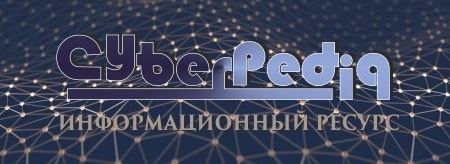
Кормораздатчик мобильный электрифицированный: схема и процесс работы устройства...
Историки об Елизавете Петровне: Елизавета попала между двумя встречными культурными течениями, воспитывалась среди новых европейских веяний и преданий...
Топ:
Организация стока поверхностных вод: Наибольшее количество влаги на земном шаре испаряется с поверхности морей и океанов...
Характеристика АТП и сварочно-жестяницкого участка: Транспорт в настоящее время является одной из важнейших отраслей народного хозяйства...
Особенности труда и отдыха в условиях низких температур: К работам при низких температурах на открытом воздухе и в не отапливаемых помещениях допускаются лица не моложе 18 лет, прошедшие...
Интересное:
Как мы говорим и как мы слушаем: общение можно сравнить с огромным зонтиком, под которым скрыто все...
Что нужно делать при лейкемии: Прежде всего, необходимо выяснить, не страдаете ли вы каким-либо душевным недугом...
Наиболее распространенные виды рака: Раковая опухоль — это самостоятельное новообразование, которое может возникнуть и от повышенного давления...
Дисциплины:
![]() |
![]() |
5.00
из
|
Заказать работу |
|
|
Высоколегированные аустенитные хромоникелевые стали (12Х18Н10Т, 20Х23Н18, 09Х14Н19В2БР и др.) имеют повышенное содержание основных легирующих элементов – хрома и никеля, придающие им соответствующую структуру и свойства: коррозионностойкость, жаростойкость, жаропрочность. Для сокращения высоколегированные аустенитные хромоникелевые стали можно обозначать в соответствии с содержанием основных легирующих элементов цифрами, например 18-8, 25-20 и др. Первая цифра обозначает содержание хрома, вторая – никеля.
Почти все аустенитные хромоникелевые стали обладают высокой пластичностью не только при комнатных и повышенных температурах, но и при низких. Все они имеют высокую коррозионную стойкость в агрессивных средах. Недаром их называют нержавеющими. Рассмотрим диаграмму состояния (рис. 21) системы железо (Fe) – никель (Ni).
Т, 0С Ж
Рис. 21. Структурная диаграмма системы Fe – Ni
Видно, что никель (Ni) является аустенитообразующим элементом и довольно сильным. При содержании Ni > 5% получаем аустенит при всех температурах. При введении в систему Fe - Ni еще и хрома (Cr) картина несколько меняется. Тройная диаграмма Fe - Cr – Ni выглядит примерно так (рис. 22).
Таким образом, стали содержащие >7% Ni, являются аустенитными. Отсутствие превращения аустенита в мартенсит упрощает технологию сварки: нет необходимости в предварительном подогреве и последующей термообработки.
Cr α+γ+σ
Fe
Рис. 22 Структурная диаграмма системы Fe – Ni - Cr
Вместе с тем однофазная аустенитная структура предопределяет ряд технологических трудностей, основными из которых являются:
1.Возникновение склонности к межкристаллитной коррозии (МКК) под действием термического цикла сварки (ТЦС).
|
2.Повышенная склонность к образованию горячих трещин (ГТ) в металле шва и ОШЗ.
Для повышения сопротивляемости образованию горячих трещин в настоящее время применяется:
- Создание двухфазной структуры металла шва (аустенитно-ферритной, аустенитно-карбидной).
- Легирование элементами, снижающими склонность металла шва к горячих трещин при температурах, близких к температуре солидуса.
- Снижение содержания вредных, в том числе ликвирующих, примесей за счет использования чистых сварочных материалов.
Влияние ТЦС на возникновение склонности к МКК и меры ее предотвращения. Обычно аустенитные хромоникелевые стали содержат углерода порядка 0,06 - 0,14 %, а растворимость углерода в хромоникелевом аустените при комнатной температуре не превышает 0,02 %. Следовательно, такие стали представляют собой пересыщенный твердый раствор углерода в хромоникелевом аустените, образующийся в результате быстрого охлаждения.
При нагревании до определенной температуры (400-800 0С) углерод выделяется из твердого раствора и становится химически активным элементом. В данной системе наибольшим средством к углероду обладает хром. Поэтому по границам зерен и вблизи границ образуются карбиды хрома (рис.23).
