроительных целей...
Дисциплины:
![]() |
![]() |
5.00
из
|
Заказать работу |
В зависимости от назначения изготовляемых изделий металлы и сплавы должны обладать определенными свойствами. Чтобы судить о том, будет ли данный металл или сплав пригоден для изготовления той или иной детали, нужно знать, какие свойства он имеет.
Свойства металла разделяют на физические, химические, механические и технологические.
К физическим свойствам относятся: удельный вес, температура плавления (плавкость), тепловое расширение, электропроводность, электросопротивление, теплопроводность, теплоемкость, способность намагничиваться и др.
Удельным весом металла или сплава называется вес 1 см3 его, выраженного в граммах.
Наименьший удельный вес из всех металлов имеет литий (0,53 Г/см3), магний (1,74 Г/см3), цезий (1,83 Г/см3) и алюминий (2,7 Г/см3).
Тепловое расширение — это способность металлов и сплавов расширяться, т. е. изменять объем и линейные размеры при нагревании.
Способность металла изменять объем и линейные размеры в процессе нагревания и охлаждения нужно учитывать при конструировании и изготовлении точных измерительных инструментов, при горячей штамповке металлов, застывании отливок и во многих других случаях.
Увеличение (приращение) единицы объема металла при повышении его температуры на 1°С называется коэффициентом объемного расширения.
Увеличение (приращение) единицы длины металла при повышении его температуры на 1°С называется коэффициентом линейного расширения.
Температурой плавления называется температура, при которой металл при нагревании переходит из твердого состояния в жидкое. Каждый металл в чистом виде имеет свою определенную температуру плавления. В зависимости от температуры плавления металлы и сплавы делятся на тугоплавкие, обладающие высокой температурой плавления, и легкоплавкие, имеющие низкую температуру плавления.
Температуру плавления металлов учитывают при плавке металлов, изготовлении отливок и нагревающихся в работе деталей машин (например, подшипников скольжения и др.), при паянии, лужении, сварке.
Электропроводностью называется способность металлов и сплавов проводить электрический ток. Сплавы, как правило, обладают меньшей электропроводностью, чем чистые металлы.
Электросопротивлением называется способность металлов сопротивляться прохождению через них электрического тока, характеризуется удельным сопротивлением в омах, показывающим величину сопротивления прохождению тока по проводнику длиной 1 м и сечением 1 мм2.
Теплопроводность — свойство металла проводить тепло. Лучшие проводники электрического тока являются вместе с тем и лучшими проводниками тепла. Теплопроводность металлов и сплавов измеряется количеством тепла, которое проходит по металлическому стержню сечением 1 см2 за одну минуту.
Удельная теплоемкость — это количество тепла, необходимое для повышения температуры 1 кг металла на 1°С.
Некоторые металлы и сплавы обладают магнитными свойствами. Способность металла намагничиваться оценивается величиной, называемой магнитной проницаемостью. Магнитная проницаемость воздуха принята за единицу, а у железа она составляет 2000—3000 единиц. У меди и алюминия магнитная проницаемость близка к единице.
К химическим свойствам металлов и их сплавам относятся окисляемость, растворяемость и коррозионная стойкость. Особенно важна коррозионная стойкость для деталей, приборов и машин, работающих в агрессивных средах (кислоты, щелочи, растворы солей и др.).
Коррозии, т. е. разрушению в результате действия внешней среды — воздуха, влаги, химических веществ и т. д.,— подвержено в большей или меньшей степени большинство металлов и сплавов, кроме так называемых благородных металлов (золото, платина и некоторые другие). Виды коррозии и меры борьбы с ней изложены в главе VIII.
§ 2. Механические свойства металлов и сплавов
К механическим свойствам относят совокупность свойств, характеризующих способность металлов и сплавов сопротивляться воздействию внешних сил. Основными показателями, характеризующими механические свойства металлических материалов, являются прочность, пластичность, твердость, ударная вязкость. Внешние силы, или, как их принято называть, нагрузки, могут иметь самый разнообразный характер.
