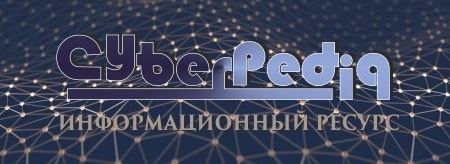
История развития хранилищ для нефти: Первые склады нефти появились в XVII веке. Они представляли собой землянные ямы-амбара глубиной 4…5 м...
Археология об основании Рима: Новые раскопки проясняют и такой острый дискуссионный вопрос, как дата самого возникновения Рима...
Топ:
Оснащения врачебно-сестринской бригады.
Комплексной системы оценки состояния охраны труда на производственном объекте (КСОТ-П): Цели и задачи Комплексной системы оценки состояния охраны труда и определению факторов рисков по охране труда...
История развития методов оптимизации: теорема Куна-Таккера, метод Лагранжа, роль выпуклости в оптимизации...
Интересное:
Наиболее распространенные виды рака: Раковая опухоль — это самостоятельное новообразование, которое может возникнуть и от повышенного давления...
Инженерная защита территорий, зданий и сооружений от опасных геологических процессов: Изучение оползневых явлений, оценка устойчивости склонов и проектирование противооползневых сооружений — актуальнейшие задачи, стоящие перед отечественными...
Средства для ингаляционного наркоза: Наркоз наступает в результате вдыхания (ингаляции) средств, которое осуществляют или с помощью маски...
Дисциплины:
![]() |
![]() |
5.00
из
|
Заказать работу |
|
|
В ведение
Основной задачей для повышения производительности труда является внедрение машин и оборудования со встроенными средствами микропроцессорной техники, многооперационных станков с числовым программным управлением и робототехнических комплексов, гибких производственных систем. Это новый вид технологического оборудования, отвечающий современным требованиям производства. Быстрые перемены в условиях и характере производства - отличительная черта последних десятилетий. Поэтому производство приобретает такие новые качества, как гибкость и экономичность, высокий уровень автоматизации. Использование высокоавтоматизированного оборудования делает труд рабочего и инженера творческим, освободившимся от рутинных действий, от тяжёлого, монотонного физического труда.
Создание и широкое внедрение гибких автоматизированных производств определяется в настоящее время ускорением развития станкостроения, робототехники, вычислительной техники, микроэлектроники и приборостроения, являющихся катализатором научно-технического прогресса.
Автоматизацию производственных процессов с использованием промышленных роботов можно разделить на две части.
Первая часть связана с созданием промышленных роботов различного технологического назначения.
Вторая часть задачи относится к созданию робототехнических комплексов различного назначения, удовлетворяющих потребности конкретного производства.
Автоматизация процесса механообработки в мелкосерийном и серийном производстве успешно решается применением автоматических станков. Автоматизация вспомогательных операций - установка и снятие детали со станка, межстаночное транспортирование - может быть решена с помощью промышленных роботов.
|
Робототехнические комплексы позволяют: увеличить производительность труда на 30-40%, сократить простои оборудования, обеспечить возможность быстрой и лёгкой переналадки комплекса при смене объектов производства. Объединяя РТК общей автоматизированной транспортно-складской системой, системой управления можно компоновать различные гибкие производственные системы.
Общая часть
Исходные данные проекта
Гибкая автоматическая линия для обработки деталей типа валов и втулок с разработкой системы управления и информации для обрабатывающего центра.
Наименование основного технологического оборудования:
Токарный прецизионный станок модели ТПК-125ВН2 с числовым программным управлением и роботом МП-254.
Цель и назначение разработки:
Увеличить годовую программу выпуска деталей типа болт, винт, гайка с повышенными требованиями к точности изготовления.
Технические требования:
Точность изготавливаемых диаметров деталей по h9, резьбы по g6, линейных размеров по h14.
Технологические требования:
· требуемая производительность, шт./год:
6000 шт./год, 3 шт./час.
· на каком виде оборудования выполнялись операции и сколько потребовалось этого оборудования для выполнения операций на заказываемую производительность:
Универсальное оборудование 16К20 и 1И611ПМ.
· наименование технических операций, которые должны выполняться на данном оборудовании в последовательности по технологическому процессу:
1. Токарная с ЧПУ
2. Токарная с ЧПУ
3. Токарная с ЧПУ
4. Фрезерная с ЧПУ
расчётное время на изготовление детали:
=7+5+6+3=21 мин;
· количество позиций при одновременной или последовательной обработке:
1.
