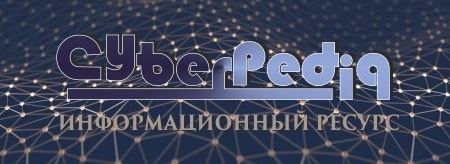
Автоматическое растормаживание колес: Тормозные устройства колес предназначены для уменьшения длины пробега и улучшения маневрирования ВС при...
Своеобразие русской архитектуры: Основной материал – дерево – быстрота постройки, но недолговечность и необходимость деления...
Топ:
Оснащения врачебно-сестринской бригады.
Выпускная квалификационная работа: Основная часть ВКР, как правило, состоит из двух-трех глав, каждая из которых, в свою очередь...
Интересное:
Берегоукрепление оползневых склонов: На прибрежных склонах основной причиной развития оползневых процессов является подмыв водами рек естественных склонов...
Мероприятия для защиты от морозного пучения грунтов: Инженерная защита от морозного (криогенного) пучения грунтов необходима для легких малоэтажных зданий и других сооружений...
Искусственное повышение поверхности территории: Варианты искусственного повышения поверхности территории необходимо выбирать на основе анализа следующих характеристик защищаемой территории...
Дисциплины:
![]() |
![]() |
5.00
из
|
Заказать работу |
|
|
Чугуном называется сплав железа с углеродом, содержащий углерода от 2 до 6,67%. Это один из основных материалов, применяемых в машиностроении.
Чугун получают из железных руд в доменных печах. Современные доменные печи строят высотой более 30 м с диаметром горна до 10 м, в них выплавляют до 4800 т чугуна в сутки. С момента задувки печь работает непрерывно в среднем 5—8 лет. В качестве исходных материалов используют железную и марганцевую руды, в качестве топлива — кокс; для понижения температуры плавления пустой породы руд и образования с пустой породой и золой топлива легкоплавких смесей, называемых шлаком, в доменную печь загружают флюсы. В качестве флюса обычно используется известняк.
Железные руды. Железными рудами называют горные породы, содержащие металл. Обычно в руде содержится металл в таком количестве, которое позволяет экономично и выгодно извлекать металл из руды.
Железные руды представляют собой главным образом соединения с кислородом (окись железа) и пустой породой (землистой примесью в виде песка, глины и известняка). Пригодность железной руды к плавке определяется содержанием в ней железа, составом пустой породы и количеством вредных примесей (сера, фосфор и др.).
В производстве чугуна используются только те руды, в которых железа содержится не менее 30%. Из железных руд, имеющих особенно большое промышленное значение, можно назвать следующие: магнитный, красный и бурый железняк.
Магнитный железняк (магнезит) представляет собой магнитную окись железа (Fe3О4). Это минерал черного цвета, обладающий магнитными свойствами. Содержание железа в нем достигает 70—72% при очень небольшом количестве вредных примесей— серы и фосфора.
|
Красный железняк (гематит) представляет собой окись железа (Fе2О3). Это минерал вишнево-красного цвета, содержащий в среднем до 60% железа. Это одна из лучших руд, в ней содержится небольшое количество вредных примесей (фосфора и серы); кроме того, эта руда весьма удобна для производства чугуна, так как железо восстанавливается легче.
Бурый железняк (лимонит) — минерал бурого цвета, содержащий от 30 до 60% железа в виде водной окиси, имеет значительное количество примесей — серы, фосфора.
Топливо. Топливо является не только источником тепла для расплавления руды, но также участвует в химических реакциях, протекающих в доменной печи при выплавке чугуна.
Применяемое в доменном процессе топливо тем ценнее, чем больше в нем углерода и меньше влаги, на испарение которой затрачивается тепло. Качество топлива также тем выше, чем меньше в нем серы и золы, так как наличие серы вызывает образование раковин в чугуне, неоднородность состава, густоплавкость и ломкость в нагретом состоянии, а зола обладает высокой температурой плавления и сама по себе не может расплавиться.
В качестве топлива при доменном процессе используется каменноугольный кокс, древесный уголь, реже торфяной кокс и антрацит.
Кокс — продукт сухой перегонки специальных, так называемых коксующихся углей, в особых коксовальных камерах, в которых уголь нагревают без доступа воздуха. Это легкое, пористое и достаточно прочное топливо.
