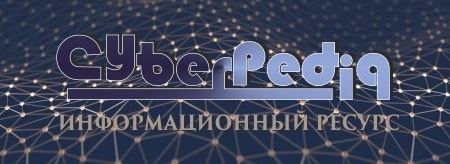
Индивидуальные очистные сооружения: К классу индивидуальных очистных сооружений относят сооружения, пропускная способность которых...
Поперечные профили набережных и береговой полосы: На городских территориях берегоукрепление проектируют с учетом технических и экономических требований, но особое значение придают эстетическим...
Топ:
Особенности труда и отдыха в условиях низких температур: К работам при низких температурах на открытом воздухе и в не отапливаемых помещениях допускаются лица не моложе 18 лет, прошедшие...
Отражение на счетах бухгалтерского учета процесса приобретения: Процесс заготовления представляет систему экономических событий, включающих приобретение организацией у поставщиков сырья...
Методика измерений сопротивления растеканию тока анодного заземления: Анодный заземлитель (анод) – проводник, погруженный в электролитическую среду (грунт, раствор электролита) и подключенный к положительному...
Интересное:
Аура как энергетическое поле: многослойную ауру человека можно представить себе подобным...
Финансовый рынок и его значение в управлении денежными потоками на современном этапе: любому предприятию для расширения производства и увеличения прибыли нужны...
Как мы говорим и как мы слушаем: общение можно сравнить с огромным зонтиком, под которым скрыто все...
Дисциплины:
![]() |
![]() |
5.00
из
|
Заказать работу |
|
|
Варианты уплотнений | Условия эксплуатации уплотнений | |||||||||||
Опора | Расположение уплотнения | Метод смазывания опоры | Быстроходность λ = dn max, мм·мин-1 | |||||||||
Передняя | Задняя | Наружное | Внутреннее | П | К | Ц | М | В | < 1,5·105 | 1,5·105…5·105 | > 5·105 | |
01 а | 1 | 0 | 1 | 0 | 0 | 1 | 1 | 0 | 0 | 1 | 0 | 0 |
01 б | 0 | 1 | 1 | 0 | 0 | 1 | 1 | 0 | 0 | 1 | 0 | 0 |
02 | 1 | 0 | 1 | 0 | 1 | 1 | 0 | 0 | 0 | 1 | 1 | 1 |
03 | 1 | 0 | 1 | 0 | 1 | 1 | 0 | 1 | 0 | 1 | 1 | 1 |
04 | 1 | 0 | 1 | 0 | 1 | 1 | 0 | 1 | 0 | 1 | 1 | 1 |
04 | 0 | 1 | 1 | 0 | 1 | 1 | 0 | 1 | 0 | 1 | 1 | 1 |
05 а | 1 | 0 | 1 | 0 | 1 | 1 | 0 | 1 | 0 | 1 | 1 | 1 |
05 б | 0 | 1 | 1 | 0 | 1 | 1 | 0 | 1 | 0 | 1 | 1 | 1 |
06 | 1 | 0 | 1 | 0 | 0 | 0 | 1 | 0 | 0 | 1 | 1 | 0 |
06 | 1 | 0 | 1 | 0 | 1 | 1 | 0 | 0 | 0 | 1 | 1 | 0 |
07 | 1 | 0 | 1 | 0 | 1 | 1 | 0 | 1 | 0 | 1 | 1 | 1 |
08 | 1 | 0 | 1 | 0 | 0 | 1 | 1 | 1 | 1 | 1 | 1 | 0 |
09 | 1 | 0 | 1 | 0 | 0 | 1 | 1 | 0 | 1 | 1 | 1 | 0 |
