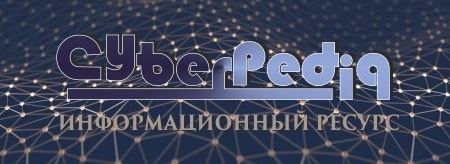
Своеобразие русской архитектуры: Основной материал – дерево – быстрота постройки, но недолговечность и необходимость деления...
Индивидуальные очистные сооружения: К классу индивидуальных очистных сооружений относят сооружения, пропускная способность которых...
Топ:
Установка замедленного коксования: Чем выше температура и ниже давление, тем место разрыва углеродной цепи всё больше смещается к её концу и значительно возрастает...
История развития методов оптимизации: теорема Куна-Таккера, метод Лагранжа, роль выпуклости в оптимизации...
Эволюция кровеносной системы позвоночных животных: Биологическая эволюция – необратимый процесс исторического развития живой природы...
Интересное:
Отражение на счетах бухгалтерского учета процесса приобретения: Процесс заготовления представляет систему экономических событий, включающих приобретение организацией у поставщиков сырья...
Финансовый рынок и его значение в управлении денежными потоками на современном этапе: любому предприятию для расширения производства и увеличения прибыли нужны...
Влияние предпринимательской среды на эффективное функционирование предприятия: Предпринимательская среда – это совокупность внешних и внутренних факторов, оказывающих влияние на функционирование фирмы...
Дисциплины:
![]() |
![]() |
5.00
из
|
Заказать работу |
|
|
Выбор и обоснование выбора системы управления роботизированного комплекса
Система управления участком состоит из двух частей:
· система управления станком;
· система управления роботом и тактовым столом.
Для управления промышленным роботом и тактовым столом могут применяться цикловые, позиционные и контурные унифицированные системы управления.
Контурные системы управления позволяют программировать и воспроизводить траектории движения любой формы. Они предназначены для управления промышленным роботом, требующим сложного пространственного перемещения исполнительного органа по заданной траектории, что необходимо при окраске, дуговой сварке, сложных сборочных операциях. Для обслуживания технологического оборудования сложных перемещений не требуется, поэтому будет достаточно позиционной или цикловой системы управления.
Цикловые системы управления применяют для управления промышленными роботами, обслуживающими оборудование в условиях массового и крупносерийного производства. Ими оснащают роботы с ограниченными манипуляционными и функциональными возможностями, имеющими небольшое число точек позиционирования по каждой степени подвижности. Проектируемый робот имеет 3 степени подвижности, поэтому для его управления такой системы будет недостаточно.
Значит, будем использовать числовую систему позиционного управления, которая предназначена для промышленных роботов со значительным числом точек позиционирования по каждой координате. На данном предприятии наиболее часто используется устройство числового программного управления типа Н22-1МТ1.
Описание устройства числового программного управления Н22-1МТ1
|
Устройство числового программного управления Н22-1МТ1 предназначено для управления токарными станками ТПК-125В, представляющее собой сборочную единицу, устанавливаемую к станку. Относится к устройствам контурного управления, построенным по аппаратному принципу со схемной реализацией заданного состава функций 2-ух координатного управления.
Устройство числового программного управления предназначено для работы в механических цехах машиностроительных предприятий при температуре окружающего воздуха от 5 до 40° С, а так же предназначено для работы в условиях наличия агрессивной среды, тряски и толчков.
Устройство числового программного управления Н22-1МТ1 построено по принципу цифровой модели, в которой все соответствующие алгоритмы работы системы «устройство-станок» выполняются посредством отдельных цепей или устройств, выполняющих ту или иную функцию.
Устройство числового программного управления выполнено в двух шкафах: шкаф интерполятора и шкаф устройства управления шаговым приводом. Стойка ЧПУ предназначена для контурного управления двухкоординатными механизмами, допускающими кратковременный останов привода подач при вводе очередного кадра. Программоносителем является пятидорожная телеграфная лента. При ручном программировании для перфорации ленты используется стандартный телеграфный аппарат типа ПЛ-20 с клавиатурой.
В системе предусмотрена работа в режиме самонастройки по подаче. Программой задаётся лишь максимальное значение скорости. Предусмотрен контроль правильности считывания информации.
Кроме работы от флеш драйва, предусмотрены следующие режимы:
преселективное управление, позволяющее задать на переключателях мерное перемещение;
ручное управление (установочные перемещения) с изменением подачи в диапазоне 1:3.
В системе предусмотрена возможность программирования до 6 технологических команд, имеющих выход на реле. Эти команды могут быть использованы для включения различных приборов по программе.
|
В устройствах числового программного управления (УЧПУ) металлорежущими станками программа определяет координаты опорных точек кривой, по которой движется рабочий орган станка; устройство аппроксимирует отрезки между опорными точками методом линейной или круговой интерполяции и выдаёт управляющие сигналы на привод.