До нагрева После нагрева
Рис. 23. Структура аустенитной стали до и после нагрева в интервале температур 400 – 800 0С
Эти карбиды имеют сложный состав (CrnСm) и содержат значительное количество хрома. В результате сталь теряет свою пластичность, а сами границы зерен обедняются хромом. Сталь, содержащая меньше 12 % хрома теряет свою способность противостоять агрессивным средам, т.е. подвержена МКК, которая, развиваясь по границам зерен, распространяется в толщину металла. Металл, пораженный МКК, разрушается под действием даже незначительных нагрузок. Скорость выделения карбидов хрома возрастает с ростом температуры и временем выдержки. Соответственно увеличивается и склонность к МКК. Особенно интенсивно карбиды хрома образуются при Т = 680-780 0С (рис. 24).
|
Т
Рис. 24. Схема влияния температуры и времени выдержки на склонность аустенитных сталей к МКК
При температуре ниже 400 0С диффузионная подвижность углерода мала, с повышением температуры она увеличивается. При дальнейшем увеличении температуры имеют место два равновесных процесса – выпадение и повторное растворение углерода, т.к. с увеличением температуры растворимость углерода в аустените увеличивается. При Т > 900 0С карбиды хрома вновь растворяются, углерод переходит в твердый раствор, возникает так называемая «повторная» стойкость к МКК. Понятно, что при V 1 -МКК нет, а при V 2 – МКК есть. Поэтому такие стали необходимо варить на жестких режимах (при малых qn) и без предварительного подогрева. Если можно – даже с принудительным охлаждением.
Основными металлургическими путями предотвращения восприимчивости металла к МКК являются:
1. Увеличение содержания хрома - недостаток этого пути: увеличение себестоимости и появление хрупкости в результате присутствия карбидов.
2. Уменьшение содержания углерода (сложно).
3. Введение стабилизирующих элементов, имеющих большее средство к углероду, чем хром и образующих наиболее устойчивые карбиды (титана, ниобия, тантала).
4. Обеспечение аустенитно-ферритной структуры - необходимое количество ферритной фазы (3-8 %) в аустенитном шве обеспечивается дополнительным легированием сварных швов хромом, кремнием; а иногда молибденом и ванадием.
При этом (при наличии феррита) общая протяженность границ зерен увеличивается, а общее количество карбидов должно сохраниться, кроме того, в двухфазном металле карбиды выделяются по границам ферритных зерен, где содержание хрома выше, чем в аустените. Ферритные зерна, расположенные между аустенитными, работают как шпонки и упрочняют металл. Однако такой способ не применим при избирательной коррозии феррита. Все эти металлургические факторы уменьшают восприимчивость к МКК.
К технологическим фактором, как уже упоминалось, относится уменьшение времени пребывания металла шва и ОШЗ в интервале опасных температур (680-780 0С), что достигается в большинстве случаев уменьшением q n.
Фактическое время пребывания металла шва и ОШЗ в интервале «опасных» температур обозначим τ. При τ > τ кр – межкристаллитная коррозия возникает, а при τ < τ кр – МКК нет.
|
Последнее и есть основное условие, которое необходимо обеспечить при сварке. Из практики (с некоторым запасом) установлено, что если
τ кр/ τ ≥1,45, то МКК не возникает. Время пребывания металла шва и ОШЗ при опасных температурах поддается расчету.
Рассмотрим термический цикл сварки какого – либо участка сварного соединения (рис. 25):
Т
Рис. 25. Термический цикл металла ОШЗ при дуговой сварке
Общее время τ складывается из τ / на ветви нагрева и τ// на ветви охлаждения, т.е. τ = τ / + τ//, но τ / - очень мало и не имеет существенного значения, так как при последующих более высоких температурах наступает повторная стойкость к МКК. Поэтому практически можно считать, что τ = τ//.
С достаточной для практики точностью можно считать, что на участке охлаждения 780-680 0С имеет место некоторая средняя скорость охлаждения (V 0). Из этого треугольника находим τ по формуле:
, (40)
где V 0 – средняя скорость охлаждения в интервале температур 780-680 0С, т.е.
. (41)
Расчет мгновенных скоростей охлаждения при этих температурах производится по формулам Н.Н. Рыкалина.
, (42)
, (43)
где ω – безразмерный критерий, зависящий от величины, обратной безразмерной температуре, определяется по графику Н.Н. Рыкалина (рис. 2). Напомним, что 1/θ определяется по формуле:
, (44)
при Т=7800 имеем θ1 и ω1, Т=6800 имеем θ2 и ω2.