Древесный уголь — искусственное твердое топливо, полученное нагреванием без доступа воздуха различных древесных пород (березы, осины, сосны и др.). Достоинством древесного угля является его небольшая зольность и незначительное количество серы, ухудшающей качество металла. Однако высокая стоимость и невысокая прочность ограничивают его применение. Древесный уголь применяется только при выплавке высококачественных чугунов.
Флюсы. Это различные минеральные вещества, добавляемые в доменную печь для понижения температуры плавления пустых пород, удаления золы и серы, а также остатков сгоревшего топлива.
|
Флюсы образуют с пустой породой и золой топлива легкоплавкие сплавы, которые отделяются от металла в виде шлака. Способствуя образованию шлаков, флюсы тем самым дают возможность отделить от металла пустую породу.
При наличии в руде песчано-глинистых примесей в качестве флюса применяют известняк, а при известковистом составе пустой породы флюсом служат вещества, содержащие кремнезем, кварц и песчаник.
В качестве флюсов в металлургии цветных металлов применяют те же материалы, что и в металлургии черных металлов, причем наиболее распространенными являются кварц, плавиковый шпат, алюмосиликаты и др.
Ход доменного процесса. Доменную печь загружают сверху через колошниковое отверстие слоями рудой, коксом, известняком, а снизу в нее вдувают через отверстия (фурмы) воздух.
Материалы в доменной печи постепенно опускаются вниз и, встречаясь с газовым потоком при различных температурах, претерпевают соответствующие изменения в составе и свойствах.
При движении материалов в направлении сверху от колошника вниз к горну происходит сушка материала, разложение плавильных материалов, восстановление железа и других элементов из окислов, науглероживание восстановленного железа и образование чугуна, образование шлака.
Продукты доменного процесса. Продуктами доменного процесса являются чугун, шлак, доменный газ и колошниковая пыль.
Чугун является основным и главным продуктом доменного процесса.
Доменный шлак в настоящее время используется в качестве строительных материалов в виде шлакового кирпича, шлакобетона. Из шлака древесноугольных печей может быть получена стеклянная вата, являющаяся хорошим теплоизоляционным материалом.
Доменный газ используется как ценное газообразное топливо для воздухонагревателей, коксовальных и нагревательных печей, в паровых котлах и других целей.
Колошниковая пыль, которая выносится из печи с отходящими газами, поступает в специальные пылеуловители, затем направляется для спекания в виде кусков и идет обратно в шахту доменных печей.
Классификация чугунов
В зависимости от химического состава и назначения доменные чугуны делятся на передельные, литейные и специальные.
|
Передельный чугун предназначается для переработки на сталь в плавильных агрегатах, называемых конверторами, а также мартеновских и электрических печах. В зависимости от способа переработки он называется мартеновским (М), бессемеровским (Б), томасовским (Т).
Литейный чугун предназначается главным образом для производства литых заготовок (литья). Он поступает в литейные цехи в виде небольших слитков (чушек) весом до 25 кг.
Специальные чугуны (ферросплавы) выплавляют с высоким процентом кремния или марганца, применяют в качестве специальных добавок при выплавлении стали.
В зависимости от характера соединения углерода с железом чугуны разделяют на белые и серые.
Белые чугуны характеризуются тем, что у них весь углерод находится в химически связанном состоянии — в виде цементита, очень твердого и хрупкого соединения, называемого карбидом железа (Fe3C). Излом такого чугуна имеет матово-белый цвет. Белые чугуны практически не обрабатываются, их используют для переделки в сталь и в ковкий чугун.
В серых чугунах весь углерод или часть его находится в свободном состоянии, в виде графита, который придает чугуну в изломе серый или темно-серый цвет. Серый чугун широко применяют в машиностроении, он дешев, хорошо обрабатывается режущим инструментом, имеет высокие литейные свойства, поэтому широко применяется для изготовления отливок самого разнообразного назначения.
Буквы СЧ в марке обозначают серый чугун, первое двухзначное число указывает предел прочности при растяжении, второе — предел прочности при изгибе. Например, СЧ 12-28, СЧ 15-32, СЧ 18-36.
К группе серых чугунов относятся модифицированные, высокопрочные и ковкие чугуны.
