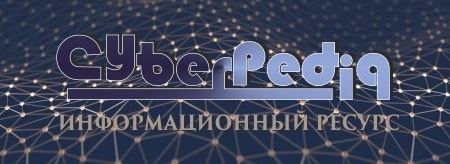
Двойное оплодотворение у цветковых растений: Оплодотворение - это процесс слияния мужской и женской половых клеток с образованием зиготы...
Типы оградительных сооружений в морском порту: По расположению оградительных сооружений в плане различают волноломы, обе оконечности...
Топ:
Организация стока поверхностных вод: Наибольшее количество влаги на земном шаре испаряется с поверхности морей и океанов...
Эволюция кровеносной системы позвоночных животных: Биологическая эволюция – необратимый процесс исторического развития живой природы...
Характеристика АТП и сварочно-жестяницкого участка: Транспорт в настоящее время является одной из важнейших отраслей народного...
Интересное:
Принципы управления денежными потоками: одним из методов контроля за состоянием денежной наличности является...
Искусственное повышение поверхности территории: Варианты искусственного повышения поверхности территории необходимо выбирать на основе анализа следующих характеристик защищаемой территории...
Что нужно делать при лейкемии: Прежде всего, необходимо выяснить, не страдаете ли вы каким-либо душевным недугом...
Дисциплины:
![]() |
![]() |
5.00
из
|
Заказать работу |
|
|
Введение
Эффективность работы на речном и морском флоте в значительной мере определяется техническим уровнем и надёжностью его механизмов, в т. ч. и валопроводов.
Технический уровень и надёжность механизмов, в свою очередь значительно зависит от качества монтажа. Задача монтажа - установка на судах механизмов согласно координатам чертежа при отсутствии деформации и напряжений в узлах и деталях.
Механизмы различаются разнообразием конструкций и требованиями к точности монтажа, которые вытекают из необходимости сохранения стендовой сборки при монтаже на судно.
При монтаже механизмов, в стеснённых условиях судна, используют ограниченное количество оснастки и приспособлений, которые не могут полностью механизировать ручные операции, особенно связанные с креплением и перемещением механизмов внутри судна.
Основным направлением снижения трудоемкости монтажа является повышение технологичности в целом и особенно узлов крепления механизмов.
Целью данного дипломного проекта является разработка мероприятий для снижения трудоёмкости и повышения качества работ по монтажу валопровода и винто-рулевого комплекса судна путём внедрения современных технологий.
Краткая техническая характеристика судна
Тип судна
Пассажирский четырех палубный теплоход “Виссарион Белинский” постройки 1979 г. (Германия, верфь Бойценбург). Район плавания по классификации Речного Регистра РФ “О”, ограничен проход через Ладожское и Онежское озера при максимальной длине волны 2,5Ч25 м. Остойчивость и спасательные средства соответствуют классу Регистра “М”.
Главные размеры и характерные данные
|
Габаритная длина судна - 125 м;
Дл. между перпендикулярами - 118 м;
Ширина по мидель-шпангоуту - 16 м;
Габаритная ширина судна - 16,7 м;
Высота борта - 4,5 м;
Осадка - 2,76 м;
Высота надводного борта - 1,14 м;
Габаритная высота судна - 13,2 м;
Водоизмещение - 3545 т3;
Пассажировместимость - 360 чел.;
Количество команды - 84 чел.;
Скорость судна при работе двигателей: Среднего ≈16км/ч. Бортовых ≈22км/ч. Всех трех ≈26км/ч.
Для привода судна предусмотрены 3 четырехтактных реверсивных судовых двигателя с наддувом “Г70-5” отечественного производства, мощностью 883 кв./ч. и числом оборотов 350об/мин. Двигатели, самортизированные на фундаменте, соединены при помощи эластичной муфты ВЭМ 1100Ч190 с валопроводом. Три пятилопастные гребные винты (ВФШ) диаметром 1,85м.
Для выработки электроэнергии напряжением 380 - 220В установлены 4 дизель - генератора (каждый по 720 э.л.с., и один аварийный марки 6VD26/20AL - I SLK)
Описание конструкции валопровода
На судне установлены три главных двигателя модели 6ЧРН 36/45 (Г-70-5) с двумя системами валопровода, бортовые валопроводы состоят из гребного вала, промежуточного вала и упорного вала, в валопроводе на диаметральной плоскости отсутствует промежуточный вал.