По характеру действий нагрузки делятся на статические и динамические. Статической нагрузкой называют нагрузку, возрастающую медленно от нуля до некоторого максимального значения и далее остающуюся постоянной или меняющуюся незначительно. Динамической нагрузкой называют нагрузку, возникающую в результате удара, когда действие нагрузки исчисляется малыми долями секунды. Виды деформации Изменение формы твердого тела под действием приложенных к нему внешних сил (нагрузок) называется деформацией тела. Деформации, исчезающие после снятия нагрузки (т. е. материал принимает первоначальные размеры и форму), называют упругими, деформации, не исчезающие после снятия нагрузки (т. е. материал получил удлинение, форма его изменилась), называют его остаточными или пластическими. Различают следующие основные виды деформаций: сжатие, растяжение, сдвиг (срез), кручение, изгиб (рис. 5). Рис. 5. Основные виды деформации металла Сжатие. Это деформация, состоящая в уменьшении объема тела под действием сдавливающих его сил. Сжатие испытывают колонны, на которые опираются своды, фундаменты машин, котлов. Растяжение. Это деформация, состоящая в увеличении длины тела (стержня), когда к обоим его концам приложены силы, равнодействующие которых направлены вдоль оси тела (стержня). Растяжение испытывают тросы, к которым подвешены грузы, болты, крепящие детали и механизмы, приводные ремни и т. д. Кручение. Это деформация тела (стержня, бруска) с одним закрепленным концом под действием пары сил (две равные противоположно направленные силы), плоскость которых перпендикулярна к оси тела (например, валы станков, двигателей). Произведение силы, вызывающей скручивание, на расстояние между обеими силами называется крутящим моментом. Сдвиг (срез). Если две силы направлены друг другу навстречу, а направление сил, действующих на тело, лежит не на одной прямой, но близко друг к другу, то при достаточной величине сил происходит срез. На срез работают заклепки, стяжные болты и т. п. Деформация, предшествовавшая срезу и заключающаяся в перекашивании прямых углов элементарных параллелепипедов, называется сдвигом. При сдвиге соседние сечения детали сдвигаются одно относительно другого, оставаясь параллельными. Изгиб. Деформация бруса (балки) под действием внешних сил, сопровождающаяся изменением кривизны деформируемой детали, называется изгибом. Изгиб испытывают балки, на которые подвешены тали для подъема груза, стрелы подъемных кранов, рельсы под тяжестью поезда, валы машин и т. д. Длинные и сравнительно тонкие детали, находящиеся на двух опорах (валы, трубы, брусья, балки) подвергаются также деформации изгиба и без приложения груза, а только от собственного веса, если расстояние между опорами больше допустимых пределов для данного сечения детали. Прочность Под прочностью металла или сплава понимают его свойство сопротивляться разрушению под действием внешних сил. В зависимости от характера действия этих сил различают прочность на растяжение, сжатие, изгиб, кручение, усталость и ползучесть. Для испытания на растяжение из металла или сплава изготовляют образцы, форма и размеры которых установлены государственным стандартом (рис. 6). Рис. 6. Образцы для испытания иа растяжение: Расчетная длина образцов равна десятикратному или пятикратному диаметру, образец диаметром 20 мм принято называть нормальным. Головки образцов, помещаемые в захваты а также закругления переходной части, не участвующие в испытании, имеют также установленные размеры. Если профиль металла не позволяет изготовить образцы круглого сечения (например, из листового металла), для испытания берут плоские образцы. Испытание прочности труб, тонких прутков и проволоки производится в натуральном виде, т. е. без изготовления образцов. Испытание на растяжение производится на разрывных машинах (рис. 7). Мощность этих машин различна и достигает 50 Т. Все узлы машины крепятся к станине 2. В верхний и нижний захваты 4 машины закрепляют головки образца 3. Верхний захват закреплен неподвижно, а нижний захват с помощью особого механизма