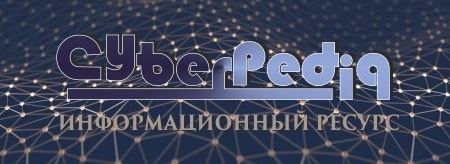
Индивидуальные и групповые автопоилки: для животных. Схемы и конструкции...
Типы оградительных сооружений в морском порту: По расположению оградительных сооружений в плане различают волноломы, обе оконечности...
Топ:
Методика измерений сопротивления растеканию тока анодного заземления: Анодный заземлитель (анод) – проводник, погруженный в электролитическую среду (грунт, раствор электролита) и подключенный к положительному...
Оценка эффективности инструментов коммуникационной политики: Внешние коммуникации - обмен информацией между организацией и её внешней средой...
Интересное:
Финансовый рынок и его значение в управлении денежными потоками на современном этапе: любому предприятию для расширения производства и увеличения прибыли нужны...
Средства для ингаляционного наркоза: Наркоз наступает в результате вдыхания (ингаляции) средств, которое осуществляют или с помощью маски...
Влияние предпринимательской среды на эффективное функционирование предприятия: Предпринимательская среда – это совокупность внешних и внутренних факторов, оказывающих влияние на функционирование фирмы...
Дисциплины:
![]() |
![]() |
5.00
из
|
Заказать работу |
Содержание книги
Поиск на нашем сайте
|
|
ПРИМЕРНЫЙ ТЕМАТИЧЕСКИЙ ПЛАН ДИСЦИПЛИНЫ
Раздел, тема | Количество учебных часов | |||||
Для дневной формы | Для заочной формы | |||||
Всего | Лабор | Практ | Всего | Лабор | Практ | |
Введение. | ||||||
Раздел 1. Основы теории рациональной эксплуатации оборудования | ||||||
1.1. Основы теории износа машин. | ||||||
1.2 Типовая система технического обслуживания и ремонта оборудования | ||||||
1.3.Основы рациональной эксплуатации оборудования. | ||||||
1.4 Пути и средства повышения долговечности оборудования | ||||||
1.5 Смазка оборудования | ||||||
Раздел 2. Основы технологии ремонта оборудования. | ||||||
2.1 Технологический процесс ремонта оборудования. | ||||||
2.2 Ремонтная техническая документация. | ||||||
2.3 Подготовка ремонтных работ | ||||||
2.4 Разборка оборудования в процессе ремонта | ||||||
2.5 Дефектация деталей. | ||||||
2.6 Сборка оборудования в процессе ремонта. | ||||||
Обязательная контрольная работа №1 | ||||||
2.7 Общая сборка, испытание, проверка и приемка оборудования после ремонта . | ||||||
Раздел 3. Методы и способы восстановления деталей. | ||||||
3.1. Основные методы восстановления деталей. | ||||||
3.2 Восстановление деталей сваркой и наплавкой |
3.3. Восстановление деталей металлизацией. | ||||||
3.4. Восстановление деталей электролитическим и электроискровым способами. | ||||||
3.5. Восстановление деталей полимерными материалами | ||||||
3.6. Слесарные и слесарно-механические способы восстановления и пригонки деталей. | ||||||
3.7. Восстановление деталей клеевым методом. | ||||||
Раздел 4. Ремонт типовых деталей, узлов и механизмов. | ||||||
4.1. Ремонт базовых и корпусных деталей. | ||||||
4.2. Ремонт деталей механизмов вращательного движения. | ||||||
4.3. Ремонт деталей механизмов передачи движения. | ||||||
4.4. Ремонт деталей механизмов преобразования движения. | ||||||
4.5. Ремонт гидравлических и смазочных систем | ||||||
4.6. Ремонт неподвижных соединений и трубопроводов. | ||||||
4.7. Ремонт пневматических приводов. | ||||||
Обязательная контрольная работа №2 | ||||||
Раздел 5. Эксплуатация, техническое обслуживание и ремонт основных видов технологического оборудования. | ||||||
5.1. Ремонт металлорежущих станков. | ||||||
5.2. Техническое обслуживание и ремонт станков с ЧПУ и промышленных роботов. | ||||||
5.3. Эксплуатация и ремонт кузнечно-прессового оборудования. |
|
5.4 Эксплуатация и ремонт литейного оборудования | ||||||
5.5 Эксплуатация и ремонт подъемно-транспортных устройств | ||||||
Раздел 6. Модернизация и паспортизация технологического оборудования. | ||||||
6.1 Основные направления модернизации технологического оборудования. | ||||||
6.2 Модернизация металлорежущего оборудования | ||||||