Гребной винт пятилопастной, диаметром 1850 мм, стальная отливка. На данном проекте судна установлены два двигателе правого и один левого вращения, гребные винты соответствуют исполнению двигателей.
Конструктивное исполнение валопровода
Упорный вал соединён с маховиком с помощью призонных болтов, с другой стороны он соединен муфтой с валом проставышем. Упорный вал вложен в литой стальной корпус упорного подшипника. Упорные усилия, движущие судно вперёд воспринимаются самоустанавливающимся аксильным роликовым подшипником, а упорные усилия, продвигающие судно назад воспринимаются самоустанавливающимся роликовым подшипником. Упорный подшипник смазывается маслом.
После упорного вала следует промежуточный вал (только на бортовых валопроводах), он соединяет гребной и упорный валы. Соединение выполнено через муфту. Промежуточный вал опирается на опорный подшипник.
|
Опорные подшипники - самоустанавливающиеся роликовые подшипники. Подшипники укрепляются на валу специальными зажимными гильзами.
Гребной вал - установлен в дейдвудные подшипники (резинометаллические). Гребной винт - установлен на гребной вал, на поверхности с конусностью 1:10, имеет шпоночную фиксацию и закреплен гайкой.
Недостатки существующих конструкций и предложения по их модернизации
Цельнолитой гребной винт
Рассматриваемый гребной винт является цельнолитым. Цельнолитые гребные винты имеют конструкцию, трудно поддающуюся обработке на станках из-за сложности криволинейных поверхностей лопастей. Обработку лопастей винтов при изготовлении осуществляют пневматическими зубилами и шлифовальными кругами.
Тяжёлые условия труда, значительный объем ручных работ при изготовлении цельнолитых гребных винтов привели к необходимости изменения их конструкции на сборную, состоящую из ступицы и лопастей. Такая конструкция винта является более технологичной, что позволило исключить ручные работы по обработке составляющих элементов винта.
В сборных гребных винтах, предназначенных для работы на судах речного флота, лопасти имеют фрикционное соединение со ступицей. Надёжность крепления лопасти со ступицей обеспечивают за счёт сил трения, которые возникают при сборке комля лопасти со ступицей с расчётным натягом.
От разворота лопасти дополнительно фиксируют фланцем специальной формы.
Сборные винты отличаются высокой ремонтопригодностью, которая заключается в возможности замены лопасти винта без подъёма судна из воды. Сборку лопастей со ступицей осуществляют путём нагрева ступицы, охлаждением лопастей или комбинированным способом - нагревом охватывающей детали и охлаждением охватываемой. Разборку прессового соединения лопастей со ступицей производят подачей масла под высоким давлением под торец комля лопасти через специальное отверстие.
Дефектация валопровода
В процессе дефектации определяют техническое состояние валопровода в целом, а также износы и повреждения сборочных единиц и деталей. Действительные износы сравнивают с нормативными значениями и дают заключения о возможности дальнейшей эксплуатации или необходимости проведения ремонта.
|
При разборке валопровода проверяют состояние центровки концевых валов − гребного и коленчатого вала оптическим методом или измерением изломов и смещений на фланцевых соединениях валов. Если расцентровка концевых валов находится в заданных пределах, то валопровод центруют плавным искривлением его оси в пределах допустимых нагрузок на подшипники концевых валов и напряжений в валах. В противном случае изменяют положение главного двигателя или производят эксцентричную расточку дейдвудных втулок.
Зазоры между антифрикционным покрытием дейдвудных втулок и шейками гребных или дейдвудных валов, а также масляные зазоры в опорных подшипниках измеряют до разборки валопровода. Значения предельно допустимых зазоров в дейдвудных втулках и втулках кронштейнов приведены в таблице 6.2
Таблица 6.2 Зазоры в дейдвудных втулках и втулках кронштейнов гребных валов
Наружный диаметр Облицовок гребного вала, мм | Установочный ![]() |
| |
В дейдвудной трубе | Во втулке кронштейна | ||
50-100 101-150 151-200 200-250 | 1,10-1,30 1,20-1,40 1,30-1,50 1,40-1,60 | 2,8 3,0 3,3 4,0 | 4,0 4,0 5,0 6,0 |
Предельно допустимые масляные зазоры в опорных подшипниках колеблются от 0,35 до 0,5 мм для диаметров от 100 до 220 мм.