медленно опускается, растягивая образец до его разрыва. Рис. 7. Разрывная машина Нагрузка (растягивающая сила), которой подвергается образец при испытании, отмечается на шкале 1. При испытании на растяжение показатели прочности могут быть получены из так называемой диаграммы растяжения, которая автоматически вычерчивается на барабане некоторых конструкций разрывных машин. Эта диаграмма характеризует поведение материала при разных нагрузках. Условная диаграмма растяжения для мягкой углеродистой стали изображена на рис. 8. По горизонтальной линии диаграммы откладывается абсолютное удлинение образца в миллиметрах, а по вертикальной линии — нагрузка в килограммах. Рис. 8. Диаграмма растяжения Как видно из диаграммы до точки Рр — увеличение нагрузки вызывает пропорциональное удлинение образца: если, например, нагрузка увеличилась в два раза, то и длина образца также увеличилась в два раза. Нагрузка, соответствующая точке Рр называется нагрузкой предела пропорциональности. Наибольшее напряжение, до которого деформации в металле растут прямо пропорционально нагрузке, называется пределом пропорциональности σр (σ — сигма). Образец при этом испытывает напряжения, которые вызывают упругую деформацию, т. е. деформацию, которая исчезает после снятия нагрузки, и образец принимает свою первоначальную длину. Очень точные измерения показали, что весьма упругие металлические материалы даже при самой небольшой нагрузке получают остаточные деформации; но практического значения они не имеют, так как величина их очень мала. При увеличении нагрузки растут и остаточные деформации. Пределом упругости σу, называют такое напряжение, при котором образец получает остаточное удлинение, равное 0,005% первоначальной длины образца. Практически величина предела упругости, например стали, очень близка к пределу пропорциональности. На диаграмме несколько выше предела пропорциональности образуется участок, на котором удлинение образца начинает расти без заметного увеличения нагрузки, металл, как говорят в этом случае, «течет». Нагрузка, при которой металл начинает течь, называется нагрузкой предела текучести Рs. Образец после снятия этой нагрузки уже не может принять первоначальную длину. Отношение нагрузки предела текучести к площади поперечного сечения образца называется пределом текучести σs. После перехода за предел текучести образец снова начинает оказывать сопротивление растяжению, но удлинение образца уже начинает расти быстрее напряжений, возникающих в образце. Затем сечение образца начинает сужаться (образуется шейка) при падении нагрузки и в точке Рь образец разрывается. Наибольшая нагрузка Рь, при которой у образца появляется шейка, называется нагрузкой предела прочности при растяжении, а напряжение, соответствующее наибольшей нагрузке, называется пределом прочности при растяжении и обозначается буквой σь. Предел прочности металла определяется как отношение наибольшей нагрузки Рь к первоначальной площади поперечного сечения образца F0, т. е. где Рь — наибольшая нагрузка, при которой образец разрушается, кГ; Предел текучести и предел прочности являются важнейшими характеристиками, они применяются в расчет прочности детали, Пластичность Пластичностью называют свойство металлов и сплавов под действием нагрузки изменять форму, не разрушаясь, и сохранять принятую форму после прекращения действия нагрузки. О пластичности металлического материала судят по величине удлинения образца и уменьшения его поперечного сечения при испытании на растяжение; чем больше удлиняется образец, тем более пластичен металл. Пластичные металлы и сплавы поддаются ковке, прессованию и другим способам обработки давлением. Хрупкие металлы при испытании на разрыв не получают удлинения или оно незначительно. Такими металлами являются чугун и закаленная сталь и другие металлы и сплавы. Характеристикой пластичности металлов являются относительное удлинение и относительное сужение. Относительным удлинением δ (дельта) называется отношение величины приращения длины образца после разрыва к его первоначальной