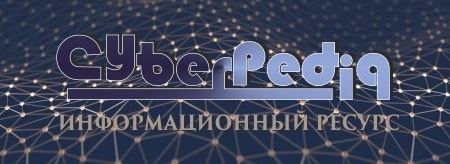
Эмиссия газов от очистных сооружений канализации: В последние годы внимание мирового сообщества сосредоточено на экологических проблемах...
Индивидуальные и групповые автопоилки: для животных. Схемы и конструкции...
Топ:
История развития методов оптимизации: теорема Куна-Таккера, метод Лагранжа, роль выпуклости в оптимизации...
Оценка эффективности инструментов коммуникационной политики: Внешние коммуникации - обмен информацией между организацией и её внешней средой...
Характеристика АТП и сварочно-жестяницкого участка: Транспорт в настоящее время является одной из важнейших отраслей народного...
Интересное:
Отражение на счетах бухгалтерского учета процесса приобретения: Процесс заготовления представляет систему экономических событий, включающих приобретение организацией у поставщиков сырья...
Лечение прогрессирующих форм рака: Одним из наиболее важных достижений экспериментальной химиотерапии опухолей, начатой в 60-х и реализованной в 70-х годах, является...
Как мы говорим и как мы слушаем: общение можно сравнить с огромным зонтиком, под которым скрыто все...
Дисциплины:
![]() |
![]() |
5.00
из
|
Заказать работу |
|
|
Особенности свариваемости
Стали этой группы содержат небольшое количество углерода, а также 3-4 % легирующих элементов, но среди этих элементов обязательно присутствует молибден (Мо), молибден – хром (Cr), молибден – хром –ванадий (V). В таких сталях Мо и Cr повышают температуру их рекристаллизации и, соответственно, жаропрочность. Для обеспечения стабильности микроструктуры вводят V, ниобий (Nb), бор (B).
Особую группу образуют стали с бором или стали низколегированные молибденом, молибденом и хромом или никелем (Ni). Содержание бора в стали обычно не превышает 0,004-0,006%, а его основное влияние заключается в стабилизации аустенита при непрерывном распаде. Таким образом, стали, подвергнутые нормализации, имеют бейнитную структуру или бейнитомартенситную, а после нормализации и отпуска достигается мелкая ферритокарбидная (сорбитная) смесь. Низколегированная сталь с молибденом не обладает высокой прочностью (600-700 МПа), однако ей присущи хорошие пластические свойства и свариваемость. Эта сталь достаточно устойчива против образования холодных трещин при сварке, однако при толщине листов более 20-25 мм требуется предварительный подогрев.
Ко второй группе бористых сталей относится низколегированная хромомолибденовая сталь, прочностные свойства которой более высокие (700-1000 МПа), и при ее сварке необходимо применять ограничивающие условия (предварительный подогрев 220-260 0С, ограничение погонной энергии).
Все приведенные выше стали имеют достаточно высокую ударную вязкость даже при - 40 0С. Поскольку механические свойства стали стабильны и при повышенных температурах, хромомолибденовые бористые стали можно применять для изготовления паровых котлов, работающих при температуре до 480 0С.
|
Так как в околошовной зоне при сварке приведенных сталей образуется мартенсит или смесь твердых структур распада, чувствительных к воздействию водорода, то при сварке хромомолибденовых и никельхромомолибденовых сталей следует применять предварительный подогрев и проверять содержание диффузионного водорода в металле сварного шва или применять последующий нагрев после сварки. Обеспечение пластических свойства зоны термического влияния (ЗТВ) не вызывает проблем, хотя трудности могут возникнуть при повышенном содержании углерода и примесей. При использовании повышенной погонной энергии на участке ЗТВ, нагретом до температуры около точки АС1, можно также наблюдать определенное снижение твердости, т.е. снижение прочностных свойств не более чем на 15 МПа. В результате отпуска при температурах ниже точки АС1 пластические свойства ЗТВ улучшаются. Однако температура отпуска ЗТВ должна быть ниже температуры отпуска основного металла.