Во время дефектации тщательно осматривают все соединения валов с целью определения ослабления посадки полумуфт на валах, а также правильности прилегания шпонок по пазам.
Перед ремонтом упорного подшипника производят измерения осевых зазоров между упорными подушками и упорным диском вала, а также замер износа баббита на упорных подушках. Состояние поверхности антифрикционного слоя оценивают визуально.
После разборки все валы валопровода подвергают наружному осмотру, обмерам шеек и облицовок, проверке биения и погиби, а также контролю физическими неразрушающими средствами.
Рабочие шейки и облицовки валов измеряют микрометрическим инструментом по наружному диаметру в двух взаимно перпендикулярных направлениях, не менее чем в трех сечениях по длине каждой носовой шейки или облицовки и пяти сечениях − для каждой кормовой.
|
По результатам измерений рассчитывают отклонения от округлости и цилиндричности для промежуточных (в числителе) и гребных валов (в знаменателе).
Таблица 6.3 Допустимые износы рабочих шеек промежуточных валов и облицовок гребных валов
Диаметр шейки (облицовки) | Отклонения от округлости | Отклонения от цилиндричности | ||
При ремонте | В эксплуатации | При ремонте | В эксплуатации | |
120-180 | 0,02/0,02 | 0,25/0,30 | 0,02/0,03 | 0,25/0,40 |
180-260 | 0,02/0,03 | 0,25/0,40 | 0,03/0,04 | 0,30/0,50 |
Погибь валов и биение шеек (облицовок) проверяют с помощью индикаторов часового типа при закреплении валов в центрах токарного станка. Погибь валов допускают до 0,5 мм на метр длины, биение валов при проверке по фланцам не должно превышать на каждые 100 мм диаметра фланца: торцевое − 0,03 мм, радиальное − 0,01 мм.
Трещины на промежуточных валах определяют визуальным осмотром, а на гребных - магнитопорошковым методом, переносными или передвижными приборами. Шпоночные пазы с этой целью контролируют вихретоковым методом с использованием накладных датчиков карандашного типа.
Износ антифрикционного покрытия опорных подшипников определяют микрометрическими измерениями. Трещины и выкрашивание антифрикционного слоя обнаруживают визуальным осмотром.
Дейдвудные трубы осматривают на месте. Толщину стенок при этом проверяют с помощью ультразвуковых толщиномеров или путем сверления контрольных отверстий. При уменьшении толщины стенки в нескольких местах до 30% построечной дейдвудную трубу заменяют.
Ремонт валов
Ремонт валов при износе рабочих шеек и конусов, предназначенных для посадки соединительных полумуфт, состоит в шлифовании или протачивании изношенных поверхностей.
Для обточки валы устанавливают на токарном станке с использованием люнетов. Положение их выверяют при помощи индикаторов часового типа, биение вала не должно превышать 0,05 мм.
Обрабатывают валы резцами с пластинками твердого сплава с обычным углом заточки при следующих режимах тонкого точения: скорость резания 100 - 200 м/мин, подача S до 0,01 мм/об, глубина резания t=0,05 ч 0,30 мм.
Рабочие шейки и конусы валов восстанавливают наплавкой. Допускается наплавка валов из углеродистой стали при содержании углерода в ней до 0,45 % и износе не более 1,5 мм. Для уменьшения напряжений вал в районе начала наплавки подогревают до 393 - 423 К.
При восстановлении рабочих шеек валов автоматическую и полуавтоматическую наплавку производят при закреплении валов на токарном станке наложение валиков на шейку по винтовой линии.
Восстановление изношенных конусов валов производят с наложением валиков вдоль оси вала до его цилиндрической части. Аналогичным путем наплавляют стенки изношенных шпоночных пазов.
|
После остывания конус вала протачивают по контршаблону, снятому с шаблона конуса полумуфты или конуса гребного винта в случае ремонта гребного вала.