длине, выраженное в процентах. Таким образом, общее выражение для расчета величины относительного удлинения имеет следующий вид где l1 — длина после разрыва, мм; Относительное сужение Ψ; (пси) — отношение уменьшения площади поперечного сечения образца после испытания к первоначальной площади его поперечного сечения, выраженное в процентах где F0 - площадь поперечного сеченая образца до начала испытания, мм2; Ударная вязкость Ударной вязкостью называется способность металлов и сплавов оказывать сопротивление действию ударных нагрузок. Ударная вязкость является важной характеристикой материала деталей, которые в процессе работы машины испытывают ударную нагрузку (например, коленчатые валы, оси колес и другие детали). Для испытания материала на ударную вязкость изготовляют образцы в виде брусков с квадратным сечением и определенных размеров. Испытание производят на машинах, называемых маятниковыми копрами. Один из таких копров показан на рис. 9. Маятник 1 весом 10; 15 или 30 кГ, укрепленный на станине 2, поднимают на высоту Н и закрепляют в этом положении защелкой. После освобождения маятник падает и производит удар по образцу 3 со стороны, противоположной надрезу. Рис. 9. Маятниковый копер (а), образец для испытания (б) Разрушение образцов имеет различный характер. У хрупких металлов образцы разрушаются без изменения формы, у вязких металлов они подвергаются значительному изгибу в месте излома. Чтобы измерить ударную вязкость металла, сначала вычисляют, какая работа А затрачена грузом маятника на излом образца. Эта работа определяется по формуле: где Р — вес маятника, кГ; Мерой ударной вязкости служит отношение величины указанной работы А к площади поперечного сечения образца F0 в месте надреза. Полученная таким путем величина ударной вязкости обозначается буквой ан: Величина ударной вязкости ан в кГ/см2: для чугуна 0,5—1, стали 2—7, меди 5—5,5, никеля 18—18,5, цинка 0,6—0,7. При испытании на маятниковом копре следует строго соблюдать следующие правила техники безопасности: 1. Установку образца на опоры необходимо производить при малой высоте подъема маятника и обязательном использовании предохранительного приспособления. Установка образца, когда маятник поднят на полную высоту, категорически запрещается. 2. При испытании стоять сбоку (перед шкалой), а не спереди или сзади маятника. 3. Защелку отводить правой рукой только за специальную рукоятку. Твердость Твердостью называется свойство металла оказывать сопротивление проникновению в него другого, более твердого тела, не получающего остаточных деформаций. Твердость тесно связана с такими основными характеристиками металлов и сплавов, как прочность, износоустойчивость, и является важной характеристикой металла при выборе режущих инструментов (напильников, резцов, метчиков, сверл и др.). Часто по измеренной твердости металла судят о его способности сопротивляться износу, например, чем тверже сталь, тем меньше она изнашивается, и наоборот. В настоящее время имеется несколько методов определения твердости, особенно широкое распространение получили следующие методы испытаний твердости: 1. вдавливанием шарика из твердой стали (метод Бринелля), ГОСТ 9012—59; 2. вдавливанием вершины алмазного конуса или закаленного шарика (метод Роквелла), ГОСТ 9013—59; 3. вдавливанием вершины алмазной пирамиды (метод Виккерса), ГОСТ 2999—59. Для измерения твердости применяют приборы: стационарные (ГОСТ 7038—63) ипереносные (ГОСТ 9030—64). Метод Бринелля заключается в том, что шарик из закаленной шарикоподшипниковой стали под действием нагрузки Р вдавливается в металл. Диаметр шарика D, нагрузку Р и время выдержки при этой нагрузке выбирают в зависимости от твердости и толщины испытуемого материала, например, для черных металлов твердостью НВ 140—450 и толщиной испытуемого образца от 6 до 3 мм принимают шарик диаметром 10 мм, нагрузку 3000 кГ и время выдержки 10 сек; образцы толщиной менее 2 мм испытывают шариком диаметром 2,5 мм; для цветных металлов твердостью НВ 35—130 и толщиной образца от 6 до 3 мм принимают