6.3 Модернизация кузнечно-прессового и литейного оборудования. | ||||||
6.4 Модернизация кранового оборудования. | ||||||
6.5 Паспортизация оборудования. | ||||||
Раздел 7. Монтаж промышленного оборудования. | ||||||
7.1. Основы технологии монтажа оборудования. | ||||||
7.2. Транспортировка и распаковка оборудования. | ||||||
7.3. Особенности монтажа оборудования на фундамент. | ||||||
7.4. Монтаж мостовых кранов. | ||||||
Курсовое проектирование | ||||||
Итого |
|
МЕТОДИЧЕСКИЕ РЕКОМЕНДАЦИИ
ПО ИЗУЧЕНИЮ РАЗДЕЛОВ, ТЕМ ПРОГРАММЫ
Самостоятельное изучение учебного материала является основной формой учебной деятельности учащихся заочной формы обучения.
Одним из условий, определяющих эффективность самостоятельной учебной деятельности учащихся, является формирование навыков культуры умственного труда, рационального планирования занятий и самоконтроля. Необходимо придерживаться следующих рекомендаций при организации самостоятельной работы по изучению дисциплины:
- равномерно распределять время, запланированное для самостоятельной работы;
- по программе и методическим указаниям ознакомиться с вопросами по теме и последовательностью их изучения;
- отыскать в учебной, справочной литературе необходимый материал, внимательно его прочитать и законспектировать; при изучении материала нельзя ограничиваться каким-либо одним пособием, так как в настоящее время еще не создано учебника, достаточно полно освещающего все разделы программ; кроме того, одной из целей изучения данной дисциплины является приобретение навыков работы со специальной технической и справочной литературой
- после детального изучения темы ответить на вопросы для самопроверки;
- по материалу, усвоение которого вызвало проблемы, обратиться за консультацией к преподавателю;
- самостоятельно выполнить контрольную работу;
- сопоставить с практическим опытом и наблюдениями полученные теоретические знания и применить их в своей профессиональной деятельности.
|
Введение
Задачи и содержание предмета "Техническая эксплуатация и ремонт технологического оборудования ", связь с другими дисциплинами. Значение ремонтной службы в народном хозяйстве. Повышение эффективности производства - принципиальная основа современного экономического развития. Значение правильной эксплуатации и своевременного качественного ремонта в улучшении использования производственных мощностей, повышении производительности труда, качества работ, надежности и долговечности машин, в экономии материальных и трудовых ресурсов
Литература: [1,c.3-7];[2, с.3-4]; [6, с.3-4]; [7, с.3-6]
Методические указания
Изучая введение, следует уяснить роль и место дисциплины «Техническая эксплуатация технологического оборудования» в специальной подготовке учащихся к практической деятельности на производстве. Затем ознакомиться с тематикой и содержанием разделов и тем.
Следует уяснить, что из-за быстрого роста и усложнения парка оборудования на предприятиях машиностроения остро встал вопрос о его рациональном использовании и обеспечении его надлежащего состояния. Во избежание аварий и преждевременного выхода оборудования из строя, что может привести к нарушению всего производственного цикла, необходимы своевременное профилактическое обслуживание и ремонт оборудования. В особенности возрастает значение технологии ремонта в связи с требованием систематического повышения надежности, долговечности станков, производительности. Повышение уровня технологической оснащенности, развитие массовых и непрерывных производственных процессов приводят к усиленному износу оборудования и, соответственно к увеличению затрат на ремонтные работы. Одной из главных задач, стоящих перед ремонтными службами, является дальнейшее повышение качества и снижение себестоимости ремонта путем более широкого внедрения индустриальных методов и развития специализированных мощностей.
Вопросы для самоконтроля:
1. Сформулируйте основные цели дисциплины.
2. Определите задачи дисциплины.