10 | 1 | 0 | 1 | 0 | 1 | 1 | 0 | 0 | 0 | 1 | 1 | 1 |
10 | 1 | 0 | 1 | 0 | 0 | 0 | 0 | 1 | 0 | 1 | 1 | 1 |
10 | 0 | 1 | 1 | 0 | 1 | 1 | 0 | 1 | 0 | 1 | 1 | 1 |
11 | 0 | 1 | 1 | 0 | 1 | 1 | 0 | 1 | 0 | 1 | 1 | 1 |
11 | 0 | 1 | 1 | 0 | 0 | 0 | 1 | 1 | 1 | 1 | 1 | 1 |
12 | 0 | 1 | 1 | 0 | 0 | 1 | 1 | 1 | 1 | 1 | 1 | 1 |
12 | 0 | 1 | 1 | 0 | 1 | 1 | 0 | 1 | 0 | 1 | 1 | 1 |
13 | 1 | 1 | 0 | 1 | 0 | 1 | 1 | 1 | 1 | 1 | 1 | 1 |
14 | 0 | 1 | 0 | 1 | 1 | 1 | 1 | 1 | 1 | 1 | 1 | 1 |
14 | 0 | 1 | 0 | 1 | 1 | 0 | 0 | 0 | 0 | 1 | 1 | 1 |
15 | 1 | 0 | 0 | 1 | 0 | 1 | 1 | 1 | 1 | 1 | 1 | 1 |
15 | 0 | 1 | 0 | 1 | 0 | 1 | 1 | 1 | 1 | 1 | 1 | 1 |
16 | 1 | 1 | 0 | 1 | 1 | 1 | 0 | 1 | 0 | 1 | 1 | 1 |
16 | 1 | 1 | 0 | 1 | 0 | 0 | 1 | 0 | 1 | 1 | 1 | 1 |
Окончание табл. 2.20
Варианты уплотнений | Условия эксплуатации уплотнений | ||||||||
Расположение оси вращения опоры | Внешняя среда | Место расположения приводного элемента | |||||||
Горизонтальное | Вертикальное А | Вертикальное Б | I | II | III | Между опорами | На заднем конце (шкив, муфта) | На заднем конце (зубчатое колесо) | |
01 а | 1 | 0 | 1 | 0 | 1 | 1 | 1 | 1 | 1 |
01 б | 1 | 1 | 0 | 0 | 1 | 1 | 1 | 1 | 1 |
02 | 1 | 0 | 0 | 0 | 1 | 1 | 1 | 1 | 1 |
03 | 1 | 0 | 1 | 1 | 1 | 0 | 1 | 1 | 1 |
04 | 1 | 0 | 1 | 1 | 1 | 0 | 1 | 1 | 1 |
04 | 1 | 1 | 0 | 1 | 1 | 0 | 0 | 1 | 0 |
05 а | 1 | 0 | 1 | 1 | 1 | 0 | 1 | 1 | 1 |
05 б | 1 | 1 | 0 | 1 | 1 | 0 | 0 | 1 | 1 |
06 | 1 | 0 | 0 | 1 | 1 | 0 | 1 | 1 | 1 |
06 | 1 | 0 | 1 | 1 | 1 | 0 | 1 | 1 | 1 |
07 | 1 | 0 | 1 | 1 | 1 | 0 | 1 | 1 | 1 |
08 | 1 | 0 | 0 | 1 | 1 | 1 | 1 | 1 | 1 |
09 | 0 | 0 | 1 | 0 | 1 | 1 | 1 | 1 | 1 |
10 | 1 | 1 | 0 | 1 | 1 | 0 | 1 | 1 | 1 |
10 | 1 | 1 | 0 | 1 | 1 | 1 | 1 | 1 | 1 |
10 | 1 | 0 | 1 | 1 | 1 | 1 | 1 | 1 | 0 |
11 | 1 | 1 | 1 | 1 | 1 | 1 | 1 | 1 | 1 |
11 | 1 | 0 | 1 | 1 | 1 | 1 | 1 | 1 | 1 |
12 | 1 | 0 | 0 | 1 | 1 | 1 | 1 | 1 | 1 |
12 | 1 | 1 | 0 | 1 | 1 | 1 | 1 | 1 | 1 |
13 | 1 | 0 | 0 | 1 | 1 | 1 | 0 | 1 | 1 |
14 | 1 | 0 | 0 | 1 | 1 | 1 | 0 | 1 | 1 |
14 | 1 | 1 | 1 | 1 | 1 | 1 | 0 | 1 | 0 |
15 | 0 | 0 | 1 | 1 | 1 | 1 | 1 | 0 | 0 |
15 | 0 | 1 | 0 | 1 | 1 | 1 | 1 | 0 | 0 |
16 | 1 | 1 | 1 | 1 | 1 | 1 | 0 | 1 | 0 |
16 | 1 | 0 | 0 | 1 | 1 | 1 | 0 | 1 | 1 |
|
Таблица позволяет сравнить между собой несколько вариантов уплотнений и выбрать наилучший из них, который наберет больше положительных ответов (больше единичек).