Модифицированный чугун обладает повышенными физико-механическими, химическими и технологическими свойствами по сравнению с обычным серым чугуном. Его получают путем добавления в жидкий серый чугун (на желоб вагранки, в ковш или литниковую чашу) модификаторов — силикокальция, ферросилиция, силикоалюминия, магния или его сплавов и др., которые изменяют структуру чугуна, а следовательно, и его свойства. Марки: СЧ 28-48, СЧ 32-52, СЧ 38-60 и др.
|
Модифицированный чугун используют для изготовления ответственных деталей, работающих на износ, например, зубчатых колес, тормозных барабанов, втулок, коленчатых валов, отливок сложной конфигурации с тонкими стенками и др.
Высокопрочный чугун является важным конструкционным материалом, в котором сочетаются многие ценные свойства стали и чугуна. Его получают из серого чугуна путем присадки в ковш перед разливкой в формы магния, в результате чего получается чугун с шаровидным графитом, обладающий хорошими литейными, механическими свойствами.
Марки высокопрочного чугуна с шаровидным графитом по ГОСТ 7293—54: ВЧ 45-0, ВЧ 45-5, ВЧ 40-10, ВЧ 50-1,5, ВЧ 60-2. Буквы ВЧ обозначают высокопрочный чугун, первые две цифры указывают предел прочности при растяжении, а последняя — величину относительного удлинения.
Высокопрочный чугун применяется для изготовления деталей, работающих с ударными и переменными нагрузками и на износ (коленчатые валы, зубчатые колеса, поршневые кольца и др.).
Ковкий чугун получают длительным отжигом белого чугуна в специальных печах.
Такой чугун применяют для изготовления литых деталей сложной формы — вентили, тройники, краны; деталей, работающих на износ — тяговые сцепления, втулки, зубчатые колеса, звенья цепей, пальцы собачки, тормозные колодки и др.
Марки ковких чугунов по ГОСТ 1215 — 59: КЧ 30-6, КЧ 33-8, КЧ 35-10, КЧ 37-12 и др. Буквы КЧ означают ковкий чугун, первые две цифры указывают предел прочности при растяжении, последние цифры — относительное удлинение при растяжении.
Антифрикционные чугуны получают путем присадки в серый чугун легирующих элементов или термической обработкой белого чугуна. Антифрикционный чугун характеризуется малым коэффициентом трения, поэтому находит широкое применение для изготовления различных трущихся деталей в машинах и механизмах (втулки, подшипники и др.).
Специальные чугуны или ферросплавы выплавляют с повышенным процентом содержания одного из элементов, например, кремния, марганца, хрома и др.
Углерод является важнейшим элементом, определяющим как структуру, так и все свойства чугуна. Углерод благоприятно влияет на жидкотекучесть чугуна, что имеет большое значение для производства тонкостенного и сложного по конфигурации литья.
Кремний увеличивает жидкотекучесть чугуна при заливке. Содержание кремния в чугунах колеблется в широких пределах от 0,3—0,5 до 3—5%. Изменяя содержание кремния, можно получать чугуны совершенно с различными свойствами и структурой.
Марганец в отличие от кремния препятствует графитизации, как говорят, способствует отбеливанию чугуна, т. е. увеличивает твердость чугуна, ухудшает литейные свойства.
|
Сера является наиболее вредной примесью, ухудшает литейные свойства, в частности снижает жидкотекучесть, способствует образованию газовых пузырей в отливках. Поэтому содержание серы в чугуне ограничивают: до 0,08% для мелкого литья и до 0,1—0,12% для более крупного литья, когда можно допустить несколько худшую жидкотекучесть.
Фосфор также понижает прочность и увеличивает хрупкость чугуна. При небольших количествах улучшает жидкотекучесть чугуна. Это качество крайне ценно при изготовлении художественного и тонкостенного литья.
Фосфор повышает твердость и износоустойчивость, но снижает пластичность и вызывает хладноломкость (хрупкость при пониженной температуре). Содержание фосфора в ответственных отливках допускается до 0,1%, в менее ответственных — до 1,2%.
Кроме вышеуказанных примесей, в чугун вводят и другие элементы. Такие чугуны называются легированными.
§ 3. Основные сведения о получении стали
Сталью называют железоуглеродистый сплав, содержащий углерода до 2%, кремния до 0,35%, марганца 0,8,% фосфора до 0,07% и серы до 0,06%.