3. Чем вызвано изучение дисциплины на завершающем этапе обучения?
|
4. Какова роль ремонтной службы для народного хозяйства?
5. Почему в настоящее время на предприятиях ремонт оборудования имеет большое значение?
6. Как можно увеличить долговечность оборудования, повысить его производительность?
Раздел 1. Основы теории рациональной эксплуатации оборудования.
Методические указания
При изучении вопросов данной темы следует исходить из того, что трение и износ являются одной из основных причин выхода из стоя оборудования, а следовательно ремонта.
Там где есть трение, есть интенсивный износ деталей машин.
Кроме того, износ-явление сложное. В природе нет предметов, не подвергаемых износу.
В условиях научно-технического прогресса процесс старения начинается еще до того, как машина сходит с заводского конвейера, и продолжается на протяжении всего амортизационного срока. Работоспособность, надежность, производительность и экономическая эффективность машин непосредственно зависят от характера и интенсивности протекания этого процесса. Изменение эксплуатационных свойств и качественных характеристик по мере старения машин происходит в результате их физического и морального износа. При эксплуатации машин процессы, вызывающие повреждения и разрушения деталей, именуют вредными.
Вопросы для самоконтроля:
1. В чем отличие механического износа от коррозионно-механического?
2. В чем сущность усталостного износа?
3. В чем сущность абразивного износа?
4. Какие вредные процессы протекают при эксплуатации детали?
5. Дайте определение понятиям «нормальный износ», «допустимый износ».
6. По каким признакам можно определить износ оборудования?
Методические указания
Основой системы технического обслуживания и ремонта технологического оборудования является профилактика, заключающаяся в проведении плановых осмотров и ремонтов, поддерживающих постоянную работоспособность оборудования. Все работы по плановому техническому обслуживанию и ремонту выполняются в определенной последовательности, образуя повторяющиеся циклы. Исходными данными при планировании ремонтов станков является структура и продолжительность ремонтных циклов. Для сохранения работоспособности оборудования и уменьшения суммы затрат на его поддержание, улучшения качества и сокращения сроков ремонта для каждого вида оборудования строится график ППР. Нужно добиться однозначного понимания каждого вида ремонта, обусловленного видами проводимых при этом работ, его назначением. При изучении данной темой следует помнить, что вывод станков в капитальный ремонт следует по их действительному техническому состоянию.
Вопросы для самоконтроля:
1. Какие виды работ предусматривает ТСТО и Р?
|
2. В чем заключается сущность капитального ремонта; среднего; текущего?
3. Чем объясняется многообразие структур ремонтных циклов?
4. Что называется ремонтным циклом; ремонтным периодом
5. Какие виды работ выполняются при техническом обслуживании?
6. Дайте определение понятию «ремонтосложнеость оборудования».
7. От чего зависит трудоемкость оборудования?
8. В чем сущность узлового метода ремонта?
Методические указания
Из всех факторов, влияющих на техническое состоянии машин, на сохранение их высокой работоспособности и как следствие этого, способности к высокопроизводительной работе, самым важным является правильная эксплуатация оборудования в установленных режимах.
Надзор за техническим состояниемоборудования осуществляет ОГМ, который не только контролирует условия эксплуатации, но и готовит технические рекомендации по улучшению состояния оборудования.
Статистика показывает, что большое число несчастных случаев на промышленных предприятиях связано с неправильной эксплуатацией грузоподъемных машин. Поэтому к ремонтному персоналу, обслуживающему такие машины, предъявляются особо строгие требования. При изучении данной темы необходимо в отделе главного механика изучить имеющиеся эксплуатационные документы на различные виды оборудования.
Вопросы для самоконтроля:
1. Перечислите правила технической эксплуатации, соблюдение которых обязательно при работе на оборудовании?
2. Кто несет ответственность за сохранность оборудования предприятия, цеха?
3. Дайте определения понятиям «поломка», «авария».
4. Какие внешние условия необходимо соблюдать при размещении оборудования в цехе?
5. Перечислить основные эксплуатационные документы согласно ЕСКД.
6. Что такое ОГМ?