· способ установки обрабатываемой детали на загрузочную позицию:
Роботом.
· способ съёма обрабатываемой детали по окончании обработки:
Роботом.
· проектная стойкость инструмента и оснастки:
|
90 мин.
· потребность в охлаждающей жидкости в зоне обработки:
Эмульсия ИПК 65020.
· способ удаления отходов производства:
Вручную с помощью щетки-смётки.
· способ и система складирования деталей и полуфабрикатов:
В накопитель.
· режимы управления:
Наладочный, автоматический.
· информация, связанная с унификацией инструмента:
Сечение резцов на всех трёх операциях должны быть одинаковыми 10x10.
· дополнительные требования:
При обработке на всех 3-ёх токарных операциях съём металла не более 3-х мм. Припуск на чистовую обработку не более 0,25 мм.
· способ получения заготовки детали:
Сертифицированный материал - сталь 06Х13Н7Д2.
· обозначение чертежа изделия (детали):
БМПВ-С. 1.01.04.072
Технологическая часть
Конструкторская часть
Кинематический расчёт
Выбор электродвигателя главного движения:
Из операций 070, 075 и 085, где используется одно и тоже оборудование выбираем операцию с максимальной мощностью резания.
N рез.макс. =1,26 кВт - черновое точение на операции 070.
Отсюда требуемая мощность электродвигателя главного движения:
кВт.
Максимальные обороты шпинделя при обработке соответствуют чистовому точению на операции 070 n макс. = 1504 об/мин.
Для обеспечения диапазона частот вращения шпинделя от 30 до 2000 об/мин выбираем двигатель постоянного тока для цепи главного движения 2ПБ112ГУ4 с возможностью главного регулирования частоты вращения ротора n ном. = 3150 об/мин и мощностью N = 2 кВт. Отсюда передаточное отношение ремённой передачи i = = 1,575 принимаем i = 1,5 согласно стандартного рода передаточных чисел.
Расчёт шпиндельного узла
Параметры шпиндельного узла
Участок №1 Стержень:
Длина (mm.)=4.000e+001
Наружний диаметр (mm.)=4.000e+001
Внутренний диаметр (mm.)=2.100e+001
Диаметр шихты (mm.)=0.000e+000
Плотность (кг/m**3)=7.850e+003
Модуль Юнга (н/m**2)=2.100e+011одуль упp.для шихты=2.100e+010
Плотность шихты (кг/m**3)=7.850e+003
Участок №2 Стержень:
Длина (mm.)=2.900e+001
Наружний диаметр (mm.)=7.000e+001
Внутренний диаметр (mm.)=2.100e+001
Диаметр шихты (mm.)=0.000e+000
Плотность (кг/m**3)=7.850e+003
Модуль Юнга (н/m**2)=2.100e+011одуль упp.для шихты=2.099e+010
Плотность шихты (кг/m**3)=7.850e+003
Участок №3 Стержень:
Длина (mm.)=4.400e+001
Наружний диаметр (mm.)=6.000e+001
Внутренний диаметр (mm.)=1.500e+001
Диаметр шихты (mm.)=0.000e+000
Плотность (кг/m**3)=7.850e+003
Модуль Юнга (н/m**2)=2.100e+011одуль упp.для шихты=2.100e+010
|
Плотность шихты (кг/m**3)=7.850e+003
Участок №4 Радиальный рол. подшипник:
Ширина кольца (мм.) = 2.600e+001
Число рол. в 1 ряду = 2.400e+001
Геом.зазор (натяг) (мм.) = -1.000e-003
Радиальная нагрузка (Н.) = 2.905e+003
Число рядов тел качения = 2.000e+000
Эф.длина ролика (мм.) = 8.000e+000
Стат.нес. способность (Н.) = 5.410e+004
Дин.нес. способность (Н.) = 5.560e+004
Нар.диаметр кольца (мм.) = 9.500e+001
Вн.диаметр кольца (мм.) = 6.000e+001
Диаметр ролика (мм.) = 8.000e+000
Участок №5 Стержень:
Длина (mm.)=3.000e+001
Наружний диаметр (mm.)=6.000e+001
Внутренний диаметр (mm.)=1.500e+001
Диаметр шихты (mm.)=0.000e+000
Плотность (кг/m**3)=7.850e+003
Модуль Юнга (н/m**2)=2.100e+011одуль упp.для шихты=2.100e+010
Плотность шихты (кг/m**3)=7.850e+003