В сравнении с чугуном сталь обладает более высокой прочностью, вязкостью, ковкостью, хорошей обрабатываемостью, свариваемостью, способностью изменять свои свойства в широких пределах в зависимости от химического состава и вида термической обработки.
Благодаря хорошему сочетанию механических и технологических свойств сталь получила исключительно широкое применение во всех отраслях народного хозяйства. Ранее было сказано, что основным сырьем для производства стали является передельный чугун. Около 90% всего получаемого в доменных печах чугуна перерабатывается в сталь. Сущность процесса переработки чугуна в сталь сводится к удалению из чугуна избытка углерода, серы, фосфора, кремния, марганца и других примесей. Примеси при высокой температуре соединяются с кислородом быстрее, чем железо. Углерод чугуна, соединяясь с кислородом, превращается в газ. Кремний и марганец превращаются в окислы, которые вследствие меньшего удельного веса всплывают на поверхность и образуют шлак. Состав, свойства и качество стали в значительной степени зависят от способа ее производства. В настоящее время в промышленности Советского Союза основными способами получения стали являются конверторный (бессемеровский и томасовский), мартеновский и плавка в электропечах. Конверторный (бессемеровский) способ. Способ заключается в том, что через расплавленный доменный чугун, заливаемый в конвертор, продувается воздух в течение 15—20 мин. Кислород, находящийся в воздухе, вступает в реакцию с углеродом, кремнием, марганцем, фосфором и другими примесями и окисляет их. В результате этого процесса получается сталь. Конвертор (рис. 16) представляет собой вращающийся сосуд 2 грушевидной формы, кожух которого сварен из толстой листовой стали и футерован внутри кремнекислым огнеупорным материалом (динасовым кирпичом) 10. Снаружи кожух опоясан литым стальным поясом 11. Рис. 16. Устройство бессемеровского конвертора Конвертор имеет два цилиндрических выступа (цапфы) 1 и 3, служащие для опоры, и зубчатую передачу 9 для поворота конвертора. Одна из цапф сделана полой и соединяется с воздухопроводом 4. От цапфы к днищу 8 воздух подводится по трубе 6 в воздушную коробку 7. В отъемном днище конвертора имеются фурмы 5, через которые под давлением 3,0—3,5 aтм воздух подается в конвертор. Перед началом процесса конвертор при помощи зубчатой передачи наклоняют в положение, показанное на рис. 17, а, и через горловину заливают жидкий чугун. После этого подают дутье, затем поворачивают конвертор в вертикальное положение (рис. 17, б). Продуваемый воздух проходит через весь чугун. Реакция горения кремния, марганца и железа происходит с большим выделением тепла, и температура сплава повышается с 1200—1300°С до 1700°. Для выпуска стали конвертор наклоняется в положение, показанное на рис. 17, в. Рис. 17. Схема работы конвертора: Емкость современных конверторов — 25—65 Т жидкого чугуна. Конверторный (томасовский) способ. Огнеупорные материалы, применяемые для футеровки, оказывают большое влияние на состав и свойства получаемой стали. При бессемеровском способе фосфор не может быть удален из чугуна, так как известь, необходимая для удаления фосфора, разрушает кремнекислый огнеупор. Поэтому при переработке на сталь доменных чугунов, содержащих значительное количество фосфора (до 2,2%), бессемеровский способ не пригоден, и в этом случае применяется томасовский способ. Особенностью конвертора (томасовского) является основная, доломитовая футеровка, а отличием самого процесса — загрузка в конвертор вместе с жидким чугуном определенного количества свежеобожженной извести. Присутствие извести приводит к образованию шлаков и удалению из чугуна фосфора и серы. Марки конверторной стали обозначают начальными буквами Б и Т, что значит бессемеровская и томасовская сталь (по именам изобретателей Бессемера и Томаса). Преимуществами конверторного способа получения стали - являются высокая производительность, компактность и простота устройства оборудования, а также выплавка с помощью воздушного дутья (без топлива), благодаря чему стоимость стали невысока. Сталь, полученная конверторным способом, легко обрабатывается резанием и давлением, хорошо сваривается, обладает повышенным сопротивлением износу. Для строительства конверторов требуется менее сложное оборудование и примерно на 30—40% меньше капитальных затрат, чем при строительстве мартеновских печей такой же производительности. К серьезным недостаткам конверторного способа получения стали относятся значительный угар металла, необходимость применения только жидкого чугуна, сложность регулировки процесса из-за кратковременности его протекания, ограниченное количество переплавляемого металла, сильное загрязнение стали шлаковыми включениями, потери части металла в шлаке и выплесках, возможность передела чугунов только определенного