Методические указания
Предприятие несет большие материальные потери из-за простоев машин и станков в связи с преждевременным ремонтом и непригодностью к использованию их деталей. Чтобы уменьшить их потери предприятия ищут пути продления времени работы оборудования между ремонтами. При изучении данной темы необходимо вспомнить виды термической и химико-термической обработки, которые изучались в курсе «Материаловедение и технология материалов». Необходимо усвоить средства повышения долговечности различных типов деталей и узлов и уяснить особенности протекания приработки оборудования.
Вопросы для самоконтроля:
1. Перечислить основные способы увеличения долговечности деталей.
2. Какие способы упрочнения поверхности применяют на валах?
3. Объясните сущность процесса улучшения.
4. В чем отличие закалки ТВЧ от объемной закалки?
5. Перечислите виды износостойких покрытий применяемых для увеличения долговечности.
6. Что называется деталью-компенсатором?
7. Что происходит с деталями в период приработки?
Методические указания
Смазочные материалы являются основным средством в распоряжении ремонтников при борьбе с износом. Промышленность выпускает в большом ассортименте смазочные материалы с различными характеристиками. От правильного выбора смазочного материала зависит работоспособность механизма. Т.е необходимо уяснить основные характеристики смазочных материалов и правила их подбора в зависимости от условий эксплуатации деталей в узле.
Смазочные устройства являются надежными помощниками ремонтников. Поэтому особое внимание надо обратить на особенности их конструкции, область применения и правила эксплуатации.
Вопросы для самоконтроля:
1. Для чего применяют смазочные материалы?
2. Приведите классификацию смазочных материалов.
3. Почему показатель кинематической вязкости является основным при выборе масел?
4. Какие показатели определяют выбор пластичных смазок?
5. Перечислите основные компоненты, входящие в состав пластичных смазок.
6. Как ведет себя пластичная смазка при увеличении нагрузки; после снятия ее? Почему?
7. Расшифруйте обозначение масла И-20А.
8. Для чего производиться регенерация масел?
Методические указания
С данной темы начинается непосредственно ремонт технологического оборудования. Поэтому при изучении материала следует усвоить основные понятия технологии ремонта, основные этапы ремонта, сущность каждого этапа, его назначение. Типовой технологический процесс - основной документ технологии ремонта. Технологический маршрут восстановления детали представляет собой перечень всех операций, которые должна пройти деталь, включая вспомогательные и контрольные. В нем приводятся наименование операции, применяемое оборудование, приспособления и инструмент, а также основное содержание операции.
Проектирование технологических процессов ремонта деталей имеет такую последовательность:
- анализ технологического процесса изготовления новой детали; анализ данных о характере дефектов;
- выбор возможных способов устранения отдельных дефектов;
- наметки последовательности выполнения технологических операций с выбором технологических баз, технологического оборудования и оснастки;
- установление режимов работы с обоснованием операционных припусков и допусков на обработку;
- обоснование экономической эффективности принятого варианта; составление технологической документации на процесс ремонта детали.
Общие принципы проектирования технологических процессов ремонта деталей остаются теми же, что и при проектировании процессов изготовления деталей.
При выборе наиболее рационального способа ремонта следует учитывать ряд исходных данных: размеры, форму и точность детали, материал детали и ее термическую обработку, условия работы детали в машине, характеристику дефектов, производственные возможности ремонтного предприятия и др.
Технико-экономическое обоснование способа ремонта должно базироваться на комплексном анализе технической, организационной, социальной целесообразности и экономической эффективности применения возможных вариантов технологии.
Вопросы для самоконтроля:
1 Предварительная механическая обработка;2 Отжиг;
3 Закалка; 4 Наплавка;5 Полирование;6 Контроль;
7 Шлифование;8 Правка.
Методические указания
Ремонтные документы- это рабочие конструкторские документы, предназначенные для подготовки ремонтного производства, ремонта и контроля изделия после ремонта. Общие требования к оформлению и разработке ремонтных документов устанавливаются основополагающими стандартами ЕСКД.
Следует ознакомиться с основными документами, применяемыми при ремонте, и правилами их оформления. С правилами заполнения документов можно ознакомиться в отделе главного механика.