Кроме информации о геометрических перемещениях в программе указываются скорость отработки и технологические команды по чертежу изделия и технологии обработки. Вся информация разбивается на кадры и в соответствующих символах заносится на флеш драйв.
Устройство ЧПУ Н22-1МТ1 предназначено для работы с токарными станками, у которых дискретность по оси Х=0,001 мм, а по оси Y=0,002 мм.
Устройство управления шаговым приводом (УУШП) предназначено для преобразования, формирования и усиления сигналов унитарного кода, поступающего из интерполятора, в сигналы управления током фазовых обмоток шаговых двигателей типа ШД-5Д1. УУШП выпускается в виде автономной стойки, которая механическим и электрическим монтажом сочленяется с интерполятором УЧПУ Н22-1МТ1.
Функционально устройство ЧПУ состоит из устройства ввода, устройства синхронизации, блока реле, устройства питания, плат индикации, блоков управления шаговыми двигателями, устройства контроля.
Описание конструкции устройства числового программного управления Н22-1МТ1.
Функционально устройство ЧПУ состоит из:
· устройства ввода;
· устройства синхронизации;
· устройства интерполяции;
· устройства задания скорости (УЗС);
· устройства управления и преобразования (УУП);
· устройства контроля;
· устройства питания
· фотосчитывающего устройства;
· плат индикации;
· пульта оператора;
· пульта коррекции;
· блоков управления шаговыми двигателями (БУШД);
· блока реле.
Выбор, обоснование и описание приводов роботизированного комплекса.
Привод можно определить как устройство преобразования сигналов, поступающих от системы управления, в механическое перемещение исполнительных звеньев.
Структурно это устройство (смотри рис. 1.2.4.) содержит ряд преобразователей энергии. По виду энергоносителя различают электрический, пневматический, гидравлический и комбинированные приводы.
Рис. 4.3.4.
СУ - система управления; МС - механическая система
|
К приводам промышленных роботов предъявляются требования, обусловленные, с одной стороны, технологическим циклом их работы, с другой, - особенностями их конструкции. Основным рабочим циклом механизма робота является позиционирование. Ускорение перемещения может достигать 30 м/мин. Режим работы приводов - повторно-кратковременный с частыми пусками и торможениями. Возмущений по нагрузке нет ввиду отсутствия процесса резания. Мощность приводов мала (не выше 1кВт), но при этом требуется большой момент и малые скорости. Таким образом, привод должен иметь диапазон регулирования порядка 1000, обладать большой перегрузочной способностью в пусковых режимах (иметь малые времена пусков и торможений на максимальную скорость). Перемещение рабочего органа робота вместе с двигателем приводит к необходимости применения двигателя с малыми массогабаритными параметрами.
Наиболее подходящими для применения в приводах роботов являются малоинерционные электродвигатели с постоянными магнитами, удовлетворяющие основным требованиям. В качестве преобразователей в основном применяют транзисторные широтно-импульсные преобразователи. Они дают возможность наиболее полно реализовать сложные алгоритмы управления, обладая высокими статистическими и динамическими характеристиками. Таким образом, в промышленном роботе будем использовать транзисторный электропривод постоянного тока (ЭШИМ).
Многокоординатный электропривод обеспечивает независимое управление по каждой оси в диапазоне регулирования скорости 1¸10000. Полоса пропускания привода - не менее 100 Гц. Привод имеет следующие виды защиты:
· максимально токовую;
· времятоковую;
· от перегрева блока регулирования при перегрузках;
· от напряжения;
· от понижения и повышения стабилизированного напряжения;
· от несоответствия скорости привода заданной;
· от обрыва фазы.
Двигатели 4ДПУ, применяемые в приводе имеют следующие характеристики:
· номинальная мощность - 0,45 кВт;
номинальный момент - 0,15 ;
номинальная частота вращения - 1000 ;
момент инерции -
;
· масса - 5 кг;
размеры (длина ширина
высота), -
мм.
|
Электрический привод обеспечивает поворот руки, выдвижение и подъём руки робота. Но для вращения кисти руки этот привод не пригоден, так как развивает малый момент и требует специальных передаточных механизмов для преобразования момента (редукторы), а так как двигатель устанавливается на исполнительном органе, то это повлечёт за собой значительное увеличение габаритов руки. Поэтому целесообразно применять поворотные приводы, основное назначение которых - осуществление поворотных движений по программе, поступающей в виде электрических сигналов. Такие приводы бывают гидравлическими и пневматическими. В нашем случае выберем пневматический привод, так как он обладает преимуществами перед гидравлическим; к которым относятся быстрота срабатывания, простота конструкции и эксплуатации, низкая стоимость, высокая надёжность; пожаро- и взрывобезопасность. К недостаткам пневмопривода относится низкая удельная мощность, обусловленная малым (не более 0,6 МПа) рабочим давлением. Так как масса болта БМПВ-С. 1.01.04.072 не превышает 0,15 кг, то большая мощность не потребуется, поэтому будем применять пневмопривод. Пневмопривод представляет собой неполноповоротный пневмодвигатель (так как требуется поворот только на 90°) и пневмоаппаратуру для управления пневмоприводом: распределительную (распределители и их электромагниты); подготовки воздуха (фильтры-влагоотделители, маслораспылители).
