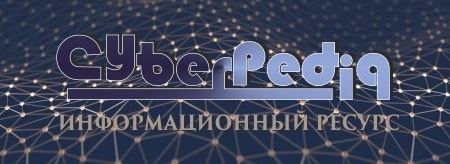
Биохимия спиртового брожения: Основу технологии получения пива составляет спиртовое брожение, - при котором сахар превращается...
Организация стока поверхностных вод: Наибольшее количество влаги на земном шаре испаряется с поверхности морей и океанов (88‰)...
Топ:
Генеалогическое древо Султанов Османской империи: Османские правители, вначале, будучи еще бейлербеями Анатолии, женились на дочерях византийских императоров...
Характеристика АТП и сварочно-жестяницкого участка: Транспорт в настоящее время является одной из важнейших отраслей народного...
Процедура выполнения команд. Рабочий цикл процессора: Функционирование процессора в основном состоит из повторяющихся рабочих циклов, каждый из которых соответствует...
Интересное:
Финансовый рынок и его значение в управлении денежными потоками на современном этапе: любому предприятию для расширения производства и увеличения прибыли нужны...
Распространение рака на другие отдаленные от желудка органы: Характерных симптомов рака желудка не существует. Выраженные симптомы появляются, когда опухоль...
Принципы управления денежными потоками: одним из методов контроля за состоянием денежной наличности является...
Дисциплины:
![]() |
![]() |
5.00
из
|
Заказать работу |
|
|
Введение
Сварка - прогрессивный технологический процесс получения неразъемных соединений деталей, позволяющий создавать конструкции с высокими эксплуатационными характеристиками. Достоинства сварных соединений способствуют широкому применению их в конструкциях разного назначения.
Использование сварки позволяет экономить материалы и время при производстве конструкций. При этом открываются большие возможности механизации и автоматизации производства, создаются предпосылки для повышения производительности, улучшаются условия труда работающих.
С развитием научно-технического прогресса расширяется возможность сварки деталей разных толщин, материалов, а в связи с этим и набор применяемых видов и способов сварки. В настоящее время сваривают детали толщиной от нескольких микрометров (в микроэлектронике) до десятков сантиметров и даже метров (в тяжелом машиностроении). Наряду с конструкционными углеродистыми и низколегированными сталями все чаще приходится сваривать специальные стали, легкие сплавы и сплавы на основе титана, молибдена, циркония и других металлов, а также разнородных материалов. От прогрессивности применяемых сварочных процессов и качества выполнения этих работ во многом зависят качество надежность готовых конструкций и эффективность производства в целом. Одно из наиболее развивающихся направлений в сварочном производстве - широкое использование механизированной и автоматической дуговой сварки. Эти вопросы решаются механизацией и автоматизацией как самих сварочных процессов (т. е. переходом от ручного труда сварщика к механизированному), так и комплексной механизацией и автоматизацией, охватывающими все виды работ, связанные с изготовлением сварных конструкций (заготовительные, сборочные и др.) и созданием поточных и автоматических производственных линий. Важное значение при этом отводится созданию специального сварочного оборудования и средств оснащения технологических процессов.
|
проведение технологической подготовки производства, в значительной степени определяющей его трудоемкость и сроки освоения, экономические показатели, использование средств механизации и автоматизации. Наибольший эффект технологической подготовки достигается при комплексном решении вопросов — технологической отработки самих конструкций, разработки технологических процессов и их оснащения на всех этапах производства.
Рост технического уровня производства, введение в эксплуатацию сложного сварочного оборудования неразрывно связаны с повышением требований к уровню общеобразовательной и технической подготовки кадров, работающих в области сварочного производства, в первую очередь рабочих-сварщиков.
Цель настоящей письменной экзаменационной работы — разработать технологию дуговой и газовой сварки стыкового соединения пластин из низкоуглеродистой стали с v-образной разделкой кромок в нижнем положении шва.
Сварное изделие | Конструктив ные элементы, мм | Положе- ние швов в прост- ранстве | Тол- щина свар. метал- ла, б, мм | Марка стали | |
стыковое соединение пластин с v-образной разделкой кромок | а=1800 | сварка в цехе | 8 | Ст 3 |
Исходные данные.
Характеристика основного металла.
Для изготовления соединения используется сталь конструкционная углеродистая обыкновенного качества Ст3сп.