Ремонтные чертежи являются основным видом документации при ремонте деталей и сборочных единиц, при сборке и контроле отремонтированного изделия, при изготовлении дополнительных деталей и деталей с ремонтными размерами. Ремонтные чертежи выполняются в соответствии с ГОСТ 2.604-87.
Вопросы для самоконтроля:
Тема 2.3. Подготовка ремонтных работ
Технологическая, материальная и организационная подготовка, состав работ, назначение видов подготовок. Календарный график производства ремонта, основные принципы его составления. Прием оборудования в ремонт, требования к оборудованию, сдаваемому в ремонт. Техническая документация.
Литература: [5,т.1 с.141-152]; [11]
Борисов Ю.С. Техническая и материальная подготовка ремонтных работ.- М.: Машиностроение, 1983.
Методические указания
Материал данной темы рассматривает порядок подготовки оборудования к ремонту включающий следующие этапы: прием оборудования в ремонт; порядок и особенности демонтажа оборудования, а так же календарный график ремонта оборудования. Следует обратить внимание на комплект документации передаваемой в РМЦ вместе с оборудованием.
Основой при построении сетевого графика является трудоемкость ремонта, нормы продолжительности простоя оборудования в ремонте и типовая технология ремонта. Необходимо помнить, что при разработке графика учитывают трудоемкость только слесарных и прочих работ (кроме станочных), так как график предназначен для организации работ ремонтной бригады, а не станочников.
Вопросы для самоконтроля:
Методические указания
Изучение вопросов данной темы следует начинать с уяснения того, что необходимость разборки узлов определяется видом и задачами ремонта и что разборка механизма ведет к нарушению плотности соединения. Поэтому разбирают только ту сборочную единицу, которая подлежит ремонту.
Разборка металлорежущего станка или другого вида оборудования должна производиться с соблюдением правил разборки. Технологические мероприятия, обеспечивающие сохранность деталей, сводятся к исключению ручной или ударной разборки. Далее следует ознакомиться с оборудованием, инструментами и приспособлениями, применяемыми при разборке.
Детали, сдаваемые на восстановление, очищают от загрязнений до такого состояния, чтобы их можно было осмотреть и выявить дефекты. Очистка деталей от загрязнений является специфической операцией ремонтного производства. От качества и полноты проведения этой операции зависят культура производства, производительность труда рабочих-ремонтников, эффективность использования оборудования и, в конечном итоге, долговечность работы отремонтированных изделий. При изучении вопросов очистки и промывки деталей особое внимание следует обратить на правильность выбора промывочного раствора, т.к. отдельные компоненты этого раствора могут войти в реакцию с металлом и ещё более ухудшить рабочую поверхность.
Вопросы для самоконтроля:
Методические указания
Цель дефектации - выявить дефекты деталей, установить возможность ремонта или определить необходимость замены детали. Дефектацию промытых и просушенных деталей производят после их комплектования по узлам. Эта операция требует большого внимания. Каждую деталь сначала осматривают, затем соответствующим проверочным или измерительным инструментом проверяют её размеры. В определённых случаях проверяется взаимодействие сопрягаемых деталей.
При дефектации деталей важно уметь определять величины износа отдельных поверхностей.
При рассмотрении вопросов данной темы необходимо вспомнить материал, изучаемый в курсе «Нормирование точности и технические измерения», т.к. при выборе способа и технологии восстановления большое значение имеют размеры дефектов, определяемые в процессе измерения универсальным и специальным измерительным инструментом. Необходимо соотносить контролируемые параметры с используемыми методами и средствами дефектации.
Вопросы для самоконтроля:
1. Сформулируйте основные цели дефектации.
2. Перечислите основные методы дефектации.
3. Объяснить сущность метода «керосиновая проба» применяемого при дефектации. Перечислить дефекты обнаруживаемые данным методом.
4. Объяснить сущность метода «гидравлическое испытание» применяемого при дефектации. Перечислить дефекты обнаруживаемые данным методом?
5. На какие группы годности классифицируются детали? Как они помечаются при дефектации?
6. Какие сведения содержаться в ведомости дефектации, карте техпроцесса дефектации?
Методические указания
При изучении вопросов данной темы необходимо вспомнить конструкции и характеристики соединений применяемых при изготовлении машин, требования к работе механизмов. Затем основное внимание надо обратить на способы сборки и регулировки, обеспечение определенных натягов и зазоров в сопряжениях, применяемый при этом инструмент, приспособления.
