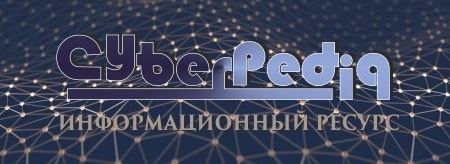
Биохимия спиртового брожения: Основу технологии получения пива составляет спиртовое брожение, - при котором сахар превращается...
Адаптации растений и животных к жизни в горах: Большое значение для жизни организмов в горах имеют степень расчленения, крутизна и экспозиционные различия склонов...
Топ:
Выпускная квалификационная работа: Основная часть ВКР, как правило, состоит из двух-трех глав, каждая из которых, в свою очередь...
Устройство и оснащение процедурного кабинета: Решающая роль в обеспечении правильного лечения пациентов отводится процедурной медсестре...
Характеристика АТП и сварочно-жестяницкого участка: Транспорт в настоящее время является одной из важнейших отраслей народного хозяйства...
Интересное:
Аура как энергетическое поле: многослойную ауру человека можно представить себе подобным...
Мероприятия для защиты от морозного пучения грунтов: Инженерная защита от морозного (криогенного) пучения грунтов необходима для легких малоэтажных зданий и других сооружений...
Как мы говорим и как мы слушаем: общение можно сравнить с огромным зонтиком, под которым скрыто все...
Дисциплины:
![]() |
![]() |
5.00
из
|
Заказать работу |
Содержание книги
Поиск на нашем сайте
|
|
Расчет ширины пролета цеха выполняется по формуле:
Впр = В1+ В2+ В3+ В4
(7.1)
где В1 - габаритные размеры самого большого оборудования в заготовительном отделении (в данном проекте рассматривается машина термической резки «Комета»);
в2- габаритные размеры самого большого оборудования в отделении сборки-сварки;
Вз - ширина проезда между двумя линиями рабочих мест, расположенных в одном пролете, принимается равный 4 метра;
в4 - припуски на расстояния между рабочим местом и складочным местом, между складскими местами, между одной из сторон оборудования и осью продольного ряда колонн.
![]() |
4- + -++ + -+-++ + + + -1-+ + 4-4+ + + + Ч-+ + 4--4+ + + + Н-+ + -+-++ + + + -Г+ + -+-++ + |
-(З^кЛЦ-
Рисунок 20 - схема расчета ширины пролета цеха
впр= = 10+10+4=24 м
Принимается впр = 24 м
В одноэтажных зданиях сборочно-сварочных цехов с продольным расположением производственного потока величина шага колон нормализована и составляет 12 м.
Высота пролета проектируемого сборочно-сварочного цеха обусловлена размерами подлежащих изготовлению в них сборочных единиц и изделий в целом, габаритными размерами запроектированного к установке в рассчитываемых пролетах производственного оборудования большей высоты и предусмотренным применением верхнего транспорта (мостового крана грузоподъемностью 5 тонн).
Высота пролета определяется из следующих выражений:
Нпр > h1+h2+h3+ h4+h5; (7.2)
Н3 > Нпр+h6+h7; (7.3)
Нц > Нз+6,67; (7.4)
где Нпр - высота пролета цеха (смотрите рисунок 20), от пола до уровня поверхности головки рельса подкрановых путей, м;
Н3 - высота пролета цеха от пола до нижнего уровня затяжки стропил перекрытия, м;
Нц - высота пролета цеха от пола до верхней точки крыши, м;
|
h1 -самое высокое оборудование, в данном курсовом проекте высота машины для термической резки «Комета», 2200 мм;
h2 - расстояние от высшей точки оборудования до нижней точки перевозимого краном груза, 1000 мм;
h3 - высота наибольшего груза, 300 мм;
h4 - максимальная высота прогиба строб, 500 мм;
h5 - расстояние от головки рельса до низшей точки подъемного крана в наиболее высоком положении, 1000 мм;
h6 - расстояние от головки рельса до наивысшей точки тележки мостового крана (по стандартам крана), 1000 мм;
h7 - расстояние от наивысшей точки тележки мостового крана до нижнего пояса фермы, принимается конструктивно 1000 мм.
1 - мостовой кран пролета цеха; 2 - железобетонная плита покрытия; 3 - 2-х слойное рубероидное покрытие с утеплителем толщиной 140мм; 4 - фонарное устройство кровли;5 - двухскатная стропильная ферма пролетом 36м; 6 -стальная подкрановая сварная балка пролетом 12м.