Поворотные пневмодвигатели PR-300S (Япония), применяемые в пневмоприводе имеют следующие характеристики:
крутящий момент на выходном валу - 70 ;
рабочий объём при повороте на полный угол - 0,36 ;
· масса - 5,1 кг;
размеры (диаметр длина) - 140
220 мм.
В станках, в зависимости от назначения различают приводы главного движения, подач и вспомогательные приводы. Приводы подач перемещают заготовку или режущий инструмент в зону резания. Вспомогательные - производят различные подготовительные операции: вращение механизмов, подачу СОЖ и смазки, вентиляцию и т.д.
В соответствии с назначением к каждому приводу предъявляются различные требования. По условиям технологии обработки скорость главного привода должна регулироваться с постоянной мощностью (P=constant). Обычно диапазон регулирования частот вращения шпинделя не превышает Д£100. Приводы подач регулируются при постоянном моменте (M=constant). Они должны иметь широкий диапазон регулирования скорости Д³10000, в этом случае может быть достигнута высокая точность и малая шероховатость, Кроме того, приводы подач должны иметь высокие скорости и быстродействие во время разгона - торможения и сброса - наброса нагрузки.
Вспомогательные приводы не участвуют в процессе резания, поэтому в них не требуется широкого диапазона регулирования (Д<10), высокого быстродействия; они должны иметь плавный разгон и торможение.
|
Для станков могут быть применены различные виды приводов: механический, гидравлический и электрический. Однако электрический привод вытесняет все виды приводов из-за их существенных недостатков и служит для регулирования скорости в широком диапазоне с высокой точностью и быстродействием, имеет широкий ряд мощностей, моментов и скоростей. Электропривод технологичен в изготовлении, достаточно прост и надёжен в эксплуатации.
Привод станков, как правило, осуществляется от одного или нескольких индивидуальных электродвигателей. Основным типом приводного электродвигателя является асинхронный короткозамкнутый электродвигатель. Они имеют самую простую конструкцию, очень технологичны, дёшевы, ремонтопригодны, обеспечивают наибольшую надёжность работы. На рис. 1.2.4а. представлена структурная схема регулируемого электропривода с частотно-токовым управлением.
Рис. 4.3.4а.
Схема управления содержит регулятор скорости (РС), включённые последовательно. Функция регулятора тока - сформировать сигнал, пропорциональный заданному значению тока. Так как задаётся синусоидальный сигнал, надо знать модуль, фазу и
частоту. Для задания модуля | | необходимо знать его составляющие
и
.
задаётся внешним устройством,
формируется пропорционально величине скольжения. Модуль тока определяется: |
|
, а фаза
. Эти процедуры производятся в регуляторе вектора тока (РВТ).
Для определения частоты статора суммируют частоту ротора
и частоту вращения вала двигателя
, где
- число пар полюсов датчика ДП, формирующего этот сигнал. Частоту скольжения
и частоту вращения вала
определяют блоками формирования частоты скольжения (ФЧС) и формирования частоты вращения (ФЧВ).
Таким образом, на выходе регулятора вектора тока заданы вектор тока и его частота
.
В регуляторе фазных токов (РФТ) происходит преобразование токов двухфазной системы в токи и
трёхфазной системы (третий ток получается как разность первых двух).
В регуляторе тока (РТ) заданные токи и
сравниваются с истинными (по сигналам, получаемым от датчиков тока, установленных в двух фазах); их разность после соответствующих преобразований поступает в преобразователь частоты (ПЧ) в виде управляющего сигнала.
В соответствии с этим силовая часть транзисторного преобразователя частоты, работа которого основана на принципе широтно-импульсной модуляции, формирует токи синусоидальной формы требуемой частоты в областях асинхронного двигателя. Такой алгоритм управления даёт возможность создать регулируемый электропривод с асинхронным двигателем, имеющим высокие статические и динамические характеристики.
Для токарного патронного станка высокой точности модели ТПК-125ВН2 будем использовать серийно выпускаемое комплектное устройство типа «Размер», который устанавливается в механизме главного движения. Привод главного движения имеет максимальную мощность 2 кВт и максимальную частоту вращения 3150 об/мин.