В случае многослойной сварки металл ОШЗ от первого прохода будет нагреваться до опасных температур неоднократно. Поэтому к величине τ от первого прохода нужно добавить τ от последующих проходов. Влияние последующих проходов на пребывание металла первого слоя шва и ОШЗ в опасном интервале температур учитывается расчетом по тем же формулам, но при определении безразмерного критерия ω по графику Н.Н. Рыкалина необходимо учитывать расстояние выполненного слоя от корня шва (рис. 26). Для этого используют зависимости ω= f (1/ θ) построенные Н.Н. Рыкалиным для плоского слоя.
|
a
Рис. 26. К расчету высоты наплавленного слоя
Высота заполнения разделки любым числом проходов определяется решением уравнения вида:
, (45)
где Н – расстояние до плоскости теплоотвода (практически высота предыдущей наплавки).
;
, (46)
F Н – площадь наплавки за 1, 2, 3 и т.д. проходов;
В, С, α - параметры разделки.
Естественно, что первый слой находится в самых невыгодных условиях и расчет надо вести на него.
При многопроходной сварке оценка склонности к МКК на основании результатов предыдущих расчетов производится по неравенству Пальчука (для аустенитных сталей).
МКК нет при К1τ01 + К2Στ0п < τкр,
где τ01 –время пребывания металла околошовной зоны в опасном интервале температур при сварке первого слоя;
τ0п - время пребывания металла первого слоя и ОШЗ в опасном интервале температур под действием ТЦС одного из последующих проходов;
К1 и К2 -эмпирические коэффициенты: К1 =2,1; К2 =1,74.
Таким образом, τкр является характеристическим параметром данной марки аустенитной стали, довольно сильно зависит от содержания углерода в стали и при средних его содержаниях значение τкр невелико. Следовательно, аустенитная хромоникелевая сталь уже при минимальном нагреве имеет большую склонность к МКК.
Второй основной трудностью при сварке аустенитных хромоникелевых сталей является повышенная склонность к образованию горячих трещин в металле шва и ОШЗ.
Горячие трещины, образующиеся в высоколегированных аустенитных швах, во многом отличаются от трещин возникающих в нелегированных и низколегированных швах. Так, например, в противоположность нелегированным и низколегированным швам, аустенитные швы оказываются более склонными к горячим трещинам при повышении температуры свариваемого металла и при увеличении ширины шва.
Общими условиями образования горячих трещин в нелегированных и высоколегированных аустенитных швах являются:
1. Межкристаллитный характер высокотемпературного разрушения металла и связанная с этим необходимость обеспечить его высокотемпературную межкристаллическую пластичность и прочность для трещиноустойчивости.
2. Отрицательное влияние увеличения толщины свариваемой стали и первичных дендритов и кристаллитов.
3. Повышенное содержание элементов и примесей, обладающих меньшей растворимостью в твердом металле, чем в жидком, и снижающих температуру плавления (расширяющих интервал кристаллизации).
Рассмотрим процесс кристаллизации металла шва. На базе подплавленных кристаллов, которые значительно увеличили свои размеры из-за перегрева, начинают расти кристаллиты металла шва. Их преимущественный рост осуществляется в направлении осей ориентации базовых кристаллов (которые имеют разный наклон). Поэтому часть растущих кристаллов, имеющих ограниченный жизненный объем, прекращает свой рост в приграничной области, натыкаясь на другие кристаллиты. Размеры этой приграничной области относительно не велики; кристаллы, росшие в преимущественном направлении, больше не встречают препятствий на своем пути и прорастают до центра шва, т.к. растут свободно. В результате возникает характерная транскристаллитная структура металла шва, свойственная однофазной стали - развитые столбчатые кристаллиты, состоящие из дендритов с неразвившимися осями высших порядков. Отсутствие структурных превращений в твердом состоянии (когда была бы возможна вторичная перекристаллизация кристаллитов) способствует сохранению транскристаллитной структуры. Соответственно и границы кристаллов имеют сквозной характер – протяженность от центра шва до основного металла. При наличии в этих границах достаточного количества легкоплавких эвтектик или малопластичных и малопрочных включений эвтектоидного типа условия образования горячих трещин существенно улучшается.
|
Как известно, такой легкоплавкой эвтектикой может являться сульфид железа (FeS) с Тпл = 980 0С, однако никель обладает большим сродством к сере, чем железо, и образование легкоплавких эвтектик сульфида никеля (NiS) с Тпл = 625 0C более вероятно. В аустенитных хромоникелевых сталях имеется достаточное количество никеля, и склонность к горячим трещинам этих сталей повышается. Поэтому нужно стремиться уменьшить содержание серы до 0,02% и ниже (0,04% S в обычных сталях).
