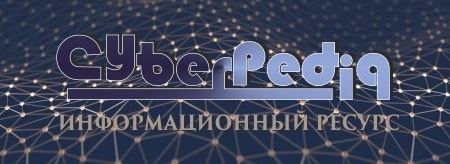
Организация стока поверхностных вод: Наибольшее количество влаги на земном шаре испаряется с поверхности морей и океанов (88‰)...
Биохимия спиртового брожения: Основу технологии получения пива составляет спиртовое брожение, - при котором сахар превращается...
Топ:
Оценка эффективности инструментов коммуникационной политики: Внешние коммуникации - обмен информацией между организацией и её внешней средой...
Устройство и оснащение процедурного кабинета: Решающая роль в обеспечении правильного лечения пациентов отводится процедурной медсестре...
Процедура выполнения команд. Рабочий цикл процессора: Функционирование процессора в основном состоит из повторяющихся рабочих циклов, каждый из которых соответствует...
Интересное:
Аура как энергетическое поле: многослойную ауру человека можно представить себе подобным...
Искусственное повышение поверхности территории: Варианты искусственного повышения поверхности территории необходимо выбирать на основе анализа следующих характеристик защищаемой территории...
Национальное богатство страны и его составляющие: для оценки элементов национального богатства используются...
Дисциплины:
![]() |
![]() |
5.00
из
|
Заказать работу |
|
|
В соответствии с рассмотренными выше требованиями при сварке разнородных перлитных сталей целесообразно использовать сварочные материалы, близкие по составу к менее легированной стали. Так как технологическая прочность перлитных швов снижается с повышением их легирования, то удовлетворение этого требования позволяет успешнее обеспечивать отсутствие в сварных швах трещин и других дефектов. В данном случае не приходится опасаться появления нежелательных структур в слоях шва, примыкающих к более легированной стали, в связи с отсутствием резкого изменения свойств в пределах возможного изменения легирования.
При большой разнице в содержании легирующих элементов в свариваемых сталях могут применяться присадочные материалы промежуточного легирования (табл. 22).
При ручной дуговой сварке следует использовать электроды с основным покрытием, обеспечивающие высокую стойкость металла сварного шва против кристаллизационных трещин и его повышенную пластичность. Применение электродов с рутиловым и целлюлозным покрытиями не рекомендуется в связи с опасностью образования трещин в слоях шва, примыкающих к более легированной стали.
Таблица 22
Рекомендации по выбору сварочных материалов для соединений из разнородных перлитных сталей
Марки свариваемых сталей | Метод сварки | Сварочные материалы | Режим термообработки | |
Ст.3, 10, 20 и др. низкоуглеродистые |
15ХМ, 12МХ, 20ХМЛ, 30ХМА | Ручная дуговая Покрытыми Электродами | Электроды типа Э-42А-Ф |
Без отпуска или отпуск при температуре 630 – 650 0С |
Под флюсом | Проволока Св-08А | |||
Конструкционные низколегированные повышенной прочности
| Ручная дуговая Покрытыми Электродами | Электроды типа Э-42А-Ф | ||
В углекислом Газе | Проволока Св-08ГС или Св-08Г2С | |||
15ХМ, 12МХ, 20ХМЛ | 12Х1МФ, 15Х1М1Ф, Х5М, Х5МФ | Ручная дуговая покрытыми электродами | Электроды типа Э-ХМ |
Отпуск при температуре 630 – 650 0С |
Под флюсом | Проволока Св-10ХМ | |||
В углекислом газе | Проволока Св-08ХГСМА |
Технологические режимы сварки и температуру предварительного подогрева желательно выбирать близкими к требуемым к более легированной стали. При сварке массивных изделий в отдельных случаях целесообразно снижать температуру предварительного подогрева или совсем его исключить путем предварительной облицовки кромок со стороны более легированной стали. После облицовки должен производиться отпуск при температуре 720 0С, а после выполнения основного шва лишь при 620-650 0С. По условию восстановления пластических свойств металла закаленных при сварке отдельных зон сварного соединения, температуру отпуска желательно выбирать для более легированной стали. Однако в связи с разным содержанием в свариваемых сталях энергичных карбидообразователей, по условию снижения до минимума диффузионных прослоек температура отпуска должна быть снижена. Точно также и достаточно эффективное снятие остаточных сварочных напряжений достигается уже при отпуске по режиму для менее легированной стали.