По формулам 8.2; 8.3; 8.4 определяется:
Нпр= 12000 мм Н3= 15000 мм
Нц= 21500 мм
Принимаем стандартную высоту цеха 21500 мм.
В дополнение к описанным выше расчетам, полученные значения высоты пролетов должны быть проверены с точки зрения соблюдения санитарных норм для промышленных предприятий, согласно которым на каждого работающего должно приходиться не менее 15 м объема производственного помещения.
7.2 Определение количества рабочих и рабочих мест В связи с изложенным определяется необходимое количество рабочих и
рабочих мест
7.3.Расчет необходимого количества рабочих мест
Принимается серийное производство изделий с точной программой производства и детальной разработкой технологического процесса.
Программа поточной линии производственного процесса рассчитывается по формуле:
П=Ф/t, (4.1)
где Ф — действительный годовой фонд времени оборудования или рабочих мест (Фм, = 2070 ч.- при односменном режиме работы [Красовский]);
П — число изделий, обрабатываемых или собираемых и свариваемых в течение года на поточной линии.
I - время такта выпуска представляет собой расчетную величину промежутка времени между выпуском одного и выпуском изготовляемого непосредственного вслед за ним другого такого же изделия, мин.
|
При серийном типе производства время такта выпуска металлоконструкций определяется по среднему времени выполнения операций на рабочих местах:
t= Ʃ Тшт.к/n, мин
где:
Тшт. к- время выполнения операций на отдельных рабочих местах,
Тшт. к=2385,88 мин(смотри);
n - количество операций в технологическом процессе, п=7.
По формуле 4.2 определяется среднее время выполнения операций:
t= 2385*88/7=341мин
По полученному значению такта определяем годовую программу П выпуска металлоконструкций:
П =Фм/ t (шт);
_ 2070*60
П =--------- = 364.22(шт).
Для дальнейшего расчёта количества рабочих мест М, выполняющих данную операцию, принимается программа равная П=365 (шт) металлоконструкций в год, используем формулу:
Нмч Тшт..кхтхП гл лл
М = ------------ =-----------------; (4.4)
(ФмхКмч) (ФмхКмч)
где:
Нмч - количество нормированных станко-часов (норма-час) для выполнения заданной годовой программы на данном типе оборудования,
Нмч= Тшт.к* П, (Тшт.к по каждой смотри);
Кмч - средний коэффициент выполнения нормы выработки по тем операциям, на которых применяется данное станочное, сборочно-сварочное оборудование и оснастка, Кмч =1,1;
т - количество одновременно задействованного оборудования на данном рабочем месте, т=1.
По формуле 4.4 определяется количество рабочих мест для каждой операции.
Количество рабочих мест для правки:
21.6x1x365 7884
М = ---------------- =-------- = 0,1,
(2070x60x1.1) 136620
Полученное по формуле 4.4 дробное М расчетное количество рабочих мест для выполнения конкретной операции округляется до ближайшего принятого (Мпр) целого числа. Принимается для правки Мпр=1.
Количество рабочих мест для термической резки:
%1 1342.84x1x365 490136.6 ог
М = ----------------- =----------- = 3.5.
(2070x60x1.1) 136620
Полученное по формуле 4.4 дробное М расчетное количество рабочих мест для выполнения конкретной операции округляется до ближайшего принятого (Мпр) целого числа. Принимается для термической резки Мпр=4.
Количество рабочих мест для сверловки:
3.7x1x365 1350.5
М =----------------- =-------- = 0,01.
(2070x60x1.1) 136620
Полученное по формуле 4.4 дробное М расчетное количество рабочих мест для выполнения конкретной операции округляется до ближайшего принятого (Мпр) целого числа. Принимается для сверловки Мпр=1.
|
Количество рабочих мест для механической резки:
..
50.19x1x365 18319.35
М= ----------------- =---------- = 0,13.
(2070x60x1.1) 136620
Полученное по формуле 4.4 дробное М расчетное количество рабочих мест для выполнения конкретной операции округляется до ближайшего принятого (Мпр) целого числа. Принимается для механической резки Мпр=1.
Количество рабочих мест для сборки-сварки узла 1:
108.39x1x365 39562.35
М = ---------------- =----------- = 0.29.