Весьма эффективным путем уменьшения склонности к горячим трещинам в аустенитных швах оказалось введение второй фазы. Эта фаза, введенная в небольших количествах, связывает зерна между собой и разобщает эвтектику. Обычно такой фазой является ферритная. Достаточно 2-5 % ферритной фазы, чтобы уменьшить или вообще устранить склонность к горячим трещинам. Кристаллизация аустенитно-ферритного металла шва вследствие совместного роста δ и γ фаз приводит к образованию более мелкозернистой и дезориентированной структуры с тонкими разветвленными ферритными участками. Кроме того, вредные примеси (Si, S, P) легче растворяются в феррите, дендритная неоднородность аустенита по этим элементам уменьшается, а его межкристаллитная пластичность увеличивается.
Дальнейшее увеличение количества ферритной фазы (свыше 8 %) еще больше уменьшает склонность к образованию горячих трещин. Однако при эксплуатации свыше 300 0С возникает другая опасность – сигматизация феррита (α→σ) в хромоникелевом аустените. Сигматизация феррита (σ -фаза) – это хрупкие интерметаллиды различного состава, и если σ -фазы немного, то это не страшно. Поэтому необходимое количество ферритной фазы обычно обеспечивается на уровне 2-3% (максимум 5%). Естественно, что количество ферритной фазы строго зависит от химического состава, а именно от соотношения элементов ферритизаторов и аустенитизаторов.
Основные ферритообразующие элементы: хром, молибден, ванадий, кремний, вольфрам, алюминий, титан, ниобий. Основные аустенитообразующие элементы: никель, углерод, азот, марганец, медь, кобальт. Приближенная связь между химсоставом металла и его структурой установлена Шеффлером и приводится в виде диаграммы его имени (рис. 27).
Зная ожидаемый химсостав металла шва, можно предвидеть структуру ему, свойственную.
Рис. 27. Диаграмма Шеффлера
Эквивалент никеля и хрома подсчитываются по следующим формулам:
Niэкв= [%Ni] + 30[%C] + 0,5[%Mn] + 26[%N], (47)
Crэкв= [%Cr] + [%Mo] + 1,5[%Si] + 0.5[%Nb] + [%V] + 3.5[%Ti] + 2[%Al] + 1,5[%W]. (48)
Таким образом, выбрав соответствующие электроды, находят химический состав металла шва:
машиностроительный низколегированный сталь сварка
, (49)
где γ – доля участия основного металла в формировании шва;
[Х]МШ, [Х]ОМ, [Х]НМ – содержание какого-либо элемента соответственно в металле шва, основном и наплавленном металле.
Далее находят Niэкв и Crэкв. В результате (рис.27) может получиться:
I – чисто аустенитная структура (зона образования ГТ).
II – аустенитно-ферритная структура со значительным количеством феррита- охрупчивание из-за сигматизации.
III – чистый мартенсит – холодные трещины.
IV – оптимальный состав.
Ограничение содержания феррита (4-5%) вводится только для коррозионостойких сталей, работающих при высоких температурах.
Жаропрочные аустенитные стали при наличии даже незначительного количества феррита теряют свою жаропрочность. Чисто же аустенитная структура склонна к образованию горячих трещин. Поэтому все же приходится идти на создание второй фазы только не ферритной, а карбидной (до 5%). Для этого в состав наплавленного металла вводят некоторое количество элементов – карбидообразователей.
Таким образом мерами, повышающими стойкость аустенитных швов против образования горячих трещин, являются:
1. Измельчение и дезориентирование структуры металла шва.
2. Снижение содержания вредных примесей (P, S, Si).
3. Обеспечение двухфазной аустенитно-ферритной, аустенитно-карбидной или аустенитно-боридной структур (там, где это допустимо).
4. Дополнительное легирование шва элементами, нейтрализующими вредное влияние серы.
К технологическим мерам повышения стойкости металла швов против образования горячих трещин относятся:
1. Обеспечение умеренной qn, чтобы не перегревать сварочную ванну.
2. Применение режимов, обеспечивающих узкий валик (его малую ширину).
3. Продольно частые колебания электрода в пределах длины сварочной ванны.
4. Обязательный зазор при сварке угловых швов.
5. Электромагнитное перемешивание сварочной ванны.
Особенности технологии и техники сварки. Высоколегированные аустенитные стали обладают комплексом положительных свойств. Поэтому одну и ту же марку стали иногда можно использовать для изготовления изделий различного назначения, например коррозионностойких, хладостойких, жаропрочных и т. д. В связи с этим и требования к свойствам сварных соединений будут различными. Это определяет и различную технологию сварки (сварочные материалы, режимы сварки, необходимость последующей термообработки и т. д.), направленную на получение сварного соединения с необходимыми свойствами, определяемыми составом металла шва и его структурой.