Для сварки бористых сталей применяют легированные электроды и проволоку. Для сварки сталей с молибденом и бором применяют сварочные материалы, содержащие марганец и молибден или марганец и никель, а в случае сварки стали с хромом, молибденом и бором или с никелем, хромом, молибденом и бором - комплексно легированные сварочные материалы (Mn-Ni-Cr, Mn-Ni-Cr-Mo), которые обеспечивают соответствующий уровень прочности и переходные температуры. Учитывая образование структур, чувствительных к водороду и к повышенным остаточным сварочным напряжениям, необходимо в процессе сварки контролировать содержание водорода или применять предварительный подогрев, а также сопутствующий нагрев. Наконец, следует отметить, что легирование стали снижает у нее температуру мартенситного превращения, что необходимо учитывать при определении температурного режима сварки.
К низколегированным конструкционным относятся и стали следующих типов: 0,5% Cr - 0,5% Mo; 1,25% Cr - 0,5% Mo; 2,25% Cr – 1% Mo. Эти стали отличаются тем, что присутствие хрома и мoлибдена повышает их прокаливаемость, повышает температуру точки АС1, несколько понижает температуру точки АС3, а температура точки мартенситного превращения приближается к 400 0С. В основном стали поставляют в состоянии после нормализации и отпуска или после улучшения. Следовательно, микроструктура основного металла сорбитная, с мелкими цементитными карбидами или карбидами молибдена (Mo2C) и частично карбидами хрома (Cr7C3). При повышенном содержании молибдена (до 1%) сталь при отпуске может оказаться в температурной области вторичного твердения в результате выделения когерентного карбида (Mo2C) или комплексного карбида (Fe4Mo2C). Температурная область возможного вторичного твердения находится в интервале 560 - 600 0С. Увеличение стабильности аустенита при непрерывном распаде приводит к тому, что в ЗТВ, как и в металле сварного шва, увеличивается содержание остаточного аустенита. Если эти стали используются в сварных конструкциях, то они, как правило, имеют сравнительно низкое содержание углерода (0,16-0,18%).
|
При изготовлении корпусов сосудов высокого давления часто применяют стали, микролегированные ванадием (до 0,15%) с целью обеспечения прочностных свойств после отпуска или отжига. Для конструкций, работающих при низких температурах, стали легируют никелем. При сварке низколегированных конструкционных свариваемых сталей применяют низкий предварительный подогрев до 150-240 0С, причем тепловой режим сварки должен включать требования к температуре промежуточных слоев (100-150 0С) и способу охлаждения или последующего подогрева. В зависимости от требуемых прочностных свойств и требуемой температуры перехода металла сварного шва в хрупкое состояние применяют низколегированные сварочные материалы следующих систем легирования: Mn-Mo; Mn-Ni-Mo; Mn-Cr-Mo.
Особую группу низколегированных сталей образуют стали, применяемыев энергетическом машиностроении для изготовления котельного оборудования, работающего под нагрузкой при температуре до 565 0С. Это стали марок 16М, 15ХМА, 20 ХМА, 20 ХМФА и др.
К этим сталям предъявляют следующие требования: они должны иметь достаточно высокое сопротивление ползучести (длительную прочность) и стойкость против поверхностного окисления. На кинетику ползучести стали при высоких температурах, кроме основного химсостава влияют структура и субструктура стали. Кроме процессов выделения, из которых особо важной является дисперсность выделений, большое значение имеет и состояние дислокационной субструктуры металла. Ползучесть связана с механизмом движения дислокаций и с диффузией вакансий.
|
С точки зрения длительной прочности стали можно разделить на несколько групп. Следует отметить, что область температур, при которых наблюдается ползучесть, начинается с 200 0С. В связи с этим различают:
1. Нелегированные углеродистые марганцевые стали, которые с точки зрения длительной прочности можно применять максимум до температуры 400 0С. В то же время их сопротивление окислению достаточно высокое при температуре до 520 0С.
2.Низколегированные хромомолибденовые (Cr-Mo), хромомолибденованадиевые (Cr-Mo-V), хромомолибденованадийвольфрамовые (Cr-Mo-V-W), хромованадиевые (Cr-V)стали, температурная область применения которых ограничена 580 0С и которые имеют повышенное содержание углерода.
3. Высоколегированные стали, например, с 13% Cr, и аустенитные стали, у которых рабочая температура может быть выше 620 0С.