химического состава. Конверторная сталь не отличается высоким качеством вследствие окисления значительного количества железа при дутье и невозможности последующего полного восстановления железа из образовавшейся закиси железа. Присутствие же закиси железа делает сталь ломкой при прокатке и вызывает ряд других недостатков. К тому же конверторный способ не создает условий для получения стали определенного состава вследствие большой скорости процесса, а также значительного уменьшения в стали вредных элементов — фосфора и серы. Поэтому конверторная сталь используется главным образом для производства изделий, к механическим свойствам которых не предъявляются высокие требования, например, для изготовления неответственных строительных изделий, листового железа, балок, труб, болтов, проволоки, гвоздей, шурупов, а также стяжек тяг, ключей и т. п. Применение кислорода. В настоящее время при выплавке стали конверторным способом широко применяется обогащенное кислородом дутье или чистый кислород; в этом случае реакция окисления примесей происходит интенсивней, качество стали значительно улучшается, производительность работы повышается. Применение дутья с подачей большого количества кислорода позволяет перерабатывать малофосфористые чугуны, т. е. непригодные для томасовского процесса, получать сталь, не уступающую по качеству мартеновской. Мартеновский процесс. Выше уже указывалось, что одним из недостатков конверторного способа является повышенное содержание в стали кислорода, ухудшающее ее механические свойства. Поэтому для изготовления многих ответственных изделий (инструментов, пружин, деталей, работающих на удар, и т. д.) конверторная сталь непригодна. Кроме этого, существовавшие ранее способы конверторного производства стали не решали задач переработки отходов (стальной лом, стружка, скрап и т. п.). В 1864 г. П. Мартеном было предложено производство стали в пламенной (мартеновской) регенеративной печи. В мартеновских печах окисление осуществляется воздухом, проходящим через шлак, который изолирует расплавленный металл от непосредственного воздействия кислорода воздуха, что уменьшает угар металла и способствует улучшению качества стали. Для выплавки стали в мартеновских печах применяется белый чугун, железная руда, лом, флюсы (известняк, обожженная известь, бокситы, плавиковый шпат). В зависимости от состава шихты в мартеновских печах различают следующие разновидности процесса выплавки стали: скрап-процесс, чугунно-рудный и скрап-рудный процессы. Скрап-процесс применяется на машиностроительных заводах, не имеющих доменных печей и располагающих большим количеством всевозможных отходов производства в виде стального лома (скрапа), пакетированной стружки, пришедших в негодность деталей машин как чугунных, так и стальных. В качестве добавки применяется чушковый чугун и известняк. Скрап-рудный процесс применяется на заводах, оснащенных доменными печами, 60—70% шихты составляет жидкий чугун, остальная часть — стальной лом. Для окисления примесей чугуна применяют значительное количество руды. Наиболее широко распространены скрап-процесс и скрап-рудный процесс. Мартеновский способ производства стали является самым распространенным. Мартеновские печи. По конструкции мартеновские печи делятся на стационарные (неподвижные) и качающиеся. В качающихся печах рабочее пространство заключено в металлический кожух, рама которого опирается на катки, позволяющие наклонять печь на определенный угол при помощи электрического или гидравлического механизма. Мартеновская печь (рис. 18). Мартеновская печь представляет собой сложное сооружение, оснащенное совершенными механизмами для загрузки шихты и уборки продуктов плавки. Она оборудована автоматическими приборами для регулирования процесса горения и температуры в печи. Мартеновская печь состоит из рабочего (плавильного) пространства 3, ограниченного сверху сводом 2, а снизу — подом 17. Передняя стенка имеет завалочные окна 1, через которые загружают шихтовые материалы. В задней стенке имеются отверстия для выпуска стали и шлака. В торцах печи расположены головки 4 и 5, 15 и 16, соединяющие плавильное пространство 3 с регенераторами 6 и 7, 13 и 14. Рис. 18. Схема мартеновской печи: Горючий газ и необходимый для его сжигания воздух перед поступлением в плавильное пространство предварительно проходят через нагретую до температуры около 1200° насадку 8 регенераторов 6 и 7. Подогретый в регенераторах газ и воздух выходят затем по вертикальным каналам в правые головки 4 и 5, смешиваются между собой в плавильном пространстве 3 и вступают в реакции горения. В результате горения газа температура под сводом 2 повышается до 1650—1760°. Газообразные продукты горения из плавильного пространства через левые головки 15 и 16 направляются в регенераторы 13 и 14, нагревают их огнеупорную