В таблице обозначено:
· метод смазывания опор: П – смазывание опор пластичным материалом; К – капельное смазывание опор; Ц – циркуляционное смазывание опор; М – смазывание опор масляным туманом; В – смазывание опор впрыскиванием;
· расположение оси вращения опоры: А – передний конец шпинделя обращен вверх; Б – передний конец шпинделя обращен вниз;
· внешняя среда: I – слабозагрязненная среда (наличие сливной стружки, отсутствие СОЖ); II – среднезагрязненная среда (наличие любой стружки, отсутствие СОЖ); III – сильнозагрязненная среда (наличие любой стружки, абразива и большого количества СОЖ).
Размеры бесконтактных (лабиринтных) уплотнений (03, 04, 05 и т.д., рис. 2.22) приведены в табл. 2.21, а манжетных уплотнений в табл. 2.22.
Таблица 2.21
Размеры лабиринтных уплотнений, мм
| ||||||||||||
d 0 | d 1 | h | D 1 | D 2 | D 3 | D 4 | D 5 | D 6 | D 7 | D 8 | D 9 | |
25 | 40 | 2,5±1 | 40,6 | 54,4 | 55 | 69,4 | 70 | – | – | – | – | |
30 | 45 | 45,6 | 59,4 | 60 | 74,4 | 75 | ||||||
35 | 50 | 50,6 | 64,4 | 65 | 79,4 | 80 | ||||||
40 | 55 | 55,6 | 69,4 | 70 | 84,4 | 85 | ||||||
45 | 60 | 60,8 | 74,2 | 75 | 89,2 | 90 | ||||||
50 | 65 | 65,8 | 79,2 | 80 | 94,2 | 95 | ||||||
55 | 70 | 70,8 | 84,2 | 85 | 99,2 | 100 | ||||||
60 | 80 | 80,8 | 94,2 | 95 | 109,2 | 110 | ||||||
65 | 85 | 85,8 | 99,2 | 100 | 114,2 | 115 | 129,2 | 130 | 144,2 | 145 | ||
70 | 90 | 90,8 | 104,2 | 105 | 119,2 | 120 | 134,2 | 135 | 149,2 | 150 | ||
75 | 95 | 95,8 | 109,2 | 110 | 124,2 | 125 | 139,2 | 140 | 154,2 | 155 | ||
80 | 100 | 3 ± 1 | 100,8 | 114,2 | 115 | 129,2 | 130 | 144,2 | 145 | 159,2 | 160 | |
90 | 110 | 110,8 | 124,2 | 125 | 139,2 | 140 | 154,2 | 155 | 169,2 | 170 | ||
95 | 120 | 121 | 134 | 135 | 149 | 150 | 164 | 165 | 179 | 180 | ||
100 | 130 | 131 | 144 | 145 | 159 | 160 | 174 | 175 | 189 | 190 | ||
110 | 140 | 141 | 159 | 160 | 179 | 180 | 199 | 200 | 219 | 220 | ||
120 | 150 | 151 | 169 | 170 | 189 | 190 | 209 | 210 | 229 | 230 | ||
130 | 160 | 161 | 179 | 180 | 199 | 200 | 219 | 220 | 239 | 240 | ||
140 | 170 | 171 | 189 | 190 | 209 | 210 | 229 | 230 | 249 | 250 | ||
150 | 180 | 181 | 199 | 200 | 229 | 220 | 239 | 240 | 259 | 260 | ||
160 | 190 | 191 | 209 | 210 | 229 | 230 | 349 | 250 | 269 | 270 | ||
170 | 200 | 201 | 219 | 220 | 239 | 240 | 259 | 260 | 279 | 280 | ||
Примечание. Размеры d 1, D 2, D 4, D 6, D 8 по h11. Размеры D 1, D 3, D 5, D 7, D 9 по H11. Глубина кольцевых пазов – 8 мм.