Участок №6 Рад.упорный подшипник:
Ном.угол контакта (град)=2.600e+001
Число шар. в 1 ряду =1.800e+001
Диаметр шарика (мм.)=1.110e+001
Диаметр нар. кольца (мм.)=9.500e+001
Диаметр вн. кольца (мм.)=6.000e+001тат.нес. способность (Н.)=2.500e+004
Дин.нес. способность (Н.)=2.887e+004
Натяг (Н.)=1.000e+002
Ширина (мм.)=1.800e+001
Участок №7 Стержень:
Длина (mm.)=2.500e+001
Наружний диаметр (mm.)=6.000e+001
Внутренний диаметр (mm.)=1.500e+001
Диаметр шихты (mm.)=0.000e+000
Плотность (кг/m**3)=7.850e+003
Модуль Юнга (н/m**2)=2.100e+011одуль упp.для шихты=2.100e+010
Плотность шихты (кг/m**3)=7.850e+003
Участок №8 Рад.упорный подшипник:
Ном.угол контакта (град)=2.600e+001
Число шар. в 1 ряду =1.800e+001
Диаметр шарика (мм.)=1.110e+001
Диаметр нар. кольца (мм.)=9.500e+001
Диаметр вн. кольца (мм.)=6.000e+001тат.нес. способность (Н.)=2.500e+004
Дин.нес. способность (Н.)=2.887e+004
Натяг (Н.)=1.000e+002
Ширина (мм.)=1.800e+001
Участок №9 Стержень:
Длина (mm.)=4.500e+001
Наружний диаметр (mm.)=6.000e+001
Внутренний диаметр (mm.)=1.500e+001
Диаметр шихты (mm.)=0.000e+000
Плотность (кг/m**3)=7.850e+003
Модуль Юнга (н/m**2)=2.100e+011одуль упp.для шихты=2.100e+010
Плотность шихты (кг/m**3)=7.850e+003
Участок №10 Стержень:
Длина (mm.)=2.700e+001
Наружний диаметр (mm.)=5.500e+001
Внутренний диаметр (mm.)=1.500e+001
Диаметр шихты (mm.)=0.000e+000
Плотность (кг/m**3)=7.850e+003
Модуль Юнга (н/m**2)=2.100e+011одуль упp.для шихты=2.100e+010
Плотность шихты (кг/m**3)=7.850e+003
Участок №11 Стержень:
Длина (mm.)=1.920e+002
Наружний диаметр (mm.)=5.000e+001
Внутренний диаметр (mm.)=1.500e+001
Диаметр шихты (mm.)=0.000e+000
Плотность (кг/m**3)=7.850e+003
Модуль Юнга (н/m**2)=2.100e+011одуль упp.для шихты=2.100e+010
Плотность шихты (кг/m**3)=7.850e+003
|
Участок №12 Радиальный рол. подшипник:
Ширина кольца (мм.) = 2.300e+001
Число рол. в 1 ряду = 2.200e+001
Геом.зазор (натяг) (мм.) = -1.000e-003
Радиальная нагрузка (Н.) = 2.885e+003
Число рядов тел качения = 2.000e+000
Эф.длина ролика (мм.) = 7.000e+000
Стат.нес. способность (Н.) = 3.660e+004
Дин.нес. способность (Н.) = 3.980e+004
Нар.диаметр кольца (мм.) = 8.000e+001
Вн.диаметр кольца (мм.) = 5.000e+001
Диаметр ролика (мм.) = 7.000e+000
Участок №13 Стержень:
Длина (mm.)=1.250e+001
Наружний диаметр (mm.)=5.000e+001
Внутренний диаметр (mm.)=1.500e+001
Диаметр шихты (mm.)=0.000e+000
Плотность (кг/m**3)=7.850e+003
Модуль Юнга (н/m**2)=2.100e+011одуль упp.для шихты=2.100e+010
Плотность шихты (кг/m**3)=7.850e+003
Участок №14 Стержень:
Длина (mm.)=1.800e+001
Наружний диаметр (mm.)=4.500e+001
Внутренний диаметр (mm.)=1.500e+001
Диаметр шихты (mm.)=0.000e+000
Плотность (кг/m**3)=7.850e+003
Модуль Юнга (н/m**2)=2.100e+011одуль упp.для шихты=2.100e+010
Плотность шихты (кг/m**3)=7.850e+003
Участок №15 Стержень:
Длина (mm.)=3.500e+001
Наружний диаметр (mm.)=4.000e+001
Внутренний диаметр (mm.)=1.500e+001
Диаметр шихты (mm.)=0.000e+000
Плотность (кг/m**3)=7.850e+003
Модуль Юнга (н/m**2)=2.100e+011одуль упp.для шихты=2.100e+010
Плотность шихты (кг/m**3)=7.850e+003адиальная и осевые жесткости (н/мкм): 5.905e+001 5.120e+001
Осевая и радиальная нагрузки: (Н) 3.000e+003 5.831e+003
Осевое и радиальные смещения: (мкм) 9.874e+001 5.859e+001
Технико-экономическая часть
Исходные данные
Табл. 1
Параметры | Базовый данные | Проектируемый вариант | |||