шарик диаметром 5 мм, нагрузку 250 кГ и время выдержки 30 сек. Испытание на твердость металла по методу Бринелля вдавливанием стального шарика производят на приборе ТБ (рис. 10, а). Стальной шарик крепят в шпинделе 1 прибора. Испытуемый образец 2 ставят на предметный столик 3, который подводят к шарику вращением маховика 4. При включении электродвигателя 5 груз 6 опускается и стальной шарик с помощью рычажной системы вдавливается в образец. Сначала вдавливание производится медленно, затем постепенно нагрузка увеличивается и выдерживается для получения точных границ отпечатка (рис. 10, б). Рис. 10. Определение твердости по Бринеллю: Исследуемый образец снимают со столика и измеряют диаметр полученного отпечатка (лунки) при помощи специальной лупы с ценой деления шкалы 0,1 мм. Твердость по Бринеллю обозначается буквами НВ и определяется как отношение нагрузки Р в кГ, приходящееся на 1 мм2 сферической поверхности отпечатка F, по формуле: где Р — величина нагрузки, кГ; Поверхность испытуемого образца обрабатывается в виде плоскости так, чтобы края отпечатка были достаточно отчетливы для измерения его диаметра с требуемой точностью. Поверхность испытуемого образца должна быть свободна от окалины и других посторонних веществ. Метод Роквелла отличается от метода Бринелля тем, что измеряется не диаметр отпечатка (лунки), а его глубина. Чем больше глубина вдавливания, тем меньше твердость испытуемого образца. Алмазный конус с углом конуса 120° и радиусом при вершине 0,2 мм (или стальной шарик диаметром 1,59 мм) вдавливается в испытуемый образец под действием двух последовательно прилагаемых нагрузок — предварительной нагрузки, равной 10 кГ, а затем полной (предварительная плюс основная) нагрузки 60 кГ (шкала А) или 150 кГ (шкала С). Испытание производится на приборе ТР (ГОСТ 7038—63). Алмазный конус (или стальной шарик) 3 крепят в шпинделе 4 прибора (рис. 11). Испытуемый образец 5 устанавливают на предметный столик 2 и поднимают при помощи подъемного винта 9 вращением маховичка 1. Ручкой 7 освобождают груз 8, который создает усилие для вдавливания алмазного конуса (или стального шарика) 3 в металл. Величину вдавливания определяют непосредственно по шкалам А, В и С циферблата индикатора 6 (без измерения отпечатка и расчетов). Рис. 11. Определение твердости по Роквеллу: При измерении твердости стандартной нагрузкой 150 кГ значение твердости HR отсчитывается по наружной черной шкале С индикатора, причем к обозначению твердости добавляется индекс шкалы С, т. е. HRC. При измерении твердости тонкого образца и поверхностного слоя металла со стандартной нагрузкой 60 кГ отсчет ведется по черной шкале А; к обозначению твердости добавляется индекс шкалы, т. е. HRA. При измерении твердости мягких металлов (цветных металлов, отожженной стали) стальным шариком со стандартной нагрузкой 100 кГ отсчет ведется по внутренней красной шкале Вив обозначение твердости добавляется индекс шкалы, т. е. HRB. Метод Виккерса применяется для испытания металлов и сплавов высокой твердости, деталей малых сечений и твердых тонких поверхностных слоев — цементированных, азотированных и др. При испытании твердости методом Виккерса на стационарном приборе ТВ в образец под нагрузкой до 100 кГ вдавливается вершина алмазной четырехгранной пирамиды с углом между гранями 136°, затем при помощи микроскопа, присоединенного к прибору, определяется размер диагонали отпечатка квадратной формы. На рис. 12 изображен прибор для испытания твердости вдавливанием вершины алмазной пирамиды, наконечник четырехгранной алмазной пирамиды и схема измерения диагонали отпечатка квадратной формы, оставленного вершиной алмазной пирамиды на поверхности испытуемого металла. Рис. 12. Определение твердости по Виккерсу Твердость металла HV в кГ/мм2 вычисляется отношением нагрузки Р в кГ, создаваемой прибором, к площади отпечатка (в мм2), вычисленного по его диагоналям. Обычно твердость по Виккерсу определяется по специальным таблицам по значению длины диагонали отпечатка. Нашей промышленностью выпускаются также твердомеры