Характерные для высоколегированных сталей теплофизические свойства определяют некоторые особенности их сварки. Пониженный коэффициент теплопроводности 25,0 – 33,3 Вт/(м×К) (для углеродистых сталей 37,6 – 41,7 Вт/(м×К)) при равных остальных условиях, значительно изменяет распределение температур в шве и околошовной зоне. В результате одинаковые изотермы в высоколегированных сталях более развиты, чем в углеродистых. Это увеличивает глубину проплавления основного металла, а с учетом повышенного коэффициента теплового расширения возрастает и коробление изделий. Поэтому для уменьшения коробления изделий из высоколегированных сталей следует применять способы и режимы сварки, характеризующиеся максимальной концентрацией тепловой энергии. Примерно в пять раз более высокое, чем у углеродистых сталей удельное электросопротивление обусловливает больший разогрев сварочной проволоки в вылете электрода или металлического стержня для ручной дуговой сварки. При механизированной дуговой сварке следует уменьшать вылет электрода и повышать скорость его подачи. При ручной дуговой сварке уменьшают длину электродов и допустимую плотность сварочного тока.
Ручная дуговая сварка. Сварочные электроды для сварки высоколегированных сталей должны удовлетворять требованиям ГОСТ 10052 – 75, согласно которому электроды для сварки разделены на 2 основные группы: аустенитные и ферритные. Всего ГОСТом предусмотрено 49 типов электродов, в том числе 5 хромистых ферритных.
Все аустенитные электроды обозначаются следующими буквами: ЭА и далее следует цифра, которая означает тип наплавленного металла по содержанию хрома (Cr) и никеля (Ni). Всего имеется 4 основных типа аустенитных электродов.
ЭА – 1 18 – 9
ЭА – 2 25 – 15 обеспечивают такое содержание
ЭА – 3 15 – 25 Cr и Ni в наплавленном металле.
ЭА – 4 15 – 35
Кроме этих символов может быть еще буквы и цифры, показывающие дополнительное легирование наплавленного металла, например, ЭА – 1М2Ф (КТИ – 5, ЦТ – 7). Каждому такому типу может соответствовать одна или несколько марок электродов.
Кроме аустенитных электродов применяются также ферритные электроды, ферритные хромистые: ЭФ – Х13, ЭФ - Х17 и др. Если имеется дополнительное легирование, то в маркировку вводятся соответственно символы: ЭФ – Х11ВМФ.
Применением электродов с фтористо-кальциевым покрытием, уменьшающим угар легирующих элементов, достигается получение шва с необходимым химическим составом и структурами. Уменьшению угара легирующих элементов способствует и поддержание короткой дуги без поперечных колебаний электрода. Это снижает вероятность появления дефектов на поверхности основного металла в результате попадания на него брызг.
Тип покрытия электрода диктует необходимость применения постоянного тока обратной полярности. Тщательная прокалка электродов, режим которой определяется их маркой, способствует уменьшению вероятности образования пор и вызываемых водородом трещин. Некоторые сведения о режимах и выборе электродов для ручной дуговой сварки приведены в табл. 10 и 11.