насадку 12 и далее поступают в трубу 10. Когда огнеупорная насадка 8 в регенераторах 6 и 7 начнет остывать, направление движения газа и воздуха посредством клапанов 9 и 11 переключается на насадку 12 регенераторов 13 и 14. Таким образом обеспечивается непрерывное поступление в плавильное пространство печи подогретых горючего газа и воздуха. Большинство мартеновских печей работает на природном газе или смеси доменного и коксовального газов. Технико-экономические показатели работы мартеновской печи резко повышаются при использовании кислорода как для интенсификации сжигания топлива, так и для ускорения окисления примесей. Кислород в этом случае подают через головки мартеновской печи. Производство стали в электропечах. Наиболее совершенным способом производства стали является выплавка ее в электроплавильных печах. Основные преимущества этих печей заключаются в следующем: 1. В плавильном пространстве температура достигает 2000° С, что способствует расплавлению металла с высокой концентрацией тугоплавких компонентов (хрома, вольфрама, молибдена и др.) и хорошему удалению серы и фосфора, а также неметаллических включений. Сталь, полученная таким способом, по химическому составу лучше мартеновской. 2. Можно выплавлять любые сорта стали с содержанием заданного количества таких элементов, как хром, никель, молибден, ванадий, вольфрам, титан и др. 3. Обеспечивается точность и простота регулирования температур. 4. Значительно уменьшается угар металла и особенно легирующих элементов. Выплавку стали производят в дуговых и индукционных (высокочастотных) электрических печах. Наибольшее распространение получили дуговые электрические печи. Идея использования образующегося при горении электрической дуги тепла для плавки металла была обоснована русским ученым, академиком В. В. Петровым еще в 1802 г. Дуговая электрическая печь, указанная на рис. 19, состоит из сварного стального цилиндрического корпуса 1, выложенного внутри огнеупорным кирпичом 2, съемного свода 3 с отверстиями, в которые пропущены соединенные проводниками с вторичной обмоткой трансформатора графитовые или угольные электроды 4. Графитовые электроды более устойчивы при высоких температурах и имеют меньшее электросопротивление, чем угольные, поэтому их применение в электроплавильных печах более целесообразно. Число электродов соответствует числу фаз электрического тока. Длина электродов достигает 2 м. Электроды укрепляются в электродержателях 5 и с помощью специального механизма могут перемещаться вверх и вниз и опускаться до верхнего уровня металла. Расстояние между электродами и металлом в печи должно быть определенным. При работе расстояние регулируется подъемом или опусканием электродов вручную или автоматически. Внизу электропечь ограничена подом. Рис. 19. Дуговая электрическая печь Нагрев и расплавление шихтовых материалов производится теплом, излучаемым тремя электрическими дугами, образуемыми между электродами и металлической шихтой при напряжении электрического тока 180—350 в. Механизм наклона позволяет поворачивать печь для выпуска стали и шлака в сторону отверстия и сливного желоба на 10—15°. Современные дуговые печи строятся емкостью от 0,5 до 180 Т. Наибольшее распространение имеют печи емкостью до 80 Т. Продолжительность плавки в печах 3—6 ч. Электрические печи потребляют много электроэнергии, поэтому они используются, как правило, для получения только высококачественной стали. В целях повышения производительности электрических печей и снижения стоимости стали предусмотрено производство электростали с помощью дуплекс-процесса, заключающегося в выплавке металла последовательно в двух плавильных агрегатах: основном конверторе и электропечи или в мартеновской печи и электропечи. Экономическая и технологическая целесообразность расплавления и предварительного удаления вредных примесей в первом агрегате и окончательная переработка металла во втором агрегате очевидны: повышается производительность, улучшается качество стали и уменьшается расход электроэнергии. Индукционная печь высокой частоты состоит из огнеупорного тигля, окруженного тепловой изоляцией и находящегося внутри змеевика в виде медной трубки, по которой циркулирует вода для охлаждения. При прохождении по змеевику переменного тока высокой частоты в металле, находящемся в тигле, образуются вихревые токи большой силы, быстро нагревающие металл до плавления. Вихревые токи способствуют хорошей циркуляции металла и очищению его от примеси. Недостатком этих печей является большая стоимость их, а также высокие требования, предъявляемые к стойкости и прочности тиглей, изготовление которых сложно. Высокочастотные печи применяют только для изготовления наиболее ценных и ответственных сортов сталей. |
Общая классификация стали
Сталь — это сплав железа с углеродом, содержащий углерода до 2%.