ТК-3, широко используемые в заводской практике (рис. 13). Рис. 13. Твердомер ТК-3 Твердомер ТК-3 предназначен для определения твердости металлов методом вдавливания алмазного конуса или стального шарика. Глубина, на которую проникает алмазный конус или стальной шарик под действием двух последовательно приложенных нагрузок, характеризует твердость испытуемого металла. На приборе рекомендуется производить испытания твердости металлов в следующих пределах: по шкале С от 20 до 70, по шкале В от 25 до 100. Прибор имеет основание 1 и корпус 13, скрепленные между собой двумя стойками 14. На основании смонтирована втулка 2, в которой с помощью маховика 3 перемещается подъемный винт 4. На винт устанавливается предметный столик 5 для испытуемых деталей. В корпусе 13 монтируется рычажная система 12 прибора, узел шпинделя 8 и индикатор 10. В шпиндель вставляется алмазный наконечник 6 или оправка со стальным шариком диаметром 1,59 мм. Предварительная нагрузка создается винтом, который поджимает испытуемый образец к наконечнику. Полная нагрузка передается на наконечник от груза 15. Приложение нагрузки осуществляется поворотом рукоятки 11 от себя, а плавность приложения нагрузки обеспечивается масляным амортизатором 9. Величину нагрузки определяют по индикатору 10. Цена деления шкалы индикатора соответствует углублению наконечника (конуса, шарика) на 0,002 мм. На испытуемой и опорной поверхностях не должно быть трещин, грубых следов обработки, царапин, выбоин, грязи, смазки или каких-либо покрытий. По выбранной шкале подбирают грузы, устанавливают и закрепляют винтом 7 соответствующий наконечник. На стол помещают испытуемый образец и вращением маховичка 3 по часовой стрелке поджимают его к наконечнику до тех пор, пока малая стрелка индикатора не станет против красной точки, а большая — в пределах пяти делений от вертикальной оси. Вращая шкалу индикатора, нужно установить ноль шкалы С (черной шкалы) против конца большой стрелки индикатора. Каждую деталь рекомендуется подвергать испытанию не менее трех раз. Первые два испытания после смены шарика или алмаза в расчет не принимаются. При более высокой твердости испытание шариком становится недостаточно точным, ввиду малой глубины проникновения шарика в металл (меньше 0,06 мм). Кроме того, при испытании твердых поверхностей шарик может деформироваться. Усталость В практике наблюдаются случаи разрушения металлов под действием нагрузок, не достигающих предела прочности этих металлов. Усталость металлов — это состояние металла или сплава, находящегося под многократным воздействием знакопеременных или однозначных, нередко вибрирующих нагрузок. Усталость металла развивается постепенно и при продолжении воздействия нагрузок может привести к разрушению металлического изделия. Свойство металлов сопротивляться разрушению от усталости называется выносливостью, Выносливость металлов и сплавов зависит от их природы, характера обработки, состояния поверхности, условий работы и т. п. Причиной разрушения металлов от усталости является хрупкое состояние, которое объясняется появлением в слабых местах металла и постепенно увеличивающихся мнкротрещин. В результате этого, разрушение наступает при напряжениях, меньших предела упругости. Данное явление необходимо учитывать в связи с применением в технике сильно нагруженных и быстроходных машин; усталостному разрушению под действием часто повторяющихся переменных нагрузок подвержены такие детали, как шатуны двигателей, коленчатые валы, пальцы, поршни и др. Испытание на усталость (выносливость) производится на различных специальных машинах. Образцы подвергаются многократной переменной нагрузке до 10 и более миллионов циклов или смен нагрузки, т. е. растяжению и сжатию, переменному по направлению изгибу, переменному по направлению кручению и др. |
§ 3. Технологические свойства
При выборе металлов и сплавов для изготовления деталей машин и конструкций большое значение имеют технологические свойства, под которыми понимают способность металла подвергаться различным видам обработки.