Обработку шпоночных пазов производят на горизонтально-фрезерных станках дисковой или пальчиковой фрезой. При обработке шпоночных пазов для ликвидации концентрации напряжений у дна паза должны быть обеспечены радиусы закруглений (от 1,0 мм до 6,0 мм). Восстановление шпоночных пазов (при смятии более 25 % длины и 30 % глубины паза) можно производить без наплавки только механической обработкой - строганием или фрезерованием с увеличением ширины паза до 10 % от номинальной. В этом случае шпоночные пазы в ступице гребного винта или полумуфты также разделывают на соответствующую ширину. Допускается установка ступенчатой шпонки с разницей по ширине верхней и нижней части не более 5 % номинальной ее ширины.
Трещины, возникшие на валах во время эксплуатации, создают значительную концентрацию напряжений, и является недопустимыми дефектами. Их устраняют механическим способом или заваркой. Отдельные незначительные трещины на цилиндрической части вала или в шпоночных пазах удаляют, вырубая металл в районе трещины и разделывая вырубленные места для обеспечения плавных переходов к прилегающим поверхностям вала. При многочисленных поверхностных трещинах выполняют обтачивание участка вала в районе трещин при условии сохранения его прочностных размеров и обеспечивая плавный переход от меньшего диаметра проточки к остальной поверхности вала.
В отдельных случаях, если глубина трещин не превышает 5 % и длина - не более 10 % диаметра вала, их устраняют с помощью сварки. Перед заваркой металл в районе трещины тщательно вырубают до полного ее удаления.
Погибь валов, полученную в период эксплуатации судна, устраняют правкой. На судоремонтных предприятиях применяют следующие методы правки валов: в холодном состоянии за счет наклепа; в холодном состоянии наклепом, с выгибом в сторону, обратную вогнутости; местным нагревом с последующим отжигом; круговым местным нагревом и применением механических усилий.
Правка валов в холодном состоянии наклепом может применятся для валов при содержании углерода в материале не более 0,45 %, суммарного количества легирующих присадок не более 2,5 %, при стреле прогиба до 0,5 мм на 1 м вала. Вал устанавливают на токарном станке на двух люнетах, размечают место на вогнутой части вала и при помощи чекана наклепывают поверхность вала в этом месте. Под действием созданных напряжений происходит правка вала. Правка считается законченной, если биение вала не превышает 0,08 мм.
Правку валов в холодном состоянии с выгибом их в сторону, обратную деформации, а также правку местным нагревом с последующим отжигом производят в тех случаях, когда напряжения в материале вала не превышают предел текучести материала вала более чем на 15 %. При больших деформациях (напряжениях) валы правят круговым нагревом с последующим приложением механических усилий.
Рис 6.3 Правка вала.
Возможность правки вала этим способом определяют следующим образом. Прогиб ft вала, при котором в нем начинают возникать пластические деформации, определяют зависимостью
=
где - предел текучести материала вала, МПа;
W - момент сопротивления сечения вала, м3;
L - расстояние между опорами, м;
E - модуль упругости материала, МПа;
I - момент инерции сечения вала, м4. По измеренной стреле f прогиба вала рассчитывают напряжения изгиба по формуле
f / WL2
Полученные расчетом напряжения изгиба сравнивают с пределом текучести материала и, если их значение не превышает предел текучести материала более чем на 15 %, то можно применить правку вала по второму способу. Для этого деформированный вал устанавливают на токарном станке или в приспособлении. Гидравлическим домкратом в месте максимальной погиби вал выгибают в сторону вогнутости на значение f1 определяемое расчетом
=
где a и b - расстояния от опор до приложения усилия.
После достижения заданной стрелки выгиба вал обстукивают медной кувалдой в районе выгиба по выпуклой стороне и в таком положении выдерживают в течение нескольких часов (от 2 до 4 ч.) в зависимости от значения выгиба. После снятия нагрузки биение вала не должно превышать 0,08 мм.
Требуемую грузоподъемность Р домкрата определяют по формуле
Р=
Правка местным нагревом с последующим отжигом заключается в том, что место наибольшего выгиба вала, установленного на станке или приспособлении, нагревают до температуры 773ч823 К через вырез в листовом асбесте, покрывающем вал на длине не менее одного диаметра.
При нагревании металл стремится расширится. Однако соседние холодные участки вала препятствуют такому расширению и в металле возникают напряжения сжатия. Дальнейшее нагревание приводит к росту этих напряжений и при достижении ими значения предела текучести материала происходит местная пластическая деформация. Охлаждение вала приводит к появлению напряжений растяжения в холодной зоне, за счет которых и происходит устранение деформации вала.