Таблица 1.
Марка: | Ст3сп |
Классификация: | Сталь конструкционная углеродистая обыкновенного качества |
Дополнение: | По ГОСТ 27772-88 сталь Ст3сп5 соответствует стали для строительных конструкций С245; сталь Ст3сп соответствует стали С285 |
Применение: | Несущие элементы сварных и несварных конструкций и деталей, работающих при положительных температурах, арматура класса Ат400С |
Зарубежные аналоги: | Известны |
|
Химический состав в % материала Ст3спГОСТ 380 – 2005
Таблица 2.
C | Si | Mn | Ni | S | P | Cr | N | Cu | As |
0.14 - 0.22 | 0.15 - 0.3 | 0.4 - 0.65 | до 0.3 | до 0.05 | до 0.04 | до 0.3 | до 0.008 | до 0.3 | до 0.08 |
KCU
- Ударная вязкость, [ кДж / м2]
HB
- Твердость по Бринеллю, [МПа]
Физические свойства:
T
- Температура, при которой получены данные свойства, [Град]
E
- Модуль упругости первого рода, [МПа]
a
- Коэффициент температурного (линейного) расширения (диапазон 20o - T), [1/Град]
l
- Коэффициент теплопроводности (теплоемкость материала), [Вт/(м·град)]
r
- Плотность материала, [кг/м3]
C
- Удельная теплоемкость материала (диапазон 20o - T), [Дж/(кг·град)]
R
- Удельное электросопротивление, [Ом·м]
Свариваемость:
Без ограничений
- сварка производится без подогрева и без последующей термообработки
Ограниченно свариваемая
- сварка возможна при подогреве до 100-120 град. и последующей термообработке
Выбор способа сварки.
Ручная сварка штучными электродами отличается тем, что требует относительно небольших вложений и может применяться в любой области. Эта технология может быть использована для сваривания большого количества материалов и гарантирует высокое качество сварных швов. Однако, в последнее время, в первую очередь по экономическим причинам, ее стали вытеснять другие технологии, которые предоставляют возможности механизации. В данной работе я рассмотрю особенности этой технологии. Она характеризуется тем, что электрическая дуга горит между плавящимся электродом и сварочной ванной. Внешняя защита не используется, любая защита от воздействия атмосферы исходит от самого электрода. Таким образом, электрод является еще и сварочной присадкой. В покрытие входят шлак и (или) защитный газ, которые помимо всего прочего защищают каплю и сварочную ванну от содержащихся в атмосфере кислорода, азота и водорода.
Выбор сварочных материалов.
Электроды, применяемые, для сварки и наплавки классифицируются по значению (для сварки стали, чугуна, цветных металлов и для наплавочных работ). Технологическим особенностям (для сварки в различных пространственных положениях, сварки с глубоким проплавлением) виду и толщине покрытия химическому составу стержня и покрытия, характеру шлака, механическим свойствам металла шва и способу нанесения покрытия (опресовка, окунание).
|
Основными требованиями для всех видов электродов являются: обеспечения стабильного горения дуги и хорошего формирования шва; получения металла шва заданного химического состава, спокойное и равномерное расплавления электродного металла и высокая производительность сварки, легкая отделимость шлака и достаточная прочность покрытий, сохранение физико-химических и технологических свойств электродов.
Электроды изготавливаются по ГОСТ 9966-75 и подразделяются:
– для сварки углеродистых и низколегированных сталей – У
– для сварки легированных сталей – Л
– для сварки легированных теплоустойчивых сталей – Т
– для сварки высоколегированных сталей с особыми свойствами – В
– для наплавки поверхностных слоев – Н
По толщине покрытия электроды подразделяются на электроды с тонким, средним, толстым и особо толстым покрытием предусматривает также три группы электродов – 1, 2, 3, 4.
По виду покрытия электроды подразделяются:
– с кислым покрытием – А
– с основным – Б
– с целлюлозным – Ц
– с рутиловым – Р
– смешанное – двумя
– с прочими покрытиями – П.
В зависимости от пространственного положения сварки электроды подразделяются:
1 – для сварки во всех пространственных положениях;
2 – для сварки во всех положениях кроме вертикального сверху в низ;
3 – для нижнего положения, горизонтального на вертикальной плоскости и вертикального снизу вверх;
4 – для нижнего и в лодочку.