(2070x60x1.1) 136620
Полученное по формуле 4.4 дробное М расчетное количество рабочих мест для выполнения конкретной операции округляется до ближайшего принятого (Мпр) целого числа. Принимается для сборки-сварки узла 1 Мпр=1.
Количество рабочих мест для сборки-сварки узла 2:
351.84x1x365 128421.6
М =----------------- =---------- = 0.94.
(2070x60x1.1) 136620
Полученное по формуле 4.4 дробное М расчетное количество рабочих мест для выполнения конкретной операции округляется до ближайшего принятого (Мпр) целого числа. Принимается для сборки-сварки узла 2 Мпр=1.
Количество рабочих мест для общей сборки - сварки:
М=1342,84*1*365/(270*60*1,1)=490136,6/136620=3,5
Полученное по формуле 4.4 дробное М расчетное количество рабочих мест для выполнения конкретной операции округляется до ближайшего принятого (Мпр) целого числа. Принимается для общей сборки-сварки Мпр=2.
При этом степень использования оборудования или рабочих мест по времени определяем проектным коэффициентом загрузки г/, который
представляет собой отношение расчетного количества оборудования к принятому:
η=M/ Мпр
для правки: η=0,1/1=0,1;
для термической резки: η=3,5/4=0,9;
для сверловки: η=0,01/1=0,
для механической резки: η=0,13/1=0,13;
для сборки-сварки узла 1: η=0,29/1=0,29;
для сборки-сварки узла 2: η=0,94/1=0,94;
для общей сборки - сварки: η=1,3/2=0,65;
Средний (η сР) по участку, отделению (цеху) коэффициент загрузки оборудования определяется по формуле:
ηср=ƩM /ƩMпр
по формуле 4.6:
ηср =6,27/11=0,57
Оформления результатов расчета количества и коэффициента загрузки рабочих мест до и после синхронизации операций по сборочно-сварочному участку приведено в таблице 4.1.
Таблица 4.1
Результаты расчёта количества рабочих мест и коэффициента загрузки
Рабочие места | ||||
М | Мпр | η | ηср | |
Правка | 0,1 | 0,1 | 0,5 | |
Термическая резка | 3,5 | 0,9 | ||
Сверловка | 0,0 1 | 0,0 1 | ||
Механическая резка | 0,1 | 0,1 3 | ||
Сборка-сварка узла 1 | 0,2 9 | 0,2 9 | ||
Сборка-сварка узла2 | 0,9 | 0,9 | ||
Общая сборка-сварка | 1,3 | 0,6 | ||
Итого: | 1 1 |
7.4 Определение состава и потребного количества работающих
|
В целом состав работающих на участке цеха можно разделить на следующие основные категории:
-производственные рабочие (правильщик, разметчик, газорезчик, сверловщик, фрезеровщик, штамповщик, сборщик, сборщик-сварщик, газоэлектросварщик, электосварщик и др.);
-вспомогательные рабочие (принимают 25-30% от числа производственных рабочих), постоянно занятые на участке (подручный, крановщик, стропальщик и др.) и занятые межремонтным обслуживанием (наладчик, смазчик, электршг и др.);
- инженерно-технический работник (8% от числа всех рабочих);
- сметно-конторские служащие (3% от числа всех рабочих);
- младший обслуживающий персонал (2% от числа всех рабочих);
- контролеры качества продукции (1% от числа всех рабочих).
Для серийного производства списочный численный состав
производственных рабочих Р производится на основе разработанного и нормированного технологического процесса по формуле:
P=Тшт.к*Х*β/Фр*Кнм
где Фр - действительный годовой фонд времени рабочего, час (сварщик, газорезчик и др.) Фр=1840час, для слесаря-сборщика (сборщик-сварщик);
β - коэффициент, учитывающий численность бригады либо многостаночное обслуживание. Принимается равным количеству работающих в отношении единицы к количеству обслуживающих машин, (3=1;
Кнм - коэффициент перегрузки Кнм=1,1;
Тшт.к - штучно-калькуляционное время выполнения операций на отдельных рабочих местах, мин, (смотри приложение А таблица А1);
П - программа выпуска металлоконструкций, шт.