Из технологических свойств наибольшее значение имеют обрабатываемость резанием, свариваемость, ковкость, прокаливаемость, жидкотекучесть.
Обрабатываемость — комплексное свойство материала, в частности металла, характеризующее способность его подвергаться обработке резанием. Обычно обрабатываемость определяется по скорости резания, по усилию резания и по чистоте обработки. Испытание по скорости и усилию резания производится путем сравнения показателей, полученных при обработке данного металла, с показателями обрабатываемости определенной марки стали (автоматная сталь марки А12). Показатель чистоты обработанной поверхности определяется измерением высоты неровностей, образующихся на поверхности металла после снятия стружки режущим инструментом. Свариваемость — свойство металла давать доброкачественное соединение при сварке, характеризующееся отсутствием трещин и других пороков металла в швах и прилегающих к шву зонах. Хорошей свариваемостью обладает малоуглеродистая сталь, значительно худшей свариваемостью обладают чугун, медные и алюминиевые сплавы. Свариваемость специальных сталей (за исключением хромистых), цветных металлов и сплавов, а также чугуна удовлетворительная при соблюдении определенных технологических условий. Ковкость — способность металлов и сплавов без разрушения изменять свою форму при обработке давлением. Железо, медь, никель, алюминий, цинк, олово, свинец, сталь, латунь и многие другие металлические материалы обладают достаточно хорошей ковкостью, что позволяет подвергать их прессованию, прокатке, протяжке, ковке и штамповке. Хорошей ковкостью обладает сталь в нагретом состоянии, а в холодном состоянии — латунь и алюминиевые сплавы; пониженной ковкостью характеризуется бронза. Прокаливаемость — способность стали воспринимать закалку на определенную глубину от поверхности. Прокаливаемость стали зависит от присутствия легирующих элементов в стали и размеров зерен стали. Прокаливаемость стали определяется экспериментально, путем измерения твердости в сечении закаленного образца, а также рядом других методов, например, с помощью торцевой закалки образцов. Жидкотекучесть — способность металла или сплава в расплавленном состоянии заполнять литейную форму. Определение жидкотекучести металла производится с помощью специальных отливок в виде стержней, спиралей, решеток, клиньев и т. п. проб. Для повышения жидкотекучести металлов и сплавов к ним добавляют легирующие компоненты, например, фосфор — к медным сплавам и чугуну, кремний — к алюминию. Усадкой называется уменьшение объема или линейных размеров расплавленного металла или сплава при его застывании и охлаждении до комнатной температуры. Соответствующее изменение линейных размеров, выраженное в процентах, называется линейной усадкой. На степень усадки влияют многие факторы: химический состав металла, скорость охлаждения и др. |
§ 4. Технологические пробы
Технологическими пробами называются испытания металлов, выполняемые несложными способами и без тщательного измерения наблюдаемых свойств.
Такие испытания имеют целью выявить способность металла к тем или иным деформациям, которым он подвергается при работе или при обработке в холодном или горячем состоянии.