Вопросы для самоконтроля:
1. В чем сущность сборки с применением компенсаторов?
2. Приведите классификацию соединений.
3. Приведите примеры подвижных разъемных соединений, неподвижных неразъемных.
4. Какие правила необходимо соблюдать при сборке группового резьбового соединения?
5. Какое термическое воздействие нужно применить при большом натяге подшипника на вал?
6. Какова последовательность действий при сборке штифтовых соединений?
7. Для чего необходимо производить балансировку? Какие детали ей подвергаются? Как производиться балансировка?
Методические указания
Изучая материал темы, следует помнить, что сборка является завершающим этапом ремонта оборудования и в процессе сборки обеспечивается качество ремонта.
Испытания относятся к завершающему этапу сборочных работ. Они как бы дают оценку качеству выполнения всех предыдущих работ. Условно эти работы можно разделить на 2 этапа. На первом этапе ведутся индивидуальные и комплексные испытания оборудования - это обкатка и испытания под нагрузкой. Второй, заключительный этап - комплексное опробование оборудования и приемка оборудования в эксплуатацию.
Вопросы для самоконтроля:
1. В чем отличие технологического процесса сборки при ремонте от технологического процесса сборки при изготовлении изделий?
2. В чем сущность понятия: «При сборке обеспечивается качество ремонта»?
3. Объяснить цель проведения обкатки оборудования после ремонта.
4. Охарактеризовать цель и порядок проведения обкатки, проверяемые параметры.
5. Объяснить цель проведения испытания оборудования после ремонта под нагрузкой и в работе.
6. Какие параметры контролируются при проведении проверки на геометрическую точность?
7. Перечислите документацию, составляемую при передаче оборудования из ремонта в эксплуатацию.
Методические указания
Материал данной темы и последующих тем данного раздела являются основными в технологии ремонта. При ремонте деталей пользуются положениями технологии и организации, действующими в процессе изготовления.
При изучении методов ремонта следует не ограничиваться каким-либо одним источником, а пользоваться несколькими учебниками, содержащими соответствующий материал. После ознакомления со способом восстановления по нескольким учебникам основные положения данного способа необходимо законспектировать, т.к. этот материал нужен при изучении последующих тем программы.
Несмотря на большое разнообразие способов восстановления деталей на практике приходиться выбирать один, но он должен быть наиболее целесообразным и эффективным в конкретных производственных условиях.
При восстановлении работоспособности сопряжений и посадок бывает целесообразно изменять первоначальные размеры деталей. Обработка производиться либо до выведения следов износа и получения правильной геометрической формы, либо до заранее установленного ремонтного размера. При изучении данного вопроса особое внимание обратить на достоинства системы регламентированных ремонтных размеров.
Вопросы для самоконтроля:
1. Перечислите факторы, от которых зависит целесообразность применения соответствующего способа восстановления деталей.
2. Почему восстановление любой детали надо начинать с восстановления исходных баз?
3. Дайте определение понятию «ремонтный размер».
4. В чем сущность и отличие свободных и категорийных ремонтных размеров?
5. В чем преимущества категорийных размеров при ремонте?
6. Какими причинами можно объяснить использование пригоночных размеров при ремонте?
7. В чем сущность и преимущества восстановления деталей до первоначальных размеров?
Практическая работа №7
Разработка технологического процесса наплавки
Литература: [2,c.166-175];[5,т.2, с.44-78]; [6, с.71-74]; [12, с.77-92]; [16]; [15]
Поляценко А.В. Современные методы восстановления и повышения долговечности деталей при ремонте.- Машиностроение, 1985
Методические указания
Виды сварки были рассмотрены при изучении дисциплины «Материаловедение и технология материалов». Рассмотрение вопросов данной темы следует начинать с четкой классификации видов сварки и особенностей ее применения при ремонте деталей из различных материалов.
При изучении данной темы особое внимание следует уделить на изучение вопросов восстановления первоначальных размеров деталей различными видами наплавки. При наплавке применяют различные источники тепла для нагрева наносимых материалов и детали. В зависимости от способа нагрева, по виду защиты сварочной ванны, по степени автоматизации различают основные виды наплавки. Обратить внимание на достоинства и недостатки данных методов, и их применимость. Четко уяснить технологическую последовательность выполнения сварки и наплавки.