Выбор, обоснование и описание системы информации роботизированного комплекса
Информационные системы в значительной степени определяют функциональные возможности РТК, эксплуатационную надёжность и эффективность его использования в производственных условиях, а также являются важным звеном в обеспечении безопасности обслуживающего персонала.
Информационная система состоит из набора первичных преобразователей (датчиков) с устройствами обработки информации.
По функциональному назначению информационные системы делятся на три группы:
· системы внутренней информации;
· системы восприятия внешней среды;
· системы обеспечения техники безопасности.
Системы восприятия внешней среды предназначены для получения и выдачи в систему управления промышленного робота информации о наличии объекта в пространстве, распознавания его формы и ориентации, определения его физических и других свойств. Так как в зону работы робота деталь поступает в ориентированном положении, постоянной формы, с одинаковыми физическими свойствами, то, значит, система восприятия внешней среды не нужна.
Система внутренней информации промышленного робота предназначена для оценки положения звеньев манипулятора, определения их скоростей и ускорений в каждый момент времени и сравнение с требуемыми параметрами движения; аварийной блокировки. Система внутренней информации токарного станка модели ТПК-125ВН2 осуществляет контроль над перемещением поперечного и продольного стола, а также фиксирует момент размещения детали в зажимном приспособлении станка. Эти системы являются обязательными.
Основными требованиями, предъявляемыми к датчикам системы, являются надёжность, малые габариты и масса, помехоустойчивость и устойчивость к воздействиям окружающей среды и низкая стоимость.
Для оценки положения и скорости перемещения удобно применять путевые (конечные) выключатели серии ВПК. Они осуществляют коммутацию переменного тока напряжением до 500 В и постоянного тока напряжением до 220 В под воздействием управляющих упоров; номинальная сила коммутируемого тока 4-6 А. Масса выключателей 0,17-1,32 кг; рабочий ход 5-12 мм. Выключатели выдерживают не менее 2 млн. циклов включения.
Путевые выключатели в промышленном роботе располагаем: в механизме поворота, где осуществляется контроль угла поворота - для управления скоростью; в механизме подъёма и опускания руки - для управления скоростью перемещения; в механизме выдвижения руки - для контроля положения руки. В станке путевые выключатели расположены: на поперечном и продольном столах - для контроля положения стола и управления автоматическим циклом обработки, используемом на станке, а также на зажимном приспособлении для фиксации положения детали в зажимном приспособлении станка.
Для контроля углового положения блока поворота кисти руки используются два бесконтактных импульсных датчика крайних и промежуточных позиций. Эти датчики отличаются высокими техническими и эксплуатационными характеристиками. Разрешающая способность датчиков 0,1°, что обеспечивает стабильность установки угла поворота кисти в пределах ±0,3°.
Для аварийной блокировки промышленного робота при упоре схвата в препятствие используем конечный микровыключатель, который подаёт аварийный сигнал в устройство управления промышленным роботом.
Контроль состояния зажима или разжима деталей губками схвата осуществляем конечными микровыключателями.
С целью контроля положения ограждения, устанавливаем конечные выключатели, которые дают сигнал для работы станка в автоматическом цикле с роботом.
Для безопасности обслуживающего персонала необходимо
ограждение рабочей зоны РТК. Оно может быть выполнено на основе устройств, использующих контактные, силовые, ультразвуковые, светолокационные и другие датчики. Относительно проектируемого РТК примем систему светозащиты рабочей зоны промышленного робота, выполненную по модульному принципу с применением светолокационных датчиков. В состав системы входят стойки светоизлучателей и фотоприёмников, применяемых попарно (смотри рис. 4.3.6.), а также блок логических преобразователей. Стойки излучателей и фотоприёмников регистрируют момент появления человека в зоне рабочего пространства промышленного робота.
Рис. 4.3.5.
Технико-экономическая часть
|
|
История развития пистолетов-пулеметов: Предпосылкой для возникновения пистолетов-пулеметов послужила давняя тенденция тяготения винтовок...
Особенности сооружения опор в сложных условиях: Сооружение ВЛ в районах с суровыми климатическими и тяжелыми геологическими условиями...
Общие условия выбора системы дренажа: Система дренажа выбирается в зависимости от характера защищаемого...
История развития хранилищ для нефти: Первые склады нефти появились в XVII веке. Они представляли собой землянные ямы-амбара глубиной 4…5 м...
© cyberpedia.su 2017-2024 - Не является автором материалов. Исключительное право сохранено за автором текста.
Если вы не хотите, чтобы данный материал был у нас на сайте, перейдите по ссылке: Нарушение авторских прав. Мы поможем в написании вашей работы!