|
Таблица 2.22
Размеры манжетных уплотнений для валов (ГОСТ 8752-79), мм
Тип 1 | Тип 2 | |||||||||
| | |||||||||
Диаметр вала, d | D 1 | h 1 | h 2 | Диаметр вала, d | D 1 | h 1 | h 2 | |||
1-й ряд | 2-й ряд | 1-й ряд | 2-й ряд | 1-й ряд | 2-й ряд | 1-й ряд | 2-й ряд | |||
20 | 40 | 35 | 8 | 12 | 42 | 62 | 65 | 10 | 14 | |
37 | 68 | |||||||||
38 | 44 | – | 62 | |||||||
42 | 10 | 14 | 65 | |||||||
21 | 37 | 8 | 12 | 45 | 65 | 62 | ||||
42 | 10 | 14 | 70 | |||||||
22 | 35 | 8 | 12 | 48 | 70 | 65 | ||||
42 | 10 | 14 | 72 | |||||||
24 | 50 | |||||||||
45 | 75 | |||||||||
25 | 42 | 40 | 8 | 12 | 80 | 12 | 16 | |||
45 | 10 | 14 | 52 | 75 | 72 | 10 | 14 | |||
26 | 45 | 40 | 8 | 12 | 80 | 12 | 16 | |||
47 | 10 | 14 | 55 | 80 | 75 | 10 | 14 | |||
28 | – | 45 | 82 | 12 | 16 | |||||
47 | 56 | – | 10 | 14 | ||||||
50 | 58 | 75 | ||||||||
30 | 52 | 45 | 82 | 12 | 16 | |||||
47 | 60 | 85 | 80 | 10 | 14 | |||||
50 | 82 | |||||||||
32 | 58 | 45 | 62 | – | 80 | |||||
50 | 82 | |||||||||
35 | 47 | 85 | ||||||||
50 | 90 | 12 | 16 | |||||||
55 | 63 | 90 | – | 10 | 14 | |||||
57 | 65 | 95 | ||||||||
36 | 52 | 67 | – | 90 | 12 | 16 | ||||
55 | 68 | |||||||||
38 | 95 | |||||||||
60 | 70 | 95 | 100 | 10 | 14 | |||||
62 | 71 | – | ||||||||
40 | 55 | 75 | 100 | |||||||
58 | 102 | 12 | 16 |
ВЫБОР СИСТЕМЫ СМАЗКИ
Система смазки в приводах станков предназначена для ввода в зону трения вращающихся деталей жидкого смазочного материала с целью повышения долговечности контактирующих между собой поверхностей деталей (подшипников, зубчатых колес и др.), снижения износа и повышения КПД привода. В приводах главного движения чаще всего используются две системы смазки: автономная и централизованная от одной насосной станции для смазки станочных узлов всего станка.