Тип оборудования | Токарный станок модели ТВ-320 | Роботизированная линия на базе станка модели ТПК-125ВН2 | |||
Годовая программа выпуска, шт. | 6000 | 6000 | |||
Занимаемая площадь, ![]() | 66 | 118 | |||
Суммарная мощность электродвигателей, кВт | 30 | 20 | |||
Категория сложности ремонта: механической части; электрической части. | 17,2 4,7 | 19,9 20,6 | |||
Себестоимость оборудования, руб.: станок ТВ-320; станок ТПК-125ВН2; станок СФП-500 робот МП-254; робот Универсал 5.02; тактовый стол. | 400.000 - - - - - | - 600.000 1.556.000 82.150 110.256 15.000 | |||
| 120 | 21 | |||
Стоимость 1 | 1000 | 1000 | |||
Цена 1 кВт/час силовой электроэнергии, руб. | 1,34 | 1,34 | |||
Разряд рабочего: станочник; наладчик. | 6 - | - 4 | |||
Выводы по проекту
В процессе дипломного проектирования была разработана роботизированная технологическая линия для механической обработки детали типа болт БМПВ-С. 1.01.04.072 на базе токарного станка с ЧПУ - ТПК-125ВН2, фрезерного станка модели СФП-500 и роботов МП-254 и Универсал 5.02.
Спроектированная роботизированная технологическая линия позволяет увеличить годовую программу выпуска от 3000 до 6000 штук и снизить себестоимость изделия с 153,74 руб. до 58,12 руб. Внедрение данной роботизированной технологической линии даёт годовую экономию на 596.220 рублей.
Для механической обработки детали в роботизированной технологической линии используется современный инструмент с механическим креплением твёрдосплавных пластин.
|
Роботизированная технологическая линия спроектирована с учётом требований безопасности жизнедеятельности и охраны окружающей среды.
Внедрение роботизированной технологической линии даёт возможность интенсификации существующего технологического процесса и стимулирования создания новых прогрессивных процессов.
Внедрение данного участка может явиться шагом к созданию базы для перехода к полностью автоматизированному производству.
Список используемой литературы
1. Аршинов В.А, Алексеев Г.А. «Резание металлов и режущий инструмент», Москва «Машиностроение» 1967.
2. Барановский Ю.В. «Режимы резания металлов» Справочник, Москва «Машиностроение» 1972.
3. Косилова К.Н. «Режимы резания металлов» Справочник, Москва «Машиностроение» 1972.
4. Минина Л.А. «Курс лекций по моделированию систем управления».
5. Васильев Д.В., Чуич В.Г. «Системы автоматического управления» Москва «Высшая школа» 1967.
6. Воронцов Л.Н. «Теория и проектирование контрольных автоматов», Москва 1985.
7. Антонина В.М. «Курс лекций по САУ».
8. Тронов В.Е. «Курс лекций по ТАУ».
9. Герасимов В.Г. «Основы промышленной электроники».
10.Грановский Г.И и В.Г. «Резание металлов» Москва «Высшая школа» 1985.
11.Перов С.С. «Курс лекций по автоматике и микропроцессорной технике».
12.Жаров В.А. «Курс лекций по оборудованию машиностроительных производств».
13.Козырев Ю.Г. «Промышленные роботы», Справочник Москва «Машиностроение» 1988.
14.Маталин А.А. «Технология машиностроения», Москва «Машиностроение» 1995.
15.Момович В.Н. Михайлов Г.М. «Технология производства измерительных инструментов и приборов», Москва «Машиностроение» 1974.
16.Новицкий П.В. «Электрические измерения неэлектрических величин», Ленинград «Энергия» 1975.
17.Осипов-Нефедов «Задачник по расчету режимов резания», Москва 1982.
18.Седых В.Н. «Курс лекций по технологии машиностроения за 7 семестр».
19.Фрайфельд И.А. «Расчеты и конструкции специального режущего инструмента», Москва 1957.