Основным типом низколегированных жаропрочных сталей являются хромомолибденовые стали, содержащие до 2,25% Cr и 1% Mo. Однако наиболее часто в сталях этого типа содержание хрома колеблется в пределах 0,5-1%, содержание молибдена 0,4-0,6%. Хром способствует не только увеличению жаропрочности, но и жаростойкости стали. Наличие молибдена в стали, с одной стороны, упрочняет твердый раствор a - Fe, а с другой - стабилизирует цементит. В хромомолибденовых сталях карбидная фаза выделяется не только в виде легированного цементита Ме3С, но и в виде пластин карбида Cr7C3 и игл карбида Mo2C. Возможно выделение карбидов Mе23C6 по границам первичных зерен. Карбиды Mo2C или Fe4Mo2C могут быть причиной вторичного твердения, а следовательно, и охрупчивания ЗТВ. Эти проблемы могут иметь значение и для металла сварного шва в случае применения присадочного материала с более высоким содержанием молибдена (1%). В результате сегрегации распределение молибдена в сварном шве неравномерно, и выделение карбида Mo2C может быть более четко выраженным.
|
Хромомолибденовые стали имеют рабочую температуру Тр, ограниченную значениями 500-520 0С. При более высоких Тр твердый раствор a - Fe не обладает достаточной прочностью, которую можно обеспечить, например, благодаря наличию большого количества мелкодисперсных выделений карбида ванадия. Хромомолибденованадиевые стали кроме 1 % Cr и 0,6 % Mo содержат еще 0,20-0,35 % V. Ванадий с углеродом образуют весьма стабильный карбид V4C3, который отличается тем, что размер его выделений является функцией температуры и практически не зависит от времени выдержки. Свариваемость хромомолибденованадиевых сталей не хуже свариваемости сталей предыдущей группы. Присутствие ванадия повышает прокаливаемость сталей, но основная проблема при многослойной сварке этих сталей заключается в том, что трудно контролировать увеличение твердости в ОШЗ в связи с тем, что именно здесь большая часть карбидов ванадия растворяется в матрице при тепловом воздействии процесса сварки на металл ОШЗ, а при выполнении последующего слоя металла сварного шва здесь снова выделяется карбид ванадия, т.е. происходит вторичное твердение.
Поскольку стали, относящиеся к группе жаропрочных, имеют повышенное содержание углерода и содержат легирующие элементы, то при сварке они склонны к образованию трещин, вызываемых водородом, и в связи с этим необходимо строго контролировать технологию сварки. Стали требуют предварительный подогрев, а также последующий нагрев или медленное охлаждение в асбестовой изоляции. Температура предварительного подогрева Тпп сравнительно высокая и может превышать 300 0С. В связи с пониженной температурой точки мартенситного превращения стали, которая может приближаться к 340-360 0С, необходимо следить за тем, чтобы Тпп или температура промежуточных слоев не превышала ее.
Определенную группу низколегированных жаропрочных сталей образуют стали, предназначенные для изготовления корпусов атомных реакторов и их узлов. Хотя эти конструкции работают при температуре ниже температурной области классической ползучести (320 – 380 0С), однако многие показатели у них общие. С точки зрения развития металлургии эти стали можно разделить на три группы:
1. Стали первого поколения, имеющие предел текучести ниже 500 МПа, из которых изготовлена большая часть корпусов реакторов, работающих в настоящее время (22К). Эти стали отличаются высокой пластичностью и ударной вязкостью и низкой температурой перехода в хрупкое состояние. В связи с относительно низкими прочностными свойствами сосуды высокого давления имеют большую толщину стенки (60 – 250 мм) и большую массу.
|
2. Стали второго поколения имеют повышенную прочность (предел текучести в улучшенном состоянии 500 – 900 МПа). Эти стали возникли на базе сталей первого поколения в результате совершенствования последних с помощью таких легирующих добавок, которые позволяют подвергать стали термообработке – улучшению, или за счет более высокого общего легирования (15Х2МФА, 15Х2М4, 25Х2МА, 10ГН2МФА). Большинство современных сосудов высокого давления изготавливают из этих бейнитных или сорбитных сталей с хорошими пластическими свойствами и радиационной устойчивостью.
3. К сталям третьего поколения относятся перспективные стали, которые можно применять для изготовления реакторов большой мощности. Это стали с пределом текучести свыше 1000 Мпа, улучшенные, с высоким требованием к технологии производства и контролю (0,12% С, 0,9% Mn, 0,35% Si, 0,01% S, 0,01% P, 5,25% Ni, 0,7% Cr, 0,65% Mo, 0,1% V). Поскольку эти стали должны иметь высокую чистоту, небольшое количество дефектов, хорошие пластические свойства и высокое сопротивление радиационному разрушению, большинство плавок производится в электрических печах с последующим вакуумированием.