После окончания правки вал в месте нагрева необходимо отжечь для снятия внутренних напряжений. С этой целью вал нагревают до температуры 600 К со скоростью не выше 150 К в час и выдерживают в течение двух часов. В месте нагрева вал покрывают асбестовым листом и в этом положении он остывает до температуры наружного воздуха.
Ремонт облицовок
Ремонт облицовок гребных и других валов заключается в их обточке на ремонтный размер или замене. Обточку облицовки на ремонтный размер производят при достижении предельного износа по всей рабочей поверхности или по отдельным участкам (менее 50 % ее расчетной толщины). При износе облицовок по всей рабочей поверхности более 50 % расчетной толщины, а также при ослаблении посадки на валу облицовки заменяют.
Перед посадкой на вал новую облицовку подвергают гидравлическим испытаниям на давление 0,15 МПа и нагреву до температуры 553 - 573 К. Температуру нагрева контролируют термокарандашами, термопарами или измерением внутреннего диаметра с помощью штихмасса. Качество посадки определяют по чистому звуку при обстукивании облицовки слесарным молотком после ее полного остывания. После установки на вал облицовку обрабатывают до заданного размера на токарном станке с обеспечением шероховатости поверхности Ra≤0.40 мкм, радиального биения не более 0,15 мм/м, и округлости не более 0,02 мм.
Ремонт опорных подшипников
Ремонт опорных подшипников, залитых баббитом, при уменьшении толщины антифрикционного слоя до 2 мм при диаметре до 150 мм, до 3 мм при диаметре от 150 до 200 мм, а также при наличии в нем трещин или отслоения заливки от основы, осуществляют, как правило, перезаливкой. После перезаливки вкладыши подшипников предварительно растачивают для снятия тепловых напряжений, возникших при заливке.
Надежность работы вкладышей во многом определяется качеством заливки, в частности, отсутствием отслоения баббита от основы. Поэтому после предварительной механической обработки их обязательно подвергают ультразвуковому контролю. Проверку ведут непосредственным сканированием пьезоэлектрическим преобразователем поверхности вкладыша или с использованием иммерсионного варианта, при котором ультразвуковые колебания вводят в тело вкладыша через слой воды. Контроль вкладышей подшипников в иммерсионной ванне проводят на специальной полуавтоматической установке. Прозвучивают подшипники на такой установке эхо-способом при наличии одного пьезопреобразователя или теневым способом двумя датчиками: излучающим и приемным.
Результаты контроля фиксируют на диаграммной ленте. В соответствии с ОСТ 24.067.40-84 любые отслоения баббита от основы в подшипниках не допустимы.
Перед окончательной обработкой внутренней поверхности вкладыши пригоняют по постелям на краску. Пригонку считают удовлетворительной при наличии одного пятна краски на 100 мм2 поверхности. После пригонки вкладыши собирают с корпусом и направляют на расточку.
При изменении положения на фундаменте подшипники после расточки окончательно пригоняют в цехе по шейкам своих валов на краску. Подшипники считают удовлетворительно пригнанными, если число пятен краски составляет не менее двух на 100 мм2 площади. Если подшипники не изменяют положения относительно фундамента, то после сборки вкладышей с корпусами производят их разметку на месте (судне).
Ремонт упорных подшипников в основном аналогичен ремонту опорных. Исключение составляют упорные подушки (сегменты). Упорные подушки являются ответственной деталью подшипника, так как воспринимают осевой упор гребного винта. Поэтому при их ремонте к качеству соединения баббита с корпусом подушки предъявляются высокие требования. Так же как и вкладыши опорных подшипников, упорные подушки подвергают ультразвуковому контролю на отслоение баббита. После перезаливки и станочной обработки упорные подушки тщательным образом подгоняют по высоте шабрением слоя баббита с точностью 0,02 мм. Это требование необходимо для того, чтобы упорный вал опирался при вращении на все подушки.
Рулевое устройство
Восстановление баллера руля
Для восстановления баллера на судоремонтных предприятиях используется автоматическая наплавка под слоем флюса.
На рис.8.2 представлена схема установки для автоматической наплавки под слоем флюса крупногабаритных деталей. Деталь закрепляется в центрах станка или патроне и центре и получает вращение с определённой скоростью от шпинделя. На суппорте станка монтируется устройство для подачи сварочной проволоки и бункер с флюсом.