20.Запятный И.И. «Курс лекций по информационно-измерительным устройствам».
21.Запятный И.И. «Курс лекций по электронике и микропроцессорной технике».
22.Чинаев П.И. Старостин А.К. «Автоматическое управление», Москва «Бланкиздат» 1996.
23.«Справочник технолога-машиностроителя» т1, т2, Москва «Машиностроение» 1985.
24.Методические указания МГТУ «СТАНКИН»:
25.№44, №46, №62, №63, №72, №87, №88 №287, №288, №1015, №1080, №1150, №1215, №1261, №1299.
В ведение
Основной задачей для повышения производительности труда является внедрение машин и оборудования со встроенными средствами микропроцессорной техники, многооперационных станков с числовым программным управлением и робототехнических комплексов, гибких производственных систем. Это новый вид технологического оборудования, отвечающий современным требованиям производства. Быстрые перемены в условиях и характере производства - отличительная черта последних десятилетий. Поэтому производство приобретает такие новые качества, как гибкость и экономичность, высокий уровень автоматизации. Использование высокоавтоматизированного оборудования делает труд рабочего и инженера творческим, освободившимся от рутинных действий, от тяжёлого, монотонного физического труда.
Создание и широкое внедрение гибких автоматизированных производств определяется в настоящее время ускорением развития станкостроения, робототехники, вычислительной техники, микроэлектроники и приборостроения, являющихся катализатором научно-технического прогресса.
Автоматизацию производственных процессов с использованием промышленных роботов можно разделить на две части.
Первая часть связана с созданием промышленных роботов различного технологического назначения.
Вторая часть задачи относится к созданию робототехнических комплексов различного назначения, удовлетворяющих потребности конкретного производства.
Автоматизация процесса механообработки в мелкосерийном и серийном производстве успешно решается применением автоматических станков. Автоматизация вспомогательных операций - установка и снятие детали со станка, межстаночное транспортирование - может быть решена с помощью промышленных роботов.
Робототехнические комплексы позволяют: увеличить производительность труда на 30-40%, сократить простои оборудования, обеспечить возможность быстрой и лёгкой переналадки комплекса при смене объектов производства. Объединяя РТК общей автоматизированной транспортно-складской системой, системой управления можно компоновать различные гибкие производственные системы.
Общая часть
История научно-исследовательского и конструкторского института энерготехники имени Н.А. Доллежаля «НИКИЭТ»
болт заготовка автоматизированный электродвигатель
История института тесно связана с первыми шагами освоения ядерной энергии в СССР и отмечена рядом крупных достижений. В конструкторском бюро Н.А. Доллежаля были спроектированы первые отечественные промышленные реакторы, необходимые для создания ядерного оружия.
В 1942 г. в Москве создается Научно-исследовательский институт химического машиностроения (НИИхиммаш), директором и научным руководителем которого назначается Н.А. Доллежаль. Именно здесь впервые реализуется давняя идея Николая Антоновича о построении комплексного научно-исследовательского и конструкторского института с развитой экспериментальной, научной и производственной базой. Успешная реализации этой идеи, знания и опыт сотрудников НИИхиммаша, умение решать нестандартные инженерные задачи и способность к работе в экстремальных условиях - вот, очевидно, причины того, что в 1946 г. Н.А. Доллежаль и возглавляемый им коллектив привлекаются к работам по созданию атомного оружия.
В 1952 г. по Постановлению Совета Министров СССР создается Научно-исследовательский и конструкторский институт энерготехники (НИИ-8, впоследствии НИКИЭТ), директором и научным руководителем которого становится Н.А. Доллежаль. Институт был призван обеспечить разработку: ядерной энергетической установки для первой отечественной атомной подводной лодки, водографитового канального реактора для первой в мире атомной электростанции в г. Обнинске, первого двухцелевого энергетического реактора для Сибирской АЭС, первого канального реактора с ядерным перегревом пара для Белоярской АЭС.
Сейчас НИКИЭТ - один из крупнейших в России центров ядерной техники и технологии.
По проектам и при участии НИКИЭТ в России и за ее пределами были построены 27 исследовательских реакторов, некоторые из которых уникальны и не имеют аналогов в мировой практике.
Институт располагает обширной экспериментальной базой, в которую входят исследовательские реакторы, теплофизические стенды, стенды для испытания систем управления и защиты реактора, комплекс горячих камер и другие установки.