По химическому составу стали делят на углеродистые и легированные.
Углеродистые стали, кроме углерода, содержат до; 0,35% кремния, 0,8% марганца, 0,06% серы, 0,07% фосфора.
Легированными называют такие стали, в состав которых специально введены легирующие элементы (хром, никель, вольфрам, ванадий, молибден, кобальт и др.) для сообщения стали требуемых свойств.
К легированным сталям относятся также стали, содержащие повышенное количество марганца и кремния (марганцовистые и кремнистые стали).
По назначению стали разделяют на конструкционные, инструментальные и стали с особыми физическими свойствами.
Конструкционные стали в свою очередь делят на строительные и машиностроительные.
По способу выплавки различают сталь обыкновенного качества, сталь качественную и сталь высококачественную.
Сталь обыкновенного качества выплавляют в бессемеровских конверторах или больших мартеновских печах, такая сталь содержит 0,06—0,62% углерода.
Качественную сталь изготовляют в мартеновских и электрических печах, в основных конверторах с продувкой кислородом сверху, она содержит меньше вредных примесей, чем сталь обыкновенного качества.
Высококачественную сталь выплавляют в кислых и основных мартеновских печах и в электрических печах, она содержит очень ограниченное количество серы и фосфора, имеет более суженные пределы содержания марганца и кремния по сравнению с качественной сталью, обладает высокой чистотой в отношении неметаллических включений и строго регламентированными механическими свойствами. В конце марки высококачественной стали ставится буква А, например, У8А, У9А, 15ХА, 30ХГСА.
§ 5. Углеродистые стали
В углеродистых сталях углерод является важнейшим элементом, определяющим как структуру, так и свойства стали. С повышением содержания углерода возрастают прочность и твердость стали, но понижается пластичность. Углерод благоприятно влияет на жидкотекучесть стали.
Марганец повышает твердость и прочность стали, увеличивает ее вязкость после термической обработки. Кремний повышает твердость, прочность и упругость стали и незначительно снижает ее пластичность. Фосфор снижает пластичность и вызывает хладноломкость (хрупкость) стали, а сера снижает литейные свойства, препятствует выходу газов из жидкой стали, что ведет к образованию газовых пузырей (раковин) в отливке, вызывает ломкость и повышает твердость стали.
Углеродистая сталь обыкновенного качеств а предназначается для производства проката. По ГОСТ 380—60 эта сталь подразделяется на три группы А, Б и В
Сталь группы А поставляется с гарантированными механическими свойствами (предел прочности, предел текучести и относительное удлинение) и маркируется буквами Ст., за которыми следует цифра: 0; 1; 2 и т. д. до 7. Чем больше цифра в марке, тем больше содержание углерода, тем выше предел прочности и тем ниже относительное удлинение.
Сталь группы А поступает с металлургических заводов в виде проката (балки, прутки, ленты, проволока и т. д.) и используется для неответственных деталей машин, металлических конструкций, арматуры, топочных устройств и других изделий, не подвергающихся термической обработке.
Сталь группы Б поставляется с гарантией по химическому составу. В марке буквами указывается способ выплавки: буквой М — мартеновская сталь, буквой Б — бессемеровская, буквой К — конверторная, полученная продувкой металла кислородом сверху; цифра в марке представляет число, характеризующее химический состав стали, а буква кп — сталь кипящая, пс — сталь полуспокойная, сп — сталь спокойная.