Так как большинство сосудов высокого давления реакторов работает в области Т = 300 – 350 0С, то обязательным является определение прочностных свойств при этих температурах. При этом следует считаться с возможностью понижения предела текучести примерно на 40 МПа и временного сопротивления разрыву на 70 – 100 МПа по сравнению с их значениями при комнатной температуре. В связи с этим большое внимание уделяется термообработке поковок, листов проката или всего сосуда высокого давления. Основной тип термообработки – нормализация с последующим отпуском. При обработке листов повышенной толщины часто применяют ускоренное охлаждение от температуры нормализации водяным душем или водяным паром, что приводит к измельчению структуры главным образом в центре листа и способствует повышению прочностных свойств. При использовании низколегированных листов в последнее время все чаще между нормализацией и отпуском применяют отжиг в интервале температур АС1 – АС3, который позволяет получить дальнейшее измельчение зерен и улучшить пластические свойства. Температура нормализации изменяется в пределах 880 – 930 0С в зависимости от химического состава стали, в основном от содержания в ней углерода, а температура отпуска – в пределах 600 – 660 0С. При улучшении в качестве закалочной среды применяют масло или воду, а поковки или листы закаливают в штампах. Стали, чувствительные к образованию трещин, подвергают визуальному контролю при 350 – 150 0С еще в процессе охлаждения. Благодаря низкому содержанию примесей, безупречным пластическим свойствам, гомогенности и пониженному содержанию углерода свариваемость сталей, используемых для корпусов реакторов, хорошая. Однако из-за большой толщины и сложной формы корпуса сосуда эти стали требуют ограничения технологических параметров процесса сварки. В основном применяют механизированные способы сварки и электрошлаковую, если позволяет химический состав материала листа.
Температура предварительного подогрева изменяется в пределах 250 – 350 0С, при этом более высокие температуры нежелательны из-за опасности появления горячих трещин. Погонная энергия сварки хотя и не ограничивается, однако при некоторых способах (АСФ, ЭШС) существует оптимальный диапазон ее значений (25 – 30 кДж/см). Термообработка после сварки в основном заключается в отпуске при Т = 580 – 660 0С для снижения уровня внутренних напряжений. В промежутке между сваркой и отпуском температура сварного изделия не должна быть ниже 180 – 150 0С. К тому же термообработка позволяет улучшить микроструктуру металла ЗТВ и сварного шва и свести к минимуму вероятность образования холодных трещин.
Микроструктура сталей для корпусов реакторов – ферритно-перлитная или ферритокарбидная для менее прочных сталей (1-е поколение), если они были подвергнуты нормализации. После термического улучшения их структура ферритнобейнитная, или представляет собой смесь продуктов распада (сорбитизированная), т.е. смесь карбидов и феррита с выделениями доэвтектоидного феррита. В структуре легированных сталей 2-го поколения доэвтектоидный феррит обычно не наблюдается.
В связи с тем, что у большинства сосудов высокого давления внутренняя поверхность наплавлена или плакирована аустенитным коррозионно-стойким металлом, эти стали должны иметь и высокое сопротивление образованию несплошностей при наплавке, особенно образованию трещин отпуска. Кроме того, одним из важнейших критериев выбора материала для корпуса реактора является обеспечение его радиационной стойкости. Поэтому в стали должно быть ограниченно содержание меди (до 0,15 %) и кобальта (до 0,02 %).
|
|
Механическое удерживание земляных масс: Механическое удерживание земляных масс на склоне обеспечивают контрфорсными сооружениями различных конструкций...
Особенности сооружения опор в сложных условиях: Сооружение ВЛ в районах с суровыми климатическими и тяжелыми геологическими условиями...
Типы оградительных сооружений в морском порту: По расположению оградительных сооружений в плане различают волноломы, обе оконечности...
Опора деревянной одностоечной и способы укрепление угловых опор: Опоры ВЛ - конструкции, предназначенные для поддерживания проводов на необходимой высоте над землей, водой...
© cyberpedia.su 2017-2024 - Не является автором материалов. Исключительное право сохранено за автором текста.
Если вы не хотите, чтобы данный материал был у нас на сайте, перейдите по ссылке: Нарушение авторских прав. Мы поможем в написании вашей работы!