Исходя из необходимости учета одновременного всех этих факторов, температура отпуска обычно выбирается средней между требуемой для однородных сварных соединений обеих марок сталей.
Для сварных узлов, предназначенных к эксплуатации при высоких температурах, необходимо особо остановиться на возможной предельной рабочей температуре Тпред комбинированного стыка. При относительно небольшой разнице в легировании она может выбираться близкой к предельной для менее легированной стали. Поэтому в сварных соединениях углеродистой стали с хромомолибденовой, содержащей до 1% Cr и 0,5% Mo, максимальная рабочая температура определяется углеродистой сталью и составляет 450 0С. При этих температурах можно не опасаться развития диффузионных прослоек в зоне сплавления хромомолибденовой стали со швом. Точно также сварные соединения хромомолибденовой стали с хромомолибденованадиевой сталью или 5%-ной хромистой сталью могут эксплуатироваться при температурах до 500 0С в соответствии с условиями работы изделий из менее легированной стали. Механические свойства и длительная прочность таких соединений находятся на уровне свойств однородных соединений менее прочной стали.
|
При большой разнице в составе свариваемых сталей и, прежде всего в содержании карбидообразователей, за счет подбора металла шва не удается полностью подавить диффузию углерода в зоне сплавления, приводящую к появлению в ней нежелательных прослоек. Поэтому для таких сварных соединений необходимо ограничивать рабочую температуру изделия. Так для сварных соединений углеродистых сталей с хромомолибденованадиевой сталью и 5% хромистой предельная рабочая температура должна быть снижена до 350 0С. В подобных соединениях следует уменьшать и температуру отпуска. При необходимости работы этих соединений при более высоких температурах можно рекомендовать облицовку кромок со стороны легированной стали или введение переходников.
В сварных соединениях трубопроводов в этих случаях наиболее рациональным следует считать введение переходника из стали 15ХМ (20ХМ). В начале следует приварить патрубок электродами типа Э-ХМ к трубе из хромомолибденованадиевой стали и произвести отпуск стыка при 680-700 0С. Затем сваривается замыкающий стык патрубка с трубой из углеродистой стали. При толщине стенки трубы до 10 мм указанный стык можно не подвергать отпуску. При большей толщине стенки трубы стык должен быть отпущен при 630-650 0С. При облицовке сначала производится наплавка высотой 6 мм электродами типа Э-ХМ и затем электродами типа Э-42А, после облицовки - отпуск при Т=700-720 0С.
Соединения высокохромистых мартенситных, ферритных и ферритно-аустенитных сталей. Выбор сварочных материалов для сварных соединений разнородных высокохромистых сталей определяется, прежде всего, требованиями получения сварных швов без трещин и отсутствием в этих сталях хрупких составляющих (табл. 23). При сварке этих сталей вследствие высокого содержания в основном металле энергичного карбидообразователя - хрома заметно снижается возможность появления диффузионных прослоек в зоне сплавления.
|
Если свариваются 12% - ные хромистые мартенситные или мартенситно-ферритные стали разного легирования, то могут применяться сварочные материалы для любой из свариваемых сталей. При автоматической сварке под флюсом или в СО2 обычно используются в этом случае сварочная проволока типа 08Х14ГТ. Режим подогрева следует выбирать по требуемому для более закаливающейся стали, имеющей, как правило, повышенное содержание углерода. Температура предварительного подогрева в зависимости от содержания в стали углерода может колебаться в пределах 200-400 0С.
После сварки обязательным является отпуск при 700-750 0С. Если толщина свариваемых элементов превосходит 30 мм, то желательно без полного охлаждения изделия (не ниже 100-150 0С) помещать его в термическую печь для нагрева под отпуск.