Электроды подразделяются по роду и полярности тока, а также по напряжению холостого хода.
М –тонкое покрытие; С –среднее; Д – толстое; Г – особо толстое.
Э46А – УОНИИ13/45-3,0-УД2 Е43 2 (5) – Б1 О | ГОСТ9466 (ГОСТ9467) |
Э – электрод для дуговой сварки.
46 – [ σВ ]временное сопротивление разрыву (минимальное значение), кг/мм2.
А – улучшенный тип электродов.
|
У – для сварки углеродистых сталей.
Д – толщина покрытия.
2 – вторая группа по содержанию S и P.
В знаменателе: цифры 43 2 (5) указывают характеристики наплавленного металла.
Б – основной тип покрытия.
1 – пространственное положение (для всех).
О – постоянный ток обратной полярности.
Е – для сварки углеродистых и низколегирующих сталей.
432 – σВ=43 кг/мм2, δ% - относительное удлинение δ=22%, ударная вязкость при 50°С не менее 3,5.
Подготовка металла под сварку.
При подготовке деталей под сварку поступающий металл подвергается правке, разметке, наметке, резке, подготовке кромок под сварку, холодной или горячей гибке.
Основной метали и присадочный материал перед сваркой должен быть тщательно очищены от ржавчины, масла, влаги, окалины и различного рода неметаллических включений. На месте указанных загрязнений приводит к образованию в сварных швах пар, трещин, шлаковых включений, что приводит к снижению прочности и плотности сварного соединения.
Подготовка кромок под сварку
Рисунок 3. Подготовка кромок под сварку.
К элементам геометрической формы подготовке кромок под сварку относятся угол разделки кромок α, притупление кромок – С, зазор между стыкуемыми кромками – b, угол разделки кромок выполняется при толщине металла > 4мм.
Разделка кромок позволяет вести сварку отдельными слоями небольшого сечения, что улучшает структуру сварного соединения. Зазор, правильно установленный перед сваркой, позволяет обеспечить полный провар по сечению соединения.
Притупление выполняется для обеспечения устойчивого ведения сечения процесса сварки при выполнении корневого шва.
Смещение кромок (δ) создает дополнительные деформации и напряжения.
Длина прихватки должна составлять (2÷10)×S, но не более 100мм, а расстояние между ними (10÷40)×S, но не более 500мм. Для разнотолщинных металлов длина (1÷5)×S, но не более 50мм, рост не более 250мм.
Рисунок 4. Схема движения конца электрода.
Третье движение – колебание конца электрода поперек шва для образования уширенного валика, который применяется чаще, чем ниточный. Для образования уширенного валика электроду сообщают поперечные колебательные движения чаще всего с постоянной частотой и амплитудой, совмещенные с поступательным движением электрода вдоль оси шва.
При сварке горкой на участке длиной 200÷300мм накладывают первый слой. Затем после очистки первого слоя от шлака окалины и брызг на него накладывают второй слой по длине в два раза больший чем первый. Отступив от начала второго слоя, на 200÷300мм выполняют третий слой.
Сварка каскадом для выполнения длинных многослойных швов.
Рисунок 5. Схема сварного шва: а) однопроходный; б) многослойный; в) многопроходный.
|
Выбор режима сварки
Под режимом сварки понимают совокупность условий создающих устойчивое протекание процесса сварки.
К основным параметрам режима сварки относят величину, род и полярность тока, диаметр электрода, напряжение, скорость сварки и величину поперечного колебания конца электрода.
Глубина провара и ширина шва зависят от всех основных параметров режима сварки. Увеличение IСВ вызывает при неизменной скорости рост глубины провара, что объясняется величиной поточной энергии (теплоты приходящейся на единицу длины шва) и от давления столба дуги.
Род и полярность тока также влияют на форму и размеры шва. При сварке постоянным током обратной полярности глубина провара на 40÷50% больше, чем при сварке постоянным током прямой полярности, что объясняется большим количеством теплоты, выделяющийся на аноде и катоде.
При сварке переменным током глубина провара на 15÷20% меньше, чем при сварке постоянным током обратной полярности.
Напряжение при ручной дуговой сварке на глубину провара оказывает незначительное влияние, которым можно пренебречь.