Рис.8.3. Схема установки для автоматической наплавки детали:
1 - патрон станка;
2 - подающий механизм;
- катушка с проволокой;
- бункер для флюса;
- деталь;
- задний центр.
Расплавление металла детали и сварочной проволоки осуществляется за счёт тепла электрической дуги, возникающей между деталью и проволокой. Режим наплавки: ток 120 - 300А, напряжение 25 - 28В.
Проволока поступает в зону горения дуги с заданной скоростью за счет подающего механизма, а флюс - самотеком.
Суппорт станка перемещается относительно детали с определенной скоростью, и наплавка поверхности детали осуществляется по винтовой линии.
Основное время наплавки для цилиндрических деталей определяется на основании следующей зависимости:
t0 = П d l s p / I н, ч
где d - диаметр детали, мм; l - длина наплавки, мм; s - толщина слоя, мм; p - плотность метала, г/ мм3. Полуавтоматическая наплавка осуществляется, в среде защитных газов. В качестве защитного газа используют углекислоту или аргон. При наплавке в среде защитных газов обеспечивается хорошая видимость зоны горения дуги. В качестве материала для наплавки широко используется электродная проволока и лента. Одним из недостатков наплавки в среде защитных газов является сравнительно большая (15%) потеря металла за счет разбрызгивания.
При ремонте деталей наплавкой, наряду с восстановлением изношенной поверхности до номинальных размеров, целесообразно обеспечить её упрочнение, т.е. повышение износостойкости, а в отдельных случаях - и усталостной прочности, что приводит к увеличению срока службы деталей.
Износостойкость деталей, восстанавливаемых наплавкой под флюсом, обеспечивают легированием наносимого металла или введением во флюс специальных присадок, при использовании других способов наплавок упрочнение достигается применением специальных материалов или металлических порошков.
Процесс восстановления деталей наплавкой является более производительным по сравнению с другими методами и зависит от способа наплавки. Электродуговая наплавка в среде защитных газов имеет производительность выше, чем автоматическая наплавка под слоем флюса. Ещё более высокой производительностью обладают плазменный и лазерный способы за счёт использования мощных источников тепла.
При наплавке изменяется структура основного металла, возникают большие остаточные напряжения, что может приводить к деформации ремонтируемых деталей. Это обстоятельство является существенным недостатком метода восстановления, ограничивающим его использование для ремонта деталей небольших размеров.
Наибольшей глубиной проплавления обладает автоматическая наплавка под слоем флюса. Поэтому область её использования - восстановление крупногабаритных деталей с износом более 2 мм(валов линии валопровода, баллеров рулей и т.д.).
Во время автоматической наплавки на поверхность детали за один проход наносят достаточно толстые слои металла, при этом обеспечиваются стабильные качества и производительность процесса.
Расчет насадки лопастей
Гарантированное соединение с натягом лопасти со ступицей обеспечивается расчётом натяга в узле комель лопасти-гжезло ступицы. Новая конструкция не нуждается в деталях крепления лопасти к ступице. Отпадает необходимость изготовления шпилек, гаек и т.п., что является ещё одним преимуществом предлагаемой конструкции.
Исходные данные:
Диаметр комля лопасти d = 250 мм
Диаметр ступицы винта D = 335 мм
Длина сопрягаемой поверхности l = 50 мм
Натяг определяется по следующей эмпирической формуле:
,
где d - диаметр комля лопасти.
мм
Значение контактного давления на сопрягаемые поверхности, МПа
,
где С1 С2 - коэффициенты жёсткости деталей; Е1 Е2 - модули упругости материала 2,06*105 МПа; Кз - коэффициент запаса, 3.
Коэффициент жёсткости материала вычисляется по формулам:
;
;
где d0 - внутренний диаметр полного конца лопасти, м; (d0=0, т.к. сечение лопасти сплошное); μ - коэффициент Пуассона; С1 =0,7 С2 =3,8
Па
Момент трения на сопрягаемых поверхностях зависит от геометрических размеров поверхности трения и контактных давлений на эти поверхности.
Мтр=πd2lfP,
где l - длина сопрягаемых поверхностей, м; f - коэффициент трения.