Таблица 10
Ориентировочные режимы ручной дуговой сварки аустенитных сталей
Толщина материала, мм | Электрод | Величина сварочного тока (А) при положении сварки | |||
Диаметр, мм | Длина, мм | нижнем | Вертикальном | потолочном | |
До 2,0 | 2 | 150 – 200 | 30-50 | - | - |
2,5 – 3,0 | 3 | 225 – 250 | 70 – 100 | 50 – 80 | 45 – 75 |
3,0 – 8,0 | 3 – 4 | 250 – 300 | 85 – 140 | 75 – 130 | 65 – 120 |
8 - 12 | 4 – 5 | 300 – 400 | 85 – 160 | 75 – 150 | 65 - 130 |
Таблица 11
Некоторые марки электродов для сварки высоколегированных сталей
Марка стали | Марка электродов | Тип электродов По ГОСТ 10052-75 | Наплавленный металл, структура |
Коррозионностойкие стали | |||
08Х18Н10, 08Х18Н10Т, 12Х18Н10Т, 08Х18Н12Т, 08Х18Н12Б, 08Х22Н6Т и подобные, работающие в агрессивных средах: к металлу шва предъявляются требования по стойкости к МКК | ЦЛ – 11 | Э – 04Х20Н9 Э – 07Х20Н9 Э – 08Х19Н10Г2Б | Аустенитно-ферритная с 2,5 – 7 % a-фазы |
к металлу шва предъявляются жесткие требования по стойкости к МКК | ОЗЛ – 7 | Э – 02Х19Н9Б | Аустенитно-ферритная с 5 – 10 % a-фазы |
Те же стали, работающие при температурах до 600 0С в жидких агрессивных средах; к металлу шва предъявляются требования по стойкости к МКК | Л – 38М | Э – 02Х19Н9Б | Аустенитно-ферритная с 3 – 5 % a-фазы |
10Х17Н13М2Т, 08Х18Н12Б, 10Х17Н13МЗТ и подобные, работающие при температурах до 700 0С: к металлу шва предъявляются требования по стойкости к МКК | СЛ – 28 | Э – 08Х19Н10Г2МБ Э– 09Х19Н10Г2М2Б | Аустенитно-ферритная с 4 – 5 % a-фазы |
к металлу шва предъявляются жесткие требования по стойкости к МКК | НЖ – 13 | Э– 09Х19Н10Г2М2Б | Аустенитно-ферритная с 4 – 8 % a-фазы |
Сварка под флюсом. Для сварки высоколегированных сталей применяется электродная проволока, которая должна удовлетворять требованием ГОСТ 2246 – 70, согласно которому предусматривается 28 марок высоколегированных проволок в том числе: 7 – хромистых, 20 – хромоникелевых, 1 – никелевая, например, Св – 04Х19Н9 и др.
Главная роль в технологии сварки высоколегированных сталей отводится составу и качеству проволоки, вспомогательная – флюсу. Общие требования к флюсам для сварки высоколегированных сталей аналогичны тем, которые предъявляются к ним и при сварке углеродистых и низколегированных сталей. Специфическим требованием является обеспечение минимального окисляющего действия флюса. Так как в расплавленном металле содержится значительное количество элементов (Cr, Ti, Al) имеющих большее, чем железо, сродство к кислороду, то они будут раскислять металл, уменьшая тем самым степень его легирования. Снижение окисляющего действия флюса достигается за счет отсутствия или малого содержания легковосстанавливающихся окислов – MnO, SiO 2.
Окисление легирующих элементов приводит к уменьшению степени легирования. Но даже не это главное. Окислы легирующих элементов, располагаясь по границам кристаллитов, повышают склонность к образованию как горячих, так и холодных трещин. Поэтому при сварке высоколегированных сталей необходимо применять безокислительные низкокремнистые фторидные и высокоосновные флюсы (табл.12).
Таблица 12
Состав плавленых флюсов для дуговой и электрошлаковой сварки высоколегированных сталей
Марка флюса | Содержание компонентов, % | |||||||
SiO2 | MnO | Ae2O3 | CaO | MgO | FeO | Na2O | CaF2 | |
АН – 22 | 20 | 7,5 | 21 | 13,5 | 13 | ≤1 | 1,5 | 22 |
ФЦЛ – 2 | 36 | - | 6 | 32 | 16 | - | - | 8 |
48-ОФ-6 | ≤4 | ≤0,3 | 23,5 | 19,5 | ≤3 | - | - | 52.5 |
АНФ – 1 | - | - | - | - | - | - | - | 100 |
Кроме плавленых флюсов для сварки высоколегированных сталей применяются керамические (не плавленые) флюсы, построенные по системам:
КС – 1 CaO – CaF2 – TiO2;
К – 2 CaO – MgO – Al2O3 – CaF2;
ФЦ – К Фториды + хлориды + Al2O3.
Замес производят на жидком стекле с плотностью γ =1,35. При этом жидкое стекло составляет 20 % от веса сухой смеси.
Отличие техники сварки высоколегированных сталей от техники сварки обычных низколегированных сталей заключается в уменьшении вылета электрода в 1,5 – 2 раза ввиду повышенного электросопротивления сварочных проволок. Для предупреждения перегрева металла и связанного с этим огрубления структуры, возможности появления трещин и снижения эксплуатационных свойств сварного соединения многослойные швы повышенного сечения рекомендуется сваривать швами небольшого сечения. Это предопределяет использование сварочных проволок диаметром 2 – 3 мм. Аустенитные сварочные проволоки в процессе изготовления сильно наклепываются и имеют высокую жесткость, что затрудняет работу подающих и токоподводящих узлов сварочных установок, снижая срок их службы. Легировать шов можно через флюс или проволоку (табл. 13). Легирование через проволоку более предпочтительно, так как обеспечивает повышенную стабильность металла шва.