При сварке 12% - ных хромистых мартенситных сталей с высокохромистыми ферритными или ферритно-аустенитными сталями наиболее целесообразно использовать сварочные материалы ферритно-аустенитного класса. Преимуществом этих материалов по сравнению с ферритными является малая склонность металла сварного шва к росту зерна и высокая его пластичность в исходном состоянии после сварки. Температура предварительного подогрева таких соединений должна выбираться по режиму 12% - ной хромистой стали. После сварки необходим отпуск при 700-750 0С. В ходе термообработки следует принимать меры к ускоренному охлаждению изделия во избежание появления эффекта 475-градусной хрупкости. Проведение отпуска заметно повышает коррозионную стойкость сварных соединений, прежде всего в районе ОШЗ ферритно-аустенитной стали. При сварке указанного сочетания сталей применяются также аустенитные сварочные материалы. В этом случае температура предварительного подогрева может быть снижена на 100-150 0С против требуемой для высокохромистой стали.
Таблица 23
Рекомендации по выбору сварочных материалов для соединений из разнородных высокохромистых мартенситных, ферритных и ферритно-аустенитных сталей
|
Условия работы | Марки свариваемых сталей | Метод сварки | Сварочные материалы | Режим термообработки | |
Температура до 600 0С |
12 % -ные хромистые коррозионно-стойкие 12Х13, 20Х13, 08Х14 |
12 % -ные хромистые жаропрочные 15Х11МФ, 15Х12ВМФ, 18Х11МФБ 15Х11В2МФ | Ручная дуговая покрытыми электродами | Электроды типов: Э-Х13, ЭФ-Х11МНФ, ЭФ-Х11ВМНФ ЭФ-Х12ВМНФ |
Отпуск при температуре 700-750 0С |
Под флюсом | Проволока Св-06Х14 | ||||
В углекислом газе | Проволока Св-08Х14ГНТ | ||||
Коррозионная среда и Температура До 600 0С | Высокохромистые ферритные и ферритно-аустенитные 15Х25Т, 12Х21Н5Т и др. | Ручная дуговая покрытыми электродами | Электроды типов ЭАФ-1МФ ЭА-2, ЭА-2Г6 | Отпуск при температуре 700 – 750 0С (ускор. охлажд) | |
Под флюсом | Св-06Х24Н6ТАФМ, Св-06Х21Н5Т | ||||
Коррозионная среда и температура до 300 0С | Высокохромистые ферритные Х17Т, 15Х25Т, Х28АН и др. | Высокохромистые ферритно-аустенитные Х25Н5ТМФ, 12Х21Н5Т и др. | Ручная дуговая покрытыми электродами | Электроды типа ЭАФ-1ФМ, ЭА-2, ЭА-2Г6 | Отпуск при температуре 700 – 750 0С |
При сварке высокохромистых ферритных сталей с ферритно-аустенитной сталью могут применяться те же сварочные материалы, что и в ранее рассмотренном случае сварки 12% -ных хромистых сталей с высокохромистыми ферритными. Температура предварительного подогрева во время сварки обычно в пределах 130-180 0С. При необходимости по условиям обеспечения требуемого уровня свойств и стойкости против МКК температура отпуска может быть повышена до 800-850 0С.
Соединения аустенитных и ферритно-аустенитных сталей. При выборе электродных и присадочных материалов для сварки разнородных аустенитных сталей необходимо, прежде всего, учитывать склонность аустенитных швов наиболее распространенных составов к образованию трещин при сравнительно небольшом отклонении легирования от оптимального. Процессы диффузии углерода в зоне сплавления для этих соединений, так же как и соединений высокохромистых сталей, в большинстве случаев могут не учитываться.
Для предварительной оценки пригодности сварочных материалов целесообразно использовать деление аустенитных сталей по свариваемости на две группы. К первой группе относятся наиболее распространенные аустенитные стали, у которых содержание основного легирующего элемента - хрома - превышает или близко к содержанию никеля. Эти стали могут свариваться наиболее технологичными аустенитно-ферритными электродными материалами. Вторая группа охватывает стали с повышенным запасом аустенитности, у которых содержание никеля превосходит содержание хрома и которые аустенитно-ферритными сварочными материалами не свариваются.
|
Установим принципы выбора сварочных материалов для возможного сочетания аустенитных и аустенитно-ферритных сталей. Если свариваются стали разного легирования 1-ой группы (например, 1Х18Н10Т и 1Х16Н14М2), то могут использоваться аустенитно-ферритные сварочные материалы, применяемые для обеих сталей. В этом случае состав шва по содержанию основных легирующих элементов будет сравнительно мало отличаться от наплавленного металла Х19Н12М2Ф, поэтому при обычных степенях проплавления основного металла во время сварки можно обеспечить в шве аустенитно-ферритную структуру.