Сталь группы Б изготовляется следующих марок: мартеновская — МСт. О, МСт. 1, МСт. 2, МСт. 3, МСт. 4, МСт. 5, МСт. 6, МСт. 7; конверторная — КСт. О, КСт. 1, КСт. 2, КСт. 3, КСт. 4, КСт. 5, КСт. 6, КСт. 7; бессемеровская — БСт. О, БСт. 3, БСт. 4, БСт. 5 и БСт. 6.
Из стали группы Б изготовляют сварные конструкции, различные резервуары, бандажи и оси вагонных колес, железнодорожные рельсы, пружины, рессоры общего назначения; при изготовлении этих изделий применяется ковка, поверхностная закалка и другие виды обработки.
Сталь группы В поставляется с гарантированным пределом прочности, пределом текучести, относительным удлинением и химическим составом; марки сталей этой группы начинаются с буквы В, затем следуют элементы обозначения те же, что и группы сталей А и Б.
Сталь группы В изготовляется следующих марок: мартеновская — ВМСт. 2, ВМСт. 3, ВМСт. 4 и ВМСт. 5; конверторная — В КСт. 2, В КСт. 3, В КСт. 4 и В КСт. 5.
Из сталей группы В изготовляют сварные конструкции, неответственные детали машин, валы, оси и т. д.
Сталь марок Ст. 1, Ст. 2, Ст. 3 и Ст. 4 всех трех групп изготовляется кипящая, полуспокойная и спокойная. Сталь марок Ст. 5, Ст. 6 и Ст. 7 изготовляется только полуспокойная и спокойная. Поэтому марки стали после цифры могут иметь индекс «кп» или «пс», либо «сп», указывающие соответственно, что сталь кипящая или полуспокойная, либо спокойная.
Углеродистая качественная сталь применяется для изготовления ответственных деталей, различных машин и механизмов (шатуны, шпиндели, зубчатые колеса, валы, оси и т. п.). Качественная конструкционная углеродистая сталь поставляется по ГОСТ 1050—60 с гарантированными механическими свойствами и химическим составом в виде обжатых болванок, слитков, листов, прутков, полос, лент и др.
Качественная углеродистая сталь делится на две группы: I — с нормальным содержанием и II — с повышенным содержанием марганца (0,7—1,2%). Сталь группы I маркируется цифрами 05кп, 10кп, 15кп, 20 и далее до 85. Цифры в марке показывают среднее содержание углерода в сотых долях процента. В стали группы II после чисел, выражающих содержание углерода, ставят букву Г (например, 15Г, 20Г, 25Г и далее до 70Г).
Углеродистые инструментальные стали делятся на качественные и высококачественные. Содержание углерода в сталях, от величины которого во многом зависят свойства стали, составляет 0,65—1,35%.
Из этих сталей изготовляют режущий, измерительный и штамповочный инструмент.
Инструмент из углеродистой инструментальной стали после соответствующей термической обработки выдерживает температуру нагрева лишь до 200—250°С; при большей температуре нагрева твердость инструмента резко снижается.
Углеродистые качественные инструментальные стали по ГОСТ 1435—54 изготовляют следующих марок У7, У8, У9 и т. д. до У13. Буква У указывает, что сталь углеродистая, а цифра — содержание углерода в десятых долях процента. В марке высококачественной углеродистой инструментальной стали ставят букву А, например У7А, У8А и т. д.
Легированные стали
Для изготовления различных машин, инструментов, аппаратов, приборов, металлических конструкций и другого оборудования широко применяются легированные стали, обладающие высокими механическими, физическими и химическими свойствами.
Элементы, специально вводимые в сталь для получения требуемых свойств, называются легирующими.
|
|
Типы сооружений для обработки осадков: Септиками называются сооружения, в которых одновременно происходят осветление сточной жидкости...
Кормораздатчик мобильный электрифицированный: схема и процесс работы устройства...
Адаптации растений и животных к жизни в горах: Большое значение для жизни организмов в горах имеют степень расчленения, крутизна и экспозиционные различия склонов...
Особенности сооружения опор в сложных условиях: Сооружение ВЛ в районах с суровыми климатическими и тяжелыми геологическими условиями...
© cyberpedia.su 2017-2024 - Не является автором материалов. Исключительное право сохранено за автором текста.
Если вы не хотите, чтобы данный материал был у нас на сайте, перейдите по ссылке: Нарушение авторских прав. Мы поможем в написании вашей работы!