По формуле (4.7) определяется численный состав производственных рабочих для каждого участка цеха:
_ 21.6x365x1 7884
для правки: Р = ------------- =-------- = 0,06;
1860x60x1,1 122760
1342.84x365x1 490136.6
для термическои резки: Р =---------------- =----------- = 3.99;
1860x60x1,1 122760
п 3.7x365x1 1350.5
для сверловки: Р = ------------- =-------- = 0,01;
1860x60x1,1 122760
50.19x365x1 18319.35 ллл
для механической резки: Р = -------------- =---------- = 0,14;
1860x60x1,1 122760
_ 108.39x365x1 39562.35 лои
для сборки-сварки узла 1: Р =-------------- =----------- = 0,34;
3 1840x60x1,1 121440
_ 351.84x365x1 128421.6, ЛГ
для сборки-сварки узла 2: Р =-------- =---------- = 1.06;
3 1840x60x1,1 121440
_ 507.3x365x1 185164.5, со
для общей сборки - сварки: Р =------- =---------- = 1.52.
* 1840x60x1,1 121440
Трудоемкость Q (чел-час, ст-час) выполнения годовой программы, затраченная (одним рабочим или одним станком) на каждую операцию технологического процесса определится по формуле:
Q= (Тшт.к*П/60)*1
|
для правки: Q=(21.6*365/60)*1=131,4;
для термической резки: Q=(1342,84*365/60)*1=8168,9;
для сверловки: Q=(3,7*365/60)*1=22,5;
для механической резки: Q=(50,19*365/60)*1=305,3;
для сборки-сварки узла: Q=(108,39*365/60)*1=659,4.
В таблице 4.2 приводятся значения полученных результатов расчета работающих (определено по формуле 4.7) по разработанному технологическому процессу.
Таблица 4.2
Количество производственных (основных) рабочих
Технологическая операция | Q- трудоёмк. Выполнения годов. Прогр. (чел-час) | Ф- действит. Годов. Фонд времени рабочих, час | Количество работающих | |
Расчёт ное | Приня тое | |||
Правка | 131,4 | 0,06 | ||
Термическая резка | 8168,9 | 3,99 | ||
Сверловка | 22,5 | 0,01 | ||
Механическая резка | 305,3 | 0,14 | ||
Сборка-сварка узла 1 | 659,4 | 0,34 | ||
Сборка-сварк \ узла2 | 2140,4 | 1,06 | ||
Общая сборка-сварка | 3086,1 | 1,52 | ||
Итого: |
Для выполнения производственной программы технологическому процессу кроме основных производственных рабочих требуется состав работающих.
Число вспомогательных рабочих принимается 30% от численности основных производственных рабочих, т.е ориентировочно принимается три человека. Для приведения работ по контролю качества сварных швов узлов и готового изделия принимается один дефектоскопист. Оплата всех работ по
ремонту, наладке оборудования, транспортных операций, уборке территории включена в арендную плату за производственные площади.
В таблице 4.3 представлена ведомость производственных рабочих.
На основании полученных расчетов количества рабочих мест и производственных рабочих принимается вариант планировки цеха с петлевым направлением производственного потока, с 10 тонным мостовым краном КР-70, обслуживающим сборочно-сварочные операции.
Таблица 4.3
Ведомость производственных рабочих
Профессия рабочего | Численность | Разряд | ||||||
Ос нов-ных | Вспог а-тельных | б | ||||||
Правильщик | + | |||||||
Резчик | + | |||||||
Сверловщик | + | |||||||
Рубщик | + | |||||||
Сборщик-сварщик (у1) | + | |||||||
Сборщик-сварщик (у2) | + | |||||||
Сборщик-сварщик (общей) | + | |||||||
Итого: |
|
|
Типы сооружений для обработки осадков: Септиками называются сооружения, в которых одновременно происходят осветление сточной жидкости...
Индивидуальные и групповые автопоилки: для животных. Схемы и конструкции...
Своеобразие русской архитектуры: Основной материал – дерево – быстрота постройки, но недолговечность и необходимость деления...
Архитектура электронного правительства: Единая архитектура – это методологический подход при создании системы управления государства, который строится...
© cyberpedia.su 2017-2024 - Не является автором материалов. Исключительное право сохранено за автором текста.
Если вы не хотите, чтобы данный материал был у нас на сайте, перейдите по ссылке: Нарушение авторских прав. Мы поможем в написании вашей работы!