Вопросы для самоконтроля:
1. Дайте определения сварки и наплавки
2. Перечислите виды сварки и наплавки применяемой при ремонте.
3. В чем сущность процесса вибродуговой наплавки?
4. При каком виде сварки применяют ацетилен, пропан-бутан?
5. Укажите основные причины появления деформаций и внутренних напряжений при дуговой и газовой сварке металлов.
6. Как влияют, содержащиеся в стали углерод и легирующие элементы на свариваемость?
7. Установить технологическую последовательность выполнения газовой сварки чугуна.
8. В каких случаях применяют сварку и наплавку в среде углекислого газа?
9. Перечислите особенности сварки и наплавки деталей из цветных сплавов.
10. Установить технологическую последовательность выполнения наплавки под слоем флюса. Перечислите ее достоинства и недостатки.
Методические указания
Металлизация широко применяется в ремонтной практике, т.к. позволяет наносить слой покрытия толщиной до 10 мм на любой металл и другие различные материалы, что позволяет исключить применение дорогостоящих и дефицитных материалов в качестве основы, а применить конструкционные стали.
Особенность напыления состоит в отсутствии расплавления поверхности основного материала, что обеспечивает незначительную деформацию. Соединение металлических частиц с поверхностью детали и между собой носит механический характер, что обуславливает важность предварительной подготовки поверхности в виде нарезания «рваной» резьбы или песко – и дробеструйной обработки. Виды напыления различают в зависимости от источника тепловой энергии, затрачиваемой на нагрев. При изучении материала данной темы необходимо провести сравнение данных способов металлизации, а именно применяемого материала для напыления, достоинств и недостатков методов.
Вопросы для самоконтроля:
1. В чем сущность процесса металлизации?
2. Какую шероховатость должна иметь поверхность, подлежащая металлизации?
3. Определите способы подготовки поверхностей деталей к металлизации.
4. Установите область применения металлизации.
5. В чем отличие металлизации напылением: электродуговой, газовой, высокочастотной, плазменной.
6. Какие основные режимы устанавливаются при проведении металлизации?
Методические указания
При необходимости восстановления многочисленных деталей с небольшим износом, но с высокими требованиями к износостойкости, твердости и сплошности покрытия и прочности соединения с основой в ремонтном производстве применяют гальванические покрытия. Однако следует помнить, что скорость нанесения низкая, процесс многооперационный и сопровождается расходом воды и загрязнением сточных вод. Поскольку процесс наращивания происходит за счет электролиза, то требуется большое количество подготовительных операций. Предварительная механическая обработка (шлифование и полирование) необходима для устранения следов изнашивания и обеспечения заданной шероховатости. Шероховатость должна быть Ra 0,63…1,6 мкм. В зависимости от видов материала покрытий гальванические процессы делятся на осталивание, хромирование, цинкование, кадмирование, никелирование и т.д.
Электроискровой обработкой можно восстанавливать изношенные детали, изменять свойства поверхностного слоя, упрочнять режущие кромки инструмента нанесением твердых сплавов и т.д. Процесс применяют для наращивания и упрочнения поверхности с износом до 0,2 мм при высоких требованиях к твердости и износостойкости поверхности. При
|
|
История создания датчика движения: Первый прибор для обнаружения движения был изобретен немецким физиком Генрихом Герцем...
Организация стока поверхностных вод: Наибольшее количество влаги на земном шаре испаряется с поверхности морей и океанов (88‰)...
Наброски и зарисовки растений, плодов, цветов: Освоить конструктивное построение структуры дерева через зарисовки отдельных деревьев, группы деревьев...
Археология об основании Рима: Новые раскопки проясняют и такой острый дискуссионный вопрос, как дата самого возникновения Рима...
© cyberpedia.su 2017-2024 - Не является автором материалов. Исключительное право сохранено за автором текста.
Если вы не хотите, чтобы данный материал был у нас на сайте, перейдите по ссылке: Нарушение авторских прав. Мы поможем в написании вашей работы!