В рамках конверсии потенциала, накопленного в области космических ядерных энергодвигательных установок, институтом разработаны системы транспортировки и глубокой очистки инертных газов и азота для микроэлектроники и организовано собственное производство сверхчистых криптона и ксенона, поставки которых осуществляются в США и ряд западно-европейских стран. Осваивается производство сверхчистых металлов (германий, теллур, висмут, селен, осмий и др.) и завершаются проектные работы по созданию комплекса по производству редкоземельных металлов и продукции на их основе. На реакторе ИВВ-2М налажено производство радионуклидов различного назначения, которые поставляются за рубеж.
Интенсивные разработки в области лазерной спектроскопии привели к созданию целой серии уникальных аналитических приборов для определения микропримесей в различных средах. Конверсионные разработки института нашли применение и в медицине. Созданы не имеющие аналогов спектрофлуориметры для ранней диагностики онкологических заболеваний. Успешно прошли клинические испытания и готовы к серийному производству циркониевые имплантанты для черепно-лицевой хирургии. Ведется работа по созданию оборудования для улавливания и рециклирования дорогостоящего ксенона в перспективных аппаратах ксеноновой анестезии.
У института широкие международные связи. Он принимает участие в ряде международных многосторонних и двусторонних программ по повышению безопасности АЭС с реакторами РБМК. В рамках международного проекта термоядерного реактора ИТЭР институт проводит исследования по бланкету и материалам первой стенки, системам преобразования энергии. Совместно с фирмами США и Франции разрабатывается ядерная энергодвигательная установка для длительных пилотируемых космических полетов.
НИКИЭТ располагает большим интеллектуальным и техническим потенциалом для решения самых сложных научно-технических задач.
Исходные данные проекта
Гибкая автоматическая линия для обработки деталей типа валов и втулок с разработкой системы управления и информации для обрабатывающего центра.
Наименование основного технологического оборудования:
Токарный прецизионный станок модели ТПК-125ВН2 с числовым программным управлением и роботом МП-254.
Цель и назначение разработки:
Увеличить годовую программу выпуска деталей типа болт, винт, гайка с повышенными требованиями к точности изготовления.
Технические требования:
Точность изготавливаемых диаметров деталей по h9, резьбы по g6, линейных размеров по h14.
Технологические требования:
· требуемая производительность, шт./год:
6000 шт./год, 3 шт./час.
· на каком виде оборудования выполнялись операции и сколько потребовалось этого оборудования для выполнения операций на заказываемую производительность:
Универсальное оборудование 16К20 и 1И611ПМ.
· наименование технических операций, которые должны выполняться на данном оборудовании в последовательности по технологическому процессу:
1. Токарная с ЧПУ
2. Токарная с ЧПУ
3. Токарная с ЧПУ
4. Фрезерная с ЧПУ
расчётное время на изготовление детали:
=7+5+6+3=21 мин;
· количество позиций при одновременной или последовательной обработке:
1.
· способ установки обрабатываемой детали на загрузочную позицию:
Роботом.
· способ съёма обрабатываемой детали по окончании обработки:
Роботом.
· проектная стойкость инструмента и оснастки:
90 мин.
· потребность в охлаждающей жидкости в зоне обработки:
Эмульсия ИПК 65020.
· способ удаления отходов производства:
Вручную с помощью щетки-смётки.
· способ и система складирования деталей и полуфабрикатов:
В накопитель.
· режимы управления:
Наладочный, автоматический.
· информация, связанная с унификацией инструмента:
Сечение резцов на всех трёх операциях должны быть одинаковыми 10x10.
· дополнительные требования:
При обработке на всех 3-ёх токарных операциях съём металла не более 3-х мм. Припуск на чистовую обработку не более 0,25 мм.
· способ получения заготовки детали:
Сертифицированный материал - сталь 06Х13Н7Д2.
· обозначение чертежа изделия (детали):
БМПВ-С. 1.01.04.072
|
|
Индивидуальные и групповые автопоилки: для животных. Схемы и конструкции...
Семя – орган полового размножения и расселения растений: наружи у семян имеется плотный покров – кожура...
История создания датчика движения: Первый прибор для обнаружения движения был изобретен немецким физиком Генрихом Герцем...
Автоматическое растормаживание колес: Тормозные устройства колес предназначены для уменьшения длины пробега и улучшения маневрирования ВС при...
© cyberpedia.su 2017-2024 - Не является автором материалов. Исключительное право сохранено за автором текста.
Если вы не хотите, чтобы данный материал был у нас на сайте, перейдите по ссылке: Нарушение авторских прав. Мы поможем в написании вашей работы!