Выбор легирования сварочных материалов определяется условиями работы конструкции и требованиями к ее термической обработке. Если сталь 1-ой группы имеет повышенное содержание никеля (Ni) и отношение Cr/Ni в ней приближается к единице, то сварку корневых слоев следует производить электродами с повышенным содержанием ферритной фазы. Аустенитно-ферритные электроды могут применяться и для сварки стали Х23Н18, которая раньше сваривалась лишь аустенитными электродами легирования близкого к основному металлу (табл.24).
Если свариваются стали 2-ой группы разного легирования, то аустенитно-ферритные электродные материалы применять не следует, так как при относительно небольшом дополнительном легировании шва никелем он будет иметь однофазную аустенитную структуру и будет склонен к трещинообразованию. В данном случае могут использоваться сварочные материалы, обеспечивающие однофазную аустенитную или аустенитно-карбидную структуру наплавленного металла при дополнительном легировании его элементами, способствующими повышению стойкости шва против трещин. При этом необходимо учитывать возможность образования трещин в переходных слоях шва. Так, электроды типа ЭА-3М6 нежелательно применять при сварке аустенитных сталей, содержащих свыше 0,5% ниобия из-за опасности образования трещин в участках шва, содержащих ниобий, за счет проплавления основного металла.
Таблица 24
Рекомендации по выбору сварочных материалов для соединений из разнородных аустенитных и ферритно-аустенитных сталей
Условия работы | Марки свариваемых сталей | Метод сварки | Сварочные материалы | Структурное Состояние шва | |
Неагрессивные среды |
12Х18Н10Т (запас аустенитности Ni/Cr < 1) |
12Х18Y12Т, 10Х17Н13М2Т, 10Х17Н13М3Т, 08Х17Н16М3Т | Ручная дуговая покрытыми электродами | Электроды типа ЭА-1 |
Аустенитно-ферритный |
Под флюсом | Проволока Св-04Х19Н9 | ||||
В углекислом газе | Проволока Св-04Х19Н9С2 | ||||
Ручная дуговая покрытыми электродами | Электроды типа ЭА-1Б ЭА-2, |
То же | |||
Под флюсом | Св-05Х19Н9Ф3С2 Св-08Х19Н9Ф2С2 | ||||
Температуры свыше 300 0С | 12Х18Н12Т, 20Х25Н20С2, 1Х16Н14В2БР | Ручная дуговая покрытыми электродами | Электроды типа ЭА-1Б |
То же | |
1Х16Н13М2Б, 20Х23Н18, Х25Н13 | Ручная дуговая покрытыми электродами | Электроды типа ЭА-1М2Ф | |||
Температуры до 700 0С | 09Х14Н18М2БР (запас аустенитности Ni/Cr > 1) | 1Х15Н35В3Т, Х15Н35В5ТР
| Ручная дуговая покрытыми электродами | Электроды типа ЭА-4В3Б2 | Аустенитно-карбидный |
Под флюсом | Проволока 06Х19Н35Г7В7М3Т | Аустенитный | |||
Коррозионная среды | 12Х18Н10Т, 10Х17Н13М2Т | 12Х21Н5Т, Х25Н5ТМФ | Ручная дуговая покрытыми электродами | Электроды типа ЭАФ-1МФ | Ферритно-аустенитный |
Высокие температуры
|
12Х18Н9Т | 09Х14Н18В2БР | Ручная дуговая покрытыми электродами | Электроды типа ЭА-4В3Б2, Э-2Х14Н18Н18Б | Аустенитно-карбидный |
Х25Н35В3Т, Х20Н18Т2Ю | Ручная дуговая покрытыми электродами | Электроды типа ЭА-4ВБ2, ЭА-3М6 | Аустенитно-карбидный |
При заметном отличии в химическом составе свариваемых сталей, например при сварке аустенитной стали на железной основе с никелевым сплавом, необходимо проверить свойства переходных составов шва в слоях, примыкающих к разнородной стали или сплаву, и оценить их склонность к образованию трещин. При сравнительно не большой жесткости конструкции можно использовать в подобных соединениях электроды типа ЭА-3М6. Сварку корневого слоя, в котором проплавление наибольшее, следует выполнять электродами типа ЭА-3М9 повышенной стойкости против трещинообразования.