Таблица 13
Некоторые марки сварочных проволок для дуговой и электрошлаковой сварки высоколегированных сталей
Марка стали | Марка проволоки |
Коррозионно-стойкие стали | |
08Х18Н10, 08Х18Н10Т,12Х18Н10Т, 08Х18Н12Т, 08Х18Н12Б, 08Х22Н6Т и подобные, работающие в агрессивных средах; к металлу шва предъявляются требования по стойкости к МКК | Св-01Х19Н9 Св-04Х19Н9 Св-06Х19Н9Т Св-07Х18Н9ТЮ |
12Х18Н10Т, 08Х18Н10Т, 08 Х18Н12Т, 08 Х18Н12Б и подобные, работающие при температурах выше 350 0С или в условиях, когда к металлу шва предъявляются требования по стойкости к МКК | Св-07Х19Н10Б Св-05Х20Н9ФБС |
10Х17Н13М3Т, 08Х18Н12Б и подобные; к металлу шва предъявляются требования по стойкости к МКК | Св-08Х19Н10М3Б Св-06Х20Н11М3ТБ |
Жаропрочные стали | |
12Х18Н9 с аустенитно-ферритными швами | Св-04Х19Н9 |
12Х18Н9Б, 08Х18Н12Т и др. с аустенитно-ферритными швами | Св-08Х18Н8Г2Б |
Жаростойкие стали. | |
20Х23Н13, 08Х20Н14С2 и подобные | Св-07Х25Н13 |
20Х23Н18 и подобные, работающие при температурах 900 – 1100 0С | Св-07Х25Н12Г2Т Св-06Х25Н12ТЮ Св-08Х25Н13БТЮ |
ХН35ВЮ, 20Х25Н20С2 и подобные, работающие при температурах до 1200 0С | Св-08ХН50 |
Электрошлаковая сварка. Важнейшая особенность способа – пониженная особенность к образованию горячих трещин, что позволяет получать чисто аустенитные швы без трещин. Это объясняется специфическими особенностями электрошлаковой сварки: малой скоростью перемещения источника нагрева и характером кристаллизации металла сварочной ванны, отсутствием в стыковых соединениях угловых деформаций. Однако малая концентрация нагрева и скорость сварки, повышая длительность пребывания металла шва и ОШЗ при повышенных температурах, увеличивают его перегрев и ширину ОШЗ.
Длительное пребывания металла при температурах 1200 – 1250 0С, приводя к необратимым изменениям в его структуре, снижает прочностные и пластические свойства. Это повышает склонность сварных соединений сталей к локальным (околошовным) разрушениям в процессе термообработки или эксплуатации при повышенных температурах. При сварке коррозионно-стойких сталей перегрев металла в ОШЗ может привести к образованию ножевой коррозии. Для предупреждения этих дефектов необходима термообработка сварных изделий (закалка или стабилизирующий отжиг). Применение неокислительных флюсов, особенно при сварке жаропрочных сталей и сплавов, не исключает угара легкоокисляющихся легирующих элементов (титана, марганца и др.) за счет проникновения кислорода воздуха через поверхность шлаковой ванны. Это вызывает необходимость в ряде случаев защищать поверхность шлаковой ванны путем обдува ее аргоном.
Электрошлаковую сварку можно выполнять проволочными или пластинчатыми электродами (табл. 14). Изделия большой толщины со швами небольшой протяженности целесообразнее сваривать пластинчатым электродом. Изготовление пластинчатого электрода более простое. Но сварка проволокой позволяет в более широких пределах, варьируя режим, изменять форму металлической ванны и характер кристаллизации металла шва, а это один из действенных факторов, обеспечивающих получение швов, свободных от горячих трещин. Однако жесткость сварочной проволоки затрудняет длительную и надежную работу токоподводящих и подающих узлов сварочной аппаратуры.
Таблица 14
Типовой режим электрошлаковой сварки высоколегированных сталей
Тол- щина металла, мм | Электрод, мм | Марка флюса | Глубина шлаковой ванны, мм | Скорость подачи электрода, м/ч | Сила тока, А | Напряжение, В | Зазор, мм |
100 100 200 200 | Проволока, диам. 3 Пластина 10х100 Пластина 12х200 Пластина 12х200 | АНФ-7 АНФ-7 АНФ-1 АНФ-6 | 25 - 35 15 - 20 15 - 20 15 - 20 | 330 2,4 1,9 1,9 | 600 - 800 1200 - 1300 3500 - 4000 1800 - 2000 | 40 - 42 24 - 26 22 - 24 26 - 28 | 28 - 32 28 - 32 38 - 40 38 - 40 |
Сварка в защитных газах. В качестве защитных используют инертные (аргон, гелий) и активные (углекислый газ) газы, а также различные смеси инертных или активных газов. Этот метод сварки по сравнению с рассмотренными выше имеет ряд существенных преимуществ. Его можно использовать для соединения металлов широкого диапазона толщин - от десятых долей до десятков миллиметров. При сварке толстых металлов в некоторых случаях этот способ сварки может конкурировать с электрошлаковой сваркой.