Выбор диаметра электрода
Диаметр электрода выбирают в зависимости от толщины свариваемого металла, положение в котором выполняется сварка, а также в зависимости от характера соединения и формы подготовки кромок. Экспериментально установлена зависимость:
S свариваемого металла, мм | 1,5 | 2 | 3 | 4÷5 | 6÷8 | 9÷12 | 13÷15 | 16÷20 |
Ø электрода, мм | 1,6 | 2 | 3 | 3÷4 | 4 | 4÷5 | 5 | 5 и 7 |
При выполнении швов в вертикальном и потолочном положениях применяют электроды Ø 3÷4мм.
Выбор силы сварочного тока
Для сварки в нижнем положении силу сварочного тока подбирают по формуле
I=K×d
Где:
I – сила сварочного тока, А;
K – Коэффициент, А/мм2;
d – Диаметр электрода, мм.
При сварке в вертикальном положении в формулу вводятся коэффициент 0,9
I=0,9K×d
При сварке в потолочном положении вводят коэффициент 0,8
I=0,8K×d
Коэффициент K выбирают в зависимости от диаметра электрода:
Ø электрода, мм | 1÷2 | 3÷4 | 5÷6 |
K, А/мм | 25÷30 | 35÷40 | 45÷60 |
Контроль качества сварки
1. Контроль качества сварных соединений производится в соответствии с требованиями ОСТ 26-291-79, технических условий на изделие, чертежей и РД.
2. Пооперационный контроль качества включает: проверку соответствия основного металла и сварочных материалов требованиям стандартов и технических условий;
– контроль качества подготовки кромок и правильности сборки; контроль режимов сварки и последовательности наложения швов;
– контроль качества сварных соединений.
3. При контроле качества подготовки и сборки деталей под сварку проверяются:
– чистота поверхности свариваемых кромок и основного металла, прилегающего к свариваемым кромкам;
– правильность сборки деталей;
– качество и расположений прихваток, зазоры в соединениях, смещение кромок и др.
4. В процессе сварки контролируются:
– режимы сварки;
– последовательность наложения швов;
– тщательность послойной зачистки швов от шлаковой пленки;
– отсутствие трещин, подрезов и других дефектов;
– правильность клеймения сварных швов.
5. Контроль качества сварных соединений производится в соответствии с ОСТ 26-291-79 следующими методами:
– внешним осмотром и измерениями (ГОСТ 3242-79);
– механическими испытаниями (ГОСТ 6996-66);
– металлографическими исследованиями (ОСТ 26-1379-76);
– просвечиванием сварных соединений рентгеновскими, гамма-лучами (Г0СТ 7512-82);
– ультразвуковой дефектоскопией (ГОСТ 14762-76);
– гидравлическими и пневматическими испытаниями (ГОСТ 22161-76);
– другими методами испытаний, если они предусмотрены техническими условиями на изготовление данного изделия.
Объем и методы контроля устанавливаются требованиями чертежей и технических условий на изделие. Качество и свойства сварных соединений должны отвечать требованиям ОСТ 26-291-79, технических условий на изделие и чертежей.
6. Испытания сварных соединений на ударную вязкость производятся на образцах для аппаратов с толщиной стенки 12 мм и более, работающих под давлением свыше 50 кгс/см2 при температуре 20°С или выше 450°С, а также - ниже минус 200С.
7. Механические испытания проводятся на образцах, вырезанных из контрольных пластин, сваренных с применением тех же материалов, режимов сварки, что и изготавливаемое изделие.
Техника безопасности.
1. Требования безопасности и производственной санитарии при выполнении сварочных работ должны обеспечиваться соблюдением условий ГОСТ 12.1.004-76, ГОСТ 12.1.005-76,
ГОСТ 12.3.003-75, "Санитарных правил при сварке, наплавке и резке металла" № 1009-73, утвержденных Минздравом СССР 5 марта 1973 года, "Санитарных правил организации технологических процессов и гигиенических требований к производственному оборудованию"
№ 1042-73, утверждённых Минздравом СССР 4 апрели 1973 г.
2. К работе по электросварке допускаются лица, прошедшие предварительный медицинский осмотр, соответствующее обучение, инструктаж и проверку знаний требований безопасности с оформлением в специальном журнале и имеющие квалификационное удостоверение. В дальнейшем электросварщики должны проходить периодический медицинский осмотр в соответствии с приказом Минздрава СССР от 30.05.69 г. № 400.