Автономная смазка смазывает только трущиеся детали одного станочного узла. На рис. 2.23 представлена принципиальная автономная схема смазки коробки скоростей консольно-фрезерного станка. Система смазки включает в себя резервуар 1, расположенный в станине, фильтр 2, плунжерный насос 3, распределитель 4 и систему разводящих трубок 5 к зубчатым колесам и подшипникам. Контроль за подачей смазки и её уровнем в резервуаре осуществляется визуально по маслоуказателям 6 и 7.
![]() |
Рис. 2.23. Принципиальная схема смазки коробки скоростей консольно-фрезерного станка |
Плунжерный насос (рис. 2.24) смонтирован на одном из валов коробки скоростей. Возвратно-поступательное движение плунжер 2 получает от пружины 5 и шарикоподшипника 1, посаженного эксцентрично на валу коробки скоростей. При движении плунжера вверх масло из резервуара через трубку и обратный клапан втягивается в полость 6. При перемещении плунжера вниз клапан 7 закрывается и масло под давлением через обратный клапан 4 поступает в трубопровод 3 и далее к деталям коробки скоростей, от которых самотеком возвращается в резервуар. Данная система смазки обеспечивает непрерывную подачу масла под давлением к точкам трения, обеспечивая при этом хороший отвод тепла. Плунжерный насос обеспечивает устойчивую работу системы, если число оборотов вала с эксцентриком составляет 500…800 мин-1.
|
![]() |
Рис. 2.24. Конструкция плунжерного насоса |
В коробках скоростей станков токарной группы широко используются пластинчатые нерегулируемые насосы, которые получают вращение от первого вала редуктора через клиноременную передачу. Источником движения является асинхронный электродвигатель.
При централизованной системе смазки в коробке скоростей показываются места входа и выхода маслопровода в редукторе и места подвода масла к подшипникам и зубчатым колесам. К подшипникам качения масло подводят таким образом, чтобы оно стекало в картер через подшипник. При вертикальном расположении вала верхнюю подшипниковую опору смазывают через специальные каналы в крышке редуктора поливом масла сверху на подшипник. Нижняя опора вертикального вала должна быть изолирована от масляной ванны редуктора, или в нижней крышке, поддерживающей подшипник, должен быть предусмотрен проход для слива масла в специальный поддон. Подшипник не должен находиться в масляной ванне, поскольку сепаратор подшипника будет «перемалывать» масло и интенсивно его нагревать. Свободный слив масла снижает температуру подшипников, в свою очередь масло в резервуаре охлаждается специальным холодильником (холодную воду прокачивают по трубам через масляную ванну), чтобы температура масла в резервуаре при работе станка не превышала 50ºС.
|
Расход масла при циркуляционной смазке зависит от типа подшипников, частоты его вращения и вязкости масла. Для конических подшипников рекомендуемый расход масла (см3/мин) составляет Q = (5…10)· d. Для радиально-упорных подшипников при d < 120 мм, Q = 800…1000 см3/мин. Для смазывания упорно-радиальных подшипников при диаметре d = 80…180 мм, Q = 500…5000 см3/мин.
Численные значения предельной быстроходности валов на примере шпиндельных узлов приведены в табл. 2.23.
Таблица 2.23
|
|
Типы оградительных сооружений в морском порту: По расположению оградительных сооружений в плане различают волноломы, обе оконечности...
Автоматическое растормаживание колес: Тормозные устройства колес предназначены для уменьшения длины пробега и улучшения маневрирования ВС при...
Опора деревянной одностоечной и способы укрепление угловых опор: Опоры ВЛ - конструкции, предназначенные для поддерживания проводов на необходимой высоте над землей, водой...
Историки об Елизавете Петровне: Елизавета попала между двумя встречными культурными течениями, воспитывалась среди новых европейских веяний и преданий...
© cyberpedia.su 2017-2024 - Не является автором материалов. Исключительное право сохранено за автором текста.
Если вы не хотите, чтобы данный материал был у нас на сайте, перейдите по ссылке: Нарушение авторских прав. Мы поможем в написании вашей работы!