При сварке аустенитной стали типа 1Х18Н9 со сплавами на никелевой основе рекомендуется применять никельхромомолибденовые присадочные материалы, содержащие до 30% молибдена (Mo). Эти рекомендации основываются на результатах оценки склонности к образованию трещин металла однослойного шва при аргонодуговой сварке листов толщиной 2,5 мм. Если использовать для этой цели ручную дуговую сварку, то в качестве сварочных материалов могут быть применены электроды марки ИМЕТ-10. При сварке листов или др. деталей толщиной больше 5 мм электродами марки ИМЕТ-10 следует выполнять лишь корневой шов. Для заполнения остальных слоев более рационально применять электроды с меньшим содержанием Mo (до 15%). В качестве таких можно рекомендовать электроды марки ЦТ-28.
В сварных соединениях сталей 1-ой группы со 2-ой более предпочтительно применение аустенитных или аустенитно-карбидных электродных материалов, чем аустенитно-ферритных. При использовании аустенитно-ферритных электродных материалов корневой слой шва, а также слои, примыкающие к стали с высоким содержанием никеля, будут обогащаться им за счет проплавления. В связи с этим структура указанных слоев будет уже не двухфазная аустенитно-ферритная, а однофазная аустенитная со склонностью к образованию трещин. Поэтому, например, в сварных соединениях стали Х15Н35В3Т со сталью 1Х16Н14М2 наиболее целесообразно использовать электроды типа ЭА-3М6, а не аустенитно-ферритные электроды.
Выбор термообработки сварных конструкций из разнородных аустенитных сталей определяется маркой стали, типом конструкции и условиями ее работы. При сварке термически не упрочняемых сталей, отсутствие требований по снятию напряжений и работе изделия в интервале умеренных температур термообработка может не производиться. Если по условиям изготовления или эксплуатации остаточные сварочные напряжения должны быть сняты, то достаточна стабилизация при 800 - 850 0С. Для конструкций, работающих при высоких температурах, предпочтительным видом термообработки сварного изделия является аустинитизация при 1100 - 1150 0С. При требовании стойкости против МКК температура аустинитизации не должна быть выше 1050 0С.
Если в сварном соединении используются термически упрочняемые (дисперсионно-твердеющие) стали, то термообработка после сварки является обязательной для восстановления свойств ОШЗ. Выбор режима термообработки в этом случае производится обычно по требуемому для дисперсионно-твердеющих сталей.
При сварке аустенитных сталей 1-ой группы с ферритно-аустенитными сталями выбор сварочных материалов определяется, прежде всего, требованиями к термообработке сварного узла. Так, например, в соединениях стали 1Х18Н10Т со сталью Х25Н5ТМФ высокая технологическая прочность сварных швов достигается как при использовании аустенитно-ферритных, так и ферритно-аустенитных электродов. Однако применение аустенитно-ферритных электродов допустимо только для сварных соединений, не подвергаемых после сварки стабилизации для снятия остаточных сварочных напряжений, т.к. подобная термообработка приводит к значительному охрупчиванию аустенитно-ферритных швов с повышенным содержанием ферритной фазы.
В отличие от этого стабилизация при 800 - 850 0С (с ускоренным охлаждением) рассматриваемых сварных соединений с ферритно-аустенитными швами значительного охрупчивания не вызывает. Поэтому целесообразно при сварке данного сочетания сталей применять ферритно-аустенитные сварочные материалы.
|
|
Автоматическое растормаживание колес: Тормозные устройства колес предназначены для уменьшения длины пробега и улучшения маневрирования ВС при...
Организация стока поверхностных вод: Наибольшее количество влаги на земном шаре испаряется с поверхности морей и океанов (88‰)...
Состав сооружений: решетки и песколовки: Решетки – это первое устройство в схеме очистных сооружений. Они представляют...
Индивидуальные очистные сооружения: К классу индивидуальных очистных сооружений относят сооружения, пропускная способность которых...
© cyberpedia.su 2017-2024 - Не является автором материалов. Исключительное право сохранено за автором текста.
Если вы не хотите, чтобы данный материал был у нас на сайте, перейдите по ссылке: Нарушение авторских прав. Мы поможем в написании вашей работы!