3. Инструктаж электросварщиков по безопасности труда должен проводиться не реже одного раза в три месяца.
4. Сварочный пост должен быть оборудован местной эффективной вентиляцией, а в случае двух постов необходима также общая приточно-вытяжная вентиляция.
5. Сварка в закрытых объемах допускается только при наличии местного отсоса с удалением воздуха от одного сварочного поста не менее 150 м3/ч, причем необходимо производить отсос, как из верхних, так и нижних зон. Целесообразно применение защитных пневмомасок с принудительной подачей очищенного сжатого воздуха в маску сварщика типа ПТС, разработанных институтом биофизики Минздрава СССР или противогазов по ГОСТ 10183-77. Классификация средств индивидуальной защиты органов дыхания приводится в
ГОСТ 12.4.034-78.
6. Питание подогревателя углекислого газа должно осуществляться от сети с напряжением не выше 36В, мощностью не более 70Вт.
7. Баллоны необходимо предохранять от толчков и ударов, при их транспортировке следует пользоваться носилками или специальными тележками, запрещается переносить баллоны на руках.
8. При эксплуатации баллоны должны устанавливаться в вертикальном положении на расстоянии не менее 1м от отопительных приборов и укрепляться хомутом или цепью в специальной стойке.
9. Сварочные посты должны быть оборудованы электрическим освещением. При необходимости применения местного освещения переносной светильник напряжением не свыше 12B должен быть защищен колпаком и сеткой, иметь исправный шланговый провод.
10. Места выполнения сварочных работ должны быть ограждены несгораемыми ширмами, щитами и т.п. Сварочные кабины рекомендуется внутри окрашивать светло-серой, зеленой окраской, снижающей интенсивность отраженных лучей. Обшивка кабин выполняется из несгораемых материалов, между обшивкой и полом следует оставлять зазор 300 мм.
11. Сварщики должны обеспечиваться спецодеждой в соответствии с ГОСТ 12.4.103-80.
12. Для защиты глаз и лица используются щитки по ГОСТ 12.4.035-78 со светофильтром по ГОСТ 12.4.080-79, покровным стеклом по ГОСТ111-78 и подложкой из оргстекла.
Литература.
1.Овчинников В.В.Технология газовой сварки и резки металлов (Учебник), М., ACADEMIA, 2013.
2.Овчинников В.В.Технология газ электросварочных и газосварочных работ (Учебник), М., ACADEMIA, 2013.
3. Овчинников В.В.Технология ручной дуговой и плазменной сварки и резки металлов (Учебник), М., ACADEMIA, 2013.
4. Овчинников В.В.Электросварщик на автоматических и полуавтоматическихмашинах (Учебник), М., ACADEMIA, 2013.
Информационные ресурсы:
1. Профессиональные информационные системы CAD и CAM.
2. Классификаторы социально-экономической информации: [Электронный ресурс]. Форма доступа – http://www.consultant.ru.
3. Электронный ресурс «Сварка».
Форма доступа:
- www.svarka-reska.ru
- www.svarka.net
- www.prosvarkу.ru
- websvarka.ru
Введение
Сварка - прогрессивный технологический процесс получения неразъемных соединений деталей, позволяющий создавать конструкции с высокими эксплуатационными характеристиками. Достоинства сварных соединений способствуют широкому применению их в конструкциях разного назначения.
Использование сварки позволяет экономить материалы и время при производстве конструкций. При этом открываются большие возможности механизации и автоматизации производства, создаются предпосылки для повышения производительности, улучшаются условия труда работающих.
С развитием научно-технического прогресса расширяется возможность сварки деталей разных толщин, материалов, а в связи с этим и набор применяемых видов и способов сварки. В настоящее время сваривают детали толщиной от нескольких микрометров (в микроэлектронике) до десятков сантиметров и даже метров (в тяжелом машиностроении). Наряду с конструкционными углеродистыми и низколегированными сталями все чаще приходится сваривать специальные стали, легкие сплавы и сплавы на основе титана, молибдена, циркония и других металлов, а также разнородных материалов. От прогрессивности применяемых сварочных процессов и качества выполнения этих работ во многом зависят качество надежность готовых конструкций и эффективность производства в целом. Одно из наиболее развивающихся направлений в сварочном производстве - широкое использование механизированной и автоматической дуговой сварки. Эти вопросы решаются механизацией и автоматизацией как самих сварочных процессов (т. е. переходом от ручного труда сварщика к механизированному), так и комплексной механизацией и автоматизацией, охватывающими все виды работ, связанные с изготовлением сварных конструкций (заготовительные, сборочные и др.) и созданием поточных и автоматических производственных линий. Важное значение при этом отводится созданию специального сварочного оборудования и средств оснащения технологических процессов.