Мтр = 3,14*0,3352*0,05*0,15*250070 =1870 Нм
Проверить эксплутационную надёжность крепления лопасти по конструктивно-технологическим параметрам, как при ремонте, модернизации, так и изготовлении новых гребных винтов можно по условиям:
Мтр≥fP
Описание конструкции
Конструкция для заводки гребного вала с гребным винтом состоит из следующих элементов:
платформ (верхней и нижней);
тележек с домкратом;
электродвигателя для перемещения тележек с домкратом;
лестницы для подъёма рабочих. Нижняя платформа перемещается по рельсам стапеля на колёсах, соединённых между сбой осями. На этой платформе находятся тележки с домкратами, с помощью которых можно перемещать верхнюю платформу в вертикальном и горизонтальном направлении при заводке гребного вала в дейдвудную трубу.
На верхней платформе находятся ещё две тележки с домкратами, на которые укладывается гребной вал. Заводка вала осуществляется с помощью этих тележек, которые перемещаются по направляющей верхней платформы с помощью электродвигателя. Домкраты служат для дополнительного перемещения вала вверх и вниз.
При расчёте конструкций для заводки гребного вала в сборе с гребным винтом проверяем прочность осей колёс и рассчитываем домкрат верхней платформы.
Расчёт прочности осей колёс
Исходные данные:
Масса конструкции М = 2512 кг;
Нагрузка на ось Р = М = 314 кг;
Длина оси λ = 2,5 м;
Материал оси Сталь 35
Рис. 10.1 Расчётная схема, эпюры сил и моментов.
Крутящий момент определён по следующей формуле, исходя из расчётной схемы (рис.10.1):
Мкр=Р
Мкр=314* =392,5 кг*м
Условие прочности:
;
Момент сопротивления;
;
где d - диаметр оси, мм.
Из предыдущих формул получаем выражение для расчёта диаметра оси:
;
мм.
Диаметр оси при соблюдении условия прочности, должен быть не менее 23,2 мм, принимаем 25 мм. Момент сопротивления в данном случае:
мм3
Из условия прочности:
МПа
,8 МПа ≤ 320 МПа - условия соблюдены.
Расчёт домкрата
Исходные данные:
Масса гребного вала Мвала = 61800 Н;
Масса гребного винта Мвинта = 48150 Н;
Количество домкратов n = 12;
Материала винта Сталь 35;
Материал гайки Сталь 3.
Рис.10.2. Схема нагружения домкрата.
Определим грузоподъемность одного домкрата:
;
Н
Определим диаметр винта домкрата по условию устойчивости:
;
где Fa - грузоподъёмность домкрата, Н; - коэффициент высоты гайки, 1,3;
- коэффициент для упорной резьбы, 0,75
- допустимое напряжение смятия, 6 МПа
мм
судно валопровод рулевой модернизация
Выбираем резьбу М24 3 со следующими размерами:
наружный диаметр резьбы - d=24 мм;
внутренний диаметр резьбы - d1=20.75 мм;
средний диаметр резьбы - d2=22,05 мм;
шаг резьбы - Р = 3
высота профиля - h = 1,624 мм;
высота гайки - Н = 19 мм;
число витков гайки - z = 6,35. Условия прочности резьбы по напряжениям среза:
;
где Н - высота гайки, мм;
- внутренний диаметр резьбы, мм;
к - коэффициент полноты резьбы, 0,65;
Кm - коэффициент неровномерности нагрузки по виткам резьбы, 0,6;
- допустимое напряжение среза, 120 МПа.
МПа
,98 ≤ 120 - условие прочности соблюдено.
Проверка ходовой резьбы по напряжениям смятия:
;
где - средний диаметр резьбы, мм; h - высота профиля, мм; z - число витков гайки;
- допустимое напряжение смятия, 240 МПа.
МПа
,8 ≤ 240 - условие устойчивости соблюдено.
Т.к. стержень винта работает на сжатие и имеет большую свободную длину, его необходимо проверить на прочность с учётом устойчивости:
;
где - коэффициент уменьшающий допуск напряжений, 0,8.
Для материала винта, принимаем коэффициент запаса прочности = 2 получаем:
МПа;
;
МПа;
Расчёт подшипников
Конструкция валопровода включает в себя упорный вал, опирающийся на подшипник качения.