Удовлетворительность или неудовлетворительность металла по технологическим пробам определяется по внешнему виду после испытания (отсутствие надрывов, трещин, расслоения или излома свидетельствует о том, что металл выдержал пробу). Некоторые технологические пробы стандартизованы, т. е. испытания производятся по определенным правилам. Этими правилами установлены размеры и формы образцов испытуемых металлов, инструментов и приспособлений для выполнения пробы. Рассмотрим наиболее часто встречающиеся в практике пробы. Проба на загиб (ОСТ 1683) служит для определения способности металла (листов, прутков, различных профилей и т. д.) принимать заданный по размерам и форме загиб без надрывов и трещин. Проба на загиб применяется для пластических металлов при толщине не более 30 мм и производится в нагретом или холодном состоянии. Различают загиб на определенный угол, до параллельности загнутых сторон (рис. 14, а) или до соприкосновения сторон. Тот и другой вид загиба должен быть оговорен в технических условиях. Рис. 14. Технологические пробы: Для проведения испытания на загиб применяют специальные машины, прессы, тиски с закругленными губками. Образцы, выдержавшие пробу, не должны иметь после загиба надлома, надрывов или трещин. Проба на перегиб (ОСТ 1688) служит для определения способности металла выдерживать повторный загиб и разгиб и применяется при испытании качества полосового и листового материала длиной 100—150 мм, шириной до 20 мм и толщиной до 5 мм, а также проволоки и прутков диаметром от 0,8 до 7 мм. Проба проводится только в холодном состоянии. Проба состоит в загибе и разгибе образца в плоскости, перпендикулярной к линии взаимного касания губок прибора, в котором образец зажимается в вертикальном положении. Загиб образца производится попеременно в правую и левую сторону на 90° с равномерной скоростью не более 60 перегибов в минуту до определенного числа перегибов, указанного в технических условиях. Проба на перегиб имеет важное значение для оценки способности к деформированию проволоки, при испытании которой на разрыв невозможно определить это свойство. Проба на навивание проволоки (ГОСТ 10447—63) позволяет определить способность проволоки диаметром до 6 мм принимать заданную форму. Кусок проволоки (рис. 14, б) навивают на круглый стержень (оправку) 5—10 витками. Качество проволоки определяется способностью выдерживать без повреждений навивание и развивание в холодном состоянии, плотно прилегающими витками на стержень. Чем пластичнее проволока, тем плотнее будет ее прилегание к стержню. Проба труб на сплющивание (рис. 14,в) производится по ГОСТ 8695—58 для определения качества труб по их свойству сплющиваться без повреждений под давлением пресса, молота или от ударов молотка до предела, установленного техническими условиями. Длина образца выбирается равной диаметру трубы. В зависимости от технических условий испытание может производиться в холодном и горячем состояниях. Признаком того, что образец выдержал испытание, служит отсутствие в нем после сплющивания трещин или надрывов. Проба труб на загиб (ГОСТ 3728—47) применяется для определения способности образца трубы загибаться без повреждений. Испытание состоит в том, что заполненную сухим чистым речным песком трубу изгибают вокруг оправки на угол 90°. После загиба (рис. 14, г) труба не должна иметь надрывов, трещин, отслоений и других дефектов. Диаметр оправки определяется техническими требованиями. Проба стали на искру производится для приблизительного определения состава стали по цвету и форме искр. Определение марки стали по искре производится на наждачном круге. При нажатии проверяемого образца металла на быстро вращающийся наждачный круг образуется сноп искр, которые отличаются друг от друга по форме и цвету. Чем больше в стали содержится углерода, тем больше в ее искрах светлых звездочек. Присутствие в стали вольфрама можно установить по красному цвету искр, хрома — по оранжевому и т. д. (рис. 15). Таким образом, при известном навыке проба на искру позволяет приблизительно судить о химическом составе стали. Более точное определение химического состава стали производится в специальных заводских лабораториях. Рис. 15. Проба стали на искру Этот метод определения состава стали применяют лишь в исключительных случаях и при наличии станков с соответствующими абразивными кругами и специальных образцовых эталонов, которые используют для сравнения характера искр. |
Типы сооружений для обработки осадков: Септиками называются сооружения, в которых одновременно происходят осветление сточной жидкости...
Наброски и зарисовки растений, плодов, цветов: Освоить конструктивное построение структуры дерева через зарисовки отдельных деревьев, группы деревьев...
Индивидуальные и групповые автопоилки: для животных. Схемы и конструкции...
Общие условия выбора системы дренажа: Система дренажа выбирается в зависимости от характера защищаемого...
© cyberpedia.su 2017-2024 - Не является автором материалов. Исключительное право сохранено за автором текста.
Если вы не хотите, чтобы данный материал был у нас на сайте, перейдите по ссылке: Нарушение авторских прав. Мы поможем в написании вашей работы!