проведение технологической подготовки производства, в значительной степени определяющей его трудоемкость и сроки освоения, экономические показатели, использование средств механизации и автоматизации. Наибольший эффект технологической подготовки достигается при комплексном решении вопросов — технологической отработки самих конструкций, разработки технологических процессов и их оснащения на всех этапах производства.
Рост технического уровня производства, введение в эксплуатацию сложного сварочного оборудования неразрывно связаны с повышением требований к уровню общеобразовательной и технической подготовки кадров, работающих в области сварочного производства, в первую очередь рабочих-сварщиков.
Цель настоящей письменной экзаменационной работы — разработать технологию дуговой и газовой сварки стыкового соединения пластин из низкоуглеродистой стали с v-образной разделкой кромок в нижнем положении шва.
Сварное изделие | Конструктив ные элементы, мм | Положе- ние швов в прост- ранстве | Тол- щина свар. метал- ла, б, мм | Марка стали | |
стыковое соединение пластин с v-образной разделкой кромок | а=1800 | сварка в цехе | 8 | Ст 3 |
Исходные данные.
Описание сварной конструкции.
Необходимость разделки кромок сварных соединений.
Основными типами сварных соединений, выполняемых электродуговой сваркой плавлением, являются стыковые, угловые, тавровые и нахлёсточные.
При сварке плавлением металла толщиной более 5 мм наибольшей проблемой является получение гарантированного сплошного проплавления. При сварке на ММА (ручной сварке штучным электродом) и MIG/MAG (полуавтоматической сварке в защитных газах) толщина металла 5 мм является пределом. Поэтому нормативной документацией устанавливается необходимость выполнения специальной разделки кромок свариваемых листов. Такая разделка выполняется как для стыковых, так и для угловых и тавровых соединений. Применение разделки кромок свариваемых деталей часто позволяет заменить двустороннюю сварку на одностороннюю, позволяя избежать излишнего тепловложения в металл, и устранить кантовку свариваемых изделий. Это особенно важно при сварке крупногабаритных конструкций и изделий сложной формы с пересекающимися сварными швами в нескольких плоскостях, таких как фермы, балки мостов, судовые конструкции. ГОСТ5264-80 «Ручная дуговая сварка. Соединения сварные» устанавливает различные формы разделки кромок и формы поперечного сечения сварного шва листовых деталей для различных толщин свариваемых деталей, видов соединений (стыковые, угловые, тавровые) и методов дуговой сварки:
По форме разделки кромок под сварку различают сварные соединения без разделки кромок, с отбортовкой и с разделкой кромок под сварку. Кроме того, сварные соединения с разделкой кромок подразделяются на сварные соединения с односторонним скосом одной или двух кромок (односторонняя разделка одной или двух кромок) и сварные соединения с двусторонним скосом одной или двух кромок (двусторонняя разделка одной или двух кромок).
При выборе формы разделки кромки следует учитывать, что наиболее экономичным является сварное соединение без скоса кромок. В случае выполнения разделки кромок более простой в исполнении по сравнению с U– образной является разделка кромок с прямолинейным скосом кромок (V, К, Х – образные). В сравнении с односторонней разделкой кромок более технологичными являются К- и Х-образные двусторонние. Однако К- и Х-образные двусторонние могут быть реализованы при возможности доступа сварочного инструмента к обеим сторонам изделия.
Швы различаются и по своей протяженности. Короткие не превышают по длине 250 мм, и делаются они на проход. От середины сопряжения двух металлических поверхностей и к краям свариваемой конструкции производятся средние швы, имеющие длину от 250 до 1000 мм. Длинные угловые швы превышают длину в 1000 мм.
По количеству слоев сварки угловые швы разделяются на однослойные и
многослойные.
Однослойный однопроходный шов выполняется за один проход. При сварке металла большой толщины шов выполняют слоями, каждый из которых накладывают за один проход (многослойный) или за несколько проходов (многослойный многопроходный).