Применение инертных газов существенно повышает стабильность дуги. Значительное различие теплофизических свойств защитных газов и применение их смесей, изменяя тепловую эффективность дуги и условия ввода тепла в свариваемые кромки, значительно расширяют технологические возможности дуги. При сварке в инертных газах наблюдается минимальный угар легирующих элементов, что важно при сварке высоколегированных сталей. При сварке неплавящимся электродом в защитных газах возможности изменения химического состава металла шва более ограничены по сравнению с другими способами сварки и возможны за счет изменения состава сварочной (присадочной) проволоки или изменения доли участия основного металла в образовании металла шва (режим сварки), когда составы основного и электродного металлов значительно различаются.
При сварке плавящимся электродом появляется возможность изменения характера металлургических взаимодействий за счет значительного изменения состава защитной атмосферы, например создания окислительных условий в дуге, путем применения смеси газов, содержащих кислород, углекислый газ и др. Этим способом можно выполнять сварку в различных пространственных положениях, что делает ее целесообразной в монтажных условиях по сравнению с ручной дуговой сваркой покрытыми электродами.
Неплавящимся (вольфрамовым) электродом сваривают в инертных газах или их смесях. Для сварки высоколегированных сталей используют аргон высшего или 1-го сорта по ГОСТ 10157 - 73. Обычно сварку вольфрамовым электродом технически и экономически целесообразно использовать при сварке для металлов толщиной до 7 мм (при толщине до 1,5 мм применение других способов дуговой сварки практически невозможно из-за образования прожогов). Однако в некоторых случаях, например, при сварке неповоротных стыков труб, сварку вольфрамовым электродом применяют на сталях и больших толщин.
Высокое качество формирования обратного валика вызывает необходимость применения этого способа и при сварке корневых швов в разделках при изготовлении ответственных толстостенных изделий. В зависимости от толщины стали и конструкции сварного соединения сварку выполняют с присадочным материалом или без него вручную с использованием специальных горелок или автоматически. Сварку ведут на постоянном токе прямой полярности. Исключение составляют стали и сплавы с повышенным содержанием алюминия, когда для разрушения поверхностной пленки окислов, богатой алюминием, следует применять переменный ток.
Сварку можно выполнять непрерывно горящей или импульсной дугой. Импульсная дуга благодаря особенностям ее теплового воздействия позволяет уменьшить протяженность околошовной зоны и коробление свариваемых кромок, а также сваривать металл малой толщины при хорошем формировании шва. Особенности кристаллизации металла сварочной ванны при этом способе сварки способствуют дезориентации структуры, уменьшая вероятность образования горячих трещин. Однако эта же особенность может способствовать образованию околошовных надрывов при сварке высоколегированных сталей. Для улучшения формирования корня шва используют поддув газа, а при сварке корневых швов на металле повышенных толщин - специальные расплавляющиеся вставки.
При сварке погруженной дугой особенности процесса, определяющие увеличение доли теплоты, идущей на расплавление основного металла, позволяют без разделки кромок за один проход сваривать металл повышенной толщины. Однако уменьшение концентрации нагрева приводит к термическому циклу сварки, сходному с термическим циклом при электрошлаковой сварке. В результате расширяется зона термического влияния и возникает опасность перегрева в ней основного металла, т. е. ней возможны те же дефекты, что и при электрошлаковой сварке.
Для высоколегированных сталей применяться и плазменная сварка. Большое ее преимущество - малый расход защитного газа. Получение плазменных струй различного сеч
|
|
Биохимия спиртового брожения: Основу технологии получения пива составляет спиртовое брожение, - при котором сахар превращается...
Индивидуальные и групповые автопоилки: для животных. Схемы и конструкции...
Адаптации растений и животных к жизни в горах: Большое значение для жизни организмов в горах имеют степень расчленения, крутизна и экспозиционные различия склонов...
Археология об основании Рима: Новые раскопки проясняют и такой острый дискуссионный вопрос, как дата самого возникновения Рима...
© cyberpedia.su 2017-2024 - Не является автором материалов. Исключительное право сохранено за автором текста.
Если вы не хотите, чтобы данный материал был у нас на сайте, перейдите по ссылке: Нарушение авторских прав. Мы поможем в написании вашей работы!