Этот подшипник предназначен для работы под радиальными нагрузками, но может одновременно воспринимать и осевую нагрузку. Подшипник имеет два ряда бочкообразных роликов. Дорожка качения на наружном кольце обработана по сфере. Подшипник может работать при значительном (порядка 2-30) перекосе внутреннего кольца относительно оси наружного.
Произведём расчёт упорного подшипника. Упорный подшипник воспринимает усилие, движущие судно, т.е. передаёт корпусу судна упор, создаваемый гребным винтом.
Расчёт подшипника производим по динамической грузоподъёмности С при частоте вращения n =10 мин-1.
Условие подбора:
С (потребная) ≤ С (паспортная)
Динамическая грузоподъёмность и ресурс связаны следующей эмпирической зависимостью:
;
где, L -ресурс подшипника, млн.об.; принимаем L = 45 тыс.час. = 1013 млн.об. P - эквивалентная динамическая нагрузка,Н; р - коэффициент для роликовых подшипников, 3,33; a1 - коэффициент надёжности, 1; a2 - обобщённый коэффициент совместного влияния качества металла и условий эксплуатации, 0,35;
Эквивалентная динамическая нагрузка, Н:
Р = Fa + 1.2Fr;
где, Fa - осевая нагрузка на подшипник, Н;
Fr - радиальная нагрузка на подшипник, Н.
В нашем случае осевая нагрузка равна максимальной тяге в швартовом режиме 255кН = 255000Н, а радиальную нагрузку принимаем равной весу вала.
Р = 255000+2675 =257675Н
Динамическая грузоподъемность, Н:
Результаты расчётов показывают, что ни один из отечественных подшипников не может воспринимать такую нагрузку при данном диаметре вала. Таким образом, приходим к выводу, что установленный на данном проекте судна упорный подшипник производства германии является наилучшим для данного условия эксплуатации.
Проверка диаметров валов
Диаметры валов для СЭУ с четырёхтактными главными двигателями должны быть не менее:
гребной вал:
мм.
где, К - бесшпоночное соединение гребного винта с валом. Р - мощность на валу, кВт; n - частота вращения, об/мин.
> 166 - условие соблюдается.
промежуточный вал:
мм.
где, F=100 для механических установок СДВС.
> 136 - условие соблюдается.
упорный вал:
мм.
> 149,6 - условие соблюдается.
Расчёт валов на прочность
Необходимость расчёта устанавливают в зависимости от типа ГД, типа передачи, конструктивных характеристик валопровода и гребного винта. К числу таких проверочных расчётов относят: расчёт прочности вала при сложном напряжённом состоянии под действием условно принимаемых статических нагрузок; расчёт на крутильные колебания; расчёт на поперечные изгибающие колебания; расчёт на продольную устойчивость.
Заключение
Целью данного дипломного проекта была разработка технологии по ремонту и модернизации винто - рулевого комплекса, для снижения трудоёмкости и повышения качества работ, а также для внедрения новых технологий.
В ходе рассмотрения существующей конструкции были выявлены следующие недостатки: - шпоночное соединение гребного винта и вала; - цельнолитой гребной винт; - шпоночное соединение румпеля и баллера;
В результате были сделаны следующие расчёты по модернизации существующих конструкций: - посадка винта на вал гидропрессовым способом; - посадка румпеля на баллер гидропрессовым способом; - расчёт сборного гребного винта; - расчёт оснастки для заводки гребного вала в сборе с гребным винтом.
Выполнено технико-экономическое обоснование разработанных предложений.
Введение
Эффективность работы на речном и морском флоте в значит
|
|
История создания датчика движения: Первый прибор для обнаружения движения был изобретен немецким физиком Генрихом Герцем...
Поперечные профили набережных и береговой полосы: На городских территориях берегоукрепление проектируют с учетом технических и экономических требований, но особое значение придают эстетическим...
Общие условия выбора системы дренажа: Система дренажа выбирается в зависимости от характера защищаемого...
Историки об Елизавете Петровне: Елизавета попала между двумя встречными культурными течениями, воспитывалась среди новых европейских веяний и преданий...
© cyberpedia.su 2017-2024 - Не является автором материалов. Исключительное право сохранено за автором текста.
Если вы не хотите, чтобы данный материал был у нас на сайте, перейдите по ссылке: Нарушение авторских прав. Мы поможем в написании вашей работы!