Сварка за один проход предпочтительнее при ширине шва не более 14-16 мм, т.к. дает меньше остаточных деформаций. При толщине металла более 15 мм сварка каждого слоя "напроход" нежелательна. Первый слой успевает остыть, и в нем возникают трещины.
Согласно ГОСТ 5264-80 соединение с V-образной разделкой условно обозначается С17. При толщине металла 10мм: ширина шва-19мм, зазор-2мм, притупление 1мм, усиление шва 0,5 мм. Сварку выполню однослойным однопроходным швом. Шов-длинный – сваривается обратноступенчатым способом.
2. Методы резки скоса кромок сварных соединений.
В технологии подготовке скоса кромок под сварку применяются как термические, так и механические методы резки.
Термические методы - газокислородная (газопламенная), плазменная и лазерная резка.
Механические методы:
- фрезерная обработка скоса кромки,
- строгание скоса кромки,
- резка скоса кромки абразивными кругами,
- резка скоса кромки кромкорезами долбежного типа.
Термическая резка скоса кромок
Применение термической резки требует подготовленного персонала и специальных мер безопасности, главным образом из-за своей пожароопасности. Возможна резка фаски для К-, V-, и Х-образные разделки с одинарным скосом кромки. Специалистам понятно, что качество кромок, подготовленных с помощью ручной термической резки, практически никогда не соответствует требованиям ГОСТ, и кромки нуждаются в последующей обработке (как минимум зачистка грата абразивными кругами или проволочными щетками).
Газокислородная резка легированных сталей осложнена тем, что во время сгорания углеводородных газов (пропана, ацетилена) в атмосфере кислорода образуется свободный углерод и угарный газ, которые, вступая во взаимодействие с легирующими элементами (прежде всего хромом и никелем), образуют тугоплавкие карбиды; удаление карбидов из зоны резки при температурах газокислородного пламени практически невозможно. Поэтому газокислородная резка, к примеру, нержавеющих хромоникелевых сталей практически невозможна.
Плазменная резка - практически единственный способ выполнять качественную резку высоколегированных сталей и алюминиевых сплавов.
При использовании машинной резки (особенно портальных машин термической резки с ЧПУ), качество кромок выше и размеры элементов разделки могут полностью соответствовать требованиям стандартов. Однако при термической резке (особенно легированных сталей) происходит интенсивное изменение химического состава и свойств поверхностного слоя реза - науглероживание, азотирование, появление рыхлостей - а также интенсивные деформации вырезанных деталей при больших толщинах металла. Рез зачастую требует зачистки для снятия дефектного поверхностного слоя, а полученная кромка имеет пониженную свариваемость и при сварке требует сварщика высокой квалификации (не ниже 5 разряда), особенно, если сварная деталь ответственная и сварное соединение подвергается неразрушающему контролю. Применение в качестве плазмообразующего газа газовых смесей типа Ar/He2, Ar/H2, N2/H2 или хотя бы кислорода существенно снижает степень науглероживания и азотирование поверхностного слоя и делает требования последующей механической зачистки реза неактуальными.
Лазерная резка применяется для весьма ограниченного диапазона толщин из-за высокой стоимости лазеров большой мощности и сложности систем фокусировки и наведения. Так как наиболее оптимальные для лазерной резки толщины лежат в пределах от 0,5 мм до 10 мм, то необходимость в резке скоса кромки для них практически отсутствует. Ручная лазерная резка, очевидно, еще долгое время будет невозможна из-за большой массы оптических головок и высокой опасности для операторов.
|
|
История развития пистолетов-пулеметов: Предпосылкой для возникновения пистолетов-пулеметов послужила давняя тенденция тяготения винтовок...
Индивидуальные и групповые автопоилки: для животных. Схемы и конструкции...
Опора деревянной одностоечной и способы укрепление угловых опор: Опоры ВЛ - конструкции, предназначенные для поддерживания проводов на необходимой высоте над землей, водой...
История развития хранилищ для нефти: Первые склады нефти появились в XVII веке. Они представляли собой землянные ямы-амбара глубиной 4…5 м...
© cyberpedia.su 2017-2024 - Не является автором материалов. Исключительное право сохранено за автором текста.
Если вы не хотите, чтобы данный материал был у нас на сайте, перейдите по ссылке: Нарушение авторских прав. Мы поможем в написании вашей работы!